Ever felt like your injection molding process is stuck in a rut?
Optimize mold design, use suitable release agents, maintain precise temperature control, and conduct regular mold maintenance to effectively tackle challenges in injection molding product releases, preventing sticking and ensuring efficient production.
I remember my first major project in injection molding—nothing went as planned. Parts were sticking, and deadlines loomed. After many late nights, I realized the importance of precise temperature control and mold maintenance. These strategies, along with optimizing mold design and using the right release agents, transformed my process. There’s so much more to explore when it comes to enhancing your operations. From innovative techniques to subtle tweaks, each change can make a world of difference in achieving seamless product releases.
Optimizing mold design prevents product sticking.True
Proper mold design reduces defects, ensuring smooth product release.
Regular mold maintenance is unnecessary for efficient production.False
Consistent maintenance ensures molds function properly, preventing issues.
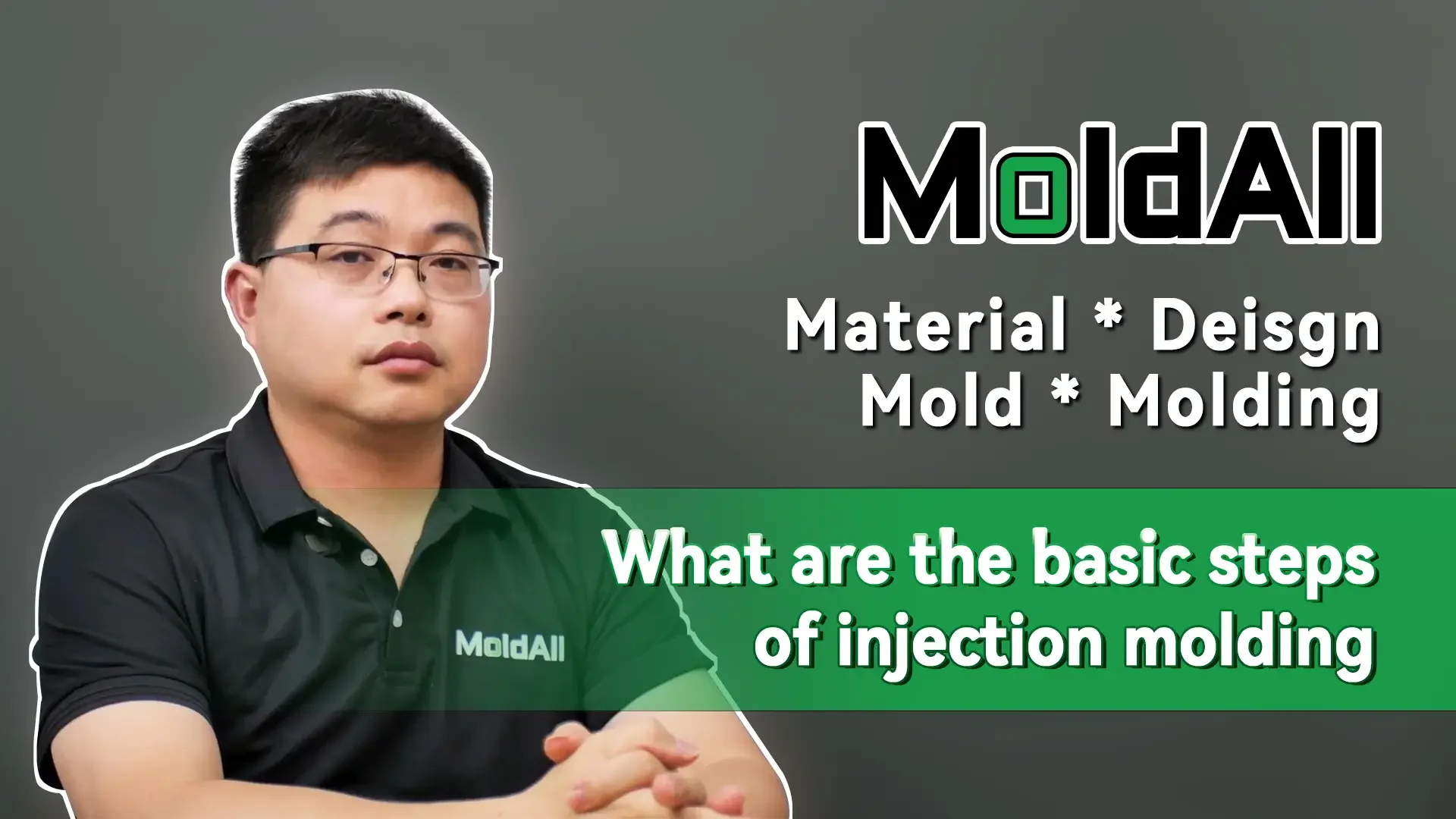
- 1. How Does Mold Design Affect Product Release?
- 2. What Role Do Release Agents Play in Injection Molding?
- 3. Why Is Temperature Control Crucial in Mold Release?
- 4. How does regular maintenance enhance mold performance?
- 5. What Innovative Techniques Are Emerging in Mold Release Technology?
- 6. Conclusion
How Does Mold Design Affect Product Release?
Ever wondered how a simple design tweak can transform a product’s journey from concept to reality?
Mold design impacts product release by enhancing production speed, quality, and cost efficiency, leading to smoother manufacturing, fewer defects, and optimized timelines.
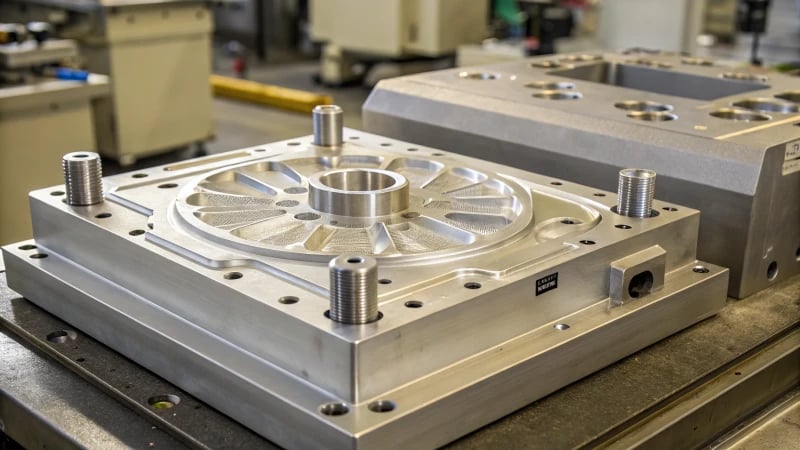
The Role of Mold Design in Manufacturing
Reflecting on my early days in mold design, I remember the thrill of witnessing how a tiny adjustment in the mold could lead to a significant improvement in production efficiency. Mold design is the backbone of injection molding1, shaping not only the product’s form but also its production pace. The choice of mold material, cavity design, and cooling systems all play pivotal roles.
Key Factors in Mold Design
- Cavity Design: I once worked on a project where precision was key, and getting the cavity design just right was like solving a complex puzzle.
- Material Selection: Picking the right material was crucial when we had to balance durability with heat resistance.
- Cooling System: On a tight deadline, optimizing the cooling system saved us precious minutes per cycle.
- Ventilation: I learned the hard way how poor ventilation could lead to costly defects.
Factor | Impact on Production |
---|---|
Cavity Design | Accuracy & Precision |
Material Selection | Durability & Resistance |
Cooling System | Efficiency & Speed |
Ventilation | Quality & Defect Reduction |
Impact on Production Timelines
There’s nothing quite like the satisfaction of seeing a product hit the market faster than expected. Efficient mold designs help achieve this by reducing production time through optimized features like cooling channels and ejection mechanisms, thus speeding up time-to-market2.
Challenges in Mold Design
But it’s not always smooth sailing. Poor designs can lead to increased defects, higher scrap rates, and unexpected delays. I remember a particularly challenging project where we had to anticipate issues like warping, which taught me invaluable lessons in foresight and preparation.
By understanding these factors, I’ve learned to create molds that not only meet aesthetic and functional requirements but also enhance manufacturing efficiency.
For further insights into how mold design impacts production processes, consider exploring advanced techniques3 in mold making.
Cavity design impacts product precision.True
Cavity design ensures dimensional accuracy, affecting the product's precision.
Ventilation has no effect on product quality.False
Ventilation prevents defects by allowing trapped air to escape, enhancing quality.
What Role Do Release Agents Play in Injection Molding?
Ever wondered how a tiny detail like release agents can make or break your injection molding process?
Release agents in injection molding prevent parts from sticking to molds, facilitate ejection, reduce defects, and extend mold lifespan.
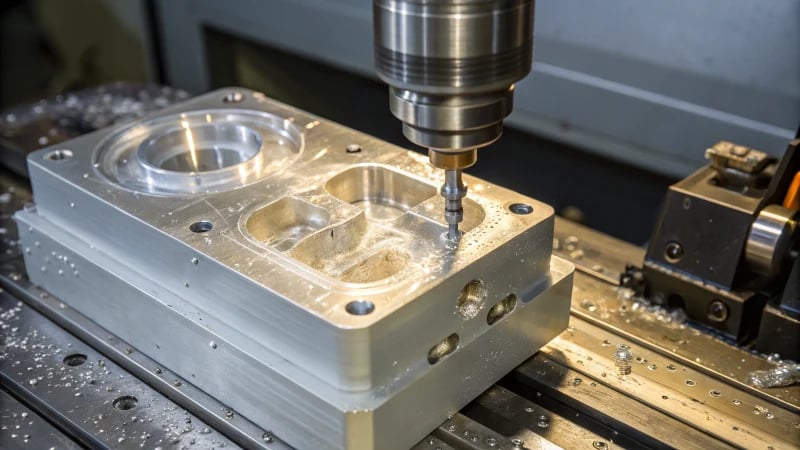
Understanding Release Agents
Let me take you back to one of my early projects in injection molding. I remember standing by the machine, watching as we struggled to remove a freshly molded piece without damaging it. It was then that the importance of release agents hit me like a revelation.
In the injection molding process, these agents are unsung heroes. They work behind the scenes as lubricants or barriers, ensuring that our carefully designed parts don’t cling to the mold like a toddler to their favorite toy. This means the finished products can be easily ejected without damage, preserving the integrity and quality that I pour my heart into every design. Whether I’m working with thermoplastics or metals, choosing the right release agent is like picking the perfect tool for a job—it just makes everything smoother.
Types of Release Agents
I’ve tried various types over the years and can vouch for their distinct benefits. Here’s what I’ve learned:
Type | Characteristics |
---|---|
Water-based | Environmentally friendly, suitable for various materials. |
Solvent-based | Offers excellent lubrication but may require ventilation. |
Semi-permanent | Bonds to mold surface, providing multiple releases before reapplication. |
Silicone-based | High-temperature resistance, effective for complex molds. |
Every time I choose a release agent, I weigh factors like material compatibility and my commitment to environmental sustainability. For instance, I often lean towards water-based agents4 for their eco-friendly nature.
Benefits of Using Release Agents
Integrating release agents into my workflow has been a game-changer. They significantly boost the efficiency of the injection molding process by reducing cycle times and minimizing defects like warping or surface imperfections—problems that used to keep me up at night!
They also help prolong the life of molds by reducing wear and tear. Imagine saving costs on maintenance and enjoying greater design flexibility! It’s like having your cake and eating it too. With proper application techniques, these agents ensure consistent part quality across all my production runs.
Application Techniques
Getting the hang of applying these agents was another journey. Whether I’m spraying, brushing, or using automated systems, even coverage is key to success. Proper training on application methods has led me to optimized production and high-quality outputs. Exploring automated systems5 has been particularly rewarding, streamlining operations while maintaining consistency across projects.
In conclusion, release agents might not be the star of the show in injection molding, but they certainly play a crucial supporting role. By understanding and utilizing them effectively, I’ve been able to achieve better operational outcomes in my work.
Release agents prevent mold damage.True
Release agents act as barriers, preventing parts from sticking to molds.
Solvent-based agents require no ventilation.False
Solvent-based agents need ventilation due to potential fumes.
Why Is Temperature Control Crucial in Mold Release?
Ever felt the frustration of a perfect design falling apart due to temperature mishaps? Let’s dive into why keeping things cool—or warm enough—makes all the difference in mold release.
Temperature control is crucial in mold release as it ensures agents maintain optimal viscosity and evaporation rates, preventing defects and enhancing product quality.
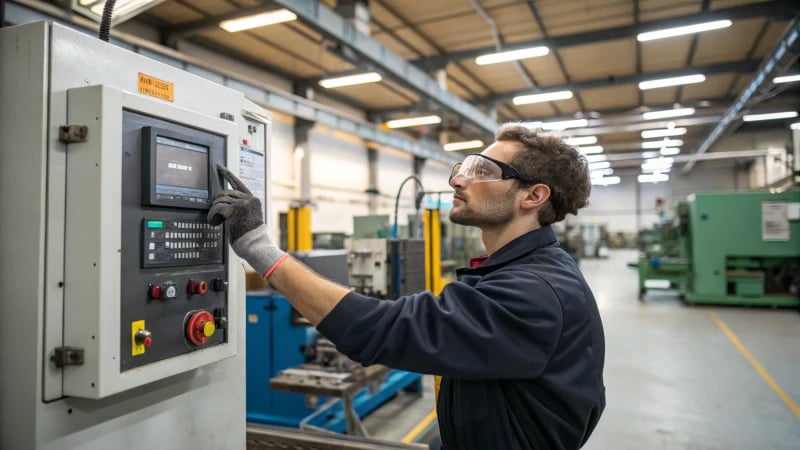
Understanding Temperature’s Role in Mold Release
I remember the first time I dealt with mold release issues. It was a project that seemed straightforward until my perfectly designed parts started sticking to the molds. That’s when I realized how pivotal temperature control really is. Temperature directly impacts the effectiveness of mold release agents6. Each release agent has a specific temperature range for optimal performance, and straying from this range can alter their viscosity, affecting how well they coat the mold surface.
Impact on Viscosity and Evaporation
I learned the hard way that when the temperature gets too high, release agents can become overly thin, leading to uneven coverage. On the flip side, if it’s too cold, they thicken up and don’t spread properly, causing defects like poor surface finishes or parts sticking to molds. Here’s a quick look at how temperature affects viscosity:
Temperature | Effect on Release Agent |
---|---|
High | Decreased viscosity |
Low | Increased viscosity |
Managing Temperature Variations
To prevent these issues, I’ve found that employing precise temperature control systems is crucial. This might involve using insulated molds or temperature-regulating equipment to maintain stability throughout the process. Trust me, once you get this right, it saves a ton of headaches down the line.
Best Practices for Temperature Control
- Monitor Regularly: Sensors are your best friends for continuously checking mold temperature.
- Calibrate Equipment: Keep everything calibrated for accurate readings—I’ve learned that neglecting this step can lead to costly mistakes.
- Material Considerations: Understanding the thermal properties of your materials is essential as they affect heat distribution.
Implementing these practices has helped me achieve consistent mold release performance and cut down on downtime due to defects and maintenance. For more detailed guidelines, you might want to explore advanced temperature control systems7.
High temperatures decrease mold release agent viscosity.True
High temperatures make the agents thinner, leading to uneven coating.
Low temperatures improve mold release agent coverage.False
Low temperatures increase viscosity, causing incomplete coverage.
How does regular maintenance enhance mold performance?
Imagine a world where your molds never fail you—where efficiency, quality, and reliability are all seamlessly in sync. Sounds like a dream, right?
Regular mold maintenance ensures high quality, extends lifespan, and prevents breakdowns through consistent cleaning, inspections, and repairs, thereby optimizing performance and minimizing downtime.
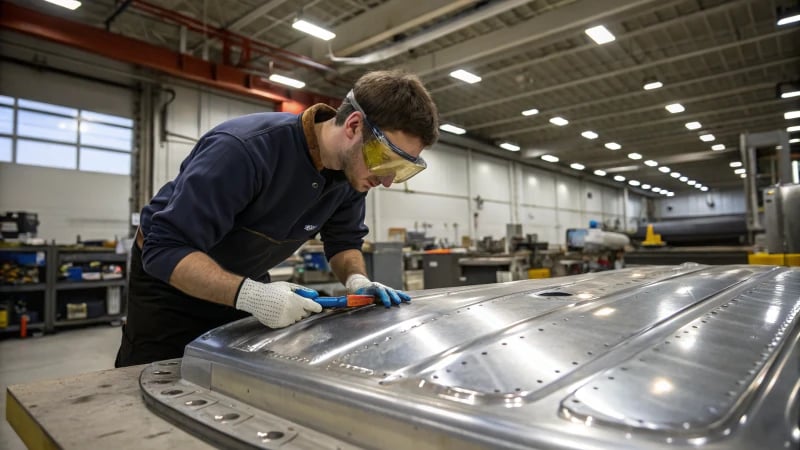
Understanding the Importance of Regular Maintenance
I remember the first time I faced a mold breakdown; it was like watching a meticulously planned domino setup collapse in slow motion. It was then that I truly understood the power of regular maintenance in mold management. By keeping a systematic eye on cleaning, inspecting, and repairing components8, I found myself preventing those dreaded production hiccups before they even began.
Key Benefits of Regular Mold Maintenance
- Enhanced Efficiency: Just like how my morning coffee kickstarts my day, well-maintained molds keep production running smoothly. Clean molds cut down cycle times, boosting output and ensuring resources are used wisely.
- Extended Lifespan: I learned that addressing minor wear and tear early is like giving my car its regular oil change—it keeps everything running longer and saves on expensive replacements down the road.
- Reduced Downtime: Scheduled maintenance has become my secret weapon against unexpected breakdowns. Knowing that production won’t grind to a halt allows me to sleep a bit easier at night.
Benefit | Description |
---|---|
Enhanced Efficiency | Reduces cycle time and increases output |
Extended Lifespan | Avoids costly replacements |
Reduced Downtime | Ensures consistent operation |
Best Practices for Mold Maintenance
- Scheduled Cleaning: Just as I tidy up my workspace to think clearly, regular cleaning of molds prevents material build-up that could lead to defects. The right cleaning agents are key to keeping them in peak condition.
- Routine Inspections: These are my regular check-ups for molds, helping me catch potential issues early on. It’s like spotting a small leak before it becomes a flood.
- Timely Repairs: Proactivity is my mantra here—addressing issues promptly helps maintain optimal functionality, much like fixing a loose doorknob before it falls off completely.
- Documentation and Analysis: Keeping detailed records of maintenance activities is invaluable. Analyzing these records uncovers patterns or recurring issues, leading to better strategies9 for mold care.
Technological Aids in Mold Maintenance
Embracing technology has been a game-changer for me. Predictive maintenance tools use data analytics to foresee potential failures, allowing me to take action before problems arise. By integrating these practices and technologies, I’ve found that mold performance isn’t just about maintaining quality—it’s about achieving it consistently while cutting costs. This approach has not only improved performance but also aligned with sustainable manufacturing practices, making it a win-win for me and my operations.
Regular maintenance reduces mold production cycle time.True
Maintenance prevents defects, ensuring molds operate smoothly, reducing cycle time.
Ignoring mold maintenance leads to increased production costs.True
Neglecting maintenance causes inefficiencies and breakdowns, raising costs.
What Innovative Techniques Are Emerging in Mold Release Technology?
Imagine the thrill of discovering a breakthrough technique that could completely transform your manufacturing process.
Innovative mold release techniques include advanced coatings, nanotechnology, and eco-friendly solutions, enhancing release efficiency, reducing waste, and improving product quality to meet modern manufacturing demands.
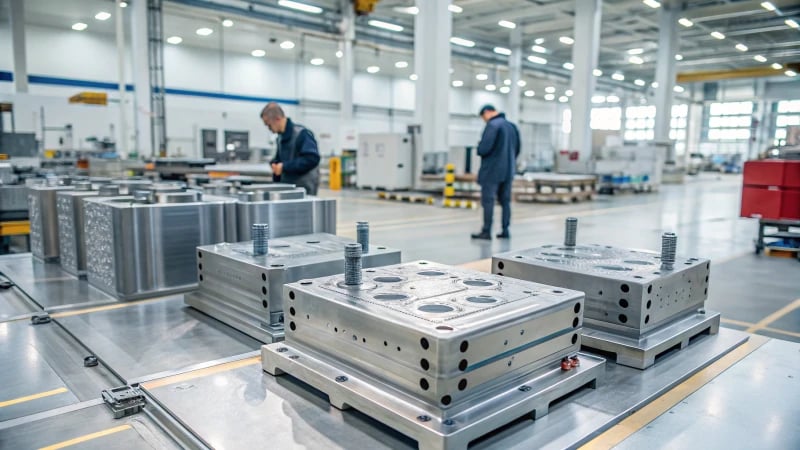
I remember the first time I stumbled upon a new mold release technique. It was like finding a hidden gem that promised to make my job smoother and more efficient. These days, the innovations in mold release technology are almost magical in how they tackle age-old problems with fresh solutions.
Advanced Coatings for Mold Release
One of the most significant advancements I’ve seen is the development of advanced coatings. These coatings are engineered to withstand the intense heat and pressure of manufacturing processes, creating a durable barrier between the mold and the product. This not only minimizes sticking issues but also extends the life of both the mold and the product itself. I found this particularly useful when working on projects for industries that demand precision and durability, like automotive and aerospace. It’s incredible how these advanced coatings10 can make such a difference.
Nanotechnology in Mold Release
Then there’s nanotechnology, which feels like something straight out of a science fiction novel. By incorporating nanoscale materials, we’re able to enhance release properties without compromising the surface of the product. This ensures a smooth release, crucial for those intricate designs or tight tolerances I’ve often dealt with. Introducing nanotechnology11 in mold release not only boosts efficiency but also cuts down on the need for post-processing steps—something I always appreciate in fast-paced projects.
Eco-Friendly Release Agents
Finally, the push for sustainability has led to eco-friendly release agents that are biodegradable and non-toxic. This shift is not just about reducing environmental impact; it also makes for a healthier workplace by minimizing exposure to harmful chemicals. Switching to eco-friendly agents12 felt like a win-win situation for our company, aligning with our green goals while maintaining high production standards.
Comparative Analysis of Techniques
Technique | Benefits | Industries Benefiting |
---|---|---|
Advanced Coatings | Durability and temperature resistance | Automotive, Aerospace |
Nanotechnology | Enhanced release properties | Electronics, Medical Devices |
Eco-Friendly Agents | Reduced environmental impact | All industries focusing on sustainability |
Each technique has its unique perks catering to different industry needs. For instance, while advanced coatings are tailored for high-temperature applications, eco-friendly agents perfectly align with sustainability goals. Understanding which technique fits best requires assessing specific production needs and environmental policies.
By exploring these innovations, professionals like myself can stay ahead in mold design and manufacturing.
Advanced coatings extend mold life in manufacturing.True
Advanced coatings reduce sticking issues, increasing the lifespan of molds.
Nanotechnology in mold release increases post-processing needs.False
Nanotechnology reduces post-processing by enhancing release properties.
Conclusion
Effective solutions for injection molding challenges include optimizing mold design, utilizing release agents, maintaining temperature control, and performing regular maintenance to enhance production efficiency and product quality.
-
Learn how injection molding works and why it’s crucial for efficient manufacturing. ↩
-
Discover the importance of cooling systems in reducing production times. ↩
-
Explore cutting-edge techniques that enhance mold design efficiency. ↩
-
Learn about how water-based release agents can contribute to sustainable manufacturing practices. ↩
-
Discover how automated systems enhance the consistency and efficiency of release agent application. ↩
-
Understanding how temperature affects mold release agents can help you choose the right product for your process and avoid common defects. ↩
-
Discover advanced systems that can help maintain consistent temperatures during mold operations, optimizing production efficiency and reducing defects. ↩
-
Learn why timely repairs are essential for maintaining mold efficiency and preventing long-term damage. ↩
-
Discover effective methods for documenting maintenance activities to enhance mold care strategies. ↩
-
Discover how these coatings enhance durability and efficiency in mold release processes. ↩
-
Explore the role of nanotechnology in improving mold release performance. ↩
-
Learn about sustainable mold release solutions that reduce environmental impact. ↩