Do you ever feel caught between desiring creativity and requiring efficiency in mold design? You’re not alone.
Mixing standard mold design with custom pieces starts with looking at what people want in a product. Discover specific personalized needs. Develop a smart plan. Use software for parametric design. This probably helps in smooth production. It satisfies both unique looks and special functions.
Balancing common designs with custom elements in molds feels like walking on a tightrope. I spent many nights trying to keep things easy and simple without losing the special touch that makes a product stand out. Let me share some ideas that worked wonders for me.
Picture the excitement at the product demand analysis stage. Here, you uncover special needs, acting like a detective finding clues about textures and fitting with standard designs. Think of creating a design plan as more art than work.
Then comes the exciting part꞉ mixing standard parts with custom details. It’s like assembling a puzzle where each piece must fit perfectly, like creating unique cooling channels for different shapes. The magic happens when using design software to adjust templates to match your vision closely.
Finally, mixing common and custom methods in making products feels like leading a beautiful orchestra. Every part plays its role, matching speed with the special demands of the project. A lovely mix of innovation and skill. Every product is crafted carefully.
Personalized needs are crucial in mold design.True
Identifying personalized needs ensures the mold design meets specific product requirements.
Standard components can't be combined with personalized ones.False
Combining standard and personalized components enhances mold design flexibility.
- 1. What is the Product Demand Analysis Stage?
- 2. How Can You Develop a Design Strategy for Mold Standardization?
- 3. Why is Combination Design Essential in the Process?
- 4. How Does Parametric Design Software Transform My Work?
- 5. How Can I Balance Customized and Standard Processing in Manufacturing?
- 6. Conclusion
What is the Product Demand Analysis Stage?
Have you ever thought about how to find the right product for what people want and need?
The product demand analysis stage focuses on understanding what the market truly wants. Analysis looks at both individual and common needs. Design strategies balance unique features with efficient mass production.
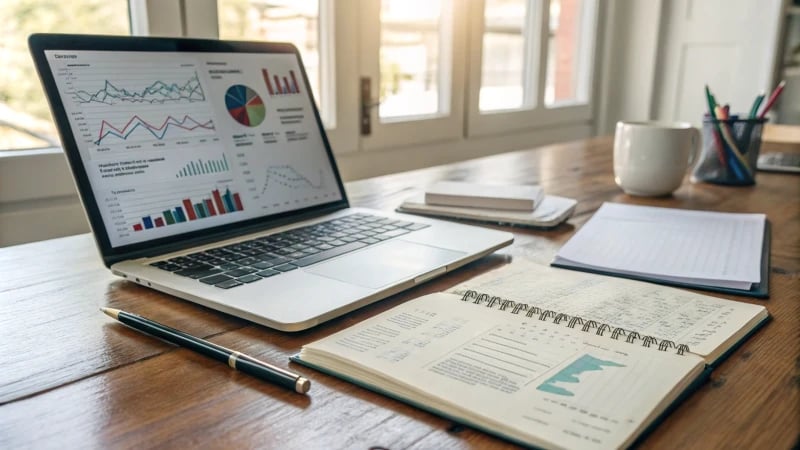
Understanding Personalized Needs
In design, understanding what people need can feel very difficult. Yet, it is very important. I once worked on a car part where the client asked for a specific texture. We carefully planned the look, depth, and pattern they wanted. Other parts still matched standard designs, like mold size or common connections. Balancing these needs felt challenging but very fulfilling when successful.
Developing a Design Strategy
Once I know what makes a product special and what fits industry norms, it’s time to plan a design strategy. The look might be unique, but the shape follows common rules. I might use a regular mold base and focus on making the surface stand out with creativity.
Design Strategy | Personalization | Standardization |
---|---|---|
Appearance Focus | Yes | No |
Internal Structure | No | Yes |
Component Combination in Design
Mixing standard and unique parts is like solving a puzzle. For example, mold cooling systems start with standard designs but often need changes for special shapes. This task combines creativity and precise engineering, which I really enjoy.
- Cooling Channels: Regular sizes with custom additions.
- Demolding Mechanism: Usual rods with special devices for removal.
Using Parametric Design Software
Parametric design software helps a lot. Changing settings in a normal structure lets me meet specific needs, like moving gates or altering mold layouts. This tool is crucial for creating molds matching both usual and special requirements. See more about parametric design1 applications.
Manufacturing Process Collaboration
Working together is essential in manufacturing. I have noticed that merging custom methods for complex parts with standard techniques for large quantities increases efficiency. Each technique, like EDM or five-axis machining, plays a vital role in crafting excellent products.
Quality Control Differentiation
Quality checking here involves telling apart standard from unique components. Common parts follow known rules while personalized parts meet special needs, always keeping strength and performance intact.
Understanding what the market demands is key to balancing custom features with productive methods. It’s about seeing the simple things while focusing on the details that make each product unique.
Personalized mold parts simplify maintenance.True
Personalized design parts are structured for easy disassembly and replacement.
Standardized mold frames hinder design updates.False
Standardized frames facilitate updates by reducing redesign workload.
How Can You Develop a Design Strategy for Mold Standardization?
Have you ever felt stressed about simplifying processes while keeping your designs unique?
Create a plan for mold standardization by looking at what the product needs. Find where standardization is possible. Mix common and unique parts well. Use parametric software. Merge custom methods with standard ones.
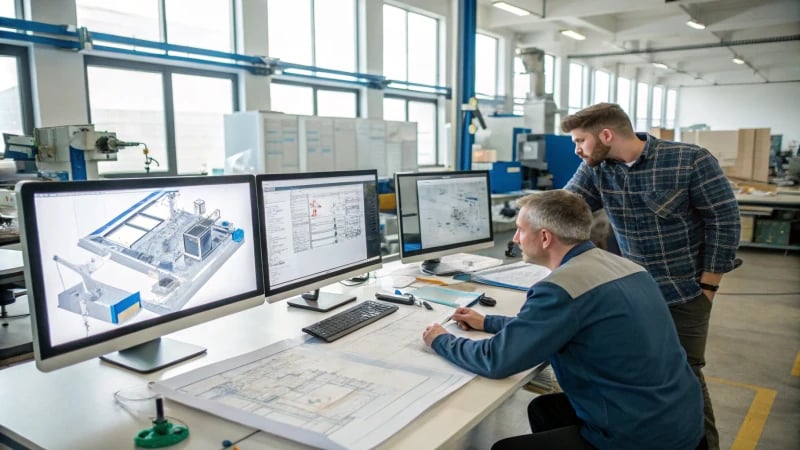
Product Demand Analysis Stage
I remember designing an injection mold for a car’s inside parts. The surface needed the perfect feel – not too rough, not too smooth. It had to be even everywhere. This task felt large and complex. A careful look at specific needs, like texture, was important. Yet, finding parts that fit standard sizes and shapes was equally vital. This starting analysis helps create a good plan. It mixes special touches with the simplicity of common parts.
Combination in the Design Process
Mixing common and special parts feels like making a great dish. I worked on a cooling system once. We had standard main paths but changed small routes to fit special cooling tasks. Adjusting design software at that time felt really amazing. It let us change simple mold shapes to meet exact needs, like where spaces and entry points were placed.
Component | Standardized Part Example | Personalized Part Example |
---|---|---|
Cooling System | Standard channel layout | Custom branches for specific needs |
Demolding Mechanism | Standard push rod structure | Auxiliary devices for unique shapes |
Manufacturing and Processing Links
Collaborating on custom and regular processing was like piecing together a tricky puzzle. For standard parts, producing in large amounts helped save time and cut costs. For unique things like detailed cores, special methods like precision machining were necessary. This gave the exact forms needed for complex builds.
Later Maintenance and Update
Thinking about upkeep while designing saves a lot of hassle later, especially for custom parts. I learned to keep detailed notes on maintenance spots. This made taking apart and changing parts much simpler. When improvements were needed, using current standard designs lessened workload while leaving room for new ideas based on changing needs.
By integrating these elements into your design strategy, you can achieve an effective balance between customization and standardization in mold design.
Personalized needs are key in mold design.True
Analyzing personalized needs is crucial for initial mold design stages.
Standard components can't be personalized.False
Standard components can be modified to meet personalized design needs.
Why is Combination Design Essential in the Process?
Picture a world where every item seems crafted specifically for you. This is the charm of combination design.
Combination design plays a crucial role. It mixes standard and custom parts. This mix improves efficiency, personal touch and fresh ideas in product creation. Adaptability rises and making becomes smoother. Unique customer needs often receive attention.
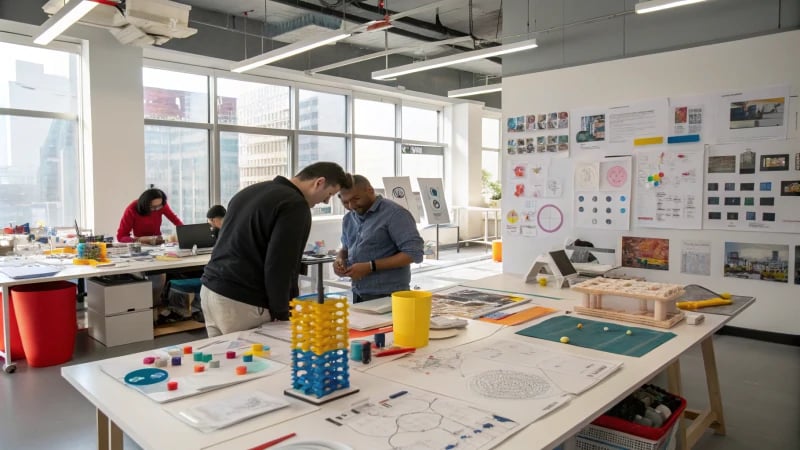
Understanding Combination Design
When I began working in product design, balance was everything. I searched for the sweet spot between usual and personalized parts to create something special. Combination design captures this balance well. Designers blend common parts with tailored touches to craft products that fit specific needs and are efficient to produce.
Importance in Product Demand Analysis
Understanding what people truly want is crucial during the product demand analysis stage. I once focused on car interiors where even small texture changes were important. By identifying these distinct needs and mixing them with usual components, we reached both precision and efficiency2.
Standard Components | Personalized Elements |
---|---|
Basic size range | Texture accuracy |
Universal interfaces | Depth and distribution |
Role in the Design Process
Combination design plays a key role throughout the design process. With parametric design software, a designer has everything needed for any task. I often adapted standard mold frameworks to add special features that clients desired. This method results in designs that save money and fit perfectly.
- Example: A standard cooling channel adjusts based on different product shapes.
Manufacturing and Processing Links
In manufacturing, this idea helps custom and usual processing work well together. Mass production reduces costs for common parts, while new tech like five-axis machining3 makes sure personalized pieces meet exact specifications.
Maintenance and Updates
Combination design simplifies future maintenance. Customized parts easily swap, allowing smooth updates without touching standard elements. This planning eases my work and likely yours when innovating new product versions.
- Consideration: Maintenance guides should explain how to remove custom parts without disturbing standard ones.
This approach lets designers create products that satisfy functional needs and appeal to consumers’ tastes. The goal is to offer solutions that feel personal and are cleverly designed for large-scale production.
Personalized needs are crucial in mold design.True
Understanding personalized needs ensures the product's aesthetic and functional success.
Standard components eliminate the need for customization.False
Standard components are combined with personalized parts to meet unique requirements.
How Does Parametric Design Software Transform My Work?
Imagine trying to put a square block into a round hole. Designing without parametric software feels like this. It might be very challenging.
Parametric design software allows changes to designs easily with just a few clicks. This is perfect for fast adjustments and adding personal details. Flexibility is very important in architecture and engineering. Precision is also crucial. Adaptability and precision are both crucial in these fields.
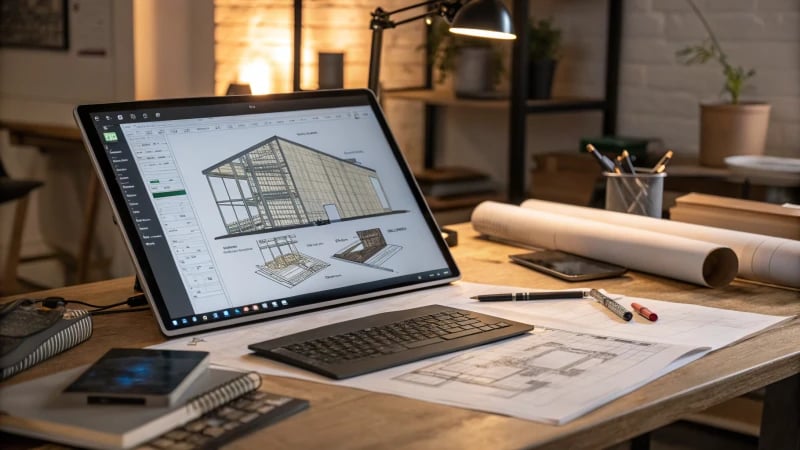
Understanding the Basics
When I tried parametric design software for the first time, it felt like entering a new world. My ideas came to life by simply changing a few numbers. This software uses math rules to form shapes based on size or angle input. Imagine altering a model by moving a slider. It changes hard tasks into easy work, saving time and creating an efficient workflow4.
Better Customization
In the product demand analysis stage, parametric design becomes very useful. I worked on car interiors and needed to customize textures carefully. Instead of beginning all over again, I adjusted the texture depth and spread. Unique designs emerged easily.
Feature | Traditional Design | Parametric Design |
---|---|---|
Time Efficiency | Time-consuming | Rapid adjustments |
Customization Level | Limited | Highly customizable |
Error Probability | Higher risk | Reduced through automation |
This accuracy is very valuable because it does not need many manual changes.
Fitting into the Design Process
Combining regular parts with custom elements is one thing I really like in mold design. Standard cooling channels mix effortlessly with special branches for specific cooling tasks. It’s like a recipe where you change ingredients for better taste, ensuring both standard efficiency and personalized requirements are met.
Parametric templates for mold frames helped save time and resources. I focused only on customizing what was needed, optimizing both time and resources.
Advances in Manufacturing
In manufacturing, this software connects personal processing with usual production. By generating precise molds for complex shapes, it enhances quality control by ensuring that personalized parts fit product needs while maintaining their strength—like a safety net catching mistakes before they arise.
Regular Maintenance and Updates
Maintenance is easier when designs adapt by changing a few numbers instead of starting over. This saves creativity and keeps efficiency intact, much like updating an old recipe with new tastes while keeping the main flavor.
Those interested in more can explore real-life case studies5 to see how parametric design tools change what is possible.
Parametric design enhances mold design efficiency.True
Parametric design allows for quick adjustments, improving design efficiency.
Standardized parts require more maintenance than personalized ones.False
Standardized parts generally require less maintenance due to uniformity.
How Can I Balance Customized and Standard Processing in Manufacturing?
Finding the right mix between personal touches and uniform methods in manufacturing goes beyond efficiency. It involves producing items that truly connect with buyers. Operations stay smooth and costs remain low.
Analyze product demand to balance customized and standard processing. Integrate design strategies to support this balance. Manufacturing processes require synchronization. Plan maintenance carefully. This method achieves efficiency. Cost savings follow this approach. The ability to meet unique customer needs probably results.
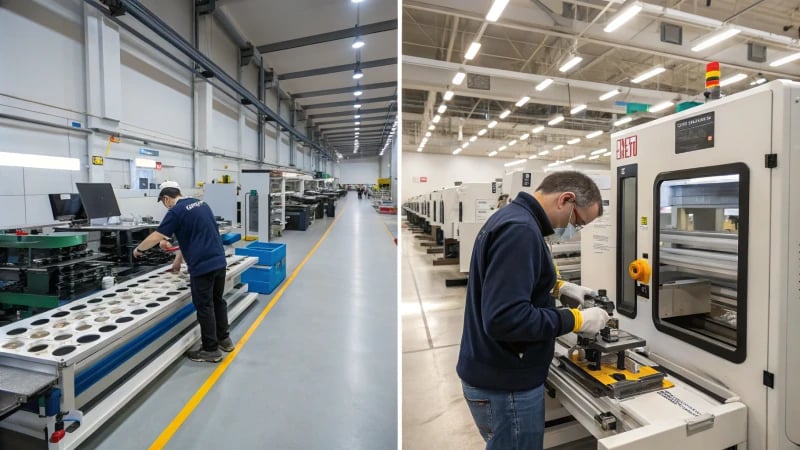
Product Demand Analysis Stage
My early work with mold designs for car parts was like solving a puzzle. Each piece needed a special surface, but it also had to fit into a standard form. Accurately finding out specific needs in the product demand analysis stage is very important. Imagine creating a car’s interior with just the right texture while keeping the design consistent across all models. This is about balancing texture accuracy with universal design elements like the installation interface6. Developing a strategy from these insights helps focus on customizing exactly where it’s necessary. It really helps.
Combination in the Design Process
Combining standard and custom parts in design feels like painting inside a frame but with freedom to be creative. I use special software to adjust settings within a standard mold to get those custom touches. Picture this: a regular cooling system layout designed with special branches for unique needs. It is like having a strong base and adding personal style.
Component Type | Standard Design | Personalized Design |
---|---|---|
Cooling System | Standard Layout | Custom Branches |
Demolding Mechanism | Push Rods/Plates | Auxiliary Devices |
Manufacturing and Processing Links
In manufacturing, coordinating between custom and standard methods is essential. Think of it as a dance where commonly made parts and special techniques for unique pieces meet. For example, when creating parts with complicated shapes, I use EDM or five-axis machining for precision complex shapes7. Quality control must tell the difference between these parts, making sure each one meets its standards.
Later Maintenance and Update Considerations
Planning for future maintenance is setting a strong safety net. Designing custom parts to be easily taken apart and replaced is very important. When updates happen, using standard parts cuts down on redesign work, letting new ideas shine in custom areas efficiently8. This way, the process stays efficient and matches with updated product specifications.
Customization is not essential in mold design.False
Customization is crucial in mold design to meet unique texture requirements.
Standard parts simplify long-term maintenance.True
Standard components ease maintenance and updates by minimizing redesign efforts.
Conclusion
Integrating mold design standardization with personalization enhances efficiency and creativity, balancing unique product features with mass production needs through strategic analysis and parametric design software.
-
Learn how parametric design software can optimize customization within a standard framework. ↩
-
Understanding efficiency’s role in design helps balance customization with streamlined processes. ↩
-
Learning about five-axis machining offers insights into precision crafting of complex shapes. ↩
-
Understand how parametric design improves efficiency and customization in various industries. ↩
-
Discover how parametric design is applied in different sectors for innovative solutions. ↩
-
Exploring this link will provide insights on aligning customization with existing standards to improve efficiency. ↩
-
Understanding advanced machining can enhance precision in creating complex customized parts. ↩
-
Discover strategies that streamline maintenance of customized components within standard systems. ↩