Injection molds are truly the backbone of efficient manufacturing processes, especially when they’re put to the test in high-temperature environments.
To enhance the durability of injection molds in high-temperature environments, select materials with excellent heat resistance and thermal conductivity, optimize mold design to minimize stress, ensure precision in manufacturing processes, and maintain regular upkeep and inspection routines.
By understanding these fundamental principles, you can prolong the life of your molds, reduce production interruptions, and ultimately lower costs. Delve into the specifics below to discover expert techniques that can transform your manufacturing processes.
H13 steel is ideal for high-temperature injection molds.True
H13 steel maintains high hardness and strength at elevated temperatures, making it suitable for molds.
What Are the Best Materials for High-Temperature Injection Molds?
Selecting the right material for high-temperature injection molds is crucial for enhancing their durability and performance under stress.
The best materials for high-temperature injection molds include steel with good heat resistance like H13, and high-performance alloy tool steels. Copper alloys, known for their excellent thermal conductivity, are also ideal for mold components, aiding in efficient heat dissipation and reducing thermal fatigue.
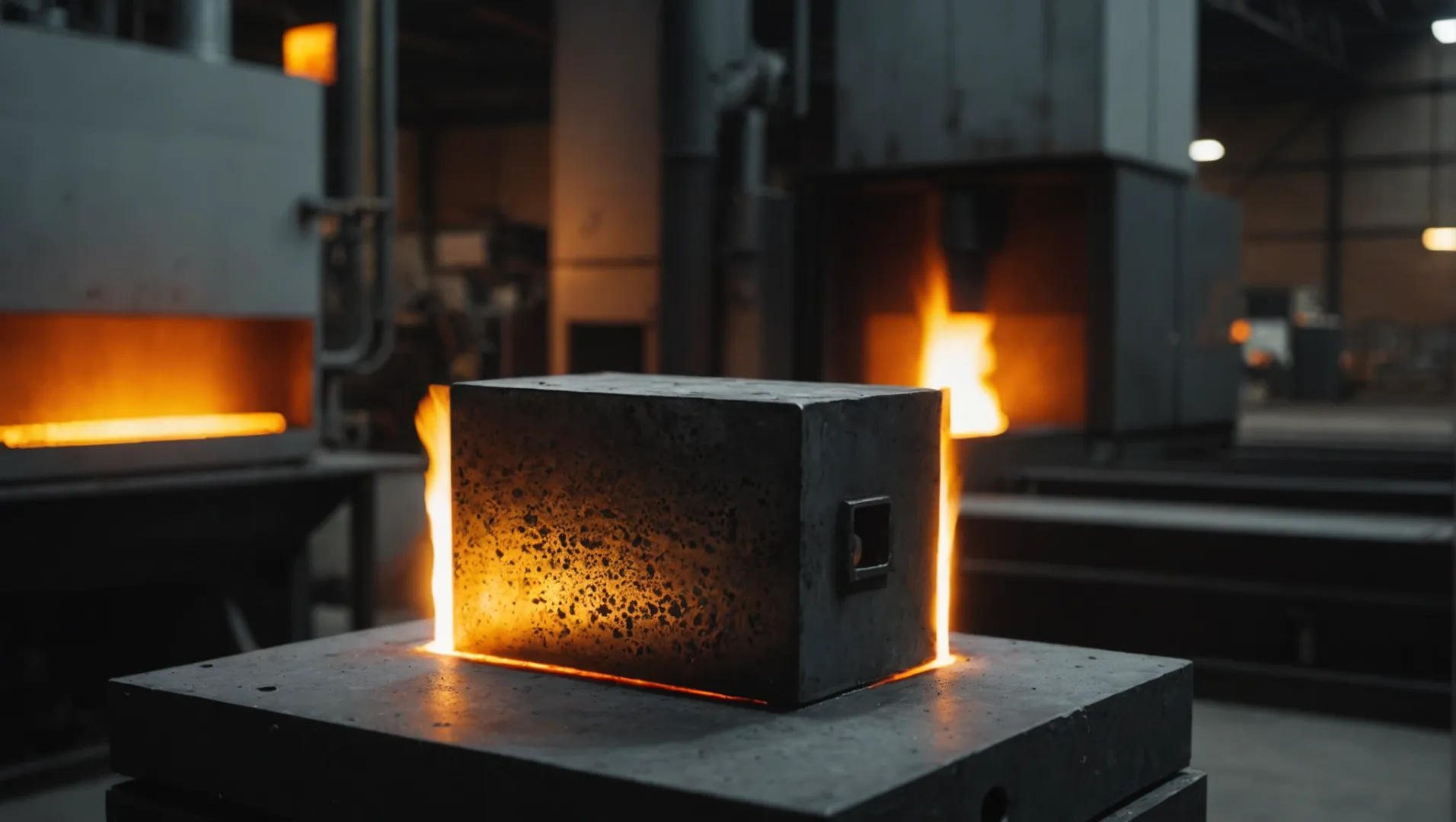
Selecting Steel with Heat Resistance
When considering materials for high-temperature injection molds, selecting steel that can withstand elevated temperatures without losing integrity is critical. Hot working die steels, such as H13, are prime examples due to their ability to maintain high hardness and strength. These steels possess thermal stability and thermal fatigue resistance, making them suitable for molds that will endure extreme conditions.
Moreover, high-performance alloy tool steels1 are developed through specialized heat treatment processes to enhance mechanical properties and ensure dimensional stability at high temperatures. These materials are integral in applications where precision and reliability are paramount.
Importance of Thermal Conductivity
Another key consideration is the thermal conductivity of the mold material. Efficient heat dissipation is vital to reduce heat accumulation and the risk of thermal fatigue. Copper alloys, noted for their exceptional thermal conductivity, are often employed as inserts or as part of a mold’s cooling system. This ensures that heat is swiftly conducted away from the mold surface, maintaining the integrity of the mold under continuous high-temperature operations.
Material | Benefits |
---|---|
H13 Steel | High hardness, strength at elevated temperatures |
Alloy Tool Steels | Good mechanical properties and dimensional stability |
Copper Alloys | Excellent thermal conductivity |
Combining Materials for Enhanced Performance
In some cases, combining different materials can yield superior performance in high-temperature environments. For instance, using copper alloys for areas requiring rapid cooling while employing steel for structural integrity can optimize the mold’s overall functionality.
Understanding the intricacies of material selection2 and how each component contributes to the mold’s performance can significantly enhance its durability in high-temperature settings.
H13 steel is ideal for high-temperature molds.True
H13 steel maintains high hardness and strength at elevated temperatures.
Copper alloys lack thermal conductivity for molds.False
Copper alloys have excellent thermal conductivity, aiding heat dissipation.
How Does Mold Design Influence Durability?
Explore how thoughtful mold design can significantly boost durability, especially in challenging environments.
Mold design influences durability through optimized cooling systems, stress concentration reduction, and mold cavity enhancements, all crucial in high-temperature scenarios.
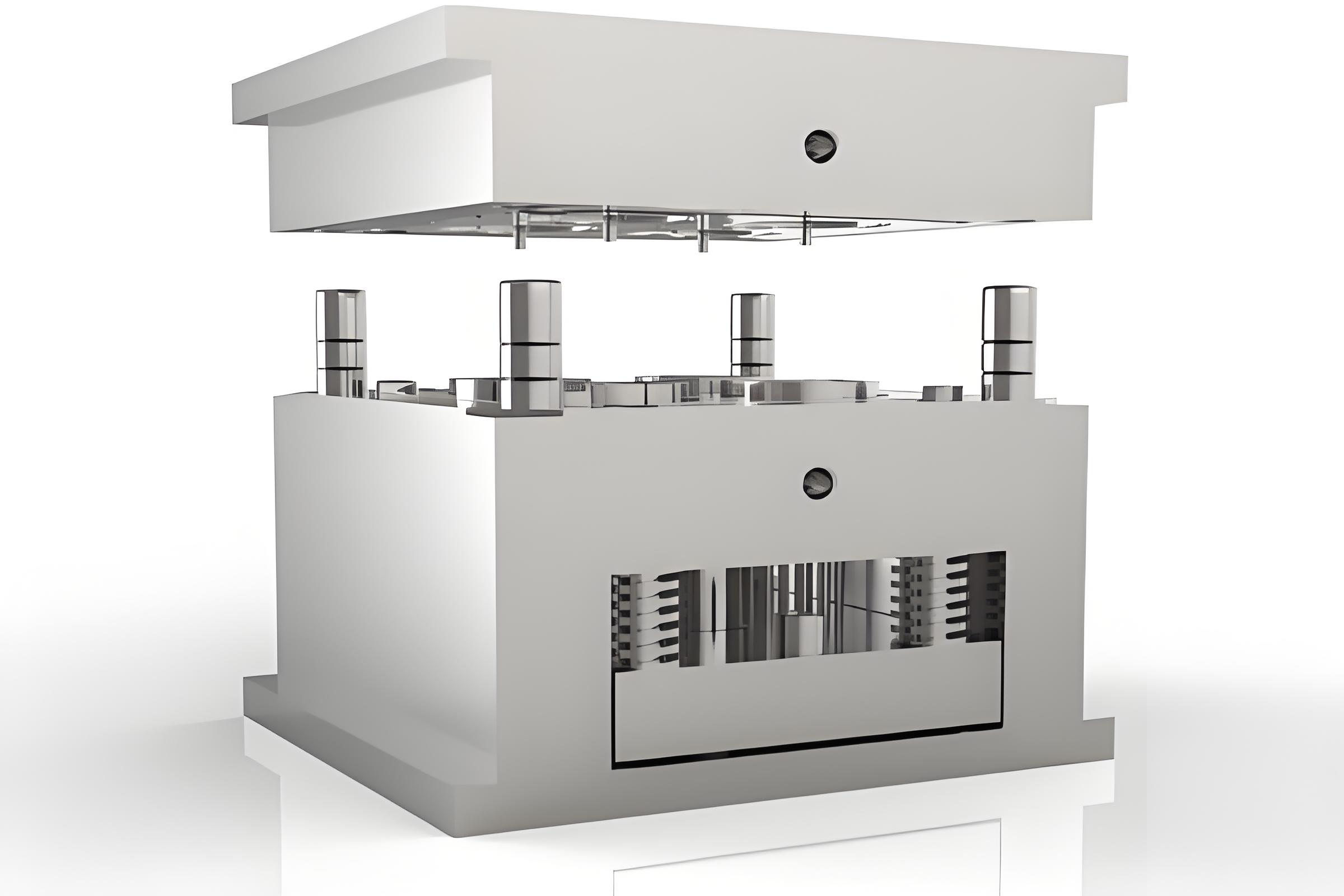
Optimizing Cooling Systems
A key factor in mold design is the cooling system. Properly designed cooling systems3 ensure efficient heat dissipation, a critical aspect when dealing with high temperatures. Increasing the number of cooling water channels and ensuring they are strategically placed close to the mold cavity surface can significantly improve heat distribution and reduce thermal stress.
Efficient cooling media, such as ice water or cooling oil, can further enhance cooling efficiency. However, it’s important to control the flow rate and temperature of these media to avoid any potential deformation of the mold due to uneven cooling.
Reducing Stress Concentration
Reducing stress concentration is another vital element. Sharp corners and abrupt transitions in the mold design should be avoided. Instead, employing smooth transition curves can help in evenly distributing stress. This not only boosts the mold’s strength but also its rigidity, minimizing deformation risks.
For larger molds, using a combined structure is advantageous. This approach not only facilitates easier processing and maintenance but also helps in reducing stress concentration by spreading it across the structure.
Enhancing Mold Cavity Structure
The mold cavity structure directly impacts the mold’s durability. A well-designed demolding slope eases product removal, thereby reducing wear and tear on the mold itself. Additionally, a properly designed exhaust system prevents gas accumulation, which could otherwise lead to high pressure and potential damage.
Using materials with superior thermal conductivity4 for inserts or cooling elements can further augment these design features. Copper alloys, for instance, are excellent for this purpose due to their high thermal conductivity, aiding in rapid heat dissipation and protecting the mold from thermal fatigue.
Summary Table: Key Design Considerations
Design Aspect | Benefits |
---|---|
Cooling System Optimization | Efficient heat dissipation |
Stress Reduction Techniques | Enhanced strength and rigidity |
Mold Cavity Enhancements | Reduced wear and gas pressure |
High Thermal Conductivity Use | Faster heat dissipation, less thermal fatigue |
Cooling systems improve mold durability.True
Efficient cooling systems enhance heat dissipation, reducing thermal stress.
Sharp corners increase mold strength.False
Sharp corners concentrate stress, weakening the mold and increasing risks.
Why Is Precision Machining Crucial for Mold Longevity?
Precision machining is the linchpin in crafting molds that withstand the rigors of high-temperature environments, ensuring prolonged functionality and reduced wear.
Precision machining is essential for mold longevity as it ensures dimensional accuracy and surface quality, reducing wear and thermal fatigue. Techniques such as EDM and wire cutting on key parts enhance precision, thereby extending mold life.
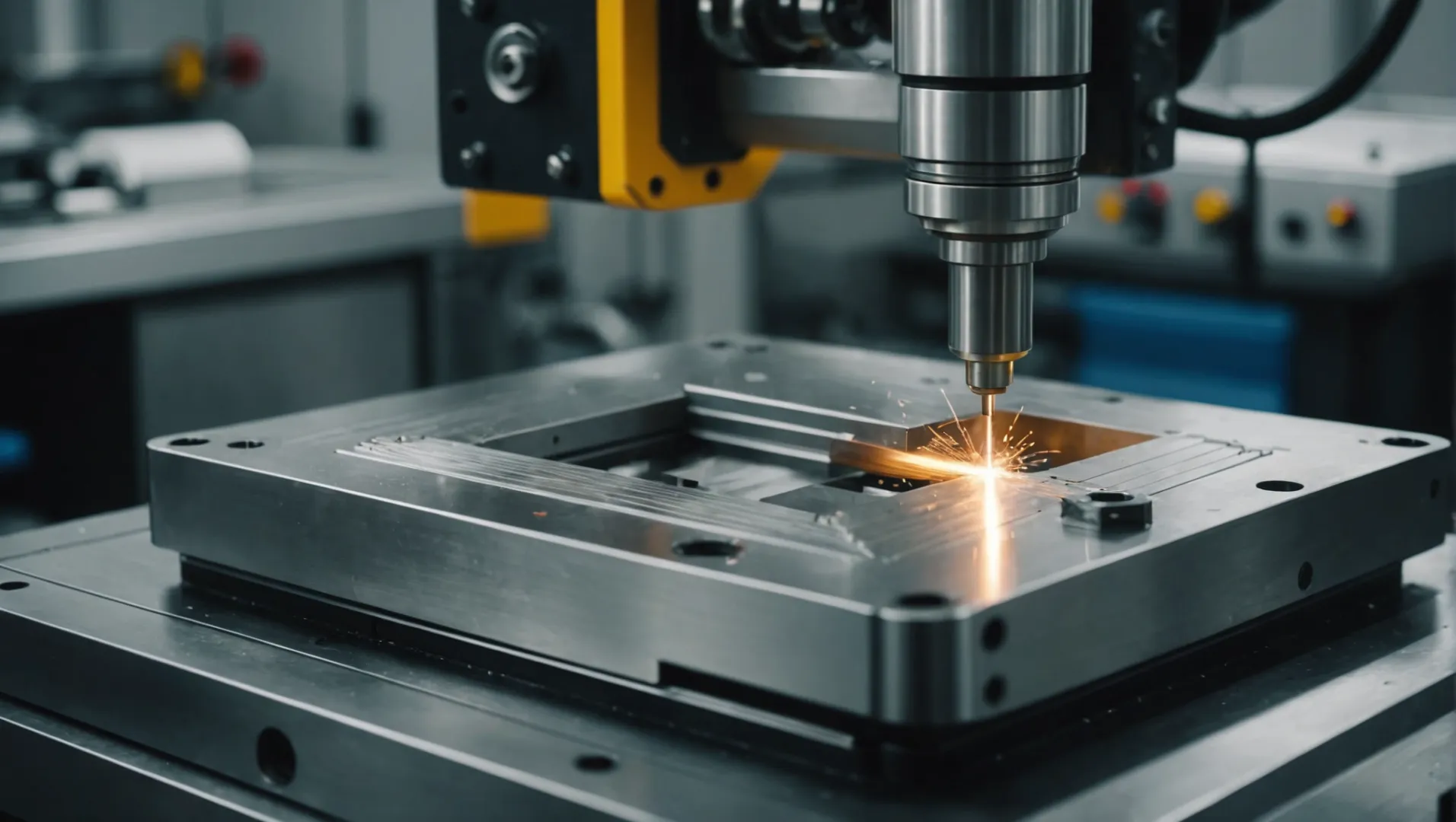
Importance of Dimensional Accuracy
In the realm of mold manufacturing, achieving high dimensional accuracy is pivotal. Precision machining allows for exact tolerances, ensuring that each component of the mold fits seamlessly. This precise fit is vital in maintaining the structural integrity of the mold, reducing the risk of deformation under stress and extending its operational life.
Surface Quality and Its Impact
The surface quality of a mold directly influences its durability. A smoother surface reduces friction during the molding process, minimizing wear and tear. Techniques like EDM (Electrical Discharge Machining)5 and wire cutting are employed to achieve this level of surface finish, providing molds with enhanced resistance to the high temperatures typically encountered in manufacturing settings.
Advanced Machining Techniques
-
Electrical Discharge Machining (EDM)
- EDM is an advanced machining process used to obtain high precision and intricate details in molds. It utilizes electrical sparks to erode material, allowing for complex shapes without inducing mechanical stresses.
- Ideal for hard materials, EDM enhances the precision of the mold’s intricate features, prolonging its life by reducing stress concentrations.
-
Wire Cutting
- This process uses a thin wire as an electrode to cut through materials with precision. It’s particularly useful for achieving fine cuts and complex geometries in metal molds.
- Wire cutting ensures that critical areas of the mold are machined with high accuracy, reducing potential points of failure over time.
Role of Heat Treatment in Machining
Following precision machining, appropriate heat treatment processes such as quenching and tempering are crucial. These processes enhance the hardness and thermal stability of the mold material, making it more resistant to wear and thermal fatigue. Proper control over heating temperatures and cooling rates during these processes ensures that molds maintain their designed specifications, further bolstering their durability.
Integrating Precision with Design Optimization
While precision machining is critical, it should be integrated with optimized mold design strategies. Features like cooling channels must be precisely machined to ensure even temperature distribution across the mold. This not only enhances efficiency but also mitigates thermal fatigue by preventing localized overheating.
In summary, precision machining forms the backbone of durable mold creation, where meticulous attention to detail during manufacturing can significantly prolong a mold’s lifespan in high-temperature environments.
Precision machining ensures dimensional accuracy in molds.True
Precision machining achieves exact tolerances, maintaining structural integrity.
EDM is ineffective for hard materials in mold making.False
EDM is ideal for hard materials, enhancing precision and reducing stress.
What Maintenance Practices Extend Mold Life?
Maximizing the lifespan of molds involves meticulous maintenance, ensuring they withstand wear and function optimally.
To extend mold life, adhere to regular maintenance schedules, perform thorough inspections, and apply preventive measures like component replacement and surface treatments. This not only prevents unexpected failures but also enhances mold performance.
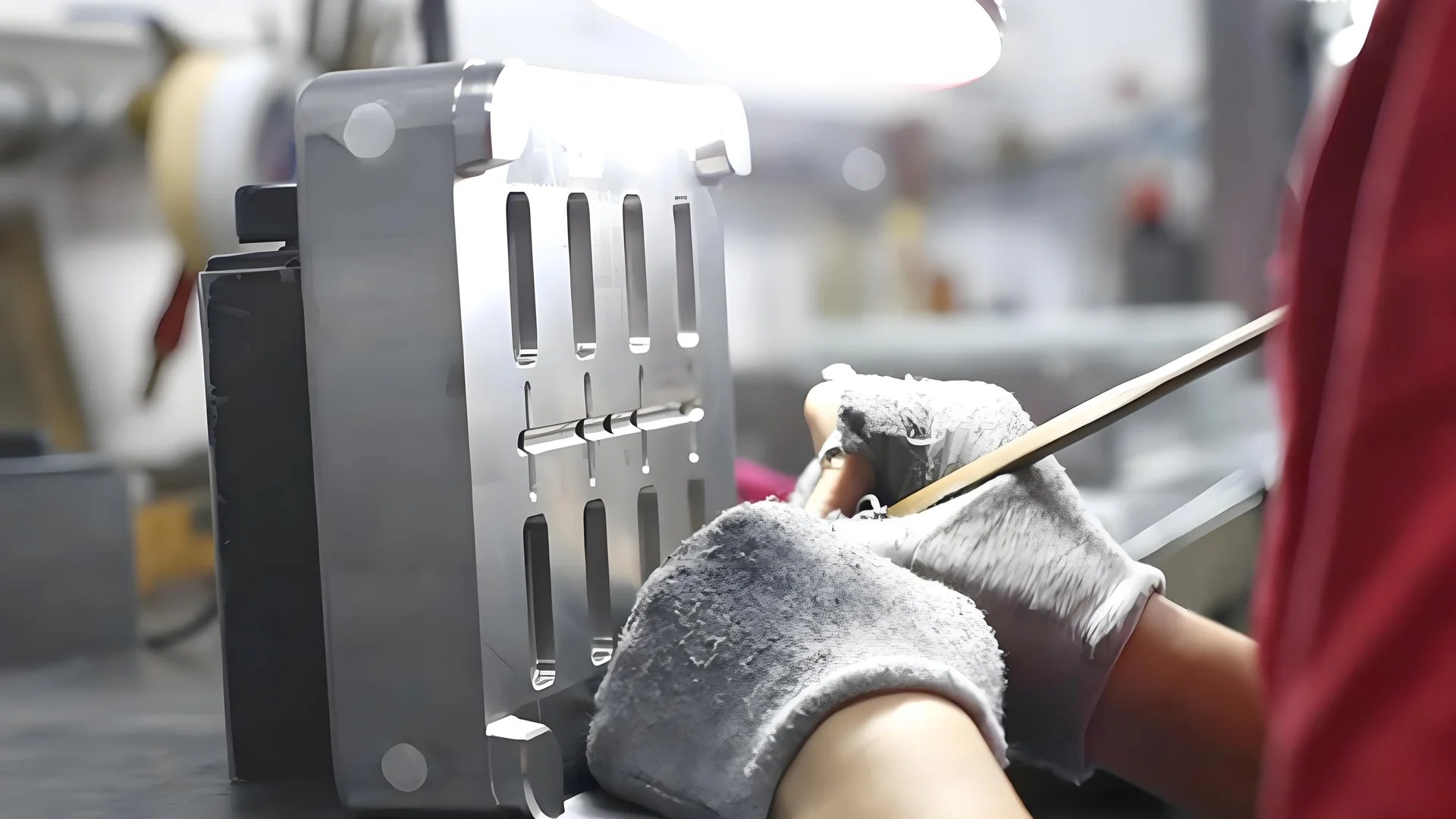
Implementing a Regular Maintenance Schedule
A structured maintenance plan is pivotal in prolonging mold life. Establishing a schedule for routine checks ensures that minor issues are identified before escalating into significant problems. Regular inspections should focus on the mold’s dimensional accuracy, cooling system efficiency, and the condition of ejector pins and seals. Developing a maintenance plan6 tailored to the specific needs of each mold can prevent costly downtimes and increase production reliability.
Conducting Thorough Inspections
Inspections are crucial in identifying potential problems early. Focus on critical areas like the surface quality of the mold cavity and any signs of wear or corrosion. Regularly check for any residue or build-up in the cooling channels that could impede heat dissipation. By using advanced inspection techniques, such as non-destructive testing methods, you can ensure comprehensive evaluation without risking mold damage.
Applying Preventive Measures
Preventive maintenance is about more than just fixing problems; it’s about taking proactive steps to prevent issues from occurring in the first place. This could include the regular replacement of vulnerable parts, such as seals and ejector pins, before they fail. Surface treatments, like hard chrome plating or nitriding, can also be applied to enhance wear resistance and reduce friction during operation. Understanding surface treatments7 can significantly extend the service life of molds by maintaining their operational integrity.
Training for Correct Operation
Ensuring that operators are well-trained can significantly reduce mold damage due to incorrect handling or operational errors. Training should cover the entire injection molding process, emphasizing the importance of adhering to established operating procedures. Proper training helps prevent excessive injection pressure or speed, which can cause undue stress and eventual failure of the mold components.
Regular Cleaning and Storage Practices
Keeping molds clean is essential for maintaining their functionality and longevity. After each use, molds should be thoroughly cleaned to remove any material residues that could cause corrosion or affect surface finish. When not in use, proper storage conditions must be maintained to prevent environmental damage. This includes controlling temperature and humidity levels to mitigate risks like rust or deformation.
Regular inspections prevent mold failures.True
Routine checks identify issues early, preventing significant problems.
Surface treatments reduce mold wear.True
Treatments like hard chrome plating enhance wear resistance.
Conclusion
Improving injection mold durability involves strategic choices in materials, design, and maintenance. By implementing these expert tips, manufacturers can ensure long-lasting mold performance, reducing downtime and costs.
-
Learn about specialized steels designed for extreme conditions.: 4140 alloy steel is a chromium-molybdenum medium-carbon steel that exhibits high toughness and good fatigue strength. With a good balance of … ↩
-
Explore techniques for optimizing mold performance.: Hot molds frequently have plate sequencing and mold actions within them. Progressive’s Plate Locks can operate to 600° F, and SRT Slide Retainers perform up to … ↩
-
Learn why efficient cooling systems are crucial for mold durability.: An improper injection mold cooling process, then, will almost always result in part defects that require rework or discard. The cooling process … ↩
-
Discover how copper alloys enhance heat dissipation in molds.: Benefits · Uniform Heating · Hardness · Coefficient of Friction · Bearing & Wear Applications · Chemical Resistance · Metal Cost · In Use Today · Useful Resources. ↩
-
Explore EDM’s role in achieving intricate details with high precision.: Electrical Discharge Machining (EDM) is a nonconventional machining process used primarily for tasks that would be unachievable with conventional methods. ↩
-
Learn to customize maintenance plans for different molds effectively.: The heart of an organized mold-maintenance plan is the Injection Mold Layout (IML) sheet. Mold-maintenance plan. ↩
-
Discover how surface treatments enhance mold durability.: Surface Treatments Protect Mold Finishes, Reduce Downtime and Part Failure. Surface treatment vendors are expanding their services to include … ↩