I’ve always been fascinated by how injection molding brings designs to life.
The ejector system in injection molding uses pins or plates to gently and efficiently remove cooled parts from the mold, avoiding damage.
I remember the first time I watched an ejector system in action; it was like watching a magician at work. While it seems straightforward, the precision and efficiency of this system are critical. It doesn’t just affect how quickly parts are made but also their quality. Each component of the system plays a vital role in ensuring every product meets the highest standards, which I find truly impressive. Let’s explore these components and understand what makes this part of injection molding so indispensable.
Ejector pins remove parts from molds in injection molding.True
Ejector pins are used to push the finished part out of the mold.
The ejector system affects only the cooling phase of molding.False
The ejector system is used after the cooling phase to remove parts.
- 1. What Are the Key Components of an Ejector System?
- 2. How Do Ejector Pins Function in Mold Design?
- 3. Why is cooling crucial in the ejection process?
- 4. How Can Ejection System Failures Be Prevented?
- 5. What are the latest innovations in ejector system technology?
- 6. How Does Ejector System Efficiency Impact Production Costs?
- 7. Conclusion
What Are the Key Components of an Ejector System?
As someone who’s always been fascinated by how things work, I’ve found ejector systems to be an engineering marvel. These systems play a crucial role in various industries, making processes run smoothly. But what exactly are the components that make them tick?
An ejector system consists of a motive nozzle, suction chamber, mixing chamber, and diffuser, which together convert pressure energy into velocity energy to facilitate fluid movement.
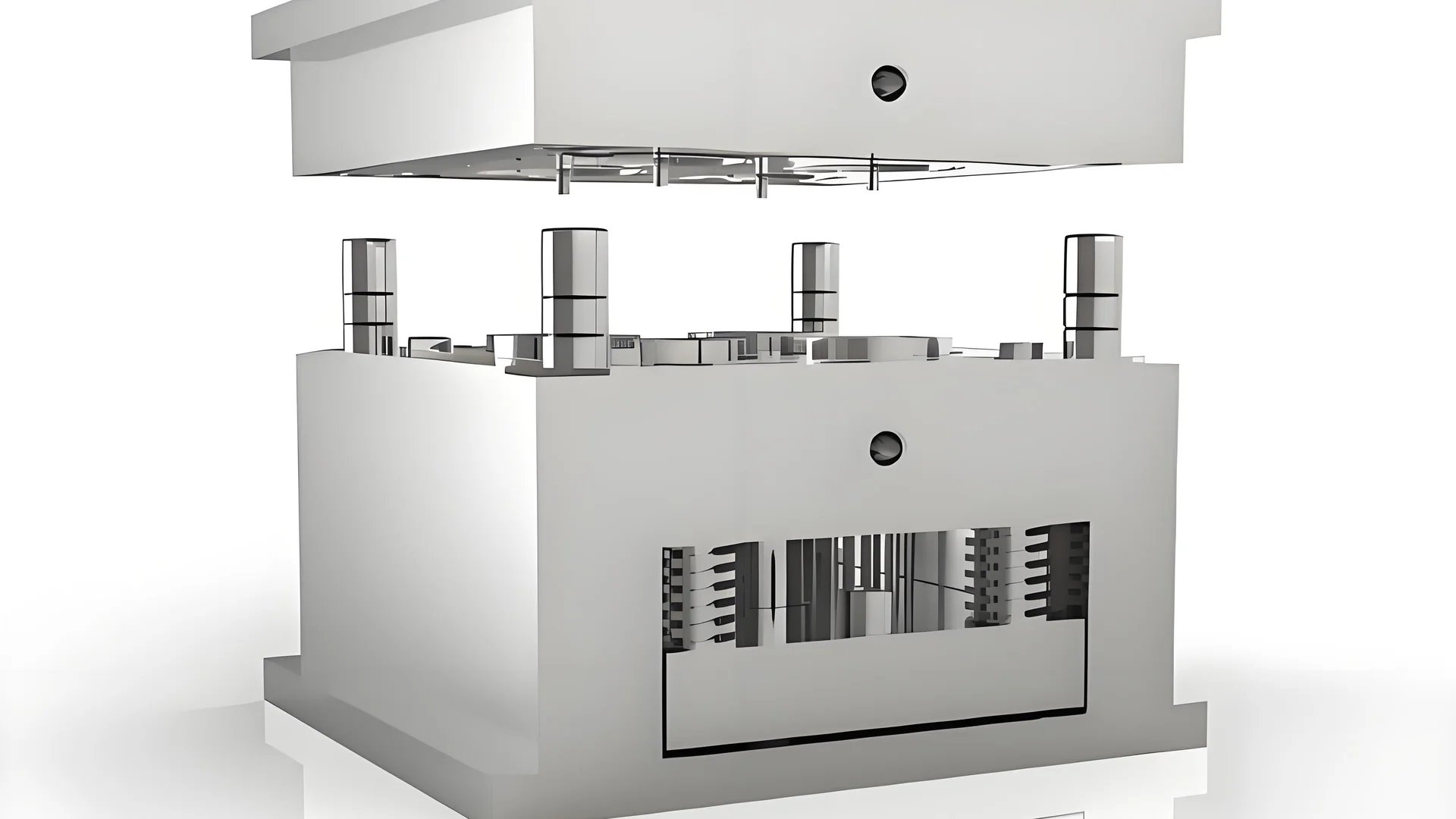
Motive Nozzle
If there’s one part of an ejector system1 that gets my heart racing, it’s the motive nozzle. Think of it as the powerhouse of the operation. It takes high-pressure motive fluid and transforms it into a high-speed jet, creating a low-pressure zone that draws in suction fluid. I remember being utterly fascinated the first time I saw this process in action.
- Material: Typically crafted from stainless steel for its resilience.
- Design: Tailored designs are often necessary to meet specific operational needs.
Suction Chamber
The suction chamber is like the welcoming host in this setup, ushering in the secondary fluid. Its role is vital as it channels this fluid into the system, aided by the low-pressure area created by the motive nozzle.
- Function: Facilitates the smooth entry of suction fluid.
- Considerations: Proper sizing is critical for performance—something I learned the hard way on a project once.
Mixing Chamber
Now, picture the mixing chamber as a bustling marketplace where fluids converge and mix. The equalizing of velocities and pressures happens here, and it’s critical for ensuring everything runs efficiently.
- Role: Ensures effective mixing of fluids.
- Impact: Directly influences the ejector’s overall efficiency.
Diffuser
Finally, we have the diffuser. It’s like the gentle slowdown at the end of a fast-paced ride, converting velocity back into pressure energy so that the ejector can discharge fluid effectively.
- Mechanism: Gradually increases in cross-sectional area.
- Outcome: Recovers previously lost pressure energy.
Material and Design Considerations
Choosing materials and design specifications for each component is crucial for optimizing performance2. Whether it’s stainless steel for corrosion resistance or custom designs to meet different industry standards, these choices significantly impact performance.
Component | Material | Function |
---|---|---|
Motive Nozzle | Stainless Steel | Converts pressure energy to velocity energy |
Suction Chamber | Various Metals | Channels secondary fluid |
Mixing Chamber | Alloy Steels | Mixes motive and suction fluids |
Diffuser | Composite | Recovers pressure energy |
By understanding these components, I’ve seen firsthand how industries can optimize their processes efficiently and sustainably. If you’re keen on enhancing your understanding further, I’d recommend diving into these performance considerations3.
The motive nozzle is made from stainless steel.True
Stainless steel is chosen for its durability and corrosion resistance.
The diffuser increases fluid velocity in an ejector system.False
The diffuser slows down the fluid, converting velocity back to pressure.
How Do Ejector Pins Function in Mold Design?
Imagine the thrill of watching your design come to life, only for it to get stuck in the mold! Ejector pins are the unsung heroes preventing this drama in mold design.
Ejector pins in mold design facilitate part removal post-cooling by applying precise force to prevent sticking, ensuring smooth ejection without product deformation.
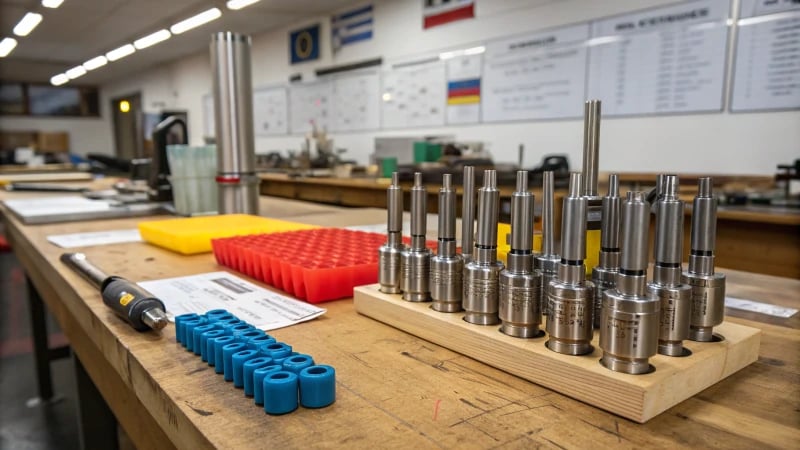
The Role of Ejector Pins in Mold Design
I remember my first major project in mold design, and how I underestimated the role of those tiny ejector pins. It was like trying to bake a cake and forgetting the baking powder—everything seemed fine until it wasn’t. Thankfully, I learned that these pins are crucial in injection molding4. They physically push the cooled part out of the mold, and their placement and type can make or break the final product’s integrity.
Types of Ejector Pins
Think of ejector pins like the different spatulas in your kitchen—each has its unique purpose. Here are some types:
Type | Description |
---|---|
Straight Pin | Standard pin used for general purposes. |
Step Pin | Used for parts requiring multiple diameters. |
Blade Pin | Best for thin-walled products that are difficult to eject. |
Choosing the right pin is like picking the right tool for your mold design5—it’s essential.
Best Practices for Using Ejector Pins
Over time, I’ve learned a few tricks to keep things running smoothly:
- Correct Placement: Place those pins correctly to avoid distorting your parts.
- Material Selection: Choosing materials like hardened steel can save a lot of headaches down the road.
- Maintenance: Regular maintenance can prevent wear and tear that might lead to defects.
These practices ensure the ejector system functions smoothly, contributing to a high-quality final product.
Troubleshooting Common Issues
Even with the best planning, things can go awry. I’ve had my share of parts sticking or showing marks and deformities:
- Part Sticking: Ensure proper lubrication and alignment can solve these issues.
- Marks or Deformation: Using a larger pin contact area can distribute pressure more evenly.
Addressing these common problems6 early on can boost your production efficiency and reduce waste. It’s all about learning from experience and making those tiny adjustments that have a big impact.
Ejector pins are essential in injection molding.True
Ejector pins physically push the part out of the mold, crucial for release.
Blade pins are used for thick-walled products.False
Blade pins are designed for thin-walled products that are difficult to eject.
Why is cooling crucial in the ejection process?
Have you ever wondered why cooling is such a big deal in injection molding?
Cooling ensures the molded part maintains its shape and size during ejection, preventing defects like warping or shrinkage. It’s all about managing temperature and cycle time effectively for consistent quality.
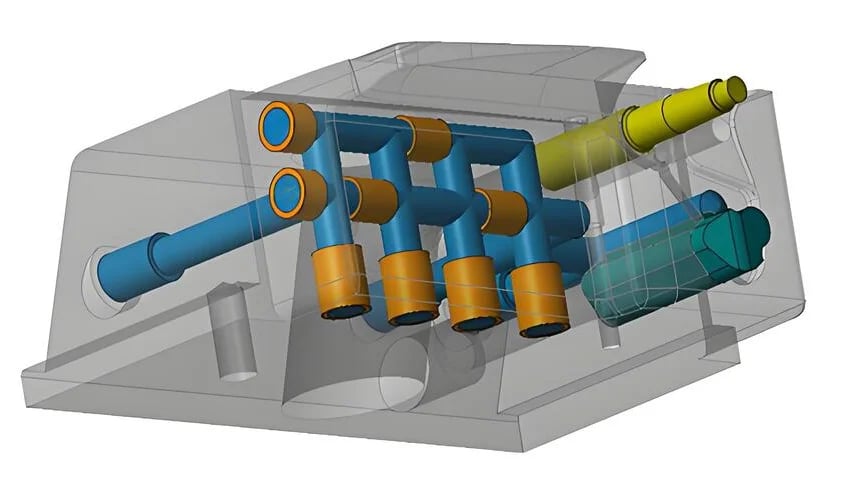
Understanding the Cooling Stage
In the injection molding process7, cooling isn’t just downtime; it’s a crucial step where your creation becomes real. This stage involves reducing the temperature of the molded part to make it firm enough for ejection without distortion.
Effects of Ineffective Cooling
Think of a time when you rushed to ice a cake before it cooled properly. It ended in a gooey mess, right? That’s what happens when cooling goes wrong in molding. Parts can warp or shrink because temperatures aren’t even across the mold. It’s vital to have uniform cooling to keep everything just as you envisioned.
Defect Type | Cause | Solution |
---|---|---|
Warping | Uneven cooling | Optimize cooling channels |
Shrinkage | Excessive temperature drop | Adjust cycle time |
Cooling Systems in Use
Remember those childhood water slides? Traditional water-based cooling systems are much like that—tried and true, but sometimes they just don’t hit all the right spots in a complex mold. Then there’s conformal cooling, the high-tech upgrade with 3D-printed channels for perfect control. It’s like switching from a garden hose to a sprinkler system.
- Water-based Cooling:
- Pros: Cost-effective and widely used.
- Cons: May not provide uniform cooling in complex molds.
- Conformal Cooling:
- Pros: Enhanced temperature control and reduced cycle time.
- Cons: Higher initial cost and complexity.
Innovations in Cooling Technology
Ever wish you had superpowers like seeing through walls? Well, some of today’s cooling technologies8 are giving designers that kind of edge. With sensors tracking real-time temperatures, it’s like having X-ray vision for your molds, ensuring every nook and cranny is perfectly chilled.
Implications for Mold Designers
For mold designers like me, understanding cooling’s role is like having a secret weapon in your toolkit. By embracing advanced techniques, we’re not just improving quality—we’re cutting costs too. Learning about these strategies helps us tailor our approaches to fit the needs of each project perfectly, ensuring we stay ahead in this fast-paced field.
Cooling prevents warping in molded parts.True
Effective cooling ensures uniform temperature, preventing warping.
Conformal cooling is less effective than water-based cooling.False
Conformal cooling offers better temperature control than traditional methods.
How Can Ejection System Failures Be Prevented?
Every time an ejection system fails, I’m reminded of the chaos it can unleash in a production line. But with the right strategies, these disruptions can be avoided.
Prevent ejection system failures with regular maintenance, proper alignment, high-quality materials, predictive maintenance schedules, and comprehensive operator training.
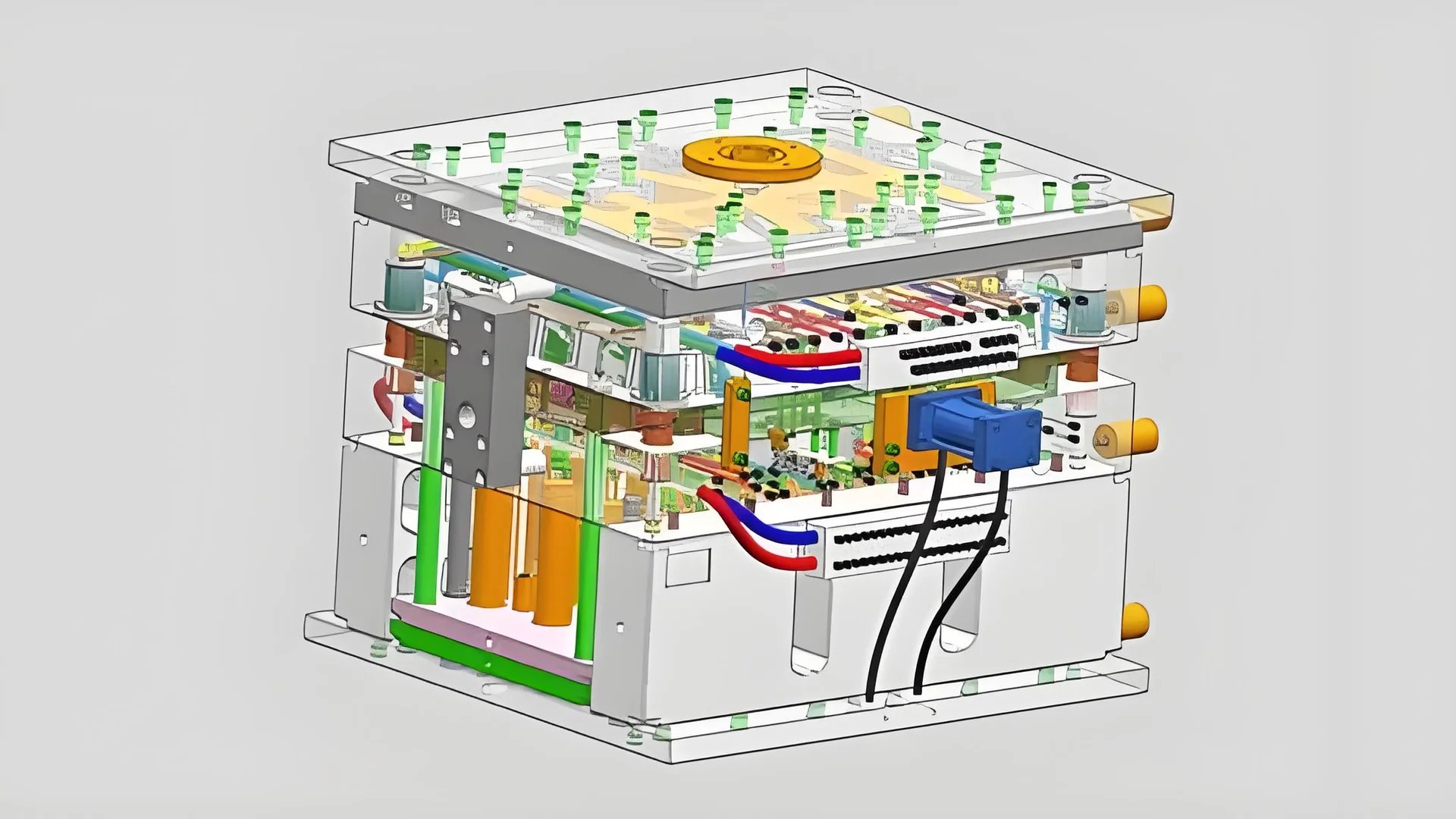
Understanding the Root Causes
Before I could effectively prevent ejection system failures, I had to dive deep into understanding why they occur in the first place. Common causes include misalignment issues9, material wear, and inadequate maintenance practices. Addressing these areas forms the basis for effective preventive measures.
Regular Maintenance and Inspection
Imagine coming into work every day knowing your production line is in tip-top shape. That peace of mind comes from a rigorous maintenance schedule. Regular inspections can catch signs of wear and tear before they lead to bigger problems. Consider creating a checklist for operators to follow daily:
Component | Check Frequency | Action |
---|---|---|
Pins | Weekly | Inspect for wear |
Plates | Monthly | Check alignment |
Springs | Bi-weekly | Test tension |
Material Selection and Quality Control
I remember the first time I saw a component fail because it was made from subpar materials. It was a costly lesson in the importance of using high-quality alloys that can handle stress without cracking under pressure. Conducting thorough quality checks10 on incoming materials prevents premature failures and extends equipment life.
Operator Training and Awareness
Training is an ongoing commitment. Proper training is critical as operators need to be aware of the signs of potential failure and understand the importance of maintaining system integrity. Regular workshops ensure they understand the warning signs of potential issues and appreciate the importance of maintaining system integrity.
Implementing Predictive Maintenance Technologies
I’ve embraced technology to stay ahead of the curve. Utilizing advanced technologies, such as predictive maintenance11 tools, can further safeguard against failures. These systems analyze operational data to predict when components might fail, allowing for proactive repairs or replacements.
Aligning Components Correctly
Proper alignment during installation can’t be stressed enough. Ensuring proper alignment minimizes stress on ejection systems, reducing failure chances. Utilizing precision alignment tools during setup has become my go-to for ensuring long-lasting operational efficiency.
By weaving these strategies into my workflow, I’ve not only enhanced the reliability of production lines but also minimized unexpected ejection system failures. Combining traditional methods with cutting-edge technology offers a robust defense against downtime risks.
Regular maintenance reduces ejection system failure risk.True
Consistent checks and timely component replacement minimize breakdown chances.
High-grade metals increase ejection system reliability.True
Quality materials withstand stress better, extending equipment life.
What are the latest innovations in ejector system technology?
Have you ever wondered how ejector systems are evolving to make our lives easier and industries more efficient?
Recent innovations in ejector systems feature 3D-printed designs, improved computational models for efficiency, and IoT integration for real-time monitoring, enhancing performance, reducing costs, and expanding application versatility.
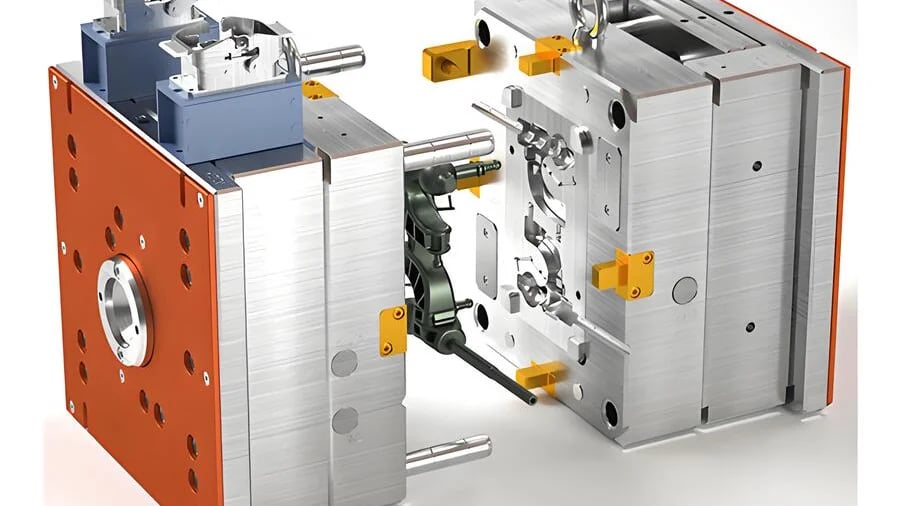
3D Printing Ejector Systems
I remember the first time I saw a 3D printer in action. It was like watching magic unfold. Now, this magic extends to ejector systems, allowing us to create customized ejector systems12 tailored precisely to our needs. The precision and intricacy achievable with 3D printing enable designs that were once confined to our imaginations, significantly improving fluid dynamics and system performance. Imagine working with ejector components that are not only lighter but also more energy-efficient—this technology is transforming what’s possible.
Advanced Computational Modeling
Advanced computational modeling is another game-changer. It’s like having a crystal ball for ejector systems, allowing us to simulate and perfect designs before they’re even built. This predictive capability means we can anticipate potential failures and nip them in the bud, drastically cutting down on downtime and maintenance costs. I’ve seen how this can transform production lines—keeping everything running smoothly as a well-oiled machine is no longer just a dream.
IoT Integration
When I first heard about IoT, I thought it was just about connecting gadgets at home. But IoT’s reach into industrial applications is profound. Integrating IoT into ejector systems provides real-time monitoring and control13, offering insights that optimize performance like never before. It’s like having an extra set of eyes that ensure everything operates at peak efficiency while alerting us to any anomalies before they become issues.
Application Versatility
The versatility of modern ejector systems has expanded incredibly. From refrigeration to desalination, and even chemical processing, these systems are now more adaptable than ever. The introduction of multi-stage ejectors14 allows them to perform efficiently under various pressures and temperatures, opening up new avenues across industries.
Innovation | Benefits |
---|---|
3D Printing | Customization and improved fluid dynamics |
Computational Modeling | Predictive maintenance and reduced costs |
IoT Integration | Real-time monitoring and efficiency optimization |
Multi-stage Ejectors | Enhanced application versatility |
These technological advancements aren’t just concepts; they have tangible effects on how professionals like us approach product and mold design. By staying updated with these trends, we can leverage these innovations to significantly enhance the effectiveness and sustainability of our projects.
3D printing allows lighter ejector components.True
3D-printed materials can produce lighter components, improving efficiency.
IoT integration reduces system versatility.False
IoT enhances monitoring and performance, not reducing versatility.
How Does Ejector System Efficiency Impact Production Costs?
Ever wondered how a small tweak in your ejector system can slash production costs?
Ejector system efficiency impacts production costs by influencing energy use, cycle times, and maintenance. Efficient systems enhance productivity, cut downtimes, and lead to savings.
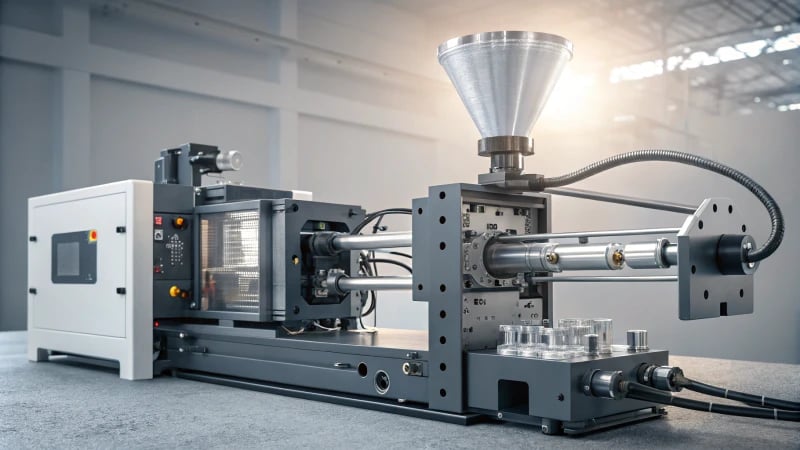
The Role of Ejector Systems in Manufacturing
I’ve spent countless hours in the bustling environment of manufacturing floors, and one thing I’ve learned is the critical role ejector systems play. They’re like the unsung heroes of injection molding, ensuring that products pop out of molds smoothly, without a hitch. Imagine trying to bake a cake and having it stubbornly stick to the pan—frustrating, right? In manufacturing, this kind of delay can add up to significant losses.
Ejector systems are crucial in various manufacturing processes, including injection molding. They help remove products from molds efficiently, minimizing defects and downtime. The efficiency of these systems affects not just production speed15 but also the quality of the final product.
Energy Consumption and Cost Implications
When I first started optimizing ejector systems, I was surprised at how much energy they consumed. Efficient systems are like those smart thermostats in homes—they regulate energy use without you having to think about it. By tweaking pressure and airflow, these systems use less power, translating into noticeable cost savings. Seeing the energy bills drop is always a satisfying moment.
Efficient ejector systems use less energy by optimizing pressure and airflow. This reduction in energy usage translates to lower operational costs. Comparing the energy requirements of different systems can highlight potential savings.
System Type | Energy Usage (kWh) | Cost Savings ($/yr) |
---|---|---|
Traditional | 10,000 | 0 |
Efficient | 7,000 | 3,000 |
Reducing Cycle Times
I’ve always been amazed by how efficiency improvements can shave precious seconds off cycle times. It’s like watching a fast-paced cooking show where every second counts. More units produced in less time means higher output without needing extra hands on deck.
By improving ejector system efficiency, manufacturers can significantly reduce cycle times. Shorter cycles mean more units produced within the same timeframe, increasing output without extra labor costs.
Maintenance and Operational Efficiency
There’s nothing more disruptive than unexpected maintenance halts. Efficient systems are built to last, reducing wear and tear. This means fewer headaches dealing with downtime and maintenance schedules that seem to pop up at the most inconvenient times. Investing in top-notch ejector systems is a decision that pays dividends in operational peace of mind.
Efficient systems require less maintenance due to reduced wear and tear. This lowers maintenance costs and minimizes production halts. Investing in high-quality ejector systems can lead to long-term operational savings16.
Impact on Product Quality
The precision of a well-functioning ejector system is akin to a maestro leading an orchestra; everything falls perfectly into place. With fewer defects and reduced waste, I’ve seen firsthand how consistent quality boosts overall cost-effectiveness.
The precision and reliability of an efficient ejector system ensure consistent product quality. Fewer defects lead to reduced waste and rework, directly affecting cost-effectiveness. Understanding these quality implications can aid decision-making in design optimizations.
Efficient ejector systems reduce energy costs by 30%.True
Efficient systems use 7,000 kWh versus 10,000 kWh, saving $3,000 annually.
Traditional ejector systems require less maintenance.False
Efficient systems have reduced wear and tear, leading to lower maintenance needs.
Conclusion
The ejector system in injection molding efficiently removes finished parts from molds, ensuring quality and precision through components like motive nozzles, suction chambers, and advanced technologies.
-
Discover how a motive nozzle works within an ejector system and why it’s crucial for efficiency. ↩
-
Learn about material choices for ejector components to optimize performance and durability. ↩
-
Learn about material choices for ejector components to optimize performance and durability. ↩
-
Learn about injection molding’s core processes to understand how ejector pins fit into the overall system. ↩
-
Discover best practices in mold design, including the strategic placement of ejector pins. ↩
-
Identify common issues with ejector pins and solutions to enhance production quality. ↩
-
Understand the role of cooling in achieving high-quality molded parts. ↩
-
Explore cutting-edge technologies improving cooling processes in mold design. ↩
-
Misalignment is a common cause of failures; understanding how to fix it can enhance system reliability. ↩
-
Ensures materials meet standards, preventing premature equipment failure and ensuring durability. ↩
-
These tools help foresee potential failures, allowing proactive maintenance and reducing downtime. ↩
-
Learn how 3D printing is revolutionizing ejector systems with custom designs for specific applications. ↩
-
Discover how IoT integration enhances real-time monitoring and control of ejector systems. ↩
-
Understand how multi-stage ejectors enhance performance across various operational conditions. ↩
-
Explore how improved ejector system efficiency can lead to faster production speeds, enhancing overall manufacturing throughput and cost-effectiveness. ↩
-
Discover how efficient ejector systems reduce maintenance needs, leading to significant operational savings over time. ↩