Imagine creating parts that just snap together perfectly, like they were always meant to be.
Design injection molded parts for seamless assembly by focusing on precise geometries, selecting appropriate materials, and incorporating alignment features, ensuring perfect fit and efficient assembly.
I remember the first time I nailed a design where everything fit together without a hitch. It was like solving a complex puzzle. Achieving this seamless assembly requires a blend of technical skill and creative thinking. Let’s dive into some strategies and expert tips that can elevate your design process to new heights.
Precise geometries ensure seamless assembly in injection molding.True
Accurate geometries are crucial for parts to fit together without gaps.
Alignment aids are unnecessary in injection molded part design.False
Alignment aids help guide parts into the correct position, ensuring fit.
- 1. What Are the Key Design Principles for Injection Molded Parts?
- 2. Why Does Material Selection Matter in Molded Part Assembly?
- 3. What Role Does Tolerance Play in Part Assembly?
- 4. How Can You Incorporate Alignment Features in Your Designs?
- 5. What Are Effective Strategies for Designing Molded Threads?
- 6. How Can Simulation Tools Enhance Your Design Process?
- 7. Conclusion
What Are the Key Design Principles for Injection Molded Parts?
I remember the first time I faced the challenge of designing an injection molded part. It felt like trying to solve a puzzle with a thousand pieces. But once you grasp the core principles, it becomes a rewarding journey.
Key design principles for injection molded parts include maintaining uniform wall thickness, incorporating draft angles, and optimizing rib design to ensure manufacturability, integrity, quality, and cost-effectiveness.
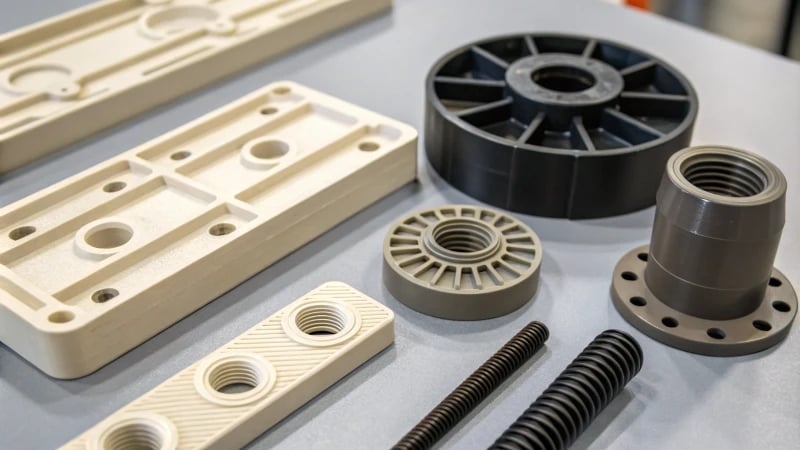
Understanding Wall Thickness
When I first started working with injection molding1, I quickly learned that keeping the wall thickness consistent was crucial. Variations can lead to defects like warping or sink marks. Maintaining uniform thickness helps prevent those pesky defects and facilitates even cooling and material flow.
Wall Thickness | Material Type |
---|---|
1.0 – 2.5 mm | ABS, Polypropylene |
2.5 – 4.0 mm | Nylon, Polycarbonate |
Keeping the wall thickness within recommended ranges for specific materials ensures optimal performance and aesthetics.
Importance of Draft Angles
Then there’s the importance of draft angles. Draft angles are slight tapers incorporated into the walls of a part to ease its ejection from the mold. These angles prevent damage to both the part and the mold itself during release. Typically, a draft angle of 1 to 2 degrees is standard, though this may vary based on texture and depth.
Including appropriate draft angles reduces ejection force2, decreasing wear on molds and extending their lifespan.
Optimizing Rib Design
When it comes to rib design, I always remember an old mentor’s advice: "Ribs are like the hidden backbone of your part." They provide essential strength without adding weight, but if not designed carefully, they can lead to sink marks—a mistake I’ve seen far too often in my early days.
A general guideline is to keep rib thickness at about 60% or less of the nominal wall thickness. The placement of ribs also matters; distributing them evenly helps maintain structural integrity while reducing material usage.
Balancing Aesthetic and Functional Requirements
Balancing aesthetics with functionality is another crucial aspect I often wrestle with, especially in consumer electronics. It’s a delicate dance between making something look good and ensuring it meets manufacturing standards.
Techniques like texturing3 can enhance visual appeal without compromising quality or performance.
By embracing these design principles, I’ve found that it’s possible to create injection molded parts that are not only efficient and durable but also meet both industry standards and customer expectations. It’s a process that continues to teach me new lessons, project after project.
Uniform wall thickness prevents warping in molded parts.True
Uniform thickness ensures even cooling, reducing defects like warping.
Draft angles increase the ejection force in molding.False
Draft angles decrease ejection force, easing part removal from molds.
Why Does Material Selection Matter in Molded Part Assembly?
Ever wonder how the right material can make or break your product design? Let’s dive into why choosing the right material for molded parts is crucial.
Selecting suitable materials for molded part assembly is vital for ensuring compatibility, durability, and cost-effectiveness, enhancing functionality and longevity, and streamlining manufacturing processes.
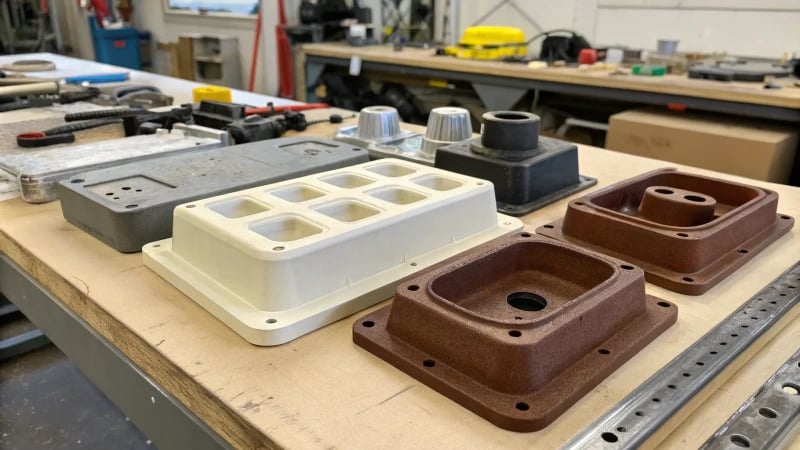
Material Compatibility and Fit
I remember the first time I faced a major hiccup with mismatched materials. It was a project where I used two different polymers that had vastly different thermal expansion properties. When the product was exposed to slight temperature changes, it warped terribly, and the parts wouldn’t align during assembly. Ever since that experience, I’ve been vigilant about picking materials with compatible thermal and mechanical properties. Imagine choosing a polymer with a similar thermal expansion coefficient4 to its surrounding components—it’s like finding that perfect puzzle piece that fits just right.
Durability and Longevity
One thing I’ve learned from years in this field is that durability isn’t just about toughness. It’s also about choosing materials that can withstand the elements they’ll face in their lifetime. High-performance polymers like PEEK or nylon have been my go-to because they resist wear and chemicals, extending the lifespan of products. Using a material properties chart5 has helped me make informed decisions tailored to specific application needs, ensuring my designs last longer.
Cost-Effectiveness
Balancing budget with performance often feels like walking a tightrope. Premium materials are tempting because they offer superior features, but they can also blow the budget if not carefully managed. Evaluating the total cost of ownership6 has been a lifesaver in making sure I strike the right balance between quality and expense.
Assembly Methods
Material choice doesn’t just affect the end product; it also dictates how you can assemble it. I’ve found that softer plastics are fantastic for snap-fit assembly methods, reducing the need for extra fasteners. Exploring various assembly techniques7 has opened up new design possibilities and improved manufacturability.
Environmental Considerations
Sustainability has become an essential part of my material selection process. Using biodegradable or recycled materials not only reduces environmental impact but also aligns with broader corporate goals. Consulting sustainable material guides8 has been incredibly helpful in making responsible choices that don’t compromise on quality.
Material | Advantages | Disadvantages |
---|---|---|
ABS | Durable, impact-resistant | Poor weather resistance |
Polypropylene | Lightweight, chemical-resistant | Prone to UV degradation |
Nylon | High strength, wear-resistant | Absorbs moisture, costly |
Incorporating these considerations into my material selection process has undoubtedly enhanced the functionality and efficiency of molded parts. Every project is an opportunity to refine this balance further, ensuring alignment with production goals and quality standards.
Mismatched materials can cause part misalignment.True
Different thermal properties lead to warping, affecting alignment.
Premium materials always reduce production costs.False
They enhance features but may increase expenses.
What Role Does Tolerance Play in Part Assembly?
Ever wondered why some products fit perfectly while others just don’t? It’s all about tolerance.
Tolerance in part assembly allows for minor variations, ensuring components fit together properly, preventing assembly issues, and maintaining consistent product performance.
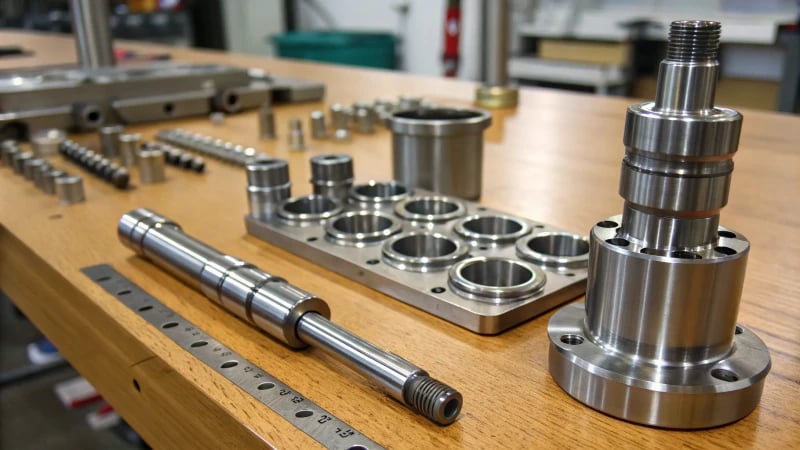
Understanding Tolerance in Engineering
Let’s dive into a little story from my early days in engineering9. Picture this: I’m fresh out of school, eager to make my mark. I was handed a design project that seemed straightforward—until it wasn’t. I quickly learned that even a tiny deviation from design specs could lead to major headaches. That’s where tolerance comes into play. It’s the unsung hero of engineering, setting the acceptable limits of variation in a dimension or measurement. Essentially, it makes sure parts fit and function as intended, preventing those ‘uh-oh’ moments.
Types of Tolerances
There’s more to tolerance than meets the eye. I learned this while working on a complex design that required precision:
- Dimensional Tolerance: This specifies how much a measurement can deviate from its specified dimension without causing issues.
- Geometric Tolerance: This takes it up a notch, focusing on the shape and positioning of features.
Importance in Part Assembly
In manufacturing, getting the tolerance right is like baking a cake—too much or too little of an ingredient can ruin the whole thing. For example, I remember working on a plastic molding project where tight tolerances were crucial. It was all about preventing warping10 or misalignment, especially since we were dealing with high-precision consumer electronics.
Component | Ideal Dimension | Tolerance Range |
---|---|---|
Gear Shaft | 10.00 mm | ±0.05 mm |
Housing | 50.00 mm | ±0.10 mm |
Consequences of Improper Tolerances
I’ve been there when things went south because of improper tolerances:
- Assembly Difficulties: When parts refuse to fit together, it’s like trying to solve a puzzle with mismatched pieces.
- Operational Failures: Misalignments can cause friction or wear, which can be disastrous.
- Increased Costs: Reworking and wasting materials add up quickly, burning through budgets faster than you can say "overtime."
Setting the Right Tolerances
I’ve often found myself deep in CAD software, simulating tolerance stacks11 to see how small deviations impact assembly. The goal is always to strike that perfect balance—not too tight to cause manufacturing issues, yet not too loose to compromise performance. Knowing how to manage these tolerances effectively helps me optimize production processes, reduce defects, and ensure product longevity—a must in competitive markets where quality truly counts.
Dimensional tolerance ensures parts fit together correctly.True
Dimensional tolerance limits variation in dimensions, ensuring proper fit.
Geometric tolerance affects only the size of the components.False
Geometric tolerance deals with shape and location, not just size.
How Can You Incorporate Alignment Features in Your Designs?
Ever felt like your design lacked that cohesive touch? Alignment might be your answer!
Incorporate alignment features by using grids, guides, and smart tools in design software to ensure consistent spacing and harmonious placement, enhancing visual appeal and functionality.
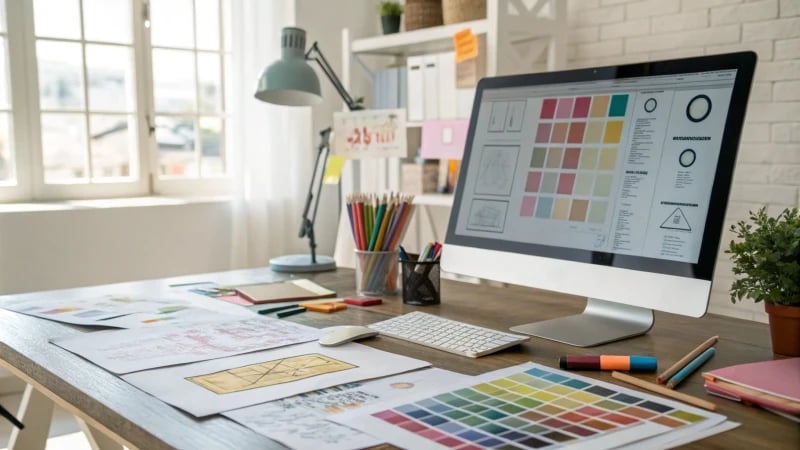
Understanding the Basics of Alignment
I remember when I first learned about alignment, it was like discovering the secret sauce to making my designs look professional. Alignment is key—it brings harmony to your layout by organizing elements so they naturally relate to each other. Whether you’re aligning left, right, center, or fully justifying text, each type of alignment serves a unique purpose based on your design goals.
Tools to Enhance Alignment
Modern design software is packed with nifty tools to help you nail alignment every time. I still remember the first time I used grids and guides in Adobe Illustrator; it was a game-changer. These tools let you structure layouts precisely, snapping elements into place with ease.
Tool | Description |
---|---|
Grids | Used for consistent spacing and alignment across the entire layout. |
Guides | Customizable lines that help position elements accurately. |
Smart Guides | Automatic alignment aids that appear when objects are moved around. |
Practical Examples of Alignment in Design
Think about designing a webpage—have you ever noticed how a grid system keeps everything looking neat and tidy? Aligning text with images not only looks great but also makes content easier to read. A tip I’ve found useful is to align edges12 of text and images; it creates those clean lines that effortlessly guide the viewer’s eyes.
Alignment for Aesthetic and Functional Purposes
While alignment definitely boosts aesthetics, it also plays a critical role in functionality. I’ve seen firsthand how consistent alignment in user interfaces can simplify navigation and reduce cognitive load. In product design, especially with control panels or displays, precise alignment can significantly improve usability. Consistent alignment13 helps users predict element placement, enhancing overall interaction.
Experimenting with Alignment
Experimentation is crucial—it’s how I discovered some of my best design tricks. Try mixing different alignments to see what fits best with your project’s vibe. For example, center a logo while justifying body text for a balanced look. Testing various alignments will reveal what resonates most with your audience’s expectations.
Alignment improves readability in web design.True
Aligning text with images creates clean lines, guiding the user's eyes smoothly.
Smart guides are not available in Figma.False
Figma offers smart guides to aid automatic alignment when objects are moved.
What Are Effective Strategies for Designing Molded Threads?
Designing molded threads isn’t just a technical task—it’s an art of precision that can make or break your project.
Effective molded thread design involves choosing appropriate thread types, considering material shrinkage, and optimizing mold design to avoid issues such as stripping and poor fit.
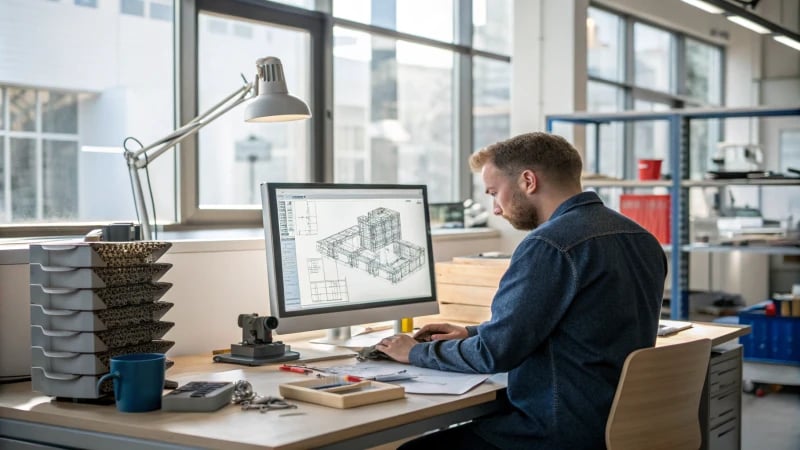
I remember the first time I tackled a molded thread project. It felt like I was trying to solve a complex puzzle with too many moving parts. Over the years, though, I’ve found that some key strategies can make this task far less daunting.
Choosing the Right Thread Type
Selecting the appropriate thread type is like choosing the perfect tool for a job—it makes everything smoother. The decision should hinge on the specific application. For example, while standardized thread profiles like Unified Thread14 work well for general-purpose fasteners, Acme Threads are ideal for power screws and heavy loads. If you ever tried to screw a mismatched thread type into place, you’ll know how frustrating that can be.
Thread Type | Application Example |
---|---|
Unified Thread | General-purpose fasteners |
Acme Thread | Power screws and heavy loads |
Buttress Thread | Applications requiring high load capacity in one direction |
Considering Material Shrinkage
Material shrinkage can be a sneaky villain, disrupting your perfect design if not accounted for. I learned this the hard way when my first batch of components came out slightly off in dimensions. Now, I always predict and compensate for shrinkage. Acetal resins15, for instance, have lower shrinkage compared to polyolefins, which significantly affects thread precision.
Optimizing Mold Design
I can’t stress enough how critical mold design is to success. Poor mold design led to stripping issues in one of my early projects. Since then, I’ve focused on features like rounded thread roots and optimized draft angles to reduce stress concentrations. Think of it as giving your design a stress-free environment—everyone performs better under less stress!
- Rounded Thread Roots: Minimize stress by avoiding sharp edges.
- Draft Angles: Ensure easy ejection from the mold without damaging threads.
Utilizing software simulations16 to predict mold behavior has saved me countless headaches by catching potential defects before they manifest in reality.
Incorporating Inserts for Reinforcement
For those applications where plastic threads alone can’t bear the load, inserts become a game-changer. Reinforcing plastic threads with materials like brass or stainless steel can enhance their load-bearing capacity and durability. It’s like giving your threads a backbone. For specifics on installation and compatibility with different plastics, refer to the inserts design guide17.
These strategies have transformed my approach to designing molded threads from trial-and-error to a reliable process that consistently delivers robust and reliable results. By carefully evaluating each design decision against performance requirements and production constraints, I’ve been able to achieve optimal outcomes in diverse applications.
Acetal resins have higher shrinkage than polyolefins.False
Acetal resins exhibit lower shrinkage compared to polyolefins.
Rounded thread roots reduce stress concentrations.True
Rounded thread roots minimize stress by avoiding sharp edges.
How Can Simulation Tools Enhance Your Design Process?
Imagine transforming your design dreams into reality with just a few clicks. Simulation tools can do just that! They bring designs to life, allowing you to tweak and perfect every detail before hitting the production line.
Simulation tools improve design by enabling early validation, flaw identification, and optimization, leading to reduced development time and cost-effective solutions.
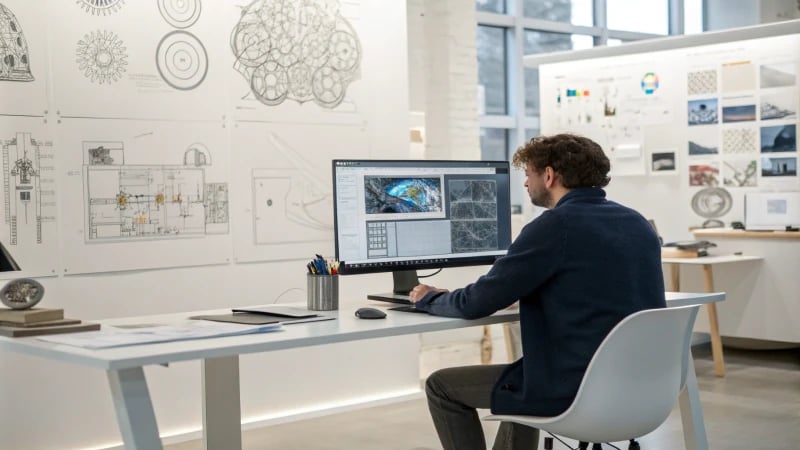
Early Validation of Designs
I remember the first time I realized the power of simulation tools. It was like having a crystal ball, but instead of predicting the future, I was foreseeing how my designs would perform in the real world. By simulating real-world conditions early on, I could test whether my ideas would hold up when put to the test. This early validation meant catching flaws that could have led to costly prototypes—or worse, failed products.
Identifying Design Flaws
One unforgettable project involved designing a component where the stakes were sky-high. Traditional methods left us puzzled over potential weak points. Enter simulation tools: they allowed me to explore various scenarios, unveiling vulnerabilities that weren’t visible before.
Example: Thermal Analysis
For instance, during a thermal analysis simulation, I was able to visualize heat distribution across a product. This insight was crucial; it guided me in making adjustments that drastically improved the product’s efficiency.
Feature | Traditional Methods | Simulation Tools |
---|---|---|
Time Efficiency | Moderate | High |
Cost | Higher | Lower |
Accuracy | Moderate | High |
Optimizing for Production Efficiency
The beauty of these tools lies in their ability to optimize designs for manufacturing processes. I could simulate different production techniques and discover the most efficient way to minimize waste while maximizing output. For someone passionate about sustainable practices18, this was an invaluable step forward.
Incorporating Feedback Loops
I’ve learned that using simulation tools is like having a feedback loop on steroids. They let me test changes instantly and see the results in real-time. It’s like having a conversation with my designs, where each tweak is a question answered immediately.
If you’re considering bringing these tools into your design arsenal, understanding how they fit into existing CAD systems is key. Many of these tools seamlessly integrate19 into CAD software, boosting capabilities without disrupting your workflow.
Simulation tools reduce design costs significantly.True
By identifying flaws early, simulation tools save on costly prototyping.
Traditional methods are more accurate than simulation tools.False
Simulation tools provide higher accuracy by modeling real-world conditions.
Conclusion
Designing injection molded parts for seamless assembly involves precise geometries, material selection, and alignment features to enhance manufacturability, product quality, and assembly efficiency.
-
Learn about the fundamental steps in the injection molding process to understand how designs translate into finished products. ↩
-
Discover why draft angles are crucial in molding, reducing production issues and increasing mold lifespan. ↩
-
Explore various texturing techniques to enhance the aesthetic appeal of molded parts without sacrificing quality. ↩
-
Understanding thermal expansion helps prevent assembly issues by ensuring material compatibility. ↩
-
Material properties charts provide quick reference for selecting suitable materials based on application needs. ↩
-
Total cost analysis helps balance budget constraints with performance expectations. ↩
-
Exploring various techniques can optimize design for manufacturability. ↩
-
Sustainable materials reduce environmental impact and align with eco-friendly goals. ↩
-
Provides a comprehensive definition of tolerance and its applications in engineering. ↩
-
Explains the impact of warping on product design and manufacturing. ↩
-
Details how CAD tools help designers manage tolerance stacks effectively. ↩
-
Explore methods to align text with images for improved web aesthetics. ↩
-
Discover why consistent alignment enhances user interface functionality. ↩
-
Learn about various standardized thread profiles to ensure compatibility with existing fasteners and ease of assembly. ↩
-
Understand how acetal resin’s low shrinkage rate affects thread precision and overall component quality. ↩
-
Discover how simulations can predict potential defects in threaded components, enhancing design reliability. ↩
-
Find detailed guidelines on selecting and installing inserts to reinforce plastic threads effectively. ↩
-
Explore how simulation tools contribute to sustainable manufacturing by optimizing design processes. ↩
-
Discover how simulation tools can seamlessly integrate with CAD software to enhance design efficiency. ↩