Have you ever wondered how something as industrial as injection molding can be scaled down to fit on your desk?
Desktop injection molding uses compact machines to melt and inject thermoplastic materials into molds, ideal for small parts, prototyping, and educational purposes due to low clamping forces and size efficiency.
Picture this: a machine small enough to sit on your workbench but powerful enough to transform raw plastic into precision parts. Desktop injection molding machines are like the little engines that could, offering clamping forces in the range of just a few tons. This makes them fantastic for those early-stage product designs or even for hobbyists who want to tinker with creating miniatures or custom figurines.
The process itself is a fascinating dance of heat and pressure. Imagine feeding thermoplastic pellets into a barrel, where they melt under heat. The material is then pushed by a rotating screw into a mold, forming into the shape you’ve envisioned. Once cooled, the mold opens, and voilà! Out comes your very own creation, ready to be admired or refined further.
I remember when I first learned about this process; it was like a light bulb moment. Suddenly, I could see the potential for turning my sketches into tangible objects right from my desk. Whether you’re designing for consumer electronics or simply curious about manufacturing, desktop injection molding offers an exciting peek into the world of product creation.
Desktop injection molding uses high clamping forces.False
Desktop machines use lower clamping forces, suitable for small parts.
Thermoplastics are used in desktop injection molding.True
Thermoplastic materials are melted and injected into molds.
Why Choose Desktop Injection Molding Machines?
Remember that moment when you wanted to create something unique, but didn’t have the space or resources for industrial machinery? Desktop injection molding might just be your answer!
Desktop injection molding machines stand out due to their compact design, lower clamping force, and ease of use for prototyping and small-scale production. These machines offer an accessible and affordable entry into custom plastic manufacturing.
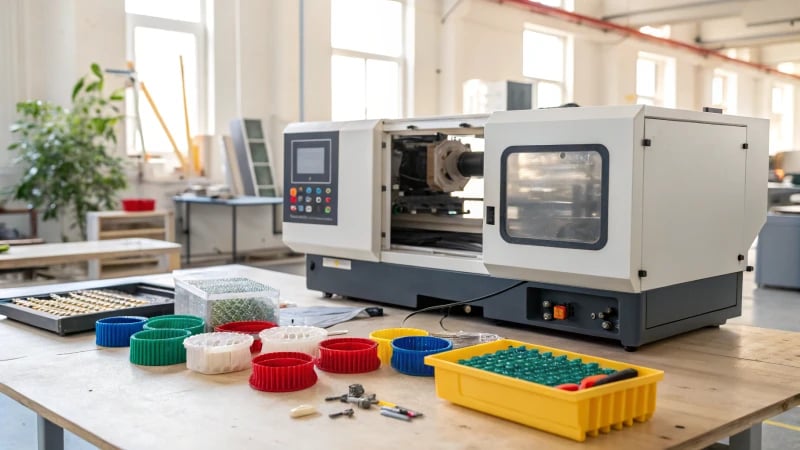
Compact Design & Clamping Force
I remember when I first set up my own little workshop, space was a luxury I simply didn’t have. Desktop injection molding machines became my go-to solution. They’re designed to fit comfortably on a workbench, making them perfect for tight spaces. Unlike the industrial behemoths that require hundreds or thousands of tons of clamping force, these desktop models are much gentler, usually offering just a few to tens of tons.
Feature | Industrial Machines | Desktop Machines |
---|---|---|
Clamping Force | Hundreds to thousands of tons | Few to tens of tons |
Size | Large, floor-standing | Compact, desktop-suitable |
This was a game-changer for me, allowing me to set up a home workshop without overwhelming my space.
Molding Process Adaptability
The process itself is fascinating. I love how similar it is to traditional injection molding1. You start with thermoplastic pellets, which are melted in a heated barrel. Then, just like magic, they’re injected into molds that I’ve custom-designed. This adaptability lets me bring my most creative ideas to life, whether I’m crafting a new gadget or a bespoke figurine.
Broad Applications
These machines have been a revelation in my prototyping adventures. They’re incredible for producing small plastic parts—perfect for anyone dabbling in model-making or teaching budding engineers. I’ve used mine to whip up everything from tiny mechanical components to unique figurines.
- Educational Use: Great for teaching manufacturing principles.
- Prototyping: Quickly produces sample parts for design verification.
For those like me, looking to push the boundaries of design capabilities2 without the hefty price tag of industrial equipment, desktop injection molding is a fantastic starting point. It’s opened up a whole new world of possibilities in manufacturing and creativity.
Desktop injection molding machines are floor-standing.False
They are compact and designed to fit on a workbench, not floor-standing.
Desktop machines use thermoplastic pellets for molding.True
Thermoplastic pellets are melted and injected into molds, similar to industrial processes.
How Does the Molding Process Work Step-by-Step?
Ever wondered how a simple plastic pellet turns into a crucial component of your everyday gadgets? Let’s take a closer look!
The molding process involves melting raw plastic, injecting it into a mold, and cooling it to form precise components, ensuring durability and accuracy.
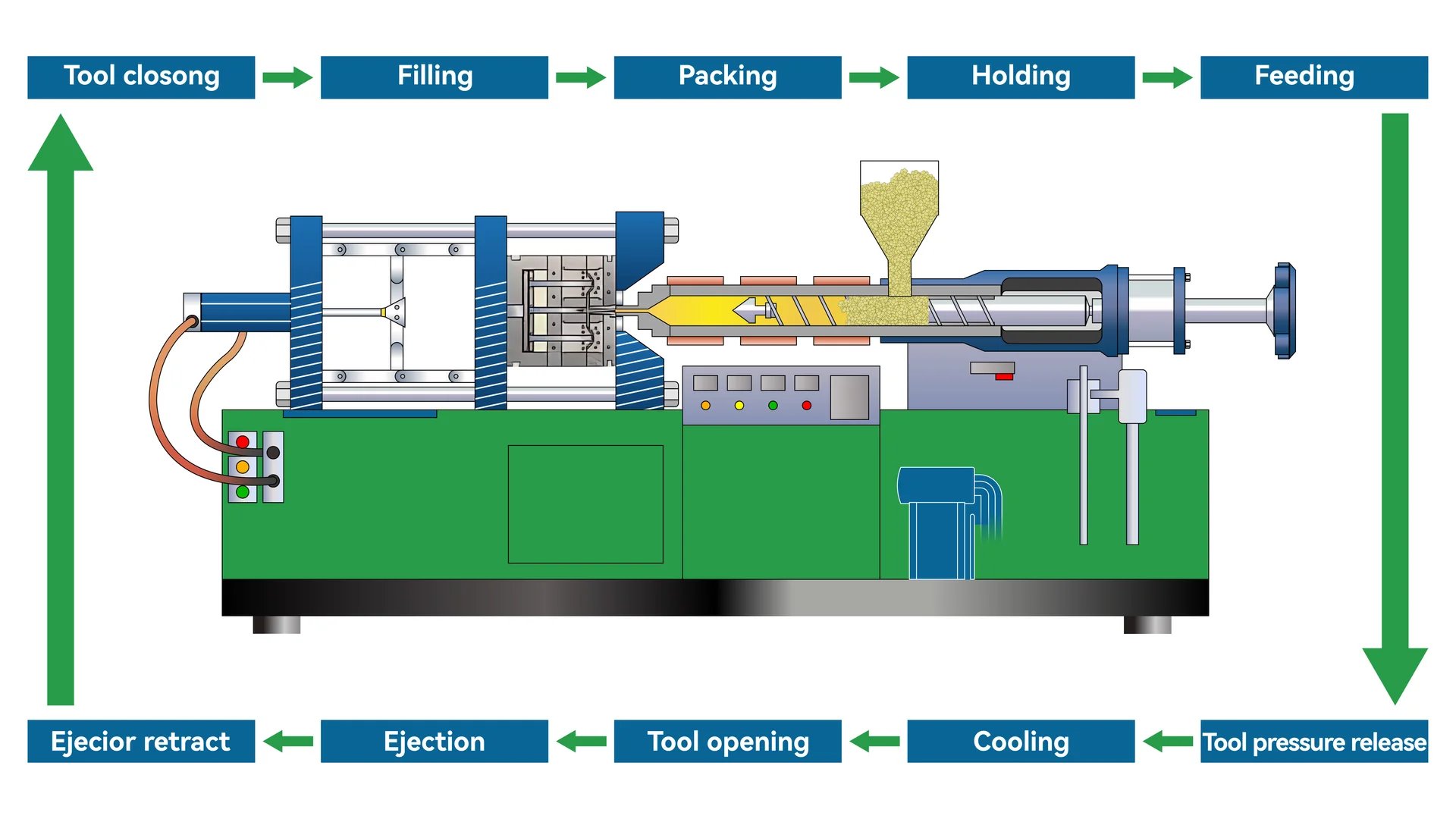
Understanding the Molding Process
I remember the first time I stood in a molding factory, mesmerized by the seamless dance of machinery. The process starts with humble thermoplastic pellets that are fed into a heated barrel3. Imagine these pellets as the raw potential of your next favorite gadget. They’re melted down with the help of heat and a rotating screw, much like how you’d stir a pot of soup, ensuring everything blends just right. This molten plastic is then injected into a mold cavity with precision and high pressure.
Table: Key Components of a Molding Machine | Component | Description |
---|---|---|
Heated Barrel | Melts the plastic pellets using heat and pressure | |
Screw | Rotates to mix and push the molten plastic forward | |
Mold Cavity | Custom-shaped space where the molten plastic is injected |
The Role of Desktop Injection Molding
Thinking back to my early days, desktop injection molding was my go-to for experimenting with new designs. These compact machines are perfect for prototyping and small-batch production—just what you need when you’re trying to turn an idea into reality without taking over an entire warehouse. They fit snugly on a workbench, perfect for someone like me who started in a cramped basement workshop. With less clamping force compared to industrial giants, they’re ideal for educational settings too, teaching future innovators about manufacturing.
Table: Comparison of Desktop vs. Industrial Machines | Feature | Desktop Machines | Industrial Machines |
---|---|---|---|
Size | Compact | Large | |
Clamping Force | Few to tens of tons | Hundreds to thousands of tons |
Step-by-Step Process Breakdown
- Material Loading: I always found this part like loading ammo in a slingshot – the thermoplastic pellets are placed into the hopper4.
- Melting: The pellets travel to the heated barrel and melt away, transforming into something entirely new.
- Injection: This liquid wonder is injected into the mold cavity through a nozzle, each drop finding its place like pieces of a puzzle.
- Cooling: Inside the mold, it cools down, slowly solidifying into its destined shape.
- Ejection: Finally, the mold opens, and out comes the finished part, ready to be admired or further refined.
Applications and Innovations
Every time I see miniatures or custom figurines, I’m reminded of how versatile molding technology is. It’s not just about function but also form, helping designers like us bring concepts to life swiftly for design verification. The innovations in this field are truly remarkable, enhancing precision and pushing boundaries in product design and manufacturing. If you’re keen to explore these applications further5, you’ll find that understanding molding techniques opens up endless possibilities across various industries.
Thermoplastic pellets are melted in a heated barrel.True
The pellets are melted by heat and a rotating screw in the barrel.
Desktop injection molding offers higher clamping force.False
Desktop machines have lower clamping forces than industrial ones.
What Are the Common Applications of Desktop Injection Molding?
Ever wonder how something as small as a desktop machine can revolutionize manufacturing? Let’s dive into the world of desktop injection molding and see where its magic is applied.
Desktop injection molding is ideal for creating small parts such as miniatures, mechanical components, and custom figurines, perfect for prototyping, small-batch production, and educational model crafting.
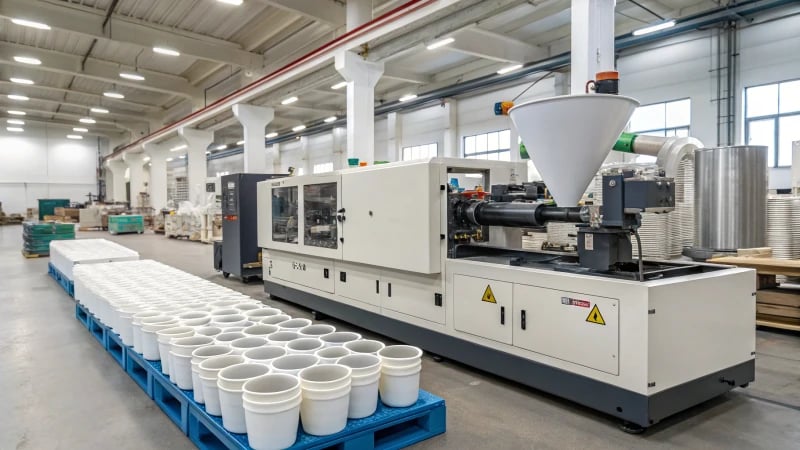
Understanding the Scope of Desktop Injection Molding
I remember the first time I saw a desktop injection molding machine in action. It was like witnessing a tiny miracle. These compact devices are ideal for workbenches or snug production spaces, and they bring a slice of industrial might to your tabletop. While they share the same operating principles as their larger counterparts, the scale is more approachable for everyday use.
Aspect | Industrial-Scale | Desktop |
---|---|---|
Clamping Force | Hundreds to thousands of tons | Few to tens of tons |
Size | Large | Compact (desktop-sized) |
Application | Mass production | Prototyping, small batches |
Prototyping and Small Batch Production
Back when I was knee-deep in a project needing rapid design iterations, desktop injection molding saved my sanity. This technology lets you whip up small plastic parts in no time, making it perfect for trial runs and niche product lines without breaking the bank. The ability to produce small plastic parts quickly allows designers to test and iterate designs rapidly.
Educational and Hobbyist Uses
In the classroom, these machines are educational powerhouses. I’ve seen students’ faces light up as they grasp the nuances of the injection molding process6 firsthand. They provide hands-on experience with the mechanics of molding and material behavior. And let’s not forget hobbyists—creating custom figurines has never been this accessible or fun!
Custom Design and Product Verification
When precision is key, desktop injection molding steps up to the plate. Whether it’s crafting custom-designed7 parts or verifying product designs with real-world models, this tech ensures that form and function are spot on before scaling up.
This technology isn’t just about making plastic bits; it’s about unlocking creativity and innovation. Whether you’re an educator, a hobbyist, or someone in need of precise prototypes, desktop injection molding offers a tangible bridge between ideas and reality.
Desktop injection molding is only used for educational purposes.False
It's also used in prototyping, small batch production, and hobbyist projects.
Prototyping is a primary application of desktop injection molding.True
It allows rapid testing and iteration of designs, making it ideal for prototyping.
Is Desktop Injection Molding Right for Your Project?
Ever tried fitting a factory on your desk? Welcome to desktop injection molding!
Desktop injection molding is ideal for prototyping, small-batch production, and education. It uses compact machines with lower clamping force for cost-effective, efficient production of small plastic parts.
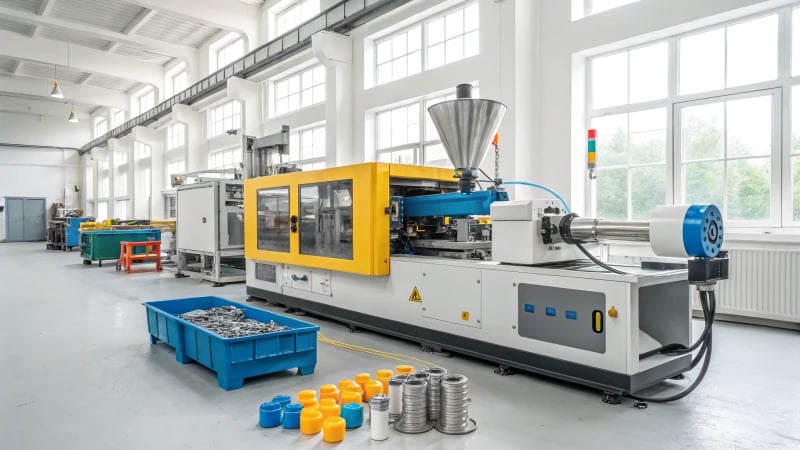
Understanding Desktop Injection Molding
Imagine having a mini factory right on your workbench—that’s what desktop injection molding feels like. These compact machines mimic their larger industrial counterparts but without requiring an entire warehouse to operate. With clamping forces ranging from a few tons to tens of tons, they are incredibly handy for prototyping, educational use, or when you just need a small batch of parts. I remember the first time I set one up in my workshop; it was like having my own little production line ready to bring my designs to life.
Feature | Desktop Machines | Industrial Machines |
---|---|---|
Size | Compact, fits on workbenches | Large, requires dedicated space |
Clamping Force | A few to tens of tons | Hundreds to thousands of tons |
Applications | Prototyping, education | Large-scale production |
How the Molding Process Works
The process is much like traditional injection molding—just scaled down. Thermoplastic pellets go into a heated barrel where they melt and mix, then they’re injected into a mold cavity. I still get a thrill watching the mold open and seeing the finished part emerge, just as perfect as I envisioned it.
- Material Feeding: Pellets are introduced into the heated barrel.
- Melting & Injection: Pellets are melted and injected into the mold.
- Cooling & Ejection: Plastic cools, solidifies, and is ejected.
Applications of Desktop Injection Molding
This approach shines when creating items like miniatures, mechanical components, or custom figurines. It’s particularly rewarding in educational settings—I’ve seen students’ eyes light up as they witness their designs come to life. Whether you’re looking to prototype quickly or run a small production line, desktop injection molding offers a unique blend of efficiency and accessibility.
Explore if desktop injection molding aligns with your project requirements by evaluating your need for quick prototyping and the scale of production desired. Consider how its benefits match your specific design goals and manufacturing constraints. For further insights on this technology, check out DIY injection molding options8 to see if a more hands-on approach might suit your project needs.
Desktop injection molding is suitable for large-scale production.False
Desktop machines have lower clamping force, ideal for small-batch production.
Desktop injection molding can be used for educational purposes.True
It allows students to learn about manufacturing principles firsthand.
Conclusion
Desktop injection molding uses compact machines to melt thermoplastics and create small parts, ideal for prototyping, education, and hobbyist projects with lower clamping forces than industrial models.
-
Understand the detailed process that desktop machines replicate on a smaller scale, ensuring familiarity with key stages. ↩
-
Learn how these machines can enhance your prototyping capabilities, offering speed and precision in creating custom parts. ↩
-
Learn how a heated barrel functions in melting plastic efficiently for molding. ↩
-
Discover how hoppers feed raw materials into injection molding machines. ↩
-
Explore diverse applications of desktop injection molding in various fields. ↩
-
Learn how educational institutions utilize desktop injection molding to teach students about manufacturing processes. ↩
-
Explore how designers use this technology to create unique, customized components for product verification. ↩
-
Explore DIY options for desktop injection molding to see if setting up a personal system might benefit your specific project needs. ↩