Exploring plastic production feels complicated, doesn’t it? Selecting the correct method seems intimidating. Understanding extrusion and injection molding is essential to turning designs into reality. These processes differ significantly.
Plastics for extrusion require low viscosity and thermal stability, enabling continuous production, while injection molding accommodates a broader range of viscosities and must handle rapid temperature changes efficiently.
Let me talk about my journey. I started learning about product design and faced this question. I struggled with melt viscosity and thermal stability. These factors had a big impact on my designs. It amazed me to see that extrusion is suitable for low-viscosity materials like polyethylene. This material works well for making things like pipes. Injection molding allowed me to use more diverse materials. It is great for complex shapes, even with higher viscosities. Both processes offer unique opportunities and challenges. They are quite like our designs.
Extrusion favors low viscosity plastics for continuous production.True
Extrusion processes typically require materials with low melt viscosity to ensure smooth, continuous flow during manufacturing.
Injection molding can use a wider range of plastic viscosities.True
Unlike extrusion, injection molding accommodates various viscosities, allowing for more versatile material choices in production.
- 1. What Factors Influence Melt Viscosity in Plastics?
- 2. How Do Thermal Stability Requirements Vary Between Processes?
- 3. How Do Shrinkage Rates Affect Product Design?
- 4. What Are the Best Materials for Toughness and Strength in Manufacturing Processes?
- 5. How Can Understanding These Differences Improve Manufacturing Efficiency?
- 6. Conclusion
What Factors Influence Melt Viscosity in Plastics?
Have you ever thought about why some plastics move smoothly while others feel thick like syrup? Knowing about melt viscosity is very important for people working with plastics. Let’s dive into the factors that determine this important quality!
Temperature, pressure, additives and molecular weight influence the flow thickness of melted plastics. Understanding these elements is very important for improving processes like extrusion and injection molding. Each factor directly impacts how easily plastics get shaped and formed.

Understanding Melt Viscosity in Plastics
Melt viscosity is a critical factor in determining how plastics behave during processing. It directly affects the ease of shaping and forming plastic materials in processes like extrusion and injection molding.
Temperature and Melt Viscosity
Temperature plays a vital role in influencing melt viscosity. As temperature increases, the viscosity of most thermoplastics decreases, allowing for better flow during processing. For instance:
Temperature (°C) | Viscosity (Pa.s) | Example Material |
---|---|---|
180 | 200 | Polyethylene (PE) |
220 | 100 | Polypropylene (PP) |
260 | 50 | Polycarbonate (PC) |
In the case of polycarbonate1, higher temperatures can significantly reduce its viscosity, facilitating smoother processing. However, excessive heating can lead to degradation, which must be carefully managed.
Pressure Effects on Melt Viscosity
Pressure also influences melt viscosity significantly. Higher pressures in the extrusion process can overcome the material’s resistance to flow, making it easier to mold complex shapes. In injection molding, increased pressure is necessary to fill molds with intricate designs effectively. For example:
- Acrylonitrile-butadiene-styrene (ABS): During injection, adjusting the pressure allows for adequate filling of the mold even with its moderate viscosity, enabling the production of detailed components such as plastic shells2.
Additives and Their Impact on Viscosity
Additives are commonly used to modify the viscosity of plastic materials. They can enhance processing performance and the final product’s properties. Some common additives include:
- Plasticizers: Reduce viscosity and increase flowability.
- Fillers: Can either increase or decrease viscosity depending on their nature and quantity.
- Stabilizers: Such as heat stabilizers for PVC that maintain viscosity during prolonged heating.
For instance, heat stabilizers3 added to polyvinyl chloride (PVC) are essential to prevent degradation during the extrusion process by enhancing its thermal stability.
Molecular Weight Considerations
The molecular weight of the polymer also plays a crucial role in melt viscosity. Higher molecular weight typically leads to increased viscosity, making the material more challenging to process. This can be critical when selecting materials for specific applications:
Polymer Type | Typical Molecular Weight | Viscosity Characteristics |
---|---|---|
Low-Density Polyethylene (LDPE) | 10,000 – 100,000 | Lower viscosity, easier to process |
High-Density Polyethylene (HDPE) | 100,000 – 1,000,000 | Higher viscosity, more challenging to process |
Polycarbonate (PC) | 20,000 – 300,000 | Moderate to high viscosity based on grade |
Adjusting molecular weight is crucial for tailoring melt viscosity to meet specific processing requirements and product performance standards.
Summary of Influencing Factors
To summarize, various factors influence melt viscosity in plastics including:
- Temperature
- Pressure
- Additives
- Molecular weight
These factors must be carefully considered during the design and manufacturing processes to ensure optimal product quality and performance in applications such as consumer electronics and other plastic components.
Higher temperatures reduce melt viscosity in thermoplastics.True
As temperature increases, the viscosity of most thermoplastics decreases, enhancing their flow during processing.
Additives always increase melt viscosity in plastics.False
Additives can modify viscosity; some reduce it (like plasticizers), while others may increase it depending on their type and quantity.
How Do Thermal Stability Requirements Vary Between Processes?
Have you ever wondered why different manufacturing processes need specific thermal stability in materials? Join us in exploring the fascinating world of extrusion and injection molding. Let’s discover these differences.
Thermal stability needs differ between extrusion and injection molding. Extrusion asks for high stability during long heating. Materials may face heat for extended periods. Injection molding needs strength against quick temperature shifts. Temperatures change fast in this process.
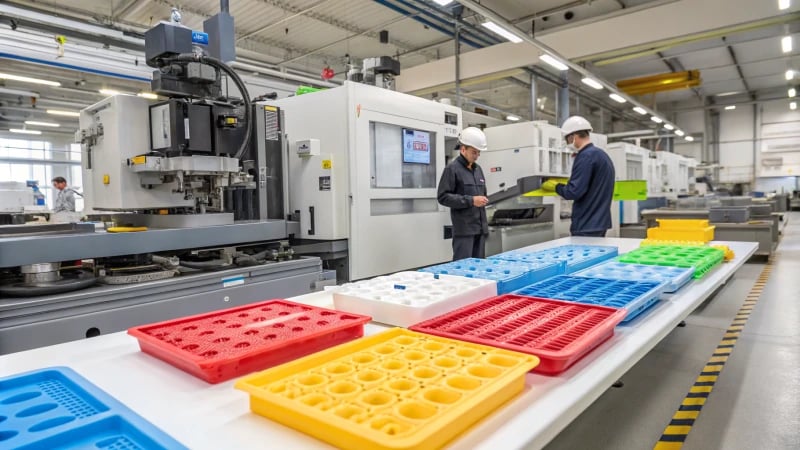
Understanding Thermal Stability in Different Molding Processes
Thermal stability is a critical factor in the processing of materials, especially plastics. The requirements for thermal stability vary significantly between extrusion molding and injection molding processes.
Thermal Stability in Extrusion Molding
In extrusion molding, the material is subjected to prolonged heating as it passes through the barrel of the extruder. Therefore, materials used in this process must demonstrate excellent thermal stability. For instance:
- Polyvinyl Chloride (PVC): This material requires the addition of heat stabilizers during extrusion to prevent degradation. The long exposure to heat can cause PVC to change color or lose its properties.
- Polyethylene (PE): Typically stable under heat, PE maintains its integrity without significant decomposition, ensuring product quality during extended processing.
The temperature profile during extrusion can be summarized as follows:
Material Type | Required Stabilizers | Decomposition Temperature | Typical Applications |
---|---|---|---|
PVC | Yes | ~140°C | Pipes, sheets |
PE | No | ~120°C | Film, containers |
Thermal Stability in Injection Molding
Conversely, injection molding involves rapid heating and cooling cycles. Materials are heated quickly to reach injection temperatures and then cooled rapidly. Hence, the thermal stability requirements differ:
- Polystyrene (PS): This material can withstand quick temperature fluctuations without quality degradation. It melts and cools quickly, making it suitable for complex shapes.
- Acrylonitrile-Butadiene-Styrene (ABS): Known for its moderate viscosity and ability to fill mold cavities efficiently, ABS maintains its properties during the fast-paced injection cycle.
The rapid temperature change can be illustrated in the following table:
Material Type | Temperature Tolerance | Cooling Time | Applications |
---|---|---|---|
PS | High | Fast | Packaging, toys |
ABS | Moderate | Moderate | Consumer products |
Key Takeaways on Thermal Stability Variations
The main differences in thermal stability requirements between extrusion and injection molding are primarily driven by the duration and nature of heat exposure. In extrusion, the focus is on maintaining properties over prolonged heating, while in injection molding, it’s essential to withstand rapid thermal changes. Understanding these variations is crucial for material selection and process optimization. For further insights on how thermal properties impact various processes, check out this detailed guide4.
By examining these factors, product designers like Jacky can better understand the implications of material choices on product performance and manufacturing efficiency.
Extrusion molding requires materials with excellent thermal stability.True
Materials used in extrusion molding must withstand prolonged heating, thus requiring high thermal stability to prevent degradation during processing.
Injection molding materials need prolonged heat exposure.False
Unlike extrusion, injection molding involves rapid heating and cooling, meaning materials do not need to endure prolonged heat exposure, which is false.
How Do Shrinkage Rates Affect Product Design?
Have you ever thought about how something as tiny as shrinkage rates affects product design? I have learned that knowing these rates is vital for keeping quality and accuracy in manufacturing methods like injection molding. Let’s explore this together!
Shrinkage rates really affect product design, especially in plastic molding. Designers must know material properties. They must also understand cooling processes. This knowledge helps optimize dimensions. It also helps maintain quality in the final product.
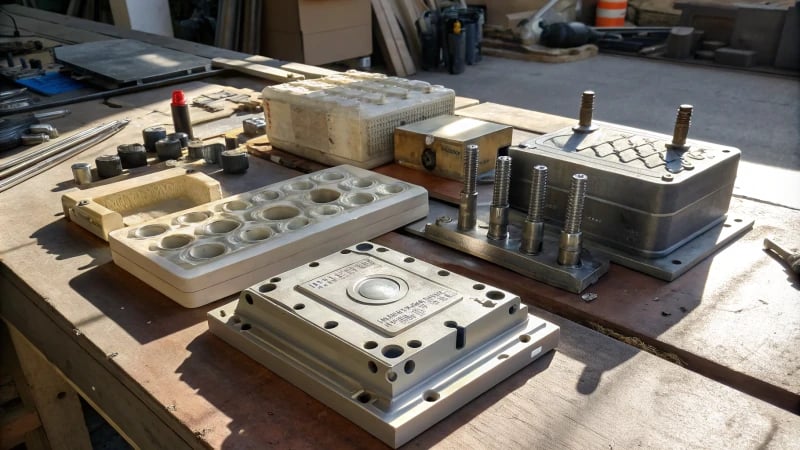
Understanding Shrinkage Rates in Product Design
Shrinkage rates are critical to consider in product design, especially when dealing with materials that undergo significant changes in dimensions during cooling. Early in my career, I faced a challenge with plastic molding. I felt humble when I saw that my carefully planned designs could change size during cooling. It’s like baking a cake; if the temperature is not perfect, the final result looks different than expected.
When designing products, it’s essential to account for the material’s behavior during cooling. In injection molding, where complex shapes are common, variations in wall thickness can lead to uneven shrinkage. For example, thicker sections may cool slower than thinner ones, potentially resulting in warping or deformation. This requires designers to carefully consider how they distribute material throughout the design, ensuring that thicker areas allow for sufficient cooling time.
The Impact of Material Selection on Shrinkage Rates
Did you know not all plastics shrink the same way? This fact surprised me. Different plastics exhibit varying shrinkage rates. Here’s a look at some common materials:
Material | Typical Shrinkage Rate | Implications on Design |
---|---|---|
High-Density Polyethylene (HDPE) | 2% – 5% | Limited adjustments needed due to consistent shrinkage rates. |
Nylon (PA) | 1% – 4% | Requires careful control of cooling parameters to minimize defects. |
Acrylonitrile Butadiene Styrene (ABS) | 0.5% – 2% | More versatile for complex shapes, but monitoring is necessary. |
Choosing the right material is like finding the perfect ingredient for a recipe. For example, HDPE usually brought good results because of its consistent shrinkage. But with Nylon, I had to be very careful in my design to get even cooling.
Optimizing Design Parameters to Account for Shrinkage
I found ways to reduce the problems from shrinkage rates using trial and error:
- Adjusting Wall Thickness: Keeping the wall thickness uniform led to even cooling and shrinkage across the part.
- Incorporating Draft Angles: This small detail really helped with mold release and cut stress on thicker areas during cooling.
- Utilizing Cooling Channels: Well-placed channels allowed me to control temperature distribution inside the mold effectively.
This information is very useful for those interested in how cooling channels impact molding5.
Conclusion: The Importance of Shrinkage Rates in Design Decisions
As I have moved through the complexities of product design, one clear truth emerged: knowing and planning for shrinkage rates is vital. My experiences taught me that smart choices about materials and design strategies lead to success in manufacturing processes.
Shrinkage rates affect product dimensions during cooling.True
Understanding shrinkage rates is vital for achieving accurate product dimensions, especially in processes like injection molding where materials change size as they cool.
All plastics have the same shrinkage rate during cooling.False
Different plastics exhibit varying shrinkage rates, impacting design strategies and material selection for optimal performance.
What Are the Best Materials for Toughness and Strength in Manufacturing Processes?
Designing products involves choosing materials with both toughness and strength. This task often feels very challenging. Truly, I understand! Which materials excel in these qualities? Let’s explore this together.
Polypropylene (PP) is very tough and strong. It is perfect for extrusion molding because of its high durability. Acrylonitrile Butadiene Styrene (ABS) has robust qualities. It is ideal for injection molding applications.
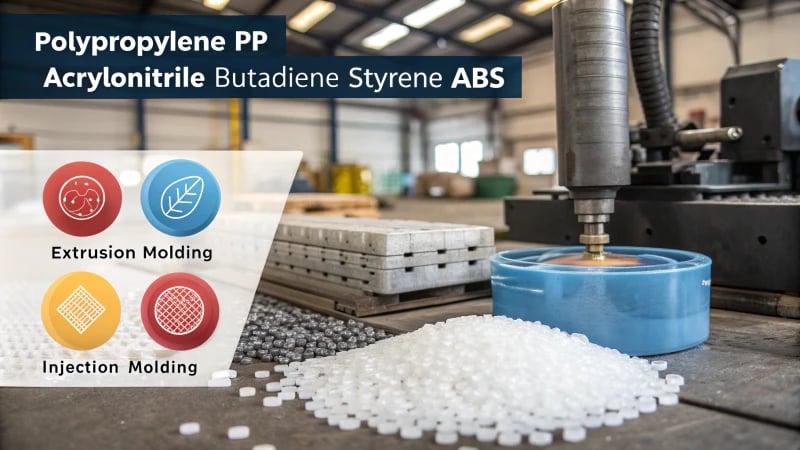
Knowing Material Toughness and Strength
I felt confused by toughness and strength in materials when I began in product design. People seemed to speak a new language. Toughness measures how much energy a material can take and bend without breaking, while strength shows the highest stress a material can handle without breaking. These properties are important for creating strong products.
Each process has its own needs, like choosing the correct tool for a task, when I think about materials for extrusion molding and injection molding.
Extrusion Molding Materials
Extrusion molding amazes because it pushes materials through a die. Materials must flow well and have low melt viscosity. I once worked on pipes using Polypropylene (PP). They had to resist water pressure and be strong during installation. Here’s a brief list of materials common in extrusion molding:
Material | Toughness | Strength | Applications |
---|---|---|---|
Polyethylene (PE) | Moderate | Moderate | Pipes, films |
Polypropylene (PP) | High | High | Rigid containers, automotive parts |
Polyvinyl Chloride (PVC) | Moderate | Moderate | Pipes, siding |
Polycarbonate (PC) | High | High | Safety glasses, electronic components |
For example, high-density polyethylene (HDPE) has very stable shrinkage. This ensures accurate dimensions. It’s crucial for long products like pipes.
Injection Molding Materials
Moving to injection molding, materials must handle quick temperature shifts and fill small mold cavities fast. Below is a table of materials good in this technique:
Material | Toughness | Strength | Applications |
---|---|---|---|
Acrylonitrile-Butadiene-Styrene (ABS) | Moderate | High | Consumer products, toys |
Polystyrene (PS) | Moderate | Moderate | Packaging, disposable cutlery |
Nylon (PA) | High | High | Gears, automotive parts |
Nylon (PA) is a favorite because it reduces defects from shrinking changes. It’s tough enough for different outside forces. This makes it great for complex shapes.
Different Needs for Toughness and Strength
Understanding needed toughness and strength varies greatly between extrusion and injection molding.
- Extrusion Molding needs strong and tough materials in a straight line. Picture materials that resist tension without breaking; materials like PP help here.
- Injection Molding needs overall toughness and strength as products face forces from all directions. I watched ABS handle impacts while keeping its shape strong; it is truly impressive!
Knowing these different material properties greatly affects design and performance. I often suggest designers explore related topics like material properties6, toughness vs strength7, and extrusion vs injection molding8. So much to learn!
Polypropylene (PP) has high toughness and strength for extrusion.True
Polypropylene (PP) is known for its high toughness and strength, making it suitable for demanding applications in extrusion molding.
Nylon (PA) is the best choice for injection molding materials.True
Nylon (PA) offers high toughness and strength, making it ideal for complex shapes in injection molding processes.
How Can Understanding These Differences Improve Manufacturing Efficiency?
Do you know the excitement when your manufacturing process works perfectly? Success depends on understanding the small differences between processes. This knowledge changes efficiency greatly. It transforms operations.
Manufacturers choose the right processes and materials by understanding melt viscosity, thermal stability, shrinkage rates and material toughness. This knowledge very directly improves production efficiency. It really helps you produce high-quality products. You avoid unnecessary problems.
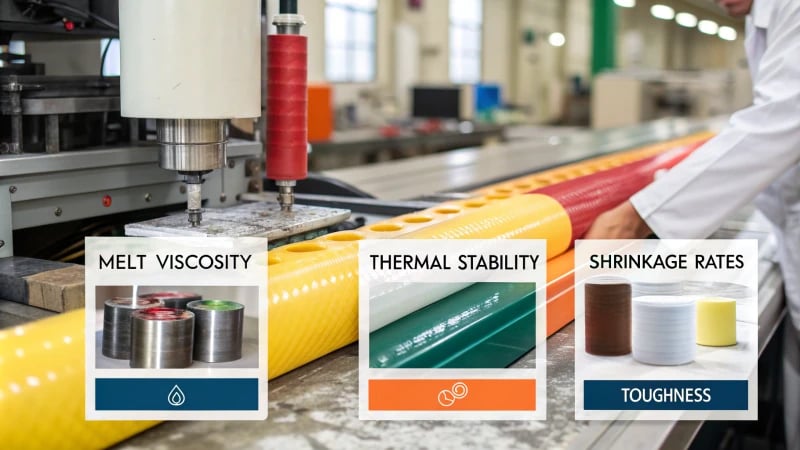
Understanding Melt Viscosity for Improved Efficiency
Melt viscosity plays a critical role in both extrusion and injection molding processes. In extrusion molding, low viscosity is essential for continuous production, allowing materials like polyethylene (PE)9 to flow smoothly through the die.
High-viscosity materials may require specialized screw designs to enhance flow.
In contrast, injection molding can accommodate slightly higher viscosities due to its ability to apply high pressure.
For instance, Acrylonitrile-Butadiene-Styrene (ABS) can be effectively injected by adjusting temperatures and pressures, thus enabling the production of complex shapes.
Process Type | Suitable Viscosity Range | Material Examples |
---|---|---|
Extrusion Molding | Low Viscosity | PE, PP |
Injection Molding | Moderate to High Viscosity | ABS |
Thermal Stability and Manufacturing Process
Thermal stability is paramount for maintaining product quality in manufacturing.
For extrusion molding, materials need good thermal stability to withstand prolonged heating without degradation. For example, polyvinyl chloride (PVC)10 often requires heat stabilizers to avoid quality issues during continuous processing.
Conversely, injection molding deals with rapid temperature changes, making materials like Polystyrene (PS) ideal due to their ability to quickly adapt without significant quality loss.
Process Type | Thermal Stability Requirement | Material Examples |
---|---|---|
Extrusion Molding | High Thermal Stability | PVC (with stabilizers) |
Injection Molding | Rapid Temperature Adaptation | PS |
Addressing Shrinkage Rates in Production
Understanding shrinkage rates during cooling can significantly affect product quality.
Extrusion molding generally yields stable shapes due to uniform cooling, exemplified by high-density polyethylene (HDPE) pipes which maintain dimensional accuracy.
In contrast, injection molded products often exhibit varying wall thicknesses, requiring materials like Nylon (PA) that can tolerate differences in shrinkage rates.
Adjusting parameters like holding time during injection can help mitigate defects caused by these differences.
Process Type | Shrinkage Characteristics | Material Examples |
---|---|---|
Extrusion Molding | Stable Shrinkage | HDPE |
Injection Molding | Variable Shrinkage | PA |
Importance of Material Toughness and Strength
Material toughness and strength are crucial for ensuring the durability of manufactured products.
In extrusion molding, products like PP-R pipes must withstand water pressure; therefore, they require materials with strong longitudinal properties.
For injection molded items, such as toys, comprehensive toughness is necessary to endure multi-directional forces during use.
Choosing materials that meet these specific requirements can enhance product longevity and reduce failures during operational use.
Process Type | Strength Requirement | Material Examples | |
---|---|---|---|
Extrusion Molding | Longitudinal Strength | PP-R | |
Injection Molding | All-round Toughness | Various Plastics for Toys | \ |
Low viscosity is essential for extrusion molding efficiency.True
Extrusion molding requires low viscosity materials like PE for smooth flow and continuous production, enhancing manufacturing efficiency.
Injection molding can only use low-viscosity materials.False
Injection molding accommodates moderate to high-viscosity materials, allowing for complex shapes and efficient production processes.
Conclusion
Explore the differences between extrusion and injection molding in plastics manufacturing, including melt viscosity, thermal stability, shrinkage rates, and material toughness for optimized design and production.
-
Explore detailed insights into how temperature affects melt viscosity for various plastics. This can enhance your understanding of processing conditions. ↩
-
Learn how pressure influences melt viscosity and its implications for extrusion and injection molding processes. Valuable for improving manufacturing outcomes. ↩
-
Discover how different additives can modify melt viscosity in plastics, improving their processing characteristics and end-use properties. ↩
-
This link provides an in-depth understanding of thermal stability concepts essential for various applications. ↩
-
Explore insights on managing shrinkage rates to enhance your product designs effectively. ↩
-
Explore comprehensive resources on material toughness to enhance your design choices. ↩
-
Gain insights into the differences between strength and toughness for better material selection. ↩
-
Learn more about the advantages of extrusion versus injection molding processes. ↩
-
This link will provide deeper insights into the impact of viscosity on manufacturing processes, crucial for enhancing efficiency. ↩
-
Explore this resource to understand the importance of thermal stability in manufacturing and how it can improve product quality. ↩