Have you ever wondered why plastic is so flexible? Scientists study what causes this material to be a designer’s best friend.
Plastic’s key properties include thermoplasticity, good fluidity and excellent processability. It also offers repeatability and cures well in molds. These features allow various molding techniques. Manufacturers produce high-quality plastic components because of them.
In the beginning of my journey in product design, I felt really amazed by plastic’s ability to change ideas into reality. Learning about thermoplasticity truly opened my eyes. Plastics become soft and melt with heat, allowing easy shaping. I clearly remember watching injection molding for the first time. It was like magic to see liquid fill a complex mold and cool into a solid object.
These important properties help create fantastic products. They range from car interiors to sleek electronics. Each molding step involves science and creativity. Every design must balance form and function. Ultimately, the product should be ready for mass production.
Thermoplasticity is essential for plastic moldability.True
Thermoplasticity allows plastics to be heated and reshaped multiple times, making it a key property for moldability.
Plastic moldability relies solely on its chemical composition.False
While chemical composition is important, properties like thermoplasticity and fluidity are crucial for moldability.
- 1. What is Thermoplasticity and Why is it Important?
- 2. How Does Fluidity Affect Injection Molding?
- 3. What Are the Various Processing Techniques for Plastics?
- 4. Why is Repeatability Crucial in Plastic Manufacturing?
- 5. What’s the Real Difference Between Thermosetting Plastics and Thermoplastics?
- 6. What Considerations Should Be Made When Choosing Plastic Materials?
- 7. Conclusion
What is Thermoplasticity and Why is it Important?
Have you ever thought about why some plastics magically change shape with a little heat? That wonderful action is called thermoplasticity. This property is very important in many industries. Let me explain this key idea and why it matters.
Thermoplasticity describes how some plastics soften with heat and harden when cooled. This feature allows for various molding methods. It plays a crucial role in production and design. Industries such as automotive, consumer electronics and medical devices rely on this property. It is very important for these fields.
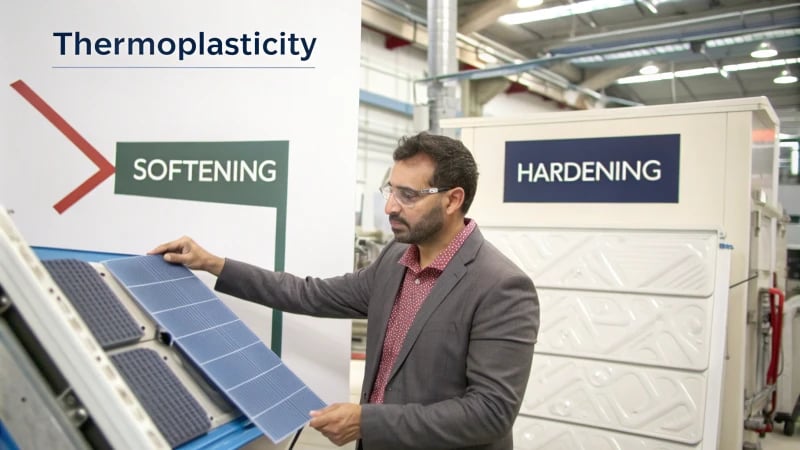
Understanding Thermoplasticity
Thermoplasticity is like a magical skill that some plastics have. You heat them and they turn from solid to soft and moldable. I still remember my first time working with these plastics. Watching them become soft and flexible fascinated me. This ability lets thermoplastics change into almost any shape without staying changed forever.
When you heat thermoplastics such as polyethylene (PE) or polypropylene (PP) past their special temperature, the molecules inside start moving. They move like a calm room suddenly full of dancing people at a party! In this heated state, plastics flow into molds or are pushed through molds. After they cool, they become solid shapes. This heating and cooling process makes thermoplastics very useful for fast and easy manufacturing.
Importance of Thermoplasticity in Manufacturing
Why is all this important? Thermoplasticity affects more than just forming materials; it also influences many areas of manufacturing.
Aspect | Description |
---|---|
Good Fluidity | Thermoplastics exhibit excellent fluidity at elevated temperatures, allowing them to fill complex mold cavities effectively. This is vital for producing intricate parts like automotive interior components and electronic housings. Learn more about fluidity1. |
Processability | The versatility in processing methods means that thermoplastics can be adapted for various manufacturing techniques, such as blow molding and extrusion. This adaptability is essential for creating diverse products from bottles to complex machinery parts. Explore processing techniques2. |
Repeatability | Once the mold design and parameters are set, thermoplastics can produce high volumes of consistent products with minimal variation in shape and quality. This repeatability is ideal for large-scale production and ensures reliability in product performance. Read about repeatability3. |
Curing in Molds | While thermoplastics are shaped by cooling, their counterparts, thermosetting plastics, undergo curing through chemical reactions during molding. This results in a stable and durable product suitable for high-precision applications. Understand curing processes4. |
Applications of Thermoplastic Materials
The true beauty of thermoplastics is their use in many industries:
- Consumer Electronics: They create attractive cases that look good and work well.
- Automotive: They help design light and strong parts inside vehicles.
- Medical Devices: They build parts that stay clean and safe for patients.
Each use of thermoplastics uses their special abilities. This lets us invent new designs while keeping production quick and easy. As I think about my time in the mold industry, these materials continuously amaze me. They let us make things that meet real needs and really improve our lives.
Thermoplastics can be reshaped multiple times without damage.True
Thermoplastics can be repeatedly heated and cooled, allowing them to be molded into new shapes without permanent changes or degradation in material properties.
Thermoplasticity is irrelevant in automotive manufacturing.False
This claim is false; thermoplasticity is crucial for producing lightweight and durable automotive components efficiently through molding processes.
How Does Fluidity Affect Injection Molding?
Have you ever thought about how fluid movement is crucial for forming the best plastic parts? Let’s explore how fluidity links with injection molding. We will uncover its secrets. Fluid movement really influences product quality.
Fluidity is critical in injection molding. It dictates how effectively molten plastic fills a mold. This process is very important. Manufacturers optimize temperature and pressure. These adjustments lead to better fluidity. Improved fluidity results in better product quality. Efficiency also really improves with good fluidity.
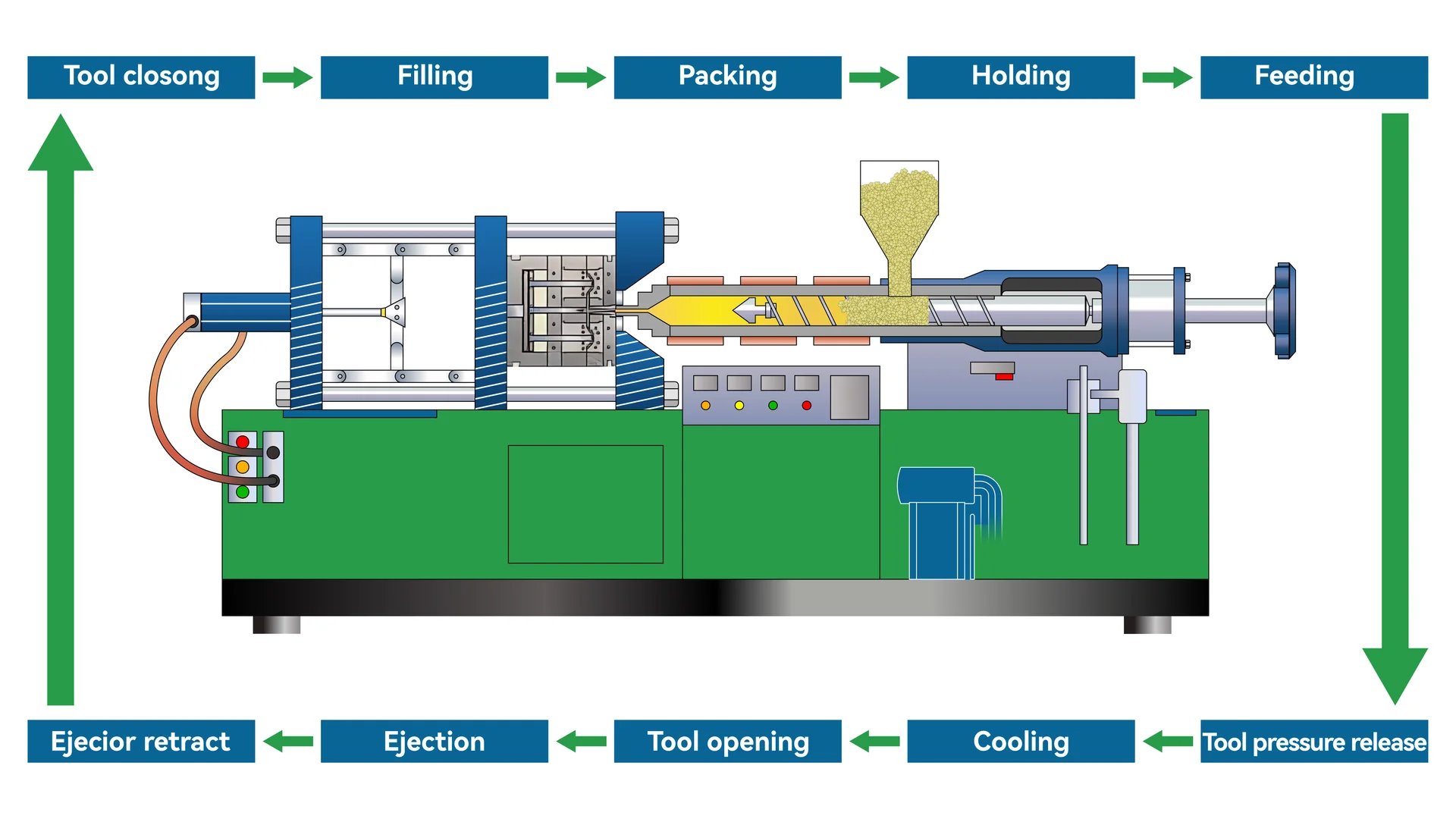
The Importance of Fluidity in Injection Molding
Fluidity plays a pivotal role in the injection molding process, impacting both the quality and efficiency of the manufactured parts. In injection molding, good fluidity is crucial as it allows molten plastic to fill the intricate shapes of the mold cavity effectively. For instance, when using materials like ABS plastic, its moderate fluidity ensures that it can navigate through the runner system smoothly, filling every corner of the mold without leaving air pockets.
Factors such as temperature and pressure directly influence fluidity. At optimal conditions, thermoplastics transition from a solid to a viscous flow state, permitting easy injection into the mold. This behavior is fundamental in producing complex parts, especially in industries like automotive and electronics, where precision is key. Learn more about thermoplastic behavior5.
Key Factors Influencing Fluidity
Fluidity is affected by several interconnected factors:
Factor | Description |
---|---|
Temperature | Higher temperatures reduce viscosity, enhancing flowability. |
Pressure | Increased pressure during injection aids in overcoming resistance within the mold. |
Molecular Weight | Lower molecular weight plastics generally exhibit better fluidity due to less entanglement. |
Additives | Incorporating plasticizers can improve fluidity without altering fundamental properties. |
These elements must be carefully balanced to achieve optimal results in the molding process. For further insights on how to optimize these parameters, check this guide on process optimization6.
Thermoplastic Behavior During Molding
Thermoplastics such as polyethylene and polypropylene demonstrate remarkable fluidity when heated beyond their glass transition temperature (Tg). As they soften, the increased mobility of their molecular chains enables them to flow easily into the mold.
For example, in practical applications:
- Polyethylene (PE) is often used for containers due to its excellent molding capabilities.
- Polystyrene (PS) is ideal for creating detailed products like packaging materials.
Understanding these behaviors can greatly enhance design decisions. Explore more on thermoplastic properties7.
Repeatability and Quality Control
The consistency of fluidity across production runs ensures repeatability in molding processes. If parameters like temperature and pressure are controlled accurately, manufacturers can produce identical parts over time, which is essential for mass production.
This repeatability leads to high dimensional accuracy and uniform quality, minimizing defects and waste in production.
To learn about maintaining quality control in your processes, visit quality assurance practices8.
Conclusion of Insights
Understanding how fluidity affects injection molding provides valuable insights for designers and engineers in optimizing production processes. This knowledge contributes to improving part quality, reducing defects, and enhancing overall manufacturing efficiency.
Good fluidity ensures effective mold filling during injection molding.True
Effective mold filling is crucial for quality parts, and good fluidity facilitates this process by allowing molten plastic to flow into intricate shapes without air pockets.
Higher temperatures always reduce viscosity in injection molding.False
While higher temperatures generally reduce viscosity, this relationship can vary based on material properties and specific conditions in the molding process.
What Are the Various Processing Techniques for Plastics?
Have you ever thought about how everyday plastic items come to be? The process of creating plastic objects is interesting. These techniques really shape our lives in many ways.
Plastic processing techniques include injection molding, extrusion, blow molding and compression molding. Each method has unique uses. These methods focus on production efficiency and product quality. Designers who truly understand these techniques improve product designs for mass production.
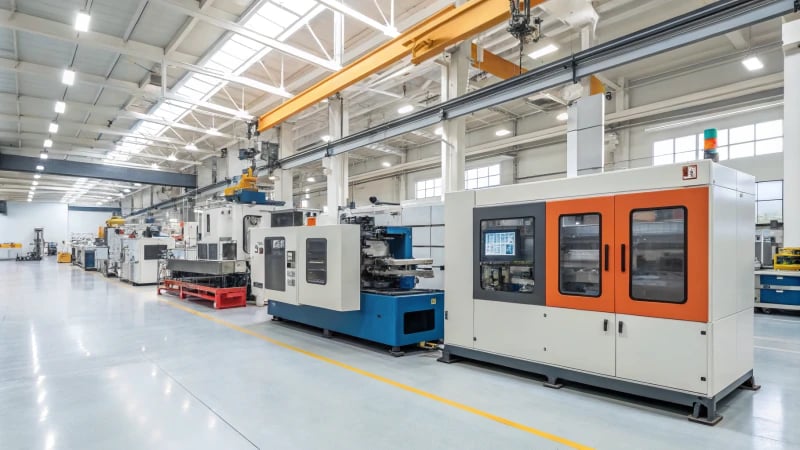
Understanding Basic Plastic Processing Techniques
Plastics are a special type of material, known for their flexibility in different industries. When I first started learning about these processes, it felt like discovering hidden secrets. Each technique – like injection molding, extrusion or blow molding – offers unique benefits.
Injection Molding
Injection molding quickly became one of my favorite topics. It’s like creating a small artwork with a machine! In this process, molten plastic fills a mold under high pressure, allowing it to fill the cavity and take its shape. Key features include:
- Thermoplasticity: A fascinating feature is how some plastics, such as polyethylene (PE) and polypropylene (PP), soften with heat. I remember being amazed by how they flow smoothly into detailed shapes.
- Repeatability: I’ve seen how this technique maintains consistent quality. As long as the mold and process remain stable, every batch turns out perfect.
For more information on injection molding, see this comprehensive guide9.
Extrusion
Extrusion taught me how long plastic products are formed. It’s similar to squeezing toothpaste from a tube but much larger! Here’s the process:
- Heating and Melting: Plastic pellets go into a heated barrel and melt. I imagine the change from solid to liquid – it’s quite the sight!
- Shaping: The melted plastic pushes through a die, forming continuous shapes like pipes and sheets. I often think about the vital role these long products play in daily life.
- Cooling: The extruded shape cools with air or water, solidifying into its final form.
The efficiency of this technique is very impressive. Learn more about extrusion in this detailed article on plastic extrusion processes10.
Blow Molding
Blow molding combines science and creativity! This process is mainly for hollow plastic items like bottles. Here’s what happens:
- Creating a Parison: A tube of molten plastic extrudes – like blowing up a balloon!
- Blowing into Shape: The parison clamps into a mold and inflates with air, matching the mold’s shape.
- Cooling and Ejecting: After cooling, the finished piece ejects and is ready for use.
This technique makes lightweight containers we often overlook. Discover more about blow molding in this informative article11.
Compression Molding
Compression molding offers its unique appeal, especially for thermosetting plastics. I find it amazing how heat and pressure blend to form strong products:
- Preheating: The plastic material heats before entering the mold.
- Shaping: It compresses in the mold, flowing and forming – much like baking a cake!
- Curing: Heat triggers a reaction, hardening the material into a sturdy structure.
This method excels at creating parts with high dimensional stability. For more on this technique, see this compression molding overview12.
Key Comparisons of Processing Techniques
Technique | Type of Plastic | Key Advantages | Typical Applications |
---|---|---|---|
Injection Molding | Thermoplastics | High precision, repeatability | Automotive parts, consumer goods |
Extrusion | Thermoplastics | Continuous production, efficiency | Pipes, sheets |
Blow Molding | Thermoplastics | Lightweight hollow products | Bottles |
Compression Molding | Thermosetting | High strength, dimensional stability | Electrical components and mechanical parts |
By understanding these processing techniques and their specific applications, designers like me can optimize their product designs for mass production effectively.
Injection molding produces plastic parts with high dimensional accuracy.True
Injection molding allows for precise replication of designs, ensuring consistent quality and accuracy in produced parts, making it a preferred method for many industries.
Blow molding is used primarily for solid plastic products.False
Blow molding is specifically designed for creating hollow products like bottles, not solid items, highlighting its unique application in plastic processing.
Why is Repeatability Crucial in Plastic Manufacturing?
Do you ever think about why repeatability matters so much in plastic manufacturing? This concept really affects product quality and efficiency. Trust me, grasping this essential idea truly changes everything.
Repeatability in plastic manufacturing is very important. It helps keep product quality consistent. Repeatability also guarantees correct dimensions. This allows efficient mass production. It also reduces waste. Manufacturers control parameters like temperature and pressure. Proper control leads to high levels of consistency. Success in the industry relies on this consistency.
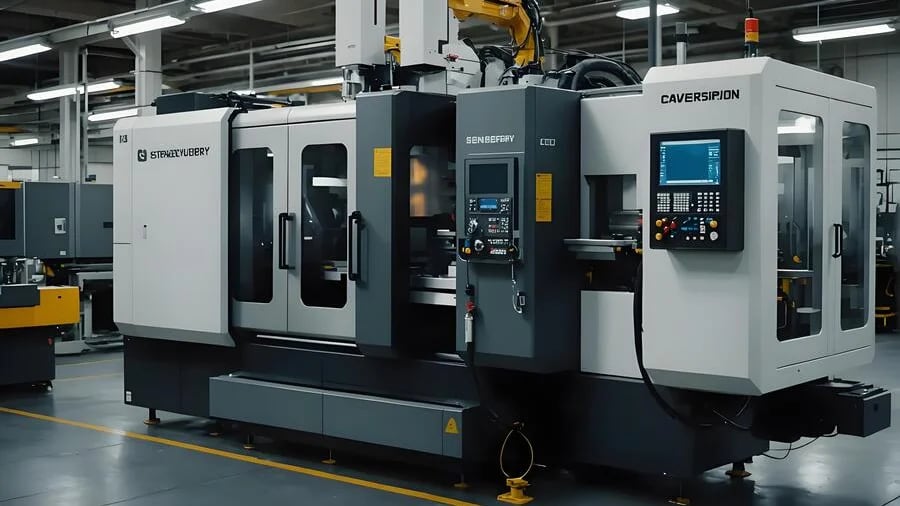
Understanding Repeatability in Plastic Manufacturing
When I first entered plastic manufacturing, I felt confused by the technical terms and complex processes. Everything seemed very complicated. Over time, I learned about repeatability. This idea is not just a fancy word; it is the core of our industry. Repeatability means producing the same part with consistent quality every time. This means that if you order a product today, you get the same one as last week. Consistency keeps customers satisfied and helps reduce waste. It also meets strict standards.
I remember working on a project with hundreds of plastic parts for a new gadget. The pressure was real! Every piece had to meet our high standards; otherwise, we would face expensive problems. Luckily, we knew how to achieve great repeatability. We controlled our process steps very carefully. It was truly satisfying. Our hard work showed in batch after batch of identical parts. Each part was perfect.
Key Factors Contributing to Repeatability
- Stable Process Parameters
Stable process parameters are essential for achieving repeatability in production. Parameters such as temperature, pressure, and injection speed must be meticulously controlled. Here’s a quick reference table illustrating the typical process parameters:
Parameter | Typical Range | Impact on Repeatability |
---|---|---|
Temperature (°C) | 180 – 240 | Affects fluidity and cure time |
Pressure (MPa) | 80 – 200 | Influences mold filling and density |
Injection Speed (mm/s) | 20 – 100 | Impacts the flow of material through the runner system |
Properly maintaining these parameters ensures that every cycle produces parts that conform to specified tolerances.
-
Material Properties
The inherent characteristics of thermoplastics play a significant role in repeatability. Thermoplastics like polyethylene (PE) and polypropylene (PP) soften upon heating, allowing them to fill molds accurately before returning to a solid state. The physical stability of these materials under controlled conditions makes it easier to predict and replicate results. -
Mold Design
A well-designed mold is fundamental for achieving high repeatability. The mold must allow for proper flow and cooling of the material to ensure even distribution and solidification. Complex geometries can pose challenges, but materials with good fluidity can fill intricate shapes effectively without compromising quality. -
Quality Control Measures
Implementing robust quality control measures is essential in maintaining repeatability. Regular monitoring of the manufacturing process through statistical process control (SPC) can help identify variations that may affect product quality. -
Training and Skilled Workforce
A skilled workforce trained in the nuances of plastic manufacturing plays a vital role in achieving repeatability.
Repeatability reduces waste in plastic manufacturing processes.True
Consistent production minimizes defects and excess material usage, leading to less waste overall.
Skilled workforce is unnecessary for achieving repeatability.False
A trained workforce is essential for maintaining process parameters and troubleshooting issues effectively.
What’s the Real Difference Between Thermosetting Plastics and Thermoplastics?
Entering the world of plastics feels really overwhelming sometimes. Understanding thermosetting plastics and thermoplastics is essential for clarity. I will share my journey to grasp these concepts. These materials greatly influence product design. Plastics affect design in very important ways.
Thermosetting plastics and thermoplastics have different molecular structures. Heat changes how they behave. Thermoplastics soften and reshape with heat. In contrast, thermosetting plastics harden permanently. Once cured, thermosetting plastics hold a rigid shape.
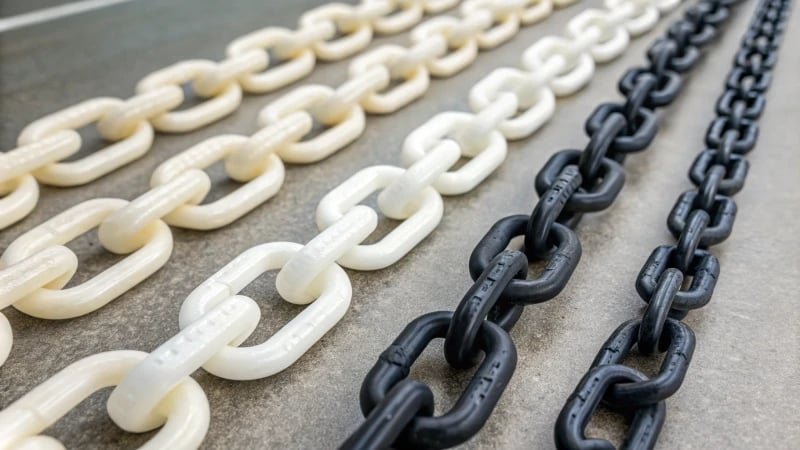
Key Differences in Composition
Thermosetting plastics and thermoplastics are fundamentally different in their composition and structure.
- Thermoplastics consist of linear or branched polymer chains that can be melted and remolded multiple times. This unique property allows for easy processing and recycling, which is crucial in many manufacturing environments. When I worked with polyethylene (PE), I heated it, molded it, and watched it solidify perfectly. This material is really adaptable and inspires creativity.
- Thermosetting plastics, on the other hand, are composed of cross-linked polymer chains. Once they are set through heat or chemical reactions, they cannot be remolded or reheated without degradation. I used phenolic resin in a project, watching it change from a thick liquid to a hard solid under heat. Seeing it hold its shape was satisfying.
Behavior Under Heat
The thermal behavior of these two types of plastics is a major distinction.
- Thermoplastics soften upon heating, allowing them to flow and fill molds easily. For example, when heated above their glass transition temperature (Tg), materials like polyethylene (PE) become pliable and can be formed into various shapes through processes like injection molding or extrusion.
- Thermosetting plastics, however, undergo irreversible curing when exposed to heat and pressure. This process forms a rigid three-dimensional structure that maintains its shape under heat and stress, making them ideal for high-strength applications like electrical sockets or automotive parts.
Applications and Use Cases
Both types of plastics serve distinct purposes in manufacturing and product design. Understanding their applications can guide material selection:
Property | Thermoplastics | Thermosetting Plastics |
---|---|---|
Recyclability | Yes | No |
Molding Process | Can be remolded | Cannot be remolded |
Typical Applications | Consumer electronics, packaging | Electrical insulators, automotive parts |
Strength & Durability | Moderate strength | High strength |
Processing Ease | Easier to process | More complex processing |
This table highlights the strengths and weaknesses of each type of plastic, demonstrating their respective roles in product design.
Processing Techniques
The techniques used to process these plastics differ significantly:
- Thermoplastics are versatile in processing, utilizing methods like injection molding and extrusion to create complex shapes efficiently. Their good fluidity allows for precise filling of molds, ensuring high-quality products.
- In contrast, thermosetting plastics require specific conditions to cure properly. They are often used in applications that demand rigidity and thermal stability, such as in molded parts that need to withstand high temperatures or mechanical stresses.
Summary of Characteristics
Here’s a quick summary of the key characteristics of both types:
-
Thermoplastics:
- Softens with heat
- Easily remolded
- Versatile processing methods
- Recyclable
- Suitable for a wide range of applications
-
Thermosetting Plastics:
- Cures into a hard structure
- Not remoldable after curing
- Requires specific processing conditions
- Generally not recyclable
- Ideal for high-strength applications
For more in-depth understanding, exploring processing techniques13 offers more insights into their application in industry. Additionally, reviewing real-world case studies14 can highlight practical differences in material performance.
Thermoplastics can be remolded after heating.True
This claim is true as thermoplastics soften when heated, allowing reshaping multiple times without degradation.
Thermosetting plastics are recyclable.False
This claim is false; thermosetting plastics cannot be recycled due to their irreversible curing process.
What Considerations Should Be Made When Choosing Plastic Materials?
Selecting the correct plastic materials feels daunting, but it is an important step. This choice affects everything. Product performance depends on it. Manufacturability also relies on it. I have gathered many insights in design. Let me share these ideas with you. These tips might really help simplify the process for you.
When selecting plastic materials, think about how they melt and cool. Also, check how easy they flow and how well you can shape them. Consider if you can create the same shape repeatedly without problems. Look at the methods used to harden them. The effects on the environment are also important. All these factors are crucial for the best performance of your product.
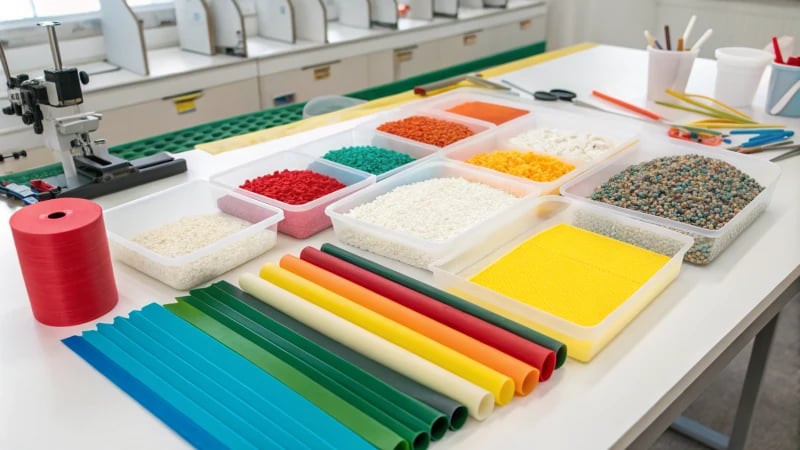
Understanding Thermoplasticity
One fascinating aspect of plastics is thermoplasticity. I see it as a kind of magic that changes plastics. Thermoplastics like polyethylene (PE) and polypropylene (PP) soften with heat and become solid when cooled.
This transition enables various molding techniques such as injection and extrusion. For example, at high temperatures, the molecular chains in these plastics increase their mobility, allowing them to fill complex molds effectively.
Fluidity and Molding Considerations
Fluidity is essential in molding. Plastics must exhibit sufficient fluidity to fill every corner of the mold cavity during processes like injection molding.
I have succeeded with ABS plastic because of its moderate fluidity, which ensures that it can produce intricately shaped parts such as automotive interiors and electronic housings efficiently.
Property | Description |
---|---|
Fluidity | Ability to fill mold cavities evenly |
Example | ABS for automotive parts |
Processability
Ease of processing is a big factor. When developing consumer electronics, I appreciated plastics’ flexibility. Various molding techniques, such as blow molding, can adapt to different parameters without major adjustments.
Plastics can also be mixed with additives to modify their properties without complicating the molding process.
This flexibility allows designers like me to create customized solutions for specific product requirements.
Repeatability in Production
Repeatability is crucial for consistent production. Early in my career, I struggled with quality variations. When the mold design and process parameters are consistent, manufacturers can achieve uniform shapes and properties across multiple production runs.
For example, with stable conditions in injection molding, high dimensional accuracy can be maintained, ensuring product quality and reliability.
Parameter | Impact on Production |
---|---|
Temperature | Affects flow and curing |
Pressure | Influences final shape |
Injection Speed | Controls material flow |
Curing and Shaping Options
Curing affects how plastics retain their shape after molding. Thermosetting plastics undergo a chemical reaction with heat and pressure that forms a strong network structure.
This process enables manufacturers to create high-strength products that maintain their shape over time, such as electrical sockets and mechanical components.
The right process creates very durable results!
Environmental Considerations
Today, sustainability is a priority. I think about the environmental impact of materials—are they recyclable? Biodegradable? Understanding these aspects helps ensure that products not only meet performance criteria but also align with sustainability goals.
I’m really passionate about this.
Summary of Key Considerations
here’s a quick recap of factors I consider:
Factor | Consideration |
---|---|
Thermoplasticity | Ability to mold upon heating |
Fluidity | Ensures effective filling of molds |
Processability | Adaptability to different methods |
Repeatability | Consistent production quality |
Curing | Stability of shape after processing |
Environmental Impact | Sustainability and regulations |
Understanding these aspects helps designers like me create better plastic components. We achieve improved performance across different applications. If you’re interested in specific material properties15 or sustainable practices16, there’s much more to discover!
Thermoplasticity allows plastics to return to solid after heating.True
Thermoplastics like PE and PP soften when heated and harden upon cooling, enabling various molding techniques.
ABS plastic has low fluidity for effective molding.False
ABS is known for its moderate fluidity, which is essential for filling mold cavities effectively during production.
Conclusion
Discover the essential properties of plastics that enable their moldability, including thermoplasticity, fluidity, and repeatability, crucial for efficient manufacturing in diverse industries.
-
Discover more about thermoplastic materials and their applications in modern manufacturing processes. Gain insights into their significance for product design. ↩
-
Learn about different processing techniques used for thermoplastics in manufacturing. Understand how these methods impact product quality. ↩
-
Understand why repeatability in thermoplastic manufacturing is essential for quality control and mass production efficiency. ↩
-
Gain insights into how curing processes differ between thermoplastics and thermosetting plastics, enhancing your knowledge of material properties. ↩
-
Clicking this link will provide you with comprehensive insights into thermoplastic behavior during injection molding, enhancing your understanding of material selection. ↩
-
This link contains expert advice on optimizing injection molding parameters for better fluidity and product quality. ↩
-
Explore this resource for effective strategies on maintaining quality control in injection molded products, ensuring consistency and excellence. ↩
-
This article offers essential information about enhancing repeatability in injection molding processes, crucial for mass production success. ↩
-
This link provides a comprehensive overview of plastic processing techniques that can enhance your understanding and application in design projects. ↩
-
Explore the details of extrusion processes to understand their applications better in product design and manufacturing. ↩
-
Learn about blow molding applications which can be beneficial for designing hollow plastic products. ↩
-
Gain insights into compression molding techniques that can improve your designs requiring high dimensional stability. ↩
-
Explore this link to uncover detailed comparisons and practical examples of thermoplastics and thermosetting plastics, enriching your understanding of their differences. ↩
-
This resource provides real-world applications and case studies that illustrate the distinct uses of thermoplastics versus thermosetting plastics. ↩
-
This query will help you find comprehensive resources on factors influencing plastic material selection. ↩
-
Discover sustainable practices in plastic selection that could benefit your designs and company reputation. ↩