Dive into the world of injection molding with me, where mastering decompression is key to unlocking superior product quality.
Decompression in injection molding reduces pressure at specific stages to prevent defects such as flash, reduce internal stress, and optimize density distribution. It enhances product quality and process efficiency by carefully controlling pressure dynamics within the mold.
While this brief overview provides an initial understanding of decompression’s role, delving deeper into its purpose, implementation methods, and necessary precautions reveals its full impact on the injection molding process. Read on to discover how mastering decompression can optimize your production outcomes.
Decompression prevents flash in injection molding.True
Decompression reduces pressure, preventing plastic overflow at mold parting lines.
What is the Role of Decompression in Injection Molding?
Decompression in injection molding is vital to minimizing defects and enhancing product quality. It ensures precision and consistency in molded parts.
Decompression in injection molding involves reducing pressure to avoid defects like flash, diminish internal stresses, and achieve optimal density distribution in plastic products. This process is essential for maintaining high quality and efficient production.
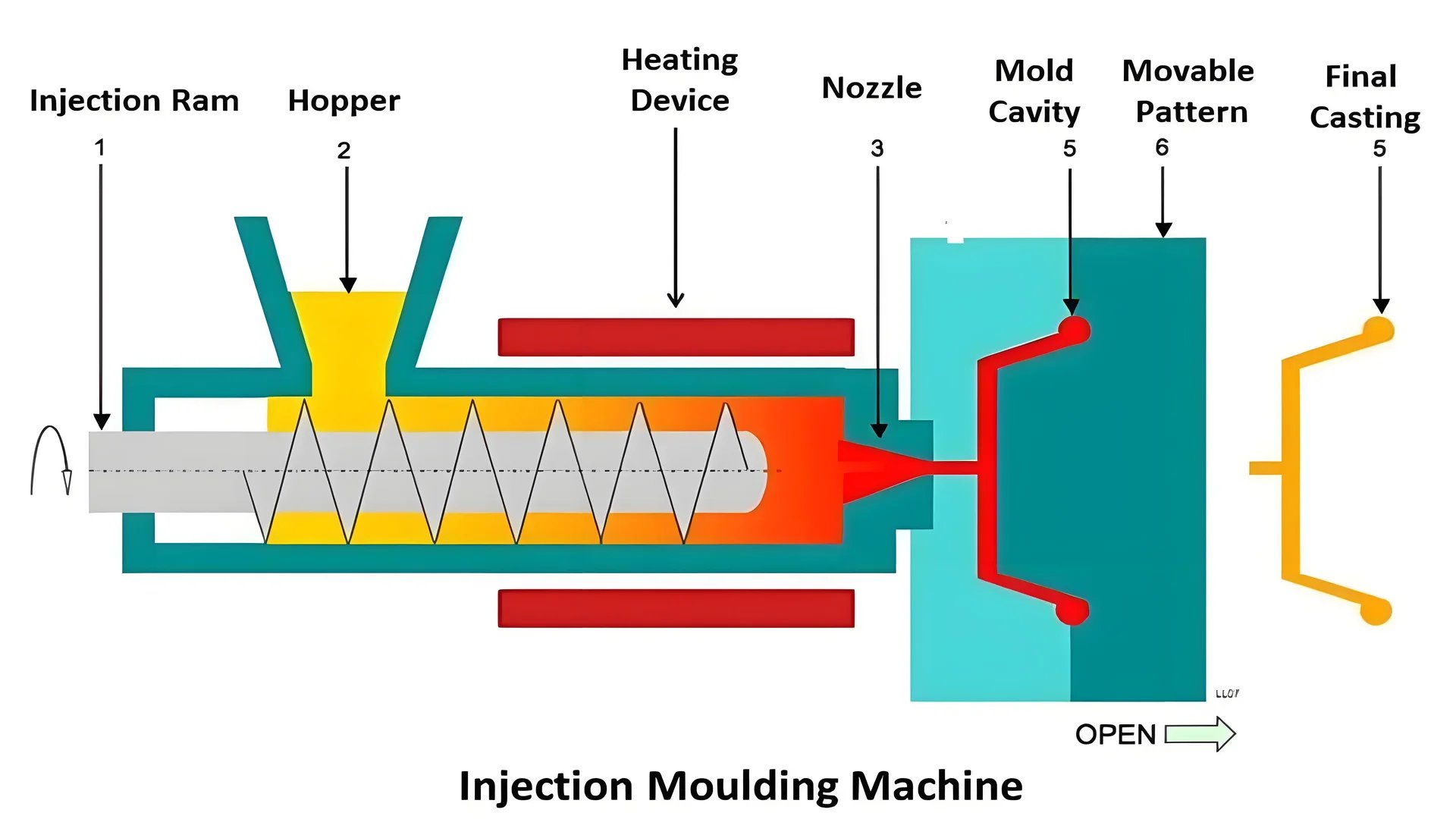
Understanding Decompression
In the context of injection molding, decompression1 is a technique applied to control pressure within the mold cavity. By doing so, manufacturers can fine-tune the quality and consistency of plastic parts, preventing common issues such as flash and internal stress.
- Flash Prevention: High pressure during injection can cause molten plastic to seep out at the mold’s parting lines, leading to undesirable flash. Decompression reduces this pressure, mitigating the risk of such defects.
- Internal Stress Reduction: Excessive pressure during molding can result in significant internal stresses, which might cause the product to warp or crack. Decompression gradually lowers this pressure during cooling, ensuring better dimensional stability.
- Density Distribution Optimization: Proper decompression ensures an even distribution of plastic within the mold, leading to uniform density across the product and enhancing overall quality.
Implementation Techniques
Effective decompression can be achieved through various methods:
- Machine Control: Modern injection molding machines come equipped with precise control systems. Operators can set specific decompression parameters to adjust screw speed and pressure automatically.
- Mold Design Adjustments: Integrating features like exhaust systems or pressure-reducing valves within molds can facilitate natural decompression by releasing trapped gases and managing cavity pressure.
Method | Description |
---|---|
Machine Control | Adjusts injection parameters for precision decompression. |
Mold Design | Includes built-in mechanisms for pressure management. |
Critical Precautions
Decompression requires careful timing and amplitude control:
- Timing: Initiating decompression too early might lead to incomplete filling, whereas late decompression may not effectively prevent flash or reduce stress.
- Amplitude: Over-decompression might cause shrinkage or dents, while insufficient decompression might fail to achieve desired effects.
Operators should conduct thorough testing to tailor decompression settings based on product specifications and materials.
By understanding and implementing these techniques, manufacturers can leverage decompression to enhance injection molding efficiency and product quality.
Decompression reduces flash in injection molding.True
Decompression lowers pressure, preventing molten plastic from seeping out.
Excessive decompression causes increased internal stress.False
Excessive decompression can lead to shrinkage, not increased stress.
How Does Decompression Prevent Flash and Reduce Internal Stress?
Decompression in injection molding is a key technique to enhance product quality by minimizing defects and stress.
Decompression prevents flash by reducing excessive pressure during molding, which stops plastic overflow at the parting line. It also lowers internal stress by allowing gradual pressure reduction during cooling, preventing deformation and improving mechanical properties.
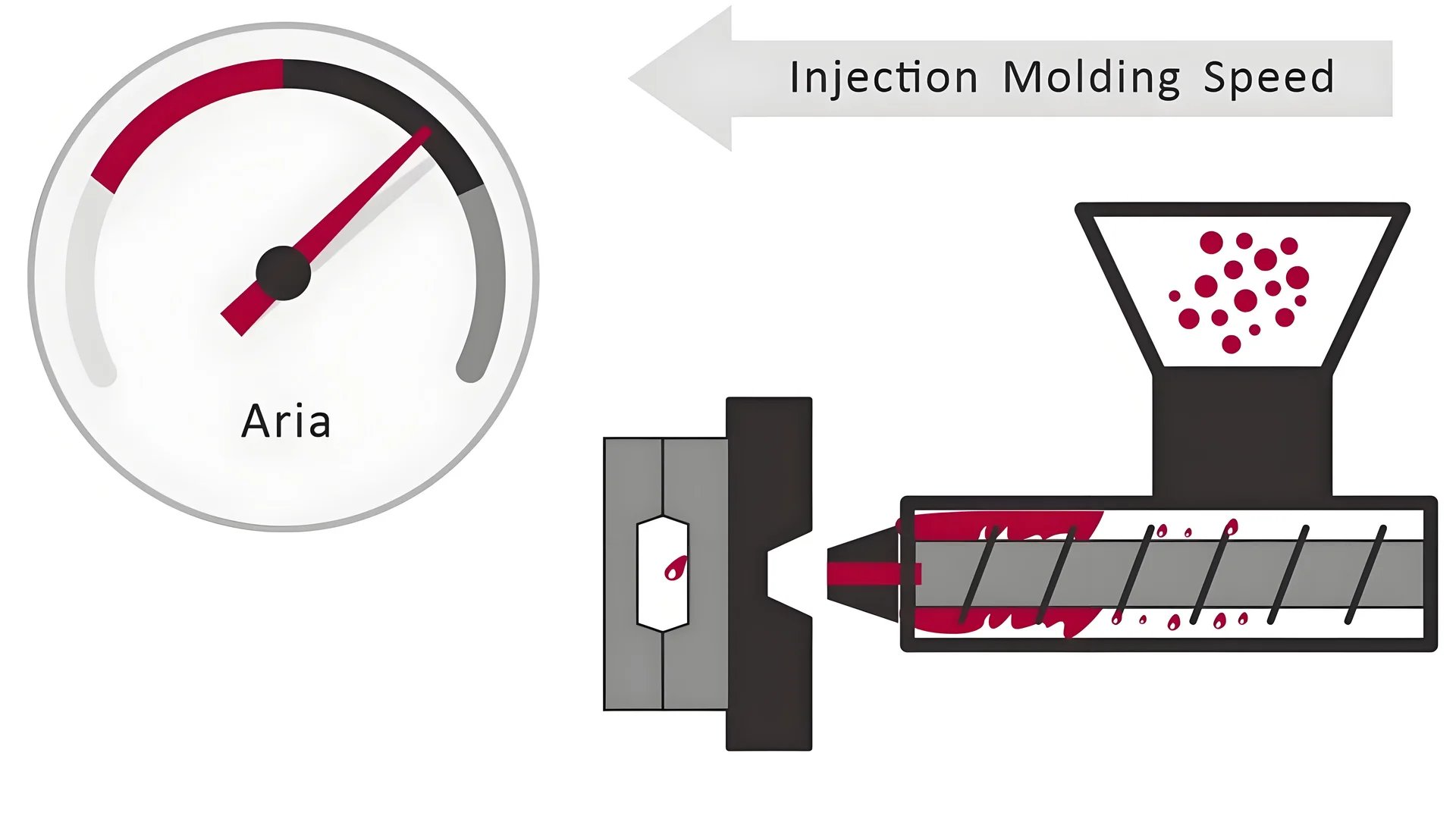
Understanding Flash and Its Prevention
Flash is an undesirable thin layer of plastic that seeps out at the mold’s parting line, creating a visible seam on the product. This defect can occur when the injection pressure is too high, forcing molten plastic beyond the intended mold cavity. By implementing decompression, the pressure is lowered at critical moments, curbing this overflow and thus mitigating flash formation.
Flash Prevention Through Pressure Management
- Pressure Reduction: Reducing pressure at the front end of the screw or within the mold cavity prevents excess plastic flow.
- Timing: Precise timing in decompression is crucial to ensure the cavity fills adequately without excessive pressure.
Lowering Internal Stress for Better Product Stability
Internal stress can lead to issues such as warping or cracking. During cooling, maintaining consistent pressure helps prevent these stresses from building up. Decompression allows for controlled pressure reduction, enhancing dimensional stability and product integrity.
Internal Stress Management Techniques
- Gradual Pressure Release: Controlled decompression reduces stress during cooling, ensuring uniformity in shape and strength.
- Density Distribution Optimization: By adjusting the flow of molten plastic through decompression, density variations within the product can be minimized, enhancing overall quality.
Practical Applications and Benefits
Implementing decompression effectively requires modern injection molding machines equipped with advanced control systems. Operators can set precise parameters for decompression to achieve desired results.
Example: Impact on Product Quality
Aspect | Without Decompression | With Decompression |
---|---|---|
Flash | Common | Significantly Reduced |
Internal Stress | High | Lowered |
Dimensional Stability | Compromised | Enhanced |
By focusing on these elements, manufacturers can produce higher-quality components, reduce waste, and improve production efficiency.
For further insights into managing decompression effectively, see our guide on injection molding machine control2 and learn about mold design strategies3.
Decompression reduces flash in injection molding.True
Decompression lowers pressure, preventing plastic overflow at parting lines.
Decompression increases internal stress in molded products.False
Decompression actually reduces internal stress by gradual pressure release.
What are the Methods for Implementing Decompression?
Decompression methods in injection molding play a vital role in ensuring product quality by managing pressure effectively. Knowing how to implement these methods is key to successful manufacturing.
Decompression can be implemented through machine control and mold design. Advanced machines adjust pressure via settings, while mold designs incorporate features like exhaust systems to facilitate decompression.
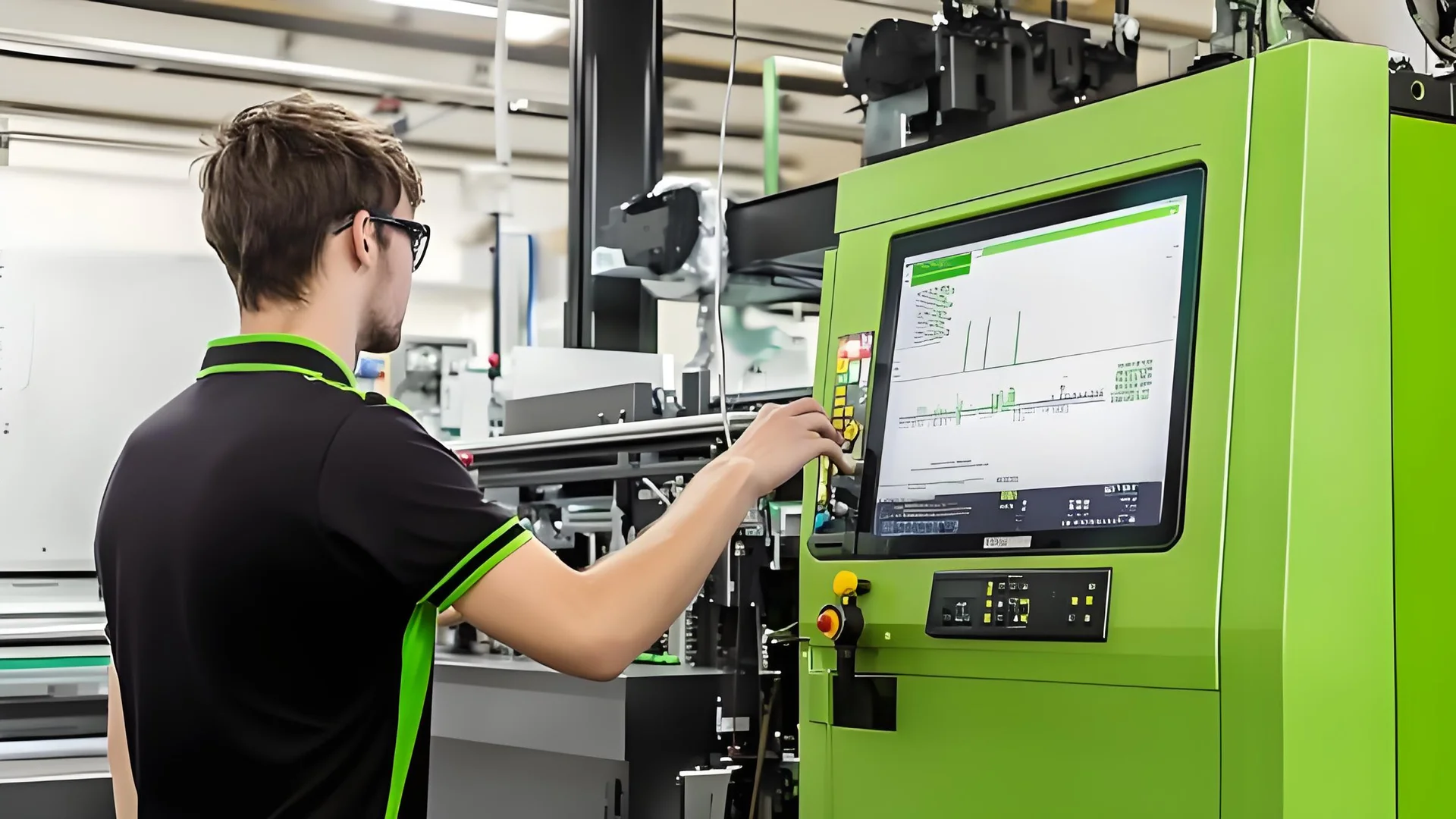
Injection Molding Machine Control
One primary method for implementing decompression is through the control systems of modern injection molding machines4. These machines come equipped with sophisticated technology that allows operators to accurately adjust the injection pressure settings. By doing so, the machine can automatically modify the screw propulsion speed and pressure to achieve the desired decompression.
Operators can set specific decompression parameters through a control panel, which directs the machine to adjust its operation dynamically. This process is crucial for preventing issues like flash and ensuring the dimensional stability of the molded product.
Mold Design Considerations
Another effective method involves strategic mold design. A well-designed mold can significantly aid in achieving decompression without relying solely on machine adjustments.
Table: Mold Design Features for Decompression
Feature | Function |
---|---|
Exhaust Systems | Releases trapped gas to reduce cavity pressure. |
Pressure Reducing Valves | Controls pressure at specific stages of the molding cycle. |
Exhaust systems are integral to mold designs, enabling the timely discharge of gases from the cavity during the injection process. This not only reduces pressure but also prevents defects such as incomplete filling or air entrapment.
Additionally, incorporating pressure-reducing valves within the mold structure can help manage decompression effectively. These valves work by allowing controlled pressure release at particular stages, ensuring a consistent flow of molten plastic and uniform density distribution.
Integrated Approach for Optimal Results
Implementing decompression effectively often requires a combination of both machine control and mold design strategies. By harmonizing these two approaches, manufacturers can fine-tune the decompression process to meet specific production needs.
Advanced systems may even integrate real-time monitoring tools that provide feedback on pressure dynamics during the molding cycle. This data-driven approach allows for ongoing adjustments, leading to improved process efficiency and product quality.
To further explore this topic, understanding how injection molding techniques5 vary across different applications can provide additional insights into optimizing decompression in various manufacturing contexts.
Advanced machines adjust pressure via settings.True
Modern machines use control systems to modify pressure settings.
Mold designs do not affect decompression.False
Mold designs with exhaust systems aid in decompression.
How to Optimize Decompression Timing and Amplitude?
Mastering the art of decompression timing and amplitude is crucial for flawless injection molding. Discover the secrets to optimizing these variables for superior product quality.
To optimize decompression timing and amplitude, adjust parameters based on product shape, size, and material. Properly timed decompression prevents defects like flash and internal stress, while controlled amplitude maintains product integrity and dimensional accuracy.
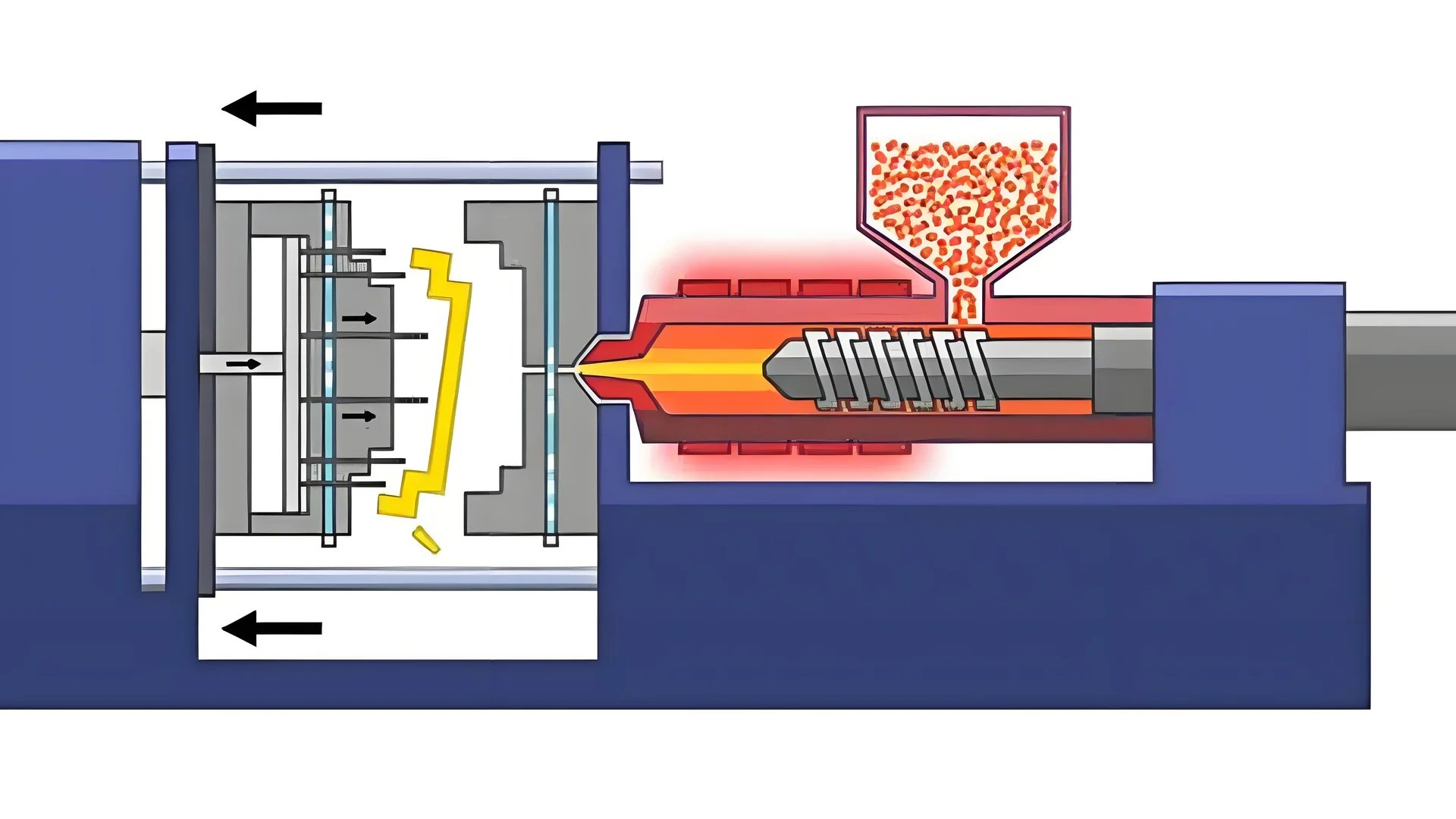
Understanding Decompression Timing
Timing is everything in decompression during injection molding. Optimal decompression timing is crucial because it determines the balance between preventing flash and ensuring complete filling of the mold cavity.
-
Early Decompression: Initiating decompression too early can result in incomplete filling, leading to defects such as short shots or poor surface finish. This typically happens when the material hasn’t fully occupied the mold cavity.
-
Late Decompression: If decompression is too late, the pressure might already have caused issues like flash or excessive internal stress. The goal is to find the sweet spot where the mold is adequately filled but before excess pressure causes defects.
Key Considerations:
- Analyze the shape and complexity of the mold to determine when the material will fill the cavity.
- Consider material-specific behavior6 under pressure, as different plastics respond uniquely.
Adjusting Decompression Amplitude
The amplitude of decompression—how much pressure is reduced—is just as important as timing.
- Excessive Amplitude: Reducing pressure too much can cause shrinkage or warping, as the material lacks sufficient support during cooling.
- Insufficient Amplitude: On the other hand, minimal pressure reduction might not alleviate internal stress or prevent flash effectively.
Strategies for Optimal Amplitude:
- Conduct trials to determine the minimum effective pressure that avoids defects while maintaining material integrity.
- Utilize advanced machine control systems7 that allow precise adjustments to decompression parameters.
Practical Tips for Optimization
- Trial Runs: Conduct controlled experiments with varying decompression settings to see what combination yields the best results.
- Data Analysis: Use data analytics to study past runs and refine settings based on successful outcomes.
- Continuous Monitoring: Implement real-time monitoring systems to adjust settings dynamically during production.
By applying these techniques, manufacturers can fine-tune their decompression processes to consistently produce high-quality products without compromising efficiency or material performance.
Early decompression causes incomplete filling.True
Decompressing too early can lead to short shots or poor surface finish.
Excessive amplitude reduces product shrinkage.False
Too much pressure reduction can cause shrinkage due to insufficient support.
Conclusion
Understanding decompression is vital for achieving high-quality injection molded products. By implementing effective techniques, manufacturers can enhance efficiency and reliability.
-
Explore detailed insights into decompression’s impact on molding quality.: Decompression can do a lot to stabilize our process and increase the longevity of our molds. ↩
-
Learn to set precise decompression parameters for optimal molding results.: On today’s machines, molders typically get the option to set decompression before and after screw rotation/recovery. Are they using this feature … ↩
-
Discover design techniques that support effective pressure management.: On today’s machines, molders typically get the option to set decompression before and after screw rotation/recovery. Are they using this feature … ↩
-
Learn how control systems enhance decompression in injection molding.: The FACTS Total Injection Molding Control (TMC) system integrates and centralizes control of the entire Injection Molding machine. ↩
-
Explore various techniques to improve decompression methods.: Types of Injection Molding Technology · 1. Gas-Assisted Injection Molding · 2. Thin-Wall Molding · 3. Liquid Silicone Injection Molding · 4. ↩
-
Discover how various plastics react under pressure to optimize molding settings.: Pressure may have different effects on dislocations depending on the class of materials. It may affect the structure, the stability, or the mobility of the … ↩
-
Explore modern control systems for precise decompression adjustments.: Kistler offers sensors to monitor cavity pressure and temperature in the injection molding process – the fundamental basis for efficient monitoring and control. ↩