DESIGN
blog & article
read our latest newsletter
Whether you’re curious about material selection, product design, mold design, mold making and injection molding, feel free to ask us anything. Our team is ready to provide the guidance and insights you need.
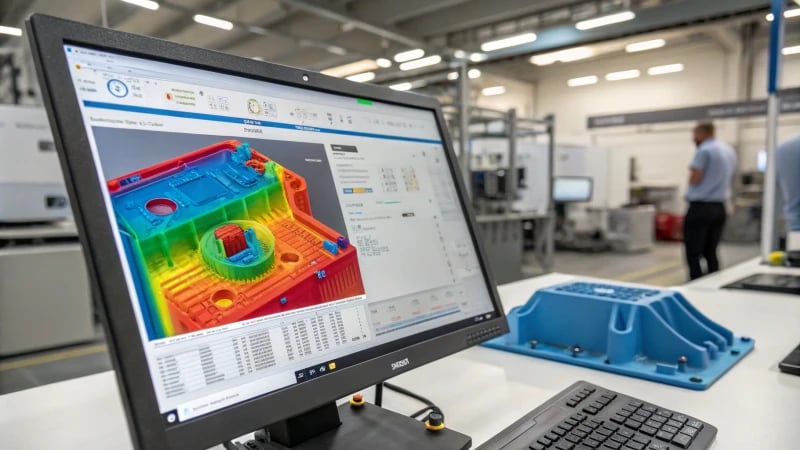
What Are the Key Benefits of Mold Flow Analysis?
Mold Flow Analysis is a vital tool in injection molding that simulates the process to optimize mold design, predict defects, enhance product quality, and improve production efficiency.
DESIGN

What Are the Best Layout Forms for Cooling Channels in Mold Cooling Systems?
This article explores the best cooling channel layouts for injection molding, including straight-through, circular, partitioned, and inlaid designs. Each layout offers unique benefits for optimizing cooling efficiency and product quality.
DESIGN
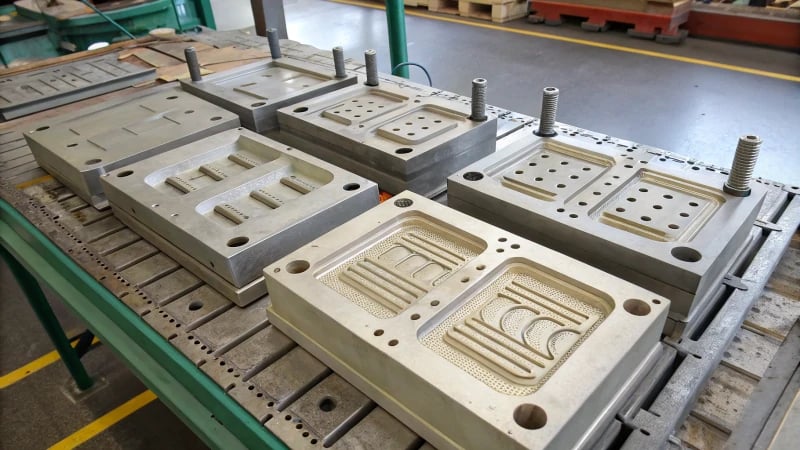
What Factors Should You Consider When Choosing a Cooling Channel Layout in Mold Design?
Choosing the right cooling channel layout in mold design is crucial for optimizing cooling efficiency, product quality, and minimizing defects. Factors like product shape, wall thickness, and precision requirements significantly influence this decision.
DESIGN
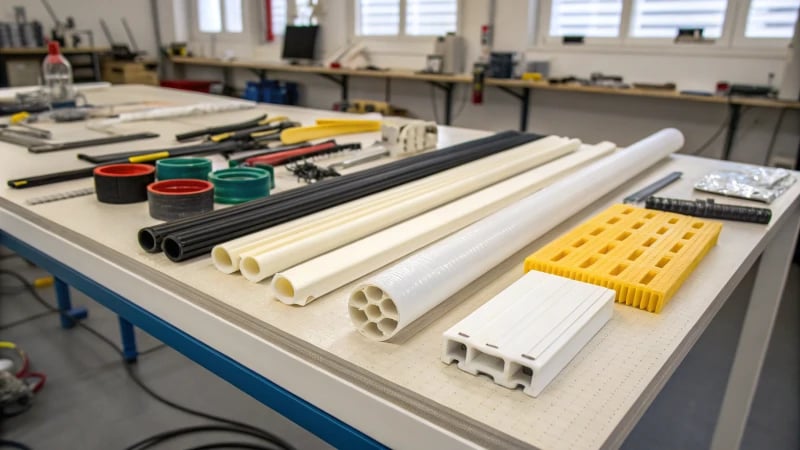
What Shape Can You Expect from the Final Extruded Product?
This article explores the extrusion process, detailing how it produces continuous shapes like pipes, rods, and special profiles. It highlights the benefits of design flexibility, cost-effectiveness, and material selection in manufacturing.
DESIGN
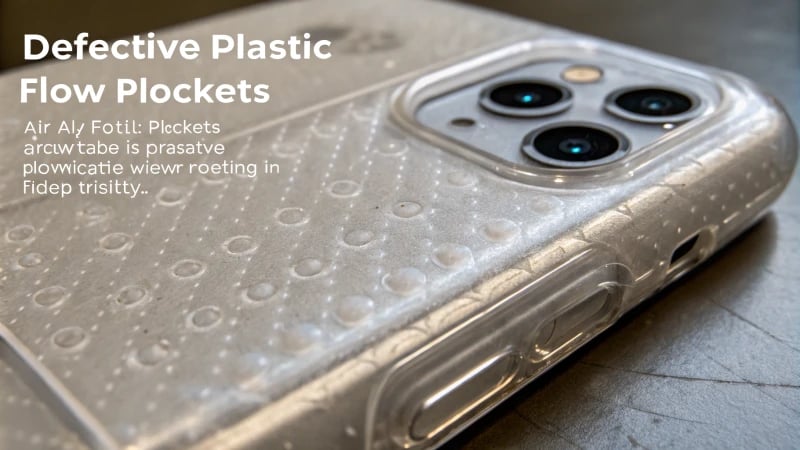
How Does Poor Mold Exhaust Design Affect Plastic Products?
This article discusses the significant impact of poor mold exhaust design on plastic products. It highlights how inadequate venting causes air pockets, flow marks, and uneven density, leading to aesthetic flaws and structural weaknesses. The piece emphasizes the importance of ...
DESIGN
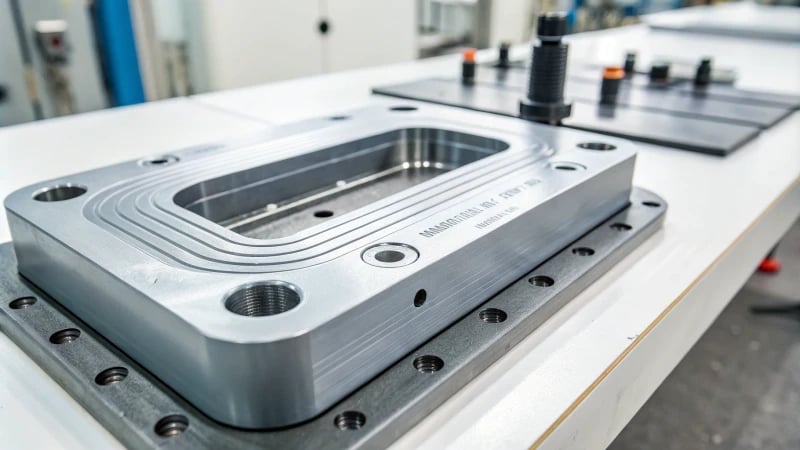
How Can Mold Design Help Reduce Fusion Lines?
This article explores how careful mold design can minimize fusion lines in injection molded products. Key strategies include optimizing gate placement for uniform melt flow, designing efficient runner systems to maintain stable flow, and implementing proper venting techniques to prevent ...
DESIGN
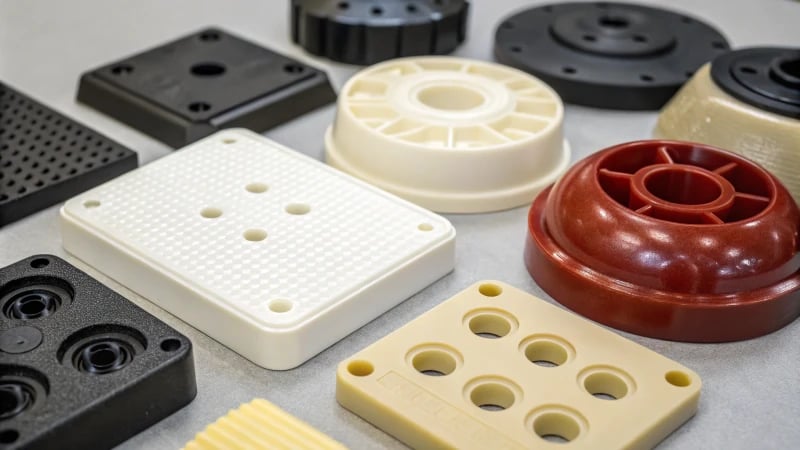
How Do Different Gate Types Influence Product Appearance?
This article explores how various injection molding gate types impact the final appearance of products. It discusses direct sprue, side gating, spot gates, submerged gates, and scalloped gates—each with unique advantages and disadvantages. Understanding these differences is crucial for designers ...
DESIGN
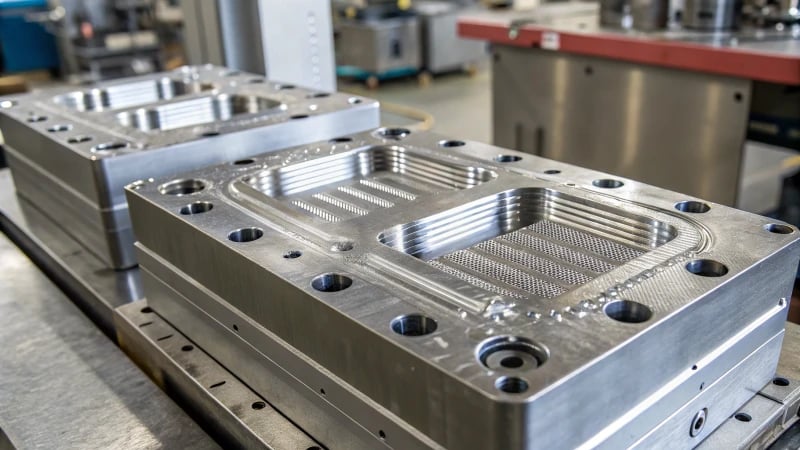
How Does the Design Principle of the Latent Gate Work?
The submerged gate is an advanced mold design feature that significantly enhances the appearance and functionality of molded parts. By positioning the feeder on the mold's parting surface and allowing it to enter diagonally into the cavity, submerged gates minimize ...
DESIGN
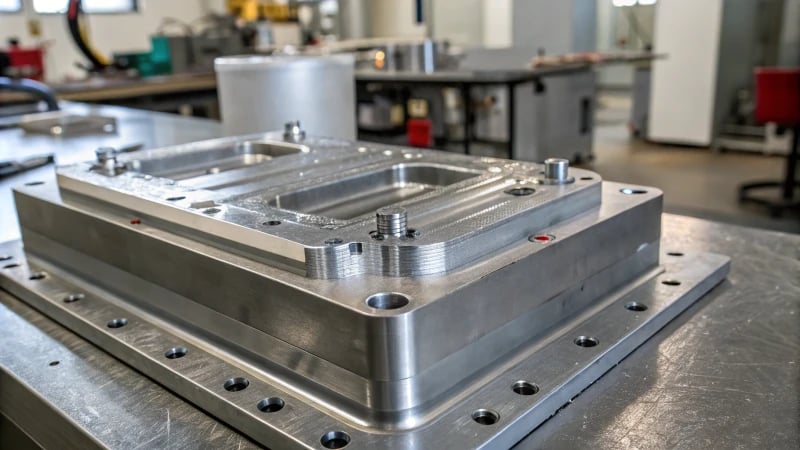
How Do You Determine the Location of the Parting Line in Molding?
This article explores how to determine the optimal location for parting lines in molding. It emphasizes the importance of considering product shape, functionality, and manufacturing ease. Proper placement can significantly enhance both the aesthetic appeal and functional integrity of molded ...
DESIGN
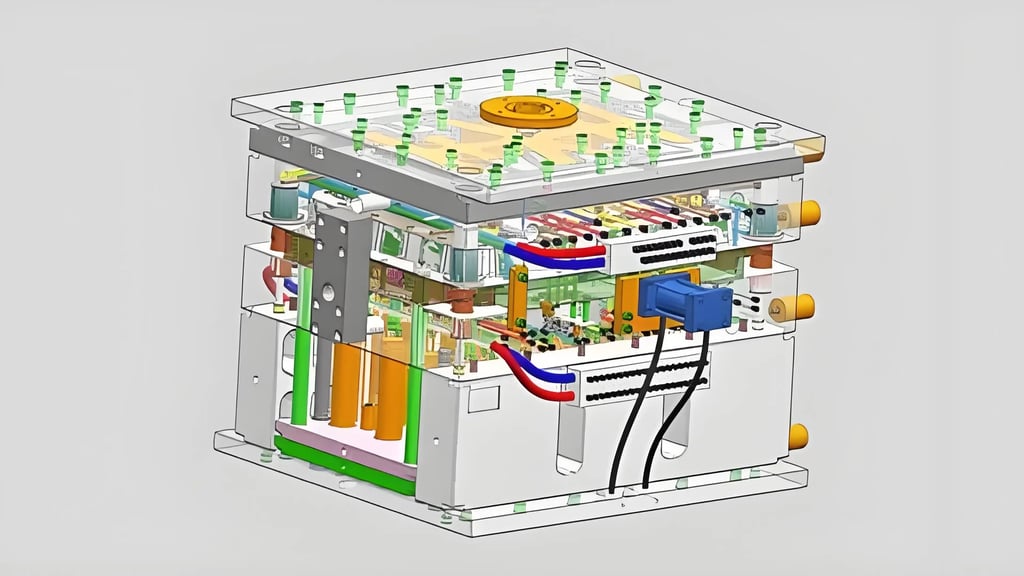
How Can Simulation Software Enhance Product Cooling Analysis?
This article explores how simulation software significantly enhances product cooling analysis. It details the steps involved in setting up simulations, including model creation, meshing, material property settings, cooling system design, boundary condition setup, and result analysis. By utilizing tools like ...
DESIGN
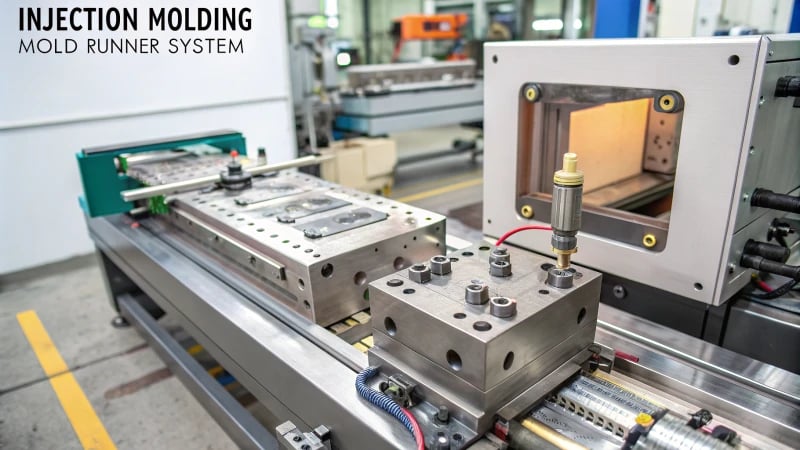
What Factors Should You Consider When Designing a Mold Runner System?
When designing a mold runner system, several critical factors must be considered to ensure efficiency and quality. Key elements include understanding material flow characteristics, which dictate the appropriate size and shape of runners based on the melt flow rate (MFR) ...
DESIGN
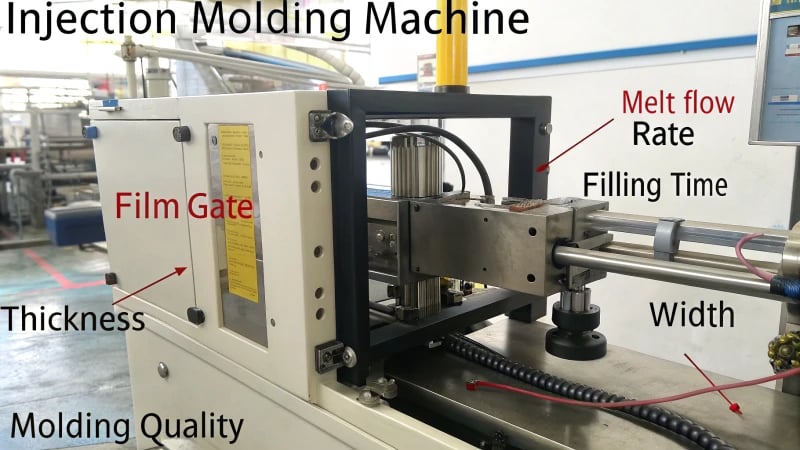
How Does the Thickness and Width of a Film Gate Relate to Each Other?
In injection molding, the dimensions of a film gate—its thickness and width—play a crucial role in determining the flow characteristics of melted materials. Properly sized gates enhance the efficiency of mold filling, improve product quality by ensuring uniform wall thickness, ...
DESIGN
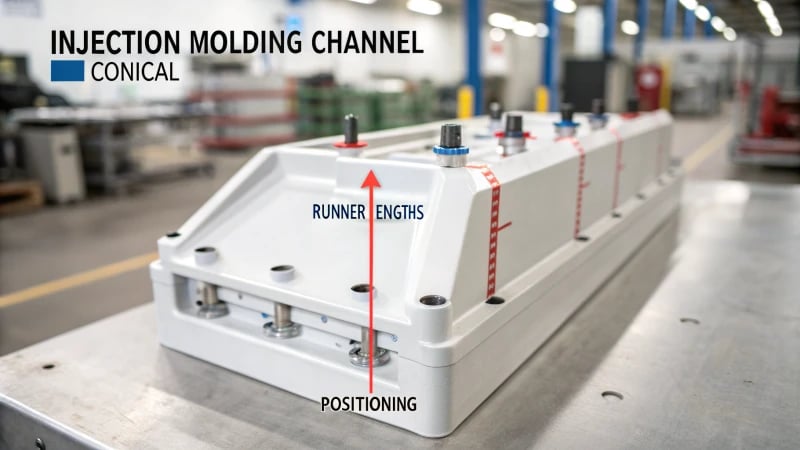
How Does Main Channel Design Affect Mold Injection Efficiency?
This article explores how the design of the main channel in injection molding affects efficiency. Key factors include the shape (preferably conical), size (ideally 0.5-1mm larger than the nozzle), length (shorter is better to reduce pressure loss), and layout (symmetrical ...
DESIGN
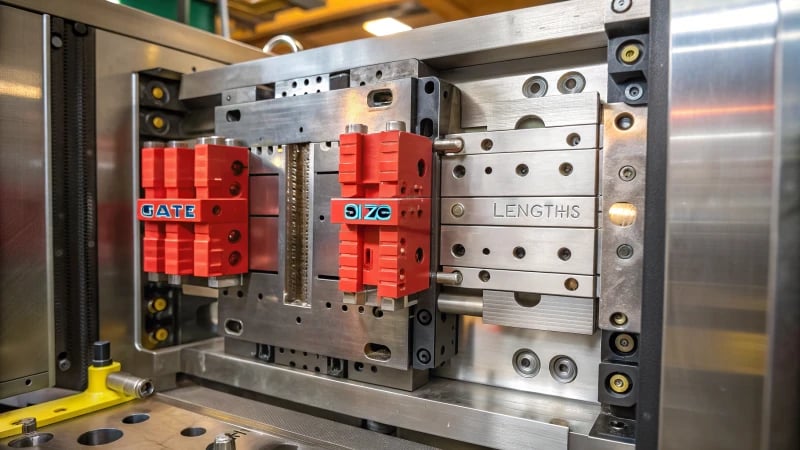
How Does the Size and Length of the Gate Affect Injection Molded Products?
The size and length of gates in injection molding play a critical role in determining the efficiency of melt flow, product appearance, internal stress levels, and overall production costs. Larger gates enhance filling efficiency but may lead to surface defects ...
DESIGN
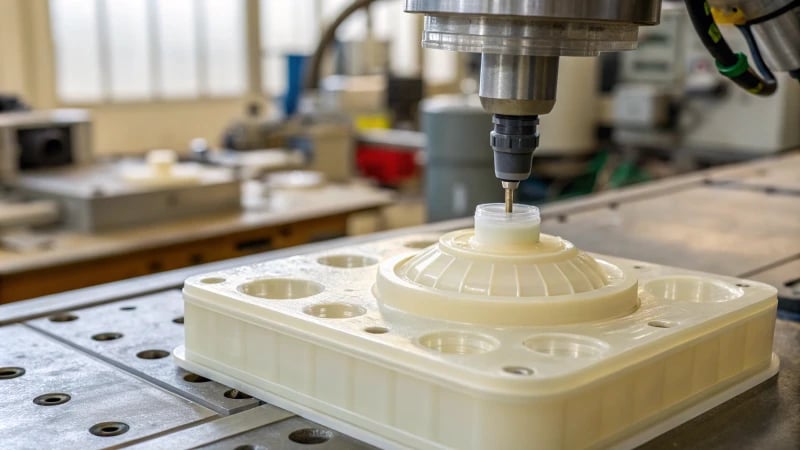
How Can You Avoid Flow Marks on Products by Designing the Gate Position?
This article explores how gate position design in injection molding can significantly reduce flow marks on products. By strategically placing gates, manufacturers can ensure a smooth melt flow that avoids eddy currents and surface imperfections. The importance of understanding melt ...
DESIGN
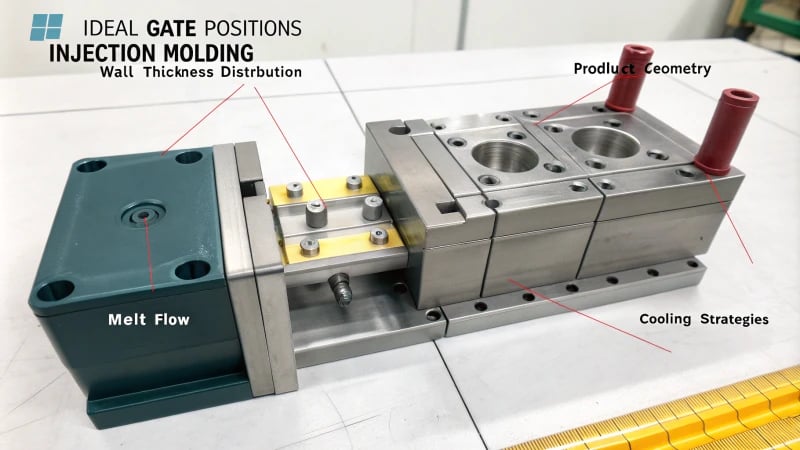
How Can You Design Gate Position to Prevent Shrinkage Marks on Products?
This article discusses the importance of gate placement in injection molding to prevent shrinkage marks on products. It emphasizes that correct positioning ensures uniform melt distribution and reduces pressure loss, particularly for items with uneven wall thickness. By strategically placing ...
DESIGN
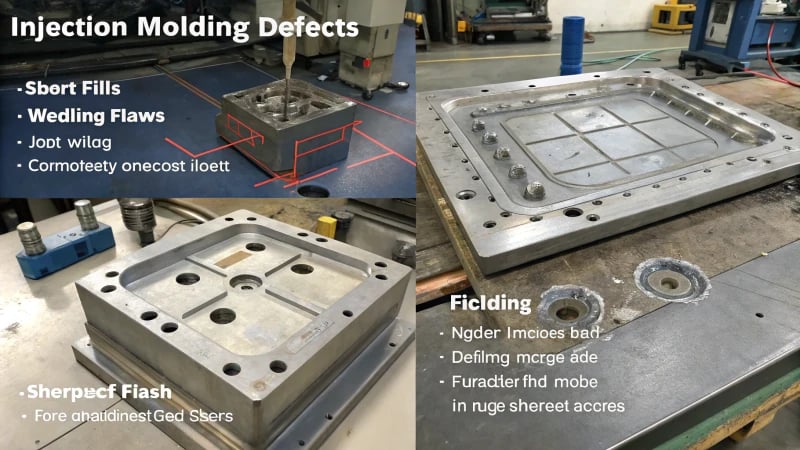
How Does Improper Injection Pressure Adjustment Cause Molding Defects?
This article explores how improper injection pressure adjustments during the molding process can result in various defects such as short shots, flash, shrinkage marks, welding marks, jet marks, and bubbles. Each defect arises from either insufficient or excessive pressure settings ...
DESIGN
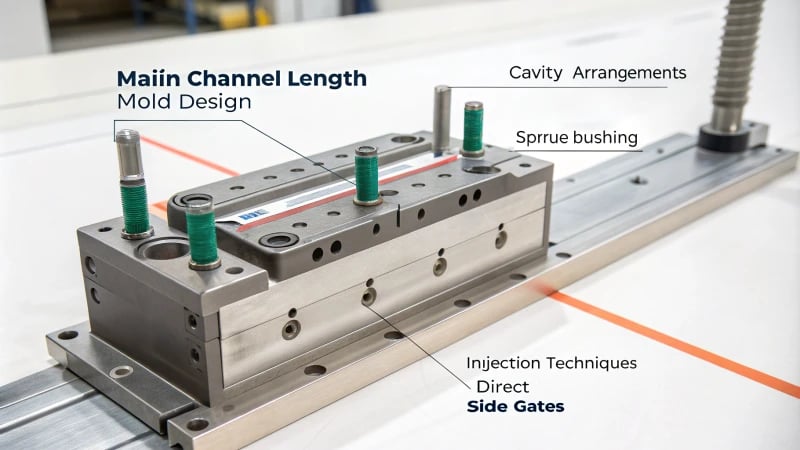
What Are the Best Methods to Ensure the Shortest Length of the Main Channel?
This article explores the best methods for ensuring the shortest length of the main channel in mold design. Key strategies include optimizing cavity layouts to minimize flow distances, strategically positioning the sprue bushing for efficient melt flow, and selecting appropriate ...
DESIGN
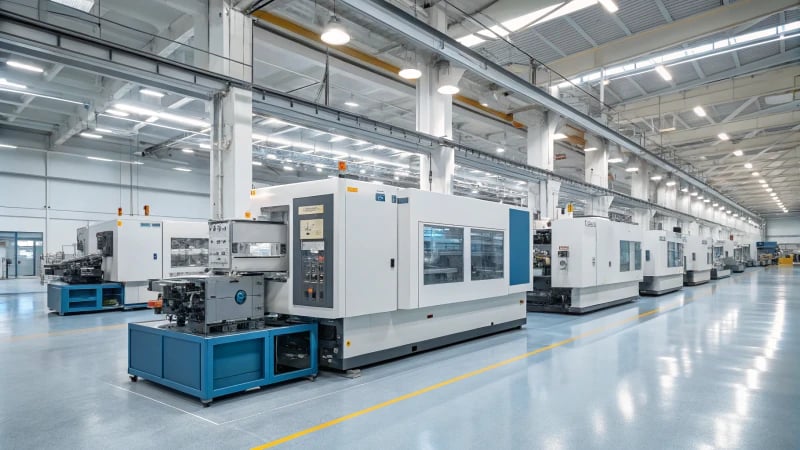
What Impact Do Mold Design Issues Have on Injection Molding Process Parameters?
This article explores how mold design issues affect the injection molding process. It highlights the importance of gate size, runner system layout, and exhaust design in optimizing production efficiency and reducing defects. By understanding these elements, designers can enhance the ...
DESIGN
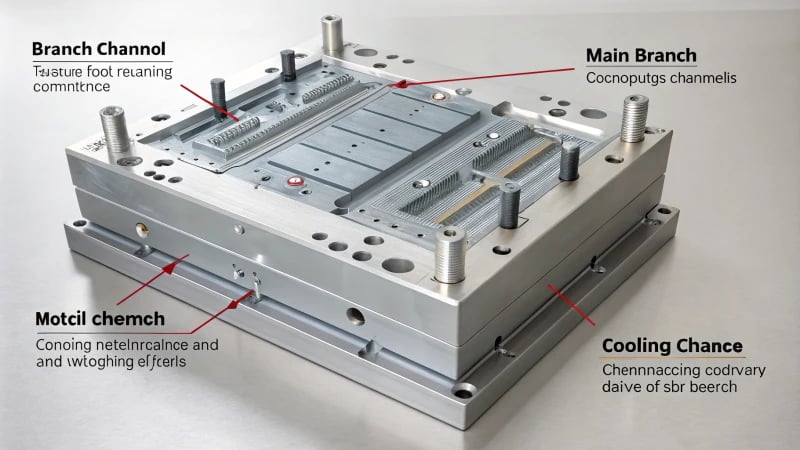
How Does the Design of Main and Branch Channels Affect Mold Service Life?
This article explores how the design of main and branch channels in injection molds affects their service life. Key factors such as channel size, surface smoothness, taper angles, and alignment with cooling systems are crucial for reducing wear and thermal ...
DESIGN
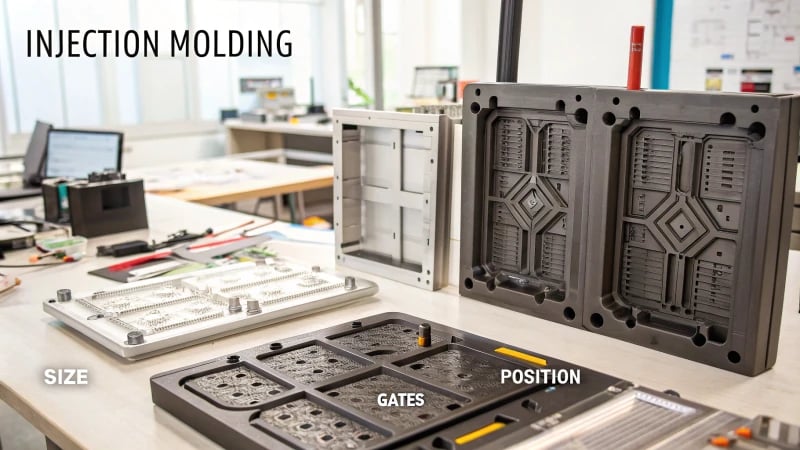
How Does Gate Design Impact Injection Molding Process Parameters?
This article explores how gate design impacts the injection molding process by influencing key parameters such as pressure, speed, and time. It discusses the importance of gate size, position, and quantity in optimizing material flow and minimizing defects like weld ...
DESIGN
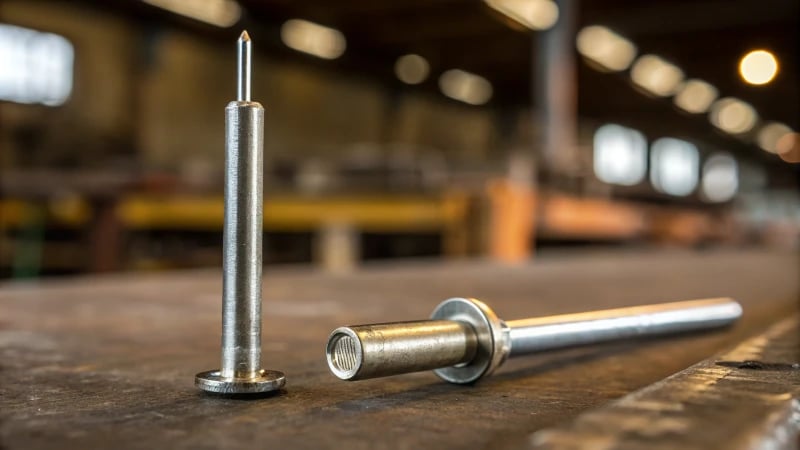
What Distinguishes an Ejector Pin from a Sleeve Pin?
This article explores the differences between ejector pins and sleeve pins in mold design. Ejector pins are straightforward cylindrical rods ideal for simple structures like bottle caps, leaving minimal marks. In contrast, sleeve pins consist of a hollow sleeve and ...
DESIGN
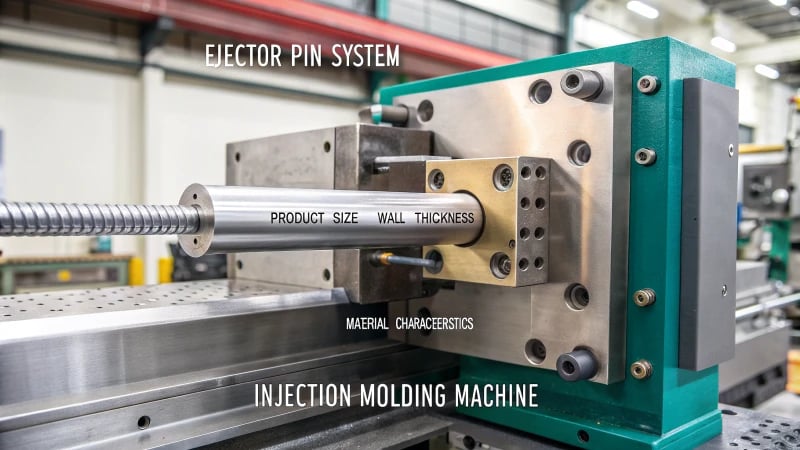
What Factors Influence the Ejection Force of an Ejector Pin?
Understanding the factors influencing ejection force in injection molding is crucial for effective mold design. Key elements include product size and shape, wall thickness, material characteristics, and the design of the ejector mechanism. Larger products typically require greater ejection forces ...
DESIGN
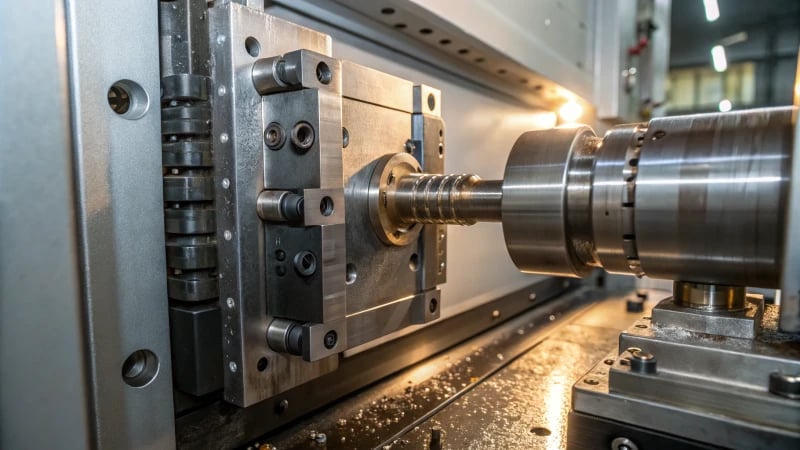
What Are the Key Characteristics and Benefits of a Film Gate?
Film gates, also known as thin-sheet or burr gates, play a crucial role in injection molding by providing excellent flow characteristics. They ensure even melt distribution, which is essential for producing large flat or thin-walled plastic parts without defects. The ...
DESIGN
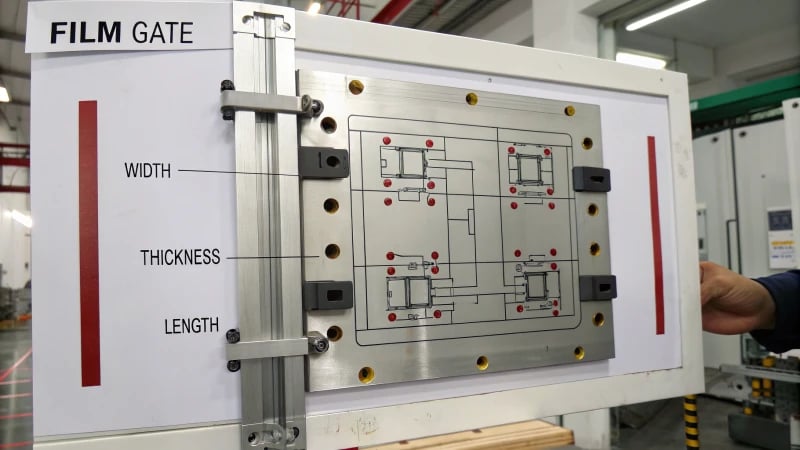
How Can You Determine the Specific Size of a Film Gate?
Determining the correct size of a film gate is crucial in mold design. This article outlines key factors such as product width, wall thickness, material behavior, and gate length. Gate width typically ranges from 25% to 100% of the product ...
DESIGN
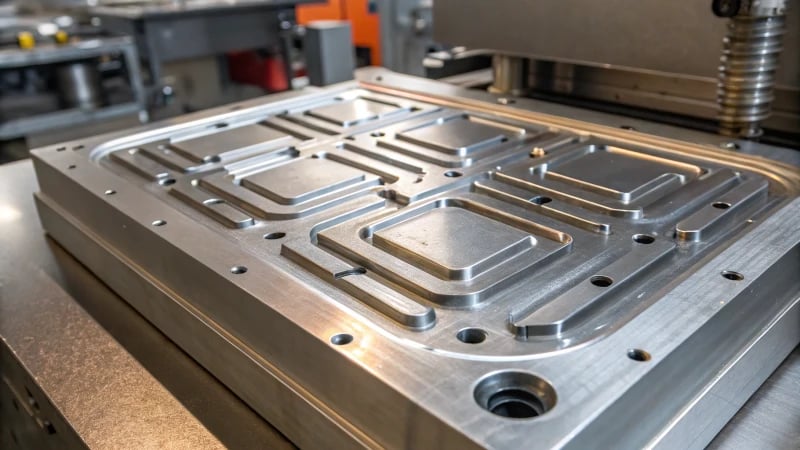
How Does the Design of Main and Branch Channels Influence Mold Production Costs?
This article explores how the design of main and branch channels in mold production affects costs. Key factors include material consumption, processing complexity, and maintenance requirements. Effective channel design can lead to significant savings while maintaining high quality. By understanding ...
DESIGN
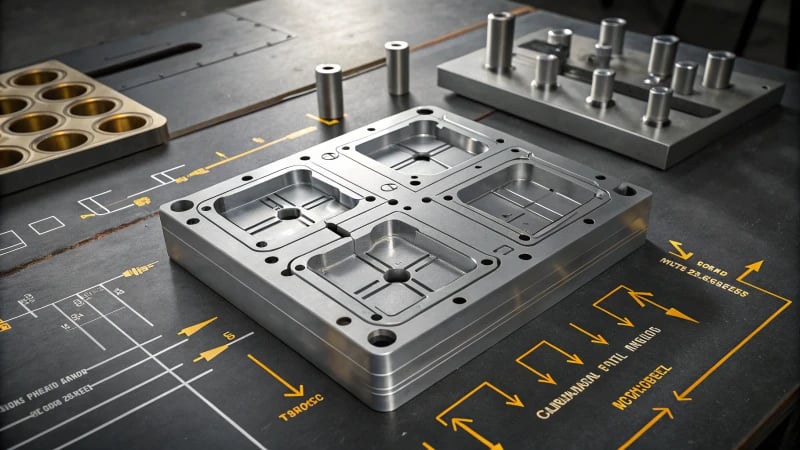
What Are the Design Standards for Main and Branch Channels in Mold Design?
In mold design, adhering to specific standards for main and branch channels is crucial for achieving smooth plastic flow. This article delves into the importance of channel shape, size, layout, and material choice. The main runner typically features a conical ...
DESIGN
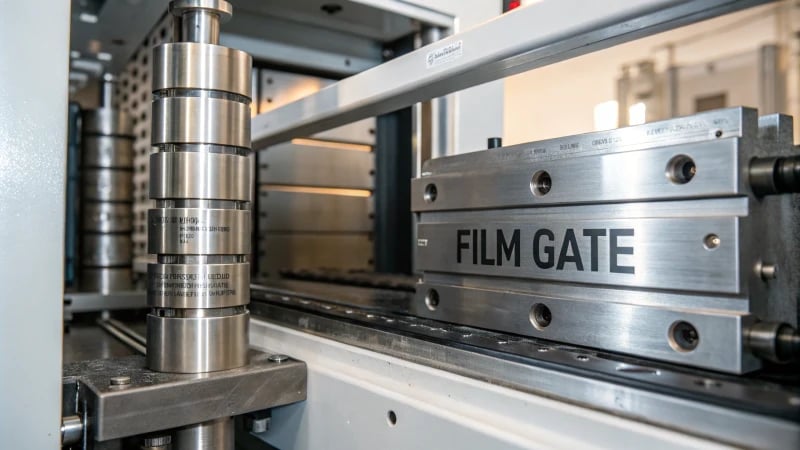
What is the Typical Gate Length of a Film Gate?
Understanding the typical gate length of a film gate is crucial in injection molding. Ranging from 0.5 to 2mm, this length minimizes pressure and heat loss during the process. Smaller products with thin walls require shorter gates (0.5-1mm) for efficient ...
DESIGN
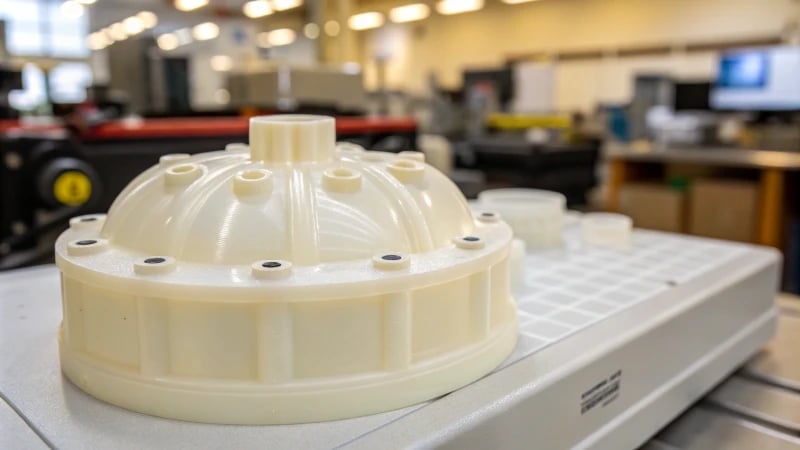
How Can Mold Design Optimization Reduce Flow Mark Defects in Injection Molded Products?
This article explores how optimizing mold design can effectively reduce flow mark defects in injection molded products. Key strategies include refining runner system shapes and sizes to minimize resistance, selecting appropriate gate types for even melt distribution, and implementing effective ...
DESIGN
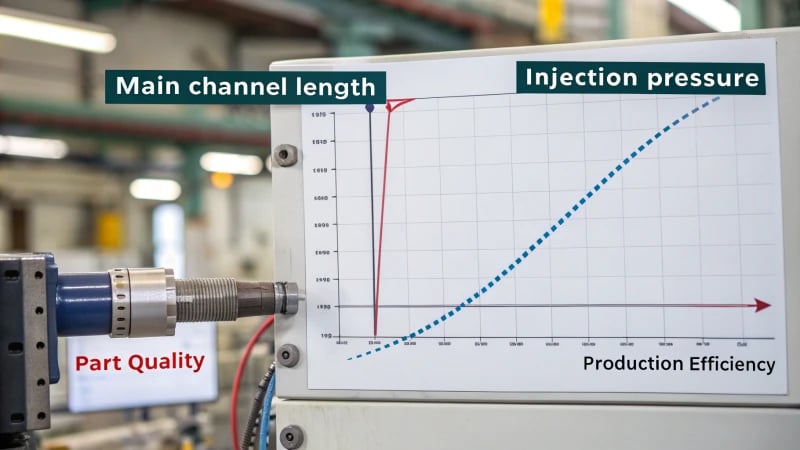
How Does the Main Channel Length Affect Mold Injection Pressure?
This article explores how the length of the main channel in injection molding affects injection pressure requirements. Longer channels increase viscous resistance, necessitating higher pressures for proper mold filling. This can lead to challenges such as uneven pressure distribution, which ...
DESIGN