Do you ever think about how changing the speed of injection molds changes your product quality?
Lowering injection mold speed increases product quality. It reduces surface defects and improves surface accuracy. Less speed also lowers internal stress and stops material degradation. Slow pouring allows molten plastic to flow smoothly. This even flow fills the mold more equally. The result is better surface finishes. Strong structure follows.
I remember the first time I changed the speed of an injection for a project. It happened during a late-night shift. I was very focused on getting a smooth surface for a difficult plastic part. Slowing the process was the solution. Less speed made the flow marks disappear and the product came out with a smooth finish. This was not only about looks. Reducing speed also addressed internal stresses that might cause future bending.
Taking time for each injection phase mattered a lot for material strength. It’s like cooking a good stew. Stews require time to let flavors meld perfectly. Plastic needs time to settle in the mold without high-speed stress. My experience showed me that slower speeds improved both the appearance and durability of our products. Yes, it really did.
Reducing mold speed minimizes surface defects.True
Slower speeds allow even filling, reducing surface imperfections.
Faster mold speed improves structural integrity.False
Fast speeds increase internal stress, compromising structural integrity.
What surface improvements can be achieved with reduced injection speed?
Do you ever think about how slowing down processes might actually encourage faster success in injection molding?
Lower injection speed during molding. This technique gives smoother surfaces. Flow marks get smaller. Silver streaks also become less noticeable. The replication of details becomes very clear. Internal stress is reduced. Products look better. Material stays strong. The product’s appearance improves. Its integrity remains intact.
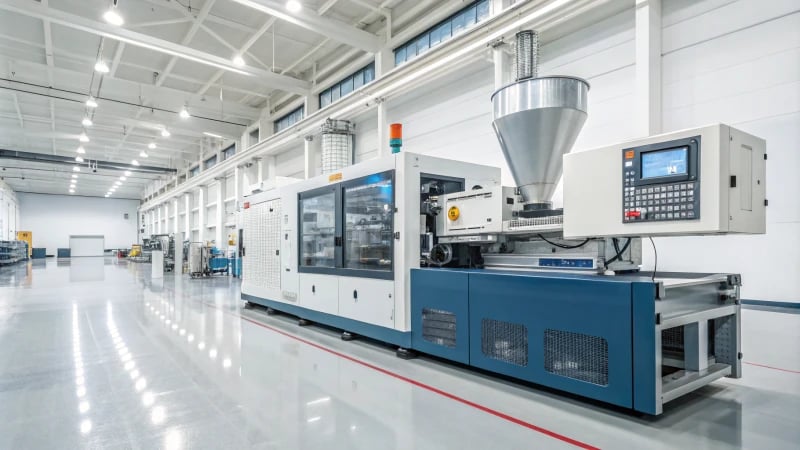
Improving How Things Look
Reducing speed lowers those annoying surface issues. I worked on a project with strict surface needs. Any flaw stood out a lot. Slowing the speed to 100-150mm/s helped the melt fill smoothly. Very few marks appeared. This is critical for clear plastics where any tiny mark shows.
- Surface Accuracy:
For items needing exact texture, slower is better. Once, we needed to copy very detailed mold patterns for decorative parts. Fast speeds couldn’t catch fine textures. But dropping the speed from 200mm/s to about 100mm/s really worked. The textures showed clearly and precisely.
Better Internal Quality
Going slow helps inside the product too. Fast injections bring strong forces, causing stress inside. This was common with thick items. Cutting speed to 120-180mm/s lowered stress and improved stability, stopping warping after opening the mold.
Speed (mm/s) | Effect |
---|---|
>250 | High stress |
120-180 | Reduced stress |
- Density and Uniformity:
A slow pace improves melt compaction, leading to better density and evenness. With high-grade engineering plastics, reducing speed to 80-120mm/s helped fusion and mechanical strength. It gives the material time to settle nicely.
Keeping Material Quality
Heat-sensitive materials like PVC are hard to deal with. Fast speeds risk breaking them down due to heat. Slowing below 100mm/s kept them steady and undamaged.
- Avoiding Property Fluctuations:
Quick injections shift molecular order, changing qualities like crystallinity. I found out that supporting natural crystallization with slow speeds keeps them stable. Steady properties matter for crystalline plastics.
Slowing injection speeds has changed both surface look and inside uniformity in molded items. For more insights, explore resources on injection speed effects1 and mold design optimization2. This exploration is really worthwhile.
Reducing injection speed minimizes surface defects.True
Slower speeds allow even flow, reducing defects like flow marks.
High injection speeds enhance texture accuracy.False
Fast speeds may skip fine textures; slower speeds improve accuracy.
How Does Injection Speed Affect Internal Stress in Molded Products?
Some molded products warp or show annoying surface defects. Speed of injecting the material plays a crucial role.
The speed of injection changes internal stress by altering the shear force on the material during molding. Lowering the injection speed decreases this stress. This really improves product stability and quality.
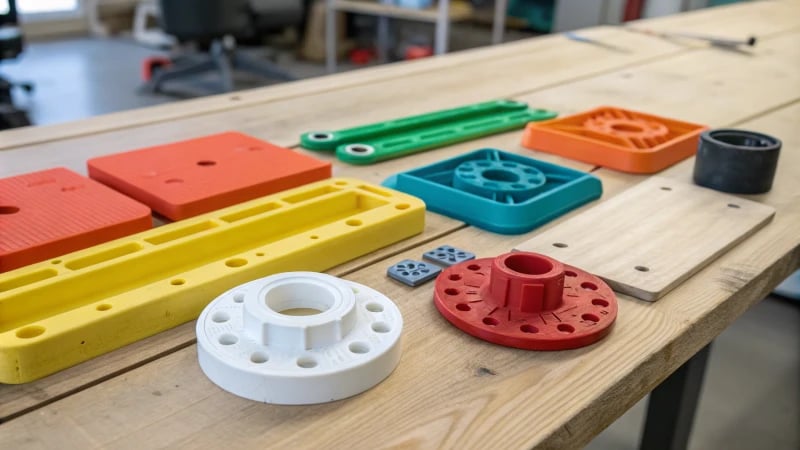
Understanding Internal Stress in Molded Products
I remember starting work with molded items and being clueless that the speed of injecting material caused many problems. Internal stress sneaks in because of quick temperature and pressure changes. This stress is not minor. It can warp or weaken structures.
Effect of Injection Speed on Internal Stress
Imagine driving a car through a narrow alley. Speed too high and something will crash. Fast molding creates strong shear forces, increasing internal stress.
The injection speed3 directly influences the shear force applied to the material. High speeds create significant shear force, increasing internal stress.
Benefits of Reducing Injection Speed
-
Improving Appearance Quality
I recall a project needing perfect looks – no room for flow marks or silver streaks. Lowering the speed gave us smoother finishes and clearer textures. It was like magic.Injection Speed (mm/s) Effect on Appearance >300 High risk of flow marks 100-150 Smooth, uniform surface -
Enhancing Surface Detail
Slower speeds capture every tiny detail, ensuring clear textures on surfaces.
Optimizing Internal Quality
Less speed leads to less shear force and stress. It’s like solving a puzzle where each piece fits perfectly without forcing it.
Slower injection speeds reduce shear forces, thus decreasing internal stress. This optimization improves dimensional stability and prevents product warping.
Product Type | Recommended Speed (mm/s) |
---|---|
Thick-walled products | 120-180 |
Engineering plastic parts | 80-120 |
- Increasing Density and Uniformity
A slower pace allows everything to pack in just right, increasing density and uniformity, which really changes product durability.
Preventing Material Degradation
I learned slowly that fast injections damage materials. For heat-sensitive items like PVC, slow speed protects them, keeping the product intact and consistent.
High-speed injection risks material decomposition due to shear heat. Slower speeds safeguard against this, especially for heat-sensitive materials like PVC.
Material | Risk at High Speed |
---|---|
PVC | Decomposition |
Crystalline Plastics | Property fluctuations |
By following the natural crystallization process4, we stabilize materials. This means every batch is reliable. This knowledge is vital for creating strong products that look good and withstand pressure. Designers must think carefully to improve product quality.
High injection speed increases internal stress in molded products.True
High speeds increase shear force, leading to greater internal stress.
Reducing injection speed enhances surface detail of molded products.True
Slower speeds allow better mold detail replication, improving texture clarity.
How Does Speed Influence Material Degradation?
Do you ever ask yourself how fast manufacturing might change the strength and quality of materials?
Speed impacts how materials break down, changing shear force and temperature. Lower speed helps stop breakdown in materials sensitive to heat. It keeps molecular structures stable. This stability enhances product quality. Product quality indeed becomes better.
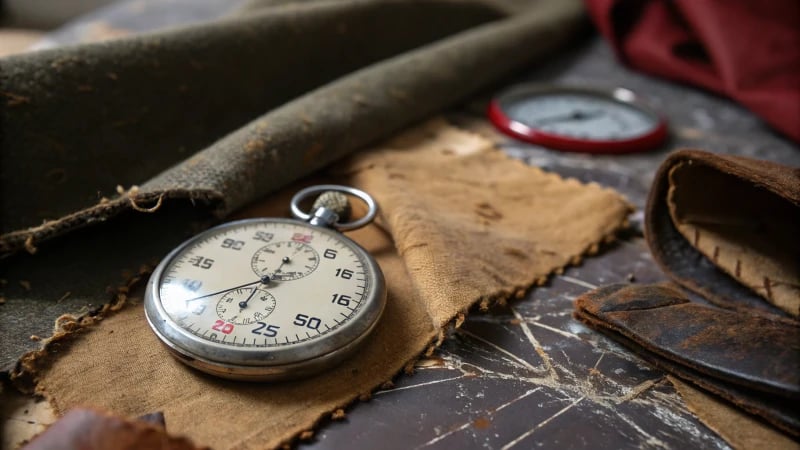
Understanding Speed’s Impact on Material Quality
In my early days in manufacturing, I realized that speed isn’t only about finishing faster – it’s essential for keeping material strong5. Take injection molding. It resembles cooking a steak; too quickly and you could burn the outside and leave the inside raw. The pace at which material enters a mold really influences both the external and internal quality of a product.
External Quality:
- Surface Defects: Picture rushing through a painting job. You’d really leave brush marks, right? Fast injection speeds cause similar issues like flow marks and silver streaks. When slowed, the flow becomes more even, which improves surface looks.
- Surface Detail Replication: Imagine painting a detailed artwork slowly; lower speeds allow for better copying of fine patterns or textures on a product’s surface. This is vital when high visual quality is important.
Internal Quality:
- Stress Reduction: Quick speeds introduce big shear forces, like pulling a rubber band rapidly – it snaps back. This creates inner stress that might bend products later. By slowing down, stress spreads evenly, resulting in steadier outcomes.
- Density Improvement: A slower approach gives time for material to fully fit, bettering density and equality – similar to letting bread dough rise properly before baking.
Speed’s Role in Material Decomposition
For materials like PVC, too much speed raises shear heat, leading to breakdown. It’s like overcooking a fragile fish; too much heat and it falls apart. Lower speed decreases heat build-up, keeping the material sound – a careful balance6 critical for heat-sensitive uses.
Consistency in Material Properties
Fast processing might cause shifts as molecules realign. Lowering speed supports natural crystallization, ensuring steady properties. This is important for crystalline plastics where the crystal structure determines strength and lasting power.
Key Takeaways in Speed Management
Material | Ideal Speed (mm/s) | Benefits |
---|---|---|
PVC | <100 | Prevents decomposition |
Transparent Plastics | 100-150 | Reduces silver streaks |
Engineering Plastics | 80-120 | Enhances density and mechanical properties |
By changing processing speeds, I really optimize both outside and inside qualities of a product, leading to better durability and performance. Good speed management makes sure that both visual and functional needs are met without losing material quality. Learn more about optimizing manufacturing processes7.
Slower speeds reduce surface defects in injection molding.True
Slower injection speeds allow melt to flow uniformly, enhancing surface appearance.
High injection speeds improve the density of molded products.False
High speeds increase shear force, causing stress and warping, not density improvement.
Can Adjusting Injection Speed Improve Mechanical Properties?
Have you ever thought about changing the injection speed to possibly create stronger and more stylish molded products?
Slower injection speeds greatly improve mechanical qualities. Better internal stress distribution and increased density happen. Uniformity is achieved in this way. It reduces surface defects like flow marks and silver streaks. Products become really high-quality. Top quality!
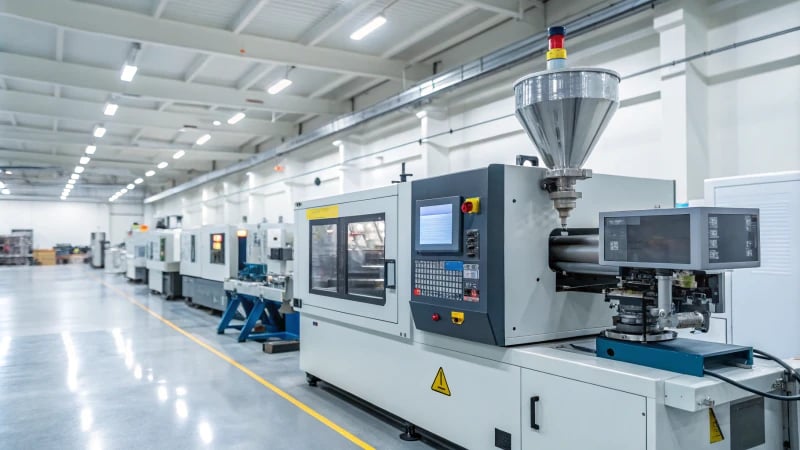
Improving Surface Quality
I remember starting work on creating top-notch plastic shells. A mentor once told me that slower injection speeds really helped reduce flow marks. Imagine reducing the speed from a swift 300mm/s to a steadier 100-150mm/s. Magic happened. The melt filled the cavity smoothly, leaving a clear surface without flow marks or silver streaks. Gases and moisture got the chance to escape, allowing the product to show its best side. Very clean.
Reducing injection speed is crucial for improving the appearance quality of molded products. A slower speed can help reduce flow marks, especially when producing high-surface-quality plastic shells.
Enhancing Internal Quality
While working on a thick product, I faced issues with internal stress. Fast speeds, like 250mm/s, caused warping after removing the mold. Frustrating. Reducing the speed to 120-180mm/s changed everything. The melt faced less shear force, which cut down residual stress a lot. This adjustment stabilized the product’s dimensions. It was amazing how effective this simple switch was.
Injection Speed | Effect on Stress | Product Type |
---|---|---|
Above 250mm/s | High Stress | Thick-walled |
120-180mm/s | Reduced Stress | Improved Stability |
Optimizing internal quality involves reducing internal stress and improving the product’s density and uniformity.
Preventing Material Decomposition
Handling sensitive materials like PVC demands care. A colleague stressed keeping speeds under 100mm/s to stop decomposition from shear heat. Fast speeds above 200mm/s could easily break PVC.
For heat-sensitive materials like PVC, a reduced injection speed prevents decomposition due to shear heat by keeping it below 100mm/s.
Furthermore, slower speeds allow natural crystallization in certain plastics, ensuring consistent mechanical properties by avoiding property fluctuations due to rapid molecular orientation changes.
Impact on Mechanical Properties
Slower injection speeds also really helped mechanical properties like strength and accuracy. Lowering speeds from 150mm/s to about 80-120mm/s improved melt compaction.
This led to better density and uniformity—very important for high-performance materials where this thoughtful approach produced items with impressive strength.
Changes in speed during plastic manufacturing8 optimized both quality and performance.
Reducing injection speed minimizes surface defects.True
Slower speeds allow gases and moisture to escape, reducing flow marks.
High injection speed improves dimensional stability.False
High speeds increase stress, causing warping and reducing stability.
Conclusion
Reducing injection mold speed enhances product quality by minimizing surface defects, improving internal stability, and preventing material degradation, leading to stronger and more aesthetically pleasing molded products.
-
Explore how different injection speeds impact the surface quality of molded products, providing practical insights for quality enhancement. ↩
-
Learn about optimization techniques in mold design to improve product quality and efficiency in manufacturing processes. ↩
-
Explore how varying injection speeds change shear forces during plastic molding, affecting internal stress levels. ↩
-
Learn about the crystallization process in plastics and its impact on maintaining consistent material properties. ↩
-
Explore how varying injection speeds influence the quality of molded products, impacting both surface finish and structural integrity. ↩
-
Discover techniques to prevent decomposition in materials like PVC by adjusting processing parameters such as speed. ↩
-
Find strategies to enhance product durability through process optimization, balancing speed with material integrity. ↩
-
This resource provides insights into various plastic manufacturing processes, enhancing understanding of how injection speed affects product quality. ↩