Do you ever think about how a simple plastic piece changes into a shiny, strong object?
The best ways to treat plastic surfaces are in-mold decoration, outside membrane decoration, spraying and NCVM non-conductive vacuum plating. Each method brings its own special advantages. These benefits cover looks, long-lasting quality and usefulness.
I remember the first time I held a beautifully crafted plastic gadget. It felt almost magical, like a piece of art. I realized then how surface treatments give life to plastic. Intricate designs from in-mold decoration or the shiny look of NCVM plating depend on your goals. Maybe you want strong products. Maybe you want products that look amazing. Knowing these techniques helps in choosing the right one for your project. Let’s explore each method and discover how they really lift your plastic products.
IMD involves injecting resin into a mold.True
In-Mold Decoration Technology uses resin injection to form products.
Screen printing is a type of laser engraving.False
Screen printing and laser engraving are distinct surface treatment methods.
How Does In-Mold Decoration Technology Work?
Have you ever thought about how those detailed patterns on your car dashboard or phone cover appear?
In-Mold Decoration uses a pre-printed film put inside a mold. Resin goes into the mold and merges with the film. This fusion creates a single, strong, decorated product. The process results in detailed designs and finishes that last a long time.
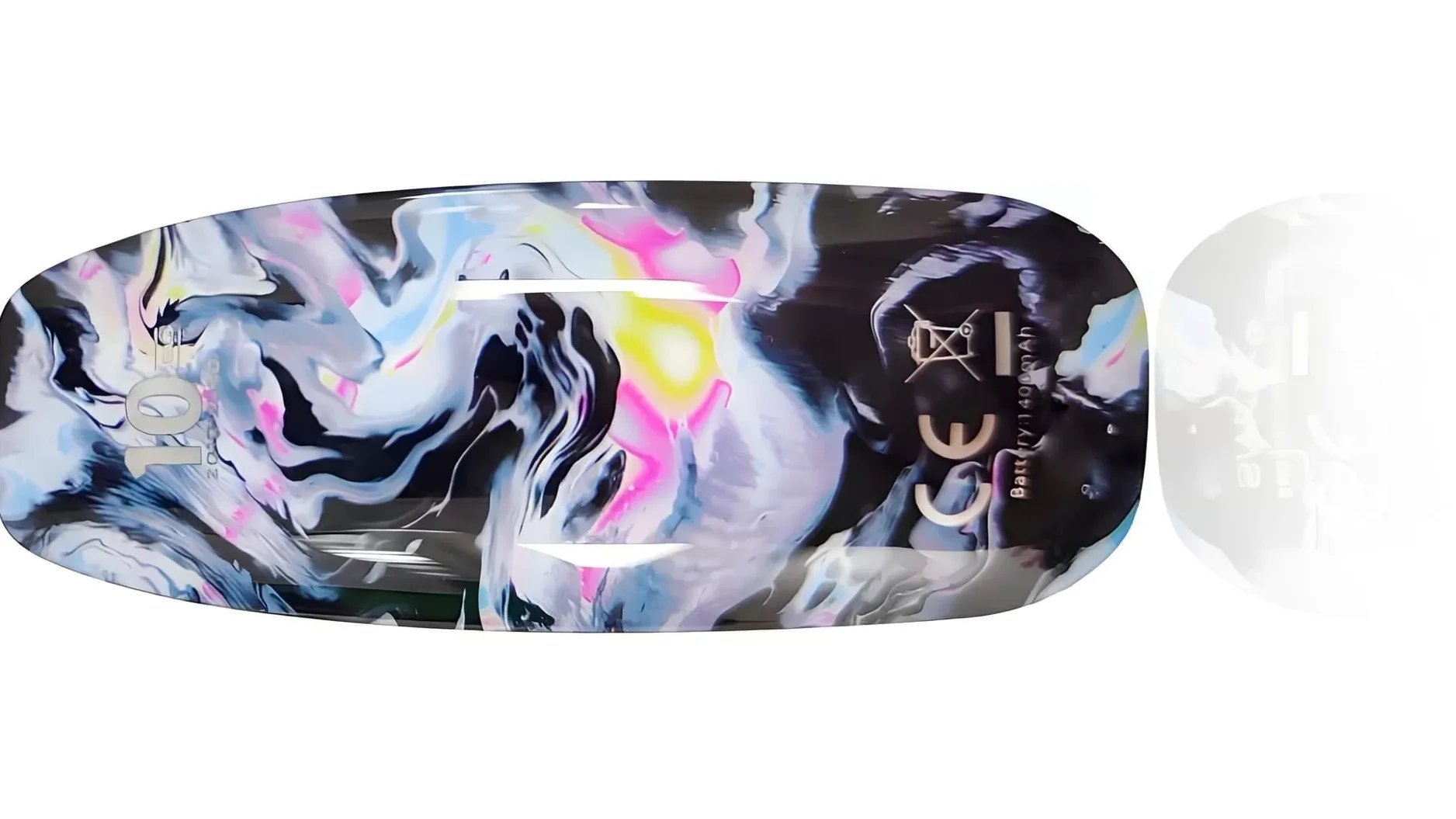
The Mechanics of In-Mold Decoration
In-Mold Decoration (IMD) combines art and engineering. It begins with a pre-printed film showing your chosen design. This film sits carefully in a metal mold, much like placing a picture into a frame.
During the molding process, resin is injected into the mold under high pressure and temperature. As the resin fills the mold, it fuses with the decorative film, creating a unified piece. Think of it like wrapping a book in a protective cover, creating a very strong bond. This combination doesn’t only look beautiful; it also stays tough against everyday damage.
Benefits of IMD Over Traditional Methods
IMD often surprises people because it performs better than older methods like Screen Printing1 or Spraying2. Designs used to fade and chip earlier. IMD puts the decoration inside the product, keeping colors bright and patterns sharp.
Moreover, IMD offers complex textures and colors similar to having an artist’s palette—something hard for methods like Plastic Plating3. Plus, it reduces material waste by avoiding extra coating steps, which really helps efficiency and the planet.
Feature | In-Mold Decoration | Traditional Methods |
---|---|---|
Process Steps | Single-step | Multiple steps |
Durability | High | Moderate |
Design Complexity | High | Limited |
Applications and Industry Use
IMD appears in many industries, from cars to electronics. Imagine sitting in a car with sleek controls or holding a smartphone that looks great and feels strong. These items transform into experiences where form meets function through IMD.
In cars, IMD creates dashboard panels that look stylish and work well with controls and screens. This technology supports the demand for 3D Surface Decoration4 like Outside Membrane Decoration5, offering both visual and tactile enhancements.
Don’t overlook consumer electronics. A need exists for stylish and tough devices. Here, IMD leads by allowing quick design changes to match trends. It’s not only about lasting products but also about making them look amazing. IMD makes production simpler while turning the final product into art.
IMD combines film and resin in a single molding process.True
IMD integrates printed film and resin into one piece during molding.
OMD is a 2D decoration technology for plastics.False
OMD is a 3D decoration technology, not limited to 2D surfaces.
What Is the Role of NCVM in Plastic Surface Treatment?
Ever thought about how your stylish devices stay shiny and still work well? That’s because of NCVM, the hidden champion.
NCVM or Non-Conductive Vacuum Metallization, uses a special method to coat plastics with thin layers of metal and insulating materials. This gives a shiny, metallic appearance. Wireless signals still work properly. Electronics look good and still function well. The process is really important.
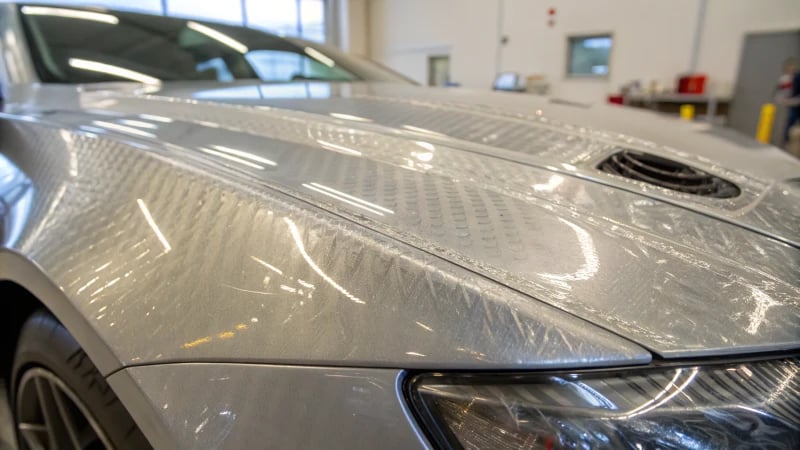
Understanding NCVM Technology
I recall the first time I touched a smartphone with a shiny metallic look. It looked so elegant, and I was curious about how it worked. This wonder comes from Non-Conductive Vacuum Metallization (NCVM). A process that covers plastic with thin metal and insulating layers. It’s like giving plastic a stylish upgrade without stopping wireless signals6. Such technology changes the game for fancy gadgets like smartphones and tablets. We can’t really live without them.
How NCVM Stands Out
Feature | Benefit |
---|---|
Aesthetic Versatility | Offers a metallic sheen while retaining non-conductivity for signal clarity |
Environmental Friendly | Avoids heavy metals, reducing environmental impact |
Durability | Provides excellent resistance to wear and tear |
In a project, I compared many coating techniques, and to be honest, NCVM was the best. Other methods, like electroplating, might affect signal strength, but NCVM lets gadgets sparkle in many ways.
Applications in Industry
Look at laptops and mobile phones. They have a smooth, metallic shine but still work perfectly. NCVM provides this beauty without harming the function. It’s the mysterious trick behind flawless designs in everyday electronics.
Comparisons with Other Techniques
- In-Mold Decoration (IMD): IMD feels like getting ready for a party. It adds decorative films during the forming process. However, NCVM is more like a final touch after molding.
- Plastic Plating: Similar but uses conductive materials, unlike NCVM.
Through my experience, when items need to be strong and uniform—especially those used frequently—NCVM wins over thermal or water transfer methods without doubt.
Looking Ahead: NCVM‘s Future Potential
As technology evolves7, our need for beautiful and useful products keeps growing too. NCVM will probably lead the way in providing solutions for our love of both looks and usefulness. Its wide-ranging abilities spread across different fields—from cars to healthcare—making it essential for future breakthroughs.
NCVM enhances plastic aesthetics without affecting functionality.True
NCVM provides a metallic look while maintaining wireless transmission.
IMD and OMD are the same plastic surface treatment methods.False
IMD involves molding with film; OMD integrates 3D decoration.
Why Choose Spraying for Plastic Products?
Spraying changes dull plastic into a masterpiece. This process mixes beauty with function. Here’s why this method is very important in plastic finishing.
Spraying gives a smooth and high-quality finish to plastic products. This finish probably makes the products last longer and look more appealing. Different colors and textures are possible. Products suit many needs with tailored solutions. Various applications benefit from this flexibility.
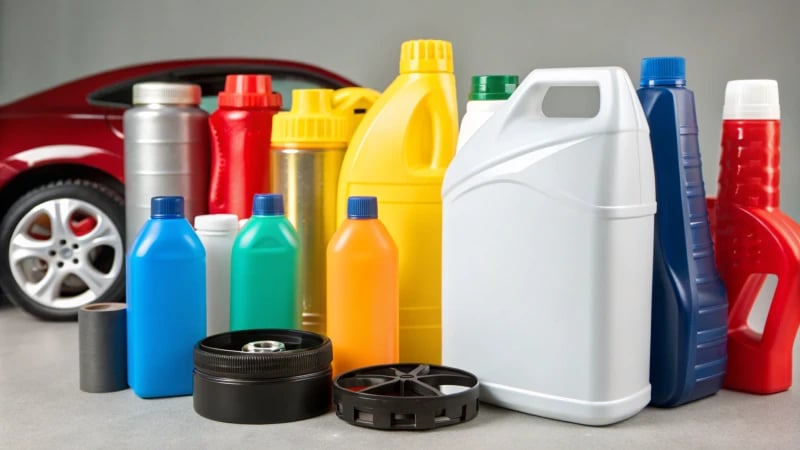
Benefits of Spraying Over Other Techniques
I remember watching a pro sprayer in action for the first time. It was amazing to see the paint smoothly cover the surface with accuracy and uniformity. Painting with a brush often left marks and uneven spots in my home projects. Spraying always left everything looking perfect. Its ability to coat evenly is a major advantage, minimizing flaws.
Speed is another plus. Spraying feels like driving fast on a highway, while screen printing8 seems like getting stuck in traffic. In busy production settings, this quickness is very valuable.
Method | Finish Quality | Speed | Cost |
---|---|---|---|
Spraying | High | Fast | Medium |
Screen Printing | Moderate | Slow | Low |
Brush-on Painting | Variable | Slow | Low |
Personalization Possibilities
I always liked the idea of adding a personal touch – be it a custom phone cover or a special car color. Spraying provides a wide range of choices. It offers shiny metallic finishes or rich, flat surfaces. Options are truly endless.
This method lets you mix different textures and colors at once, enabling designers like me to fully explore our creativity and precisely meet brand styles through techniques such as NCVM technology9.
Environmental Aspects
I care about our planet. Traditional spraying uses chemicals known as volatile organic compounds10, but new developments like water-based paints bring change. Spraying may be better for the environment than plastic plating when using green materials. It often results in less waste.
Strength and Protection
Spraying really impressed me with its ability to protect plastic surfaces. It’s like a shield defending against sunlight and moisture—perfect for outdoor items, especially car parts where durability is key.
In summary, while there are many methods to finish plastic products, spraying stands out for its speed, flexibility, and ability to protect. Its capability to provide high-quality, long-lasting, and attractive finishes makes it my favorite choice in many industries.
Spraying provides superior adhesion on plastic surfaces.True
Spraying ensures even paint distribution, enhancing adhesion on plastics.
Laser engraving is a chemical process for marking plastics.False
Laser engraving uses high energy lasers, not chemicals, for marking.
How do you choose the best surface treatment method for your project?
Ever felt confused by so many choices for surface treatments for your project? Me too! It’s very important to choose the right one so that everything turns out just right. Everything must turn out perfectly.
I look at many things when picking the best way to treat a surface. The type of material matters a lot. The finish I want is also important. I really think about environmental issues. The budget is also a key factor. Different methods offer unique advantages. Spraying, vacuum coating and laser engraving suit different needs.
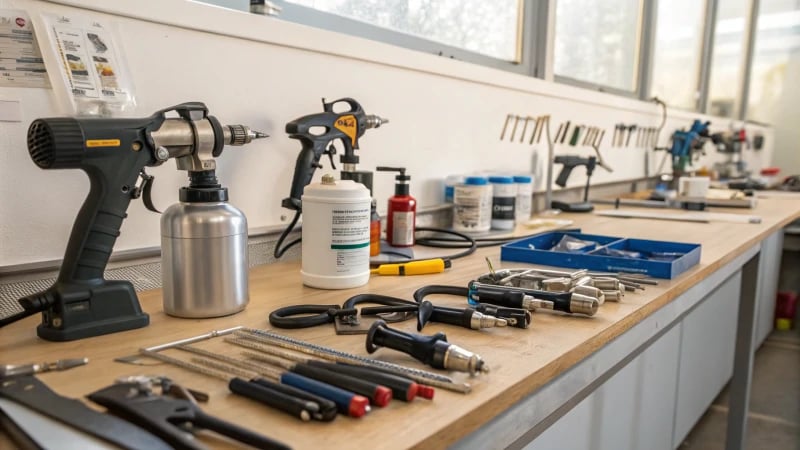
Evaluating Material Compatibility
The material is my first focus in any project. Each material reacts in a special way to treatments. Understanding these differences is very important. Once, I used plastic and NCVM plating11 was amazing. It added a shiny look but did not block wireless signals. Another time, I wanted a smooth surface on acrylics and flame polishing was the best choice.
Assessing Desired Finish and Aesthetics
Aesthetic needs are crucial. They hugely impact any project. An intricate design came to mind once. Only In-Mold Decoration Technology (IMD)12 could create its lively patterns during molding. For simpler looks, a quick spray or screen print worked well enough.
Method | Finish Type | Suitable Materials |
---|---|---|
Laser Engraving | Textured or Patterned Markings | Metals, Plastics |
Water Transfer | Colorful Patterns | Plastics |
Electrophoresis | Metallic Coatings | Metals |
Environmental Considerations
I think more about how my choices affect nature now. Vacuum coating attracts me because it harms the earth less than older methods such as plastic plating do. It really matters.
Budget Constraints and Efficiency
Budget limits are always present. Methods like screen printing13 save costs for big orders. However, sometimes NCVM is the pick due to its strength, even though it’s expensive. Balancing cost with benefits is the goal.
Functional Requirements
Functionality is crucial. Non-negotiable. A textured grip needs abrasive treatments. For sleek looks, polishing is the best. Different methods have unique advantages14. It all depends on what the final product needs.
By weighing these factors together, I stay informed about my project’s surface treatment choices.
IMD and OMD are identical technologies.False
IMD and OMD are distinct; OMD extends IMD with additional features.
Spraying can be used to apply patterns on plastic surfaces.True
Spraying uses tools to atomize paint, allowing pattern application.
Conclusion
Explore effective surface treatments for plastic products, including In-Mold Decoration, NCVM plating, and spraying, each offering unique benefits in aesthetics, durability, and functionality.
-
Explore how screen printing compares to IMD in terms of design flexibility and application. ↩
-
Understand the benefits of spraying techniques in industrial applications compared to IMD. ↩
-
Discover how plastic plating achieves metallic finishes and its limitations compared to IMD. ↩
-
Learn about 3D surface decoration methods that enhance visual and tactile features. ↩
-
Investigate how OMD expands upon IMD with added functionalities. ↩
-
Explore how NCVM ensures device functionality by not interfering with wireless signals. ↩
-
Discover the expanding applications of NCVM across different industries. ↩
-
Learn about the pad printing process to understand alternative methods and how they compare to spraying. ↩
-
Explore how NCVM technology enhances spraying with metallic finishes without interfering with electronic signals. ↩
-
Understand the impact of VOCs in spray painting and discover eco-friendly alternatives that reduce environmental harm. ↩
-
NCVM plating provides a metallic appearance without hindering wireless communication, making it perfect for electronic enclosures. ↩
-
IMD creates durable, intricate patterns directly into products, offering superior aesthetic appeal and longevity. ↩
-
Screen printing is cost-effective for large runs and allows vivid designs on various surfaces. ↩
-
Explore various methods to find their unique benefits, such as durability or environmental impact. ↩