Do you sometimes feel like your injection molding process isn’t giving you the best results?
Improving injection mold efficiency requires looking at mold design closely. Adjust molding settings for better results. Try smart production methods for even more success. These steps help lower cycle times. Waste goes down too. Productivity goes way up.
That feeling occurs when optimizing something clicks together. Diving into advanced techniques and technologies in manufacturing causes this. It resembles finding rhythm in a complex dance. Every step times perfectly. Every move supports the next. These advancements turn your manufacturing processes into a well-oiled machine.
Optimizing mold design reduces cycle time.True
Improved mold design enhances efficiency by minimizing production delays.
Implementing management strategies increases waste.False
Effective strategies aim to reduce waste, not increase it.
How Does Mold Design Influence Manufacturing Efficiency?
Have you ever thought about how the complex design of molds speeds up the production process?
Mold design is very important in increasing production efficiency. It shortens cycle times. It improves product quality. It reduces material waste. Balanced runner systems are helpful. They are crucial. Effective cooling channels assist the process. Simplified mechanisms simplify work. Manufacturers increase their output significantly.
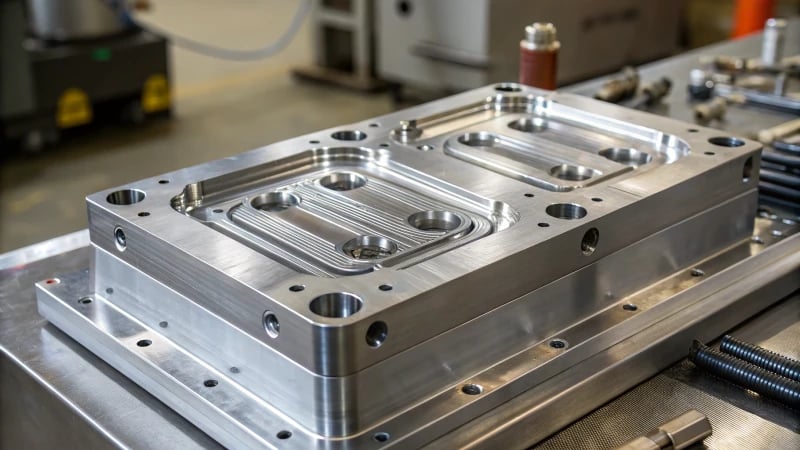
Optimizing Mold Structure
In the beginning, mold design seemed like solving a tricky puzzle. Success promised increased efficiency. Using a balanced runner system distributes equally, just like frosting on a cake, reducing differences in filling times1. Hot runner systems changed everything. They keep plastic hot, avoiding the cooling process that wastes time.
Efficient Cooling Systems
I discovered one day how important a good cooling channel is. It works like a river winding through the mold, cooling faster. A well-designed cooling channel follows the cavity contour to facilitate fast cooling. Conformal cooling can be achieved through technologies like 3D printing, significantly cutting cooling times.
Choosing the Right Materials
Picking the right materials feels like choosing the best tool. Hard steels such as P20 or H13 are reliable like a strong hammer. They last, handling many cycles and decrease downtime.
Material | Hardness | Wear Resistance |
---|---|---|
P20 | Medium | High |
H13 | High | Very High |
Standardization and Simplification
Standardizing parts is like sorting a toolbox. It makes tasks easier. Spare parts like guide sleeves or ejectors save time and aid in quick replacements and shorter procurement cycles. Simplifying tasks like core pulling speeds up cycles, much like a quick morning routine.
Process Optimization
Adjusting injection parameters seemed tough but became easier; it is like tuning a car engine for the best performance without compromising quality. Gas-assisted injection uses less material while keeping quality high.
Advanced Techniques
Multi-color injection offers fresh opportunities by allowing different colors all at once, saving time on extra steps from secondary processes. Automated systems help a lot; they improve output and reduce mistakes.
Automated material transportation2 keeps machines supplied, avoiding unexpected stops.
Using these mold design strategies raises production efficiency and ensures quality remains steady – a very satisfying result from careful planning.
Balanced runner systems reduce filling time discrepancies.True
Balanced runners ensure even cavity filling, decreasing time variations.
Conformal cooling channels increase cooling time.False
Conformal cooling shortens cooling time by following cavity contours.
How Can Injection Molding Parameters Be Optimized?
Struggled with injection molding settings, pondering if everything could simply fall into place?
Optimizing injection molding parameters involves adjusting factors such as how fast the injection goes, the force applied and the cooling duration. Modern techniques like gas-assisted molding play a role too. These adjustments increase efficiency and product quality. Efficiency improves. Quality improves.
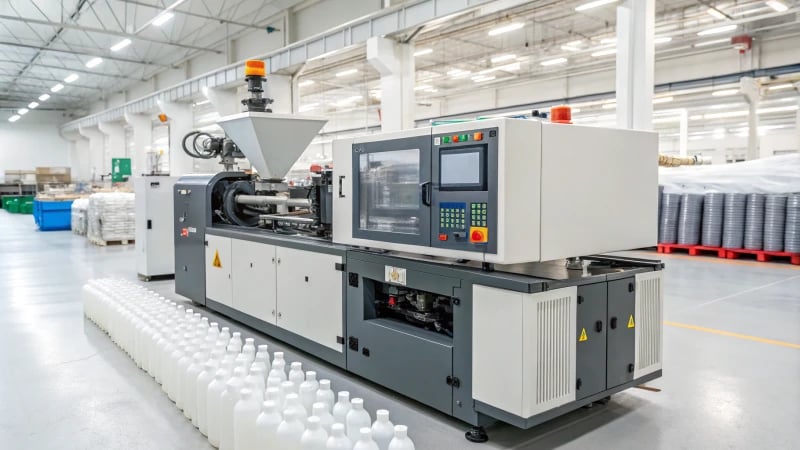
Injection Speed Optimization
Injection speed is like driving a car. Driving too fast may cause problems, like defects or trapped air. But the right speed leads to a smooth ride. Thin-walled items need quick injection to avoid cooling too soon. Keeping a steady melt flow3 really matters for holding product quality.
Balancing Holding Time and Pressure
In the beginning, I often adjusted holding times and pressures. Important for getting exact measurements. Mold flow analysis tools feel like looking into the future. They show ideal settings for holding time, securing quality without delay.
Parameter | Impact |
---|---|
Holding Time | Dimensional stability |
Pressure | Product strength |
Adjusting these settings is like solving a puzzle. Each part must fit perfectly to meet design needs well.
Efficient Cooling System Design
Cooling time is the hidden hero of molding. Creating a good cooling system is like crafting the best escape path for heat. Conformal cooling channels greatly shorten cycle times, reducing defects. I tried using cooler water to speed things up, but it needed care to prevent mold deformation4.
Advanced Technologies
Finding advanced tech like gas-assisted molding really changed the game. It’s like discovering a shortcut – less plastic, same quality. Multi-material products using two-color or multi-color molding save time and simplify steps.
Automation in Production Management
Automation brings the magic. Robots for tasks, like part removal, changed our process, cutting down non-molding time a lot. Automating material transport meant we never lacked raw materials mid-production – those were impressive days.
Keeping up with regular maintenance schedules5 showed me how taking care of molds keeps efficiency and quality working together. It’s all about making the complex field of injection molding feel easier and, maybe, even enjoyable.
Higher injection speed reduces filling time.True
Increasing the injection speed can decrease the time needed to fill the mold.
Automation increases non-molding time in production.False
Automation reduces non-molding time by streamlining tasks like part removal.
How Can Advanced Technologies Enhance Injection Molding Efficiency?
Do you ever wonder how to dramatically increase the efficiency of injection molding?
Hot runner systems, conformal cooling and production robots transform injection molding. They slash cycle times and improve consistency. These technologies simplify operations. Product quality goes up.
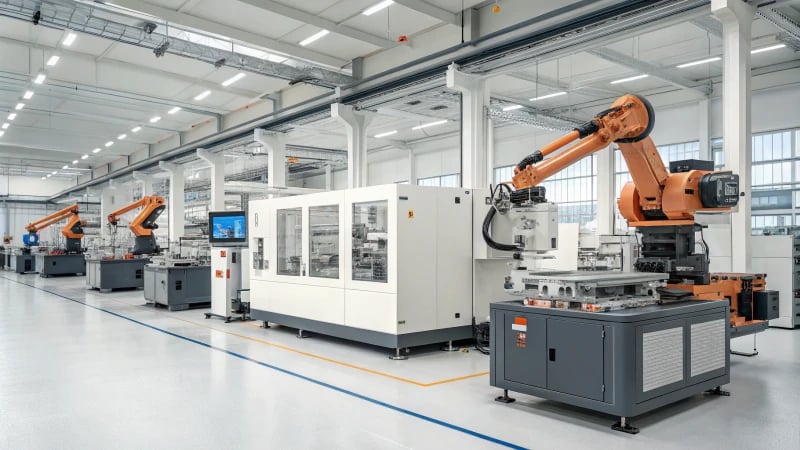
Optimizing Mold Design
1. Hot Runner Systems
The first time seeing a hot runner system was unforgettable. It reduced waste and saved time by keeping plastic soft, removing unwanted parts. This completely improved our production process.
2. Conformal Cooling Channels
These are the quiet champions of mold design. With 3D printing6, these channels fit the mold’s shape perfectly, cooling evenly and reducing cycle times.
Technology | Benefits |
---|---|
Hot Runner | Reduces waste and cycle time |
Conformal Cooling | Enhances cooling efficiency |
Injection Molding Process Innovations
1. Gas-Assisted Injection Molding
On a project with a tricky shape, gas-assisted molding was essential. It filled the mold efficiently, using less material and time, and it also lowered costs.
2. Multi-Color Injection Molding
Combining materials or colors in one step saves huge amounts of time. This method reduces transfer and processing time, increasing productivity.
Automation in Production
1. Robotic Integration
Introducing robots for tasks like part removal was like adding new skills to our team. Their precision and speed really reduced mistakes.
2. Automated Material Handling
Automated systems keep our machines filled, ensuring smooth production without unwanted breaks.
For a deep understanding of how these technologies change production efficiency, dive into recent industry insights7.
Hot runner systems reduce injection molding waste.True
Hot runner systems keep plastic molten, eliminating sprues and reducing waste.
Multi-color injection molding increases cycle times.False
It reduces cycle times by combining materials/colors in one setup.
Why Is Production Management Crucial for Efficiency?
Ever thought about how a well-tuned machine keeps running efficiently? Production management does this for manufacturing.
Production management is essential for efficiency. It organizes operations and brings resources together. Quality control is also part of this process. This careful planning reduces waste and improves production methods. Product quality rises.
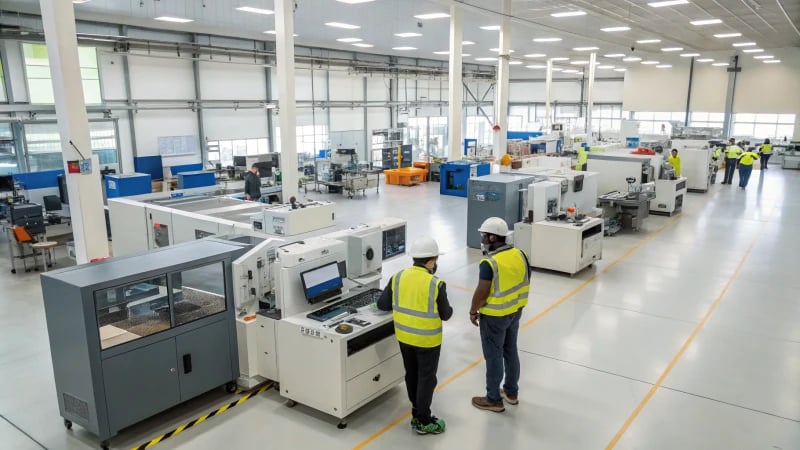
Streamlining Operations for Top Results
When I started in production management, I found it was about managing everything well. Imagine planning a family road trip so everyone arrives on time without problems. Smart resource allocation8 uses every machine and team member fully to hit goals without wasting time.
Coordination of Resources
Think of it as organizing a big dinner. Appetizers, main course, and dessert should be ready together. Production managers do this by aligning materials, equipment, and labor to avoid issues. Tools like automated scheduling systems9 act like skilled helpers, predicting jobs and shifting plans for smooth operations.
Resource | Benefit |
---|---|
Labor | Reduces idle time through better task allocation |
Materials | Minimizes waste with precise usage forecasts |
Equipment | Enhances uptime through scheduled maintenance |
Implementing Quality Control Methods
Quality control checks that every dish at a dinner tastes great. By watching and adjusting processes, production managers keep defects away and efficiency high with quality assurance protocols10.
Integration of Technology
New technology is like better kitchen gadgets – everything becomes easier! IoT and AI transformed how we track production. With real-time monitoring systems11, changes happen fast, maintaining quality without wasting resources.
Case Study: Injection Molds
In injection molding, smart management shines in mold design. It’s like fine-tuning a recipe for faster cooking without losing flavor. A balanced runner system fills cavities evenly, cutting cycle times and lifting productivity12. Conformal cooling channels greatly reduce cooling times.
- Mold Design Stage
- Improve mold structure with a hot runner system.
- Create smart cooling systems using 3D printing for tricky shapes.
- Simplify mold parts to speed up cycles.
- Injection Molding Process Optimization
- Adjust settings like injection speed and cooling time.
- Use advanced methods like gas-assisted molding.
Continuous Improvement
Continuous improvement focuses on being better every day. By adopting systematic reviews and pushing for new ideas, businesses stay competitive and adapt quickly13 to market changes.
Examining these aspects of production management gives companies big chances to increase their efficiency and grow their presence in the industry.
Production management reduces manufacturing downtime.True
Effective planning and control minimize unnecessary machine idle times.
Quality control increases defect rates in production.False
Quality control reduces defects by ensuring standards are consistently met.
Conclusion
Enhancing injection mold efficiency involves optimizing design, cooling systems, and automation while adjusting parameters like speed and pressure to reduce cycle times and improve product quality.
-
This link explores the advantages of balanced runner systems in injection molding, crucial for uniform cavity filling. ↩
-
Learn how automated material transport boosts efficiency by ensuring uninterrupted raw material supply to machines. ↩
-
Learn about strategies to ensure consistent melt flow, crucial for maintaining product integrity during high-speed injection. ↩
-
Discover techniques to prevent mold deformation by optimizing cooling parameters, crucial for maintaining product quality. ↩
-
Explore why regular maintenance is essential for optimal mold performance and reducing downtime. ↩
-
Discover how 3D printing enhances conformal cooling channels for more efficient mold design. ↩
-
Gain insights into automation’s role in boosting injection molding efficiency with cutting-edge technologies. ↩
-
Explore how effective allocation of resources enhances manufacturing efficiency by minimizing waste and optimizing productivity. ↩
-
Learn how automated scheduling can streamline operations by efficiently managing workloads and reducing delays. ↩
-
Understand how implementing quality assurance measures can reduce defects and ensure consistent product quality. ↩
-
Discover how real-time systems enhance production by allowing quick adjustments and maintaining product standards. ↩
-
Find out how balanced runner systems improve mold efficiency by ensuring even filling and reducing cycle times. ↩
-
Learn how continuous improvement strategies help businesses adapt to market changes and maintain competitiveness. ↩