DEVELOPMENT
blog & article
read our latest newsletter
Whether you’re curious about material selection, product design, mold design, mold making and injection molding, feel free to ask us anything. Our team is ready to provide the guidance and insights you need.
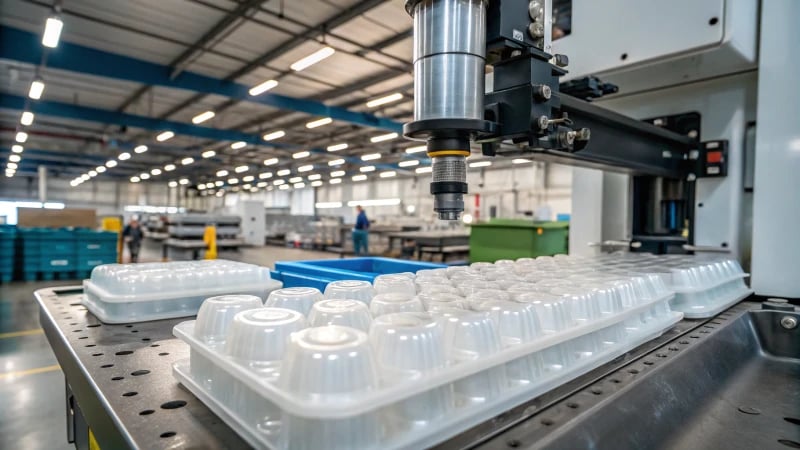
Is Acquiring a Plastic Molding Business a Smart Investment?
Investing in a plastic molding business can be lucrative due to stable demand and technological advancements, but challenges like raw material price volatility and environmental regulations must be carefully considered.
DEVELOPMENT
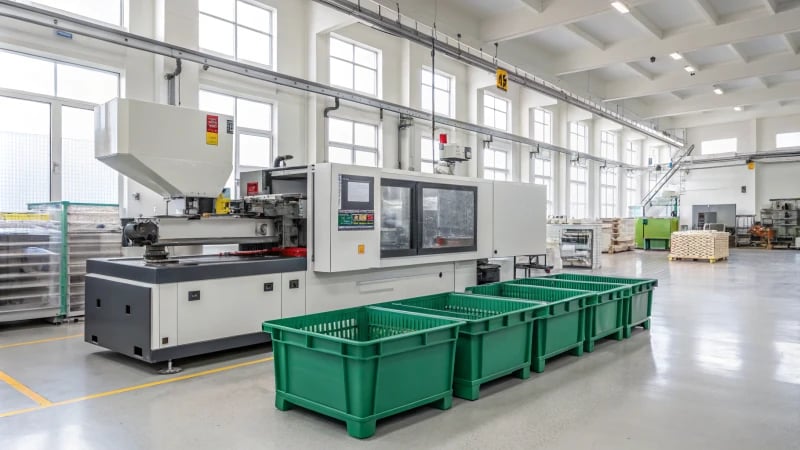
What is Plastic Injection Molding and How Does It Work?
Plastic injection molding is a vital manufacturing process that melts plastic and injects it into molds, producing precise and efficient products across various industries. This article explores its advantages, challenges, and applications.
DEVELOPMENT
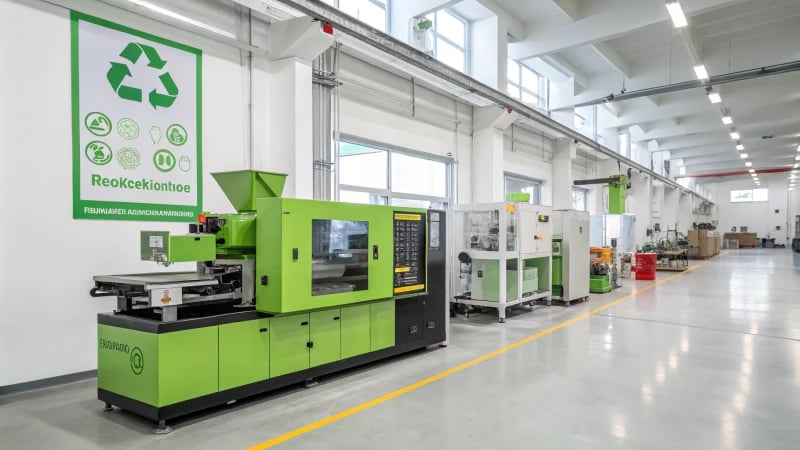
What Are the Key Advantages of Injection Molding?
Injection molding is a highly efficient manufacturing process that offers numerous advantages, including high production efficiency, design flexibility, low costs, and excellent product quality, making it ideal for large-scale production.
DEVELOPMENT
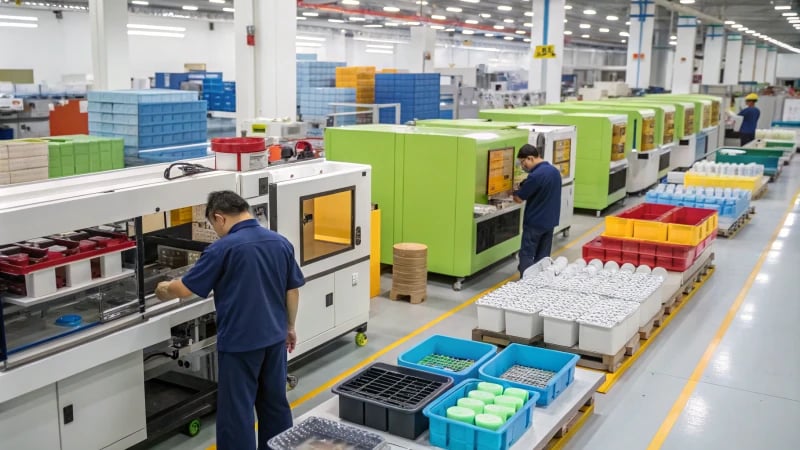
What Are Plastic Molding Services and How Can They Benefit Your Business?
Plastic molding services, including injection, extrusion, blow, and compression molding, enhance manufacturing efficiency and reduce costs. Proper mold design and material selection are crucial for product quality and operational success.
DEVELOPMENT
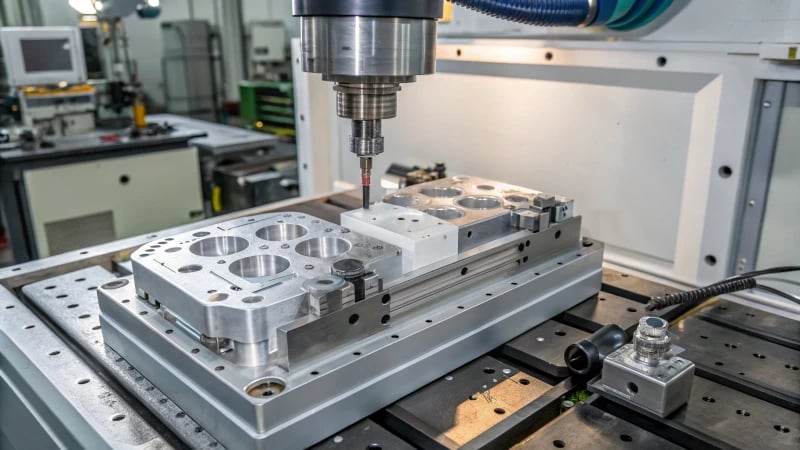
What is the Precision Level of Injection Molding?
Injection molding achieves high precision with dimensional tolerances of ±0.01 to ±0.5mm, influenced by mold design, process parameters, and material properties, crucial for industries like automotive and electronics.
DEVELOPMENT
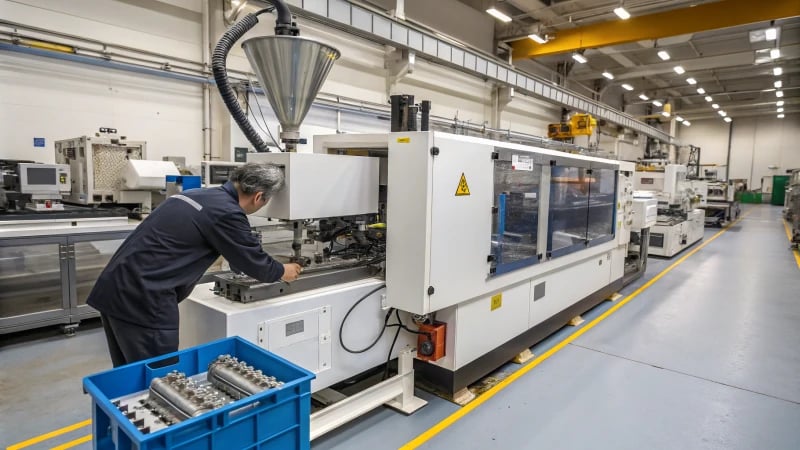
What Factors Influence the Output of an Injection Molding Machine?
The output of an injection molding machine is influenced by various factors including performance parameters, mold design, and raw material characteristics. Optimizing these elements enhances production efficiency and product quality.
DEVELOPMENT
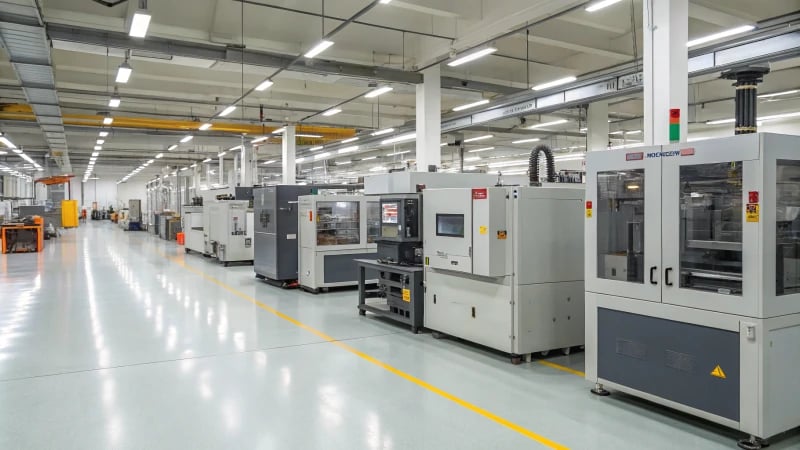
What Are the Most Common Types of Injection Molding Machines?
This article explores the various types of injection molding machines, including hydraulic, electric, and pneumatic options. It highlights their classifications by appearance, power source, plasticization methods, and clamping techniques to aid in selecting the right machine for manufacturing needs.
DEVELOPMENT
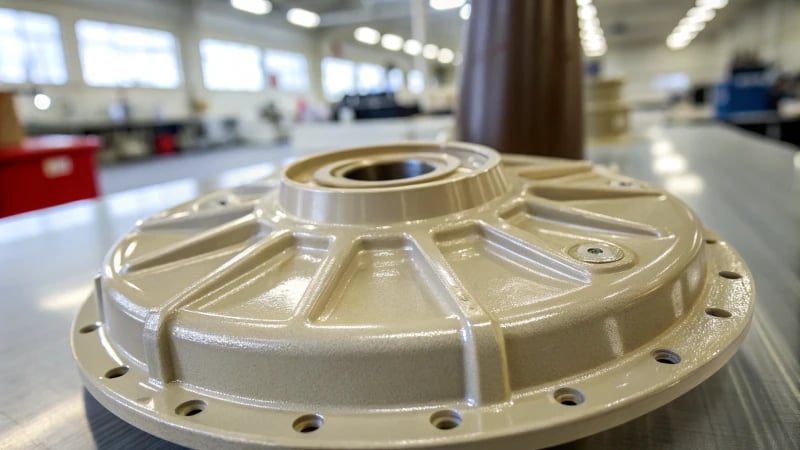
What Are the Best Techniques for Creating High-Quality Injection Molded Parts?
Creating high-quality injection molded parts requires careful attention to raw material selection, mold design, process parameter control, and rigorous quality monitoring. Each step is crucial for optimal results.
DEVELOPMENT
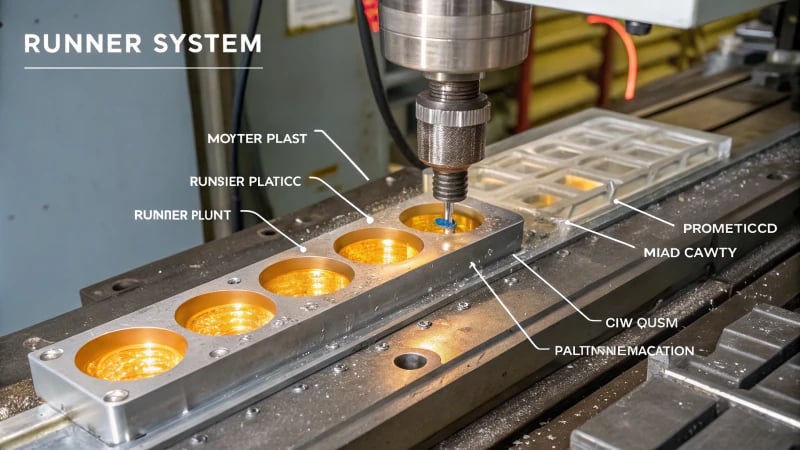
What Role Does the Runner Play in Plastic Molding?
The runner system in plastic molding is crucial for transporting molten plastic from the injection machine to the mold cavity. Its design impacts production efficiency, product quality, and waste reduction.
DEVELOPMENT
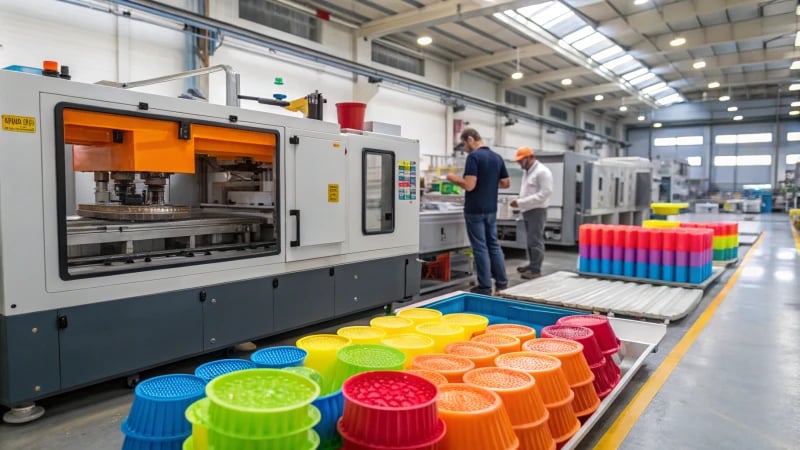
What Is Plastic Molding and Why Is It Important?
Plastic molding is a crucial manufacturing process that shapes plastic materials into various forms using techniques like injection, extrusion, and blow molding. It enhances efficiency, reduces waste, and supports diverse industries.
DEVELOPMENT
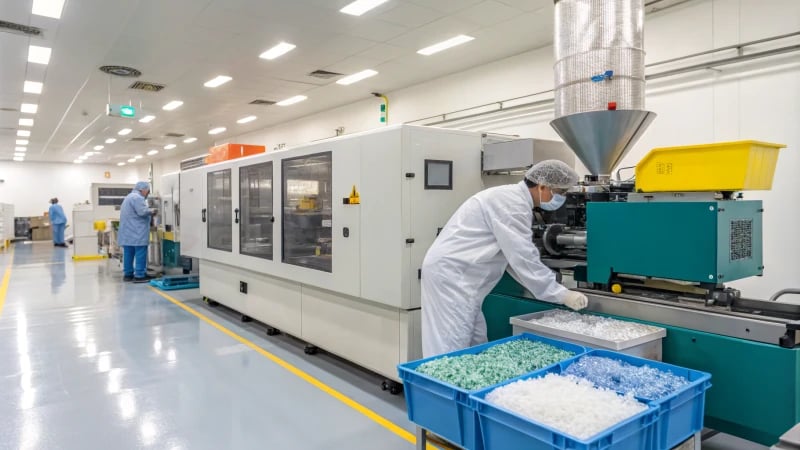
What Are the Benefits of Plastic Molding Services?
Plastic molding services offer numerous benefits, including efficiency, cost-effectiveness, design flexibility, and strict quality control. These advantages make them ideal for various manufacturing needs and enhance product quality.
DEVELOPMENT
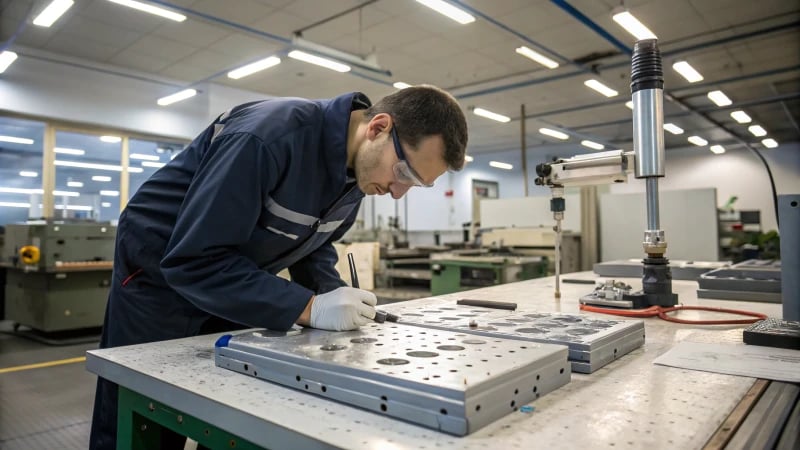
What Are the Best Techniques for Making a Hard Plastic Mold?
This article explores the essential techniques for creating hard plastic molds, covering design, material selection, processing, assembly, trial production, and maintenance to ensure high-quality results.
DEVELOPMENT
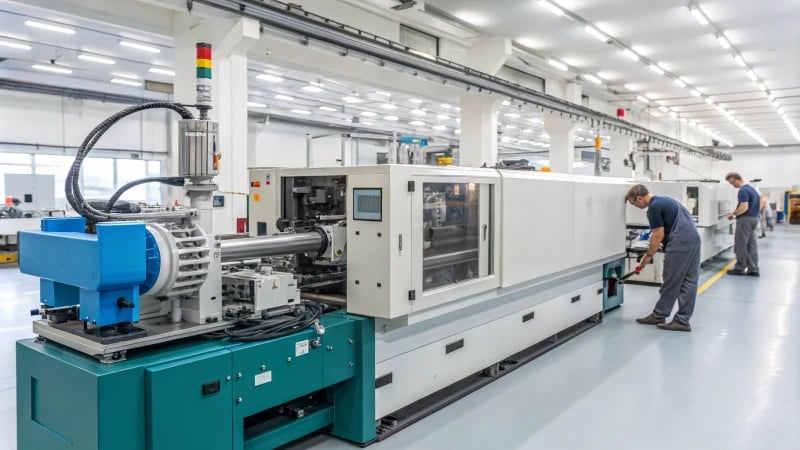
What is Tool Life in Injection Molding and Why Does It Matter?
Tool life in injection molding refers to the duration molds and components last before needing replacement. Factors like material quality, design complexity, and process parameters significantly influence tool longevity and production efficiency.
DEVELOPMENT
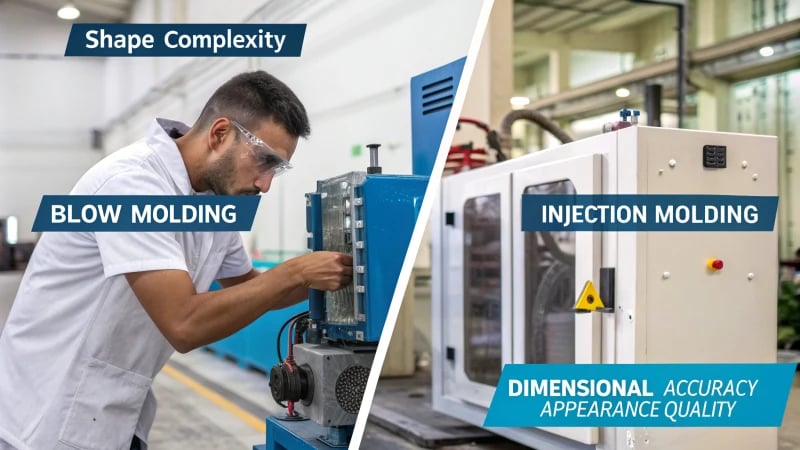
What Are the Key Limitations of Blow Molding Compared to Injection Molding?
This article explores the limitations of blow molding compared to injection molding, highlighting issues such as limited shape complexity, low dimensional accuracy, and poor appearance quality that affect product design.
DEVELOPMENT
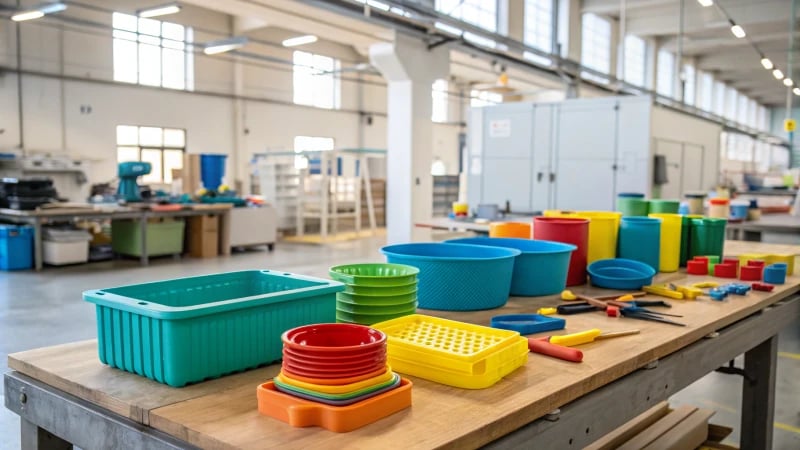
What Are Plastic Mold Products and How Are They Made?
This article explores plastic mold products, detailing their creation through various molding techniques like injection and blow molding. It highlights their applications in packaging, electronics, automotive, and household items.
DEVELOPMENT
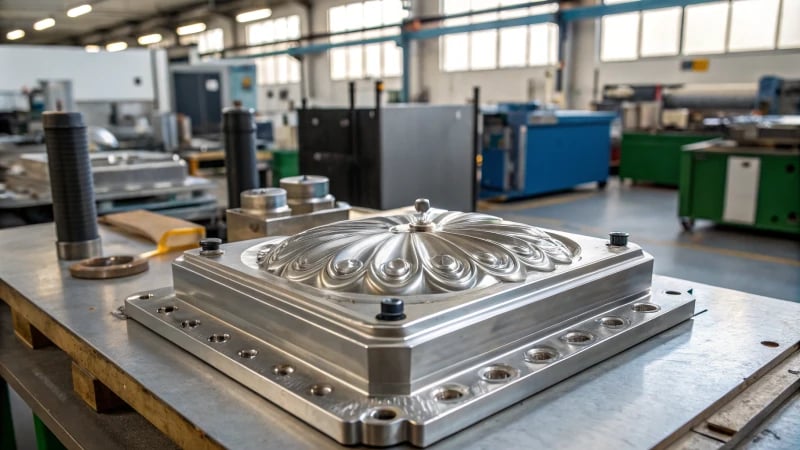
What Exactly Is a Preform Mold and How Does It Work?
Preform molds are essential tools in manufacturing, shaping raw materials into precise forms for various industries, including construction and packaging. Understanding their components enhances production efficiency and product quality.
DEVELOPMENT
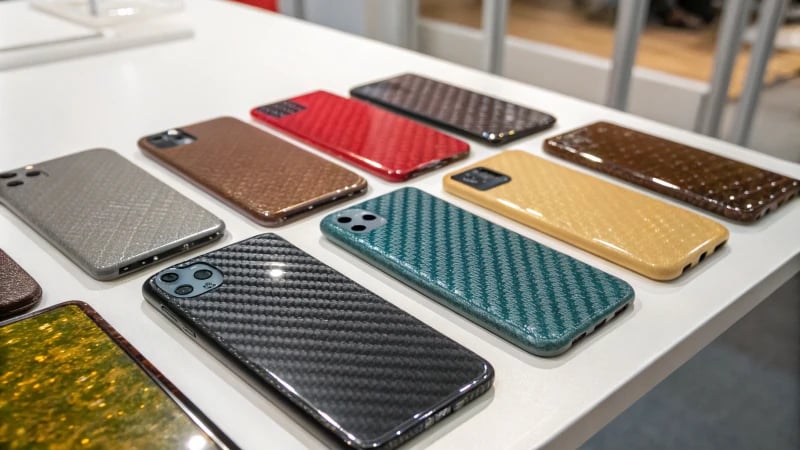
What Are the Best Surface Finish Options for Injection Molding?
This blog post explores the best surface finish options for injection molding, including paint, electroplating, and texture treatments. It highlights their benefits in enhancing aesthetics, functionality, and cost-effectiveness.
DEVELOPMENT
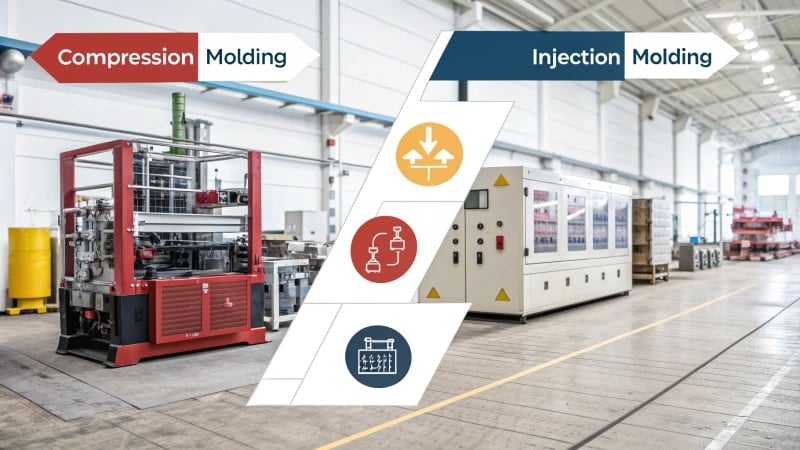
What Are the Key Differences Between Compression Molding and Injection Molding Processes?
This blog post explores the key differences between compression molding and injection molding processes, highlighting their principles, efficiency, costs, and suitability for various applications in plastic manufacturing.
DEVELOPMENT
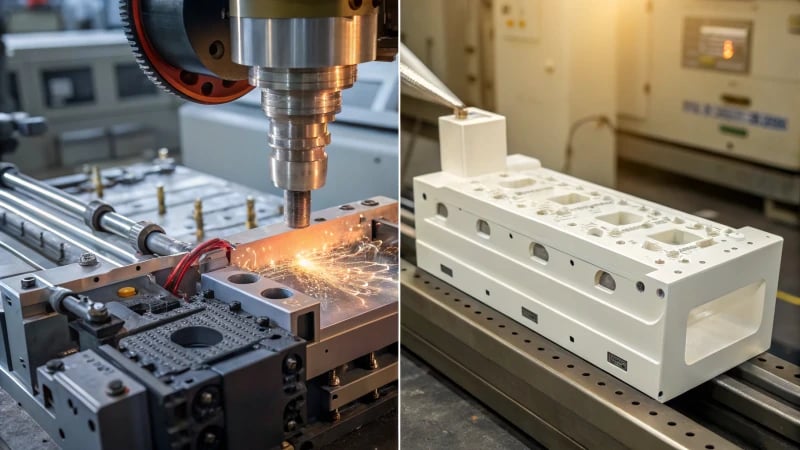
When Should You Choose Injection Molding Over Extrusion for Your Project?
This article explores the differences between injection molding and extrusion, highlighting when to choose each method based on product complexity, dimensional accuracy, production batch size, and material flexibility.
DEVELOPMENT
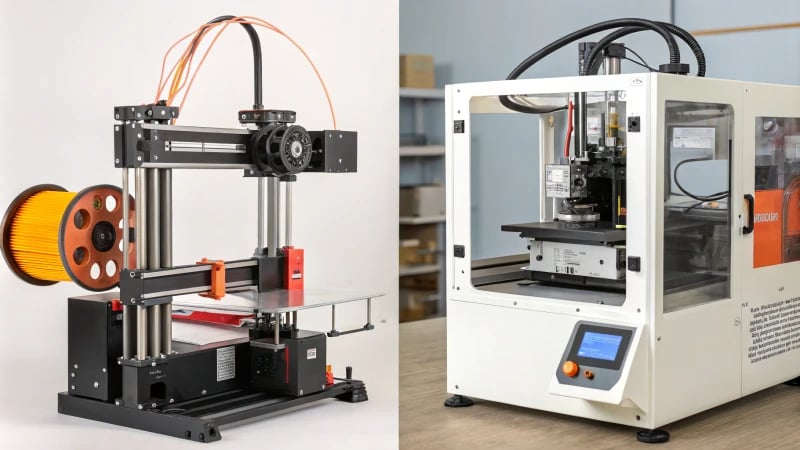
What Are the Key Differences Between 3D Printing and Injection Molding?
This article explores the key differences between 3D printing and injection molding, highlighting their unique strengths in production volume, design complexity, material selection, cost structures, and product quality.
DEVELOPMENT
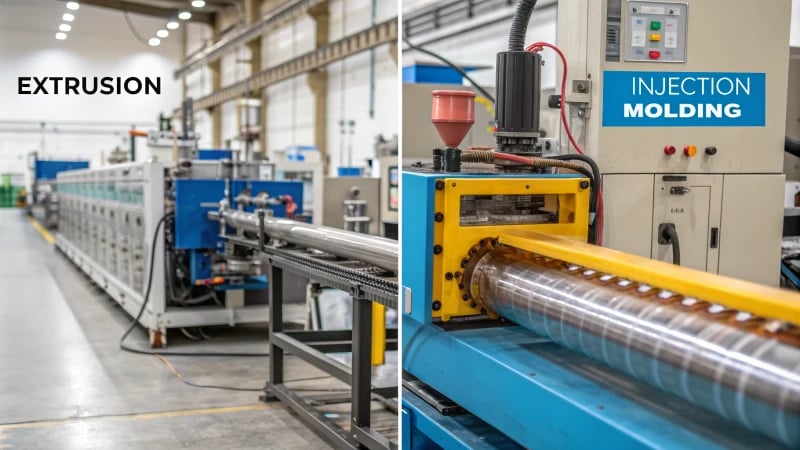
What Are the Production Speeds for Extrusion vs. Injection Molding?
This article compares extrusion and injection molding production speeds, highlighting the continuous efficiency of extrusion versus the cyclical nature of injection molding, along with their respective cost implications.
DEVELOPMENT
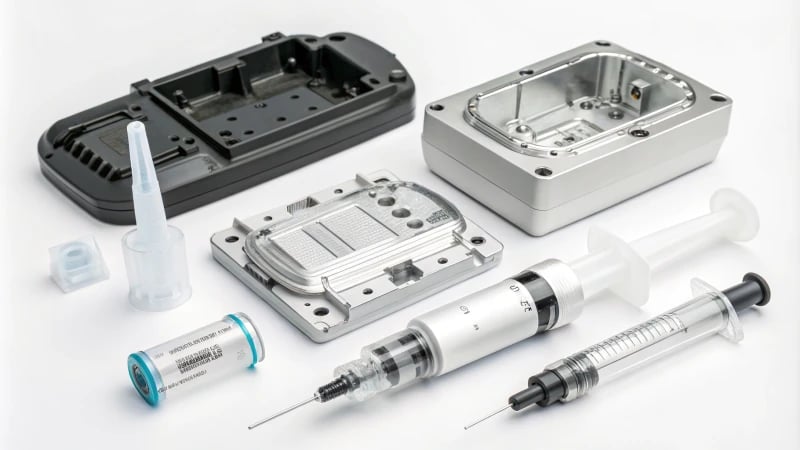
What Products Are Best Suited for Injection Molding Over Blow Molding?
This article explores the advantages of injection molding over blow molding for producing precision electronic parts, automotive interiors, small plastic toys, and medical devices, emphasizing accuracy and efficiency.
DEVELOPMENT
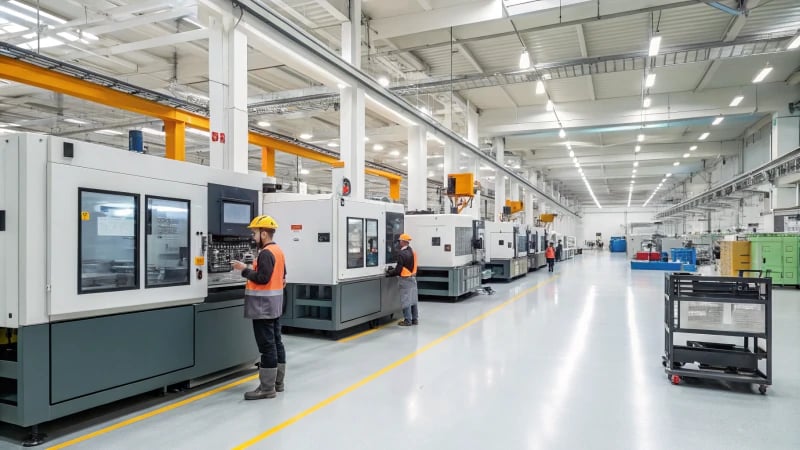
How Are Advances in Materials Science Transforming Extrusion and Injection Molding Capabilities?
Advancements in materials science are revolutionizing extrusion and injection molding by expanding material options, enhancing product quality, improving efficiency, and promoting sustainability in manufacturing processes.
DEVELOPMENT
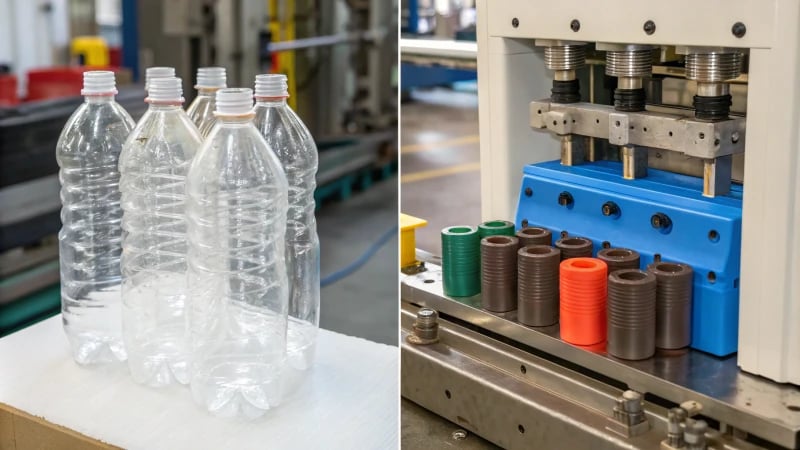
What Are the Key Differences Between Blow Molding and Injection Molding Shapes?
This article explores the key differences between blow molding and injection molding, highlighting their unique characteristics, advantages, production costs, and material choices to guide designers in selecting the right method for their projects.
DEVELOPMENT
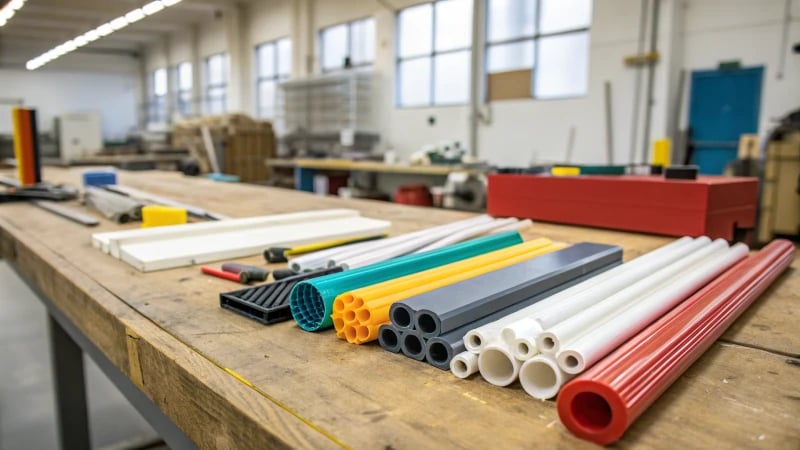
What Shape Does the Final Extruded Product Take?
The extrusion process transforms raw materials into continuous profiles like pipes, rods, and special shapes. Key factors include material properties, die design, cooling methods, and application requirements for optimal functionality.
DEVELOPMENT
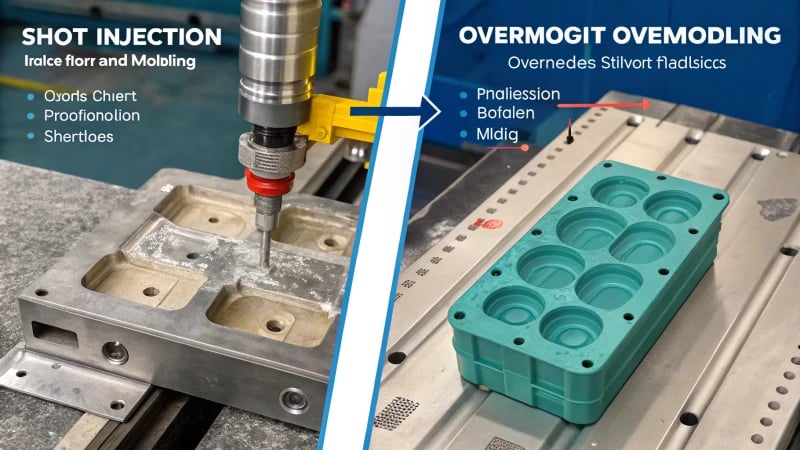
What Are the Key Differences Between Two-Shot Injection Molding and Overmolding?
This article explores the key differences between two-shot injection molding and overmolding, highlighting their processes, advantages, applications, and cost implications to help designers choose the right method for their projects.
DEVELOPMENT
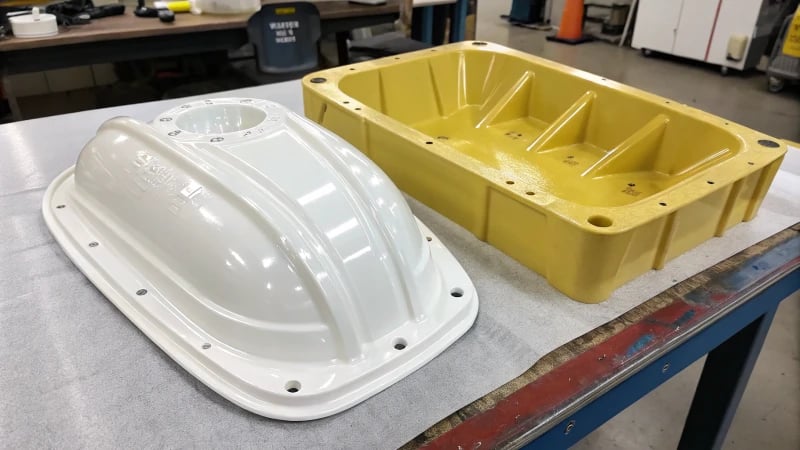
What Are the Key Differences in Surface Finishes Between Extruded and Injection Molded Parts?
This article explores the differences in surface finishes between extruded and injection molded parts, highlighting factors like mold quality, process parameters, and post-processing techniques that influence product aesthetics and functionality.
DEVELOPMENT
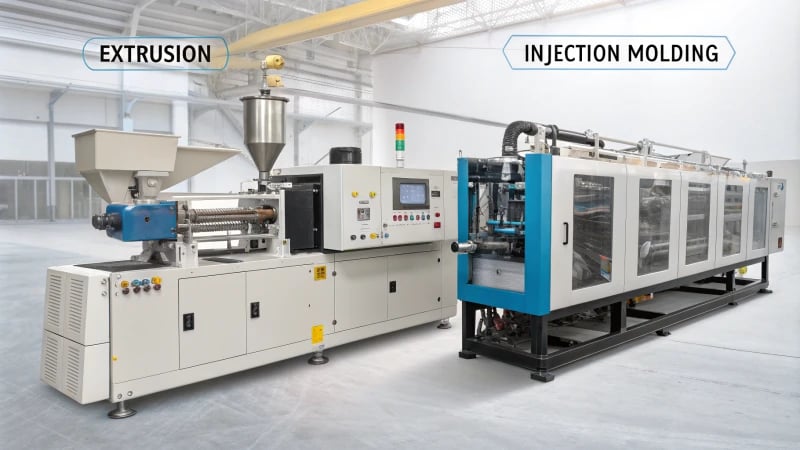
What Are the Key Differences in Material Feeding Between Extrusion and Injection Molding?
This article explores the key differences in material feeding between extrusion and injection molding, highlighting their methods, efficiency, production rates, and suitability for various product designs.
DEVELOPMENT
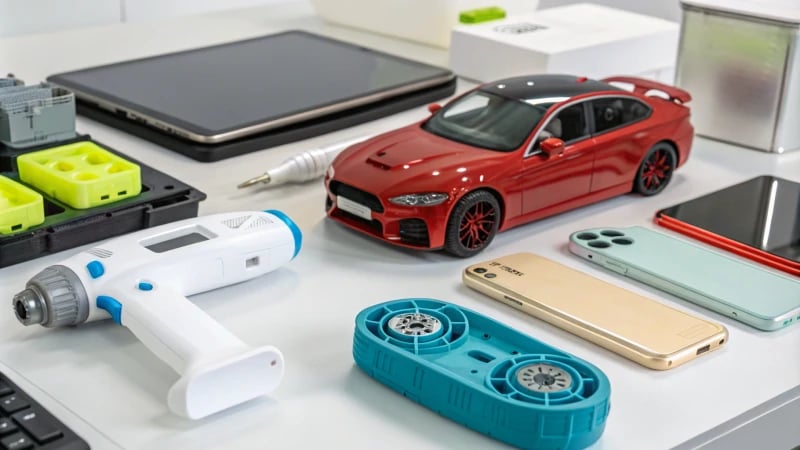
What Are the Top Applications for Two-Shot Molding Products?
Two-shot molding revolutionizes product design by combining aesthetics and functionality across various industries, including electronics, automotive, and healthcare. This innovative technique enhances user experience while improving production efficiency.
DEVELOPMENT
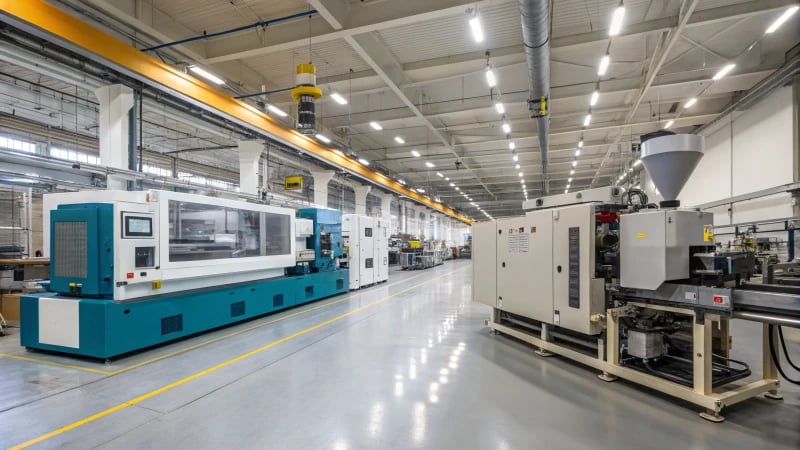
When Should You Choose Injection Molding Over Extrusion?
Choosing between injection molding and extrusion depends on factors like shape complexity, accuracy, production volume, and material flexibility. Injection molding excels in intricate designs, while extrusion suits simpler shapes.
DEVELOPMENT