Let me take you on a journey into the fascinating world of manufacturing—where innovation meets necessity.
Detachable injection molds are advantageous due to their ease of maintenance, cleaning, and ability to adapt to different product requirements. They are essential in industries requiring flexibility, precision, and cost-effectiveness.
But there’s so much more beneath the surface! Understanding how these molds can transform production processes is key to embracing their full potential.
Detachable molds reduce manufacturing costs significantly.True
They allow easy maintenance and component replacement, cutting expenses.
How Do Detachable Injection Molds Enhance Production Efficiency?
In the realm of manufacturing, enhancing efficiency is key to success. Detachable injection molds are pivotal in this pursuit.
Detachable injection molds boost production efficiency by allowing easy maintenance, cleaning, and rapid adaptation to product changes. This flexibility leads to reduced downtime, lower costs, and a streamlined manufacturing process, making them indispensable in dynamic production environments.
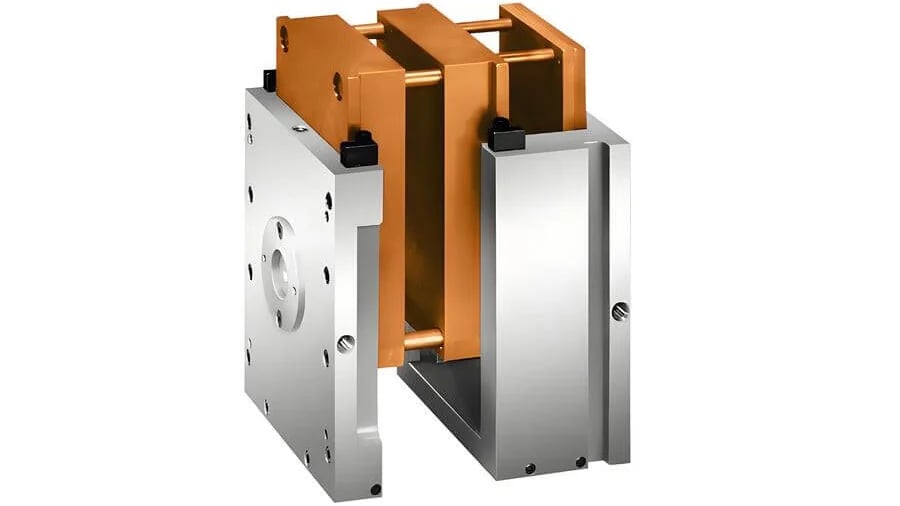
Facilitating Maintenance and Reducing Downtime
One of the primary ways detachable injection molds enhance production efficiency is through simplified maintenance. Traditional molds often require significant downtime for repair or maintenance, impacting productivity. With detachable molds, components can be easily removed and replaced without halting the entire production line. For instance, when a core becomes worn, only that part needs replacement rather than the entire mold. This targeted maintenance not only minimizes downtime but also prolongs the life of the mold.
Simplifying Cleaning Processes
Clean molds are critical for maintaining the quality of injection-molded products. The design of detachable molds allows for comprehensive cleaning since they can be disassembled into smaller components. This design feature ensures that no plastic residue remains in hard-to-reach areas, which is especially beneficial for complex mold shapes prone to residue buildup. By maintaining a clean mold, manufacturers can consistently produce high-quality products while reducing the risk of defects.
Enhancing Flexibility and Adaptability
In industries where product specifications frequently change, such as electronics or consumer goods, the ability to quickly adapt molds is invaluable. Detachable injection molds offer this flexibility by allowing specific components, like cores or cavities, to be swapped out with ease. This adaptability reduces the need for entirely new molds when product designs are updated or modified, saving time and resources. For example, if a product’s design requires slight alterations, only the necessary components need adjustment rather than creating a new mold from scratch.
Supporting Multi-variety Production
Detachable injection molds are particularly advantageous in environments where multiple product variants are produced in small batches. Industries such as medical devices or toy manufacturing often face rapidly changing demands. Detachable molds enable these industries to swiftly change components to meet diverse product requirements without extensive downtime or cost.
Case Study: Automotive Industry Applications
The automotive industry frequently relies on large, complex molds for producing components like dashboards or bumpers. The detachable nature of these molds means they can be transported more easily and assembled on-site, reducing transportation costs and risks of damage. Additionally, when a specific part within a mold requires adjustment due to design changes or wear, it can be replaced or repaired independently, ensuring that production continues smoothly with minimal interruptions.
By adopting detachable injection molds, manufacturers across various sectors can significantly enhance their production efficiency, maintain high-quality standards, and remain agile in the face of evolving product demands.
Detachable molds reduce manufacturing downtime.True
They allow quick maintenance without stopping production.
Detachable molds increase production costs significantly.False
They actually lower costs by reducing downtime and resource use.
What Industries Benefit Most from Detachable Injection Molds?
In the realm of manufacturing, certain industries stand to gain significantly from the flexibility and precision of detachable injection molds.
Industries such as electronics, medical devices, automotive, aerospace, and toy manufacturing benefit the most from detachable injection molds due to their need for rapid adaptation, precision, and cost efficiency.

Electronics Industry: Rapid Adaptation to Change
The electronics industry is characterized by fast-paced innovation and ever-changing consumer demands. Detachable injection molds offer a solution by allowing quick modifications to accommodate new designs. For instance, when producing smartphone components1, manufacturers can swiftly replace specific mold parts to adapt to different models or features without halting production.
Medical Devices: Precision and Compliance
In the medical field, precision is paramount. Detachable molds facilitate the production of intricate devices such as surgical instruments2 and diagnostic equipment. These molds allow easy replacement of components to meet stringent regulatory standards and ensure high-quality outputs.
Automotive and Aerospace: Handling Large and Complex Parts
The automotive and aerospace sectors often require large, complex components that are costly to produce and maintain. Detachable molds enable the production of these parts by allowing sections to be separately manufactured and assembled on-site. This modular approach simplifies logistics and reduces downtime during repairs.
Toy Manufacturing: Flexibility in Small Batch Production
Toy manufacturers frequently deal with small batches and diverse product lines. Detachable molds provide the versatility needed for frequent design changes, enabling quick reconfiguration for new toy models3. This flexibility is crucial for seasonal trends and special editions.
Conclusion: Versatility Across Diverse Fields
The adaptability and cost-effectiveness of detachable injection molds make them indispensable across various industries. Whether it’s achieving precision in medical devices or adapting swiftly in electronics, these molds revolutionize production by meeting unique demands efficiently.
Detachable molds benefit the electronics industry.True
Detachable molds allow quick modifications for new designs in electronics.
Toy manufacturing does not use detachable molds.False
Toy manufacturing benefits from detachable molds for design flexibility.
How Can Detachable Molds Reduce Manufacturing Costs?
In the competitive manufacturing landscape, reducing costs while maintaining quality is paramount. Detachable molds offer a promising solution, significantly cutting down expenses.
Detachable molds reduce manufacturing costs through easy maintenance, flexibility, and reduced transportation and storage expenses. These molds extend the life of tooling and adapt swiftly to product changes, leading to lower overall costs.

Maintenance and Repair Cost Reduction
One of the most significant ways detachable molds reduce costs is through easy maintenance and repair4. In traditional molds, any damage or wear typically necessitates replacing the entire unit. However, with detachable molds, only the affected parts need replacement or repair, thereby saving considerable costs. For example, if a core becomes worn out, it can be individually replaced without discarding the entire mold setup. This approach not only saves material costs but also reduces downtime, ensuring a quicker return to production.
Flexibility in Production
Detachable molds are inherently flexible, allowing manufacturers to adapt swiftly to changes in product design without incurring high costs. When a new product design requires a different mold configuration, only specific components like cores or cavities need replacing. This adaptability is particularly beneficial in industries with frequent product updates, such as electronics and consumer goods. By enabling rapid adjustments, detachable molds eliminate the need for entirely new molds, thus reducing development and production costs.
Transportation and Storage Savings
The modular nature of detachable molds makes them easier and cheaper to transport and store. These molds can be broken down into smaller components, which simplifies logistics and reduces shipping costs. Moreover, smaller components take up less storage space, which translates into lower warehousing expenses. This is especially advantageous for large-scale molds used in industries like automotive and aerospace, where size and weight significantly impact transportation costs.
Extending Mold Lifespan
By allowing for targeted repairs and replacements, detachable molds extend the lifespan of each component. This longevity means less frequent investments in new molds, effectively spreading the initial investment over a longer period. Moreover, the extended lifespan contributes to sustainability by reducing waste and material consumption over time.
By embracing these cost-saving benefits, manufacturers can not only enhance their bottom line but also invest resources into further innovation and expansion.
Detachable molds reduce maintenance costs by 50%.True
Detachable molds allow for part-specific repairs, reducing overall costs.
Detachable molds increase production downtime.False
They decrease downtime by enabling quick part replacements.
What Are the Common Challenges in Using Detachable Molds?
While detachable molds offer flexibility, they also present unique challenges in design, operation, and maintenance.
Common challenges of detachable molds include complex assembly processes, potential misalignment, and increased initial design costs. Addressing these issues requires precision engineering and thorough quality checks.

Complex Assembly Processes
One major challenge when working with detachable molds is the complexity involved in their assembly. Unlike traditional molds, detachable molds consist of multiple parts that must be perfectly aligned and assembled for effective operation. Any misalignment can lead to product defects, such as poor surface finish or inaccurate dimensions. Ensuring seamless assembly often requires skilled technicians and additional time in the setup process.
Potential for Misalignment
The very nature of detachable molds—being composed of multiple components—makes them susceptible to misalignment. Even a slight deviation in alignment can cause issues during injection molding, such as uneven pressure distribution or flash formation. Regular quality checks and precise calibration are essential to mitigate these risks. Employing advanced measurement tools can also help maintain alignment accuracy.
Increased Initial Design Costs
Detachable molds, by virtue of their complexity, often incur higher initial design and manufacturing costs compared to traditional molds. The need for precision engineering and custom components can drive up expenses. However, these costs may be offset by the mold’s longevity and versatility in adapting to various product designs. Companies must weigh these upfront costs against the long-term benefits of using such molds.
Maintenance and Component Wear
While detachable molds are designed for easy maintenance, they can also experience frequent wear due to their modular nature. Components such as cores and cavities may require regular replacement or repair, which can disrupt production schedules. Implementing a preventive maintenance program5 is crucial to minimize downtime and ensure consistent mold performance.
Balancing Cost with Flexibility
Detachable molds offer significant flexibility by allowing easy modifications for different products. However, balancing this flexibility with cost-effectiveness remains a challenge. Companies must carefully plan production schedules and mold modifications to avoid unnecessary expenses. Understanding the full potential of modular mold systems6 can aid in achieving this balance effectively.
Detachable molds increase initial design costs.True
Complexity and precision engineering drive up initial costs.
Misalignment in detachable molds is easily avoidable.False
Multiple components make them susceptible to misalignment.
Conclusion
Detachable injection molds provide unmatched benefits in flexibility, efficiency, and cost reduction. By incorporating these molds into production processes, industries can enhance product quality and adaptability.
-
Explore how detachable molds enhance smartphone component production.: What are some common plastic injection-molded accessories for your smartphones? · Phone cases · Screen protectors · Stands and holders · Charging docks · Mounts for … ↩
-
Understand the role of detachable molds in medical device manufacturing.: Designing custom injection molds for precision plastic parts is a complex process that involves many unique considerations. ↩
-
Learn about the flexibility detachable molds offer in toy production.: This article aims to provide a comprehensive understanding of plastic toys, from their advantages and disadvantages to their production and design methods. ↩
-
Explore how detachable molds simplify maintenance and reduce associated costs.: Maintenance of injection molds is critical for maintaining product quality, reducing costs, minimizing downtime, ensuring safety, and prolonging the life of … ↩
-
Explore strategies to reduce downtime and improve mold performance.: Performing fundamental maintenance inspections frequently assures press longevity and process stability. Here’s a checklist to help you stay on top of seven … ↩
-
Learn how modular systems enhance mold flexibility and cost-efficiency.: Modular molds offer cost savings by reducing design time, mold making hours, repair costs, inventory, material costs, and more. Dedicated to … ↩