Have you ever thought about how something as complex as mold design fits together so perfectly?
In mold design, standards focus on the shape, size and layout of main and branch channels. The goal is smooth plastic flow. High-quality products depend on smooth flow. These rules are very important for efficient and uniform injection molding. Efficiency matters. Consistency is key.
I remember the first time I worked on mold design at my job. It felt like solving a complex puzzle. Understanding the details of mold channels is very important. Each craft has its secrets. Basic standards lay the groundwork. Specifics like picking the right materials and balancing flow really matter. These small details turn a good mold into something great. Let’s explore these parts more deeply.
Main channels in mold design must be straight.False
Main channels can have bends to optimize flow paths, not necessarily straight.
Material choice affects channel efficiency in mold design.True
Different materials have varying thermal and flow properties, impacting efficiency.
How Do Shape and Size Affect Main Runner Efficiency?
Have you ever thought about how the form and dimensions of a main runner affect mold efficiency? Join me on a journey through the intriguing world of mold design.
The shape and size of a main runner are crucial for mold efficiency. They influence how plastic melt moves. A cone-shaped design with exact measurements leads to a smooth flow. This reduces problems during production.
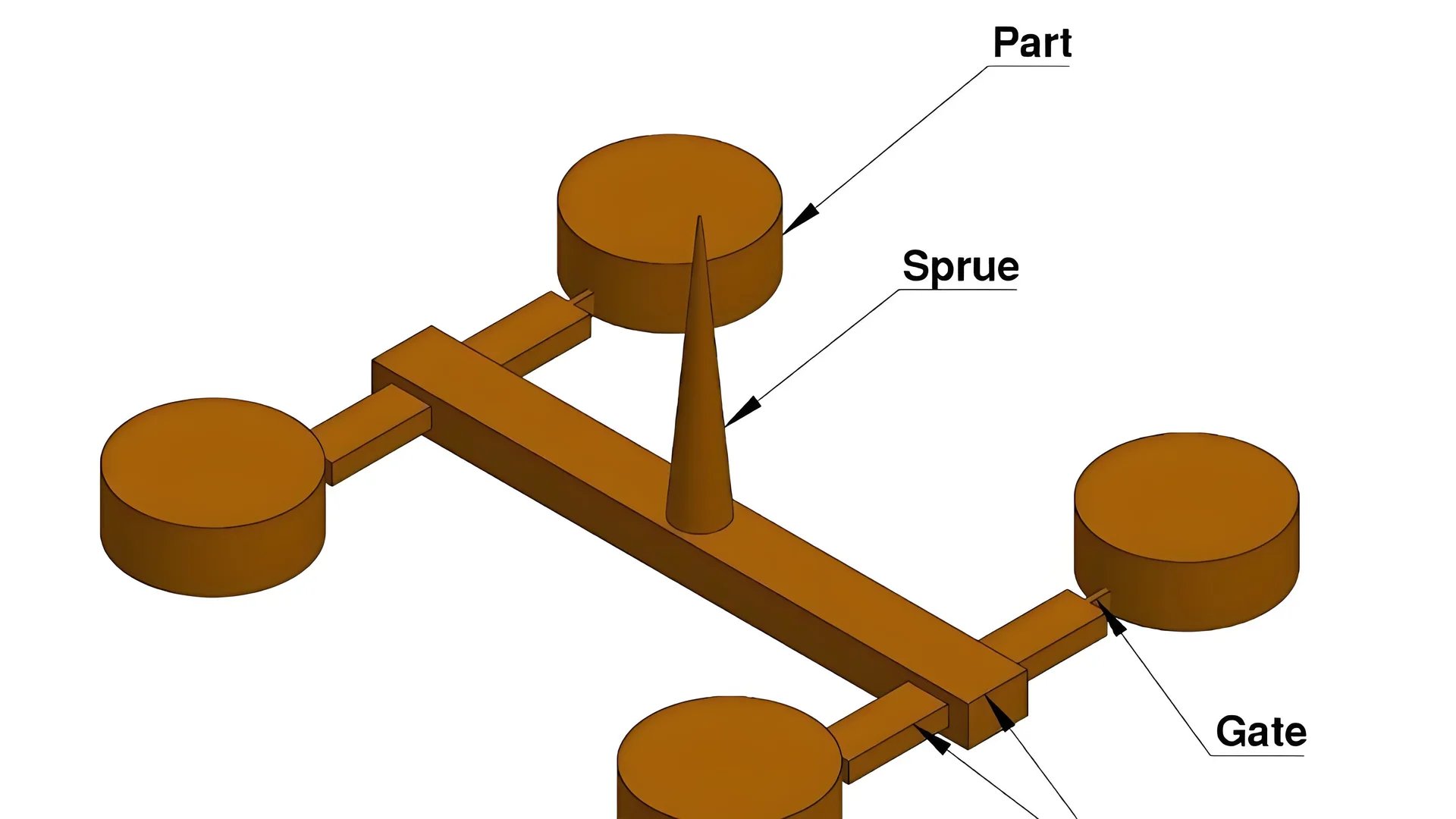
Shape Considerations in Main Runner Design
Picture a puzzle where each piece has to fit perfectly. That’s how designing a main runner felt to me. The conical shape, with a cone angle between 2°-6°, was like finding that perfect edge piece – it just clicked. This shape isn’t just for looks; it plays a vital role in directing the plastic melt properly, leading to a steady flow. I read design standards1 that stressed a rounded corner at the large end. This design choice made perfect sense when I saw how smoothly it helped material flow.
Shape | Benefits |
---|---|
Conical | Enhances directional flow |
Circular | High efficiency but challenging to process |
Size Specifications and Their Impact
The diameter of the main runner is another piece that must fit well. I discovered that the small end should be 4-8mm, which is a bit bigger than the nozzle for easy removal of condensate. This sizing method helps reduce cold material recovery, pressure drop, and heat loss. It’s like tuning an instrument perfectly; when done right, everything works in harmony.
Position and Layout Efficiency
Positioning the main runner at a right angle to the mold parting surface taught me about balance. It ensures the layout avoids direct strikes on small cores or inserts, preventing damage. The efficient layout design2 considers the whole mold cavity, making sure each section fills properly.
Material and Processing Standards
I remember learning about using top-quality steel for the main runner due to its repeated exposure to hot plastic melt. It’s like giving a knight the finest armor – crucial for enduring tough conditions. Keeping the gate sleeve fixed to avoid rotation during production was another important lesson. This knowledge made a big difference in maintaining performance over time.
Considering these factors – shape, size, position and material – has allowed me to improve main runner performance in my designs. Production results are better, balancing looks and function for consumer electronics.
For anyone curious, detailed resources or mold design guides3 offer more information on industry rules and best methods.
Conical runners improve plastic melt flow consistency.True
Conical shape enhances directional flow and maintains consistent flow rate.
Circular runners are easier to process than conical ones.False
Circular runners are efficient but challenging to process compared to conical ones.
Why is runner layout so crucial in mold design?
Remember when a little change completely altered your day? That’s what runner layout achieves in mold design. It plays a big role.
Runner layout in mold design is crucial for even material flow. It reduces problems. It also increases production efficiency. Part quality is impacted by this. Cycle time is affected as well. Material usage changes too. It probably influences manufacturing results a lot.
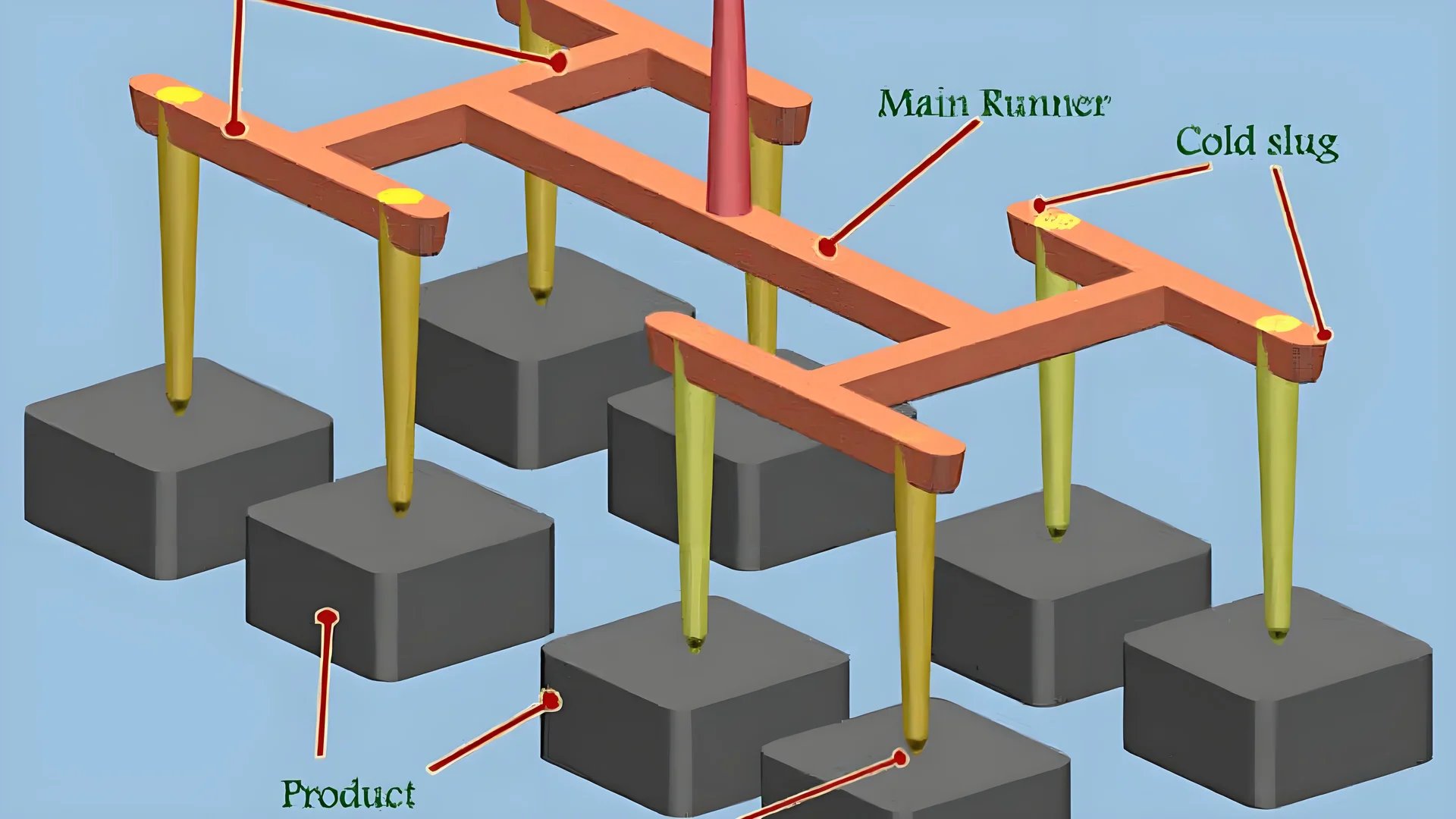
The Role of Runner Layout in Material Flow
A river flows around rocks, making calm spots and swirls. This is like how hot plastic moves through a mold. The runner layout helps guide this flow evenly. Good design spreads the material smoothly, like butter on warm toast, avoiding problems like short shots or sink marks. When I started with molds, I saw that a balanced runner layout felt like an orchestra playing perfectly. Everything worked well together.
For example, using a balanced runner layout can help achieve uniform pressure across multiple cavities, leading to consistent part quality.
Impact on Production Efficiency
The first time I noticed runner design’s effect on costs was eye-opening. Adjusting the runner system cut cycle times and energy use. More products came out quickly with less waste. It’s like a shortcut saving time and fuel. A well-sized runner works just like that.
Efficient runner design can significantly enhance production by minimizing pressure loss and heat dissipation, which translates into cost savings and increased production rates. For instance, a properly sized runner4 reduces material waste and streamlines demolding processes.
Design Standards for Runners
For me, knowing these standards is like a trusty recipe leading to great results. The main runner acts as the backbone. It is conical to help material flow, fitting the injection machine nozzle right to avoid errors.
Here’s a brief look at key measures:
Parameter | Main Runner | Branch Runner |
---|---|---|
Shape | Conical | Circular/U-shaped |
Diameter | 4-8mm | 2-10mm |
Angle | 2°-6° | 5°-10° |
These standards ensure that the molten plastic can fill each cavity efficiently, maintaining product quality.
Challenges in Runner Design
Creating a good runner layout feels like solving a tricky puzzle. Balancing runner length to save material while keeping proper flow is tough but important. I often use advanced CAD tools to see designs clearly. These tools act like a crystal ball, helping spot issues early.
Advanced CAD tools have really helped improve mold designs, ensuring they are precise and effective. Consider exploring advanced CAD tools5 to refine your mold designs for enhanced precision.
Learning these elements lets designers craft molds that work well and create high-quality products. In Jacky’s Canadian company, dealing with issues like uneven filling or wasted material needs full understanding of these details.
Additionally, choosing materials that resist high heat and repeated use is crucial. Heat-treated steel for runners means they last long and keep product quality high during long production runs—it’s like picking good hiking boots that handle tough paths and keep you comfortable.
These factors show how important runner layout is for great mold designs and smooth production cycles.
Balanced runner layout reduces defects like short shots.True
A balanced runner layout ensures uniform pressure, reducing defects.
Runner design has no impact on production efficiency.False
Efficient runner design enhances production by reducing cycle time.
How Does Material Selection Influence Channel Durability?
Do you often question how your selected material affects the strength of mold channels?
Choosing the right material greatly affects how long a channel lasts. It really improves the ability to handle wear, heat and force. Steel of high quality is a common choice. It balances these qualities very well. This extends both the channel’s life and its performance.
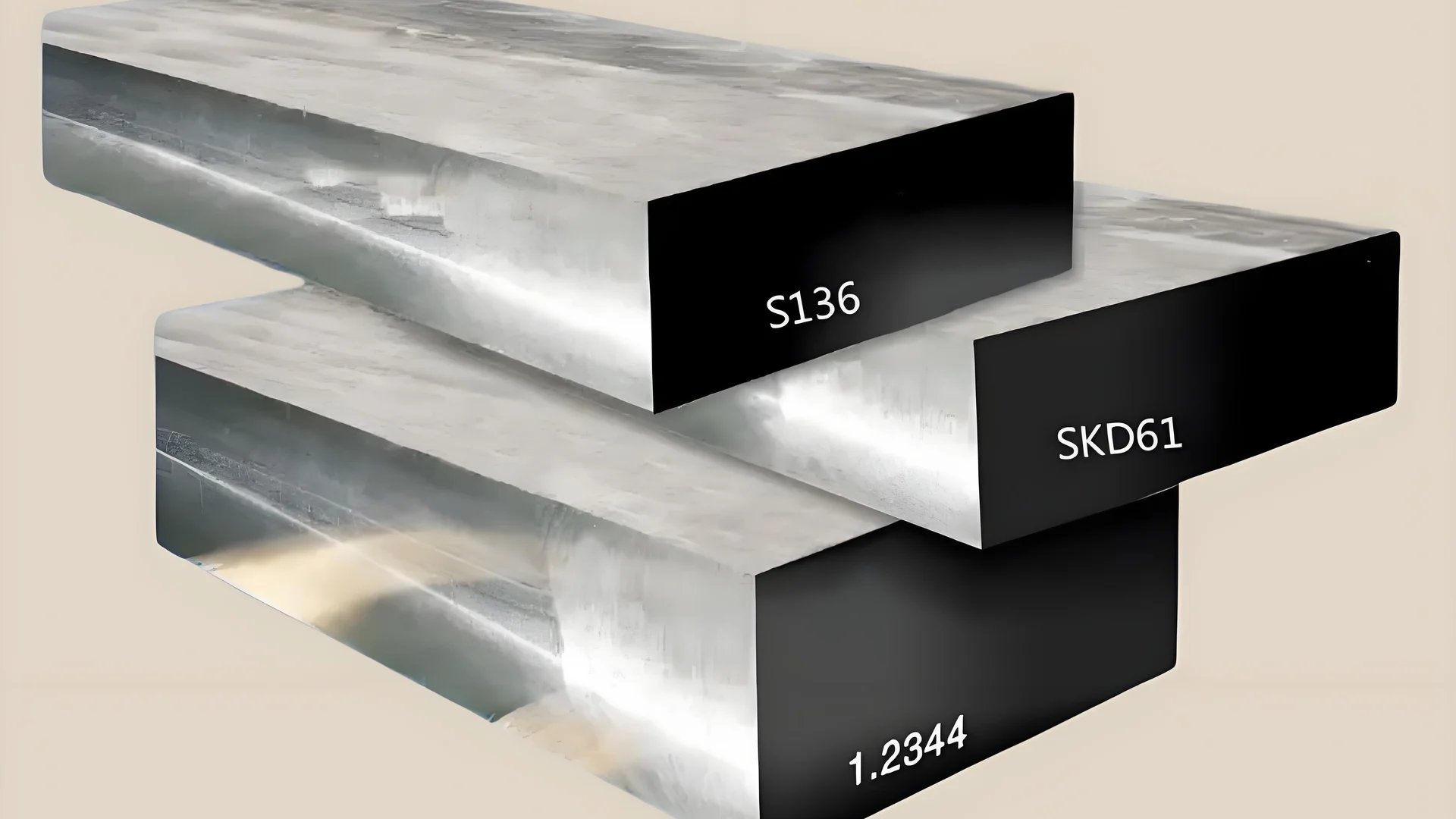
Importance of Material Properties
There was a moment during a project when I saw how important choosing the right material really is. Imagine this: I was designing a mold and picked a cheaper material. Bad choice. The channels quickly wore out, causing production stops and quality problems. From then on, I’ve understood the need to focus on material properties like how well they pass heat, their toughness, and their ability to resist corrosion.
- Thermal Conductivity: At first, I didn’t truly grasp the need for good thermal conductivity. Picture a hot summer day; materials should spread heat well, just like wearing clothes that let air in.
- Hardness: Hardness compares to sturdy boots – tough and long-lasting.
- Corrosion Resistance: Like a raincoat protects you, it guards channels from breaking down in harsh environments.
Comparing Common Materials
Once, I talked with a coworker about materials. We made a short comparison list that shows the strengths and weaknesses of usual materials:
Material | Thermal Conductivity | Hardness | Corrosion Resistance |
---|---|---|---|
Steel | Moderate | High | Moderate |
Aluminum | High | Low | High |
Plastic | Low | Low | High |
In my experience, steel6 usually stands out in mold design because it is very strong and works well in many conditions.
Impact on Channel Design Standards
In my work, following channel design standards is necessary. It’s like trying to fit a square peg into a round hole – picking materials that meet these standards ensures a perfect fit and smooth function.
- Shape and Size: I’ve observed how materials control our ability to keep exact shapes and sizes in designs.
- Length and Layout: Strong materials allow fewer supports, making the design process easier.
Selecting materials that align with these standards is vital to optimizing channel performance and longevity.
Factors Affecting Material Selection
Picking the right material is not just about technical details; it’s also about knowing the unique needs of your project. Here are some factors I’ve learned to consider:
- Operational Environment: Early in my career, I learned that high temperatures or corrosive environments need specific materials.
- Cost Considerations: Finding a balance between strength and cost feels like a tightrope walk – hard but possible with practice.
- Manufacturing Compatibility: Think about baking a cake without the correct-size pan; selecting the right materials is essential for smooth manufacturing.
When high temperatures are likely, choosing materials with great heat resistance7 has become a habit to avoid issues later.
High thermal conductivity prevents channel overheating.True
Materials with high thermal conductivity dissipate heat efficiently, reducing thermal stress.
Plastic channels have the highest hardness among materials.False
Plastic has low hardness compared to metals like steel, making it less wear-resistant.
Why Is Flow Balance Crucial in Runner Design?
Runner design holds key importance in molding. It focuses on flow balance. Every product must be flawless and efficient, so this design is very crucial.
Flow balance in runner design keeps molten plastic distribution uniform, preventing defects and guaranteeing even product quality. Balanced systems cut waste and increase injection molding efficiency. Systems really reduce waste.
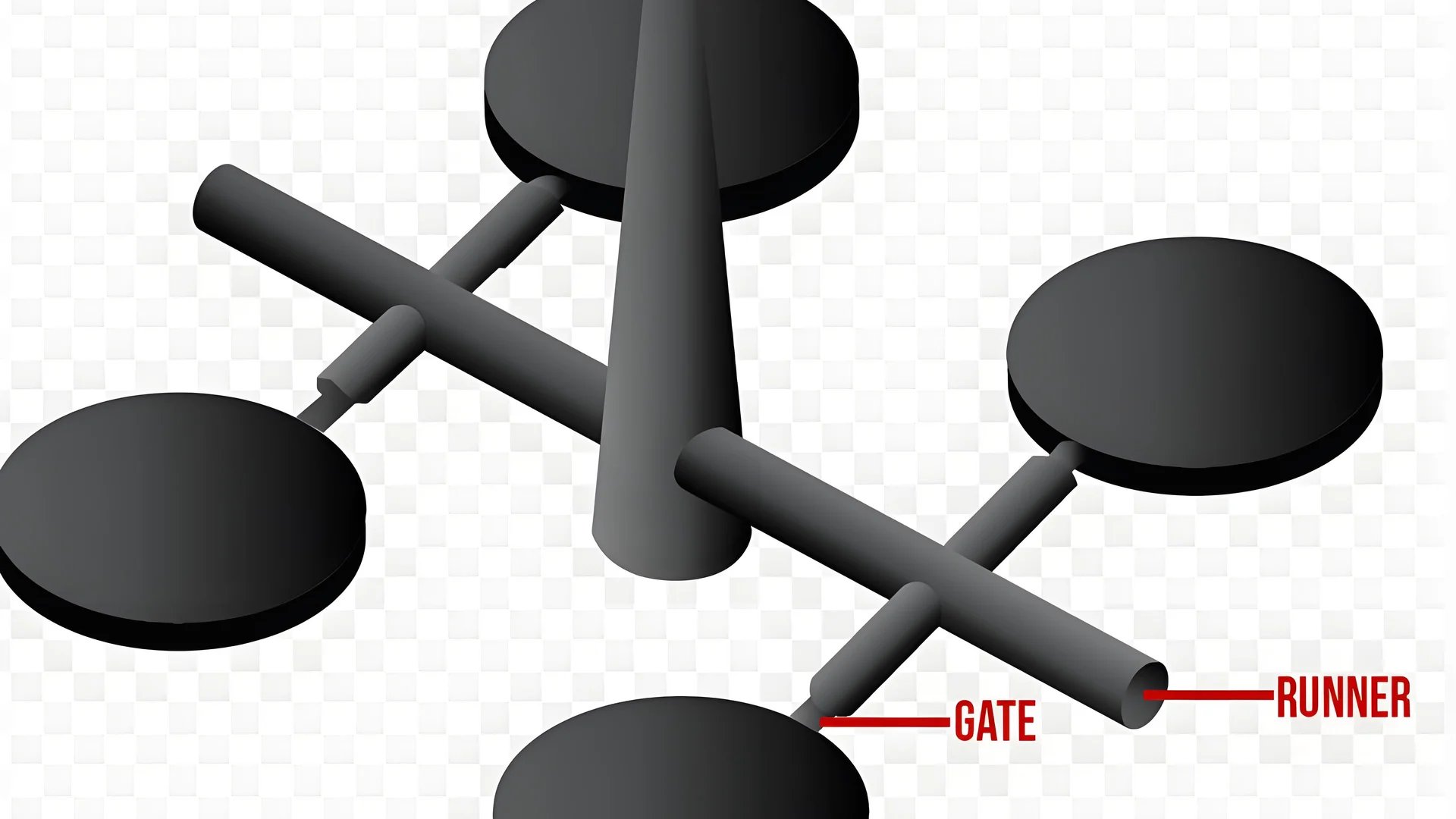
Understanding Flow Balance in Runner Design
Many years tinkering with molds taught me that flow balance8 is the core of reliable manufacturing. Imagine pouring pancake batter into a mold without spilling or missing spots. That’s our aim with molten plastic. Balanced flow fills each cavity equally, reducing defects like voids or uneven surfaces.
Effects of Imbalanced Flow
Imbalanced flow causes a chaotic chain reaction. Problems can arise, such as:
- Defective Products: Think of sink marks and short shots ruining the product’s look and function.
- Increased Waste: More material ends up used to make up for issues.
- Higher Costs: More defects mean spending more time and money fixing or discarding bad products.
Achieving Proper Flow Balance
Perfecting flow balance depends on a few main factors:
Factor | Description |
---|---|
Runner Shape | A conical shape usually works well for the main runner. It fits tightly with the machine nozzle, reducing mishaps. |
Cross-sectional Area | Cross-sectional areas need adjusting to ensure even fill rates across all cavities. |
Length | Shorter runners reduce pressure loss and heat dissipation. |
Design Standards for Effective Runner Systems
- Main Runner Specifications:
- A conical shape usually works well for the main runner. It fits tightly with the machine nozzle, reducing mishaps.
- Good positioning is crucial. Avoid direct hits on small cores to keep them safe.
- Choose materials that tolerate high heat and frequent use.
- Branch Runner Standards:
- Keep the setup neat and balance the flow – simple but effective.
- Flow should stay smooth to avoid unwanted currents or stalls.
- Adjust cross-sectional areas to maintain consistent fill rates across all cavities.
Following these standards secures product consistency9 across various cavities, hitting quality aims every time. Optimizing production and minimizing defects is the goal. Reviewing and tweaking designs based on production feedback matters a lot. CAD simulations and real testing offer very valuable insights.
Balanced flow reduces defects in molded products.True
Balanced flow ensures even filling of cavities, reducing defects like voids.
Circular runners are easier to process than U-shaped ones.False
Circular runners are efficient but challenging; U-shaped runners offer better performance.
Conclusion
This article explores design standards for main and branch channels in mold design, emphasizing shape, size, layout, and material selection to ensure efficient plastic flow and high-quality production.
-
Discover comprehensive guidelines on designing efficient main runners in molds for optimized production. ↩
-
Learn how strategic layout choices enhance flow and efficiency in injection mold designs. ↩
-
Access detailed guides on mold design to improve efficiency and product quality. ↩
-
Learn how to size runners properly to ensure efficient material flow and reduce waste. ↩
-
Discover top CAD tools for enhancing precision in mold design projects. ↩
-
Explore materials known for their high thermal conductivity to understand their applications in channel design. ↩
-
Discover materials that offer high resistance to heat, crucial for channels in high-temperature environments. ↩
-
This link explains why flow balance is crucial in maintaining product quality and reducing defects. ↩
-
Discover methods to ensure each molded product meets high-quality standards through proper runner design. ↩