Injection molding is not just a manufacturing process; it’s an art form that shapes the future of durable products. But ensuring these products can withstand the test of time and impact is where the real challenge lies.
To ensure impact resistance during injection molding, select high-impact resins, optimize processing parameters, design molds thoughtfully, and apply suitable post-processing techniques. These practices improve product durability and quality.
While these strategies provide a solid foundation, let’s delve deeper into the intricate details that truly make a difference in achieving superior impact resistance.
Polycarbonate is a high-impact resin for injection molding.True
Polycarbonate (PC) is known for its toughness and ability to absorb energy, enhancing impact resistance in molded products.
What Role Does Material Selection Play in Impact Resistance?
Material selection is pivotal in determining a product’s ability to withstand impacts, especially in injection molding. Choosing the right materials enhances strength and longevity.
Selecting high-impact resins like polycarbonate (PC) or acrylonitrile-butadiene-styrene (ABS) enhances impact resistance. Ensuring material purity and proper moisture control also mitigates defects, fortifying the product’s durability.
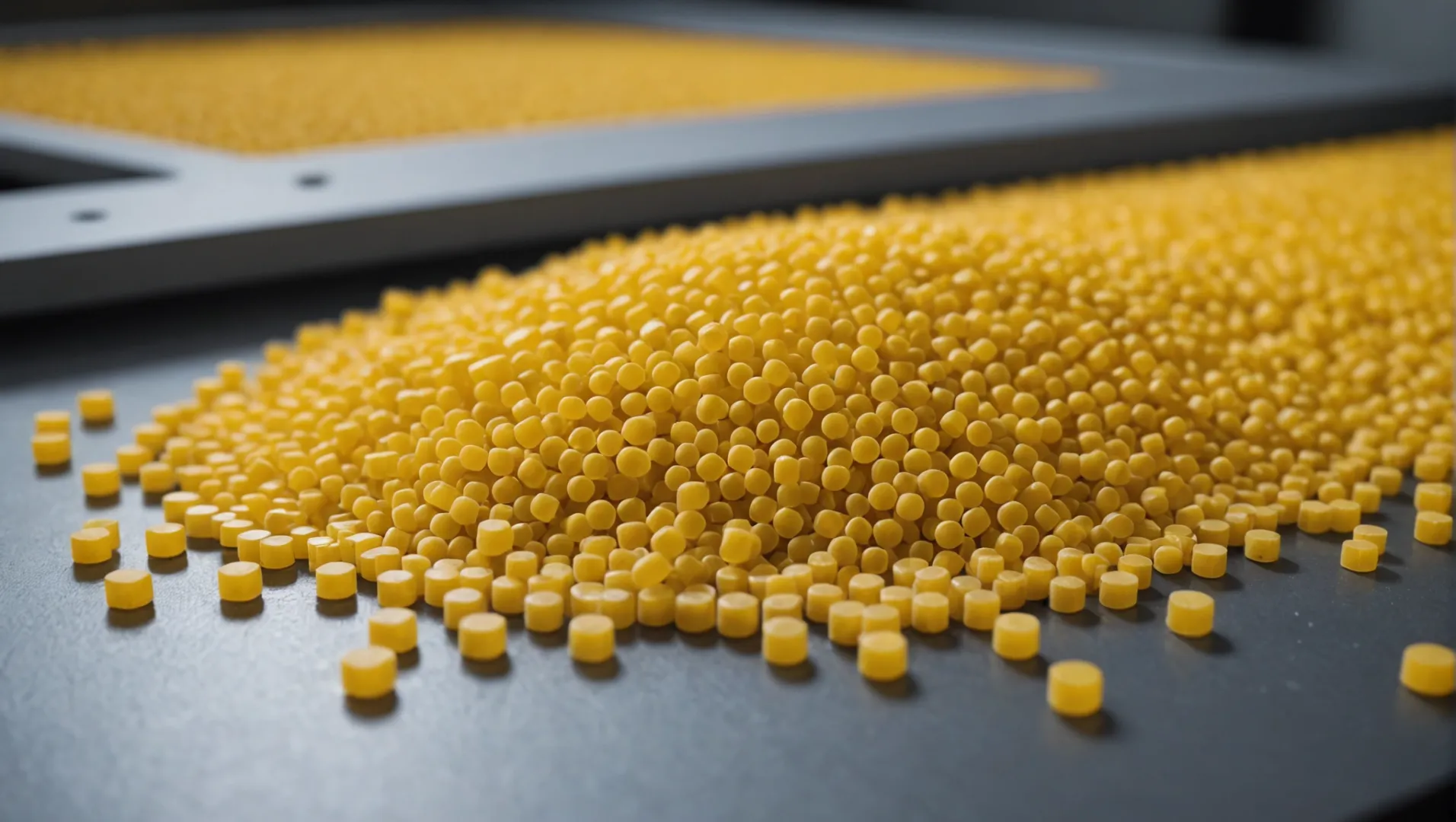
Importance of Resin Choice
In injection molding, the choice of resin significantly affects the impact resistance of the final product. Polycarbonate (PC) and acrylonitrile-butadiene-styrene (ABS) are commonly preferred due to their inherent toughness and ability to absorb energy without cracking. For instance, selecting high-impact resins1 ensures that the molded products can endure substantial mechanical stress, making them ideal for applications requiring enhanced durability.
The decision to use modified resins also plays a crucial role. Resins can be toughened by adding rubber components or other additives, which improve flexibility and impact resistance. This customization allows manufacturers to tailor the material properties to specific application requirements while balancing cost considerations.
Ensuring Material Purity
Impurities within raw materials can lead to weak points that compromise impact resistance. Ensuring high material purity reduces these risks, as impurities can cause internal defects like bubbles or silver streaks. Such defects can manifest during the molding process, leading to weak spots that are susceptible to breaking under stress.
Moreover, controlling moisture content is crucial. Excess moisture in the resin can lead to poor quality issues such as bubbles or cracks during molding. Therefore, drying the raw materials thoroughly before processing is essential to maintain the integrity of the finished product.
Cost-Effectiveness and Performance
While high-impact resins generally offer superior performance, they often come at a higher cost. Balancing these factors is critical. Opting for cost-effective materials without compromising on quality involves strategic selection and testing of various resin types and blends to find an optimal solution.
By prioritizing material selection, manufacturers not only enhance impact resistance but also improve overall product quality. This selection process is a fine balance between performance, cost, and application-specific requirements, which can significantly influence the end-product’s success in the market.
Polycarbonate is preferred for its impact resistance.True
Polycarbonate's inherent toughness makes it ideal for impact resistance.
Impurities in materials enhance impact resistance.False
Impurities create weak points, reducing impact resistance.
How Do Process Parameters Affect Impact Resistance?
Mastering process parameters is pivotal in optimizing the impact resistance of injection molded products.
Process parameters such as temperature, pressure, and cooling time significantly influence the impact resistance of injection molded products. Proper optimization ensures the material fills the mold correctly, minimizes internal stress, and enhances product durability.
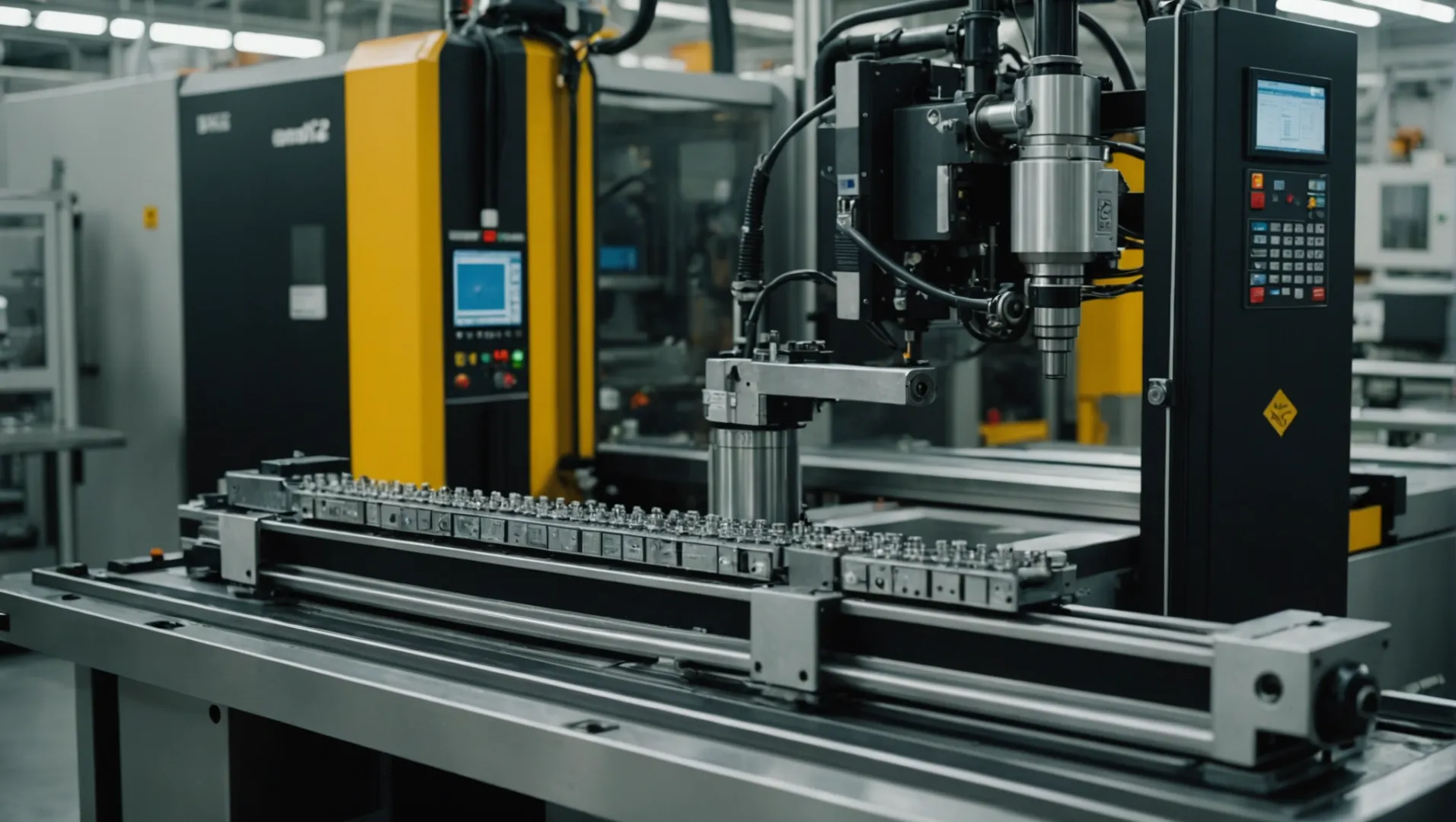
The Significance of Temperature Control
Temperature control plays a crucial role in the impact resistance of molded products. Barrel temperature affects how well the resin melts and flows. Ensuring the temperature is just right prevents material decomposition and maintains fluidity, essential for achieving a uniform fill without defects. Similarly, mold temperature influences crystallinity and molecular orientation, crucial for enhancing impact resistance.
Example: Using polycarbonate (PC), which requires precise temperature management, can showcase how temperature adjustments improve product resilience.
Balancing Injection Pressure and Speed
Both injection pressure and speed are integral to filling the mold effectively. An optimal injection pressure ensures complete cavity filling, reducing defects like pores. However, excessive pressure might introduce internal stresses, detracting from impact strength.
A moderate injection speed prevents material turbulence during filling, reducing stress concentration and improving impact resistance. For instance, adjusting these parameters when using acrylonitrile-butadiene-styrene (ABS) can make a substantial difference in performance.
Holding Pressure and Time Considerations
Post-injection, maintaining adequate holding pressure compensates for material shrinkage, enhancing density and structural integrity. Adjusting holding time based on wall thickness and material properties ensures proper shrinkage compensation without over-pressurizing the product.
Process Parameter Optimization Table
Parameter | Optimal Range | Impact on Product |
---|---|---|
Barrel Temperature | Adequate melting point | Prevents decomposition |
Mold Temperature | Enhances crystallinity | Increases uniformity |
Injection Pressure | Reduces defects | Enhances density |
Injection Speed | Prevents turbulence | Reduces stress points |
Holding Pressure | Compensates shrinkage | Improves strength |
Holding Time | Tailored to design | Balances shrinkage |
Cooling Time and Its Impact
Finally, cooling time ensures the product solidifies correctly. Insufficient cooling can lead to deformation post-molding, while excessive cooling prolongs cycles, affecting productivity. Finding the right balance is key to maintaining impact resistance without sacrificing efficiency.
Understanding these factors provides a framework for enhancing the impact resistance of injection molded products through strategic manipulation of process parameters. For more insights into optimizing these parameters, refer to process optimization techniques2.
Mold temperature affects product crystallinity.True
Mold temperature influences crystallinity, enhancing impact resistance.
Excessive cooling time improves impact resistance.False
Excessive cooling prolongs cycles and doesn't enhance impact resistance.
Why Is Mold Design Critical for Impact Resistance?
Mold design significantly influences the impact resistance of injection-molded products. By focusing on wall thickness, rib structure, and gate placement, manufacturers can enhance product durability.
Effective mold design enhances impact resistance by ensuring uniform wall thickness, strategic rib placement, and optimized gate design. These factors help distribute stress evenly and prevent defects.
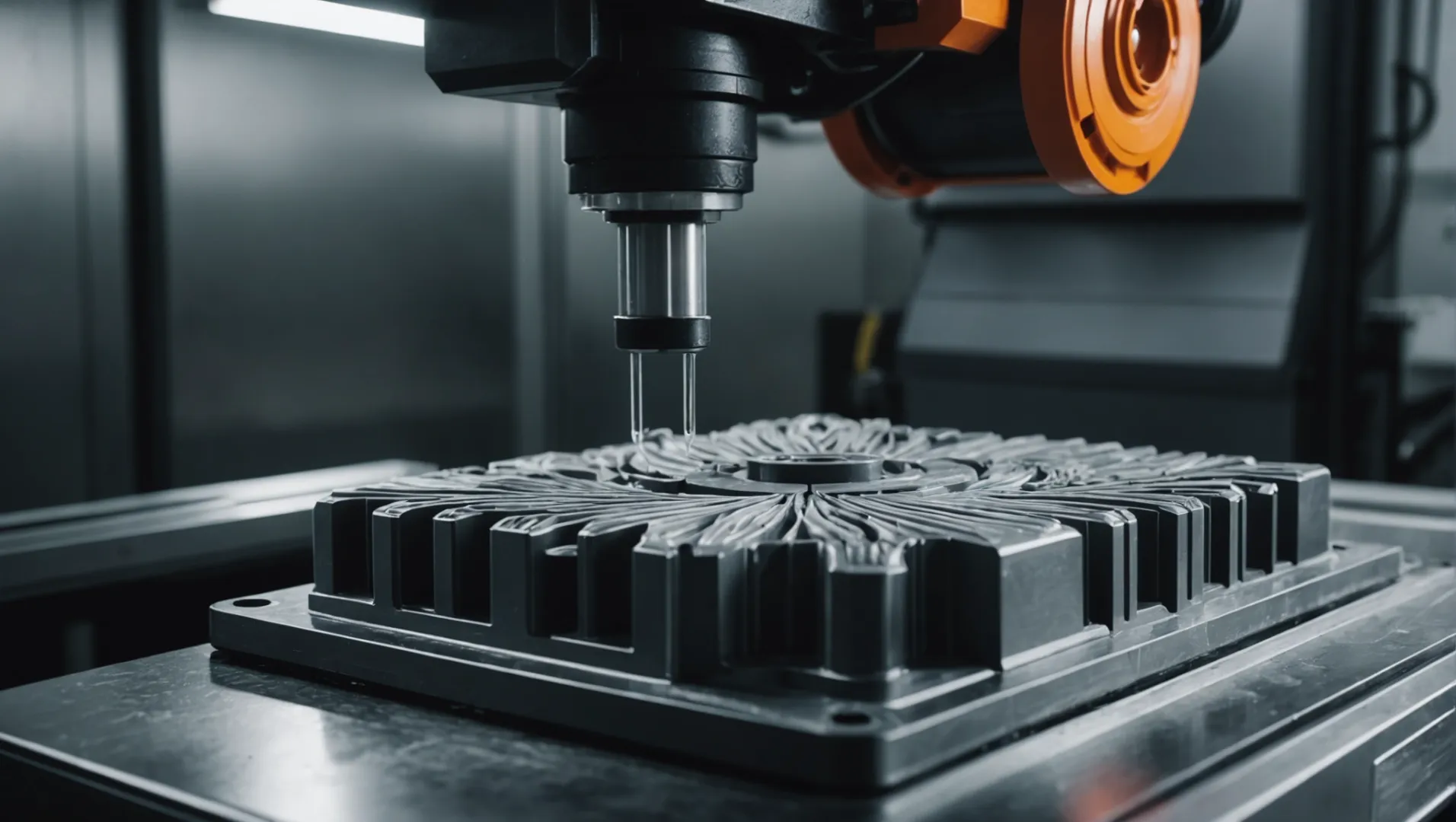
Importance of Uniform Wall Thickness
Uniform wall thickness in mold design is essential to prevent defects such as shrinkage holes or bubbles, which can compromise impact resistance. Thick sections can lead to uneven cooling and stress concentrations, while thin areas may not provide enough strength.
Designing for Uniformity
- Consistent Wall Thickness: Ensures even cooling and solidification, reducing internal stresses.
- Stress Dispersion: Helps the product effectively disperse stress upon impact, enhancing durability.
Role of Ribs and Fillets in Mold Design
Incorporating ribs and fillets in the mold design strengthens the product by increasing rigidity without adding excessive weight. Proper rib placement and rounded fillets can minimize stress concentration points.
Strategic Rib Placement
- Ribs for Reinforcement: Placed strategically, ribs support structural integrity without compromising flexibility.
- Avoiding Overcrowding: Too many ribs can lead to material flow issues, potentially trapping air and forming weak spots.
Optimizing Gate Design for Impact Resistance
The gate is where the molten resin enters the mold cavity, and its placement significantly affects material flow and eventual product strength. An optimized gate design ensures even filling and reduces stress concentrations.
Gate Placement Considerations
- Avoiding Weak Points: Position gates away from areas prone to high stress or potential weak spots.
- Multi-Point Gates for Large Products: Distribute material flow uniformly to prevent defects and improve impact resistance.
In conclusion, thoughtful mold design plays a critical role in enhancing the impact resistance of injection-molded products. From uniform wall thickness3 to strategic rib and gate placement, each element contributes to a product’s ability to withstand mechanical stress.
Uniform wall thickness prevents shrinkage holes.True
Consistent wall thickness ensures even cooling, reducing defects like shrinkage.
Overcrowding ribs enhances product flexibility.False
Too many ribs can cause flow issues, reducing flexibility and creating weak spots.
What Post-Processing Techniques Enhance Impact Resistance?
Discover how post-processing techniques can significantly boost the impact resistance of injection-molded products, ensuring durability and performance.
Post-processing techniques like annealing and surface treatment enhance impact resistance by reducing internal stress and increasing surface hardness. These methods help in achieving superior product durability.
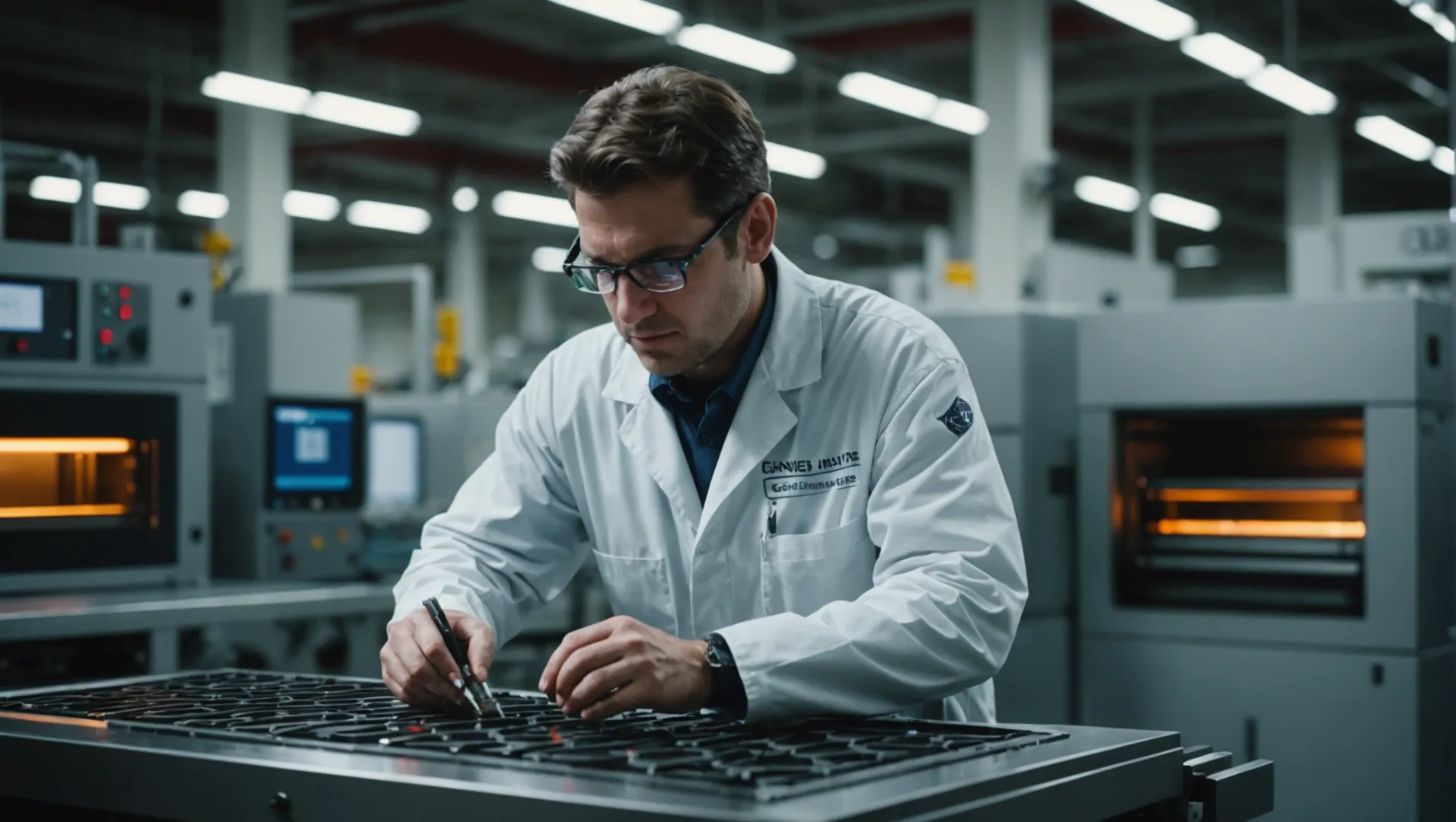
Annealing Treatment: Reducing Stress for Better Durability
Annealing involves heating a product to a specific temperature and then gradually cooling it. This process is essential for relieving residual stresses that can occur during injection molding4. Such stresses often lead to weaknesses in the final product, which can compromise its impact resistance.
-
Temperature and Time: The exact annealing temperature and time depend on the material properties and the size of the product. For instance, polycarbonate (PC) might require different settings compared to ABS.
-
Benefits: By eliminating internal stress, annealing enhances the dimensional stability of the product. This stability is crucial for products expected to undergo physical impacts in their everyday use.
Surface Treatment: Enhancing Surface Hardness
Surface treatments such as spraying and coating play a pivotal role in enhancing the impact resistance of products by improving surface hardness and wear resistance.
-
Methods: Various methods can be employed, including painting or applying special coatings that fortify the product’s surface. Choosing the right materials and techniques is vital to ensure that the product meets its intended usage requirements.
-
Applications: These treatments are particularly beneficial for products exposed to abrasive conditions or those needing additional protection against wear and tear.
Importance of Comprehensive Approach
While annealing and surface treatment are critical, a holistic approach involving material selection5 and process optimization6 ensures maximum impact resistance. By integrating these techniques with thorough raw material quality checks and precise mold design, manufacturers can produce robust, high-performance products capable of withstanding substantial impacts.
Annealing reduces internal stress in molded products.True
Annealing involves controlled heating and cooling to relieve stress.
Surface treatment decreases the hardness of products.False
Surface treatment increases surface hardness, enhancing resistance.
Conclusion
By prioritizing these strategies, manufacturers can significantly enhance impact resistance, ensuring products that stand the test of time and use.
-
Explore how high-impact resins enhance product durability.: In the area of food packing, High-Density Polyethylene trumps most plastic resins. This resin is resistant to high impact, moisture, and heat. ↩
-
Discover advanced strategies to fine-tune injection molding processes.: 1. Temperature Control: · 2. Injection Speed: · 3. Cooling Time: · 4. Plastic Material Selection: · 5. Screw Speed and Back Pressure: · 6. Injection … ↩
-
Learn how uniform wall thickness prevents stress concentrations and enhances durability.: Proper wall thickness will reduce the risk of cosmetic defects in plastic parts. Walls in any plastic-molded part should be no less than 40 to 60 percent that … ↩
-
Understand how annealing reduces stress and improves impact resistance.: Well it’s simply a process that involves heating a specific type of plastic below its glass transition temperature in order to ease all the internal pressures … ↩
-
Learn how choosing the right material boosts product durability.: Impact strength is the material’s ability to resist cracking, fracturing, and deformation under sudden and intense impact. ↩
-
Explore strategies for refining process parameters to enhance impact resistance.: The strength parameters, including impact strength, are influenced by the additives used: fillers, fibers and masterbatches. Additives can … ↩