Join a journey through the complexities of injection molding. The process shines with proper injection pressure. The magic truly happens here.
The best pressure for injection molding depends on material characteristics, product structure and mold design. Pressure usually lies between 30 and 150 MPa. Factors like viscosity and flowability affect this pressure. Testing and adjusting during mold trials help find the right pressure. Practical tests really matter.
When I started learning about injection molding, I felt very amazed. A small change in pressure could really improve or ruin the final product. It is not just about numbers. It involves both art and science. People need to understand small details, like the thickness of the material or the complex design of the product. I remember a project with polycarbonate (PC). This material had high thickness and needed a lot of pressure, about 80 to 130 MPa, to fill every part of the mold properly.
The mold design matters a lot. The size and position of the gate really impact the pressure needed. I faced a tough problem with a product that had a complex inside part. I had to change the gate design to fill the product perfectly without any mistakes. These experiences showed me that finding the perfect injection pressure is not the same for every project. It needs a special approach. It often involves repeated trials and very precise changes.
Optimal injection pressure is always 100MPa.False
Optimal pressure varies with material and mold design, not fixed at 100MPa.
Empirical testing helps determine injection pressure.True
Testing during mold trials assists in optimizing injection pressure.
- 1. How Does Material Viscosity Affect Injection Pressure?
- 2. How Does Product Structure Influence Injection Pressure?
- 3. Why Is Mold Design Crucial in Injection Pressure Settings?
- 4. How Do I Optimize Pressure in Mold Trials?
- 5. What Are Common Mistakes When Setting Injection Pressure?
- 6. Conclusion
How Does Material Viscosity Affect Injection Pressure?
Have you ever thought about why some materials require more pressure in injection molding? Explore the interesting world of viscosity and injection pressure!
Material thickness matters a lot in choosing the injection pressure for molding. Thick materials need more pressure to fill molds than thin materials. High pressure guarantees molds fill properly and good products.
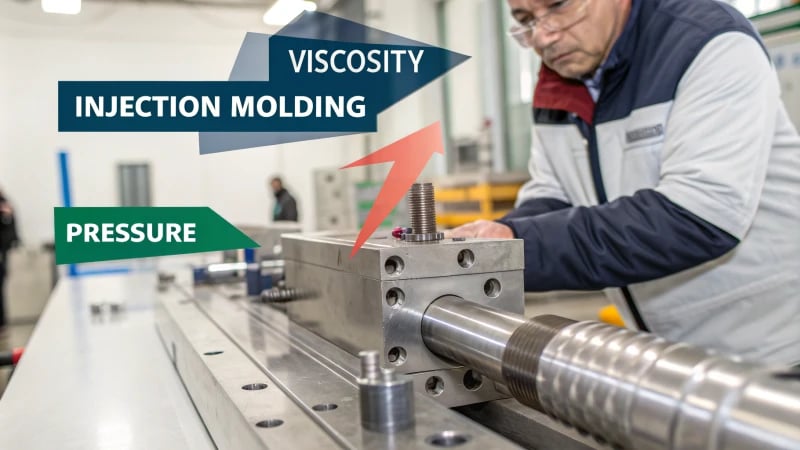
Understanding Material Viscosity
Viscosity plays a quiet yet crucial role in injection molding. I remember my first experience with polycarbonate. This material has high viscosity. It’s like pushing honey through a straw. Using high pressure is necessary to fill every part of the mold. In contrast, low-viscosity materials like polyethylene act like water. They slide in with little effort.
The Role of Flowability
Flowability offers an interesting perspective. Picture a party with two buffet lines. The slow line has people taking a long time choosing food. This resembles materials with poor flowability, needing more pressure to move. Meanwhile, polystyrene flows smoothly like a fast-moving line, even with less pressure.
Material | Viscosity | Injection Pressure (MPa) |
---|---|---|
Polycarbonate | High | 80-130 |
Polyethylene | Low | 30-80 |
Polystyrene | Moderate | 40-90 |
Analyzing Product Structure
Product design can be compared to planning a trip. Designing thick-walled items is like driving on a wide highway, moving steadily with minimal extra pressure. Thin-walled products resemble winding mountain roads, requiring more force (or pressure) to stay smooth.
Mold Design Considerations
Mold design involves gate size and position. A large gate resembles open concert doors, allowing easy entry with less pressure. Smaller gates act like few open doors, needing more force to prevent bottlenecks.
A good runner system1 works like a smooth path, lowering resistance and reducing needed pressure. Once, switching to a hot runner system helped decrease pressure by 20MPa, like discovering a shortcut for easier processing.
Mold Trial and Optimization
Adjusting the pressure right is truly an art. I start with educated guesses and refine based on trial results. It reminds me of cooking, where heat adjustments achieve the perfect simmer. Fine-tuning elements like injection speed and holding pressure brings out ideal products without surprises.
Understanding viscosity’s effect on injection pressure2 transformed my approach. It’s like a secret recipe for efficiently making top-quality products. This knowledge indeed benefits every designer, especially Jacky.
High-viscosity materials require higher injection pressures.True
Materials like polycarbonate need more pressure due to their resistance to flow.
Thicker-walled products require higher injection pressures.False
Thicker walls face less resistance, allowing lower pressure for molding.
How Does Product Structure Influence Injection Pressure?
Have you ever thought about why some products need various pressures when being made? Products often need this to achieve the right shape. During production, diverse pressures help create detailed designs. Some materials respond better to high pressure, while others need less force. Manufacturers use these techniques often. This method improves the final product’s quality.
Product structure is very important for setting the needed injection pressure in manufacturing. Wall thickness, complexity and gate design affect how material moves. This movement influences efficiency. It also impacts the final product’s quality.
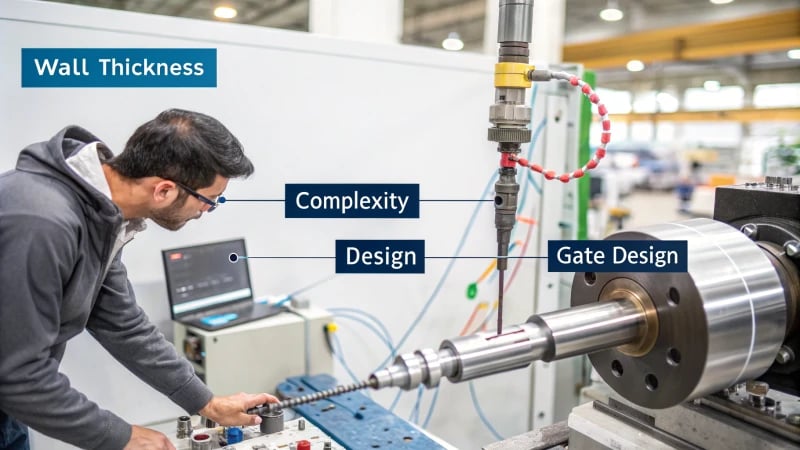
Exploring Material Properties
Viscosity and Flowability
At the beginning of my work with many materials, viscosity and flowability became more than theory. High-viscosity materials like polycarbonate3, with its thick nature, often required hefty force – around 80-130MPa – to fill molds. Conversely, low-viscosity materials like polyethylene behaved differently, moving easily with much lower pressures – about 30-80MPa.
Once, we used polystyrene because it flowed effortlessly into molds at 40-90MPa. But reinforced plastics were tough. I remember a time we pushed pressure up to 150MPa just for a good fill.
Understanding Product Structure
Wall Thickness
Wall thickness often surprises me. The thickness of product walls directly affects pressure requirements:
Wall Thickness | Pressure Range |
---|---|
Thicker walls | Less pressure needed |
Thinner walls | More force required |
Thicker walls are forgiving, using less pressure. Thinner ones need more force for complete filling.
Complexity
Intricate designs in electronic housings often challenge me. They usually need up to 150MPa to avoid annoying weld marks.
Mold Design Skills
Gate Size and Position
Gate size and position play crucial roles in mold design:
- Larger gates allow easier flow with lower pressure.
- Smaller gates require higher pressure.
- Gate placement is critical too; bad positions ruin the process.
The runner system greatly influences pressure needs. I experimented with different designs and saw how a smart design can really cut down on pressure compared to cold systems.
Improving Through Testing
Each project starts with setting initial pressures using data. It’s a back-and-forth process of adjusting and watching, often in 5-10MPa steps, until everything aligns perfectly without flaws.
Every change reveals new tricks for pressure optimization, simplifying future projects. Every successful tweak is a milestone in my pursuit of design and manufacturing mastery.
High-viscosity materials need higher injection pressures.True
Materials like polycarbonate require 80-130MPa to fill molds.
Thinner walls require lower injection pressures.False
Thin walls cool rapidly, needing 80-140MPa for full cavity filling.
Why Is Mold Design Crucial in Injection Pressure Settings?
Have you ever thought about how mold design might really help or destroy your injection molding work?
Mold design plays a vital role in deciding injection pressure settings. It affects how material moves and fills a mold. Knowing the design allows setting the right pressure. Complete cavity filling needs the correct pressure. This avoids defects and improves both efficiency and quality.
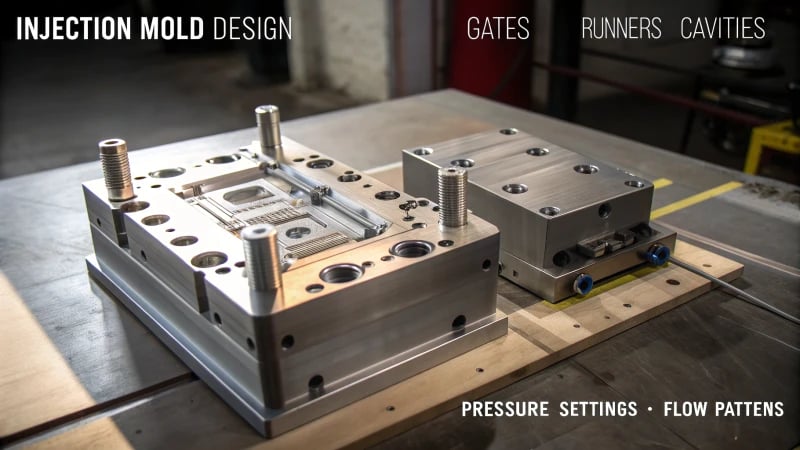
The Role of Material Properties
I remember when I first used polycarbonate – it felt like fighting a stubborn animal! This material has high resistance to flow, so you need to crank up the pressure, sometimes to 130 MPa, just to fill the mold. In contrast, polyethylene was easy to work with, needing much less pressure, around 30 to 80 MPa, because it flows more easily.
Mold design must consider material properties like viscosity4 and flowability to ensure efficient injection molding. Materials with higher viscosity require increased pressure to fill the mold cavity, while those with lower viscosity need less pressure.
Material Type | Viscosity | Pressure Range (MPa) |
---|---|---|
Polycarbonate (PC) | High | 80-130 |
Polyethylene (PE) | Low | 30-80 |
Product Structure Analysis
Studying the product structure is something I never skip. I once worked on a housing with a wall only 2mm thick. These thin walls cooled so quickly that I needed pressure close to 140 MPa to fill the form properly. In another project with 8mm thick walls, only about 70 MPa of pressure was enough.
Designers must analyze the product structure to set appropriate injection pressures. Wall thickness plays a crucial role: thicker walls reduce resistance and require less pressure, while thinner walls demand higher pressure due to rapid cooling and increased flow resistance.
Mold Design Factors
Gate size and position change everything. I once underestimated the effect of a small gate on a complex design, which taught me an important lesson about injection pressures. Now I pay close attention because even a well-placed gate saves much effort by giving an even fill.
Never ignore the runner system! The first time I used a rough runner system, it was like pushing syrup through a straw. It showed me that smooth, short runners reduce resistance and keep pressures low.
Gate size and position are fundamental in managing injection pressure. Larger gates reduce melt resistance, lowering necessary pressure, while smaller gates require higher pressure. Additionally, a well-positioned gate ensures even cavity fill.
The runner system’s design—its length, diameter, and surface roughness—also affects melt flow resistance.
Mold Trial and Optimization
At first, I was nervous during mold trials. I quickly saw that using basic formulas and adjusting 5 to 10 MPa at a time helped find the perfect settings. Fine-tuning not only really improved quality but also gave useful data for future tasks.
Initial injection pressure settings can be estimated using empirical formulas and adjusted during mold trials. Gradual adjustments (5-10 MPa increments) help achieve optimal settings where the cavity fills completely without defects.
Polycarbonate requires higher injection pressure than polyethylene.True
Polycarbonate has high viscosity, needing 80-130 MPa, while polyethylene needs 30-80 MPa.
Thicker walls in molds require higher injection pressures.False
Thicker walls reduce resistance, requiring less pressure compared to thinner walls.
How Do I Optimize Pressure in Mold Trials?
Adjusting the pressure in mold trials raises product quality from good to excellent. This process is critical. Here’s how I handle it.
To run mold tests well for pressure settings, I study how materials behave, look at the product’s shape and check the mold’s layout. I slowly change the settings and watch the results. This helps me adjust pressure for better product quality. Yes, better quality.
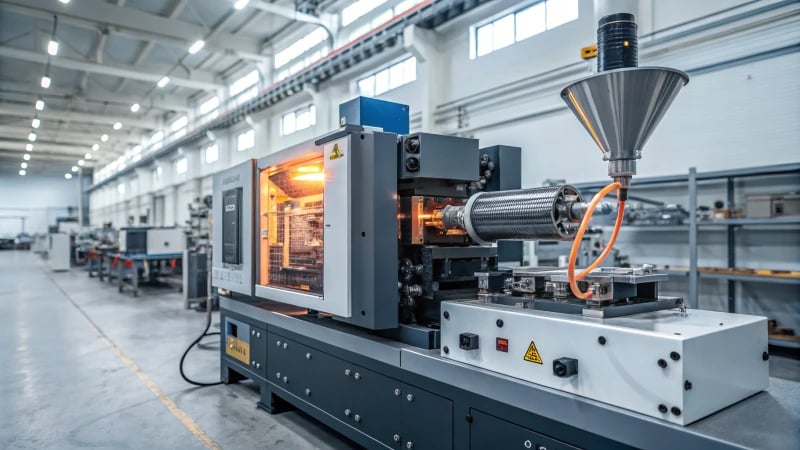
Understanding Material Properties
Studying mold trials, I have learned how important material qualities are, such as thickness and how well they spread. For example, thick materials like polycarbonate5 need higher injection pressures, maybe from 80 to 130 MPa. Easy-flow materials like polyethylene need only 30 to 80 MPa. Materials that spread well fill the spaces with lower pressure. Others often need more pressure for a good fill.
Analyzing Product Structure
Product design really changes pressure needs. Wall thickness plays a crucial part. Thicker walls offer less resistance, needing only 50 to 90 MPa for walls between 5-10mm. Thin walls under 3mm require more effort. Higher pressures of 80-140 MPa fight the resistance and prevent issues like not filling enough.
Evaluating Mold Design Factors
Mold design is crucial. Gate size and position and the runner system matter a lot. Big gates reduce resistance, while small gates need more pressure. A well-planned runner system6 can cut resistance significantly, especially with hot runner systems. These lower pressure needs by 10-30 MPa compared to cold systems.
Factor | Impact on Pressure |
---|---|
Gate Size | Larger gates reduce pressure |
Runner System | Hot runners lower pressure needs |
Conducting the Mold Trial
Starting with an initial pressure based on tested formulas is my usual approach. I gradually adjust by 5-10 MPa while closely watching product fill quality. The goal? Perfectly filled cavities without flaws like flow marks or bubbles. While adjusting speed and other settings, I log the best pressure range for each mold and product type to streamline future production.
This helps maintain consistent quality and improve efficiency in injection molding processes7.
High-viscosity materials require higher injection pressures.True
Materials like polycarbonate need 80-130MPa due to high viscosity.
Thin walls require lower injection pressures than thick walls.False
Thin walls need higher pressures (80-140MPa) due to increased resistance.
What Are Common Mistakes When Setting Injection Pressure?
Has a mistake ever stopped you in the workshop while looking at a flawed mold, pondering the error? Common blunders in setting injection pressure often cause such issues. Understanding these errors helps you steer clear of them.
Common mistakes in setting injection pressure involve ignoring material traits, overlooking product design details, forgetting mold design factors and skipping mold tests. Fixing these errors really leads to better injection molding results.
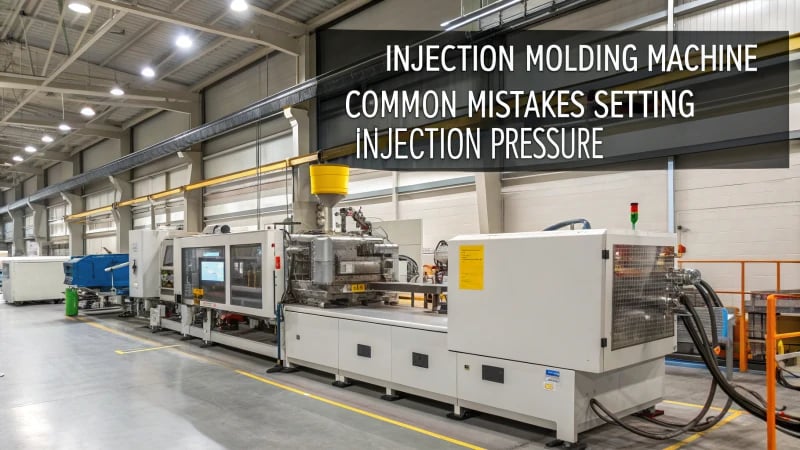
Not Considering Material Properties
Imagine making cookies without thinking about the dough. Materials in injection molding are similar. Each has unique traits. Polycarbonate, for instance, resembles thick batter. It needs more pressure, around 80 to 130 MPa, to flow well. Conversely, polyethylene flows like melted butter, needing much less pressure.
Understanding these properties can prevent filling issues due to variations in viscosity8 and flowability.
Forgetting Product Structure
Putting a puzzle together without all the pieces feels frustrating. This happens if I ignore product structure details in molding. Thicker products might not need as much pressure because less resistance occurs. The challenge lies with thin or complex designs. Thin walls or tricky corners, like in electronic housings, need precise pressure. Without it, defects like weld marks or incomplete fills appear.
Wall Thickness | Recommended Pressure Range (MPa) |
---|---|
>5mm | 50-90 |
<3mm | 80-140 |
Overlooking Mold Design Factors
Gate size and runner systems act as vital roles. A big gate size lets material flow freely, like opening floodgates. Smaller gates demand more pressure for smooth flow.
Similarly, an efficient hot runner system can decrease pressure by 10-30 MPa compared to a cold system.
Ignoring Mold Trials and Optimization
Producing without mold trials is like starting a trip without a map—it’s risky. I use data and conduct tests, adjusting settings slowly. Finding the sweet spot is essential for perfect fills, avoiding bubbles and flow marks.
Initial settings should be based on empirical data but fine-tuning during mold trials is crucial.
Extra Considerations
Documenting successful parameters is key for consistency; it’s like keeping recipes of good dishes—it helps replicate success consistently.
By avoiding these common mistakes, you ensure better product quality and process efficiency.
For further reading, think about these mold design tips9 that probably enhance your process.
High-viscosity materials need lower injection pressure.False
High-viscosity materials like polycarbonate require higher injection pressures.
Thicker walls require lower injection pressure.True
Thicker product walls generally need lower injection pressures to fill properly.
Conclusion
Optimal injection pressure in molding varies based on material viscosity, product structure, and mold design, typically ranging from 30 to 150 MPa, requiring empirical testing for precise adjustments.
-
Discover how different runner systems can influence injection pressure and overall mold efficiency. ↩
-
Explore how different viscosities affect injection pressure requirements for various materials. ↩
-
Learn about polycarbonate’s properties to understand why it requires higher injection pressures. ↩
-
Understanding material viscosity is crucial for setting the right injection pressures and avoiding defects. ↩
-
Understanding viscosity helps in determining appropriate injection pressures for different materials. ↩
-
A well-designed runner system can reduce resistance, optimizing pressure settings. ↩
-
Exploring best practices can lead to enhanced efficiency and product quality. ↩
-
Learn why understanding viscosity is essential for setting correct injection pressures and improving fill quality. ↩
-
Explore practical mold design strategies that optimize injection pressure settings and prevent common defects. ↩