Faced difficulties with those tough plastic parts stuck in the mold? I certainly have. Learning the secrets of perfect ejection force in injection molding really changes everything.
To increase ejection force in injection molding, first optimize the mold design. Improve the ejector mechanism by making it more efficient. Upgrade guiding and support structures. Adjust demolding angles and surfaces. Do this to allow products to release smoothly and reduce defects. It is important. Very important.
I remember when I first had a big problem with molding. The pieces stuck and caused many delays and problems. I understood that good tools were not enough; knowing how to design molds was really important. I learned new methods like adding more ejector points and smoothing mold surfaces. My frustrating experiences turned into smooth production runs.
We should look at these methods together. Adjusting the demolding angle or making the mold structure stronger really helps. Every change really surprises you with its impact on the ejection process and improves efficiency.
Optimizing ejector mechanism increases ejection force.True
Improving the ejector mechanism design enhances force efficiency.
Demoulding angles have no effect on ejection force.False
Adjusting demoulding angles aids in smooth product release.
How Can Optimizing Ejector Mechanisms Revolutionize Manufacturing?
Have you ever thought about why ejector mechanisms are so important in molding? These parts play a big role in taking products out of molds. Let’s explore their benefits and see how improving them changes manufacturing efficiency and product quality. Better results and higher quality often result from these changes.
Improving ejector mechanisms very often raises product quality. Equal force distribution during ejection is important. This reduces the risk of deformation. This is very important. Molds last longer with such methods. More ejector points help. Suitable types of ejectors work best. Better guiding systems assist in this process.
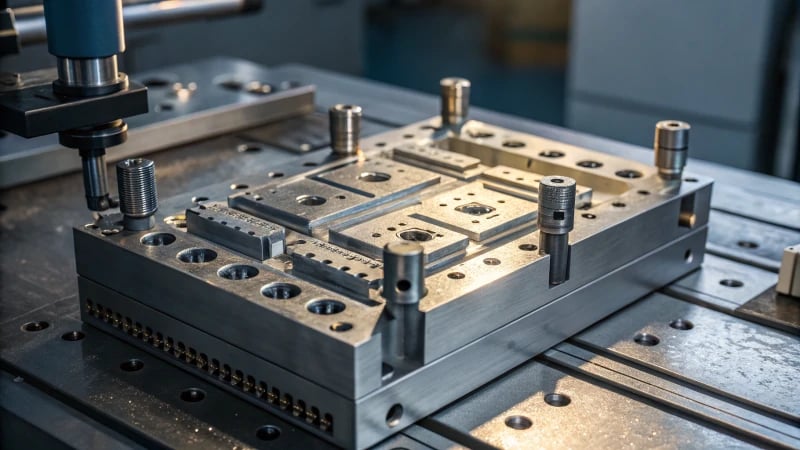
Increase Ejector Points and Distribution Density
Imagine a busy kitchen. Every tool has its place, and every move has a purpose. That’s how optimizing ejector points feels. I once redesigned a mold for a flat plastic piece. By increasing the number of ejector pins1 at key spots like the edges and center, it was like solving a puzzle where each piece had to fit perfectly. Using mold flow analysis felt like using a map for this puzzle; it showed me where to place each pin, making ejection smoother and reducing stress on the mold, thus extending its life.
Choose the Right Ejector Mechanism
Ejector mechanisms are like shoes for an event—they are essential for comfort and success. In one project with large hollow structures, we selected a push plate ejector2, which spread force evenly, much like sneakers support feet, making a big difference in smooth demolding. For products with undercuts, I chose an inclined ejector mechanism that converted vertical force into lateral movement, similar to adjusting your walk uphill.
Strengthen Guiding and Support Structures
Strengthening guides is akin to building a strong house foundation. Installing guide columns was like putting sturdy beams in place; they maintained stability during ejection by preventing deflection and uneven force—much like how a strong frame holds up a building. Adding ribs in larger molds was comparable to adding extra support beams, ensuring consistent performance under pressure.
Optimization Aspect | Benefit |
---|---|
Increased Ejector Points | Even force distribution, reduced deformation risk |
Push Plate Ejector | Uniform force for hollow structures |
Inclined Ejector Mechanism | Effective ejection of undercuts |
Enhanced Guiding System | Accurate movement direction, improved force transmission efficiency |
Reinforced Support Structure | Reduced mold deformation, improved operational consistency |
Optimize Demoulding Angle and Surface Treatment
Changing the demoulding angle is like adjusting your chair—you want the right angle to relax without strain. I found that slightly increasing angles from 1° to 2° significantly reduced ejection problems for deep products. Polishing surfaces made everything glide smoothly; improving surface roughness lowered friction during ejection while applying release agents was akin to adding oil to keep movement smooth.
Using these methods focuses on efficiency and quality while helping extend mold life—key aspects in any competitive manufacturing environment. For me, it’s about having the right tools ready to tackle any design task with care and precision.
Increasing ejector points reduces deformation risk.True
More ejector points distribute force evenly, minimizing deformation.
Inclined ejector mechanisms are unsuitable for undercuts.False
Inclined ejectors effectively handle undercuts by converting forces.
How Do Guiding and Supporting Structures Affect Ejection Force?
Ever thought about how a small change in design might completely transform mold removal? A tiny adjustment could have a really big impact. A little change matters a lot.
Supporting structures hold great importance in shaping by steadying the ejector system. They help keep ejection forces even and lower product distortion. This occurs through precise movement. They reduce force imbalance during ejection.
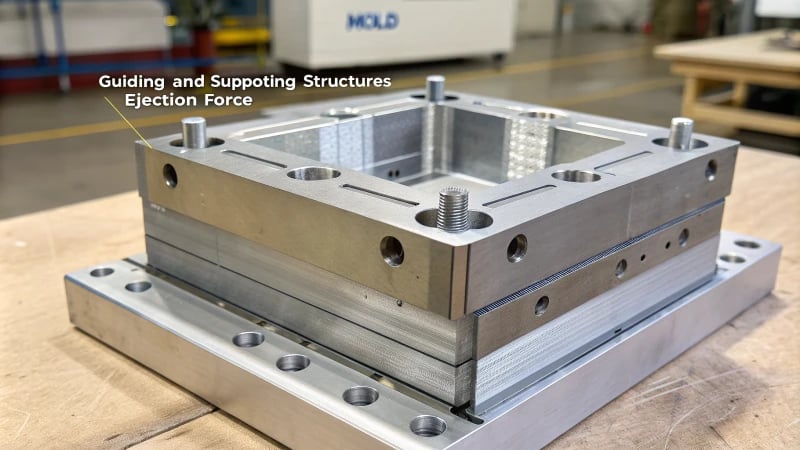
The Job of Guiding Systems in Ejection Setups
I recall the first time I tried improving a mold design. It was like piecing together a puzzle. Guiding systems, such as guide columns and sleeves, are necessary parts. These parts help the ejector plate move smoothly and correctly. Without proper guidance, just like walking a tightrope without safety, the ejector mechanism might tilt and unevenly push out materials.
High-precision guiding devices serve as trusted maps. They lower chances of mistakes and spread ejection force evenly.
Vital Parts of Guiding Systems:
Component | Function |
---|---|
Guide Columns | Ensure linear movement of ejector plates |
Guide Sleeves | Provide a smooth path for guide columns |
Support Structures Give Firmness
Support structures look like the mold design’s backbone. Solid supports are important to endure the forces during ejection. I once fortified a mold template with thicker materials. It felt like giving the mold a strong shield against bending and crushing.
This firmness keeps the ejection mechanism3 running well, lessening deformation and bettering energy transfer.
Effects of Better Support Structures:
- Less bending of mold plates
- Better energy transfer of ejection force
Enhancing Mold Release for Easier Ejection
I found increasing the mold’s angle and refining surface finishes can really change ejection strength. A bigger angle works like a gentle push that helps release products. A smoother mold surface compares to adding oil to a rusty hinge, lessening friction and the needed ejection force.
Techniques for Surface Enhancement:
- Polishing: Get low surface roughness (Ra0.8 – Ra0.2μm)
- Release Agents: Better release of products
Real-world Uses and Thoughts
Tailoring designs to fit specific items is fundamental. Mold flow software acts like a crystal ball. It shows scenarios and helps pick the best ejector setup4. This keeps ejection forces even and stops product bending.
Adding exact guiding systems and strong supports greatly influences how well ejection mechanisms work, creating a more dependable process for making complex molded items. These small changes lead to big upgrades, making me admire the mix of art and science in mold design even more.
Guide columns ensure linear movement of ejector plates.True
Guide columns are designed to facilitate straight, precise movement.
Thicker materials in molds decrease ejection force.False
Thicker materials enhance stability, not directly affecting ejection force.
Why is the demoulding angle crucial for efficient ejection?
Picture shaping the perfect mold for an important part. It stays stuck and won’t let go. Annoying, isn’t it?
The demoulding angle is very important for easy removal from molds. This angle lowers friction and resistance. Usually, it is between 0.5° and 3°. This small range protects parts from damage. It also really increases production speed. Production goes faster.
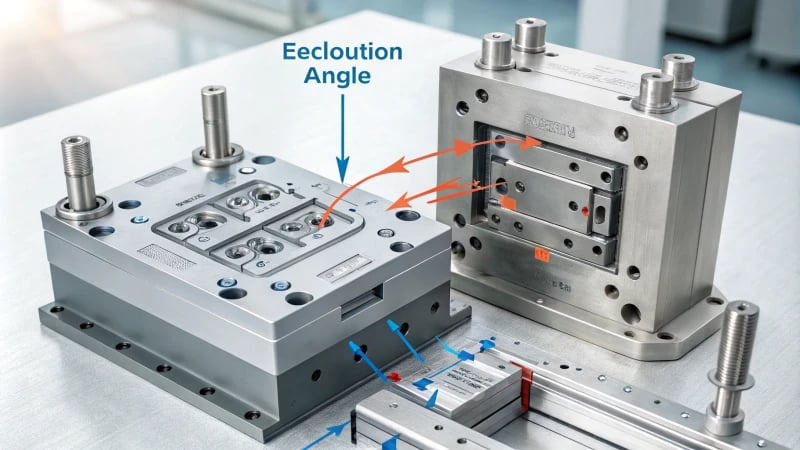
Understanding the Demoulding Angle
I remember a time when I worked on a tough mold design. The demoulding angle, known as the draft angle, was crucial. It helped parts come out easily by reducing resistance and friction with the mold walls. This angle is usually between 0.5° to 3°, adjusted based on material and design needs.
Impact on Ejection Force
Once, I tackled a deep-cavity product5. An incorrect demoulding angle almost ruined the project. A well-chosen angle can greatly lessen the ejection force, protecting both the part and the mold. Increasing the angle simplified the ejection process by decreasing surface adhesion. This was a crucial lesson I learned.
Feature | Regular Products | Deep-Cavity Products |
---|---|---|
Demoulding Angle | 1° | 2°-3° |
Optimizing Ejector Mechanism Design
Tweaking the ejector mechanism helps a lot. More ejector points6, spread out evenly, distribute forces evenly. This prevents product warping. In a project with large, flat plastic pieces, adding extra ejector pins in key spots made everything smooth.
Role of Mold Surface Treatment
A smooth mold surface is vital. Polishing after EDM can achieve a surface roughness of Ra0.8 – Ra0.2μm, making ejection smoother and reducing friction. A release agent further improves demoulding performance, reducing the need for excessive ejection force and increasing productivity.
In challenging times, expert tips on surface treatments7 were very helpful to me.
Enhancing Mold Structural Support
Strengthening mold structures improved my designs. Using guide columns and sleeves ensured precise ejection motion, minimizing uneven forces that can occur due to mechanism deflection.
Adding ribs to mold plates cut down on deformation during high pressure operations.
Exploring these aspects through mold flow analysis8 helped refine designs, making them more efficient with less downtime.
Demoulding angle ranges from 0.5° to 3°.True
The demoulding angle typically ranges between 0.5° and 3° for efficiency.
Increasing ejector points decreases ejection force.True
More ejector points distribute forces evenly, reducing overall ejection force.
How Can Surface Treatment Improve Mold Performance?
Surface treatment really changes the game for people wanting to increase mold efficiency and lifespan.
Surface treatment improves mold performance by making it stronger. These treatments reduce friction. Products eject smoothly. Polishing and coating stop wear. These methods improve product quality. Very good quality.
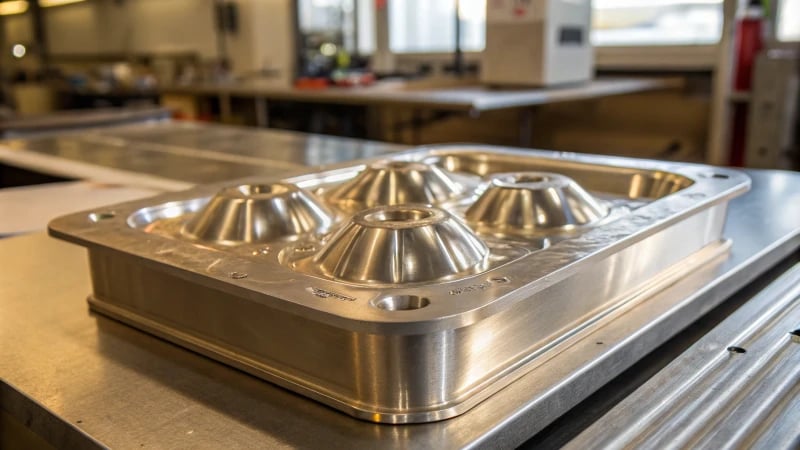
Strengthening Molds with Surface Coatings
I remember the first time I saw a mold improved with coatings like nitriding or hard chrome plating. It felt like witnessing a small wonder. These methods create a protective layer that fights against damage, acting like a superhero shield for your mold. This not only makes the mold last longer but also reduces costs for new ones. For example, nitriding increases hardness9 and protects against rust.
Lowering Friction for Easy Ejection
Polishing a mold for smoothness is important. I learned this lesson early on. A sleek surface lowers friction between the mold and plastic, allowing easy ejection—like that pleasant moment when butter smoothly slides off a non-stick pan. Polishing after EDM to reach an Ra of 0.8-0.2μm is often suggested. Additionally, applying a release agent may simplify demolding10.
Treatment Method | Benefits |
---|---|
Nitriding | Increases hardness and reduces wear |
Chrome Plating | Protects against corrosion and abrasion |
Improving Mold Design with Surface Coatings
Surface coatings do more than just protect; they also refine mold design. Changing the demolding angle or the surface texture reduces the force needed for ejection. I once adjusted the angle on deep-cavity molds from 1° to 2°. It felt like unlocking a hidden trick.
Moreover, innovative designs can include inclined ejector systems11 that handle tricky shapes easily by converting vertical forces into lateral ones.
Supporting Structures and Surface Coatings
Strong guiding and support structures for molds are very important. High-precision guide columns act as quiet heroes ensuring smooth movement during ejection, reducing unequal forces. I’ve watched how reinforcing mold templates with ribs helps with reaction forces during ejection, greatly boosting stability and performance.
These methods make products better and production faster, showing why surface coatings are crucial in modern mold design and manufacturing.
Nitriding increases mold hardness.True
Nitriding creates a hard, protective layer on molds, enhancing durability.
Polishing increases mold surface roughness.False
Polishing decreases surface roughness, reducing friction for easier ejection.
Conclusion
Enhancing ejection force in injection molding involves optimizing mold design, improving ejector mechanisms, and adjusting demolding angles to ensure smooth product release and reduce defects.
-
Learn how strategic placement of ejector pins can enhance product quality and prevent deformation. ↩
-
Understand why push plate ejectors are ideal for large hollow products and how they ensure uniform force distribution. ↩
-
Explore effective design strategies for ejection mechanisms that minimize force imbalances. ↩
-
Discover how mold flow analysis predicts optimal configurations for efficient ejection. ↩
-
Learn how adjusting angles benefits deep-cavity product ejection by reducing holding force. ↩
-
Explore strategies for optimizing ejector designs to enhance force distribution. ↩
-
Discover techniques for surface treatments that improve mold efficiency. ↩
-
Find out how mold flow analysis aids in determining optimal ejector designs. ↩
-
Discover how nitriding increases mold hardness and resistance to corrosion. ↩
-
Learn how release agents improve demolding efficiency and product quality. ↩
-
Understand the benefits of inclined ejector mechanisms for complex mold designs. ↩