Imagine stepping into a factory where every machine communicates seamlessly, optimizing production in real time. This is the new era of injection molding!
Digital transformation in injection molding involves upgrading traditional machinery to smart, interconnected systems that improve efficiency, production quality, and process optimization through real-time data analytics and automation.
But there’s so much more beneath the surface! Join me as we explore how digital tools are reshaping product design, supply chains, and quality control in this fascinating industrial evolution.
Intelligent equipment reduces downtime in injection molding.True
Intelligent systems predict maintenance needs, reducing unexpected downtimes.
What Role Does Intelligent Equipment Play in Modernizing Injection Molding?
Intelligent equipment is redefining injection molding by enhancing precision, efficiency, and integration across production processes.
Intelligent equipment modernizes injection molding by transforming traditional machines into smart systems. These systems utilize advanced sensors and networking capabilities to enable real-time data collection, process optimization, and efficient management of multi-brand machinery, ultimately improving production quality and reducing downtime.

Transforming Traditional Machines
The core of modernizing injection molding lies in upgrading conventional machines into intelligent systems. By integrating advanced sensors and controllers, these machines can monitor key parameters like temperature and pressure in real time. For instance, a temperature sensor provides continuous data that helps in adjusting the molding process to maintain quality standards. This transformation enhances process accuracy, minimizes material waste, and reduces human error.
Networking for Integration
One significant advancement is the ability to network diverse injection molding machines, breaking down technical barriers between different brands. This connectivity allows for centralized management of equipment operations. Managers can remotely access operational data, receive fault alarms, and perform timely maintenance, thus ensuring seamless operations across the production floor.
Real-Time Data Analytics
Intelligent equipment facilitates the collection of vast amounts of operational data, which is crucial for process optimization1. Big data analytics are employed to decipher this information, allowing operators to tweak process parameters for enhanced efficiency and product quality. Predictive models generated through artificial intelligence (AI) can forecast production outcomes under varying conditions, providing a strategic edge.
Enhancing Predictive Maintenance
Predictive maintenance is a game-changer in equipment reliability. Using machine learning algorithms, intelligent systems analyze operation data to predict potential failures. This foresight enables proactive maintenance scheduling, reducing unexpected downtimes and prolonging machinery lifespan.
Remote Support and Services
The advent of intelligent equipment paves the way for improved remote services. A dedicated platform can facilitate remote diagnostics and technical support, allowing technicians to resolve issues without physical intervention. This approach not only cuts service costs but also significantly boosts customer satisfaction by providing quick solutions.
Overall, intelligent equipment serves as the backbone of injection molding modernization by elevating operational efficiency, ensuring consistent product quality, and fostering an integrated production environment.
Intelligent equipment enhances injection molding precision.True
Intelligent systems use sensors for real-time monitoring, improving accuracy.
Traditional machines lack real-time data analytics capabilities.True
Conventional machines don't integrate advanced sensors for data analytics.
How Does Digital Management Enhance the Production Process?
Digital management is reshaping production lines, offering enhanced efficiency and quality through advanced technology.
Digital management streamlines production by integrating MES systems and optimizing process parameters, enhancing operational efficiency and decision-making.
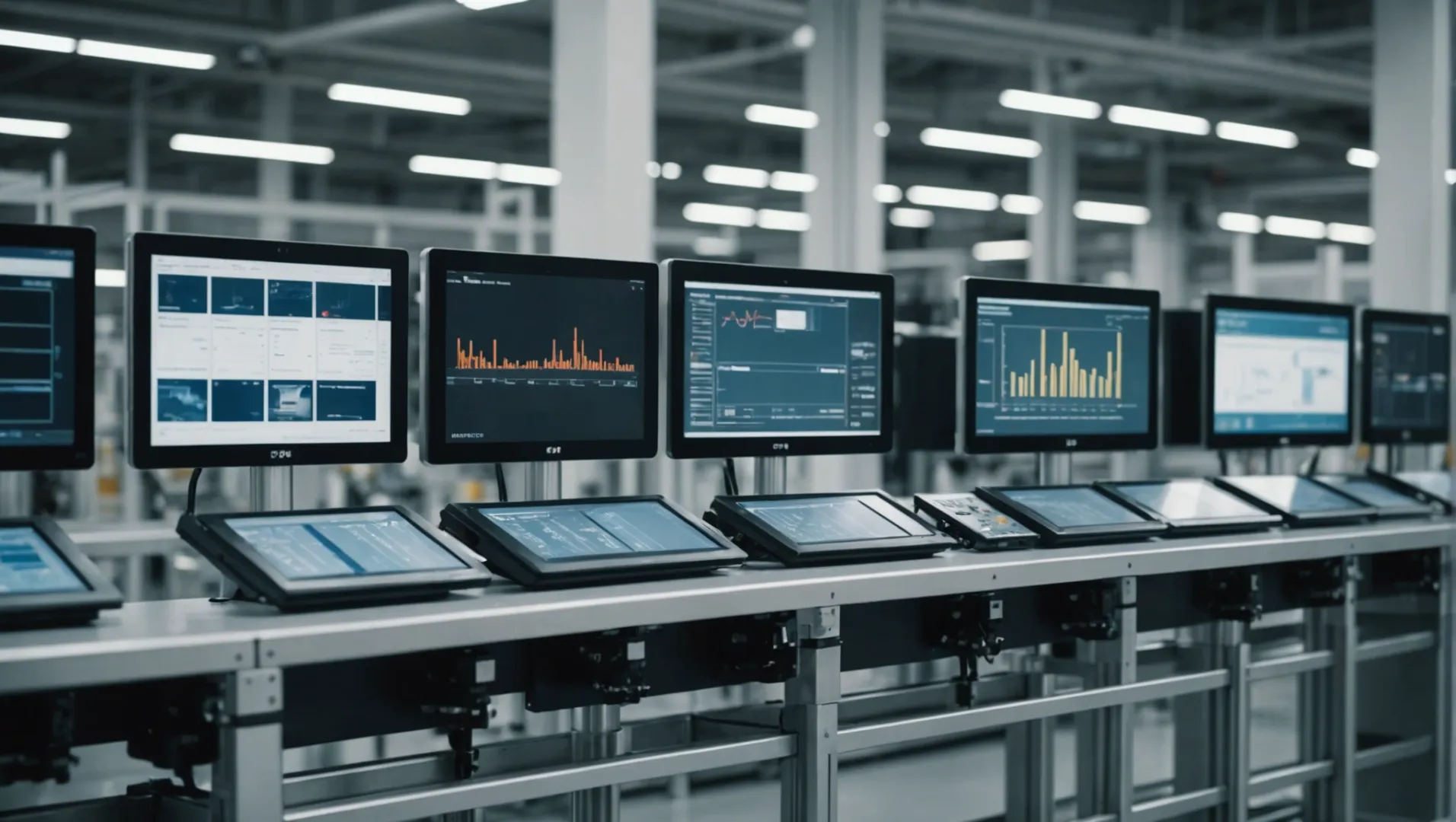
Introduction of Manufacturing Execution System (MES)
One of the cornerstones of digital management in the production process is the Manufacturing Execution System (MES)2. This system acts as a bridge between the shop floor and higher-level business systems, providing real-time data to facilitate decision-making. By integrating with machinery, MES captures live data on production status, work order progress, and quality metrics. This enables managers to make informed decisions and respond quickly to any issues that arise.
Process Parameter Optimization
Incorporating big data and AI into the production process allows for the optimization of process parameters3. By analyzing vast amounts of data, companies can identify optimal parameter combinations to enhance product quality and efficiency. This not only improves consistency but also minimizes waste and reduces costs.
For instance, companies can develop predictive models that forecast product quality based on parameter settings, enabling proactive adjustments.
Process Parameter | Traditional Approach | Digital Approach |
---|---|---|
Monitoring | Manual checks | Automated real-time data |
Adjustment | Post-production | Real-time optimization |
Analysis | Historical review | Predictive analytics |
Real-Time Production Monitoring
Digital management facilitates seamless communication across different stages of production. Through real-time monitoring systems4, operators can view dashboards that display crucial metrics like machine performance, energy consumption, and throughput rates. This transparency ensures that all team members are aligned and can react swiftly to deviations from the expected performance.
Enhanced Quality Control
Integrating digital management with quality control processes transforms how defects are detected and addressed. Advanced technologies such as visual inspections and spectral analysis provide instant feedback on product quality, reducing the incidence of defective products.
Moreover, by analyzing quality data, companies can identify root causes of defects and establish early warning systems to prevent future occurrences.
Conclusion
Digital management fundamentally changes how production processes are executed, monitored, and optimized. With systems like MES and real-time monitoring, businesses can achieve greater efficiency and quality control, setting a new standard for modern manufacturing practices.
MES systems provide real-time data in production.True
MES bridges shop floor and business systems, offering real-time data.
Digital management increases production waste.False
Digital management minimizes waste through optimized processes.
In What Ways Does Product Design Benefit from Digitalization?
In today’s fast-paced world, digitalization is reshaping product design by integrating advanced technologies and enhancing collaboration.
Digitalization streamlines product design through software simulations, collaborative platforms, and real-time data sharing, leading to faster development cycles and improved design accuracy.
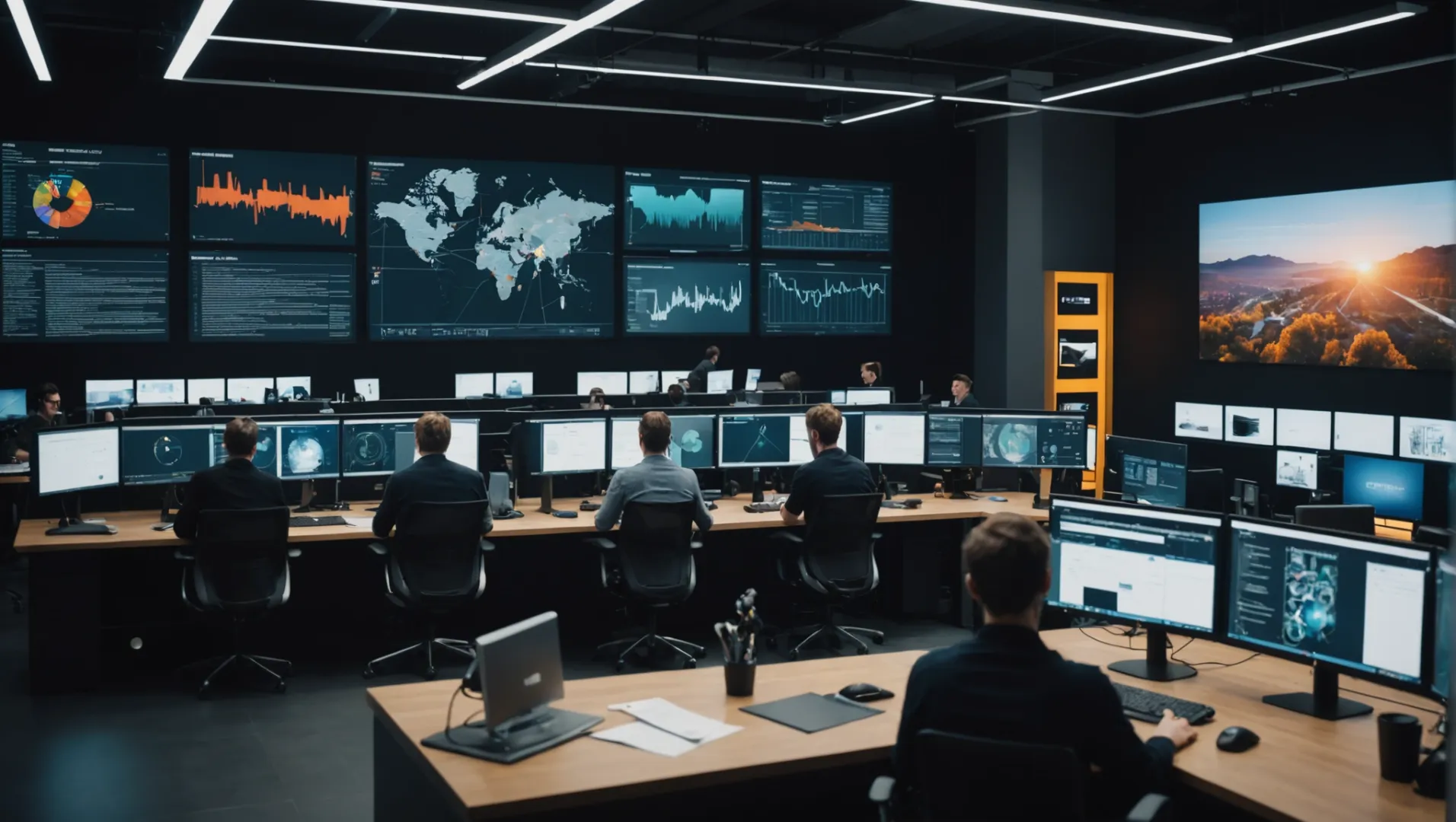
Enhancing Accuracy with Software Simulations
One of the most significant impacts of digitalization on product design is the use of software simulations, such as mold flow analysis software5. This technology allows designers to predict the flow, cooling, and other behaviors of materials in a virtual environment. By simulating the injection molding process, designers can foresee potential defects and optimize both the mold structure and manufacturing process before physical trials. This not only enhances accuracy but also significantly reduces the cost and time involved in multiple mold trials.
Collaborative Design Platforms
The integration of collaborative design platforms is another remarkable benefit brought by digitalization. These platforms enable seamless communication between designers, mold makers, and process engineers. By working on a unified platform, teams can share real-time updates, access shared resources, and promptly address design challenges as they arise. This level of collaboration not only shortens the product development cycle but also enhances innovation by leveraging diverse expertise across different domains.
Real-Time Data Sharing and Feedback
With digital tools, real-time data sharing has become integral to the product design process. Designers can access critical feedback and data from various stages of production instantly. This immediate access to information aids in making informed decisions quickly, thereby accelerating the design refinement process. Moreover, it empowers designers to test and validate concepts more efficiently, leading to higher-quality products.
Example: Automotive Industry
In the automotive industry, digitalization has transformed the way new vehicle components are designed. Engineers use virtual testing environments to simulate crash tests or aerodynamic performance, drastically reducing the need for physical prototypes. By employing these digital techniques, automakers can bring safer and more efficient vehicles to market faster than ever before.
Overall, digitalization offers a multi-faceted enhancement to product design processes, driving innovation, reducing time-to-market, and improving product quality.
Digitalization reduces time-to-market in product design.True
Digital tools streamline processes, allowing faster development cycles.
Collaborative platforms hinder innovation in design.False
They enhance innovation by leveraging diverse expertise across domains.
How Are Supply Chains Evolving with Digital Technologies?
Supply chains are rapidly transforming with digital technologies, enhancing efficiency and transparency.
Digital technologies in supply chains enable real-time tracking, improve supplier management, and optimize logistics through IoT and data analytics.
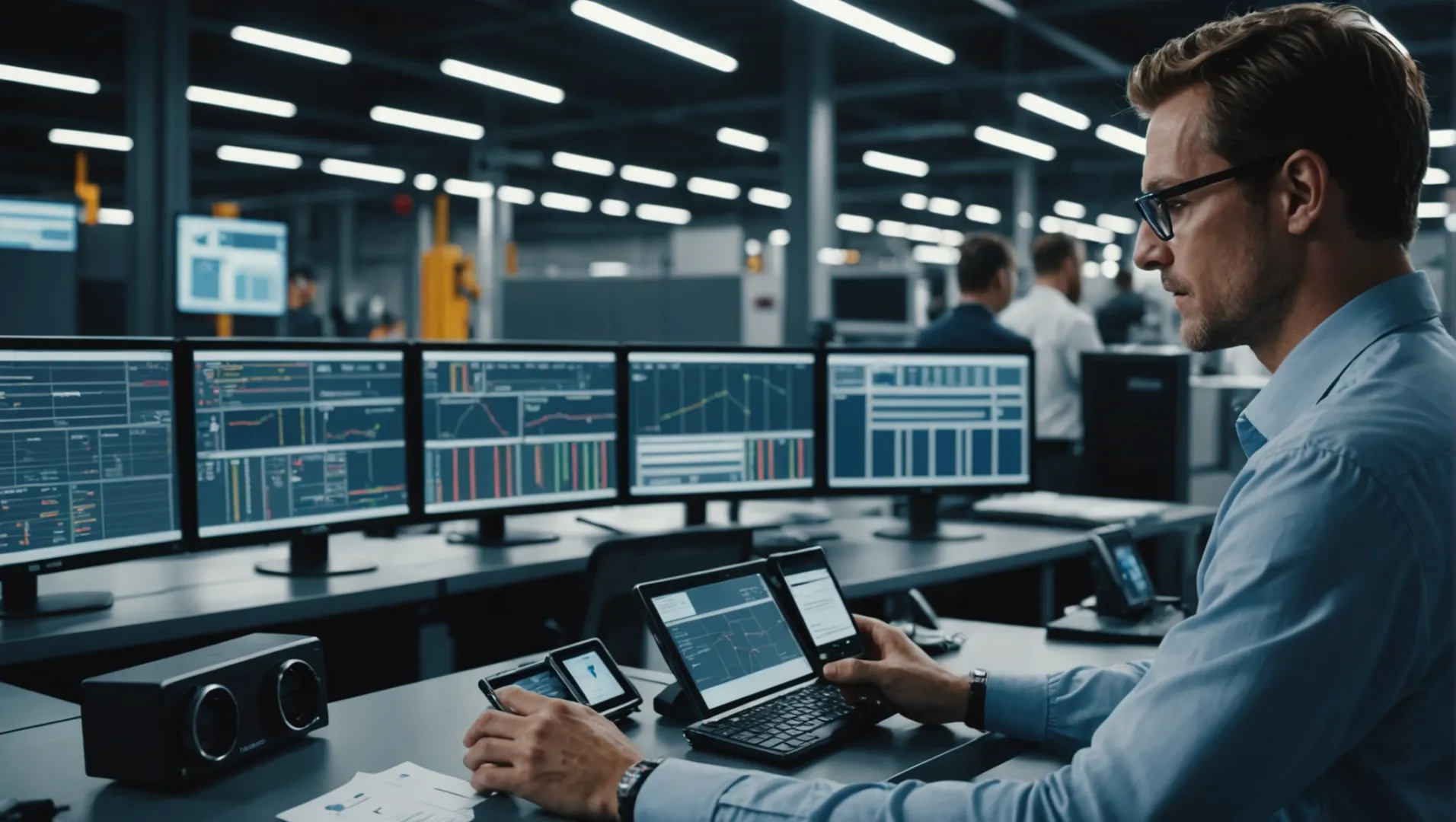
Revolutionizing Supplier Management
The integration of digital technologies into supply chain management begins with establishing a digital connection with suppliers. This digital linkage facilitates real-time sharing and communication of supplier information, allowing companies to manage and evaluate suppliers’ qualifications, product quality, and delivery times efficiently. Through these platforms, businesses can select high-quality suppliers, ensuring a stable supply of raw materials.
In addition, by leveraging digital platforms for supplier management6, companies can conduct comprehensive evaluations of supplier performance. These platforms provide a holistic view of supplier metrics, enabling more informed decision-making and fostering stronger supplier relationships.
Optimizing Logistics with IoT
The Internet of Things (IoT) plays a crucial role in enhancing logistics management by providing real-time tracking and tracing of raw materials and finished products. IoT devices monitor the condition and location of goods during transit, offering valuable insights into logistics routes and transportation methods.
For instance, by utilizing IoT-enabled logistics solutions7, companies can optimize their logistics operations, reducing costs and improving delivery efficiency. Real-time data from IoT sensors can also help in quickly responding to any potential disruptions in the supply chain, maintaining a seamless flow of goods.
Enhancing Transparency through Data Analytics
Data analytics is another transformative force in the evolution of supply chains. By collecting and analyzing vast amounts of data from various points in the supply chain, businesses gain deeper insights into every stage of their operations.
This analytical approach helps in identifying patterns and predicting potential issues before they arise. For instance, using predictive analytics in supply chains8, companies can anticipate demand fluctuations, optimize inventory levels, and make proactive decisions to mitigate risks.
Table: Benefits of Digital Technologies in Supply Chains
Digital Technology | Key Benefits |
---|---|
Supplier Management | Improved evaluation and selection processes |
IoT for Logistics | Enhanced tracking and route optimization |
Data Analytics | Predictive insights for better decision-making |
Towards Collaborative Supply Chains
The future of supply chains lies in collaboration. By implementing collaborative platforms that integrate multiple stakeholders, businesses can create a more resilient and responsive supply chain ecosystem. These platforms facilitate seamless communication and coordination across all levels, from suppliers to end consumers.
Through collaborative supply chain networks9, organizations can share resources, synchronize production schedules, and respond collectively to market changes. This collaborative approach ensures agility and strengthens the entire supply chain against disruptions.
IoT enables real-time tracking in supply chains.True
IoT devices monitor goods' location and condition during transit.
Data analytics decreases transparency in supply chains.False
Data analytics enhances insights, improving transparency across operations.
Conclusion
Digital transformation is more than a trend; it’s an essential shift. Embrace these innovations to enhance efficiency and quality in your injection molding processes.
-
Learn advanced techniques for optimizing injection molding processes effectively.: Steps to INJECTION MOLDING Process Optimization · 1. Tool functionality examination · 2. Short shot testing · 3. Gate seal studies · 4. Sample parts evaluation/ … ↩
-
Explore how MES connects shop floor operations with business systems.: A manufacturing execution system (MES) is a software application that helps businesses manage their manufacturing operations. ↩
-
Discover how AI-driven data analysis enhances production efficiency.: Find out how artificial intelligence optimizes production processes and transforms manufacturing plants into digitized powerhouses. ↩
-
Learn about systems that provide instant feedback on production metrics.: Essentially, by tracking real-time production performance, a company can improve efficiency, productivity, and quality related to both machine and process … ↩
-
Discover how mold flow analysis improves design accuracy and efficiency.: Autodesk Moldflow is used for simulating the plastic injection molding process and the plastic compression molding process. It enables engineers, analysts, and … ↩
-
Discover how digital platforms enhance supplier evaluation and selection.: Benefits of well-executed supplier management include streamlined production, improved supply chain functionality, and vertical interaction of branded products … ↩
-
Explore how IoT improves logistics efficiency through real-time tracking.: IoT logistics solutions automate goods tracking from a warehouse to a client, and vice versa, enhance customer services and communications. ↩
-
Learn how predictive analytics helps anticipate supply chain issues.: Predictive analytics for the supply chain leverages data, statistical algorithms, and machine learning techniques to identify the likelihood of … ↩
-
Understand the benefits of collaborative networks in supply chains.: 1. Supply Chain Talent and Partner Retention · 2. Lower Your Long-Term Costs · 3. Improve Product Quality and Safety · 4. Drive Better Ethical Standards Through … ↩