In the fast-paced realm of plastic injection molding, I often find myself pondering a crucial question: How do we create an efficient feeding system? This isn’t just about mechanics; it’s about understanding the very essence of quality production.
An efficient feeding system for injection molds ensures optimal flow of molten plastic into the mold cavity, minimizing defects like weld marks and pores. Key considerations include selecting suitable gate positions and types, designing an effective runner system, and ensuring balanced filling for consistent product quality.
While understanding the basics is important, mastering the nuances of feeding system design can significantly impact your production efficiency and product quality. Let’s explore each element in detail to uncover advanced strategies that can transform your manufacturing process.
Balanced runner systems reduce product defects.True
Balanced runner systems ensure even distribution of molten plastic, minimizing defects.
What Are the Key Factors in Selecting Gate Positions?
Choosing the right gate position in injection molding can make or break your production efficiency. What should you consider?
Selecting the right gate position involves considering product shape, avoiding weld marks and pores, and optimizing flow efficiency. Proper gate placement ensures even filling of the mold, enhances product quality, and reduces defects. Utilizing simulation analysis tools can help determine optimal positions for various design requirements.
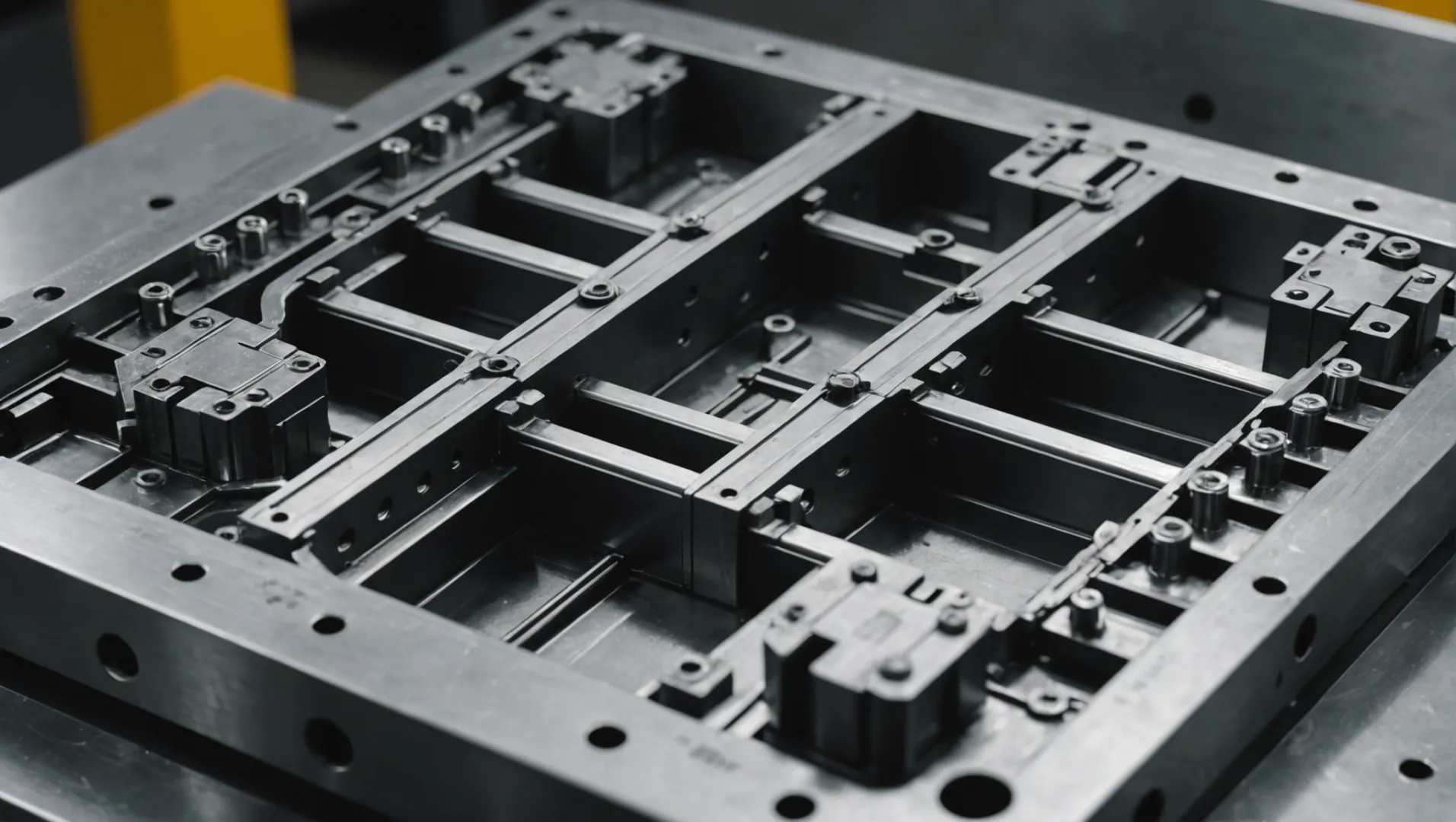
Understanding the Product’s Shape and Requirements
The primary consideration when selecting a gate position is the shape and specific requirements of the product. For items with intricate designs, it’s crucial to position the gate so that the plastic melt fills the cavity uniformly. For instance, thin-walled products benefit from a gate near the cavity edge to decrease flow distance and minimize pressure loss. If a product demands high surface finish or hidden gate marks, options like a latent or point gate are preferable.
Avoiding Weld Marks and Pores
Weld marks and pores are common issues in injection molding that can compromise product strength and appearance. Placing gates away from stress-bearing areas or regions prone to these defects is essential. Utilizing simulation analysis software can effectively reduce weld marks and pores by suggesting optimal gate positions, thereby enhancing the overall quality of the product.
Optimizing Flow Efficiency
The position of the gate significantly impacts how the molten plastic flows into the mold cavity. An ideal gate location minimizes flow resistance, ensuring that the material fills every part of the mold evenly. This is particularly important for products requiring precise dimensions and consistent quality. By strategically selecting gate positions, manufacturers can improve both production efficiency and end-product reliability.
Practical Application: Simulation Analysis Tools
Advanced simulation tools play a pivotal role in determining the best gate positions. These tools simulate the injection process, allowing engineers to visualize how changes in gate positioning affect the flow and filling patterns. By analyzing different scenarios, manufacturers can make informed decisions that optimize the gate placement for each specific product design.
To further explore simulation tools and their benefits in injection molding, visit simulation analysis software for injection molds1. This resource will guide you through various software options available today and how they can revolutionize your manufacturing process.
Gate position affects product surface finish.True
Proper gate placement can hide gate marks, enhancing surface finish.
Simulation tools are unnecessary for gate selection.False
Simulation tools help optimize gate positions, improving product quality.
How Do Different Gate Types Affect Mold Performance?
The choice of gate type in injection molding significantly influences mold performance and product quality. But how exactly does each type of gate impact the process?
Gate types such as direct, side, point, and submerged play distinct roles in injection molding, affecting melt flow, pressure loss, and product appearance. Choosing the right gate type ensures efficient mold performance by balancing these factors with production needs.
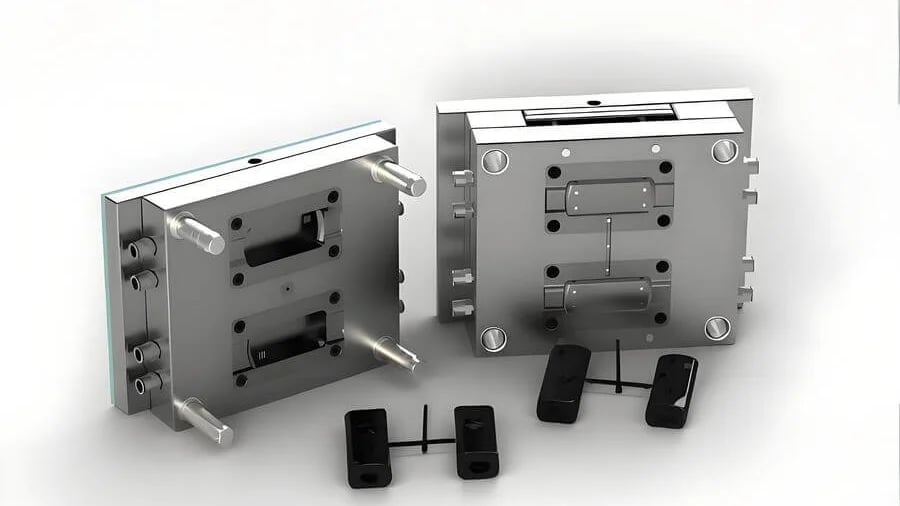
Understanding Gate Types in Injection Molding
Injection molding involves several gate types, each with unique characteristics that influence mold performance. Selecting the appropriate gate type can be critical to ensuring that the plastic melt flows effectively into the cavity and that the final product meets desired specifications.
Direct Gate
A direct gate2 is often used for single cavity, deep cavity, or large products due to its short melt flow path and minimal pressure loss. This design facilitates efficient filling of the cavity, which can enhance mold performance by reducing cycle times.
Advantages:
- Short melt flow path
- Minimal pressure loss
Disadvantages:
- Large trace at the gate requiring post-processing
- Potential for stress concentration
Side Gate
The side gate3 is versatile and commonly used for products of various shapes. It is positioned on the side of the part, allowing for smaller gate traces and straightforward removal.
Advantages:
- Small gate traces
- Simple to process and remove
Disadvantages:
- Longer melt flow path leading to potential uneven filling
- Increased pressure loss
Point Gate
A point gate4 is ideal for products with high aesthetic requirements, such as electronic device casings. It offers minimal impact on appearance due to its small trace.
Advantages:
- Extremely small gate trace
- Minimal impact on appearance
Disadvantages:
- Requires complex three-plate molds
- Higher production costs
Submerged Gate
A submerged gate5 is suited for automated production lines. It is concealed within or on the product side and automatically detaches when the mold opens.
Advantages:
- Minimal visible gate marks
- No need for further processing
Disadvantages:
- Complex design and processing needs
- High precision required in mold design
Choosing the Right Gate Type for Mold Performance
When selecting a gate type, consider factors such as product shape, aesthetic requirements, and production efficiency. For example, if minimizing visible gate marks is crucial, a point or submerged gate may be preferred.
Furthermore, the choice of gate type should align with the design of the runner system6 to optimize melt flow and minimize defects like weld marks and pores. Evaluating these considerations helps ensure consistent product quality and efficient manufacturing processes.
Direct gates reduce cycle times in injection molding.True
Direct gates have short melt flow paths and minimal pressure loss.
Submerged gates require no further processing post-molding.True
Submerged gates detach automatically, leaving minimal visible marks.
Why Is Runner System Design Crucial for Efficiency?
An efficient runner system in injection molding ensures seamless flow and distribution of molten plastic, crucial for product integrity and cost-effectiveness.
The runner system’s design is pivotal for optimizing the distribution of molten plastic, reducing defects, and enhancing production efficiency. Key elements include the main runner, branch runner, and sprue bushing, each needing precise design to minimize resistance and maintain uniform flow.
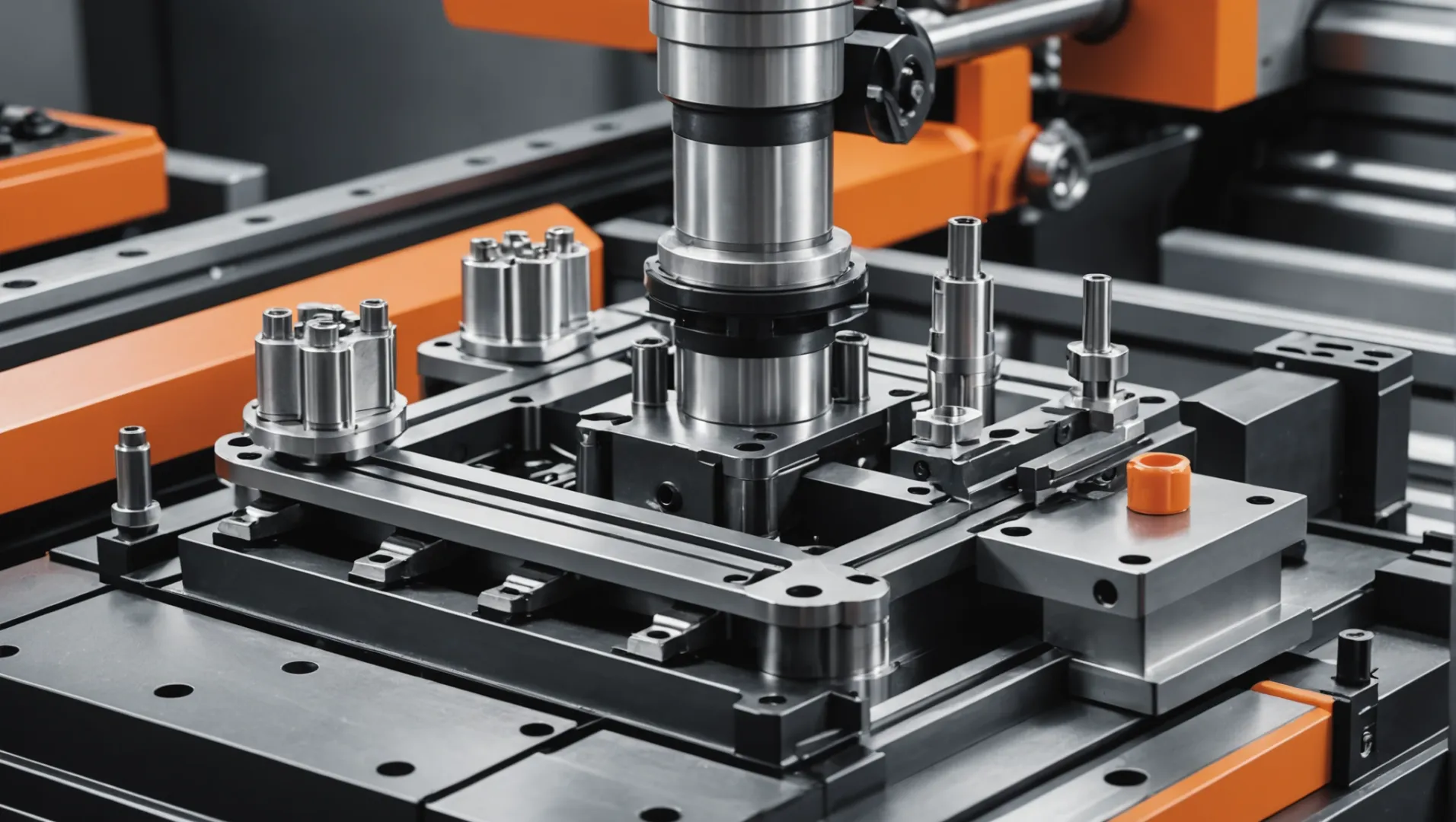
Understanding the Runner System’s Role
In injection molding, the runner system7 serves as the pathway through which molten plastic travels from the machine nozzle to the mold cavity. An efficiently designed runner system can significantly influence the quality of the final product and the overall productivity of the manufacturing process.
Main Runner Design
The main runner connects the injection molding machine’s nozzle to the branch runners. Its conical shape facilitates smooth flow, but its dimensions must be tailored to the size of both the nozzle and the end product. A well-designed main runner should also include a cold material well to prevent solidified plastic from entering the cavity.
Aspect | Design Consideration |
---|---|
Shape | Typically conical to reduce flow resistance |
Size | Matches nozzle size; appropriate for product dimensions |
Features | Includes cold material well |
Branch Runner Configuration
Branch runners distribute molten plastic from the main runner to each gate. The shape of these runners—whether circular, semicircular, or trapezoidal—affects flow resistance and ease of processing. Circular runners offer minimal flow resistance but are challenging to manufacture.
- Circular Runners: Minimize resistance but difficult to process.
- Semicircular/Trapezoidal Runners: Easier to manufacture with moderate resistance.
Sprue Bushing Considerations
The sprue bushing8 channels molten plastic from the nozzle into the main runner. Made from high-quality steel, it must resist wear and ensure precise alignment with the mold’s main channel. Properly aligned sprue bushings contribute to a seamless flow and reduce wear on the mold.
Efficiency Through Balance
An unbalanced runner system can lead to inconsistent filling, causing variations in product dimensions and inducing stress concentrations. A balanced design ensures even distribution of molten plastic across multiple cavities, enhancing uniformity in product quality.
- Simulation Analysis: Use software tools to model flow dynamics and adjust runner design for balance.
- Gate Adjustments: Modify gate positions and sizes to achieve balanced flow.
By focusing on these key design elements, manufacturers can enhance their production processes, reduce defects, and optimize material use. The intricate balance of design considerations ultimately leads to increased efficiency and cost savings in injection molding operations.
Circular runners minimize flow resistance.True
Circular runners are designed to offer minimal resistance, enhancing flow.
Sprue bushing alignment is not crucial.False
Proper alignment of sprue bushing ensures seamless flow and mold longevity.
How Can Balanced Design Improve Product Quality?
Balanced design in injection molding isn’t just a luxury—it’s a necessity for high-quality production.
Balanced design in injection molding ensures uniform flow of materials, reducing defects like uneven filling and stress concentration, thereby enhancing product quality. By adjusting gate positions and optimizing the runner system, balanced design minimizes inconsistencies and boosts efficiency.
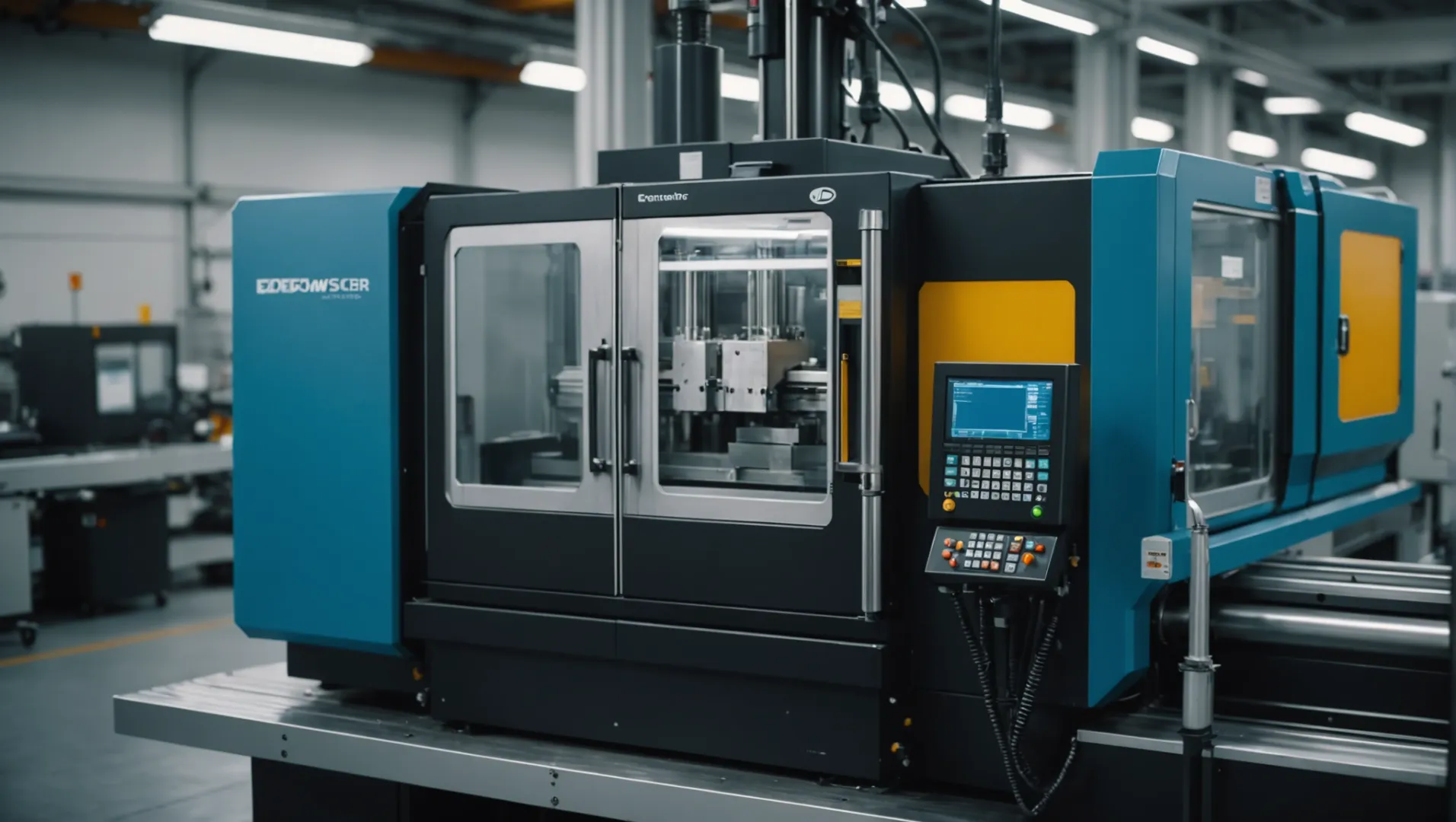
The Significance of Balanced Design in Injection Molding
Balanced design is critical in the world of injection molding because it ensures that the molten plastic fills each cavity evenly. This uniformity is essential for maintaining consistent product dimensions and structural integrity. When the flow of material is balanced, it reduces defects such as warping, dimensional inaccuracies, and stress concentrations.
For instance, when designing a multi-cavity mold9, it is crucial to maintain balance in the feeding system. This can be achieved by adjusting gate sizes, positions, and layouts to ensure even filling across all cavities. Simulation analysis software often assists designers in evaluating and optimizing this balance.
Strategies to Avoid Unbalanced Filling
Unbalanced filling is a common issue that leads to inconsistent product quality. It can cause some cavities to fill faster than others, resulting in variations in size and weight. To avoid these problems, designers can implement several strategies:
- Increase the Number of Gates: More gates can help distribute the melt evenly across the mold.
- Adjust Gate Positions: Strategic placement of gates can ensure that the flow reaches all areas simultaneously.
- Use a Balanced Runner System: A runner system that distributes material evenly can significantly reduce unbalanced filling issues.
Table: Impact of Balanced vs. Unbalanced Design
Aspect | Balanced Design | Unbalanced Design |
---|---|---|
Flow Consistency | High | Low |
Product Quality | Consistent | Inconsistent |
Defects | Minimal | Frequent |
Stress Distribution | Even | Concentrated |
Enhancing Production Efficiency Through Balance
Balanced design not only improves product quality but also boosts production efficiency. By reducing waste and minimizing defects, manufacturers can lower costs and enhance throughput. Moreover, balanced designs often lead to shorter cycle times because the material flows more predictably through the mold, which speeds up the cooling process.
In conclusion, adopting a balanced approach in injection molding design is not just about improving quality; it’s about creating a more efficient and cost-effective production process. By understanding and implementing balanced design principles, manufacturers can achieve superior results in both quality and efficiency.
Balanced design minimizes injection molding defects.True
Balanced design ensures uniform material flow, reducing defects.
Unbalanced runner systems boost product quality.False
Unbalanced systems lead to inconsistent filling and defects.
Conclusion
Ultimately, a well-designed feeding system boosts production efficiency and product quality while reducing costs. By mastering these design elements, you pave the way for superior manufacturing outcomes.
-
Explore tools that optimize gate positioning for improved product quality.: Moldex3D eDesign is cheaper and gives accurate results in 95% or more of real life cases. It’s really simple to read and mesh a model, create … ↩
-
Explore how direct gates enhance cavity filling efficiency.: Injection molding gates are openings in molds that allow molten plastic to enter the cavity while controlling the direction and volume of flow. ↩
-
Understand why side gates are versatile in molding.: Derived from the variation of side gate, the gate widens and becomes thinner in the feeding direction, allowing the melt to enter the cavity … ↩
-
Learn how point gates preserve aesthetic quality.: Gate marks are unavoidable so the location of gates should not affect the appearance of plastic parts, like the edge, bottom and inside of the … ↩
-
Discover why submerged gates are ideal for automation.: The results showed that the submerged gate filling can improve the mold filling conditions, which may reduce the occurrence of inclusion defects during casting … ↩
-
See how runner design influences melt flow efficiency.: The material flow from the runner to the gate is less restrictive, and there is less shear sensitivity due to the elimination of the sharp edges … ↩
-
Learn how runner system impacts mold efficiency and product quality.: This will keep the product quality and minimize material wastage. The runner system is a fundamental component in the injection molding process … ↩
-
Discover how sprue bushing enhances flow and reduces wear.: Sprue bushings accept the machine nozzle and allow for plastic to enter the mold. PCS Sprue Bushings are manufactured from SAE 6145 steel and are hardened and … ↩
-
Explore techniques for achieving balanced filling in multi-cavity molds.: Multi-cavity molds can boost production and reduce part costs, but only after certain design ‘tweaks’ are made · Consider Material Flow for Multi-Cavity Tooling. ↩