Navigating the dynamic landscape of mold making requires a keen eye for the latest rapid prototyping techniques.
Effective rapid prototyping techniques for mold making include 3D printing, CNC machining, and injection molding. They provide speed, precision, and cost-efficiency, enhancing production and design outcomes.
Every time I dive into a new project, I find myself weighing the benefits of these techniques—3D printing for its flexibility, CNC machining for its precision, and injection molding for its efficiency. It’s like having a toolbox where each tool has its own special role. Let’s explore how these techniques can transform your design process and see what else might elevate your next project.
3D printing offers the fastest prototyping for molds.True
3D printing is known for its rapid production capabilities, making it ideal for quick prototyping.
Injection molding is cost-effective for small production runs.False
Injection molding is typically more cost-effective for large production runs due to initial setup costs.
- 1. How is 3D Printing Revolutionizing Mold Making?
- 2. What Are the Pros and Cons of CNC Machining in Rapid Prototyping?
- 3. Why Is Injection Molding a Key Technique in Prototyping?
- 4. What Are the Best Materials for Rapid Prototyping in Mold Making?
- 5. How Can You Optimize Your Mold Designs for Faster Prototyping?
- 6. What Future Trends Should Mold Designers Watch in Rapid Prototyping?
- 7. Conclusion
How is 3D Printing Revolutionizing Mold Making?
Ever wondered how 3D printing is changing the game for mold makers like us?
3D printing revolutionizes mold making by enabling rapid prototyping, reducing costs, and allowing for complex, customized designs, enhancing efficiency in production processes.
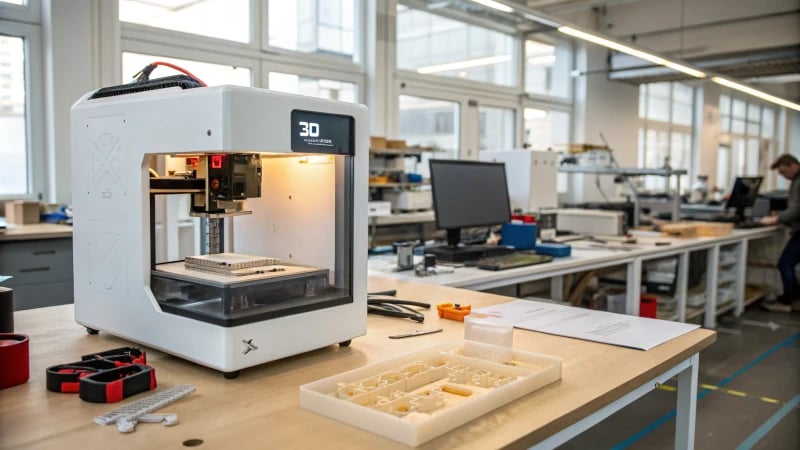
The Power of Rapid Prototyping
I remember the first time I witnessed a 3D printer in action—it felt like watching a sci-fi movie come to life. In traditional mold making, creating a prototype could stretch into weeks. But with 3D printing, it’s like having a magic wand that turns your CAD designs into tangible objects overnight. This speed isn’t just about saving time; it slashes the costs tied up in multiple iterations, making the whole process more economical and less stressful. This speed not only reduces development time1 but also lowers costs associated with multiple iterations.
Cost Efficiency and Material Savings
Back in the day, I’d cringe at the sight of material waste during the mold-making process. It was as if we were cutting down trees just to build a single birdhouse. But with 3D printing, every layer is meticulously added, and nothing goes to waste. It’s a relief knowing that we’re not only saving money but also being kinder to our planet. This cost-effectiveness2 makes it an attractive option for companies looking to save on production expenses.
Enhanced Design Complexity
I once tackled a project that required an incredibly intricate mold design. The complexity was daunting with traditional methods, but 3D printing turned what seemed impossible into reality. This technology enables us to push boundaries in industries like automotive and aerospace, where detailed precision is everything.
Traditional Mold Making | 3D Printing |
---|---|
Longer lead times | Faster prototyping |
Higher material waste | Minimal waste |
Limited design options | Complex designs |
Customization and Flexibility
One of the joys of working with 3D printing is the freedom to customize. I can tweak designs on the fly without worrying about blowing the budget. This adaptability enhances product development3 cycles, providing a competitive edge in rapidly evolving markets.
Overcoming Limitations
Of course, it’s not all sunshine and roses. I’ve encountered challenges with the strength of 3D-printed molds compared to their traditional counterparts. But with advancements in materials and technology, we’re steadily overcoming these hurdles. The integration of cutting-edge technology4 promises even stronger, more durable molds as cutting-edge developments continue to evolve.
It’s clear that 3D printing is not just a passing trend—it’s reshaping how we approach mold making, offering endless possibilities for creativity and efficiency.
3D printing reduces mold development time.True
3D printing allows for rapid prototyping, speeding up mold development.
Traditional mold making produces less material waste than 3D printing.False
Traditional methods often lead to more waste, unlike 3D printing.
What Are the Pros and Cons of CNC Machining in Rapid Prototyping?
Ever found yourself knee-deep in a project and wondering if CNC machining is the right call? I sure have. Let’s dive into what makes this technique a game-changer—and what might make you pause.
CNC machining in rapid prototyping provides high precision and fast production with diverse materials but incurs higher costs and material waste. Balancing these factors is crucial for making informed decisions.
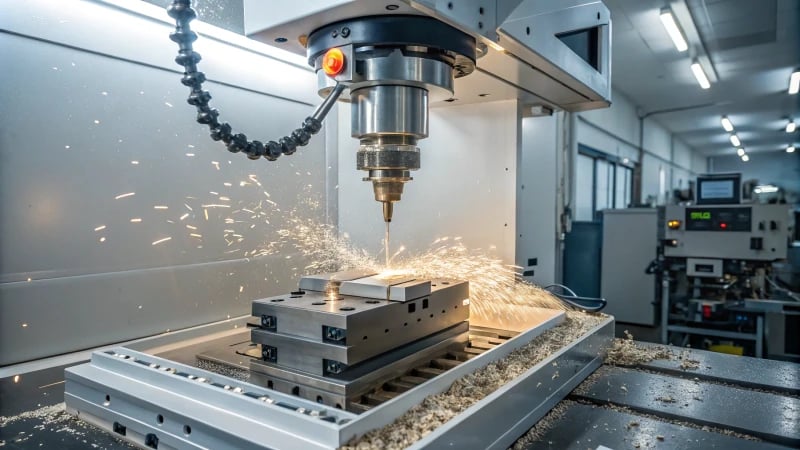
Advantages of CNC Machining
1. Precision and Accuracy: CNC machining is like having an artist’s steady hand on your side. It’s all about getting those intricate details just right, which is something I’ve come to rely on when creating complex prototypes. Every time I see a design turn out exactly as planned, it’s like witnessing a small miracle.
2. Speed and Efficiency: Deadlines are the bane of my existence, so having a process that speeds things up is invaluable. Once you’ve got that design programmed, the machine churns out parts with impressive speed. This capability has saved my bacon more than once on projects that demanded quick iterations in rapid prototyping5.
3. Material Versatility: The flexibility to work with different materials is another huge plus. Whether I’m working with metals, plastics, or composites, CNC machining accommodates my creative whims without batting an eye.
Disadvantages of CNC Machining
1. Cost Considerations: Now, let’s talk money. The initial investment in CNC machinery can make your wallet wince, and the ongoing costs aren’t much friendlier.
Aspect | Cost Implication |
---|---|
Machine Purchase | High initial cost |
Operational Costs | Energy and maintenance |
2. Material Wastage: Here’s the rub—CNC is a subtractive process, meaning there’s always some material left over that doesn’t make it into your final product. It’s like baking a cake and tossing half the batter; not ideal when you’re thinking about sustainability.
3. Geometrical Limitations: Sometimes, I dream big—maybe too big for CNC machining. Some designs just don’t translate well due to tooling constraints or compromising on design integrity6. It’s crucial to keep these limitations in mind unless you’re okay with redesigning or compromising on your vision.
CNC machining is ideal for rapid prototyping due to high precision.True
CNC machining allows for precise and accurate prototype creation.
CNC machining is cost-effective compared to all other prototyping methods.False
CNC has high initial and operational costs, making it less cost-effective.
Why Is Injection Molding a Key Technique in Prototyping?
Ever wondered how those perfectly shaped plastic parts are made so precisely? Let me share my journey with injection molding and why it’s a game-changer in prototyping.
Injection molding is pivotal in prototyping for its precision, cost-efficiency, scalability, diverse material options, and superior surface finishes, making it ideal for design refinement.
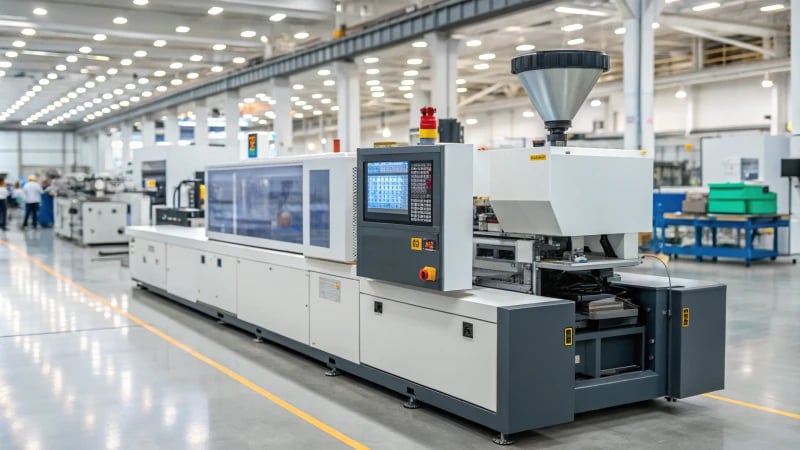
The Role of Injection Molding in Prototyping
I remember the first time I saw an injection molding machine in action—it was like watching magic unfold. This technique is truly revolutionary during the prototyping phase. Imagine being able to create high-quality, consistent parts that fit together seamlessly. For me, it’s all about ensuring that each component of my design not only fits perfectly but also functions just as intended before diving into full-scale production. Unlike other methods, injection molding lets me work with intricate designs and tight tolerances, which is crucial when you’re crafting something that has to meet precise specifications7.
Speed and Efficiency
Speed is another reason I swear by injection molding for prototyping. Once I’ve got the mold ready, it’s like flipping a switch—the production cycles are fast, enabling me to iterate quickly. This speed is vital because it means I can test and tweak designs based on real-world feedback without wasting time. In my experience, having the ability to refine a product swiftly often makes the difference between success and missed opportunities.
Cost-Effectiveness
I won’t lie—the initial cost of creating a mold can be steep. However, when I look at the bigger picture, the per-unit cost for manufacturing becomes incredibly economical, especially at scale. For any project where multiple iterations are required or where prototypes need to be tested under different conditions, this cost-effectiveness is a huge advantage. It allows me to experiment and refine without burning through the budget.
Factor | Injection Molding | 3D Printing |
---|---|---|
Precision | High | Moderate |
Speed | Fast (after mold creation) | Slower |
Material Versatility | Extensive | Limited |
Cost per Unit | Low (at scale) | High |
Material Versatility
One of the things I love about injection molding is its versatility with materials. Whether it’s plastics or metals, I can choose the perfect material that aligns with the functional needs of my prototype. This choice ensures that the prototype’s properties are closely aligned with what the final product will offer, giving me invaluable insights into any potential performance issues8.
Surface Finish Quality
The surface finish quality with injection molding is often superior to other methods I’ve tried, like 3D printing. When I’m working on aesthetic prototypes where appearance is everything, this quality is a massive plus. It also cuts down on the need for additional processes like sanding or painting.
In essence, injection molding bridges the gap between design and production with unmatched precision, efficiency, and material versatility. Understanding these benefits has dramatically influenced my decision-making process in product development.
Injection molding offers superior surface finish quality.True
Injection molding provides a high-quality finish, reducing need for post-processing.
3D printing is faster than injection molding after mold creation.False
Once the mold is created, injection molding cycles are quicker than 3D printing.
What Are the Best Materials for Rapid Prototyping in Mold Making?
Choosing the right materials for mold-making prototypes feels like selecting the perfect ingredients for a cake—get it right, and everything just works! Dive into the options to discover which ones suit your project best.
The best materials for rapid prototyping in mold making include thermoplastics (ABS, PLA), photopolymers, and urethane, valued for their ease of use, strength, and versatility.
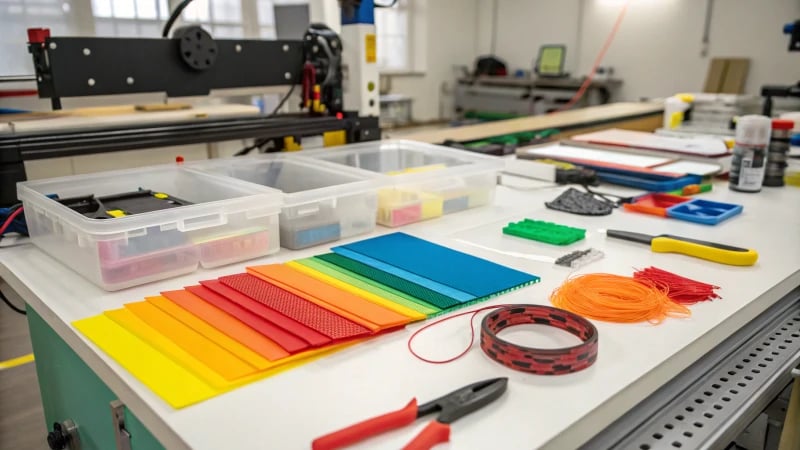
Understanding Material Properties
As I stood in my workshop, surrounded by sketches and 3D models, I realized that choosing the right material was like picking the right pair of shoes for a hike—durability, flexibility, and comfort were non-negotiable. Thermoplastics such as ABS9 and PLA10 came to mind because they offer robust strength and can handle heat like a pro.
Photopolymers are another option. The first time I used them in stereolithography11, it was like magic seeing my design come to life with such precision and smoothness. These materials are perfect for projects where high detail is essential.
Material | Benefits | Applications |
---|---|---|
ABS | Strong, heat-resistant | Automotive parts |
PLA | Easy to print, biodegradable | Consumer electronics |
Photopolymers | High precision, smooth finish | Medical devices |
Exploring Alternative Materials
I remember a project where nothing seemed to fit until I stumbled upon urethane. Its flexibility allowed me to create molds with intricate details, almost like crafting a sculpture out of clay. With CNC machining12, urethane molds transformed the production process, bringing accuracy and speed.
While metallic powders aren’t the go-to for every project, they’re invaluable for metal additive manufacturing techniques like Selective Laser Sintering13. They reminded me of those rare spices you only use for special dishes—they’re not always necessary, but when they are, they add immense value.
Factors Influencing Material Choice
Balancing cost, strength, and environmental impact14 feels like juggling; one wrong move and everything crashes down. For instance, PLA is budget-friendly but might not withstand all demands. Meanwhile, photopolymers deliver precision but can stretch the budget.
In my experience, understanding these nuances helps make decisions that not only elevate prototype performance but also ensure they fit seamlessly into larger manufacturing goals. It’s about finding that sweet spot where functionality meets feasibility. And when you get it right, it’s like hitting a home run—everything just clicks.
ABS is heat-resistant and strong for prototypes.True
ABS is widely used due to its strength and heat resistance.
Photopolymers are not suitable for high-detail prototypes.False
Photopolymers offer excellent surface finish and high precision.
How Can You Optimize Your Mold Designs for Faster Prototyping?
Ever wondered how you can tweak your mold designs to speed up prototyping without cutting corners? Let me show you how it’s done!
Optimize mold designs for faster prototyping by simplifying geometry, utilizing advanced CAD software, and adopting rapid tooling methods. These strategies reduce complexity, improve accuracy, and speed up production.
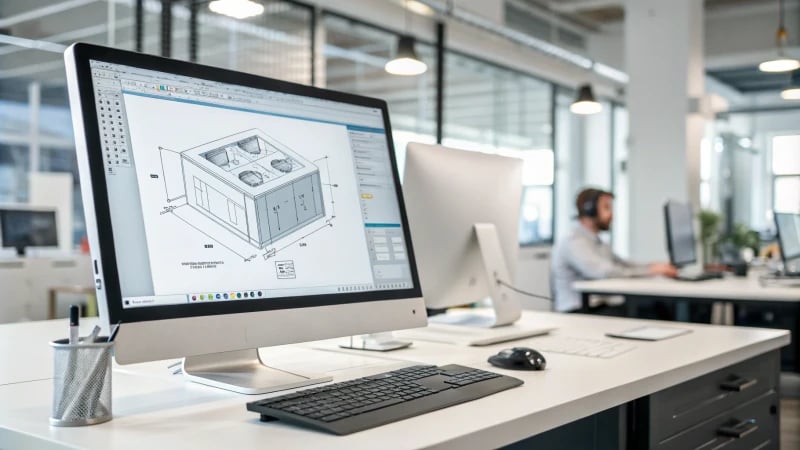
Simplifying Mold Geometry
Back in my early design days, I learned the hard way that intricate designs, though beautiful, can be a nightmare during prototyping. Imagine the frustration of waiting for a complex mold only to find it riddled with errors due to its intricate geometry. By honing in on just the essential features and trimming down unnecessary details, I’ve found production becomes smoother and much faster. Trust me, it’s about working smarter, not harder.
Leveraging Advanced CAD Software
I can’t stress enough how revolutionary advanced CAD software has been for my design process. It’s like having a crystal ball to foresee potential molding issues before they’re set in stone—or rather, plastic. By simulating the entire molding process15, I’ve managed to spot and rectify issues early on. This not only saves valuable time but also conserves resources, enabling quick adjustments on the fly.
Software | Features |
---|---|
SolidWorks | Simulation tools, collaborative design |
AutoCAD | 3D modeling, precise measurements |
Implementing Rapid Tooling Methods
Rapid tooling has been a game-changer for me. I recall a project where traditional methods would have delayed us by weeks. Instead, by using 3D printing16 to create prototype molds, we were able to iterate quickly and effectively test out ideas. This approach works wonders, especially when dealing with low-volume production runs where time is of the essence.
Design for Manufacturing (DFM) Principles
Incorporating DFM principles into my designs has been another key strategy. By considering draft angles, wall thickness, and undercuts from the get-go, I ensure the mold design is easier to manufacture. Reducing manufacturing complexity17 not only minimizes defects but also speeds up the prototyping phase significantly.
Collaborating with Cross-functional Teams
One thing I’ve learned over the years is that collaboration is key. Working closely with engineering and manufacturing teams has provided me with invaluable insights that I couldn’t have achieved alone. By identifying potential challenges early and developing solutions collectively, we’ve enhanced design efficiency18. Regular feedback loops are essential—they foster continuous improvement and innovation across the board.
Simplifying mold geometry speeds up prototyping.True
Reducing complexity in design minimizes machining time and errors.
3D printing is not useful for rapid tooling.False
3D printing accelerates mold production, ideal for quick iterations.
What Future Trends Should Mold Designers Watch in Rapid Prototyping?
Ever feel like you’re trying to keep up with a never-ending wave of innovation? As mold designers, staying on top of rapid prototyping trends is crucial.
Mold designers should watch for automation advancements, sustainable materials, and AI integration in rapid prototyping to enhance design efficiency and maintain competitiveness.
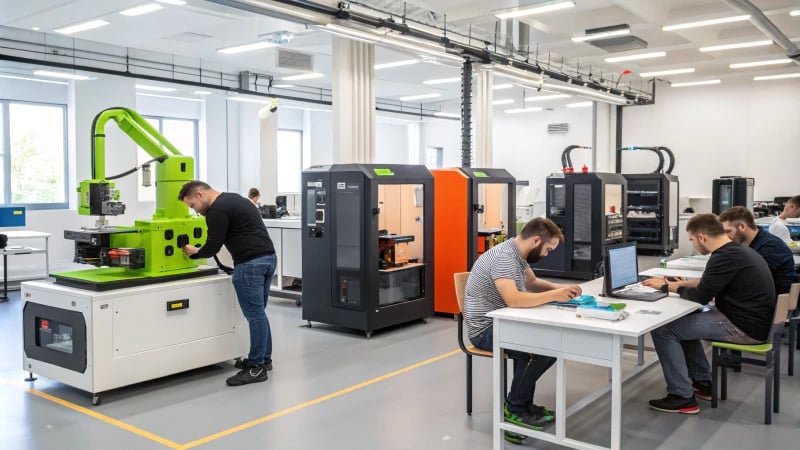
Automation and Robotics in Prototyping
I remember when I first saw a robotic arm in action at a trade show. It was mesmerizing, watching it carve out intricate shapes with such precision and speed. That moment made me realize how robotics could revolutionize our field. Today, the integration of robotics19 in prototyping is indeed transforming how molds are designed and produced. Automated systems take over the mundane tasks, allowing us to focus on creativity and problem-solving.
Table: Automation Benefits
Benefit | Description |
---|---|
Speed | Faster production timelines due to reduced manual labor |
Precision | High accuracy in creating complex mold shapes |
Cost Efficiency | Reduced labor costs and material waste |
Sustainable Materials
A few years ago, I attended a workshop on sustainable design, and it opened my eyes to the possibilities of using eco-friendly materials. Nowadays, with rising environmental concerns, incorporating sustainable materials20 into our work isn’t just a trend—it’s a responsibility. Experimenting with biodegradable plastics and recycled materials not only helps reduce our ecological footprint but also maintains the high standards we strive for.
AI and Machine Learning
The first time I tested an AI tool that could predict design flaws, it felt like having a superpower. The potential to foresee problems before they arise is game-changing. Artificial Intelligence (AI) is transforming our design processes, analyzing vast datasets to optimize designs both functionally and aesthetically. Machine learning algorithms offer predictive capabilities that are invaluable in rapid prototyping21, where time and accuracy are of the essence.
Embracing these trends allows us to push our creative boundaries and improve our craft, ensuring we stay relevant in a fast-evolving industry. Keeping pace with technological advancements not only boosts efficiency but also fosters innovation—a crucial edge in today’s competitive landscape.
Robotics reduce mold production time.True
Automation in prototyping speeds up production by reducing manual labor.
AI cannot predict design flaws in prototyping.False
AI and machine learning can predict design flaws, saving time and resources.
Conclusion
Explore effective rapid prototyping techniques for mold making, including 3D printing, CNC machining, and injection molding, highlighting their speed, precision, and cost-efficiency in enhancing production processes.
-
Understanding how rapid prototyping accelerates development can help you leverage speed in your projects. ↩
-
Exploring cost-saving strategies can lead to more efficient budgeting in manufacturing processes. ↩
-
Customization insights can enhance your approach to tailored product solutions. ↩
-
Staying updated on material innovations can improve mold strength and application possibilities. ↩
-
Discover how CNC machining enhances rapid prototyping with improved speed and efficiency. ↩
-
Learn about the geometrical constraints faced in CNC machining to better plan your designs. ↩
-
This link explores how injection molding tests fit and functionality in designs effectively. ↩
-
Learn how choosing the right material in injection molding prevents performance issues. ↩
-
Explore why ABS is favored for prototypes needing strength and heat resistance. ↩
-
Discover the reasons behind PLA’s popularity in rapid prototyping. ↩
-
Learn how stereolithography achieves high-detail prototypes. ↩
-
Understand how CNC machining complements urethane’s versatility. ↩
-
Find out how SLS helps create functional metal prototypes. ↩
-
Evaluate how different materials affect environmental sustainability. ↩
-
Advanced CAD software helps simulate processes and identify issues early. ↩
-
3D printing accelerates prototype mold creation for faster testing. ↩
-
DFM principles reduce manufacturing complexity and defects. ↩
-
Collaboration uncovers challenges early, enhancing design efficiency. ↩
-
Explore how robotics is changing the prototyping landscape, increasing precision and efficiency. ↩
-
Learn about eco-friendly materials that are shaping the future of prototyping. ↩
-
Discover AI tools that enhance design accuracy and speed in rapid prototyping. ↩