Ever wondered how the intricate parts of your gadgets come to life?
Die casting uses metals like aluminum and zinc, while injection moulding relies on polymers. These processes differ in temperature, pressure, mould design, and the final product’s characteristics.
Back when I was knee-deep in my first major project, I realized the importance of choosing the right manufacturing process. The nuances between die casting and injection moulding aren’t just technical details; they can shape everything from material costs to product durability. Let’s delve into how these differences matter.
Die casting uses metals, not polymers.True
Die casting involves the use of metal materials, unlike injection moulding, which uses polymers.
Injection moulding requires higher temperatures than die casting.False
Injection moulding typically uses lower temperatures compared to die casting, which melts metals.
- 1. What Materials Are Used in Die Casting and Injection Moulding?
- 2. How Do Temperature and Pressure Affect Each Process?
- 3. What Are the Design Considerations for Moulds in Each Process?
- 4. How Do Product Characteristics Differ Between Die Casting and Injection Moulding?
- 5. Which Manufacturing Process is More Cost-Effective?
- 6. Conclusion
What Materials Are Used in Die Casting and Injection Moulding?
Ever held a shiny new gadget and wondered about the magic materials behind its creation?
Die casting uses non-ferrous metals like zinc and aluminum; injection moulding employs thermoplastics like polyethylene, chosen for their fluidity and suitability for product requirements.
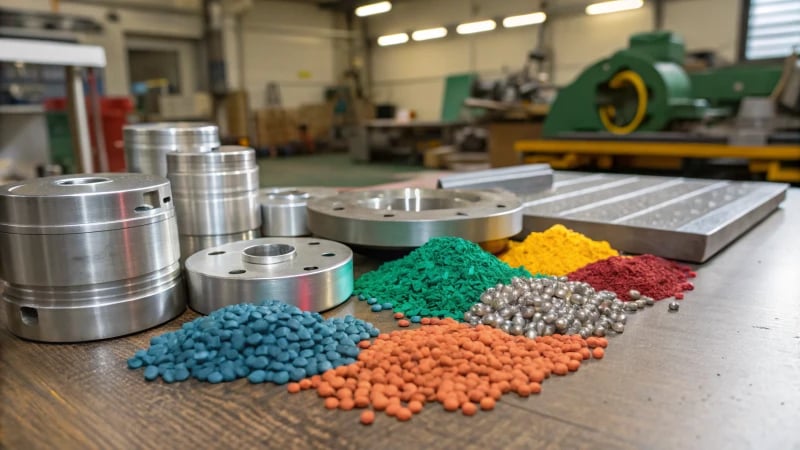
Die Casting Materials
When I first dove into the world of die casting1, I was amazed at how non-ferrous metals transform under high temperatures. Metals like zinc, aluminium, magnesium, and copper-based alloys are the stars here, thanks to their incredible fluidity when molten. Imagine trying to fill a mold with cake batter—it needs to flow smoothly to get all those details just right. These metals do exactly that in die casting, ensuring precision and strength in the final product.
Material | Properties |
---|---|
Zinc | High ductility, good impact strength |
Aluminium | Lightweight, corrosion-resistant |
Magnesium | Lightest structural metal, good strength-to-weight ratio |
Copper Alloys | Excellent thermal and electrical conductivity |
Each metal has its unique charm, making them perfect for everything from car parts to sleek electronics.
Injection Moulding Materials
On the flip side, injection moulding2 opens up a whole new realm with thermoplastics and thermosetting polymers. I remember the first time I realized how versatile these materials are—like discovering a new set of tools for an artist. Thermoplastics such as polyethylene, polypropylene, and ABS can be melted over and over again, offering recyclability that’s music to a designer’s ears. In contrast, thermosetting plastics become rock-solid after curing, providing unmatched stability.
Type | Common Examples | Characteristics |
---|---|---|
Thermoplastics | Polyethylene, ABS | Recyclable, versatile in shapes |
Thermosetting Plastics | Epoxy, Phenolics | Heat-resistant, durable after curing |
The choice between these materials often feels like picking the right spices for a dish—it all depends on what you want to achieve: flexibility, durability, or heat resistance.
Comparing Material Attributes
I often think about how crucial understanding these material differences is for designers like Jacky, who rely on precision and efficiency. Here’s a quick comparison:
- Temperature Tolerance: Metals in die casting endure higher temperatures than plastics in injection moulding.
- Reusability: Thermoplastics can be reused unlike thermosetting plastics.
- Dimensional Accuracy: Die-cast metals typically offer better dimensional accuracy than plastics.
For designers aiming to optimize production3, balancing cost, strength, and design complexity is key. While die casting ensures robust components, injection moulding excels at creating intricate shapes with smooth finishes—each process plays a vital role in today’s manufacturing landscape.
Zinc is a ferrous metal used in die casting.False
Zinc is a non-ferrous metal, commonly used for its ductility and impact strength.
Thermoplastics can be re-melted and reshaped.True
Thermoplastics like polyethylene can be melted multiple times, allowing recycling.
How Do Temperature and Pressure Affect Each Process?
Ever wondered how the invisible forces of temperature and pressure shape the world around us?
Temperature and pressure are crucial in processes like die casting and injection molding, where high temperatures melt materials and pressure shapes them. Mastering these conditions ensures optimal manufacturing outcomes.

The Role of Temperature and Pressure in Manufacturing
I remember when I first stepped into a manufacturing facility, the air filled with a tangible hum of machinery, and I was awestruck by how everything relied on such precise conditions. Temperature and pressure are the unsung heroes, especially in processes like die casting and injection moulding, where precision is king.
Die Casting
- Raw Materials: Non-ferrous metals like aluminium and zinc.
- Temperature: Requires temperatures soaring to over a thousand degrees Celsius to melt metals.
- Pressure: High injection pressure ranging from tens to hundreds of megapascals.
It’s like watching a well-rehearsed ballet, where each element must perform perfectly to create automotive engines or those sleek aluminium alloy wheels4.
Injection Moulding
- Raw Materials: Uses thermoplastics.
- Temperature: Set between 150-300°C.
- Pressure: Ranges from 50-200 MPa.
This process is an artist’s dream, ideal for crafting intricate designs used in consumer electronics5 and packaging.
Process | Material | Temperature (°C) | Pressure (MPa) |
---|---|---|---|
Die Casting | Metal | 1000+ | 100 – 200+ |
Injection Moulding | Plastic | 150 – 300 | 50 – 200 |
Impact on Chemical Reactions
Remember that high school chemistry experiment where we watched reactions speed up with a bit of heat? That’s temperature at work! It provides kinetic energy to molecules, cranking up reaction rates. Pressure changes can be game-changers in reactions involving gases, as Le Chatelier’s principle beautifully illustrates. For example, increasing pressure can tip the scales towards fewer gaseous products, altering yields in processes like ammonia synthesis involving gaseous reactants6.
Temperature and Pressure in Physics
And let’s not forget about physics, where temperature and pressure influence phase changes. Higher pressures can push a liquid’s boiling point up—a concept that’s crucial in geothermal energy extraction. Here, pressure dictates how steam and water behave underground—a fascinating dance of elements that reminds me of our interconnected world. This principle is crucial in understanding phenomena like geothermal energy7 extraction.
Understanding this dynamic duo—temperature and pressure—across various domains empowers us to tweak and optimize processes, boosting efficiency and quality. Whether it’s manufacturing marvels or unlocking energy potential, their impact is profound and far-reaching.
Die casting requires temperatures over 1000°C.True
Die casting melts metals like aluminium, needing high temperatures.
Injection moulding uses pressures above 300 MPa.False
Typical pressures for injection moulding range from 50-200 MPa.
What Are the Design Considerations for Moulds in Each Process?
Have you ever wondered why designing molds feels like solving a complex puzzle? Each process demands unique considerations.
Mould designs vary by process: die casting uses high-strength steel for heat and pressure endurance, while injection moulding prioritizes efficient material flow and cooling, enhancing each method’s effectiveness.
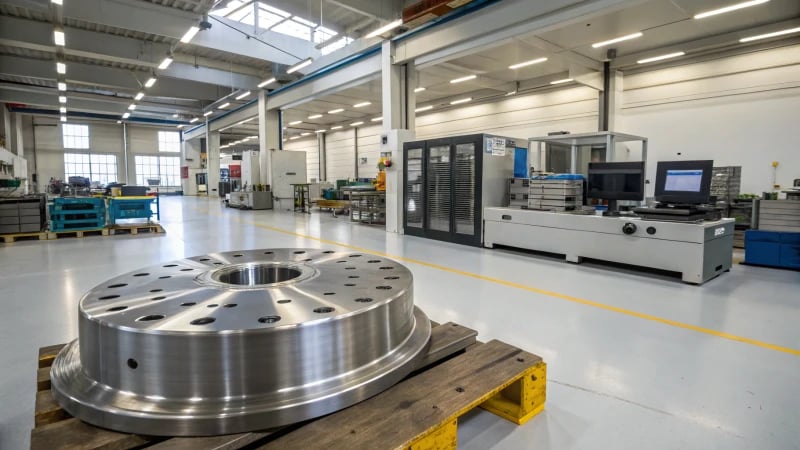
Material and Temperature Considerations
When I first delved into mold design, I was amazed at how much the choice of materials could make or break a project. For die casting, using high-strength steel is non-negotiable because it must resist the high temperatures8 and pressures typical of metals like aluminum or zinc. I remember a time when a colleague used an inappropriate material, and we ended up with warped products—an expensive mistake that taught us the value of the right materials.
In contrast, injection moulding deals with lower temperatures, typically between 150-300°C for thermoplastics, so materials like steel, aluminum, or even specialized plastics can be used. Cooling channels are another key factor; they ensure quick solidification of plastics, which is crucial for keeping production efficient. I’ve spent countless hours tweaking these channels to reduce cycle times without compromising product quality.
Structural Requirements
The structural complexity in die casting molds can be daunting. Managing the flow of molten metal requires intricate components like runners and gates. I once had to redesign an entire section of a mold because the metal wasn’t flowing smoothly, which really drove home how vital these elements are.
For injection moulds, it’s all about optimizing the plastic flow9 and ensuring that finished products eject cleanly. The dynamics of plastic flow can be tricky; I’ve had designs that worked perfectly in theory but needed serious tweaking in practice.
Product Characteristics Impact
The end product dictates so much of the mould design process. For die-cast items, which require high mechanical strength and precision, I’ve often worked on automotive components where every micron counts.
On the flip side, injection-moulded items excel in detailed designs with thin walls, perfect for consumer electronics. The satisfaction I feel when a complex, internally structured piece comes out perfectly is hard to beat.
Process-Specific Design Elements
Each process requires unique design considerations:
Process | Key Design Element |
---|---|
Die Casting | High-temperature resistance materials |
Injection Moulding | Cooling channels for rapid solidification |
These elements are not just technical details—they’re the heart of what makes each process efficient and cost-effective. A deep understanding of these differences is crucial for making informed mould design10 decisions, ultimately shaping the success of manufacturing projects. Every design challenge is an opportunity to apply lessons learned from past experiences.
Die casting moulds must withstand temperatures above 500°C.True
Die casting involves molten metals requiring moulds to endure high heat.
Injection moulding uses cooling channels for slow solidification.False
Cooling channels in injection moulding ensure rapid solidification of plastics.
How Do Product Characteristics Differ Between Die Casting and Injection Moulding?
Choosing between die casting and injection moulding can feel like picking the perfect tool from a crowded shed. Each process has its unique strengths, depending on what you’re aiming to create.
Die casting produces strong, precise parts for complex designs; injection moulding is ideal for detailed, thin-walled components. Each method’s suitability depends on specific product characteristics and applications.
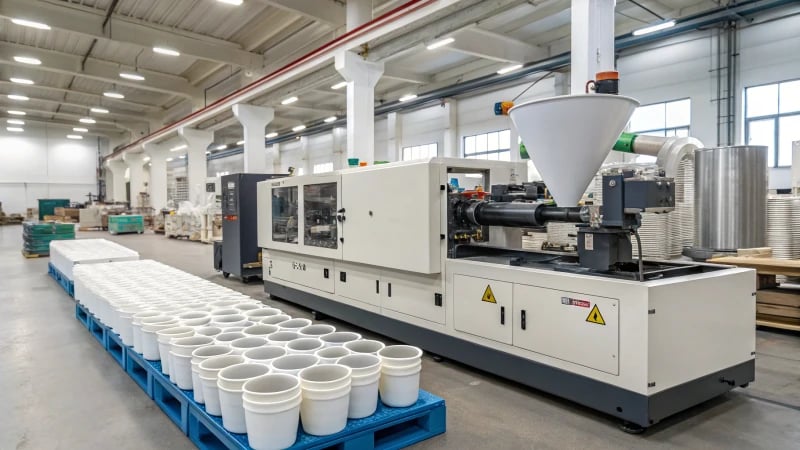
Material Differences Impacting Product Characteristics
Imagine you’re crafting something as intricate as a puzzle piece. With die casting11, the choice of non-ferrous metals like zinc and aluminium means your creation will boast high mechanical strength and dimensional accuracy. These metals are like the steadfast guardians of the automotive world, providing the muscle behind car parts that need to stand up to the elements.
On the flip side, injection moulding is your go-to for flexibility. It uses thermoplastics and thermosetting polymers, materials that transform like chameleons under the right conditions. This makes them perfect for a variety of shapes and reusable designs, ideal for consumer electronics.
Characteristic | Die Casting | Injection Moulding |
---|---|---|
Material | Non-ferrous metals (e.g., aluminium) | Thermoplastics (e.g., polyethylene) |
Strength | High | Moderate to high |
Process Conditions and Their Effects
In my experience, the process conditions can dramatically alter the outcome of your project. With die casting, you’re dealing with metal liquefied by fiery temperatures over 1000°C and injected with pressures akin to a volcano’s eruption. This results in robust products with enviably smooth finishes—ideal when you want that extra polish.
Injection moulding, however, operates at a gentler temperature range of 150-300°C. The lower pressure here makes it the superhero for producing thin-walled12 components—think sleek gadget casings that fit perfectly in your hand.
Mould Design: Complexity vs. Versatility
Mould design is where these processes really part ways. In die casting, moulds are crafted from resilient high-strength steel to brave the heat and pressure, featuring intricate gateways for seamless metal flow. This is like crafting a fortress capable of withstanding any siege.
Meanwhile, injection mould moulds may not need such a fortress approach. They’re often made from materials like aluminium with cooling channels to quickly solidify plastics. It’s all about speed and versatility here, allowing rapid production cycles without sacrificing detail.
In essence, choosing between these methods is about understanding what you need most: the unyielding strength and precision of die casting or the adaptable versatility of injection moulding. Your decision hinges on what you’re building—a durable component or a flexible design marvel. Dive deeper into how these manufacturing processes13 can be optimized for various industrial applications by exploring their core differences.
Die casting uses non-ferrous metals like aluminium.True
Die casting predominantly uses non-ferrous metals such as aluminium and zinc.
Injection moulding operates at temperatures over 1000°C.False
Injection moulding operates at lower temperatures, typically between 150-300°C.
Which Manufacturing Process is More Cost-Effective?
Hey there! Ever found yourself tangled in the web of manufacturing choices? Well, let’s dive into the die casting and injection molding maze together and figure out which one really saves those precious dollars.
Die casting is cost-effective for metal parts, while injection molding suits plastic products. The best choice depends on materials, production volume, and specific project needs.
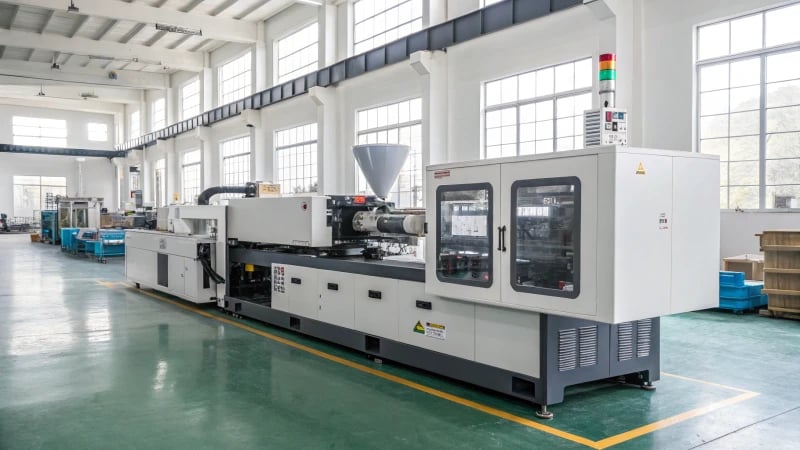
Raw Material Considerations
Choosing the right raw materials is like picking the right ingredients for a recipe—each affects the final outcome and cost. In my experience, die casting often involves using non-ferrous metals like zinc or aluminum. These metals remind me of those rare spices I once tried in a new recipe—expensive but adding a unique flavor. This method suits high-temperature processes and is worth considering if your product demands strength and precision.
On the flip side, injection molding uses thermoplastics and polymers, similar to the everyday ingredients in my kitchen that offer versatility without breaking the bank. It’s a great choice if you’re focusing on design flexibility and cost savings.
Material Type | Die Casting | Injection Molding |
---|---|---|
Examples | Zinc, Aluminum | Polyethylene, ABS |
Cost Implications | Higher material cost | Lower material cost |
Reusability | Limited due to single-use molds | High with thermoplastics |
Process Temperatures and Pressures
Reflecting on my journey, each manufacturing process feels like its own adventure with unique challenges. Die casting operates at high temperatures14 and pressures, demanding robust equipment that’s akin to gearing up for a tough hike—it requires preparation but pays off with strength and durability.
In contrast, injection molding is more like a casual walk in the park, with lower temperatures and pressures making it energy-efficient and easier to manage.
Mould Characteristics
From my personal trials, I’ve learned that moulds are like the backbone of any process. Die casting moulds are sturdy and complex, much like those heavy-duty tools I once invested in—they come with a high upfront cost but offer longevity for large-scale production.
Meanwhile, injection molding moulds are simpler, reminiscent of those nifty gadgets that are less expensive yet highly effective for varied applications.
Mould Type | Die Casting | Injection Molding |
---|---|---|
Initial Cost | High due to material strength requirements | Lower due to simplicity |
Durability | High, suitable for mass production | Moderate, may wear faster |
Product Characteristics
Reflecting on past projects, selecting the right method boils down to understanding your product’s needs. Die casting works wonders for parts requiring high strength and precision—think of those moments when you need a solid foundation.
On the other hand, injection molding shines in versatility and detail—a go-to for intricate designs akin to crafting a delicate sculpture.
Evaluating product strength15 requirements will help you choose the right path for your unique project challenges. Each factor plays a crucial role in determining whether die casting or injection molding will offer the most cost-effective solution for your needs.
Die casting uses higher temperatures than injection molding.True
Die casting operates at high temperatures, unlike injection molding.
Injection molding is more energy-efficient than die casting.True
Injection molding requires lower temperatures, reducing energy use.
Conclusion
Die casting and injection moulding are distinct manufacturing processes differing in materials, temperatures, pressures, and product characteristics, impacting design choices for strength and complexity.
-
Learn more about how die casting works and why it’s favored for producing metal components. ↩
-
Discover the fundamentals of injection moulding and its applications in various industries. ↩
-
Explore strategies to enhance production efficiency by choosing the right materials for your project. ↩
-
Exploring this link reveals the intricate process of crafting high-strength wheels through die casting. ↩
-
This link provides insights into how injection moulding shapes the world of consumer electronics. ↩
-
Learn how pressure changes can shift chemical equilibria involving gases. ↩
-
Discover how temperature and pressure affect geothermal energy extraction. ↩
-
Explore materials suitable for handling extreme temperatures in die casting. ↩
-
Understand how plastic flow dynamics affect injection mould design. ↩
-
Learn about best practices in mould design across different processes. ↩
-
Learn about die casting fundamentals, which enhance understanding of its strengths and applications. ↩
-
Find out how injection moulding efficiently produces thin-walled components with detailed designs. ↩
-
Explore comparative studies on optimizing these processes for different industrial uses. ↩
-
Understanding why die casting demands high temperatures can offer insights into its operational costs. ↩
-
Exploring the strength advantages of die-cast products aids in evaluating their suitability for specific applications. ↩