Imagine the thrill of seeing your designs come to life in a seamless production line. Designing multi-cavity molds is your ticket to achieving that dream.
When designing multi-cavity molds, consider optimizing cavity layout, balancing material flow, implementing effective cooling strategies, and minimizing defects for efficient and high-quality large-scale manufacturing.
I remember my early days in mold design, grappling with the intricacies of cavity layouts and the relentless challenge of maintaining balance in material flow. Itโs not just about getting it right; itโs about making sure everything runs smoothly, without a hitch. In the following sections, Iโll delve into these essential aspects and share strategies that have proven invaluable over my years of experience. Whether youโre embarking on a new project or looking to refine your current designs, Iโm here to guide you with insights that have been honed through real-world application.
Optimizing cavity layout reduces production time.True
Proper cavity layout ensures efficient use of space, speeding up production.
Balanced material flow is not crucial for mold quality.False
Balanced flow prevents defects, ensuring consistent quality across cavities.
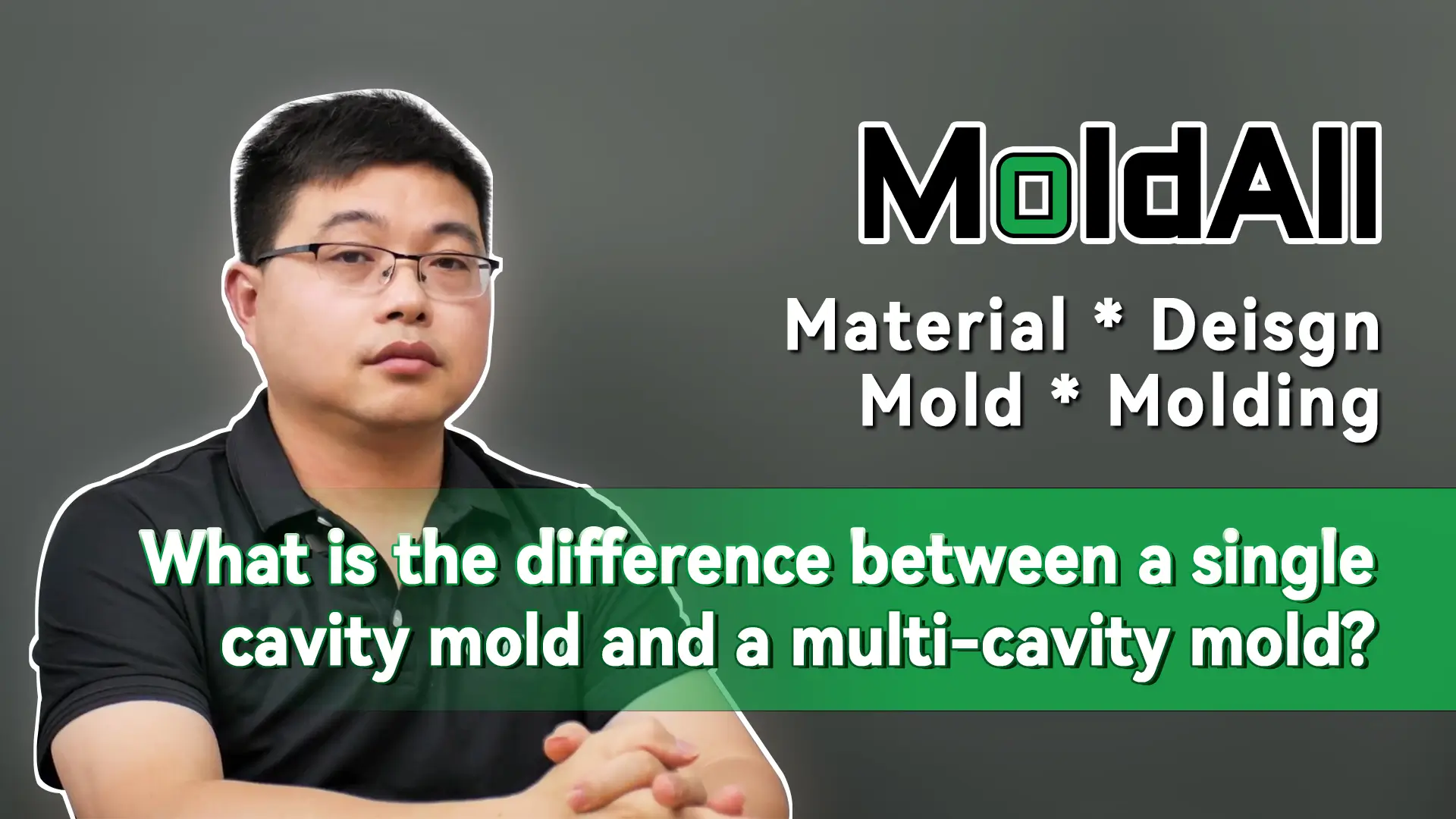
How Does Cavity Layout Affect Mold Performance?
Ever wondered how the layout of cavities in a mold can change everything from efficiency to quality in your injection molding projects?
Cavity layout significantly impacts mold performance, affecting material flow, cooling, and part quality. Optimal design ensures uniform fill rates and reduces defects, enhancing injection molding efficiency.
Understanding Cavity Layouts
I remember when I first started working with molds; I was amazed at how the tiniest adjustments in cavity layouts could make a huge difference. Itโs all about where those cavities sit within the mold. This arrangement affects material flow, cooling efficiency1, and how quickly we can churn out parts. When we nail the layout, everything runs smootherโfewer hiccups, better quality.
Material Flow Considerations
In my early days, I learned the hard way that uneven material flow can wreak havoc on part quality. I once had a project where parts kept coming out warped. After some digging, we realized it was all about how the gates were placed and the runners balanced. Making sure the material flows evenly is crucial.
- Gate Placement: Think of it like placing a faucet; you want that pressure just right.
- Runner System Design: Balancing these is like making sure all your garden hoses have equal pressure.
Cooling Efficiency
Cooling time can make or break your cycle times. During one of my projects, optimizing cooling channels was a game-changer. We cut down cooling times significantly, which not only boosted efficiency but also improved the final productโs stability.
Cavity Layout Type | Cooling Efficiency Impact |
---|---|
Symmetrical | Uniform cooling |
Asymmetrical | Potential hotspots |
Quality and Cost Implications
Iโve seen poorly designed layouts lead to defects like sink marks or weld linesโa nightmare for aesthetics and integrity. These hiccups can really drive up costs due to rework or wasted materials.
- Defect Reduction: An optimized layout acts as a preventative measure.
- Cost Efficiency: Shorter cycles mean less money spent.
Case Study: Multi-Cavity Molds
Multi-cavity molds were particularly challenging when I first encountered them. Ensuring each cavity had the same conditions was like a puzzle. But once we got it right using flow analysis tools2, it was like flipping a switchโeverything just clicked into place.
By really understanding these elements, I found that strategic decisions in cavity layout design could significantly enhance mold performance and product quality. Itโs those small tweaks and careful planning that make all the difference.
Symmetrical layouts ensure uniform cooling efficiency.True
Symmetrical cavity layouts provide even cooling, reducing hotspots.
Poor cavity layout increases production speed.False
Inefficient layouts cause defects, slowing down production due to rework.
How Does Material Flow Impact Multi-Cavity Molds?
When I first started working with multi-cavity molds, the concept of material flow seemed daunting. But mastering it can make all the difference in achieving top-notch product quality.
Proper material flow in multi-cavity molds ensures even distribution, crucial for maintaining quality and consistency, reducing defects, and boosting production efficiency.
Understanding Material Flow Dynamics
When I think back to my early days in mold design, I remember the challenge of managing material flow. It was like trying to conduct a symphonyโeach cavity had to be filled evenly to avoid any discord in the final product. In a multi-cavity mold, material flow affects how each cavity is filled, and uneven flow can lead to variations in product dimensions and properties.
Managing material viscosity3 is crucial, as different flow rates can result in fluctuating pressures and temperatures across cavities. I learned that controlling these variables is key to achieving consistent results.
Factors Influencing Material Flow
Several factors influence material flow:
Factor | Description |
---|---|
Temperature | Affects viscosity; higher temperatures lower viscosity, enabling easier flow. |
Pressure | Influences how far and fast the material flows into cavities. |
Mold Design | Cavity layout and runner systems can impact flow uniformity. |
I often remind myself and my team that considering these factors during the design phase can significantly optimize mold performance.
Challenges in Multi-Cavity Molds
One major challenge is balancing flow across all cavities. I remember a time when unequal flow led to defects like short shots or flash, which was quite frustrating.
Implementing flow simulation software4 has been a game-changer for me, predicting potential issues and allowing for adjustments before manufacturing begins.
Optimizing Material Flow
Optimizing material flow involves:
- Adjusting gate locations to ensure balanced filling.
- Employing advanced materials that offer consistent flow characteristics.
- Utilizing cooling channels5 efficiently to maintain uniform temperature across the mold.
These strategies have helped me achieve high-quality outputs while minimizing waste and cycle times. Balancing these elements requires precision and a deep understanding of the material properties involved. Itโs like fine-tuning an instrument; once you get it right, everything harmonizes perfectly.
Uneven flow in multi-cavity molds causes product defects.True
Uneven flow leads to inconsistencies like short shots or flash.
Higher temperature increases material viscosity in molds.False
Higher temperatures lower viscosity, facilitating easier flow.
How Can I Minimize Defects in Multi-Cavity Mold Designs?
Ever found yourself scratching your head over those pesky defects in multi-cavity mold designs?
To minimize defects in multi-cavity mold designs, optimize the cavity layout, maintain consistent wall thickness, control temperature precisely, and perform regular maintenance to enhance product consistency and address common issues.
Importance of Cavity Layout
Ah, the art of planning a cavity layout. I remember my first project where everything seemed perfect on paper, yet the reality was an array of warped pieces. Aligning cavities symmetrically is like arranging a puzzle; it keeps material flow smooth, balancing pressure and temperature across all parts. Think of it as ensuring everyone gets a fair slice of the pie.
- Symmetry: This is key for even distribution, like making sure everyone in line at a buffet gets equal servings.
- Spacing: Just like social distancing, proper spacing reduces unwanted heat concentration.
Material Selection and Wall Thickness
Choosing the right material feels like picking the right running shoesโcritical for performance. Iโve learned that materials with good flow characteristics and optimize wall thickness6 can be a game changer. This helps avoid those nasty sink marks and voids that pop up when least expected.
Material Type | Flow Characteristic | Common Issues Reduced |
---|---|---|
Polypropylene | High | Warping, Shrinkage |
ABS | Medium | Surface Finish Defects |
Polycarbonate | Low | Internal Voids |
Temperature Control
I once underestimated the power of temperature control, and it taught me a lesson I wonโt forget. Using sensors to keep an eye on temperature helps maintain uniformityโan essential step to sidestep uneven cooling issues. This prevents common issues7 like uneven cooling.
Maintenance and Inspection
Regular check-ups arenโt just for carsโtheyโre vital for molds too. Imagine discovering a small abrasion too late. Regular inspections can save you from unexpected surprises. A solid schedule for maintenance ensures everything stays in top shape.
- Wear and Tear: Keep an eye out for any abrasions or deformities.
- Cleaning: Just like keeping a workspace tidy, cleaning prevents contamination that could hinder performance.
Process Parameters Optimization
Tuning injection speed, pressure, and cooling time feels like fine-tuning a musical instrument. Each tweak brings you closer to defect-free production. Tailor these adjustments to fit the specific material and design needs to achieve optimal results.
Use of Simulation Software
Imagine foreseeing potential defects before even starting productionโlike having a crystal ball. Simulation tools are your best friends here, allowing you to make adjustments early on, boosting product quality8.
Symmetrical cavity layout reduces warping.True
Symmetry in cavity layout ensures even material distribution, reducing warping.
Polycarbonate has high flow characteristics.False
Polycarbonate has low flow characteristics, leading to internal voids.
How Can You Ensure Consistent Production Quality?
Ever wondered how some manufacturers consistently nail their production quality while others struggle? Let me share a few strategies that have been game-changers in my experience.
Ensure consistent production quality through regular equipment maintenance, strict SOP adherence, ongoing employee training, and effective quality control, reducing defects and boosting efficiency.
Equipment Maintenance: The Backbone of Quality
I remember my first big project where a minor equipment glitch caused a major setback. That taught me the hard way that regular equipment maintenance9 is not just importantโitโs vital. Scheduling check-ups and updates keeps everything running smoothly and prevents those unexpected downtimes that can throw your whole schedule off.
- Routine Checks: I make it a point to implement daily checks, which helps catch issues like wear and tear before they escalate.
- Calibration: Regularly calibrating tools ensures accuracy, which is key to maintaining consistency.
Standard Operating Procedures (SOPs)
Creating Standard Operating Procedures felt like a chore at first, but now I see them as a structured approach10 that saves time and energy. They provide clear instructions so everyone on the team knows exactly what to do, reducing variability and confusion.
Benefit | Description |
---|---|
Clarity | Clear guidelines for processes. |
Consistency | Uniformity across production. |
Continuous Employee Training
Keeping up with the latest techniques through training programs11 has been crucial for me and my team. Regular training sessions ensure we stay on top of our game, improving our skills and efficiency.
- Workshops: We conduct monthly workshops to stay updated on new methods.
- Certifications: I always encourage my team to obtain relevant industry certifications to boost their credentials and confidence.
Quality Control Tools
Incorporating advanced quality control tools12 like statistical process control and Six Sigma has been transformative. These tools offer invaluable insights into our production processes, allowing us to intervene before issues arise.
- Statistical Process Control: This helps us monitor production trends effectively.
- Six Sigma: It focuses on reducing variation, which is crucial for maintaining consistency.
By implementing these strategies, Iโve seen firsthand how manufacturers can build a robust framework for consistent production quality, meeting both internal standards and customer expectations with ease.
Routine equipment checks prevent unexpected downtimes.True
Regular checks identify wear and tear early, ensuring peak performance.
SOPs increase variability in production processes.False
SOPs reduce variability by providing clear, consistent instructions.
How Do Different Materials Influence Mold Design Choices?
Ever wondered how the material you choose can totally change the game in mold design? Itโs fascinating! Let me walk you through it.
Materials impact mold design by influencing cooling rates, viscosity, and shrinkage, thereby shaping the moldโs geometry, cooling layout, and surface finish to ensure excellent product quality.
Impact on Cooling Rates
I remember the first time I realized how much thermal conductivity could affect cooling rates. It was during a project with aluminum, which cools much faster than most plastics. This meant I had to rethink the cooling channel designs13 to prevent warping. On the other hand, when dealing with materials that had lower thermal conductivity, I learned the importance of extending cooling cycles to ensure the product quality wasnโt compromised.
Viscosity Considerations
Viscosity is another intriguing aspect. Picture this: working with high-viscosity thermoplastics felt like trying to squeeze honey through a straw. It became clear that molds required larger gates and runners to accommodate the material flow. Conversely, low-viscosity materials like liquid silicone rubber allowed us to play with more intricate designs, akin to painting with a fine brush. Hereโs a quick snapshot:
Material Type | Typical Viscosity | Design Implication |
---|---|---|
Thermoplastics | High | Larger gates |
Liquid Silicone Rubber | Low | Smaller gates |
Shrinkage Factors
One lesson I learned the hard way was about shrinkage. Crystalline polymers, for instance, shrink significantly more than amorphous ones. This meant having to constantly adjust my calculations to avoid unwanted surprises in the final dimensions. Imagine designing a sleek phone case only for it to end up slightly too snug or looseโitโs all about getting those compensatory measures14 right.
Surface Finish and Texture
A materialโs ability to achieve a smooth surface finish can make or break the final aesthetic of a product. Metals generally offer smoother finishes compared to some plastics, which I often have to remind myself when designing products that need a high-end look. Understanding these texturing capabilities15 has become second nature.
Environmental Impact and Sustainability
Nowadays, sustainability canโt be ignored. While biodegradable materials are great for reducing environmental impact, they bring their own set of challenges in mold design. Figuring out how to balance eco-friendly materials with design functionality is an ongoing journey. Itโs about embracing these environmental implications16 and finding innovative solutions.
Aluminum molds require less cooling time than plastic ones.True
Aluminum's high thermal conductivity leads to faster cooling than plastics.
High-viscosity materials need smaller gates in mold design.False
High-viscosity materials require larger gates for effective mold filling.
Conclusion
Designing multi-cavity molds requires optimizing cavity layout, material flow, cooling efficiency, and defect reduction to enhance production quality and efficiency in large-scale manufacturing.
-
Learn how different cavity layouts impact cooling efficiency, influencing cycle times and part quality.ย โฉ
-
Explore effective strategies using flow analysis tools to optimize cavity layouts for improved mold performance.ย โฉ
-
Understanding material viscosity helps optimize injection molding by controlling flow rates and ensuring uniform part quality.ย โฉ
-
Flow simulation software identifies potential defects in mold design, helping designers make necessary adjustments pre-production.ย โฉ
-
Cooling channels maintain uniform temperatures, reducing cycle times and ensuring consistent part quality.ย โฉ
-
Understanding wall thickness optimization helps improve part quality by ensuring even material distribution and cooling.ย โฉ
-
Temperature control is vital for consistent part quality and defect prevention in injection molding.ย โฉ
-
Simulation software allows early detection of potential design flaws, saving time and resources.ย โฉ
-
Discover why regular maintenance is critical to sustaining machinery efficiency and preventing defects.ย โฉ
-
Learn how SOPs standardize processes, ensuring consistency across production lines.ย โฉ
-
Explore the significance of continuous employee training in maintaining high-quality production.ย โฉ
-
Find out how advanced tools enhance quality control, reducing defects and increasing efficiency.ย โฉ
-
Discover best practices for designing efficient cooling channels in aluminum molds to optimize production speed and product quality.ย โฉ
-
Learn techniques to effectively compensate for material shrinkage in mold design, ensuring precise final product dimensions.ย โฉ
-
Explore methods to achieve superior surface finishes in injection-molded products, enhancing aesthetic appeal and functionality.ย โฉ
-
Understand the environmental benefits and challenges of using biodegradable materials in molding processes.ย โฉ