DEVELOPMENT
blog & article
read our latest newsletter
Whether you’re curious about material selection, product design, mold design, mold making and injection molding, feel free to ask us anything. Our team is ready to provide the guidance and insights you need.
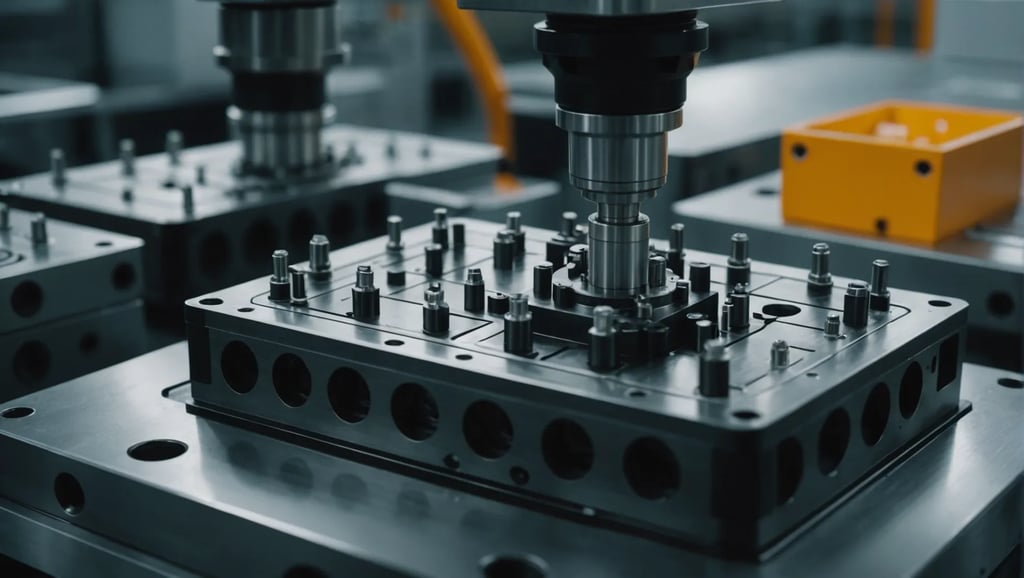
How Can You Enhance the Durability of Injection Molds in High Temperature Environments?
Injection molds play a crucial role in manufacturing, especially when subjected to high temperatures. By choosing the right materials, optimizing design, ensuring precision machining, and adhering to maintenance practices, manufacturers can significantly enhance mold durability. This article explores practical strategies ...
DEVELOPMENT
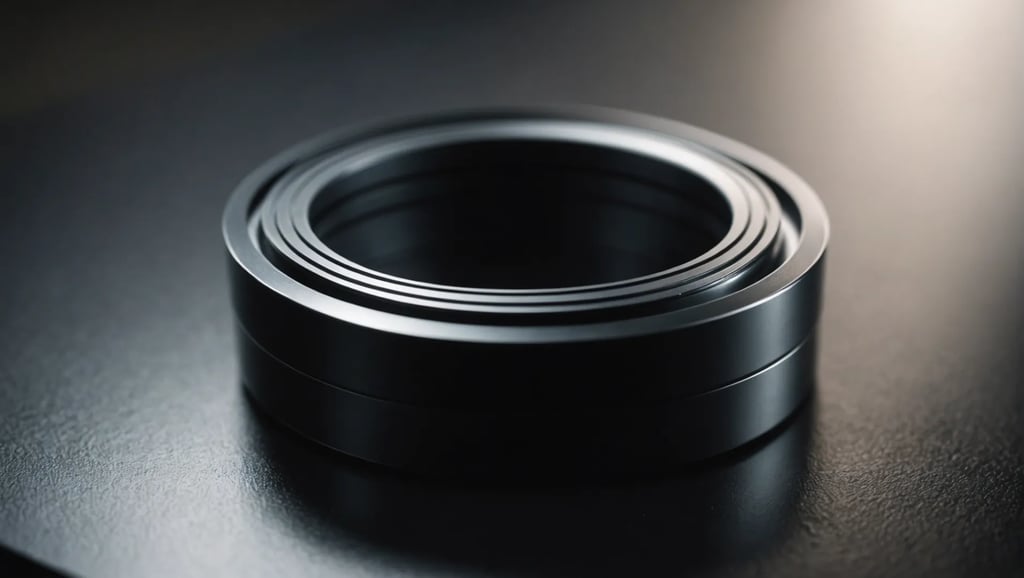
How Can You Enhance the Surface Gloss of Injection Molded Products?
Achieving a glossy finish on injection molded products is not just about aesthetics; it’s about making a statement in quality. In this article, I explore essential strategies from material selection to advanced techniques that can elevate the visual appeal of ...
DEVELOPMENT
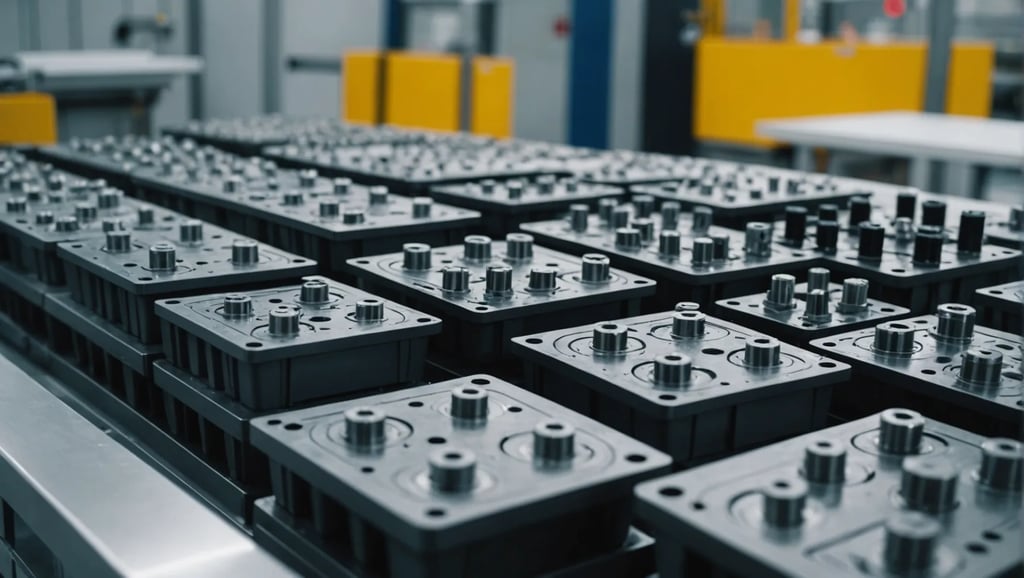
How Can You Improve the Precision of Injection Molds?
Achieving precision in injection molding is paramount for producing high-quality, consistent products in manufacturing. This guide explores effective strategies, technologies, and insights that can elevate your molding process, from temperature control to advanced software applications. Dive in to discover actionable ...
DEVELOPMENT
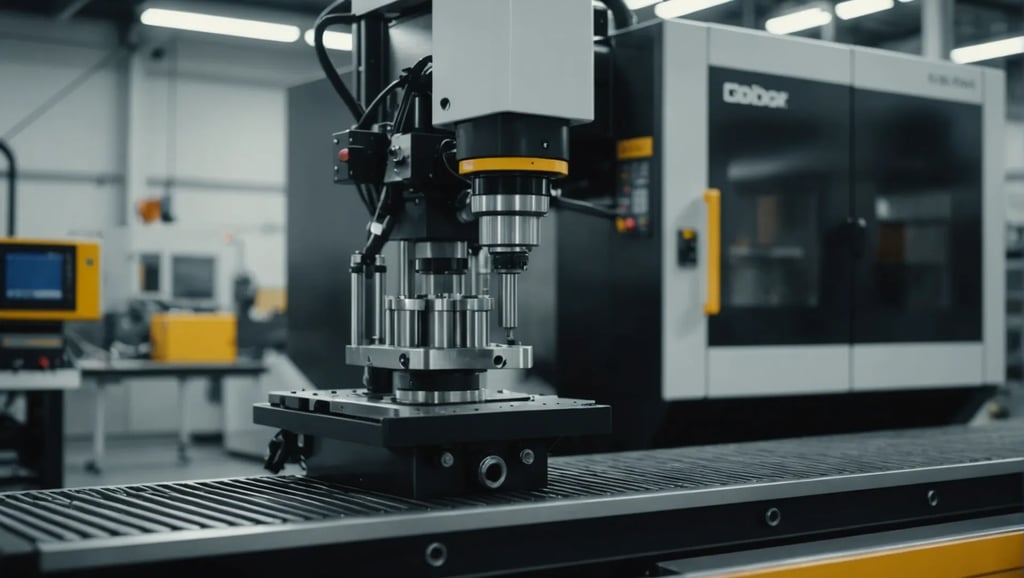
How Can You Optimize an Injection Mold Exhaust System?
In the world of injection molding, a well-optimized exhaust system is not just important—it's essential for producing high-quality products. From designing effective exhaust grooves to selecting the right materials and maintaining your equipment, there are several strategies to enhance your ...
DEVELOPMENT
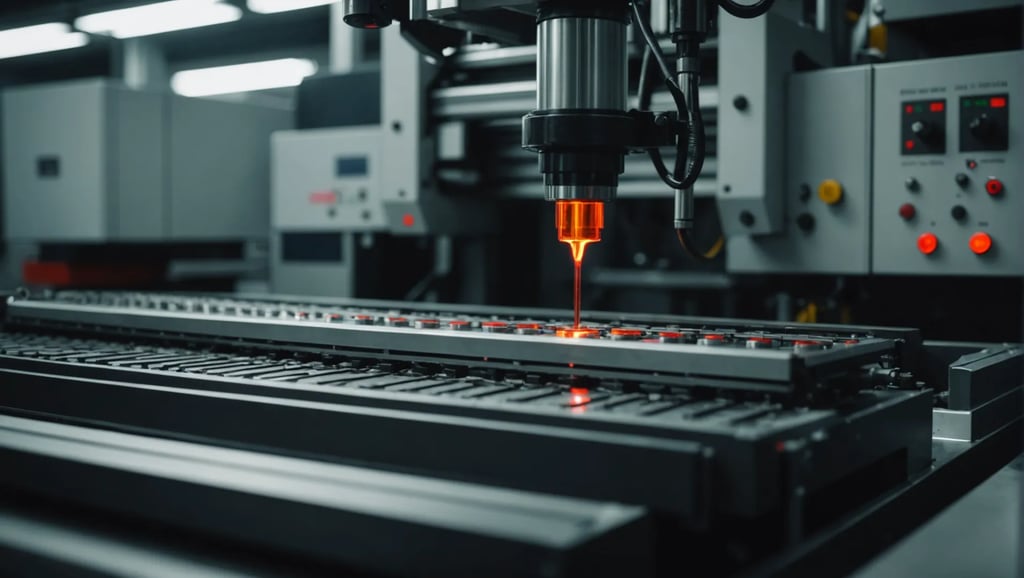
What Are the Challenges and Solutions for Injection Molding in High Temperature Environments?
Navigating the complexities of injection molding in high temperature environments can be daunting. The challenges include changes in material properties, mold design issues, and increased demands on equipment. However, with strategic planning and innovative solutions, manufacturers can maintain efficiency and ...
DEVELOPMENT
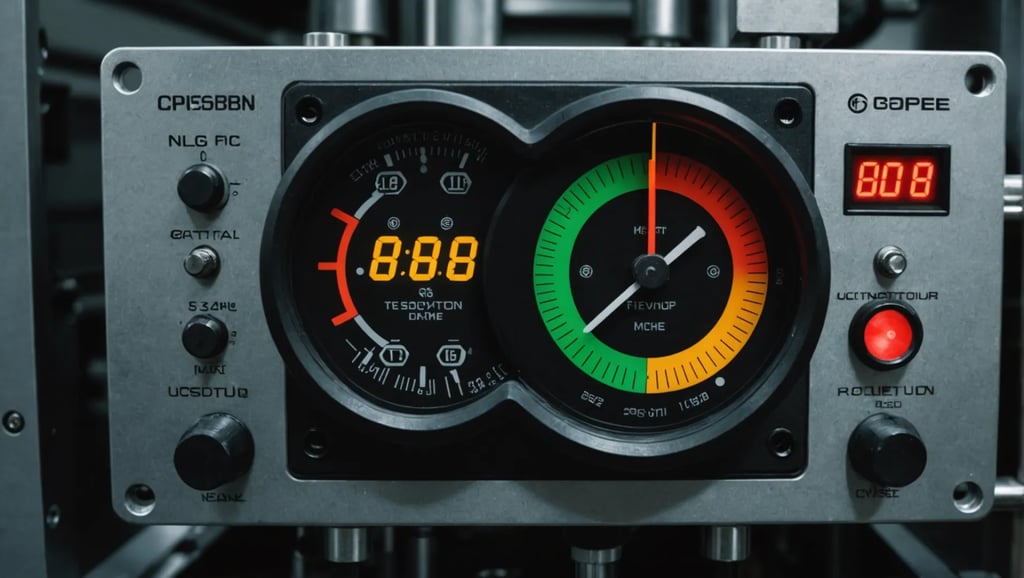
How Does Back Pressure Affect Injection Molding?
Injection molding is a sophisticated process where back pressure plays a crucial role in determining product quality. It impacts material homogeneity, density, and flow characteristics. Understanding and optimizing this parameter is essential for achieving superior manufacturing outcomes.
DEVELOPMENT
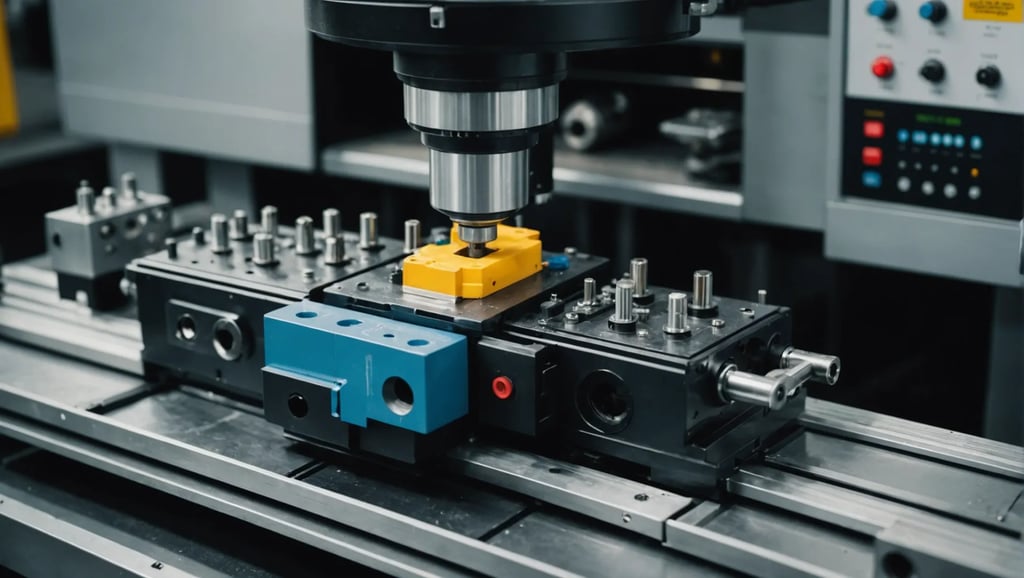
How Does Coring Enhance Injection Molding Efficiency?
Coring plays a pivotal role in injection molding by facilitating the efficient removal of complex parts from molds. By utilizing core pulling mechanisms, manufacturers can reduce material waste, decrease cooling times, and enhance overall product quality. This article delves into ...
DEVELOPMENT
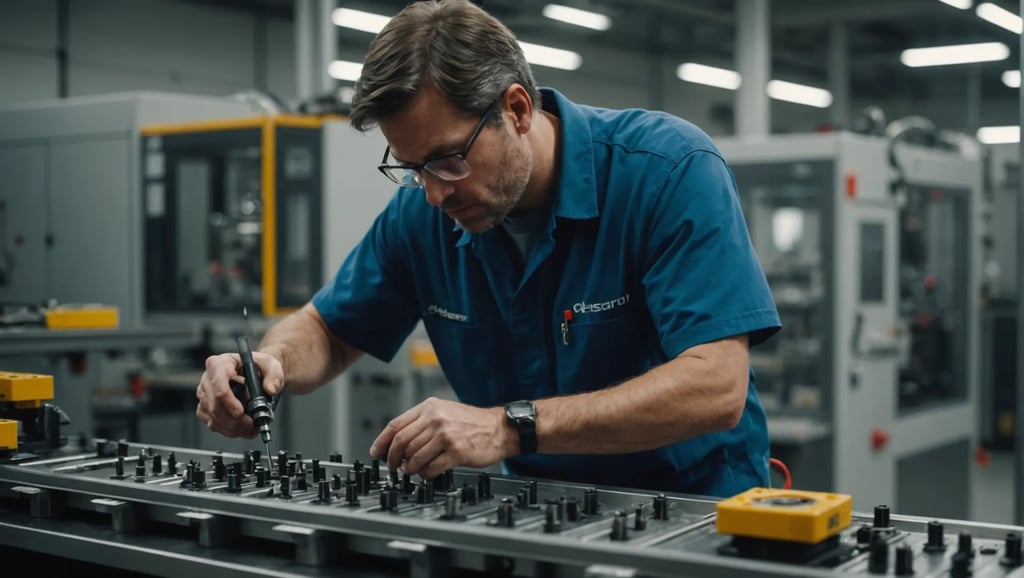
How Can You Improve Injection Mold Change Efficiency?
Improving injection mold change efficiency is crucial for manufacturers aiming to boost productivity and minimize downtime. This guide delves into the essential steps, optimization techniques, and collaborative strategies that can transform your operations. Discover how thorough preparation, process optimization, and ...
DEVELOPMENT
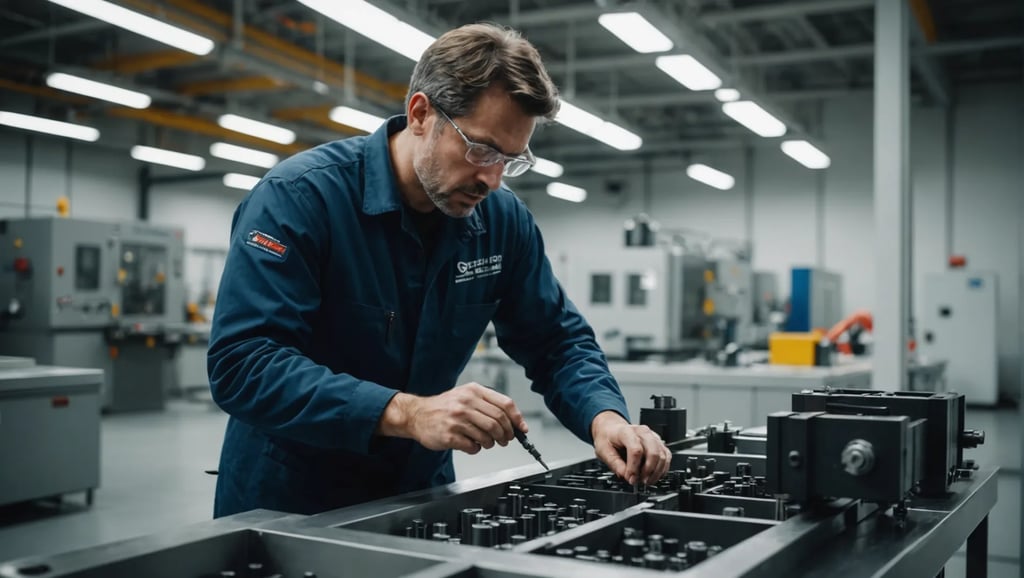
How Can a Well-Planned Injection Mold Maintenance Schedule Boost Production Efficiency?
In the fast-paced world of manufacturing, staying ahead means maximizing efficiency, especially in injection molding. A solid maintenance schedule is not just about keeping machines running; it’s about enhancing production quality and longevity while saving costs. Let’s explore how a ...
DEVELOPMENT
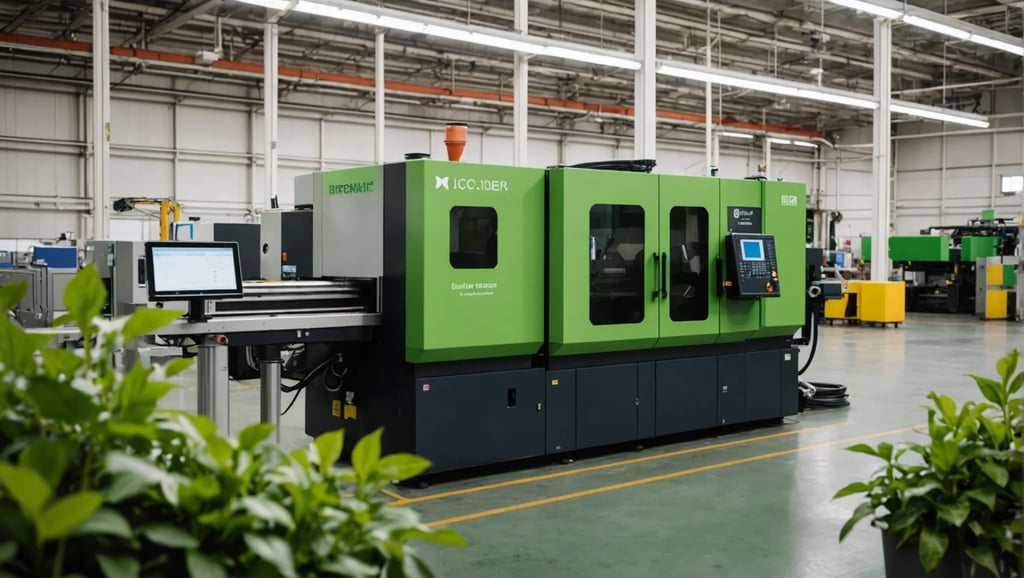
What Are the Challenges and Opportunities of Environmental Protection in Injection Molding?
Injection molding is crucial in manufacturing, but its environmental impact raises significant concerns. This article delves into the challenges and opportunities faced by companies navigating sustainable practices in injection molding, including material selection, technological advancements, energy efficiency, and supportive policies.
DEVELOPMENT
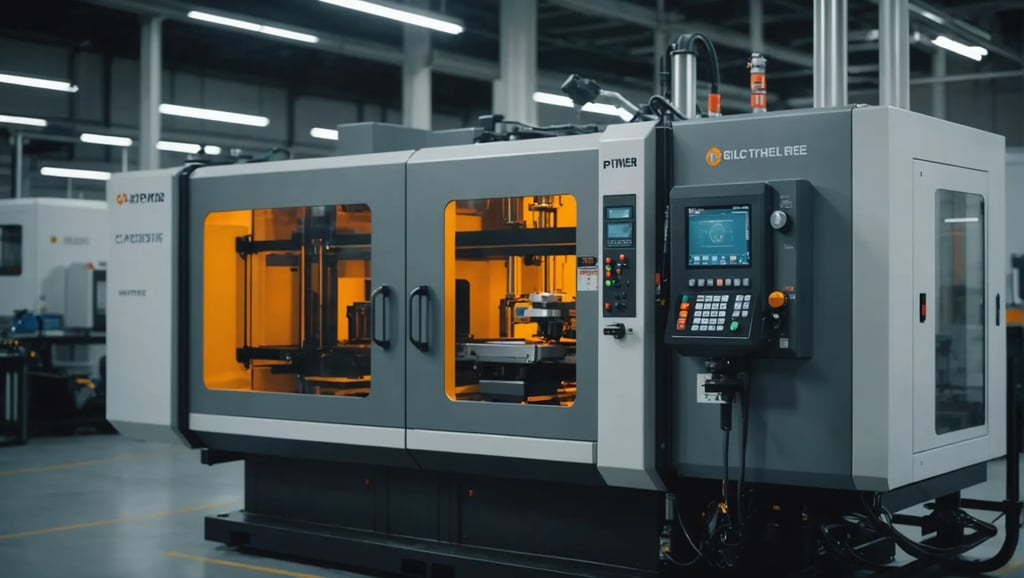
What Are the Best Methods to Optimize Injection Molding Cycles?
Optimizing injection molding cycles is crucial for manufacturers aiming to enhance efficiency and reduce costs. This article explores various strategies, including mold design, material selection, cooling system enhancements, and the importance of operator training, to ensure a seamless production process ...
DEVELOPMENT
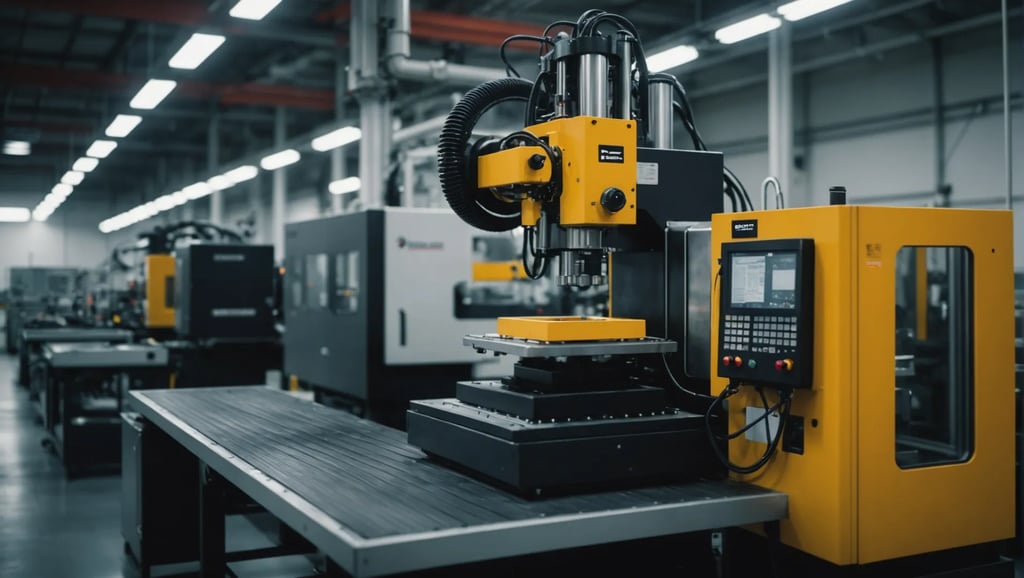
What Are the Solutions to Demolding Problems in Complex Structure Injection Molding?
Demolding challenges in injection molding of complex structures can significantly impact production efficiency and product quality. Understanding these challenges and implementing effective solutions is crucial for manufacturers. From optimizing mold design to improving surface quality, this article explores comprehensive strategies ...
DEVELOPMENT
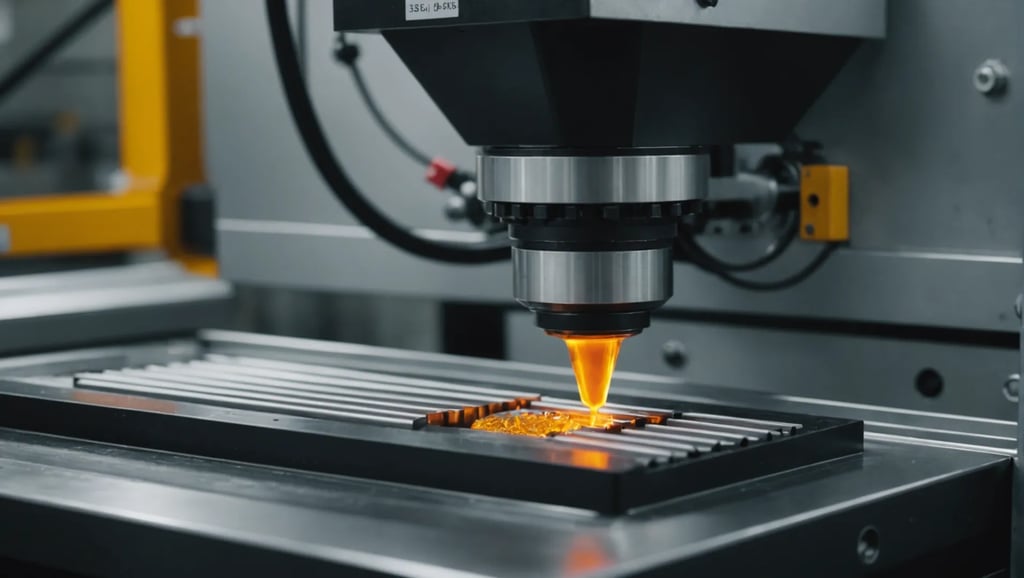
How Does Plastic Fluidity Affect Injection Molding and How Can It Be Controlled?
Understanding plastic fluidity is essential for optimizing injection molding processes. It directly influences filling performance, product quality, and production efficiency. This guide explores how to control fluidity through material selection, process parameters, and mold design for improved manufacturing outcomes.
DEVELOPMENT
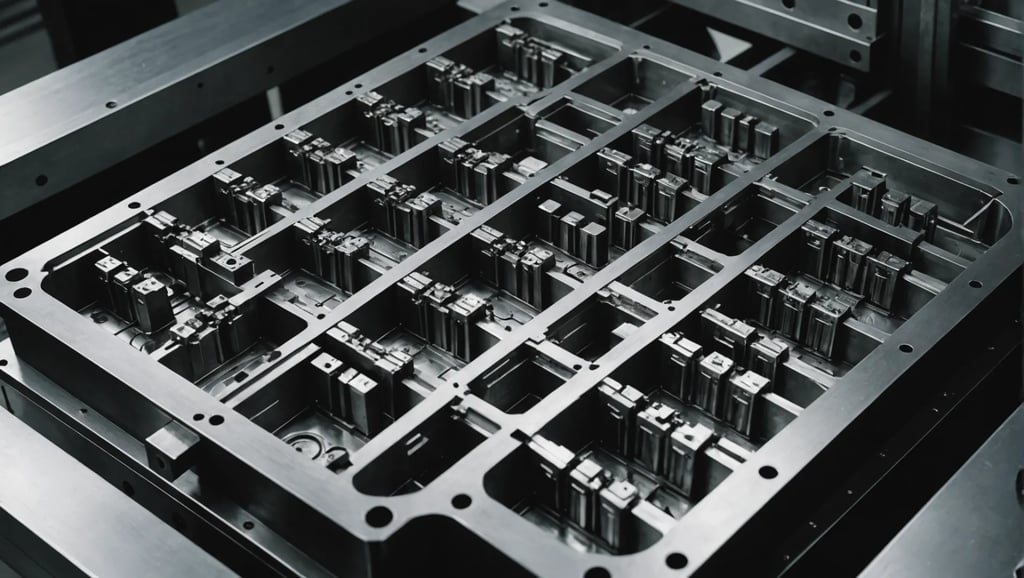
What Are the Best Strategies to Optimize Filling Balance in Multi-Cavity Molds?
Achieving optimal filling balance in multi-cavity molds is essential for high-quality injection molding processes. By focusing on runner and gate design, process parameter adjustments, and rigorous equipment maintenance, manufacturers can significantly improve both product quality and operational efficiency.
DEVELOPMENT
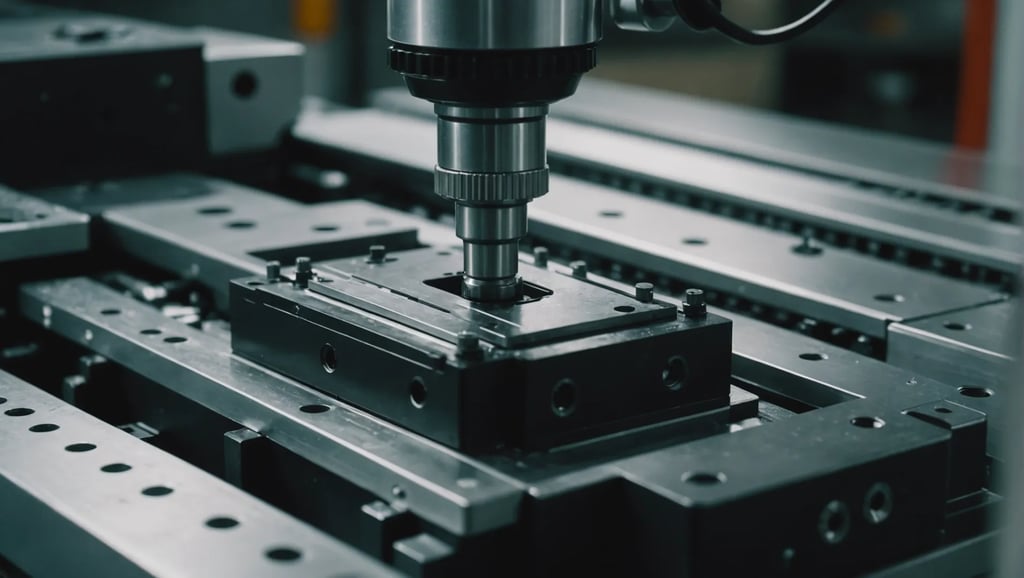
What Are the Causes and Preventive Measures for Mold Sticking in Injection Molded Products?
Mold sticking in injection molded products poses a significant challenge for manufacturers, impacting efficiency and product quality. Understanding the underlying causes—such as mold design flaws, improper process parameters, and unsuitable material choices—is crucial. This article explores effective preventive measures to ...
DEVELOPMENT
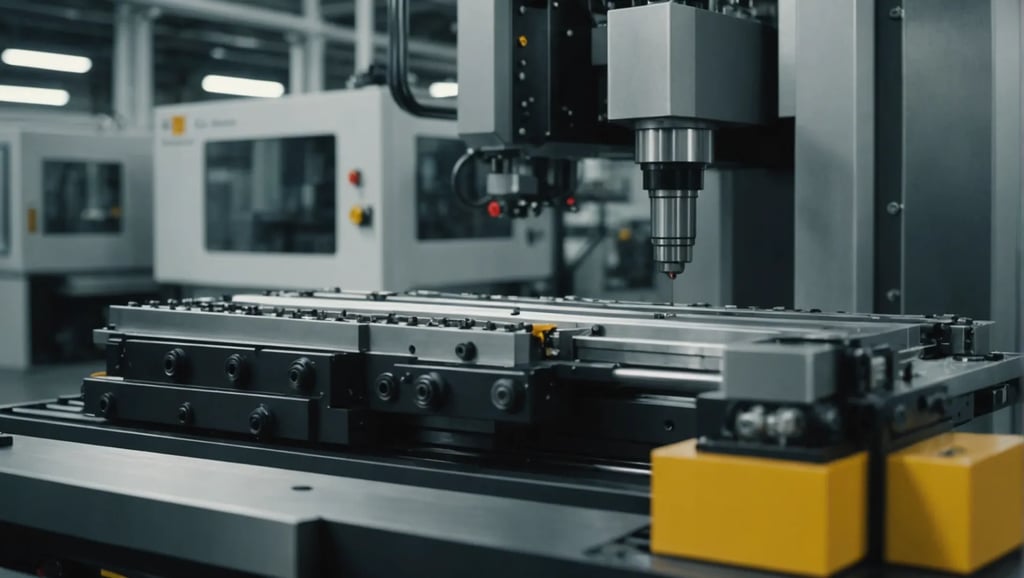
How Can You Effectively Reduce Product Differences in Dual-Cavity Molds?
In the competitive world of manufacturing, consistency is key. When using dual-cavity molds, ensuring uniformity between products is essential for quality and efficiency. By focusing on strategies like precise mold design and stringent process controls, manufacturers can significantly enhance product ...
DEVELOPMENT
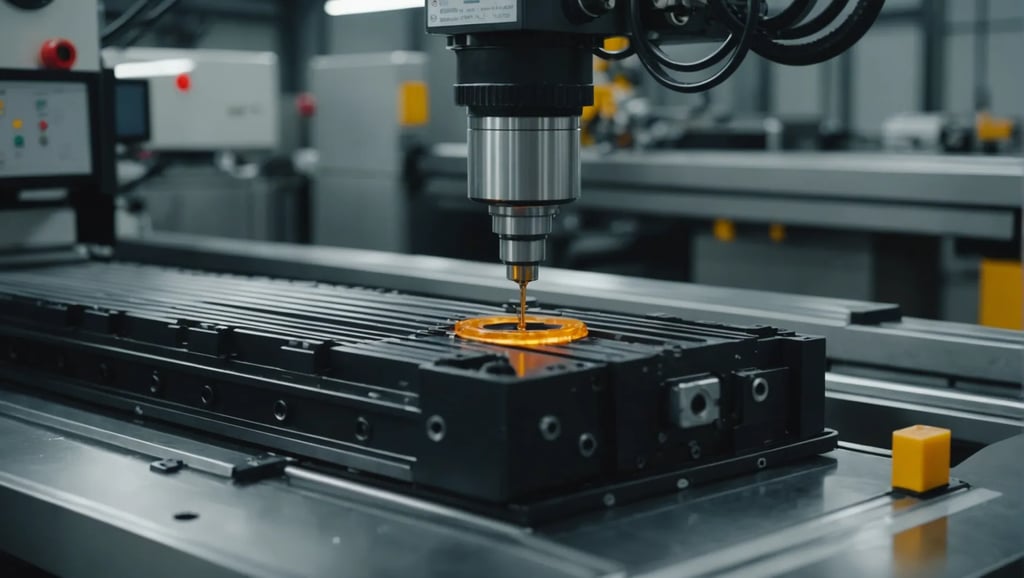
How Can You Maintain Material Fluidity in Injection Molding Production?
Injection molding is a complex process that demands precision and control, especially when it comes to maintaining material fluidity. By selecting the right materials, controlling temperature and pressure, and optimizing mold design, manufacturers can significantly enhance their production efficiency and ...
DEVELOPMENT
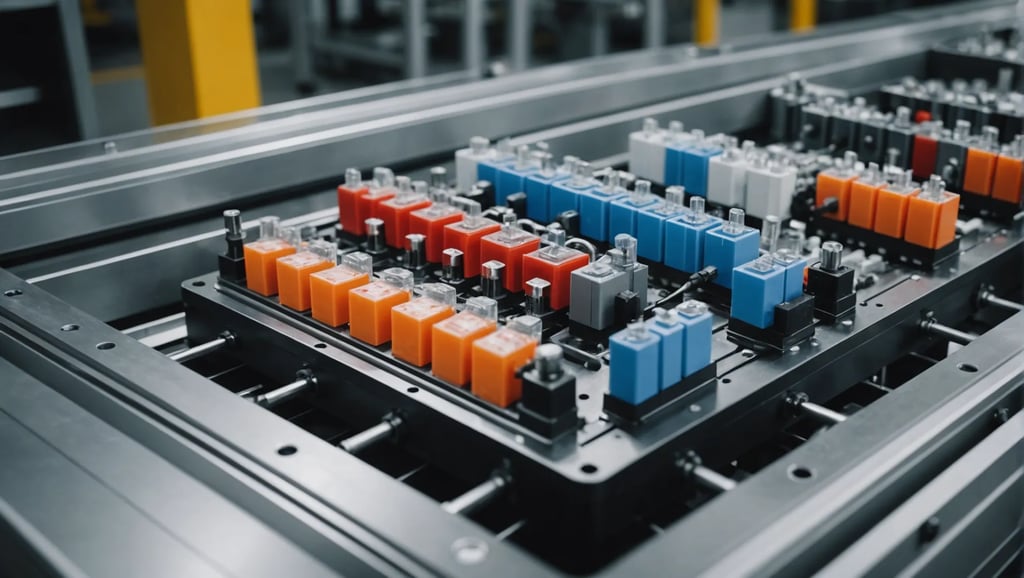
How Can Runner Design Boost Injection Molding Efficiency?
Injection molding is fundamental to modern manufacturing, yet achieving optimal efficiency remains a challenge. By focusing on runner design, manufacturers can significantly enhance their processes. From understanding hot and cold runner systems to optimizing sizes and layouts, this article explores ...
DEVELOPMENT
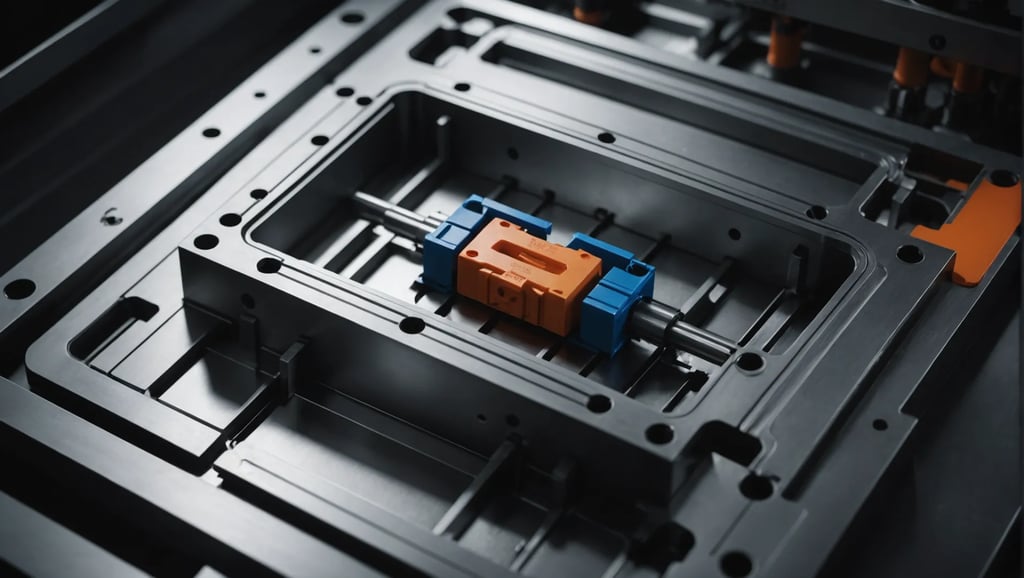
What Are the Best Optimization Techniques for Runner Layout in Injection Molds?
If you're grappling with defects in your injection molded parts, optimizing your runner layout might just be the game changer you need. Discover expert techniques for enhancing product quality and production efficiency, ensuring your molds operate at their best. Let's ...
DEVELOPMENT
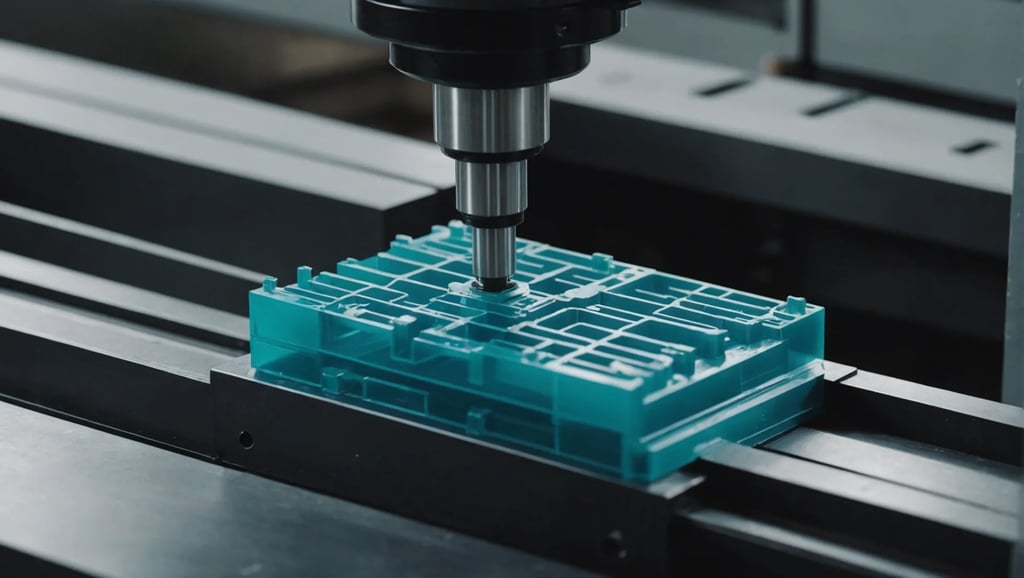
What Are the Best Strategies to Optimize Wall Thickness Distribution in Injection Molded Products?
In the intricate world of injection molding, achieving the perfect wall thickness distribution is crucial for both product quality and efficiency. This article explores essential strategies, from product design to material selection, that can significantly enhance your results. Discover how ...
DEVELOPMENT
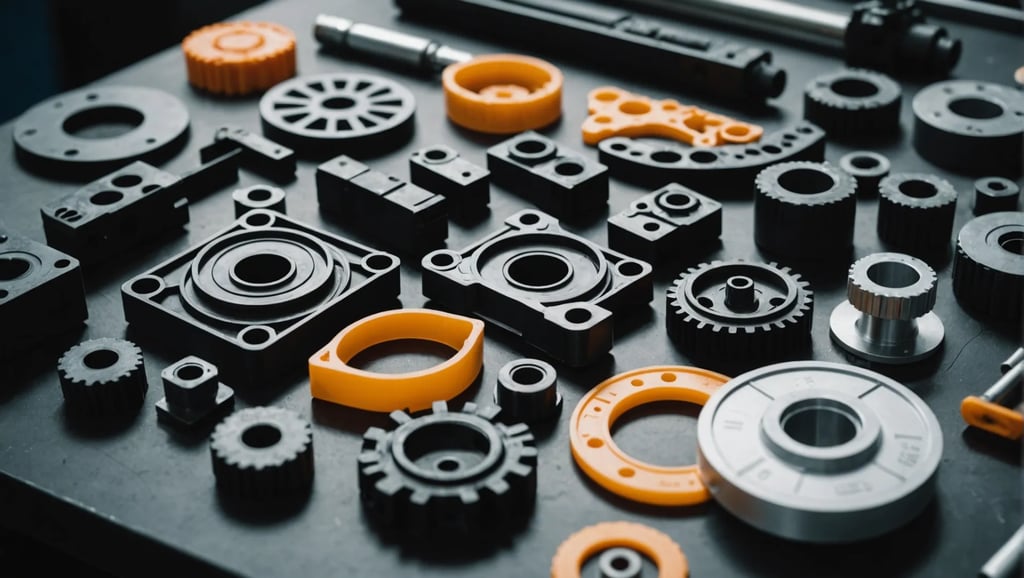
How Can You Balance Rigidity and Toughness in Plastic Injection Molded Parts?
Crafting the perfect plastic injection molded part requires a delicate balance between rigidity and toughness. Achieving this equilibrium ensures durability and performance in demanding applications. In this article, we will explore essential strategies for material selection, structural design, and process ...
DEVELOPMENT
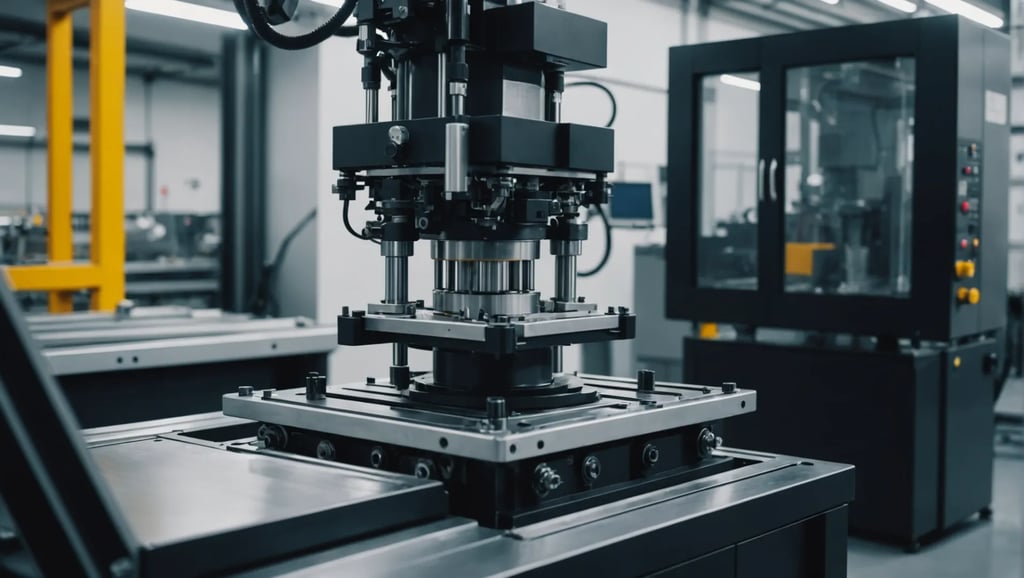
How Can You Optimize Clamping Accuracy in Injection Molds?
Clamping accuracy is a cornerstone of successful injection molding, directly impacting product quality and operational efficiency. By focusing on mold design, manufacturing techniques, proper operation, and maintenance, manufacturers can enhance their processes and ensure top-notch outputs.
DEVELOPMENT
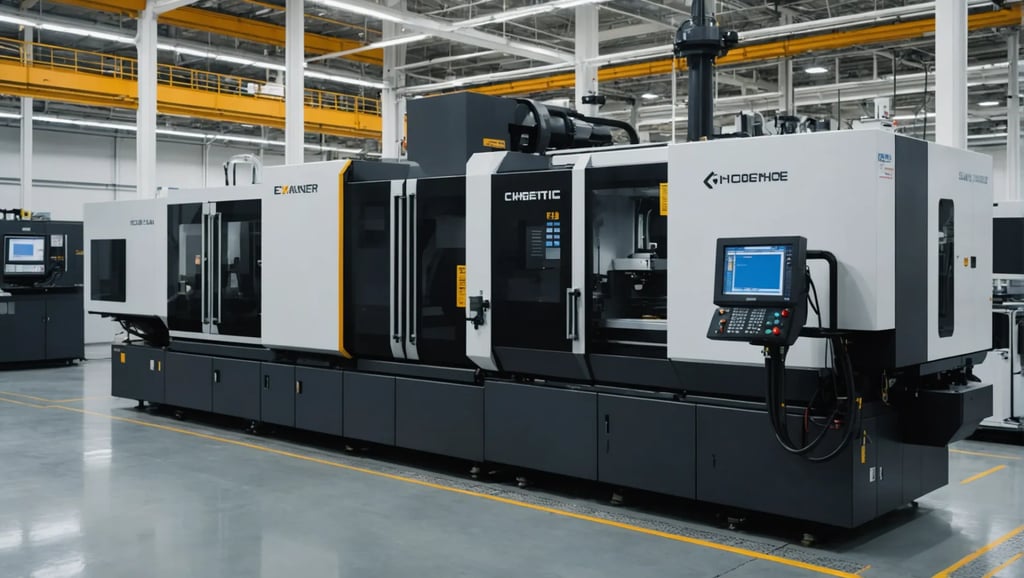
How Does Rapid Cooling Technology Enhance Injection Molding Efficiency?
In today's fast-paced manufacturing landscape, efficiency is not just a goal; it’s a necessity. Rapid cooling technology is at the forefront of revolutionizing injection molding processes. By optimizing cooling, it not only accelerates production but also enhances the quality of ...
DEVELOPMENT
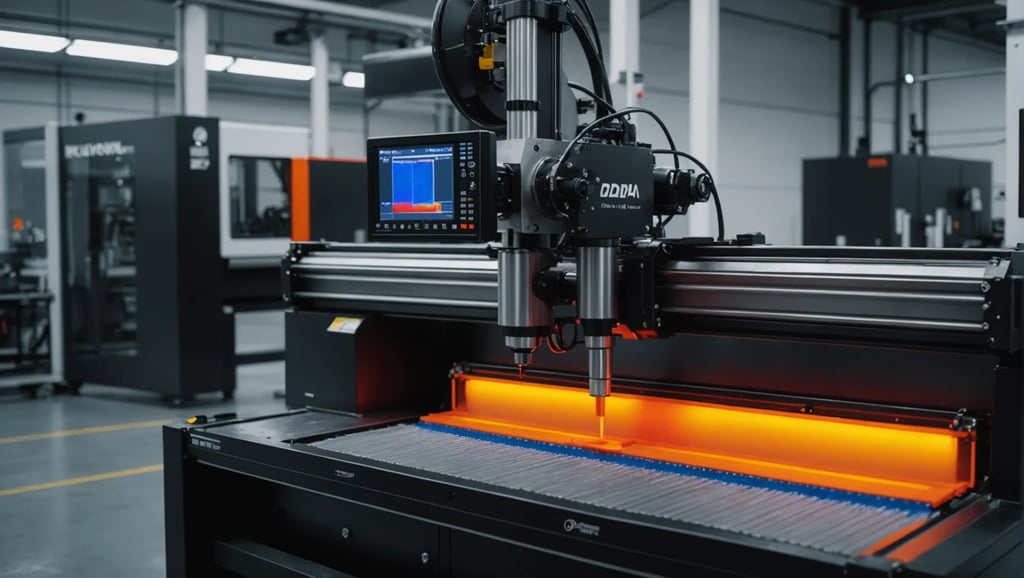
How Can You Effectively Control Heat Loss During Injection Molding?
In the world of manufacturing, particularly in injection molding, controlling heat loss is vital. By optimizing equipment design, ensuring proper insulation, and managing environmental factors, manufacturers can enhance energy efficiency and product quality. Dive into the details of effective heat ...
DEVELOPMENT

What Are the Best Techniques for Controlling Thickness Tolerance in Injection Molded Products?
Maintaining precise thickness in injection molded products is a challenge that manufacturers often face. This article explores essential techniques to control thickness tolerance, including mold design, process parameter adjustments, material selection, and quality inspection. Discover how these strategies can enhance ...
DEVELOPMENT
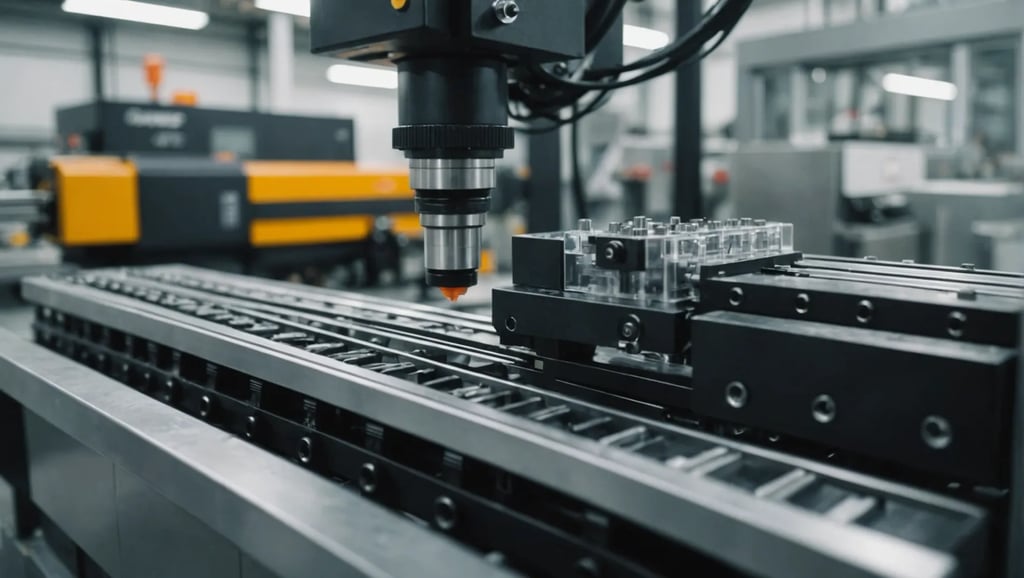
How Can You Optimize the Filling and Holding Stages in Plastic Injection Molding?
Optimizing the filling and holding stages in plastic injection molding is essential for achieving high-quality products. This article explores the critical parameters involved, including injection speed, pressure, and temperature. By understanding how these factors interact, you can significantly enhance your ...
DEVELOPMENT
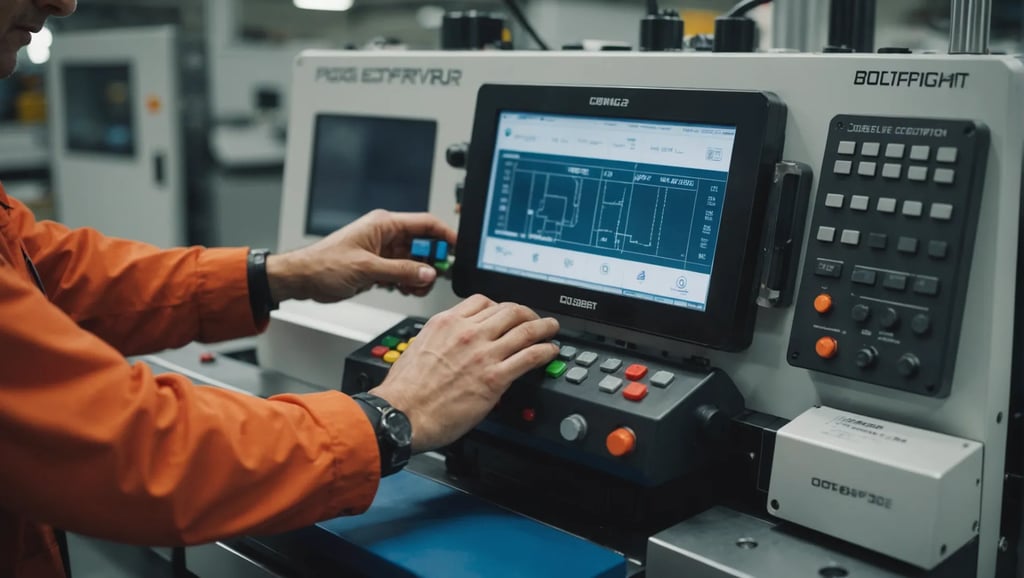
How Can You Adjust Back Pressure in Injection Molding for Better Quality?
Injection molding is a precise science, where even minor adjustments can significantly impact the final product's quality. Understanding back pressure is key to achieving optimal product consistency and minimizing defects. Let's explore effective strategies to adjust back pressure and improve ...
DEVELOPMENT
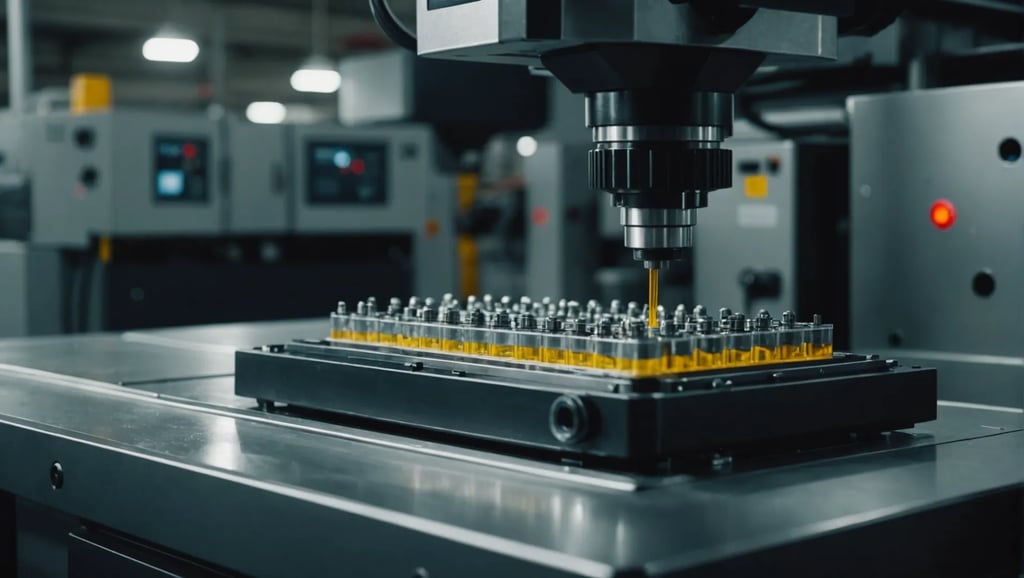
What Are Effective Strategies to Reduce Molding Stress in Injection Molding?
Injection molding is a critical process in manufacturing, but managing stress within the mold is vital to avoid defects like warpage and cracking. By implementing effective strategies, manufacturers can enhance product quality and durability. This article explores various methods including ...
DEVELOPMENT
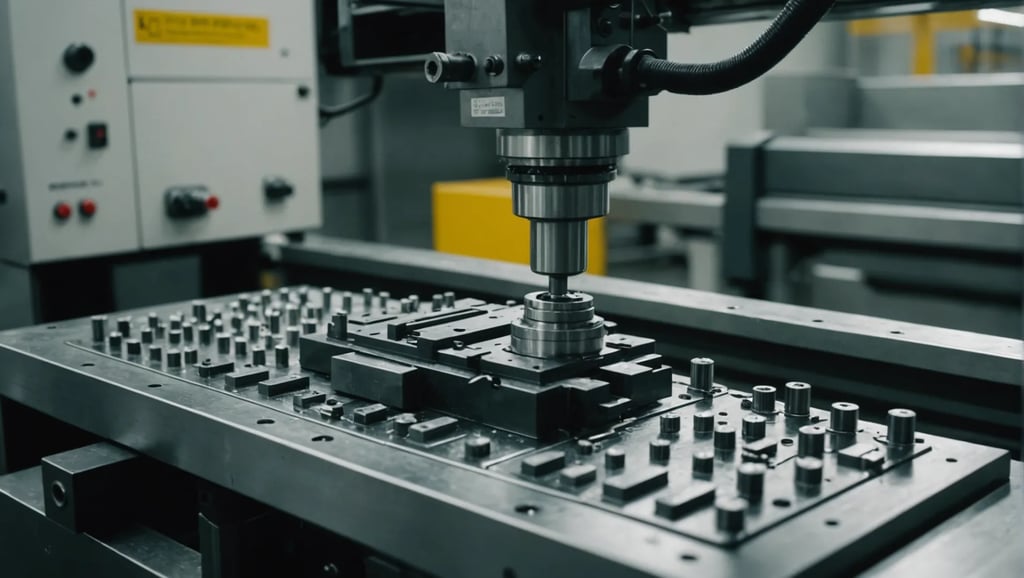
What Factors Determine the Best Mold Opening Time in Injection Molding?
In the world of injection molding, getting the mold opening time just right is crucial. It can significantly impact both production efficiency and product quality. Understanding the various factors that play into determining this timing—like product characteristics, material types, process ...
DEVELOPMENT
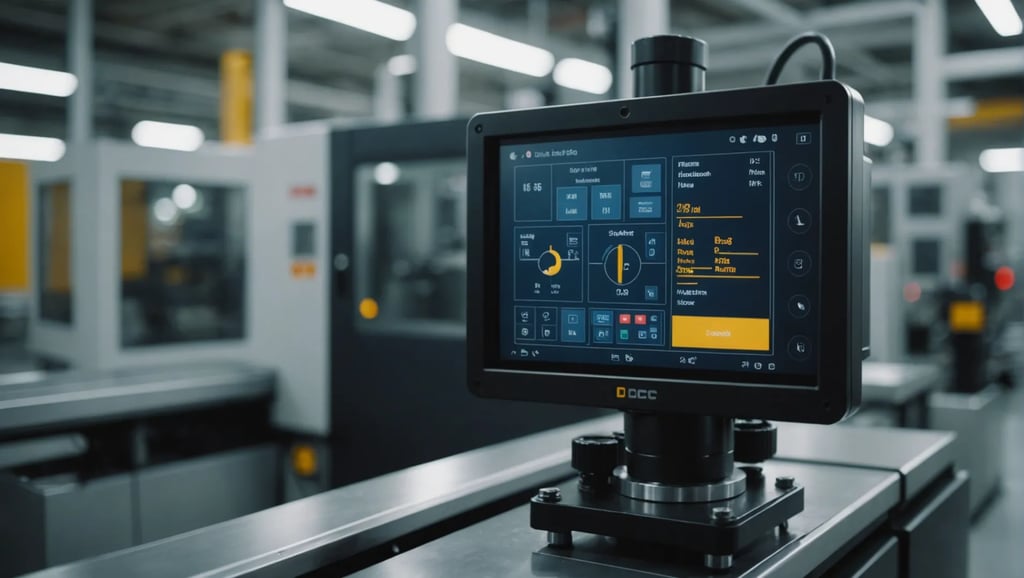
What Are the Best Techniques for Controlling Liquid Plastic Flow Rate in Injection Molding?
Controlling the flow rate of liquid plastic during injection molding is essential for achieving high-quality products. In this article, I'll explore various techniques, including mechanical adjustments, electrical controls, and intelligent systems. Each method has its own strengths and weaknesses, and ...
DEVELOPMENT