In the bustling realm of manufacturing, every detail counts, especially when it comes to injection molds. Understanding how to care for them can make all the difference.
The most effective surface treatments for injection molds include polishing, sandblasting, electroplating, and PVD titanium plating. These methods enhance mold durability, improve product quality, and reduce maintenance costs by offering abrasion resistance, corrosion protection, and improved surface finish.
While these treatments provide immediate benefits, understanding the nuances of each can significantly impact your manufacturing process. Dive deeper into these techniques to discover how they can be tailored to meet specific production requirements.
Electroplating improves mold durability by increasing surface hardness.True
Electroplating adds a metal layer, enhancing abrasion and corrosion resistance.
How Does Polishing Improve Mold Performance?
Polishing is a crucial process in mold making, significantly enhancing both the lifespan and efficiency of molds.
Polishing improves mold performance by enhancing surface finish, reducing friction, and minimizing defects in molded products. This process involves the use of tools like oil stones and sandpaper to smooth out imperfections, leading to better product quality and increased mold longevity.
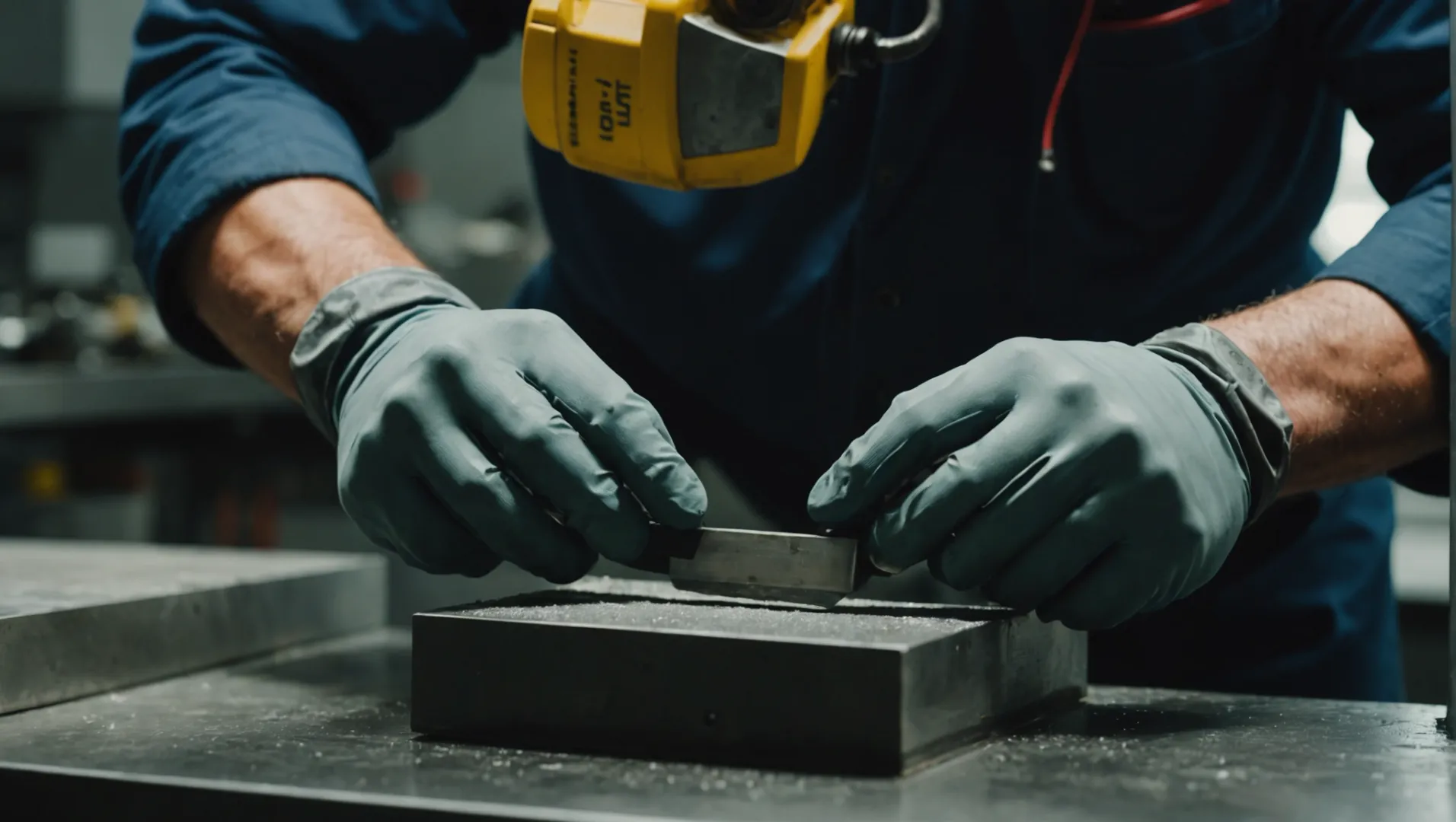
Understanding the Polishing Process
The primary goal of polishing is to achieve a flawless surface that enhances mold performance. The process involves using abrasive materials such as oil stones, sandpaper, and wool wheels to cut and plastically deform the mold surface. By smoothing out imperfections and rough areas, polishing significantly improves the surface finish, which is essential for producing high-quality molded parts.
Benefits of Polishing on Mold Performance
-
Enhanced Surface Finish: A well-polished mold ensures a smooth surface on the final product, which is crucial for components with aesthetic or functional requirements. For instance, polished molds are essential for producing optical lenses with high transparency and clarity.
-
Reduced Friction: Polishing reduces friction between the mold surface and the injected material, facilitating easier ejection of parts and reducing wear on the mold. This prolongs the mold’s service life and decreases maintenance needs.
-
Minimized Defects: By eliminating surface irregularities, polishing minimizes defects such as sink marks or flow lines in molded products. This is particularly vital for products where visual appearance is crucial.
-
Improved Product Quality: A polished mold leads to better-quality products with consistent dimensions and finishes, meeting both industry standards and customer expectations.
Comparing Polishing Standards
Polishing follows specific standards to ensure uniformity and quality. The SPI1 (Society of the Plastics Industry) standard is widely recognized for its detailed grading of surface finishes:
Grade | Grit Used | Surface Roughness (μm) | Typical Applications |
---|---|---|---|
A-1 | 6000 grit | 0.012-0.025 | High-end electronics |
A-2 | 3000 grit | 0.025-0.05 | Automotive interiors |
A-3 | 1200 grit | 0.05-0.10 | Plastic tableware |
Understanding these standards can help manufacturers choose the appropriate polishing level for their specific needs, ensuring optimal mold performance across various applications.
When to Use Polishing Over Other Treatments
While polishing2 offers distinct advantages, it’s essential to consider its application in context with other treatments like sandblasting or electroplating. For parts where a high degree of surface smoothness is not critical, alternatives may be more cost-effective. However, when aiming for maximum smoothness and appearance quality, polishing remains unmatched.
By evaluating these factors, manufacturers can make informed decisions about incorporating polishing into their production processes, ultimately leading to enhanced mold performance and superior product quality.
Polishing reduces friction in molds.True
Polishing smooths the mold surface, reducing friction and easing part ejection.
Polishing increases mold defects like sink marks.False
Polishing minimizes surface irregularities, reducing defects such as sink marks.
What Role Does Electroplating Play in Mold Durability?
Electroplating is a key player in extending the lifespan of molds used in manufacturing processes.
Electroplating enhances mold durability by depositing a metal layer on the mold surface, improving abrasion and corrosion resistance, and increasing surface hardness. Common metals used include chromium, nickel, and copper.
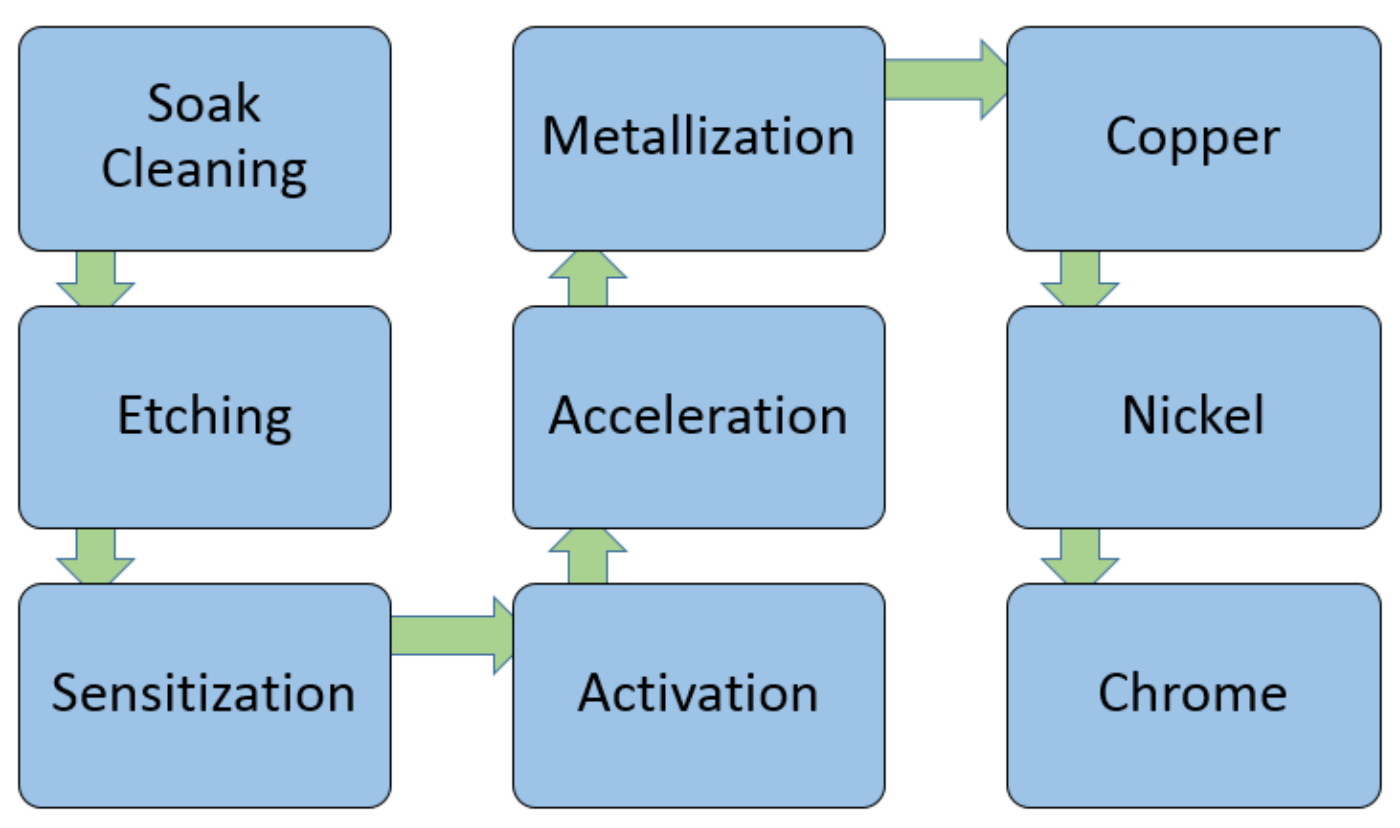
Understanding Electroplating in Mold Manufacturing
Electroplating involves depositing a layer of metal onto the surface of a mold through electrolysis. This process significantly enhances the durability of molds by providing a hard, wear-resistant surface that can withstand the rigorous demands of injection molding.
Common metals used in electroplating3 include:
- Chromium: Offers excellent hardness and corrosion resistance.
- Nickel: Provides a smooth finish with good wear resistance.
- Copper: Used for its excellent conductivity and ability to form a strong bond with other plating metals.
These metals create a protective barrier against wear and tear, reducing the frequency of maintenance required and enhancing the lifespan of the mold.
Benefits of Electroplating for Mold Durability
-
Abrasion Resistance: The additional metal layer helps resist scratches and wear from the constant friction during the injection molding process.
-
Corrosion Resistance: By forming a protective layer, electroplating prevents chemical reactions between the mold material and external elements, thus preventing rust and degradation.
-
Surface Hardness: Metals like chromium increase the surface hardness, making molds more robust against mechanical stress.
These benefits cumulatively contribute to longer-lasting molds that maintain their structural integrity over time.
Comparing Electroplating with Other Surface Treatments
While electroplating offers substantial benefits, it’s important to compare it with other treatments such as PVD titanium plating4, which also improves surface hardness but through physical vapor deposition technology.
Treatment | Method | Benefits |
---|---|---|
Electroplating | Electrolysis | Hardness, abrasion & corrosion resistance |
PVD Titanium Plating | Physical vapor deposition | Hard, wear-resistant, aesthetic finishes |
Polishing | Manual/mechanical abrasion | Smooth surface finish |
Sandblasting | Abrasive material projection | Surface roughness & adhesion improvement |
Choosing the Right Surface Treatment
Selecting the appropriate surface treatment involves considering factors like material compatibility, environmental conditions, and cost. For manufacturers focusing on enhancing mold durability with minimal downtime, electroplating is an effective option due to its comprehensive protection capabilities.
Understanding each treatment’s unique benefits can lead to more informed decisions that optimize both production efficiency and mold longevity. By choosing electroplating, you can ensure that your molds are equipped to handle high production volumes without compromising quality.
Electroplating enhances mold surface hardness.True
Electroplating increases surface hardness by depositing metals like chromium.
Copper is not used in electroplating for molds.False
Copper is used for its conductivity and bonding strength in electroplating.
Is Sandblasting Suitable for All Mold Types?
Sandblasting is a popular surface treatment in mold manufacturing, but is it universally applicable?
Sandblasting is not suitable for all mold types. While effective for cleaning and increasing surface roughness, it may damage delicate or intricate mold features and is best suited for robust molds requiring enhanced adhesion and texture.
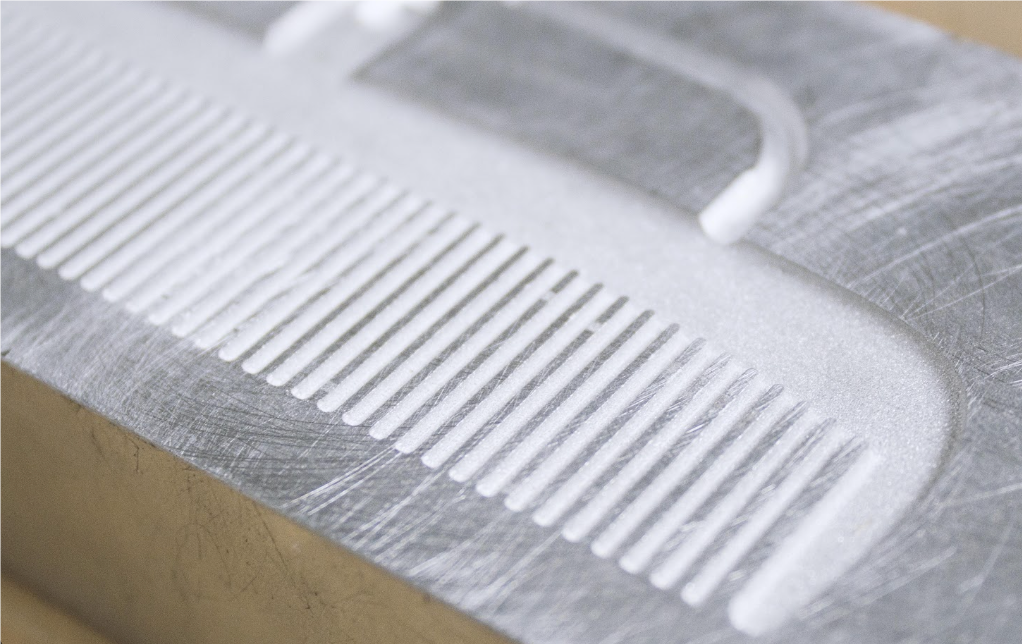
Understanding Sandblasting
Sandblasting involves the high-speed injection of abrasive materials like sand against a surface to remove dirt, oxidation layers, and defects. It’s known for increasing surface roughness, which enhances the adhesion of coatings, a critical requirement in various manufacturing processes.
Benefits of Sandblasting for Molds
One of the primary benefits of sandblasting is its ability to prepare the mold surface for subsequent treatments. By increasing surface roughness5, it allows coatings such as electroplating or PVD titanium to adhere more effectively, thus enhancing the durability and performance of the mold. This process also assists in creating specific textures that might be necessary for certain product aesthetics.
Potential Drawbacks
Despite its advantages, sandblasting is not universally applicable to all molds. The aggressive nature of sandblasting can lead to excessive wear or damage, particularly in molds with fine or intricate features. It may alter precise dimensions or create undesired surface textures, which could affect the final product quality.
Evaluating Mold Type Suitability
When considering sandblasting, it’s essential to evaluate the mold’s material and design. Robust molds made from durable metals like hardened steel can typically withstand sandblasting. However, molds with sensitive features or those made from softer materials may require gentler surface treatments.
Table: Mold Types and Suitability for Sandblasting
Mold Material | Suitability for Sandblasting | Notes |
---|---|---|
Hardened Steel | High | Ideal for roughening surfaces; enhances adhesion |
Aluminum | Medium | Use with caution; risk of surface damage |
Plastic | Low | Generally unsuitable; may cause deformation |
Intricate Designs | Low | Avoid; risk of feature damage |
Alternatives to Sandblasting
For molds unsuitable for sandblasting, alternatives like chemical etching6 or polishing might be more appropriate. These methods can achieve similar goals without compromising mold integrity.
In conclusion, while sandblasting is an effective tool in the arsenal of mold surface treatments, it’s crucial to consider the specific characteristics of each mold type before application.
Sandblasting enhances mold surface adhesion.True
Sandblasting increases surface roughness, improving coating adhesion.
Plastic molds are ideal for sandblasting.False
Plastic molds are unsuitable for sandblasting due to deformation risk.
How Do SPI and VDI Standards Impact Surface Treatment Choices?
Navigating the landscape of surface treatments for injection molds requires understanding industry standards like SPI and VDI.
SPI and VDI standards dictate the surface finish of injection molds, influencing choices in polishing and texturing techniques. These standards help ensure consistency and quality, impacting the aesthetic and functional properties of molded parts.
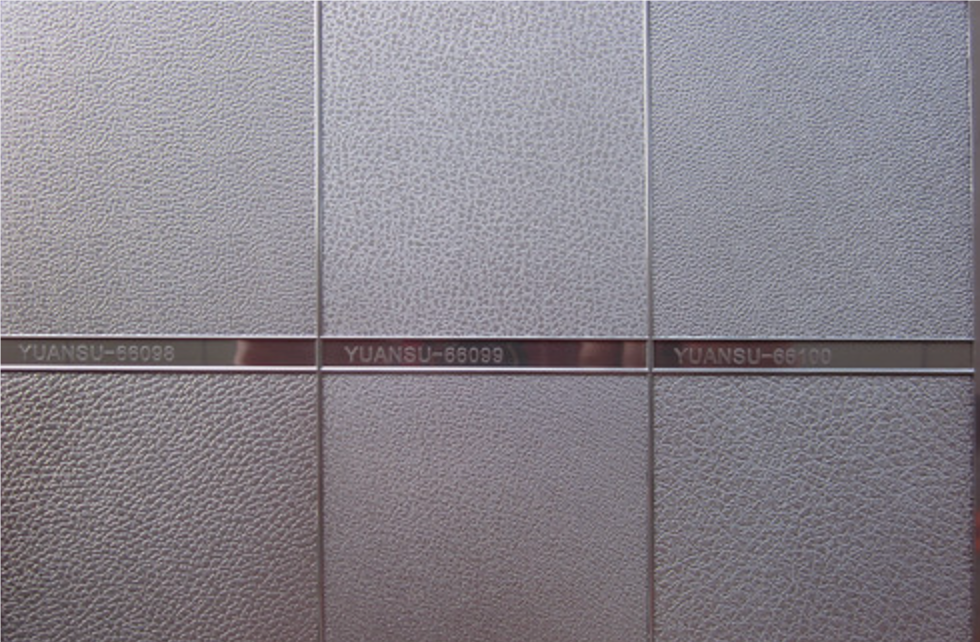
Understanding SPI and VDI Standards
The Society of the Plastics Industry (SPI) and the German Engineering Association (VDI) provide guidelines for surface finishes that are crucial in determining how molds are treated.
SPI Standards
The SPI standard classifies mold finishes into grades A, B, C, and D, with each grade offering specific roughness parameters. For example:
SPI Grade | Polishing Method | Surface Roughness (µm) |
---|---|---|
A-1 | 6000 grit diamond gesso | 0.012-0.025 |
A-2 | 3000 grit diamond plaster | 0.025-0.05 |
D-1 | Sandblasted with coarse glass beads | 0.80-1.00 |
These grades help manufacturers choose appropriate treatments based on desired finish quality. Injection mold polishing7 enhances finish for optical lenses or high-end electronics.
VDI Standards
VDI guidelines focus on texturing, providing a scale from VDI 12 to VDI 42, each with defined roughness.
VDI Level | Finish Method | Surface Roughness (µm) |
---|---|---|
VDI 12 | Oilstone low-polish | 0.40 |
VDI 18 | Sandblasted with coarse glass beads | 0.80 |
VDI 30 | #24 Oxide Blast | 3.15 |
Implications of Standards on Surface Treatment Choices
-
Polishing: The choice between different SPI grades depends on the final product’s aesthetic and functional requirements. Higher grades like A-1 offer mirror-like finishes ideal for products needing clarity or reflectivity, while lower grades are suitable for everyday items.
-
Texturing: VDI standards guide texturing processes such as chemical etching8. The decision to use a particular VDI level is influenced by how much friction or texture is needed.
-
Material Compatibility: Both standards account for material-specific behaviors, ensuring that surface treatments align with material properties to prevent degradation or unwanted interactions.
-
Cost Considerations: Higher precision and smoother finishes often involve increased costs. Manufacturers must weigh these against the product’s market value and intended use.
Practical Applications and Decision-Making
When choosing between SPI and VDI standards, manufacturers must consider:
- End-use requirements: Products requiring visual appeal or specific tactile qualities may demand higher-grade finishes.
- Production volume: Larger runs might benefit from finishes that increase mold longevity and reduce maintenance.
- Cost-benefit analysis: Balancing the expense of high-quality finishes against their functional advantages is critical.
Understanding these standards is essential for optimizing mold surface treatment9 strategies, ultimately influencing product quality and manufacturing efficiency.
SPI Grade A-1 offers a mirror-like finish.True
SPI Grade A-1 uses 6000 grit diamond gesso, resulting in a mirror-like finish.
VDI Level 30 results in the smoothest surface finish.False
VDI Level 30 is rougher, using #24 Oxide Blast, not the smoothest finish.
Conclusion
Enhancing mold performance through effective surface treatments is crucial for optimizing production. Evaluate options like polishing and electroplating to suit your needs, ensuring product quality and cost efficiency.
-
Learn about SPI standards to ensure consistent and high-quality surface finishes.: VDI 3400 standard is mainly a reference for surface roughness (focus on “ROUGH”). SPI Finish is mostly for mold polish (focus on “SMOOTH”). Although they are … ↩
-
Discover how polishing can improve product quality and mold longevity.: Polishing is responsible for achieving a surface finish on plastic. Click here to read all about the injection molding polishing types! ↩
-
Explore how electroplating enhances mold lifespan through abrasion resistance.: Artists often use electroplating to preserve natural elements prone to decay, such as leaves, and turn them into more durable works of art. ↩
-
Understand how PVD compares to electroplating for durability.: Physical Vapor Deposition (PVD) is an increasingly popular alternative to electroplating that also increases abrasion resistance and assists in part release. ↩
-
Learn how sandblasting effectively enhances surface adhesion.: Changes in blasting pressure resulted in the greatest changes in the surface roughness, the highest surface roughness values were achieved with … ↩
-
Discover how chemical etching offers an alternative to sandblasting.: Chemical etching is a method of engraving that uses a high-pressure high-temperature chemical spray to remove material to create a permanent etched image in … ↩
-
Learn how different polishing techniques meet SPI standards.: Texas Injection Molding uses these SPI mold polish standards to specify mold polish finishes for multiple applications, guides, and finishes. ↩
-
Discover the chemical etching methods aligned with VDI standards.: In recent years, mold makers achieve VDI 3400 textures by chemical etching after mold polishing. It could get uniform textures surface as the VDI 3400 standard. ↩
-
Explore strategies to enhance mold durability and product quality.: Plating (Chrome Plating, Electroless Nickel, Nickel Boron Nitride) · Physical Vapour Deposition … ↩