Ever wondered how the plastic spoon you use daily is made?
An injection molding machine produces plastic spoons by melting plastic pellets and injecting the molten plastic into a spoon-shaped mold cavity under high pressure. This method allows for high precision, efficiency, and the use of various plastic materials like polypropylene.
I remember the first time I held a freshly minted plastic spoon, straight from the mold. It was astonishing how something so common started as tiny pellets. The process is truly fascinating—imagine melting down those pellets until they’re a gooey liquid and then pressing them into a mold shaped like a spoon. It’s like magic, but with a touch of engineering genius! This method doesn’t just make one spoon; it churns out hundreds, each identical to the last, thanks to its remarkable precision and efficiency.
Choosing the right material is crucial too. I’ve often opted for polypropylene, given its durability and food-safe properties. It’s amazing how these choices affect not just the final product’s look but its usability. Each time a spoon comes out perfectly smooth with all its details intact, it feels like a small triumph in precision crafting. Seeing the transformation from raw materials to a neat stack of plastic spoons ready for use is incredibly rewarding. It’s not just about making spoons; it’s about perfecting a process that combines creativity with technical prowess.
Injection molding uses plastic pellets for spoon production.True
Plastic pellets are melted and injected into molds to form spoons.
Polypropylene is unsuitable for making plastic spoons.False
Polypropylene is commonly used due to its durability and safety.

Why is Injection Molding Perfect for Making Spoons?
Imagine the thrill of creating thousands of perfectly shaped spoons with just the press of a button. Injection molding makes this a reality, combining speed and precision like no other.
Injection molding is perfect for spoon production because it ensures high precision and efficiency while offering compatibility with various materials, allowing for consistent and durable plastic spoons.
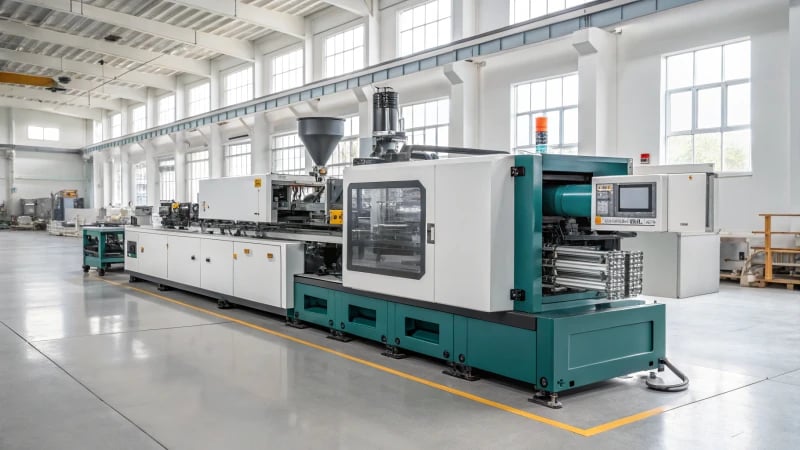
Process Suitability
Injection molding is highly suited for spoon production as it involves melting plastic pellets and injecting them into a mold cavity under high pressure. This ensures each spoon has a consistent shape, including detailed elements like the bowl and handle. The process guarantees that every spoon produced meets exact design specifications without deviation.
Material Compatibility
A major advantage of injection molding is its compatibility with various plastic materials. Polypropylene (PP) is often preferred for spoons due to its durability and food-safe properties. However, alternatives such as polystyrene or acrylonitrile-butadiene-styrene1 can be used when specific characteristics like transparency are desired.
Material | Key Properties |
---|---|
Polypropylene (PP) | Durable, heat-resistant |
Polystyrene (PS) | Cost-effective, clear |
ABS | Strong, impact-resistant |
Production Efficiency and Precision
There’s something immensely satisfying about watching an injection molding machine in action. It’s not just the speed—though producing thousands of spoons in a short timeframe is impressive—but the precision. Each spoon emerges with smooth surfaces and accurate details that are crucial for usability and aesthetic appeal. This consistency reassures me that every single spoon is up to standard, ready to meet the high demands of the market.
Advantages Over Other Techniques
Unlike other manufacturing methods, injection molding provides unique benefits in terms of speed and quality. The ability to quickly switch between different spoon designs by changing molds makes it particularly versatile2. This flexibility ensures manufacturers can adapt to market trends rapidly without significant downtime.
In essence, injection molding isn’t just about making spoons; it’s about mastering a craft that marries rapid production with unwavering quality, making it indispensable in today’s fast-paced utensil industry.
Injection molding ensures consistent spoon shapes.True
The process uses high pressure to mold plastic into precise, uniform shapes.
Polystyrene is the most durable material for spoons.False
Polypropylene is more durable and heat-resistant than polystyrene.
Which Plastic Materials Are Best for Making Spoons?
Ever wondered which plastic makes the best spoons? I have too, and here’s what I’ve learned on this journey of discovery.
The top plastics for crafting spoons are polypropylene (PP) for heat resistance, polystyrene (PS) for cost-effectiveness, and acrylonitrile butadiene styrene (ABS) for durability.
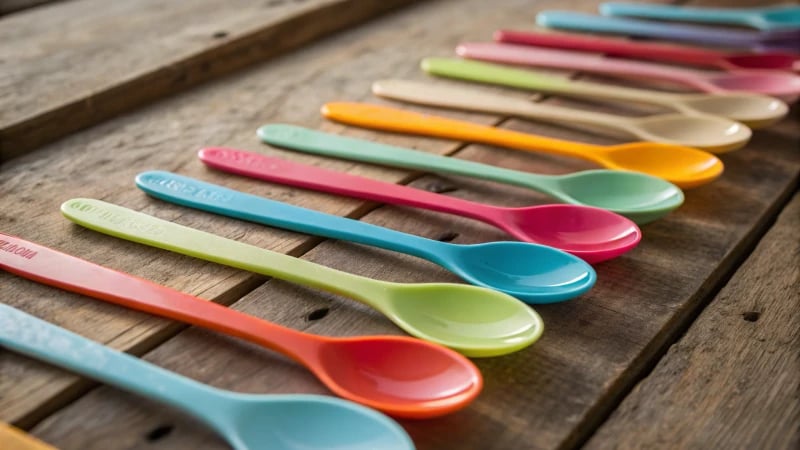
Understanding Different Plastics for Spoon Manufacturing
When I first dipped my toes into the world of manufacturing spoons3, it was like being handed a mystery novel full of different characters, each with their unique traits. Here’s a quick rundown of the key players:
Material | Properties |
---|---|
Polypropylene | Durable, heat-resistant, food-safe |
Polystyrene | Affordable, easy to mold, rigid |
ABS | Impact-resistant, strong, aesthetic finish |
Why Polypropylene Stands Out
Polypropylene (PP) truly shines in this ensemble. It’s like the reliable friend who can handle the heat — literally! Perfect for hot foods, PP’s durability means fewer spoons tossed into the trash, making it a green warrior in disguise.
The Role of Polystyrene in Spoon Production
Think of Polystyrene (PS) as the budget-friendly option that doesn’t skimp on style. It’s great for disposable spoons, which are rigid and sometimes even transparent, making them ideal for those chic dinner parties where you want to impress without breaking the bank.
ABS: The Durable Alternative
Then there’s Acrylonitrile butadiene styrene (ABS), the sturdy athlete of the group. Its impact resistance4 is what makes it a go-to for reusable spoons. And let’s not forget the glossy finish — talk about making a statement at the dinner table!
The Process Suitability of Injection Molding
I’ve found that an injection molding machine5 is like having a magic wand in spoon production. It injects molten plastic into molds precisely crafted to our specifications. This process doesn’t just ensure quality; it guarantees each spoon is a perfect match to the last.
Comparing Environmental Impacts of Plastics
Being eco-conscious is important to me, and understanding the environmental impact6 of these materials is a big part of that. While PP and ABS can be recycled, giving them a second life, PS often finds its way to landfills due to its lower recycling rate.
For designers like Jacky, balancing production efficiency7 with material properties is crucial. It’s about meeting both aesthetic and functional needs, ensuring every choice is just right for the application at hand.
Polypropylene is heat-resistant and food-safe.True
Polypropylene withstands high temperatures and is safe for food use.
Polystyrene spoons are not recyclable.False
Polystyrene can be recycled, but often isn't due to low recycling rates.
How Does Injection Molding Ensure Precision and Efficiency?
I remember the first time I saw an injection molding machine in action. The precision and speed were mesmerizing!
Injection molding ensures precision and efficiency through a highly automated process that melts and injects plastic into molds with incredible accuracy, creating uniform products swiftly.
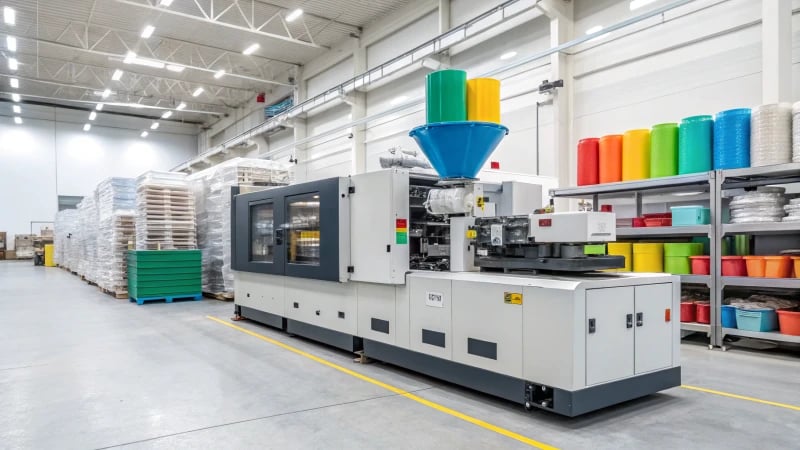
The Process of Injection Molding
Watching plastic pellets transform into usable items is fascinating. It starts with these tiny pellets being heated until they melt into a molten state. This molten plastic is then forced into a mold cavity8, shaped exactly like the finished product—think of a spoon’s smooth curve or the perfect depth of its bowl. The mold’s design is vital; it’s the blueprint for the final product.
Material Compatibility
I’ve always been intrigued by how different materials can change the qualities of a simple object like a spoon. In injection molding, the choice of material can significantly alter its properties. Take polypropylene (PP), for example; it’s known for its durability and heat resistance, making it a go-to for kitchen utensils. On the other hand, if you’re after something with more transparency or impact resistance, polystyrene might be the better choice.
Material | Properties | Applications |
---|---|---|
Polypropylene | Durable, heat-resistant, food-safe | Kitchen utensils |
Polystyrene | Transparent, rigid | Disposable cutlery |
Automation and Precision
There’s something almost magical about automation in injection molding. Once the process kicks in, machines can churn out hundreds of identical items, each with precise dimensions and smooth finishes. This repeatability ensures that every product meets quality standards without deviation.
Efficiency in Production
Setting up the mold correctly is like laying a solid foundation for a house. Once that’s done, the production rate soars. A single injection molding machine9 can produce large quantities quickly, making it indispensable for industries facing high demands.
Quality Control Measures
Ensuring precision doesn’t end with the mold; it continues throughout the injection molding process. With advanced tools like computer-aided design (CAD), meticulous planning occurs even before production begins. Real-time monitoring with sensors and feedback systems helps catch errors early, minimizing waste. This integration of quality control10 techniques with automation makes injection molding not only efficient but also incredibly reliable in producing precision-engineered components.
Injection molding can use only plastic materials.False
Though primarily used for plastics, injection molding can also work with metals.
Automation enhances precision in injection molding.True
Automation allows consistent product replication, ensuring precision and efficiency.
What Challenges Might Arise in Spoon Production?
Ever wondered what it takes to create the perfect spoon? Let’s dive into the world of spoon production, where every detail counts.
Spoon production challenges include choosing the right materials, ensuring efficient manufacturing processes, minimizing environmental impact, and maintaining quality. Overcoming these obstacles is key for manufacturers aiming to improve production and sustainability.
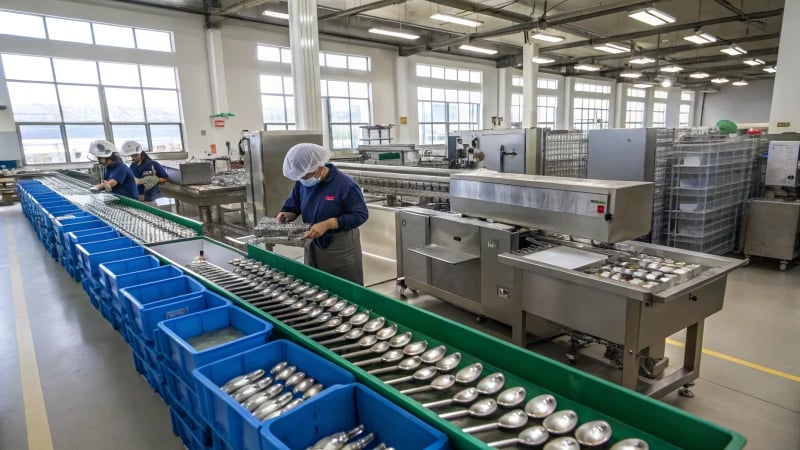
Process Suitability and Material Compatibility
Let me take you back to when I was tinkering with molds, trying to get the perfect spoon shape. It’s more than just about making something that scoops up soup; it’s about the perfect blend of durability and design. Through injection molding11, we can use materials like polypropylene (PP), polystyrene (PS), and acrylonitrile-butadiene-styrene (ABS) to craft spoons that meet varied demands. Each of these materials has its pros and cons:
Material | Advantages | Challenges |
---|---|---|
PP | Durable, heat-resistant, food-safe | May be less transparent |
PS | Transparent, good rigidity | Lower impact resistance |
ABS | High impact resistance, aesthetic appeal | More expensive, not as heat-resistant as other options |
I remember my first successful mold design. The joy of watching a perfect spoon come out of the mold after numerous trials was unmatched. The intricacy required in designing a mold that precisely captures every curve and detail of a spoon is crucial.
Production Efficiency and Precision
Once the mold is perfected, it’s like magic watching injection molding machines12 produce spoons at a rapid pace. However, this magic show comes with its own set of hurdles. I’ve learned that precision is everything—any slight miscalibration or inconsistency can lead to defects. And don’t even get me started on setup times! It can feel like setting up for a grand concert, where every second counts.
- Precision Issues: Any variability in machine calibration or material consistency can lead to defects.
- Setup Time: Initial setup can be time-consuming, impacting lead times.
Environmental Considerations
As someone who loves nature hikes, I’m deeply concerned about plastic waste. The single-use nature of plastic spoons is a real problem. Thankfully, many manufacturers are now exploring sustainable alternatives. The idea of edible utensils might sound futuristic, but imagine enjoying your dessert with a spoon you can eat afterwards!
- Plastic Waste: The single-use nature of plastic spoons contributes significantly to waste.
- Innovative Solutions: Companies are researching edible utensils13 to reduce their environmental footprint.
Understanding these challenges not only helps manufacturers like me adopt more sustainable practices but also ensures that quality and efficiency are maintained as the industry evolves. Addressing these issues is crucial for anyone looking to succeed in spoon production.
PP spoons are more transparent than PS spoons.False
PP is less transparent than PS, which is known for its transparency.
ABS spoons have higher impact resistance than PS spoons.True
ABS offers high impact resistance, unlike PS which has lower impact resistance.
Conclusion
Injection molding machines efficiently produce plastic spoons by melting pellets and injecting them into molds, ensuring precision, material compatibility, and high production rates for durable utensils.
-
Explore the unique characteristics of polystyrene and ABS to understand their suitability for different applications beyond spoon production. ↩
-
Gain insights into why injection molding is preferred over other techniques by understanding its advantages in speed and quality control. ↩
-
Explore various manufacturing methods and understand why injection molding is preferred for plastic utensils. ↩
-
Learn more about why ABS plastic is chosen for durable, reusable products due to its strong impact resistance. ↩
-
Discover how injection molding machines work to produce high-quality plastic spoons efficiently. ↩
-
Gain insights into how different plastics affect the environment and which options are more sustainable. ↩
-
Understand how injection molding achieves high production efficiency with precision and consistency in products. ↩
-
Explore how the intricacies of mold design directly affect the precision and quality of final products. ↩
-
Learn about the capabilities of modern injection molding machines in terms of speed and precision. ↩
-
Discover how quality control measures ensure high standards and precision in injection molding. ↩
-
Discover how injection molding optimizes spoon production through efficient design and material selection. ↩
-
Explore how injection molding machines enhance production speed and consistency. ↩
-
Find out how edible utensils offer a sustainable alternative to plastic. ↩