Are you struggling with shrinkage in your injection molded products? You’re not alone—it’s a common challenge in the manufacturing process.
To effectively address shrinkage in injection molded products, consider optimizing materials, mold design, process parameters, and post-processing techniques. Each plays a crucial role in minimizing defects and enhancing product quality.
While these initial insights provide a solid foundation, there’s so much more to explore. Dive deeper into these strategies to discover nuanced methods and expert tips that can truly transform your approach.
Material selection impacts shrinkage in injection molding.True
Choosing materials with low shrinkage and good fluidity reduces defects.
How Does Material Selection Influence Shrinkage?
Material selection is pivotal in determining shrinkage rates in injection molded products. Here’s why it matters.
Material selection impacts shrinkage in injection molding through factors like plastic type, fluidity, and moisture content. Choosing materials with low shrinkage characteristics and good fluidity ensures better mold filling and dimensional accuracy. Pre-drying plastics to control moisture can further minimize shrinkage issues.
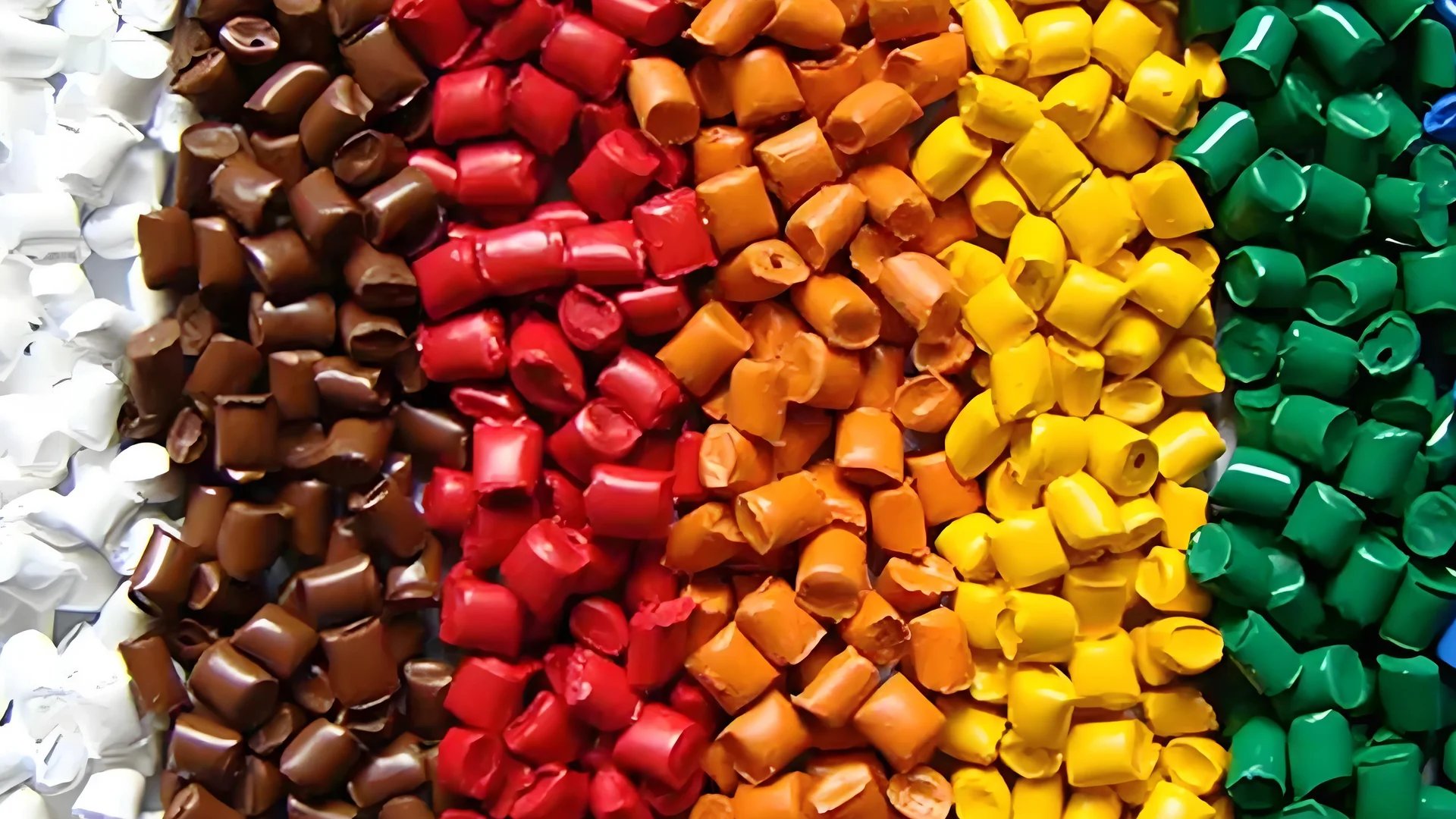
Understanding Shrinkage Characteristics of Plastics
When selecting materials for injection molding, it’s crucial to understand the inherent shrinkage characteristics1 of different plastics. Thermoplastics, for example, tend to have higher shrinkage rates compared to thermosets. Engineers often choose engineering plastics like polycarbonate for applications demanding high dimensional accuracy due to their relatively low shrinkage.
Importance of Fluidity in Plastic Selection
The fluidity of plastic greatly influences the ability to fill molds effectively, which in turn affects shrinkage. Plastics with good fluidity ensure that the material fills the mold cavities evenly, reducing potential for uneven shrinkage and voids in the final product. Materials such as ABS (Acrylonitrile Butadiene Styrene) are often preferred for their excellent flow characteristics.
Managing Moisture Content to Reduce Shrinkage
Moisture in plastics can vaporize during injection molding, leading to pores and shrinkage within the product. Hence, pre-drying plastics is a critical step. For instance, nylon needs thorough drying to prevent moisture-induced defects. Different plastics require specific drying times and temperatures to achieve optimal results.
Plastic Type | Recommended Drying Temperature | Typical Drying Time |
---|---|---|
Nylon | 80°C (176°F) | 4-6 hours |
Polycarbonate | 120°C (248°F) | 2-4 hours |
ABS | 80°C (176°F) | 2-3 hours |
Real-World Examples of Material Selection
Consider an automotive component manufacturer choosing between polypropylene and polyamide for a dashboard component. Due to the lower shrinkage rate and better dimensional stability of polyamide, they opt for it despite its higher cost, resulting in fewer rejects and better overall quality.
To sum up, material selection is a balancing act between cost, desired properties, and processing considerations. By understanding how each aspect influences shrinkage, manufacturers can make informed choices that enhance product quality.
Thermosets have higher shrinkage than thermoplastics.False
Thermoplastics generally have higher shrinkage rates compared to thermosets.
Pre-drying plastics reduces moisture-induced shrinkage.True
Pre-drying removes moisture that can vaporize during molding, reducing shrinkage.
What Role Does Mold Design Play in Reducing Shrinkage?
Mold design significantly impacts the shrinkage of injection molded products, influencing dimensional accuracy and product quality.
Effective mold design minimizes shrinkage in injection molding by optimizing cooling systems, gate and runner configurations, and mold sizing. By tailoring these aspects to specific plastic materials and product requirements, manufacturers can significantly reduce defects and enhance product quality.
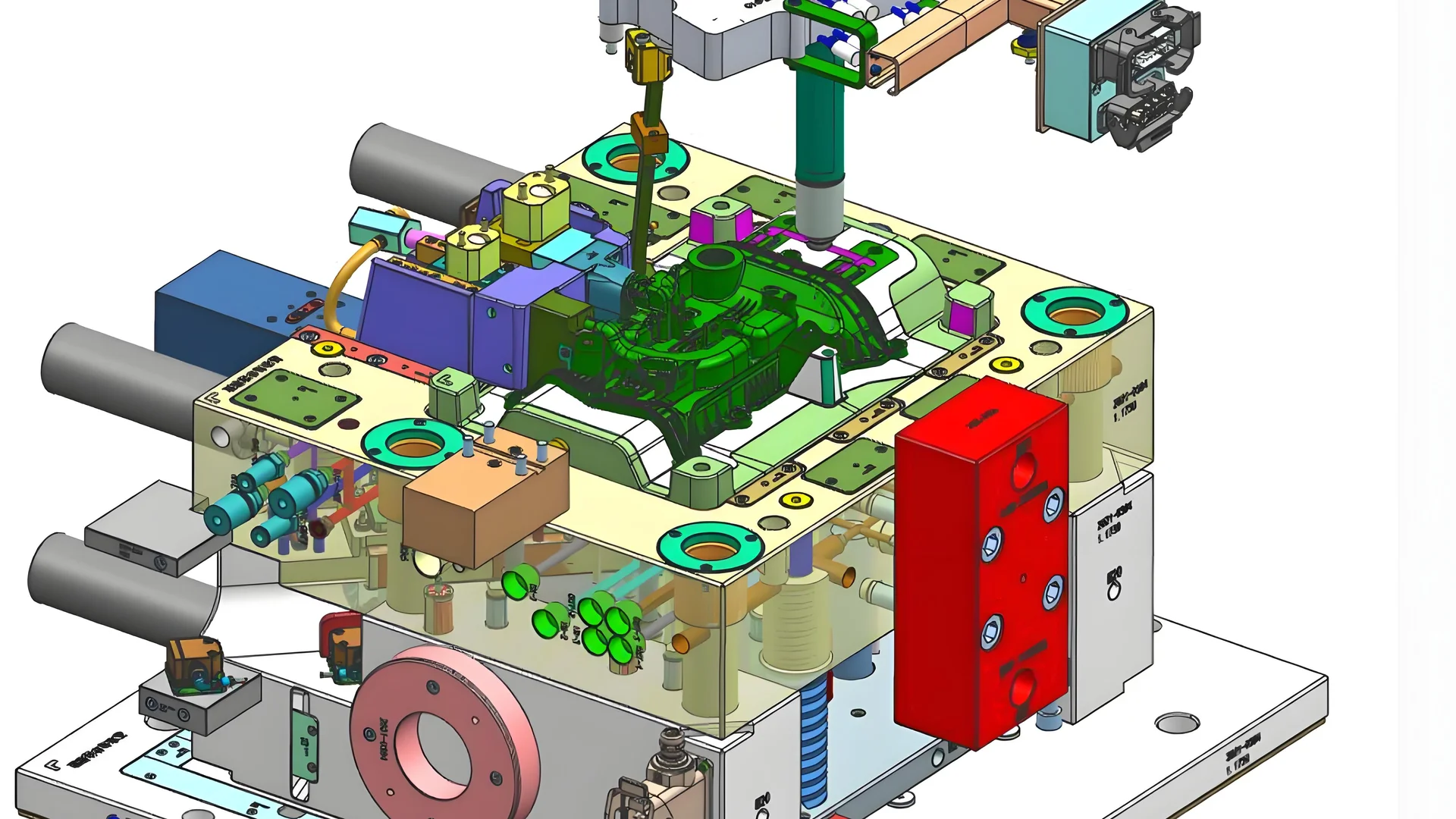
Importance of Cooling Systems in Mold Design
Cooling systems are a pivotal component of mold design that directly influence the degree of shrinkage in injection molded products. By incorporating a sophisticated cooling system, molds can ensure uniform temperature distribution, allowing products to cool evenly and minimize shrinkage. For instance, strategically placed cooling channels can reduce the temperature gradient across the mold, leading to consistent shrinkage compensation. This approach is particularly effective for complex geometries or large parts, where uneven cooling might otherwise lead to warping or dimensional inaccuracies.
Explore more about advanced cooling techniques2 to understand how they can be integrated into modern mold designs.
Gate and Runner System Configuration
The gate and runner system serves as the conduit through which molten plastic flows into the mold cavity. A well-designed system ensures that the plastic fills the mold evenly, reducing the likelihood of shrinkage discrepancies. For example, balanced runner systems can distribute plastic uniformly, while gate placement can be optimized to reduce pressure drop and avoid areas of high shrinkage. An understanding of the flow characteristics of the chosen plastic material is essential to configure these systems effectively.
Learn how gate design impacts shrinkage3 and can be adjusted to mitigate common defects.
Adjusting Mold Size for Shrinkage Compensation
Mold size is inherently linked to the shrinkage rate of the plastic being used. By precisely enlarging the mold dimensions according to the predicted shrinkage rate, manufacturers can offset the shrinkage that occurs during cooling. This practice is critical for maintaining dimensional accuracy, particularly for products with stringent tolerances. Regularly updating mold designs based on empirical data from previous production runs can further refine this approach.
Discover ways to calibrate mold size adjustments4 for different materials and achieve optimal results.
Ensuring Mold Accuracy and Maintenance
The accuracy of a mold is fundamental to controlling shrinkage. High-precision molds, created using advanced machining technologies, provide superior surface quality and dimensional accuracy, minimizing potential shrinkage issues. Regular maintenance is also crucial; wear and tear over time can affect the mold’s dimensions and surface finish, leading to increased shrinkage variance.
Find out why regular mold maintenance5 is key to reducing shrinkage-related defects.
By comprehensively optimizing these aspects of mold design, manufacturers can effectively reduce shrinkage in injection molded products, enhancing both the quality and precision of their output.
Cooling systems are essential to reduce shrinkage.True
Cooling systems ensure uniform temperature distribution, minimizing shrinkage.
Gate design does not affect shrinkage in molding.False
Gate design impacts plastic flow and pressure, influencing shrinkage.
Which Process Adjustments Are Most Effective for Minimizing Shrinkage?
Tackling shrinkage in injection molding demands precise process adjustments. Discover the techniques that significantly reduce defects and improve product quality.
Key process adjustments to minimize shrinkage include optimizing injection temperature, pressure, holding time, and cooling duration. These parameters ensure uniform material flow and solidification, reducing internal stresses and enhancing dimensional accuracy.
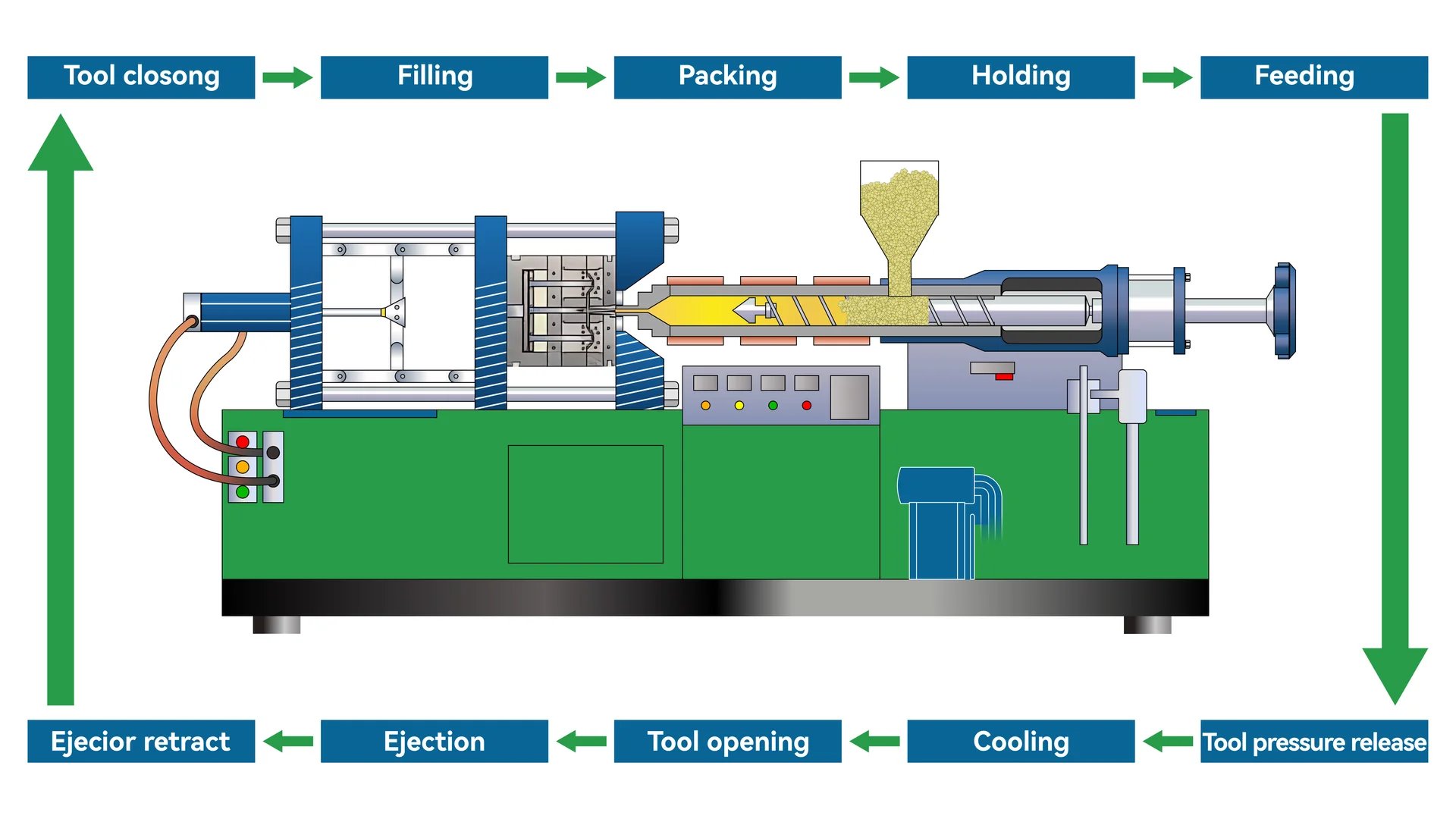
The Role of Injection Molding Temperature
Balancing the injection molding temperature6 is critical. Lowering the temperature can minimize shrinkage, but it’s a fine line; too low, and it hampers fluidity, leading to incomplete fills. Therefore, each plastic’s unique characteristics should guide the temperature settings, ensuring an optimal balance between fluidity and solidification.
Fine-Tuning Injection Pressure
Increasing the injection pressure tightens the fill within the mold cavity, thus mitigating shrinkage. However, it’s essential to avoid excessive pressure that could induce internal stress. Carefully calibrating the pressure according to the material and product specifications ensures a robust yet stress-free final product.
Holding Time and Pressure Optimization
Holding time and pressure are pivotal in compensating for shrinkage during cooling. Extending these can reduce voids and enhance density but must be finely tuned to prevent internal stress. Tailoring these parameters based on material needs can significantly boost product integrity.
Parameter | Effect on Shrinkage | Best Practices |
---|---|---|
Injection Temperature | Lower reduces shrinkage but affects fluidity | Balance per material characteristics |
Injection Pressure | Increases fill density, reduces shrinkage | Avoid excessive pressure to limit stress |
Holding Time & Pressure | Compensates shrinkage during cooling | Optimize to prevent internal stress |
Extending Cooling Time
Prolonging cooling time ensures complete solidification within the mold, reducing residual shrinkage. However, longer cycles can impede production efficiency, so determining an ideal cooling period that balances quality with throughput is necessary for effective manufacturing.
Controlling Production Environment
Stability in the production environment regarding temperature and humidity helps in maintaining consistent shrinkage rates. Sudden changes can alter material behavior, impacting dimensional accuracy. Hence, maintaining controlled conditions is crucial for uniformity.
Explore these process adjustments to achieve superior outcomes in injection molding by minimizing shrinkage effectively. This nuanced approach not only enhances product quality but also optimizes the manufacturing process for efficiency and reliability.
Lowering injection temperature reduces shrinkage.True
Decreasing the temperature minimizes shrinkage but affects fluidity.
Excessive injection pressure increases product stress.True
Too much pressure can induce internal stress, affecting quality.
Can Post-Processing Techniques Help Mitigate Shrinkage?
Post-processing techniques can be a game-changer in addressing shrinkage issues in injection molded products.
Post-processing techniques such as annealing and humidity conditioning can significantly reduce shrinkage in injection molded products by relieving internal stresses and balancing moisture content.
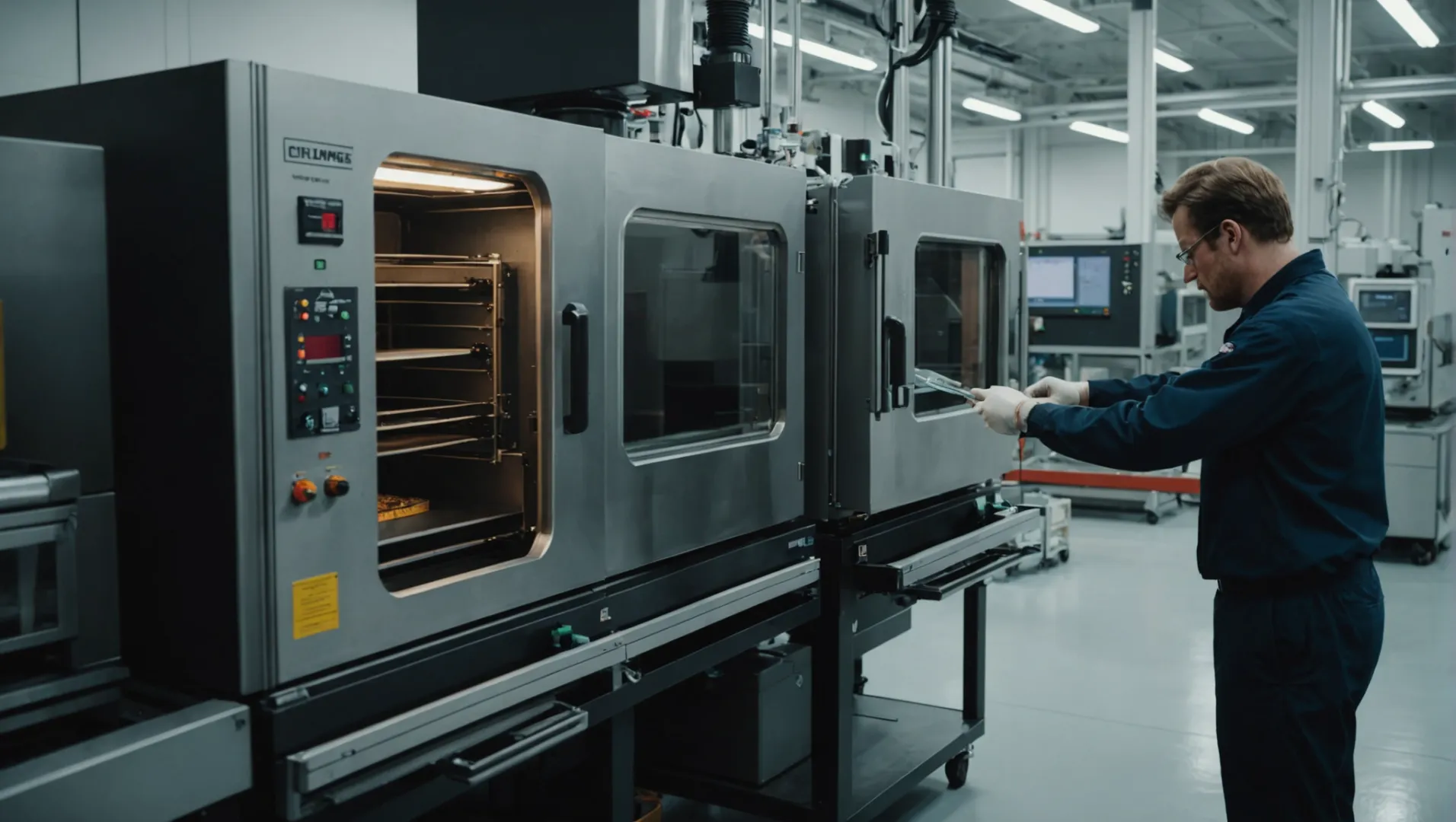
Understanding the Importance of Post-Processing
Post-processing in injection molding is crucial not just for refining the surface quality of the product but also for addressing defects like shrinkage. While other steps in the production process lay the groundwork, post-processing offers a final opportunity to enhance dimensional accuracy.
Annealing: Relieving Stress for Stability
Annealing involves heating the molded product to a specific temperature and then cooling it slowly. This process is particularly beneficial for products that have experienced significant shrinkage during initial cooling. By relieving internal stresses, annealing allows the material to stabilize, which reduces the chances of further shrinkage.
For instance, in high-performance engineering plastics, annealing can significantly improve dimensional stability, making it an indispensable step when precise measurements are crucial.
Humidity Conditioning: Balancing Moisture Content
Plastics known for their hygroscopic nature, like Nylon, often suffer from shrinkage due to moisture imbalance. Humidity conditioning treatments allow these materials to reach a balanced state of moisture content, which helps in reducing shrinkage. By exposing the products to controlled humidity levels, manufacturers can ensure uniform dimensional stability.
A real-world example would be the automotive industry, where interior components must maintain precise dimensions despite fluctuations in ambient humidity levels.
Case Study: A Comprehensive Approach
A manufacturing firm specializing in consumer electronics faced significant shrinkage issues with their casings. By implementing a dual strategy of annealing7 followed by humidity conditioning8, they managed to reduce shrinkage by 30%, improving product quality and reducing returns.
The success of this approach highlights the need for customized post-processing techniques based on the material and application requirements. By integrating these techniques into the production workflow, manufacturers can significantly enhance product integrity and performance.
Annealing reduces shrinkage in molded products.True
Annealing stabilizes materials by relieving internal stresses.
Humidity conditioning increases shrinkage in plastics.False
Humidity conditioning balances moisture, reducing shrinkage.
Conclusion
Tackling shrinkage is a multifaceted challenge. By embracing these strategies, you can enhance both the quality and precision of your products.
-
Learn about how various plastics impact injection molding outcomes.: Shrinkage in plastic materials is the dimensional change that occurs as the material cools and solidifies. This process is inherent to the nature of plastics … ↩
-
Unveil how modern cooling methods enhance mold efficiency.: For example, building several smaller cooling channels into the mold rather than one large one will provide more consistent results. ↩
-
Understand gate placement strategies to minimize shrinkage.: The location of gates will affect the orientation of polymer molecular and shrinkage of parts. The figure above shows that if a long and thin … ↩
-
Learn techniques for adjusting mold size to counteract shrinkage.: Scaling does work well. Print a cube of known size, measure it precisely, scale it by the shrinkage factor you calculated, print, measure. ↩
-
Discover how maintenance reduces dimensional inaccuracies.: Regular, careful injection mold maintenance can prevent part failures and lower the overall cost of your injection molding program. ↩
-
Learn how to set temperatures for different plastics efficiently.: Typical Settings: Mold temperatures typically range from 20°C to 120°C (68°F to 248°F), depending on the material and the complexity of the part. For instance:. ↩
-
Learn how annealing relieves stress and improves stability.: Well it’s simply a process that involves heating a specific type of plastic below its glass transition temperature in order to ease all the internal pressures … ↩
-
Discover how controlling moisture levels reduces shrinkage.: More humid areas will absorb more moisture. Colder areas may cause barrels to be lest efficient, or if someone leaves a door open you might have … ↩