Injection molding is more than just a manufacturing process; it’s an art form that can make or break a product’s success.
To avoid common defects in injection molding products, it’s essential to adjust process parameters, optimize mold design, and ensure high-quality materials. These strategies help prevent issues such as shrinkage, flash, bubbles, flow marks, warping deformation, and poor surface gloss.
While these initial steps provide a solid foundation for defect prevention, delving deeper into specific techniques can significantly enhance outcomes. Discover how expert insights and practical tips can transform your injection molding processes.
Increasing injection pressure reduces shrinkage in molding.True
Higher pressure ensures complete mold filling, minimizing shrinkage.
How Does Material Selection Impact Injection Molding Quality?
The choice of materials in injection molding is crucial, as it directly influences the quality, durability, and functionality of the final product.
Material selection impacts injection molding quality by affecting shrinkage, surface finish, and mechanical properties. Using appropriate materials ensures fewer defects, better performance, and cost-efficiency.
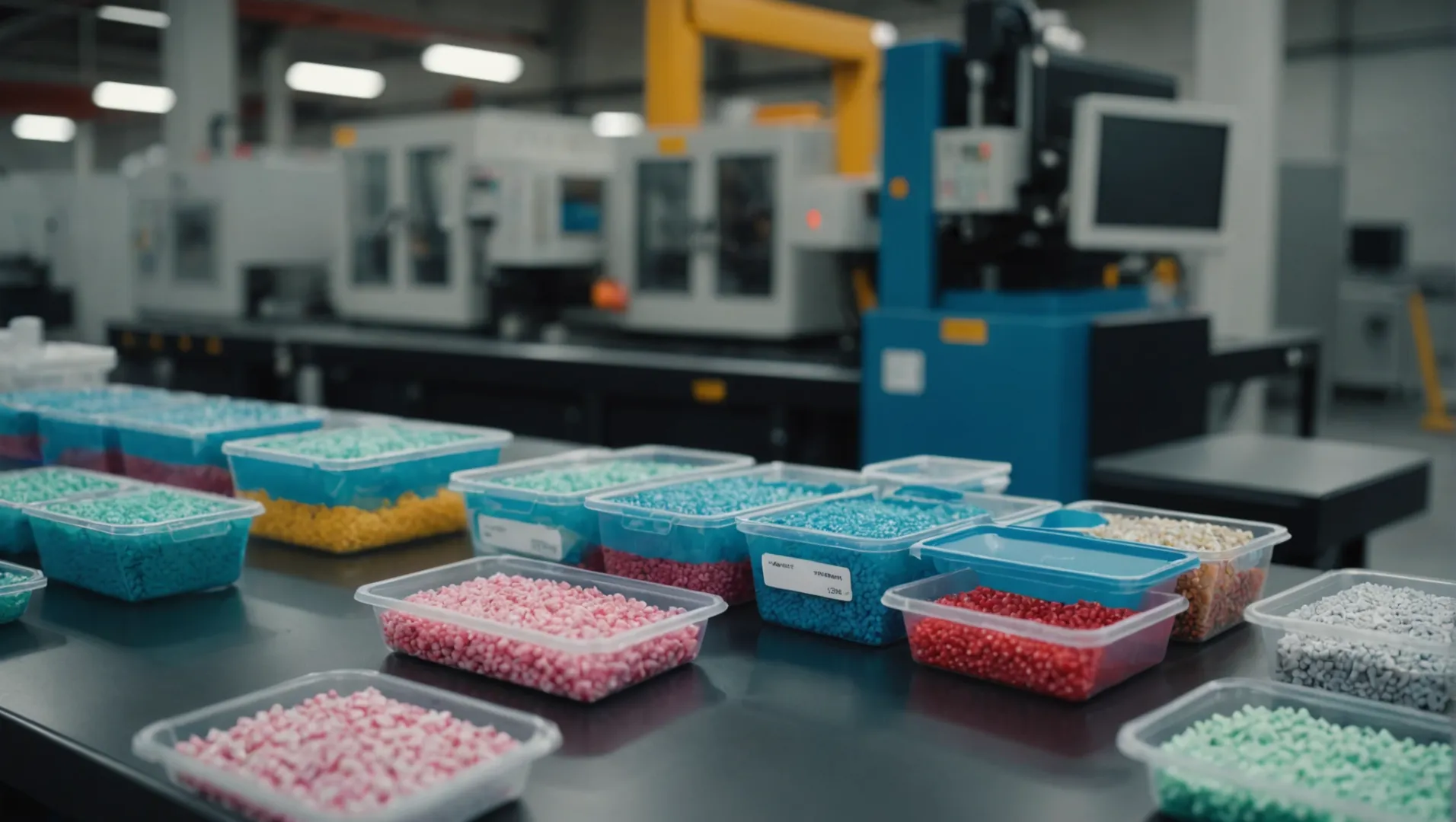
Importance of Material Selection in Injection Molding
Material selection is a critical step in the injection molding process as it determines the mechanical properties, thermal stability, and surface quality of the final product. The choice of material can influence production efficiency and defect rates, impacting the overall success of the project.
Influence on Defect Prevention
-
Shrinkage Control: Materials with predictable shrinkage rates can be more easily managed to reduce defects. For instance, engineering-grade plastics with low shrinkage rates minimize dimensional inaccuracies.
-
Surface Finish Quality: The choice of material affects the appearance and texture of the final product. Using high-quality polymers can prevent issues such as poor surface gloss or flow marks.
-
Mechanical Properties: Selecting materials with suitable mechanical properties ensures the product can withstand its intended use without failure.
Material Type | Shrinkage Rate | Surface Finish Potential | Common Applications |
---|---|---|---|
ABS (Acrylonitrile Butadiene Styrene) | Low | Excellent | Automotive parts, consumer electronics |
Polypropylene | Medium | Good | Packaging, textiles |
Nylon | Variable | Good | Mechanical components, textiles |
Balancing Cost and Quality
While selecting materials, it’s essential to balance cost considerations with quality requirements. Often, choosing a slightly more expensive material can result in lower defect rates and reduced post-production costs. Material cost analysis1 provides insights into making economically viable choices without compromising quality.
Case Studies: Success Through Material Selection
-
Automotive Industry: In the automotive industry, selecting materials like reinforced polypropylene has led to improved durability and reduced weight, showcasing how material choice directly enhances product performance.
-
Consumer Electronics: The use of high-quality ABS in consumer electronics has minimized defects such as warping and poor surface finish, underscoring the importance of material selection in maintaining product aesthetics and functionality.
To delve deeper into how specific materials can affect your injection molding process, consider reviewing industry-specific case studies2. These examples demonstrate practical applications of material selection strategies and their outcomes.
Material choice affects injection molding shrinkage rates.True
Materials with predictable shrinkage rates reduce defects, enhancing quality.
Polypropylene has a low shrinkage rate in injection molding.False
Polypropylene typically exhibits a medium shrinkage rate in molding.
What Role Does Operator Expertise Play in Defect Prevention?
Operator expertise is crucial in minimizing defects during injection molding, directly influencing product quality and production efficiency.
Operators with extensive experience and professional knowledge can significantly reduce defects in injection molding by accurately adjusting process parameters and adhering to operating procedures. Their expertise ensures the consistent quality of injection molded products, highlighting the human factor’s importance in modern manufacturing processes.
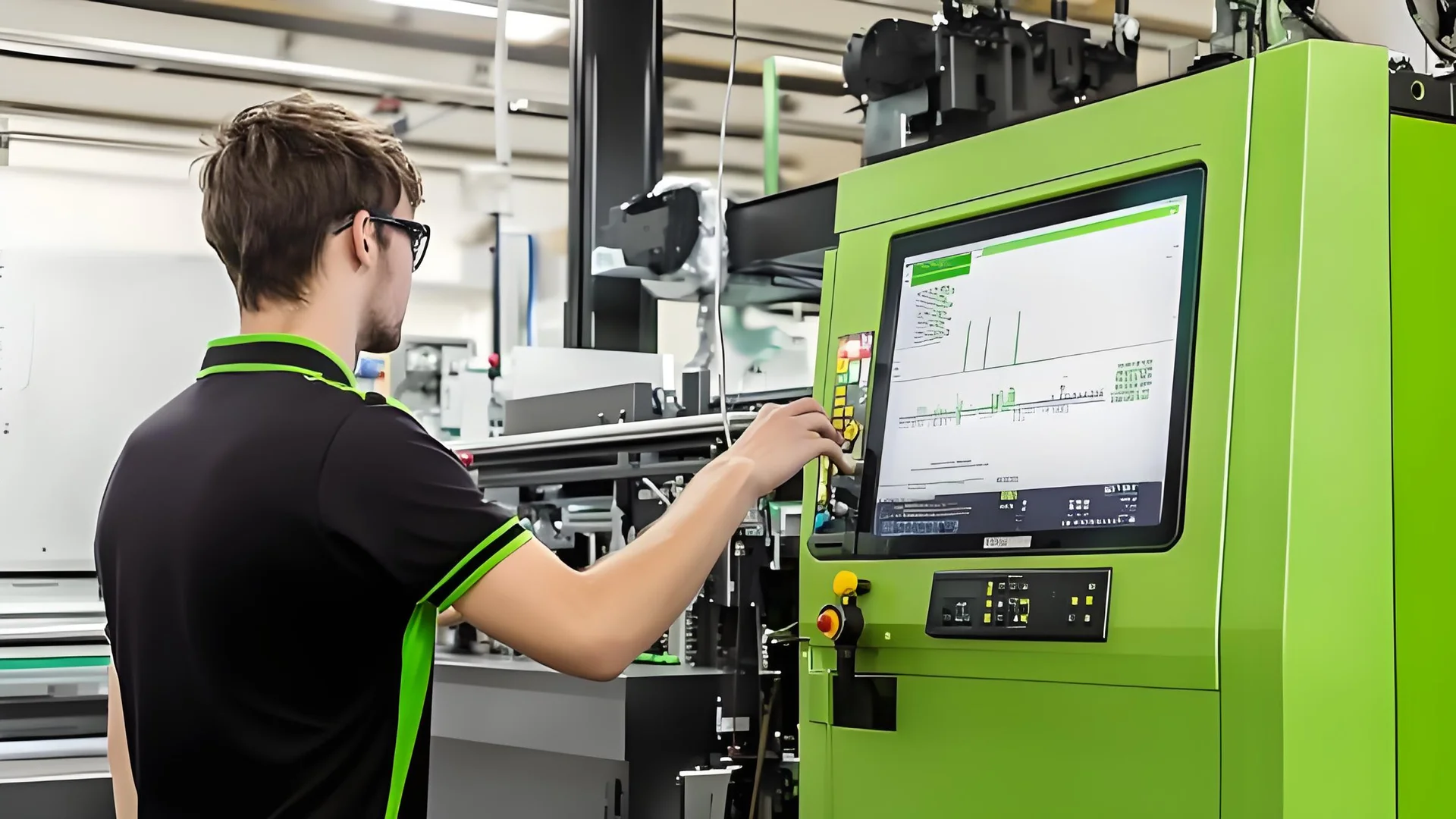
Understanding Injection Molding Dynamics
Injection molding is a complex process involving multiple variables such as temperature, pressure, and time. Operators with deep understanding of these dynamics can make real-time adjustments to prevent defects like shrinkage and warping. For instance, by increasing injection pressure3 and optimizing cooling cycles, they ensure that the molten plastic fills the mold uniformly and cools evenly, minimizing the risk of defects.
The Importance of Process Control
Expert operators are adept at process control, which involves fine-tuning machine settings to maintain optimal conditions throughout production. This skill is vital in preventing issues such as flash and bubbles. By controlling the injection speed and pressure4, they prevent excessive force that might cause the mold to overflow or trap air within the product.
Troubleshooting and Problem Solving
Experienced operators excel in troubleshooting and problem-solving. When defects occur, their ability to quickly identify root causes and implement solutions is invaluable. They draw on their knowledge of mold design, material properties, and process parameters to resolve issues efficiently. This proactive approach not only reduces downtime but also enhances overall product quality.
Continuous Learning and Adaptation
The manufacturing industry constantly evolves with technological advancements. Skilled operators stay updated with the latest techniques and tools through continuous learning. By embracing new technologies, such as automated monitoring systems, they can further refine defect prevention strategies. This adaptability ensures that their skills remain relevant and effective in a rapidly changing environment.
Ultimately, operator expertise bridges the gap between theory and practice in injection molding. While technology provides the tools, it is the skilled hands and minds of operators that drive successful defect prevention and high-quality production outcomes. Their role cannot be overstated in ensuring that injection molded products meet stringent quality standards.
Operator expertise reduces defects in injection molding.True
Experienced operators adjust parameters to prevent defects, ensuring quality.
Technology alone can prevent all defects in injection molding.False
Human expertise is crucial alongside technology for defect prevention.
How Can Technology Innovations Reduce Injection Molding Defects?
In an era of rapid technological advancement, innovations in injection molding technology offer promising solutions to reduce production defects and enhance product quality.
Technology innovations, such as advanced monitoring systems, automated adjustments, and improved mold designs, significantly reduce injection molding defects by providing real-time data, precision, and efficiency in the manufacturing process.
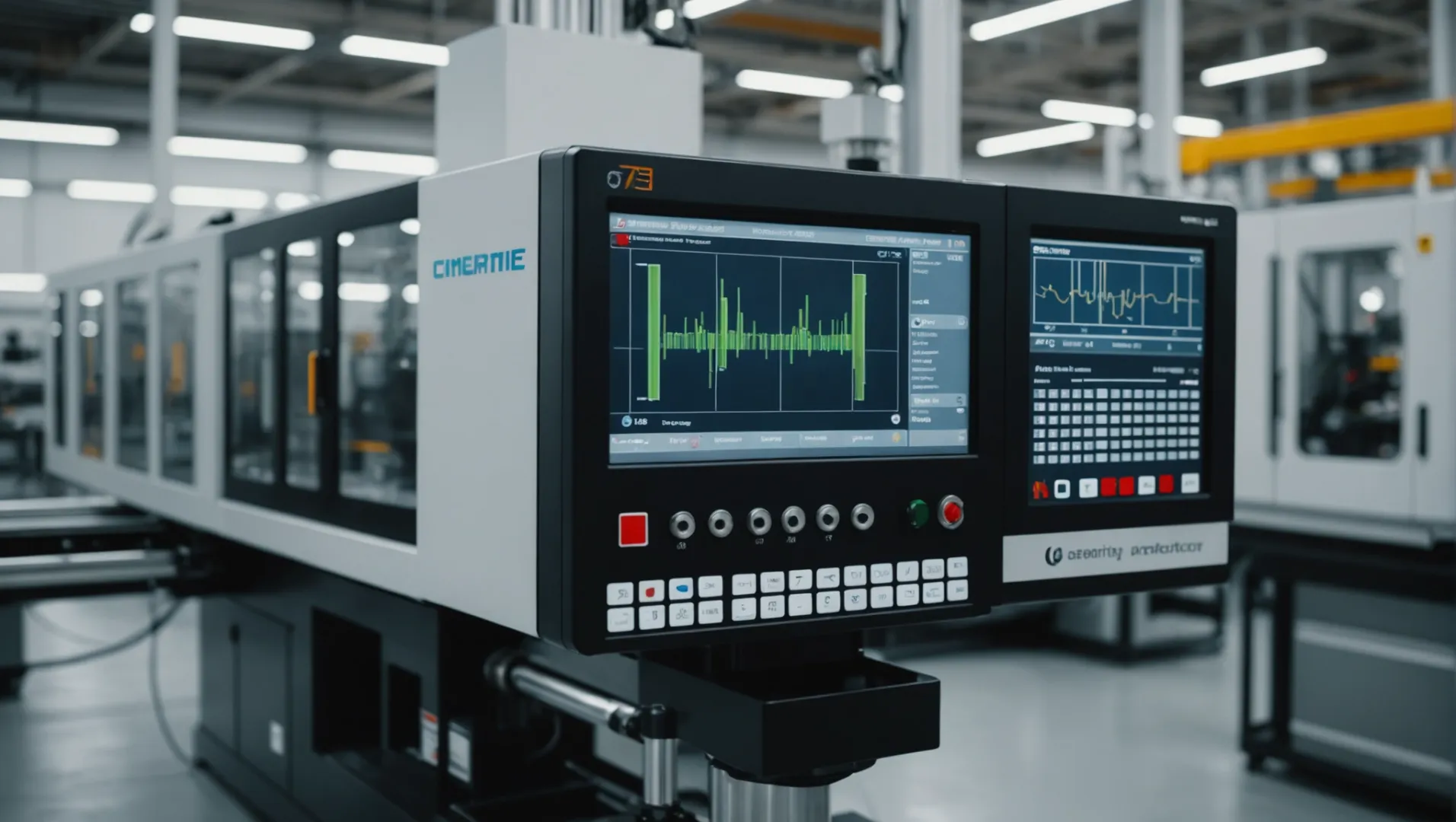
Integrating Advanced Monitoring Systems
The use of advanced monitoring systems in injection molding allows for real-time tracking of crucial parameters such as temperature, pressure, and injection speed. These systems can instantly detect deviations from the optimal settings, enabling immediate corrective actions. By analyzing data patterns, manufacturers can predict potential defects like shrinkage5 and adjust the process accordingly.
Automation and Precision Control
Automation plays a pivotal role in minimizing human error and ensuring consistent quality. Automated systems can precisely control injection parameters, such as pressure and speed, reducing the likelihood of defects like flash6 and bubbles. Furthermore, automation facilitates the quick adaptation of process settings to accommodate varying material properties, which is essential for maintaining uniformity across batches.
Innovations in Mold Design
Technological advancements have led to the development of molds with improved cooling channels and gate designs. Enhanced mold designs ensure even cooling and filling, which are critical for preventing defects like warping deformation7 and flow marks. For example, conformal cooling channels, which closely follow the mold’s contours, provide more efficient heat dissipation compared to traditional straight-line channels.
Use of Simulation Software
Simulation software enables manufacturers to model and test the injection molding process virtually before actual production begins. This preemptive approach helps identify potential issues related to material flow and mold filling, reducing trial-and-error during production runs. Software simulations offer insights into optimal gate placement and cooling system configurations, directly impacting the final product’s quality.
Data-Driven Decision Making
The integration of Industry 4.0 concepts into injection molding processes leverages big data analytics to enhance defect prevention strategies. By collecting and analyzing vast amounts of production data, manufacturers can implement predictive maintenance and optimize process parameters dynamically. This approach reduces downtime and maintains high-quality output consistently.
By embracing these technological innovations, manufacturers can significantly reduce injection molding defects, leading to higher efficiency, reduced waste, and improved product quality. Exploring further advancements and staying abreast of new technologies will be crucial for staying competitive in this evolving industry.
Advanced monitoring systems reduce shrinkage defects.True
Real-time tracking of parameters allows quick adjustments, reducing shrinkage.
Automation increases flash defects in injection molding.False
Automation reduces human error, thus minimizing the occurrence of flash defects.
What Are the Long-Term Benefits of Optimizing Injection Molding Processes?
Unlocking the full potential of injection molding requires strategic optimization, promising enduring benefits in quality, efficiency, and sustainability.
Optimizing injection molding processes offers long-term benefits such as improved product quality, reduced waste, lower operational costs, and enhanced production efficiency. These improvements lead to a competitive advantage and sustainability in manufacturing.
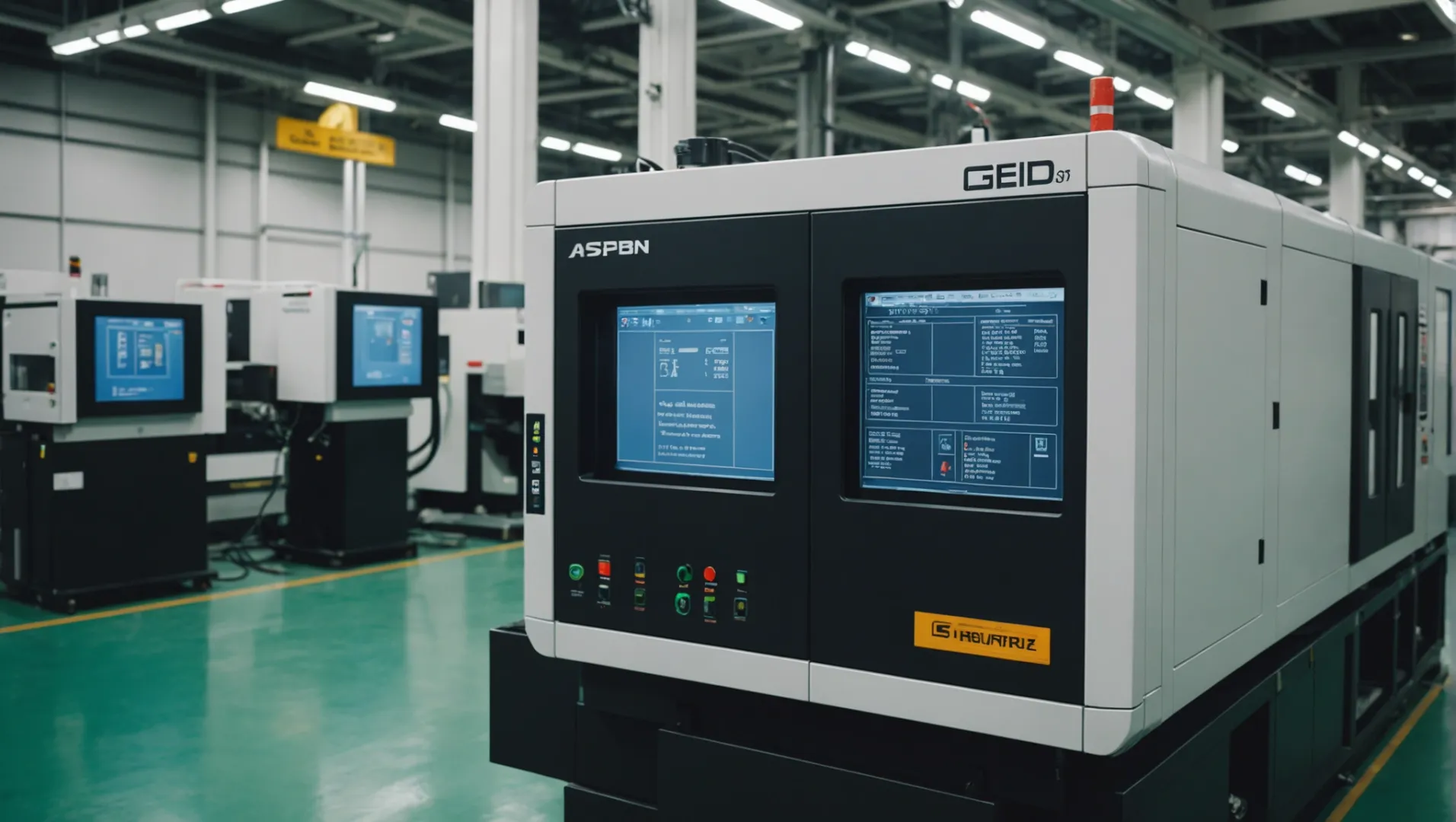
Enhancing Product Quality
By fine-tuning the injection molding processes, manufacturers can significantly elevate the quality of their products. Ensuring precision in process parameters such as injection pressure, holding time, and temperature control reduces defects like shrinkage and flow marks. Over time, these adjustments lead to consistent production of high-quality parts, boosting customer satisfaction and brand reputation.
Reducing Waste and Improving Sustainability
Optimization not only minimizes defects but also decreases material waste. By reducing injection speed8 and optimizing mold design, manufacturers use raw materials more efficiently. This reduction in waste aligns with sustainable manufacturing goals, conserving resources, and lowering environmental impact.
Lowering Operational Costs
Efficient use of materials and energy directly translates into cost savings. By minimizing defects such as bubbles and flash through controlled machine parameters and mold maintenance, companies can decrease the need for rework and scrap. Additionally, extended mold life from optimal design reduces tooling costs over time.
Cost Factor | Before Optimization | After Optimization |
---|---|---|
Material Waste | High | Low |
Energy Consumption | High | Moderate |
Rework Costs | Frequent | Rare |
Boosting Production Efficiency
An optimized process enhances the overall production cycle time. Adjustments like increasing cooling efficiency and improving material flow can lead to faster cycle times without sacrificing quality. This improvement enables manufacturers to meet higher demand and reduce lead times, offering a distinct market advantage.
Gaining Competitive Advantage
In a highly competitive market, the ability to deliver high-quality products quickly and sustainably sets a company apart. Optimization of injection molding processes ensures manufacturers can offer consistent products at lower prices due to reduced operational costs and waste. This capability strengthens market position and opens opportunities for growth.
By continually refining these processes, manufacturers not only improve their immediate operations but also lay a foundation for long-term success in a dynamic industry.
Optimizing injection molding reduces material waste.True
Process optimization leads to efficient material use, reducing waste.
Improved injection molding increases production cycle time.False
Optimization decreases cycle time, enhancing production efficiency.
Conclusion
Avoiding defects in injection molding requires a comprehensive approach involving process optimization, mold design refinement, and high-quality materials. Implementing these strategies ensures superior product quality and operational efficiency.
-
Understand cost-quality balance for better material selection decisions.: Material cost is defined by a model’s design, the material chosen, and the amount of material used to execute the injection molding process. Labor or … ↩
-
Explore real-world applications and outcomes of material choices.: Learn how Plastic Molded Concepts utilized custom automotive plastic injection molding to provide innovative solutions for their client. Read our case … ↩
-
Learn how adjusting pressure prevents shrinkage and improves product quality.: It leads to an increase in the velocity of material via the tip of the injection nozzle. If the mold is empty, the excessive injection pressure … ↩
-
Discover techniques for managing speed and pressure effectively.: Increasing back pressure increases the rotate time. Lowering back pressure leads to a shorter rotate time. Decompression after rotate. Speed … ↩
-
Learn how real-time monitoring reduces shrinkage in molded products.: Implementing advanced monitoring and control systems (such as CoPilot®) allows real-time tracking of various parameters. This enables quick … ↩
-
Explore automated solutions to minimize flash defects effectively.: This article looks at the main strategies for preventing injection molding flash, as well as methods for removing flash (deflashing) after the molding process … ↩
-
Discover new mold designs that combat warping effectively.: Moldex3D supports its users to better evaluate the mold deformation issue by providing the detailed stress and displacement analyses on mold-basecomponents. ↩
-
Learn how slower injection speeds enhance material efficiency and reduce waste.: High-speed flow reduces heat loss and, due to high shear heat from friction, causes an increase in melt temperature, slowing down the thickening … ↩