Have you ever tried adjusting injection molds to achieve strong products without increasing the pressure?
Changing mold settings greatly increases the strength of injection molded items. Improving gate systems, runner layouts, exhaust parts and mold temperature plays a part. These changes lead to smoother melt flow into cavities. This reduces defects. It also keeps structural strength. It happens even at lower pressures.
I remember my first attempt at low-pressure molding. It felt like threading a needle in the dark. Experimenting with mold adjustments really changed everything. Improving the gate system by enlarging or moving it was amazing. This adjustment alone created a big difference in how the melt filled the spaces.
The runner system was next. Polishing and adjusting its size lowered resistance and reduced heat loss. The whole process then felt easy. Attention on the exhaust system mattered a lot too. Adding venting grooves or choosing breathable materials stopped trapped gases from causing problems. Mold temperature is important as well! Slightly raising it helped the melt flow smoothly. I moved closer to the perfect product.
Mold temperature affects product strength in injection molding.True
Proper mold temperature ensures smooth flow, reducing defects and enhancing strength.
Runner design does not impact injection molded product quality.False
Optimized runner design improves melt flow, enhancing product quality and strength.
- 1. How Does Gate System Optimization Impact Injection Molding?
- 2. How Do Runner System Improvements Boost Product Strength?
- 3. Why is Exhaust System Enhancement Crucial in Mold Design?
- 4. How does mold temperature control affect product quality?
- 5. How Do Breathable Materials Enhance Mold Performance?
- 6. Conclusion
How Does Gate System Optimization Impact Injection Molding?
Picture shaping complex plastic parts smoothly and accurately; that’s the wonder of refining the gate system.
Optimizing the gate system in injection molding adjusts gate size and position. This adjustment improves flow dynamics and decreases pressure. Product quality becomes better with these changes. Achieving the best fill and strength in molded parts is important. It truly matters.
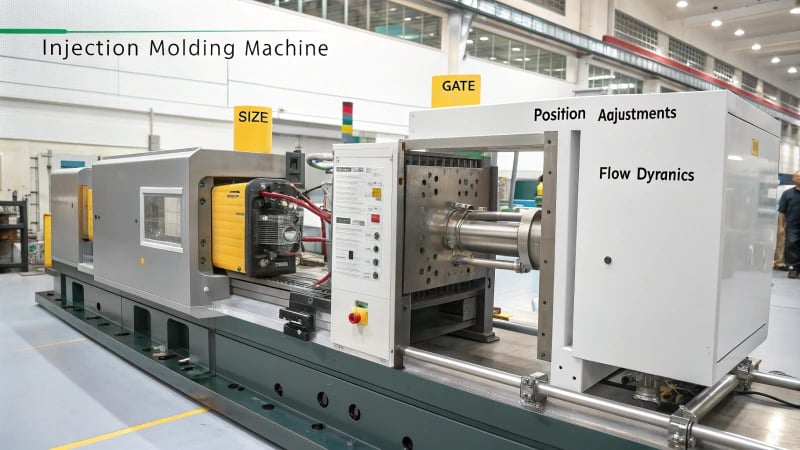
Understanding Gate System Optimization
When I began learning about injection molding, the idea of gate system optimization felt like opening a new part of a complex book. Amazing changes happen by adjusting gate size and position. These adjustments help plastic flow smoothly into a mold.
I discovered that gate size and position are not just technical terms. They are key elements that change raw material into usable objects. Here is how this process works.
Optimization Aspect | Benefits | Example |
---|---|---|
Gate Size Adjustment | Reduces melt resistance | Increase pinpoint gate from 0.8mm to 1.2mm |
Gate Positioning | Ensures even filling | Place gates near thin-walled sections |
Gate Size Adjustment
Changing gate size was a big discovery for me. It was like finding a secret that makes everything go perfectly. Optimized gate size lowers resistance for the melt1, leading to better fills and stronger items. Increasing a pinpoint gate’s diameter seems minor but greatly improves flow.
Gate Position Optimization
Gate position is also crucial. Proper gate placement ensures all parts of a mold fill correctly. Once, I worked on a design where placing gates near thin areas avoided incomplete fills, which was very important for ensuring even cavity filling and improving product durability.
Complementary Strategies
Aside from gate optimization, additional strategies like runner system tweaks and mold temperature adjustment support the process.
- Runner System Adjustments
- Changing runner size and shape smoothens melt flow.
- Surface treatments act like a slide, reducing friction and helping fill molds effectively.
- Mold Temperature Control
- Higher mold temperatures resemble warming hands to mold clay, allowing easier melt flow at reduced pressures.
These strategies together achieve efficient injection molding and high-quality production. Reading more about runner system2 tweaks and temperature controls is suggested for deeper understanding.
Gate size affects melt resistance in injection molding.True
Larger gates reduce melt resistance, improving flow dynamics.
Runner system improvements have no impact on gate optimization.False
Runner system improvements aid smoother melt flow, complementing gate optimization.
How Do Runner System Improvements Boost Product Strength?
Ever thought about how a tiny runner system changes product strength in injection molding?
Better runner systems in injection molding give stronger products. Improving melt flow and lowering injection pressure help a lot. Making sure the cavity fills efficiently is really important. Bigger runner diameter and polishing the surface help. These changes are very good. Such changes really improve product durability.
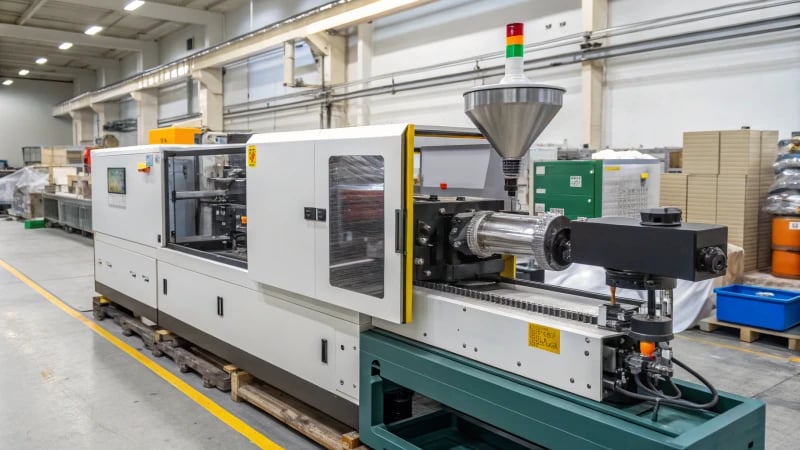
Changing Runner Size and Shape
I remember learning how important runner design is in molding. We once changed the cold runner size from 5mm to 7mm, and the result was amazing! The plastic melt smoothly filled the cavity, making the product stronger and better looking. Shortening the runner by only 10% seemed to speed up our process, greatly reducing heat and pressure loss. It was a big improvement.
Polishing Runners
There is something almost magical about shiny runners. I once spent a whole weekend polishing runners carefully, and the results were clear – a smoother flow and a denser product. It felt like giving the product an extra protective coat. Plus, it saved energy, which is always great in manufacturing.
Effect on Injection Pressure
Lowering injection pressure was eye-opening. By changing runner sizes and improving surface quality, we kept delicate parts intact without losing strength. Combined with gate system optimization3, we discovered a path to greater durability. We did not compromise on strength.
Runner Improvement | Benefit |
---|---|
Larger diameter | Reduced melt resistance |
Shortened length | Decreased heat/pressure loss |
Polished surface | Enhanced melt flow |
Working with Exhaust Systems
Exhaust systems seemed less important until I saw them work with a good runner system. Adding more exhaust grooves and using materials that let air through made operations much smoother. It was like moving to cruise control on a highway. Filling cavities consistently at low pressures was very impressive.
Interaction with Temperature Control
Increasing mold temperatures to lower melt thickness was a real breakthrough. It helped flow through a well-optimized runner system, similar to oiling a noisy wheel. It filled every corner of the cavity evenly, preventing weak spots. This gave us a product that was both tough and trustworthy. Mold temperature control4 is now vital to our process improvements.
Larger runner diameter reduces melt resistance.True
Increasing the runner diameter allows smoother melt flow, reducing resistance.
Polished runners increase injection pressure needs.False
Polished runners decrease friction, reducing the needed injection pressure.
Why is Exhaust System Enhancement Crucial in Mold Design?
When I began studying mold design, I noticed the important job of a good exhaust system in forming perfect products. This system acts like a hero nobody talks about. It quietly keeps everything going well.
Improving the exhaust system in mold design is important. It efficiently gets rid of trapped air during injection molding. This process stops defects like burn marks and voids. Product quality becomes better. Better quality is crucial.
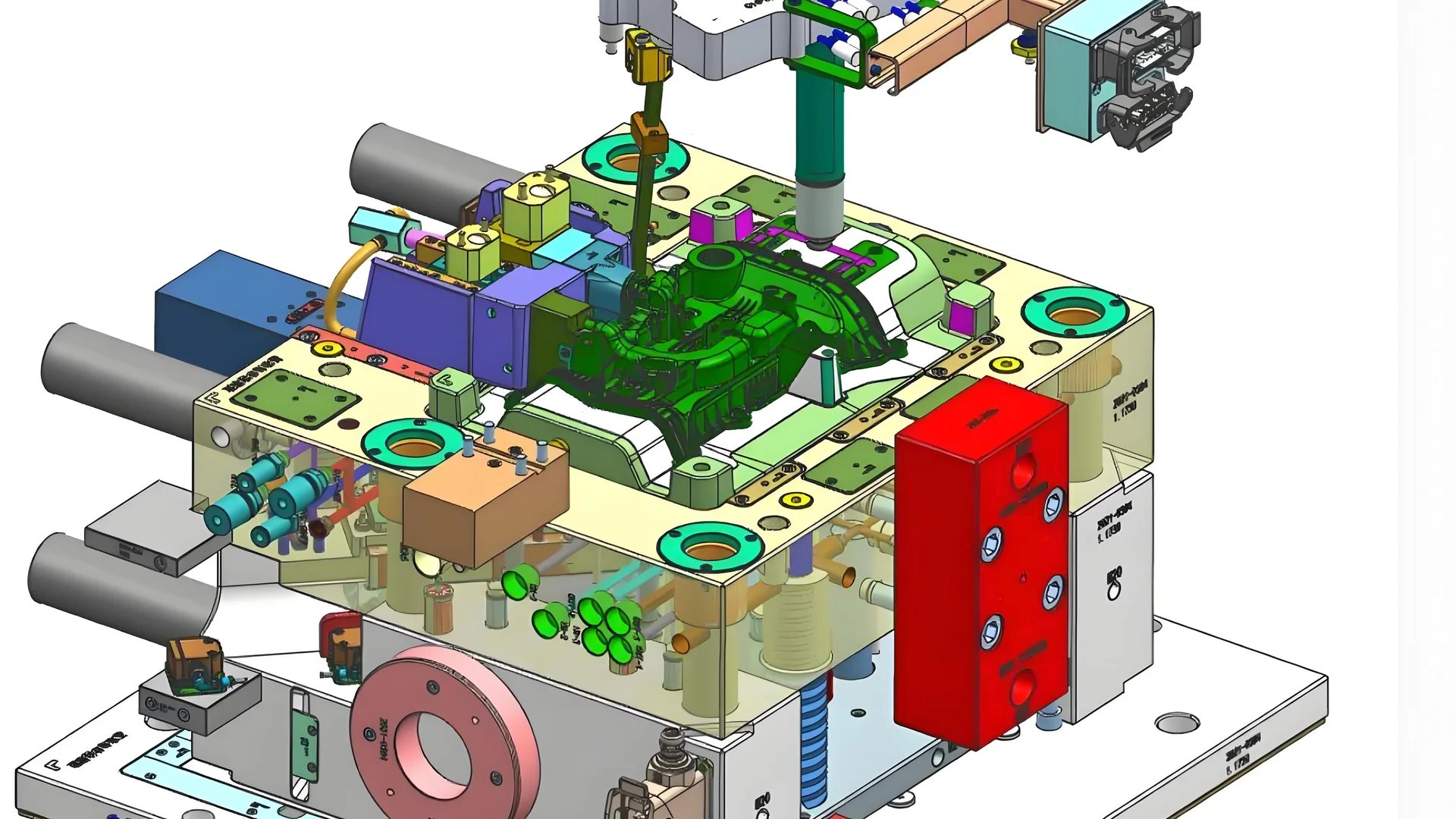
Understanding Mold Exhaust Systems
In mold design, the exhaust system is essential. It removes unwanted gases and air. If not, imperfections like burn marks5 and voids occur. Imagine baking a cake and forgetting to poke holes in the foil. Steam builds up and the cake ends up soggy. The same idea applies here. Good exhaust prevents incomplete fillings and strengthens parts.
Strategies for Improving Exhaust Systems
Increase the Number and Size of Exhaust Grooves
One strategy includes placing and sizing exhaust grooves smartly. Think about squeezing air from a sealed bag. Adding grooves where air often gets trapped helps. It gives the air a path to escape. Increasing groove depth from 0.02mm to 0.03-0.04mm is significant.
Use of Breathable Materials
If traditional grooves don’t work, breathable materials help. They are like tiny windows for escaping gases, ensuring even filling and increasing part strength.
Combining Exhaust Systems with Other Mold Improvements
The best happens when these exhaust methods combine with other mold improvements:
Element | Enhancement |
---|---|
Gate System | Larger gate sizes reduce resistance, enabling smoother cavity filling at lower pressure. |
Runner System | Polishing runner surfaces decreases melt flow friction, complementing improved exhaust efficiency. |
Mold Temperature | Increased temperatures reduce melt viscosity, enhancing flow and air expulsion during injection. |
These work together like a well-played orchestra to cut defects and uplift product quality in injection molding.
Following these strategies means my mold designs meet needs and excel in production efficiency and durability—key for success6 in today’s tough market.
Exhaust systems prevent burn marks in mold design.True
Efficient exhaust systems reduce trapped gases, preventing burn marks.
Breathable materials hinder cavity filling in molds.False
Breathable materials aid in cavity filling by allowing gas escape.
How does mold temperature control affect product quality?
Ever thought about how even a small change in mold temperature might really affect the quality of your products?
Mold temperature control has a big impact on product quality. It influences how the melt flows and cools and it also affects material properties. Precise temperature management achieves even cavity filling. This reduces defects in products. It also keeps the structure of the products strong. A consistent temperature really matters.
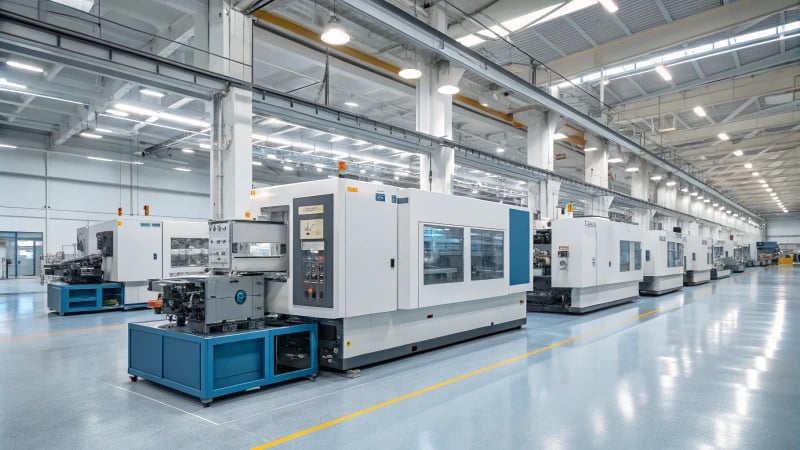
The Importance of Mold Temperature
Mold temperature really affects the quality of designs. One night, I realized how crucial it was when my pieces didn’t fit well. Changing the mold temperature was like magic; suddenly, everything fit perfectly. When I manage the melt thickness7, it fills the space evenly. Higher mold temperatures thin the melt, helping it flow better with less force.
Effect on Cooling Speed
Cooling speed is very important for the final product’s strength. By adjusting the mold temperature, cooling speed changes affect crystal structure and strength. Even a small change from 30-40°C to 40-50°C in temperature for some plastics really optimizes material characteristics8.
Influence on Melt Flow
Good mold temperature control leads to better melt flow. This is key to avoiding issues like incomplete fills or lines where parts meet. I remember a project where a small boost in temperature greatly improved fill and finish.
Practical Application
- Gate System Adjustment: Changing gate size and place lowers resistance and helps even melt spread.
Adjustment | Effect |
---|---|
Increase gate size | Reduces melt resistance |
Optimize gate place | Ensures even filling |
- Runner System Improvement: Polishing runner surfaces complements temperature tweaks to enhance flow behavior9.
Better Exhaust System
Efficient exhaust systems control mold temperature effects. Larger grooves let air escape, improving cavity fill.
- Choosing Materials: Use materials that allow air through when normal venting can’t, so mold temperature changes don’t trap air.
Total Temperature Control
Using mold temperature control with system tweaks raises product quality. Real-time tracking technology10 can refine the process, giving insights into how temperature affects products.
Higher mold temperature reduces melt viscosity.True
Higher temperatures decrease viscosity, enhancing flow at lower pressures.
Increasing mold temperature always weakens product strength.False
Controlled temperature can optimize crystallinity, enhancing strength.
How Do Breathable Materials Enhance Mold Performance?
Recall the last occasion you encountered an irritating mold problem? I certainly experienced it as well, until breathable materials revealed their wonders to me.
Breathable materials in molds introduce new possibilities to manufacturing. These materials help with gas escaping, reducing imperfections and improving how molds work. They help the melt flow smoothly, leading to excellent quality in production. Very excellent quality.
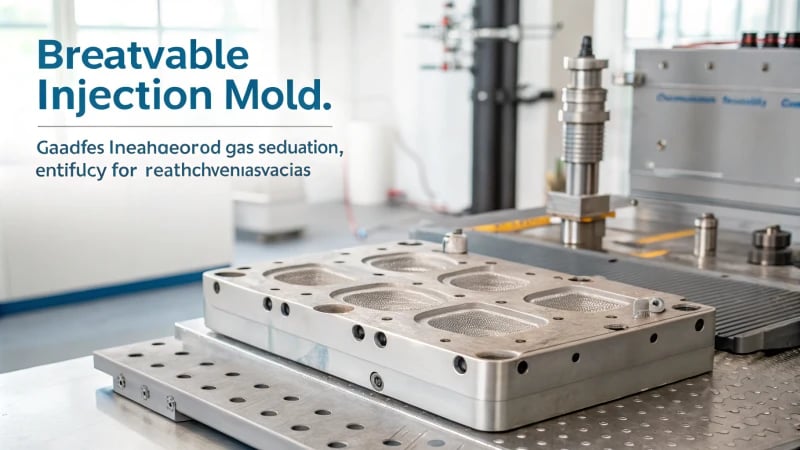
Improved Gas Removal
Imagine dodging those annoying flaws that used to bother your production line. Breathable materials in molds help get rid of gases efficiently. During injection molding11, trapped air might leave ugly holes or burns in products. I remember the irritation of dealing with this until breathable materials came along. They let gases escape quickly, reducing pressure and leading to a perfect finish.
Fewer Defects and Better Product Quality
Recall a time when short shots or surface marks appeared on your products – annoying, isn’t it? Breathable materials help solve these problems. They allow smooth flow at lower pressures, resulting in less damage and more strength in the product. I once worked with very thin-walled sections where these materials greatly improved thickness and strength. It really made a difference.
Defect | Caused by | Solution |
---|---|---|
Voids | Trapped gases | Breathable materials |
Surface burns | Air entrapment | Efficient gas evacuation |
Short shots | Insufficient pressure | Improved melt flow |
Improvement of Mold Parts
Using breathable materials in molds changed the way I design gate and runner systems. By adjusting gate size and position, I’ve lowered injection pressure needs a lot, which reduces energy consumption. Breathable steel in tough ventilation spots has transformed exhaust issues, improving mold performance.
Breathable materials are like a hidden tool in mold design – they manage pressure better, protecting the product’s integrity. Exploring gate system improvements12 can probably reveal even more possibilities in your designs.
Breathable materials reduce injection pressure in molds.True
They allow gases to escape, reducing pressure build-up.
Using breathable materials increases mold defects.False
They minimize defects by improving gas evacuation and melt flow.
Conclusion
Optimizing injection molds through gate adjustments, runner improvements, and temperature control enhances product strength and quality while reducing defects at lower pressures.
-
Understanding melt resistance aids in optimizing gate design for better product quality. ↩
-
Gain insights into optimizing runner systems for enhanced melt flow and reduced pressure loss. ↩
-
Learn how gate system optimization complements runner improvements for enhanced product strength. ↩
-
Understand how mold temperature adjustments can improve product strength when used with optimized runners. ↩
-
Explore how burn marks impact product aesthetics and structural integrity in injection molding. ↩
-
Discover comprehensive strategies that lead to success in injection molding, focusing on quality and efficiency improvements. ↩
-
Exploring this link reveals how adjusting mold temperature affects melt viscosity and flow, crucial for improving injection molding outcomes. ↩
-
Understanding optimal temperatures for various materials enhances quality by improving strength and durability in molded products. ↩
-
Learn about enhancing runner systems to support better melt flow dynamics, crucial for reducing defects in molded components. ↩
-
Discover technologies that aid in managing mold temperatures effectively, improving consistency and quality in manufacturing processes. ↩
-
Learn how breathable materials specifically enhance injection molding by addressing common defects and improving quality. ↩
-
Discover strategies for optimizing gate systems to enhance mold efficiency and reduce defects. ↩