Picture this: You’re in the workshop, fine-tuning a design, and the question of safety lingers.
Enhance flame retardancy in injection molding by adding flame retardant additives to the polymer mix, which create a protective char layer, dilute flammable gases, or disrupt combustion to reduce flammability.
While this approach sets the groundwork for safer products, diving into the specifics of each additive can refine my strategy even more. I recall the time I discovered how different retardants influence the molding process, opening up new possibilities in product safety and performance. Understanding these nuances helps me ensure that every design not only meets safety standards but also enhances the overall quality of the product.
Flame retardant additives can form a protective char layer.True
Additives form a char layer, reducing material flammability.
All flame retardant additives interrupt the combustion process.False
Some additives dilute gases or form char, not interrupt combustion.

What Types of Flame Retardant Additives Are Available?
As a product designer, ensuring fire safety in my designs is crucial, and it all starts with understanding flame retardant additives. These additives are the unsung heroes, boosting material safety and compliance.
Flame retardant additives include halogenated, phosphorus-based, and metal hydroxide compounds, each suited for different industrial uses such as electronics and construction, with unique benefits and challenges.
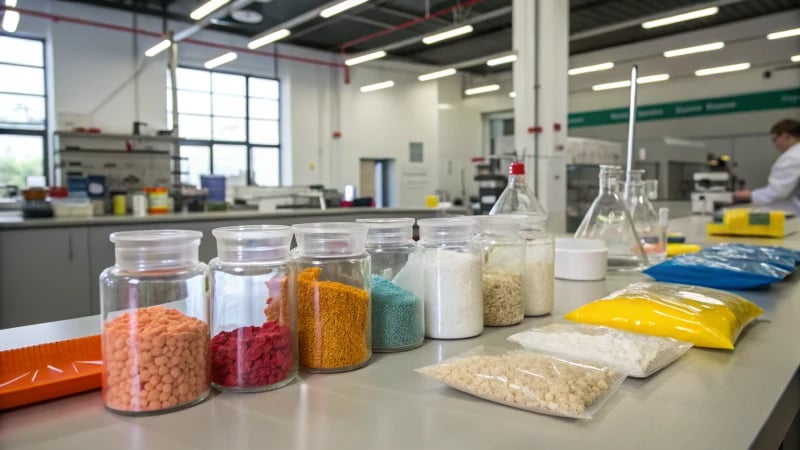
Halogenated Flame Retardants
When I first started working with electronic casings, I was introduced to halogenated flame retardants. These additives often incorporate bromine or chlorine, working their magic by disrupting the combustion process. Picture this: when flames get hungry, these additives1 release halogen radicals, stepping in like a heroic firefighting squad to break up the chemical reactions. They’ve been my go-to for those stringent fire regulation projects. However, I’m always mindful of their potential environmental and health impacts due to toxic byproducts.
Pros | Cons |
---|---|
Highly efficient at low concentrations | Potential toxicity and environmental impact |
Versatile in various polymers | Regulatory restrictions in some regions |
Phosphorus-based Flame Retardants
I remember a project involving textiles where phosphorus-based additives were my saving grace. They work by promoting charring and forming a protective barrier on the material’s surface. These are particularly useful when low smoke emission is a must, making them perfect for our textile and polyurethane applications. Plus, they’re less likely to produce that unpleasant toxic smoke during combustion, which always eases my mind.
Phosphorus-based flame retardants2 are less likely to produce toxic smoke during combustion, making them a preferred choice for applications needing lower smoke emission.
Metal Hydroxide Flame Retardants
Then there are the metal hydroxide flame retardants, like aluminum hydroxide or magnesium hydroxide. I often describe them as the eco-friendly option. When heated, they release water vapor, cooling the material and diluting flammable gases—nature’s way of lending a hand. The only catch? They require high loading levels which can impact the mechanical properties of the material. But hey, nothing’s perfect!
Type | Function |
---|---|
Aluminum Hydroxide | Releases water vapor to cool the substrate |
Magnesium Hydroxide | Acts similarly but with higher thermal stability |
Choosing the right flame retardant is a balancing act—one I’ve come to appreciate over years of trial and error. Understanding each type’s attributes helps me make informed decisions that are tailored to specific design needs, always keeping effectiveness, safety, and material compatibility at the forefront of my mind.
Understanding the selection process3 for flame retardants involves balancing effectiveness, safety, and material compatibility.
Halogenated flame retardants release halogen radicals.True
Halogenated additives release radicals that disrupt combustion, reducing fire risk.
Phosphorus-based flame retardants produce toxic smoke.False
They are preferred for low smoke emission, posing less health risk.
How Do Flame Retardants Affect Material Properties?
When I first encountered flame retardants, I was amazed by their dual role in safety and performance. But how exactly do they change the materials we rely on every day?
Flame retardants enhance fire resistance but may affect mechanical properties like strength and flexibility and pose environmental or health risks due to their chemical composition.
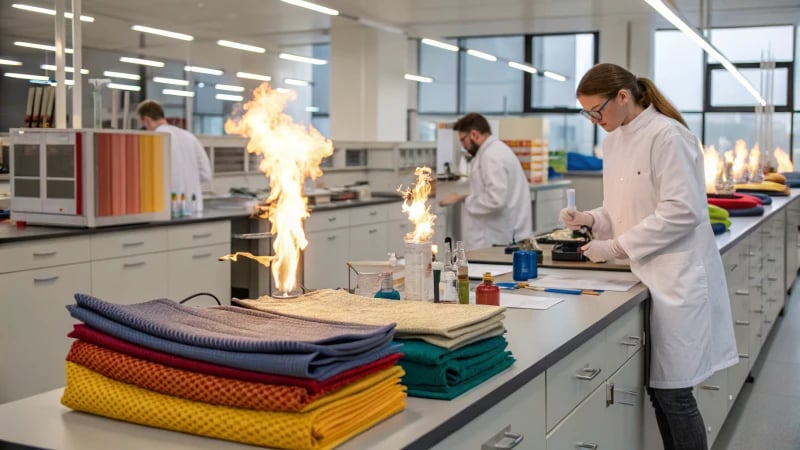
Mechanical Properties of Materials
From my early days as a designer, I realized how crucial it is to understand what goes into the materials we use. Flame retardants are no exception. They are added to materials to boost fire resistance, but this can significantly impact the mechanical properties. Take polymers, for example—adding flame retardants might decrease their tensile strength because these additives can alter the polymer chain structure, making them more brittle.
Property | Impact | Example |
---|---|---|
Tensile Strength | Decrease | Polymer chains break easily |
Flexibility | Reduced | Stiffer material |
In my line of work with consumer electronics, such changes can affect everything from the design to the manufacturing process4, often requiring us to rethink our material choices.
Thermal Stability and Durability
I’ve learned that while flame retardants often enhance a material’s thermal stability by creating a protective layer that slows down heat transfer, they can also reduce durability under cyclic thermal stress. This is something I’ve had to consider carefully when designing products that must withstand fluctuating temperatures. Balancing these factors is crucial in creating reliable, long-lasting products.
Health and Environmental Concerns
The potential health risks associated with flame retardants have always been a concern for me. Their chemical composition can pose significant risks, especially with prolonged exposure. Some studies have even suggested that certain flame retardants release toxic by-products when heated, which is troubling for both manufacturers and consumers. This has prompted me to look into more environmentally friendly alternatives5, particularly when dealing with halogenated flame retardants6, which are under scrutiny for their environmental impact.
Considerations for Product Design
Incorporating flame retardants into product design is a balancing act between safety and performance. I’ve often had to reevaluate our designs or choose different materials altogether due to their impact on mechanical properties. Utilizing tools like CAD software has become invaluable in simulating these changes, allowing me to visualize the effects before moving to physical prototyping. Staying informed about innovative materials7 has also helped me find solutions that meet both performance and safety standards.
Flame retardants increase polymer tensile strength.False
Flame retardants decrease tensile strength by altering polymer chains.
Halogenated flame retardants pose environmental risks.True
These retardants may release toxic by-products, impacting the environment.
What Are the Key Industry Standards for Flame Retardancy in Plastics?
As a designer, knowing the flame retardancy standards for plastics is like having a secret recipe for safety and innovation. Let’s uncover the key benchmarks that keep our designs fire-safe and compliant.
Key standards for flame retardancy in plastics include UL 94, ASTM E84, and ISO 4589-2, which define testing methods and safety criteria for ensuring materials meet fire safety requirements.
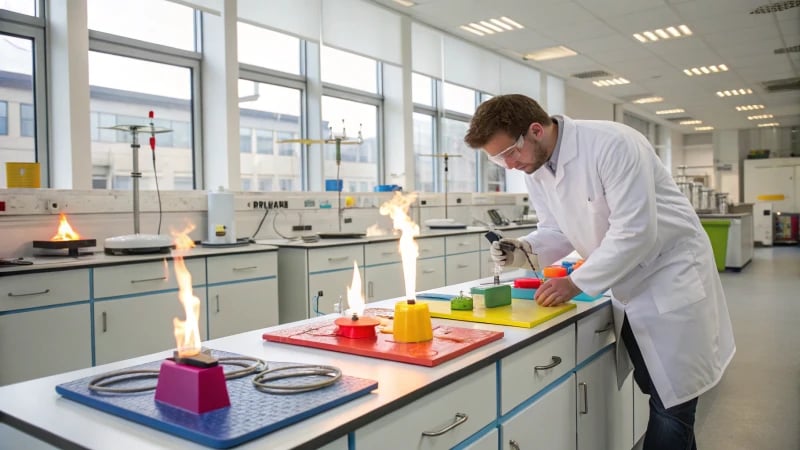
Key Flame Retardancy Standards
Imagine this: I’ve just designed a sleek new casing for an electronic gadget. It looks amazing, but the real test is whether it meets those crucial safety standards. That’s where understanding flame retardancy comes into play.
-
UL 94: You know, the first time I encountered UL 94, I felt like I was cracking a secret code. It’s widely recognized across North America and helps us determine how quickly a material stops burning once ignited. The UL 94 tests8 classify materials from V-0 (which is the gold standard) to V-2 based on how they burn and drip.
-
ASTM E84: Also known as the "Standard Test Method for Surface Burning Characteristics of Building Materials," this one hits close to home for me because I’ve worked on projects where building-related plastics were involved. It evaluates how flames spread and how much smoke is produced.
-
ISO 4589-2: This international standard measures the oxygen index required to sustain combustion. I remember a project where getting the right oxygen index9 was crucial in making sure our materials were as flame-retardant as possible.
Standard | Purpose | Classification |
---|---|---|
UL 94 | Evaluates material’s burning characteristics | V-0, V-1, V-2 |
ASTM E84 | Assesses flame spread and smoke development | Flame Spread Index |
ISO 4589-2 | Measures the minimum oxygen concentration needed | Oxygen Index Rating |
Applications and Considerations
In my world of consumer electronics, making sure every plastic component meets these standards is non-negotiable. For instance, I recently worked on a plastic casing10 that passed UL 94 V-0, significantly reducing fire risks.
Choosing the right plastic isn’t just about ticking boxes; it’s about ensuring safety while maintaining functionality. Every decision we make about materials has to balance these aspects delicately.
Moreover, global compliance is another layer to this puzzle. While UL 94 is the go-to in North America, international sales demand adherence to ISO standards. Navigating through these international standards11 can be complex, but it’s part of ensuring our designs reach a worldwide audience.
These standards aren’t just regulations to me; they’re integral to creating safer, more reliable products. Keeping up with them isn’t just about compliance—it’s about innovation and excellence in design.
UL 94 is a global standard for flame retardancy.False
UL 94 is primarily recognized in North America, not globally.
ISO 4589-2 measures oxygen needed for combustion.True
ISO 4589-2 evaluates the oxygen index required to sustain combustion.
How Can I Balance Cost and Performance in Flame Retardant Applications?
Navigating the world of flame retardants often feels like walking a tightrope between cost and performance.
To balance cost and performance in flame retardant applications, select suitable materials, choose optimal methods, and ensure regulatory compliance to meet safety and budget objectives efficiently.
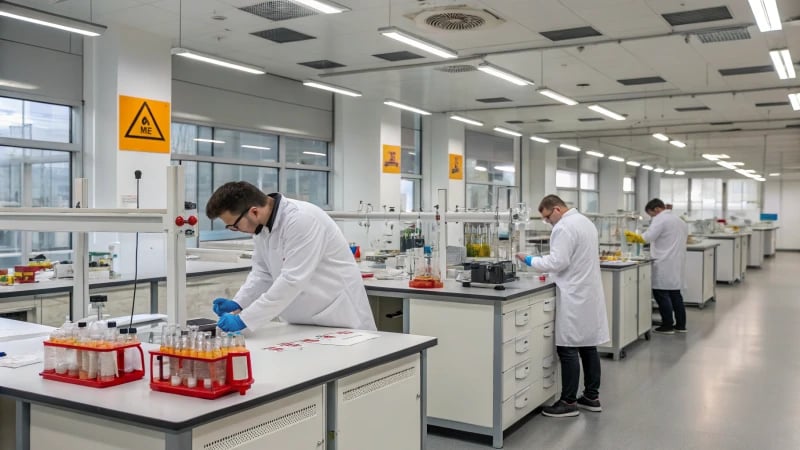
Material Selection: Weighing Options
Choosing the right material for flame retardancy is like picking the right tool for a job. Each type of flame retardant—halogenated or non-halogenated—brings its own set of benefits and drawbacks. I remember a time when I had to choose between these options for a project. Halogenated materials12 were efficient and cost-effective but raised environmental concerns that I couldn’t overlook. On the other hand, non-halogenated alternatives, although a bit pricier, offered peace of mind with their eco-friendliness.
Type | Advantages | Drawbacks |
---|---|---|
Halogenated | Cost-effective | Environmental concerns |
Non-Halogenated | Eco-friendly | Generally more costly |
Application Method: Efficient Integration
The way flame retardants are applied can significantly impact both cost and performance. I’ve had my fair share of trials with different methods. Mixing them as additives was a more economical route, but it often altered the product’s physical properties. The reactive method, where chemicals are bonded directly, provided greater durability at a higher price point.
- Additive: Mixed with base materials, which can be more cost-effective but may affect physical properties.
- Reactive: Chemically bonded, offering durability but often at a higher price.
Deciding which method to use can feel like solving a puzzle—each piece must fit perfectly to achieve the desired outcome.
Regulatory Compliance: Ensuring Safety Standards
Meeting regulatory compliance is an absolute must. I learned this lesson early on when a project failed due to non-compliance with local standards. Standards like UL 9413 dictate how we choose materials and application methods to avoid costly setbacks. It’s vital to keep these in mind throughout the design process.
Market Trends: Staying Ahead
Staying ahead of industry trends can be a game-changer. As sustainability becomes a priority, I’ve seen a shift towards innovative materials14 that meet both performance and cost criteria. Keeping an eye on these trends not only helps in making informed decisions but also gives me a competitive edge.
Balancing these elements might require conducting cost-benefit analyses or having collaborative discussions across departments. By aligning design, manufacturing, and compliance efforts, I can achieve successful flame retardant applications without compromising on quality or budget.
Halogenated flame retardants are more eco-friendly.False
Halogenated options have environmental concerns, unlike non-halogenated ones.
Additive application of flame retardants is cost-effective.True
Additive methods are generally more cost-effective but can affect properties.
Conclusion
Enhancing flame retardancy in injection molding involves using additives like halogenated, phosphorus-based, and metal hydroxides, balancing safety, performance, and environmental impact for effective product design.
-
Learn about different halogenated flame retardants and their applications, enhancing your understanding of their use in electronics. ↩
-
Explore the benefits of phosphorus-based flame retardants, focusing on their reduced smoke production. ↩
-
Discover guidelines for selecting suitable flame retardants for plastic applications. ↩
-
Learn how flame retardants affect material selection in manufacturing, influencing product design. ↩
-
Discover alternative flame retardants that reduce environmental impact while maintaining safety standards. ↩
-
Explore the environmental concerns associated with halogenated flame retardants. ↩
-
Find cutting-edge materials offering improved fire resistance and mechanical performance. ↩
-
Discover detailed testing procedures for UL 94 to understand how plastics are classified based on flammability. ↩
-
Learn why a higher oxygen index improves flame resistance and its significance in material selection. ↩
-
Explore why using V-0 rated plastics enhances safety in consumer electronics. ↩
-
Understand differences between various international standards to ensure global compliance. ↩
-
Explore the benefits and environmental impacts of halogenated flame retardants to make informed material choices. ↩
-
Learn about the UL 94 standard for understanding flammability ratings, crucial for regulatory compliance. ↩
-
Discover cutting-edge flame retardant materials that balance eco-friendliness with performance. ↩