When I first ventured into the world of injection molding, I quickly realized that the small details could make or break a product’s success. One of those details? The design of reinforcing ribs.
Designing effective reinforcing ribs is essential for maximizing strength and preventing defects in injection molded products. Key considerations include rib thickness, height, angle, layout, and material choice.
But there’s so much more to it than just knowing the basics! Let’s dive deeper into each element to uncover how they impact real-world applications.
Rib thickness should not exceed 50% of wall thickness.True
Maintaining rib thickness under 50% prevents defects like warping.
How Does Rib Thickness Affect Injection Molding?
Rib thickness is a critical factor in injection molding, impacting the structural integrity and aesthetic quality of molded products.
Rib thickness affects injection molding by influencing cooling rates, shrinkage, and the potential for defects like warping. Ideally, rib thickness should not exceed 50% of the product wall thickness to maintain uniform cooling and prevent defects.
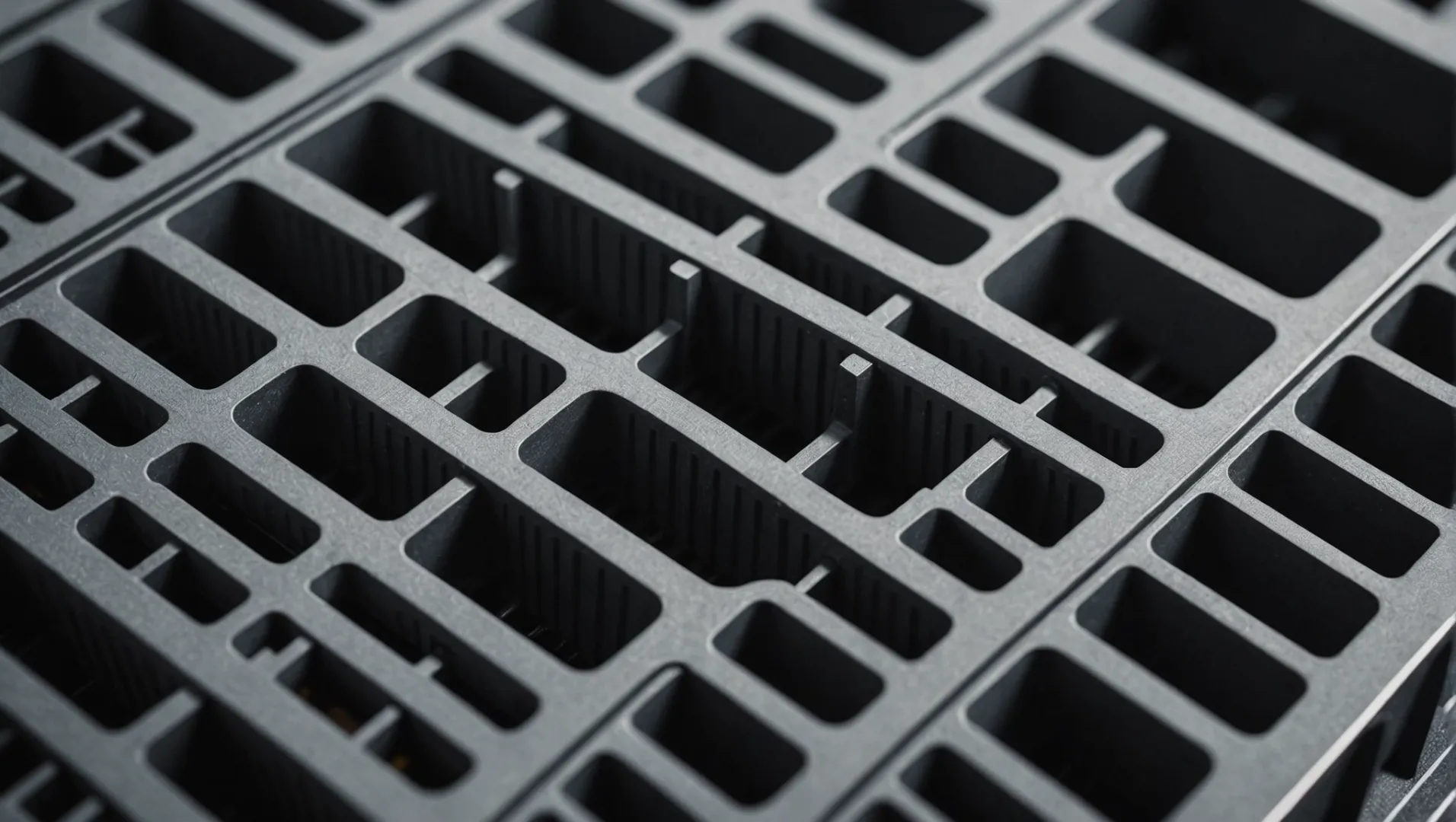
Understanding Rib Thickness and Its Implications
In injection molding, rib thickness is not just a design choice; it is a crucial parameter that dictates the overall success of the molding process. Ribs are integral to enhancing the strength and rigidity of molded parts without significantly increasing weight or material usage. However, improper thickness can lead to defects such as shrinkage marks, warping, and even structural failure.
Importance of Proportionate Rib Thickness
The general guideline for rib thickness is that it should not exceed 50% of the wall thickness of the main component. This proportion ensures that cooling occurs evenly across the part. Uneven cooling can cause differential shrinkage, leading to internal stresses that manifest as warping or distortion. Moreover, excessive rib thickness can result in prolonged cooling times, thereby increasing cycle times and production costs.
Consider a scenario where the rib thickness is too large compared to the wall thickness. In such cases, the thicker areas cool more slowly than thinner sections, creating a gradient in cooling rates. This discrepancy can generate internal stress within the part, ultimately leading to warping or even cracking under operational conditions.
Balancing Rib Thickness with Structural Needs
While maintaining appropriate rib thickness is essential, it’s equally important to balance this with the product’s structural requirements. For instance, in applications demanding high rigidity, ribs might need to be thicker. Here, using materials with higher strength-to-weight ratios can allow for thinner ribs while still meeting structural demands. Explore more on materials with high strength-to-weight ratios1.
In some cases, employing simulation tools during the design phase can aid in optimizing rib dimensions and predicting how different thicknesses will affect the final product. These tools provide valuable insights into potential defect areas and allow designers to tweak parameters before actual production.
Practical Application: A Case Study
Consider an automotive component that requires ribs for added structural support. By maintaining rib thickness at or below 50% of the wall thickness, manufacturers ensure that the component does not suffer from cosmetic defects such as sink marks on visible surfaces. Additionally, by optimizing rib placement and thickness, they can achieve necessary mechanical properties without compromising on part aesthetics or manufacturing efficiency.
In conclusion, rib thickness plays a pivotal role in injection molding. By adhering to best practices regarding rib dimensions, manufacturers can mitigate common defects and ensure high-quality outcomes.
Rib thickness should exceed 50% of wall thickness.False
Exceeding 50% leads to uneven cooling, causing defects like warping.
Thicker ribs can increase cycle times in injection molding.True
Thicker ribs cool slower, extending the overall production cycle time.
What Role Does Rib Layout Play in Structural Integrity?
Rib layout is a fundamental aspect of structural integrity in injection molded products, significantly influencing their strength and durability.
Rib layout is crucial for structural integrity as it affects the distribution of stress and the overall stability of injection molded products. Proper rib arrangement ensures even stress distribution, minimizes warping, and enhances rigidity.
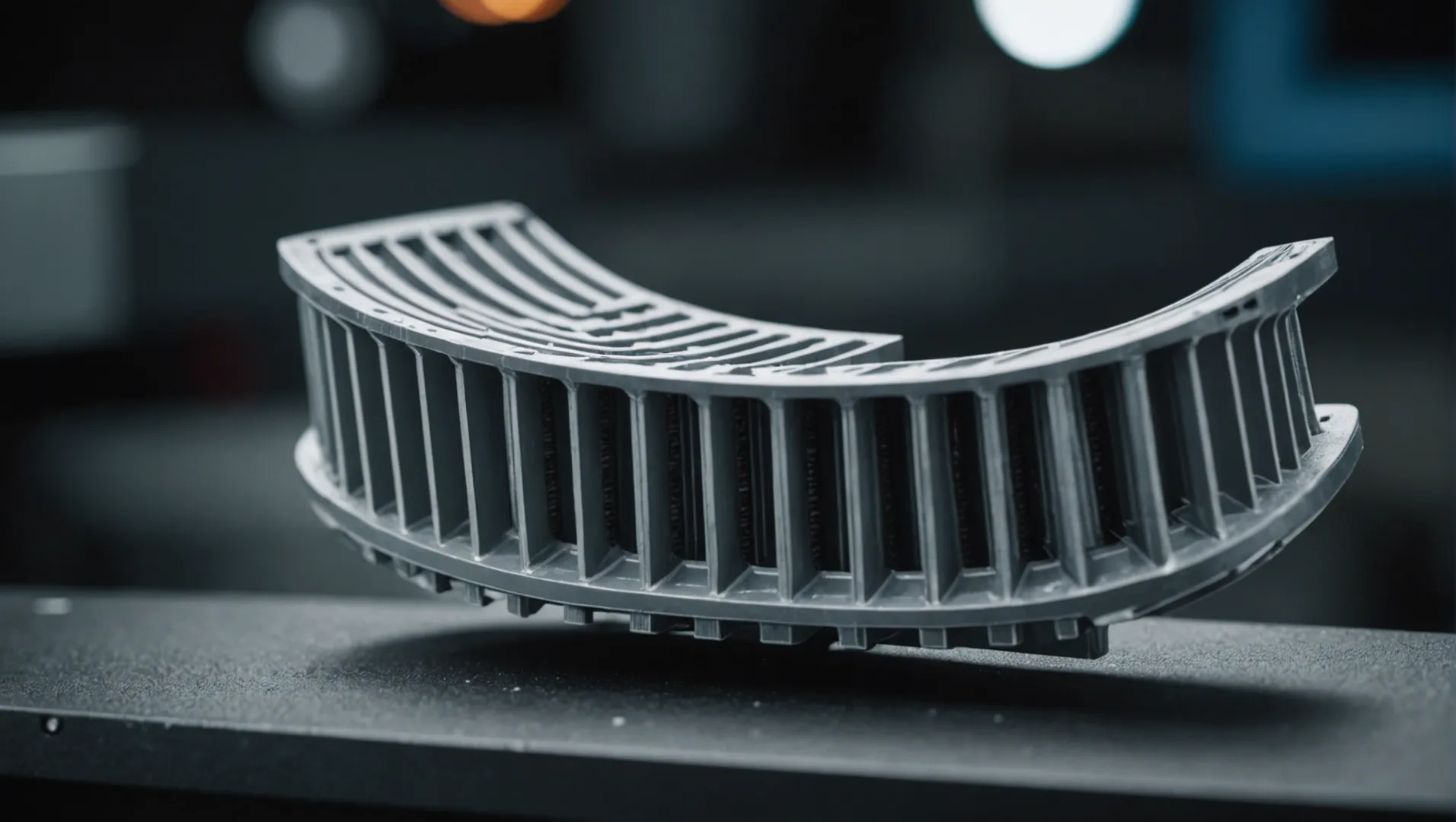
Understanding the Importance of Rib Layout
Rib layout is not just about placing ribs haphazardly across a product. It involves strategic positioning to ensure that the structural integrity of the component is maximized. The layout affects how stress is distributed across the product, which in turn influences its performance under load.
-
Even Distribution: Reinforcing ribs should be evenly distributed across the product to prevent any single area from bearing too much stress. An uneven distribution can lead to warping and other defects during the injection molding process2.
-
Quantity and Location: The number of ribs and their locations should be determined based on the product’s shape and the expected stress points. For instance, areas that will experience higher loads may require additional ribs for reinforcement.
Optimal Spacing for Maximum Effectiveness
The spacing between ribs is another critical factor. Ideally, ribs should be spaced at about 2 to 3 times the wall thickness of the product. This spacing helps in maintaining the balance between providing support and avoiding issues such as weld marks.
Table: Recommended Rib Spacing
Wall Thickness | Recommended Rib Spacing |
---|---|
1 mm | 2-3 mm |
2 mm | 4-6 mm |
3 mm | 6-9 mm |
Connection with Product Walls
A smooth transition between the ribs and the product wall is necessary to avoid stress concentration. This can be achieved using a fillet transition with a radius that is a fraction of the rib thickness. Additionally, incorporating a demolding slope of about 0.5° to 1° aids in easy removal from molds, preventing damage.
Real-world Applications and Examples
Consider automotive components, where rib layout plays a crucial role. In parts like dashboards and bumpers, well-designed rib layouts ensure that these components can withstand impacts and stresses over time without deforming. This principle can be applied across various industries, including aerospace and consumer electronics.
By understanding these aspects of rib layout, designers can create more robust and reliable injection molded products that stand up to real-world demands.
Rib layout ensures even stress distribution in products.True
Strategic rib placement distributes stress evenly, enhancing product stability.
Rib spacing should always match wall thickness for best results.False
Optimal rib spacing is 2-3 times the wall thickness, not equal to it.
Why Is Material Selection Crucial for Reinforcing Ribs?
Choosing the right material for reinforcing ribs is key to ensuring the durability and quality of injection molded products.
Material selection for reinforcing ribs impacts their strength, rigidity, and shrinkage, influencing product quality and functionality.
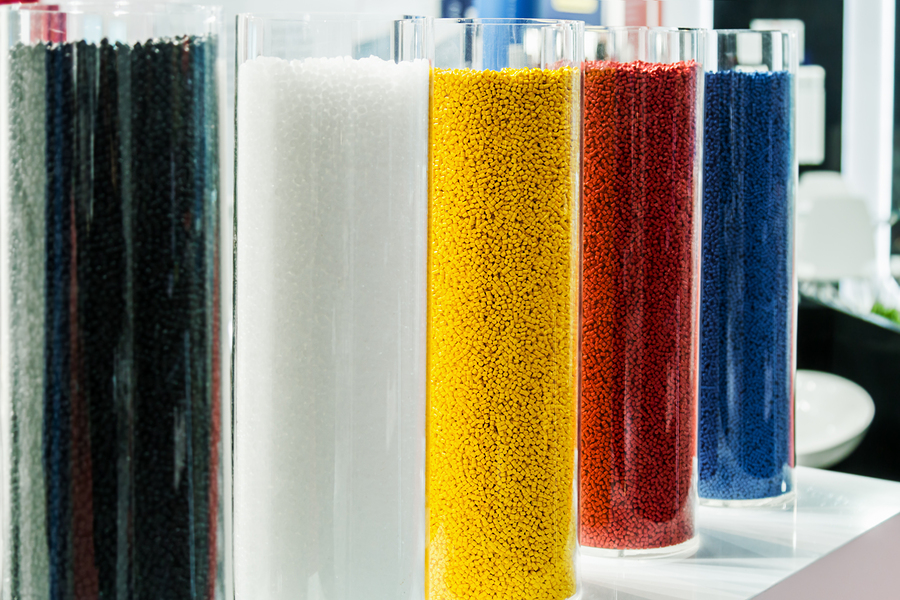
Importance of Material Properties
Selecting the right material for reinforcing ribs is critical because it directly affects the strength3 and performance of the final product. Materials with high strength and rigidity, such as polycarbonate or glass-filled nylon, are typically preferred to maintain the structural integrity of the product.
-
Strength and Rigidity: These properties ensure that the ribs can withstand external forces without deforming. Materials like ABS (Acrylonitrile Butadiene Styrene) offer a good balance between toughness and rigidity, making them ideal for parts that need impact resistance.
-
Shrinkage: Low shrinkage materials minimize the risk of warping or misalignment, which is crucial for maintaining precise dimensions. Polymers with low thermal expansion coefficients are often chosen to mitigate these risks.
Compatibility with Manufacturing Process
The material must also be compatible with the injection molding process, which involves high temperatures and pressures. The thermal stability of the material determines its ability to be molded without degradation.
-
Injection Pressure and Speed: Materials should withstand high injection pressures without compromising on quality. For instance, polypropylene can handle high speeds and pressures well, reducing cycle times and improving efficiency.
-
Mold Temperature: Selecting a material that can tolerate varied mold temperatures is essential to prevent issues such as cracking or surface defects.
Cost-effectiveness and Availability
While performance is a priority, cost-effectiveness cannot be overlooked. The selected material should offer a balance between cost and desired properties.
-
Cost: Common materials like polypropylene are economical while still providing reasonable strength and flexibility.
-
Availability: The material should be readily available to avoid production delays. Local availability also reduces shipping costs and lead times.
Environmental Considerations
Increasingly, the environmental impact of materials is considered in the selection process.
-
Recyclability: Opting for recyclable materials can reduce waste and align with sustainability goals. Materials like recycled PET (Polyethylene Terephthalate) offer eco-friendly options without sacrificing quality.
-
Biodegradability: In some cases, biodegradable materials are chosen for applications where environmental impact is a critical concern.
In conclusion, the selection of material for reinforcing ribs is a multifaceted decision that influences not only the performance and quality of injection molded products but also production efficiency and environmental sustainability. By understanding these factors, manufacturers can make informed choices that lead to superior product outcomes.
Polycarbonate is ideal for reinforcing ribs.True
Polycarbonate offers high strength and rigidity, suitable for ribs.
ABS has high shrinkage in injection molding.False
ABS provides a good balance of toughness and low shrinkage.
How Can Injection Molding Parameters Impact Rib Quality?
Injection molding parameters play a pivotal role in determining the quality of ribs in molded products, influencing their strength and integrity.
Optimizing injection molding parameters such as pressure, speed, and temperature is crucial for achieving high-quality ribs. These parameters ensure even material flow and minimize defects like warping and shrinkage, thereby enhancing the structural performance of the ribs.
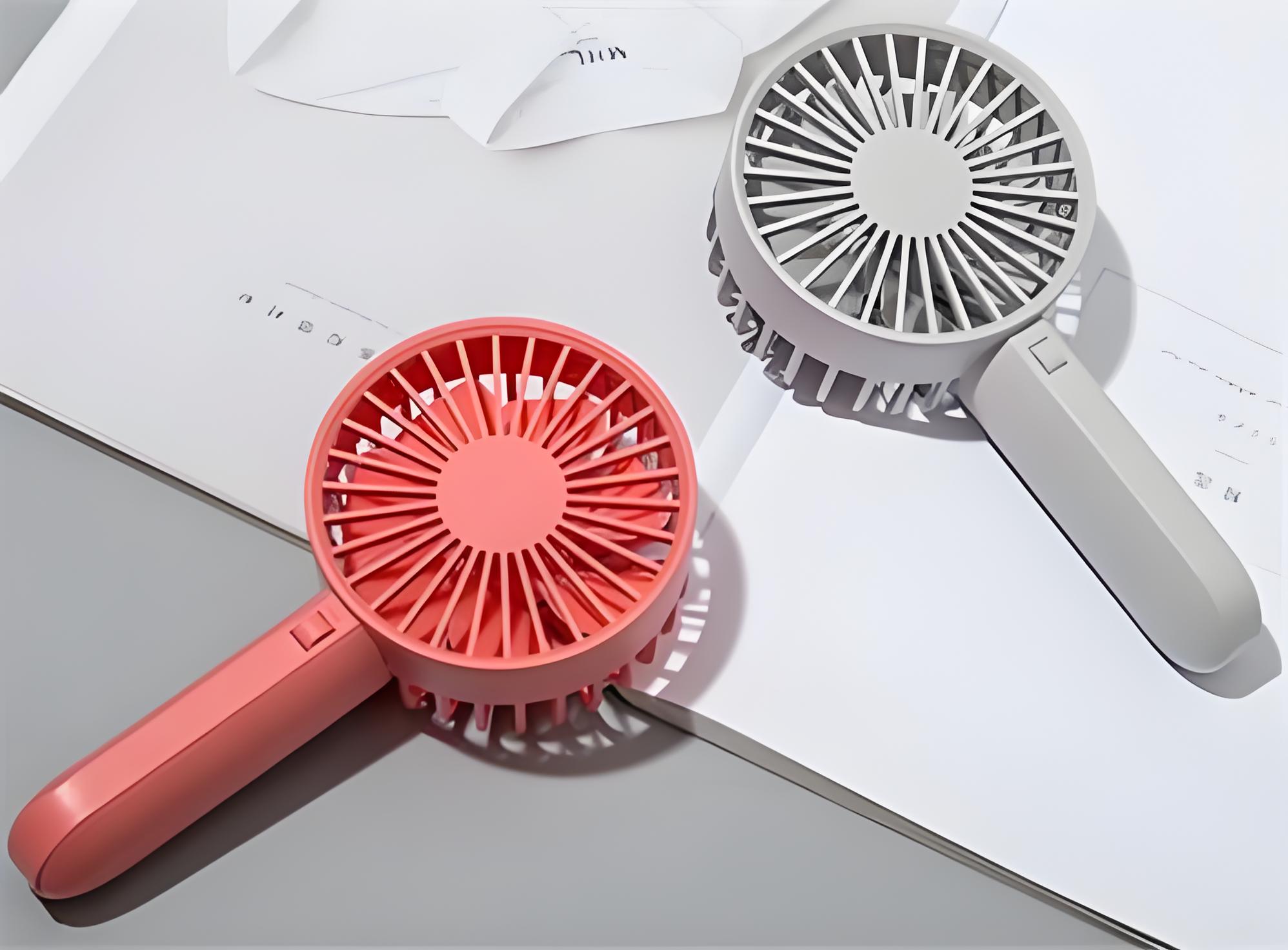
The Role of Injection Pressure and Speed
Injection pressure and speed are critical parameters that directly impact the rib’s final quality. High injection pressure ensures that the molten material fills intricate rib shapes thoroughly, reducing the risk of incomplete filling or voids.
However, excessive pressure can lead to flash or increased stress within the ribs, potentially causing warping. Similarly, adjusting injection speed4 allows for better control over the material flow, which is particularly crucial for complex rib geometries.
Mold Temperature Considerations
Mold temperature significantly affects the cooling rate and, consequently, the dimensional stability of ribs. A higher mold temperature can improve surface finish and reduce internal stresses by allowing a more gradual cooling process.
On the flip side, if the mold temperature is too high, it may prolong cycle times and increase production costs. Therefore, balancing mold temperature is essential for optimizing rib quality while maintaining efficiency.
Cooling Time Optimization
The cooling phase is critical as it solidifies the shape and dimensions of the ribs. Insufficient cooling time can result in defects such as warping or residual stress, while excessive cooling can lead to higher cycle times and costs.
Utilizing simulation tools to determine optimal cooling times can help maintain rib integrity and uniformity across batches.
Material Flow and Rib Design
The design of the rib itself influences how material flows during injection. Ensuring that ribs are appropriately thick and spaced can aid in achieving a consistent fill without defects.
For instance, a rib thickness exceeding 50% of the product wall thickness can cause shrinkage marks. In contrast, a well-calibrated rib design can facilitate smoother material flow, reducing stress concentrations and enhancing overall part quality. Incorporating a fillet transition between ribs and walls5 also helps distribute stress more evenly during demolding.
By understanding these parameters and their interplay with rib design, manufacturers can significantly enhance the quality of their injection molded components.
High injection pressure reduces voids in ribs.True
High pressure ensures molten material fills intricate rib shapes thoroughly.
Excessive mold temperature shortens cycle times.False
High mold temperature prolongs cycle times, increasing production costs.
Conclusion
By mastering rib design, I can ensure that my injection molded products are not only strong but also reliable and efficient.
-
Find materials allowing thinner ribs without compromising strength.: Key features: High rigidity • Resistance to scratches • Good strength-to-weight ratio • High weldability; Applications: ABS is widely used in the manufacture … ↩
-
Discover how rib layout influences injection molding efficiency and product quality.: Ribs are thin wall-like structures that add support and rigidity to injection molded parts. They are thinner than primary walls and are used to support these … ↩
-
Discover which materials enhance strength and rigidity effectively.: This article will discuss the best practices for designing one type of critical feature: injection-molded ribs. ↩
-
Learn how speed adjustments optimize material flow and reduce defects.: Even though high-speed injection minimizes the temperature difference of the melt within the mold cavity, shortens the molding cycle, enhances … ↩
-
Discover how fillet transitions help distribute stress evenly.: Aesthetics: Fillets can enhance the appearance of a part. Smooth, rounded transitions are often visually pleasing and provide a tactilely safer surface. Size … ↩