Some plastic items might not look or work properly. The reason could be the injection pressure!
High or low injection pressure in molding causes defects such as flash, short shots, sink marks, weld marks and spray marks. These problems result from incorrect pressure settings. The look and strength of the product suffer. Very high pressure or very low pressure affects the result.
Years ago, when I first started exploring the details of injection molding, I quickly found out how essential correct pressure was. I once watched a batch of plastic casings with ugly extra edges. These edges spilled over the mold. This revealed that high pressure pushed the melted plastic into unwanted areas, leading to more work in trimming and affecting the product’s exact size.
Another time, I encountered the opposite issue꞉ short shots. Imagine parts that are not fully formed and fail to meet function or design needs. Low pressure left some spaces barely filled, which was very tough for complex models with thin walls or detailed parts.
Sink marks were another challenge. A project with car interiors became particularly frustrating. Visual quality was crucial in this case. Too little pressure created uneven surfaces, resembling small craters. Not ideal for showing to a client.
Each of these problems taught me how to balance injection pressure. Excess pressure results in flash and spray marks. Low pressure leads to short shots, sink marks and weld marks, which are really troublesome. Understanding these details has been important in improving molding methods and achieving very high quality.
Flash defects occur due to high injection pressure.True
Excessive pressure forces material into mold gaps, causing flash.
Sink marks are caused by low injection pressure.True
Insufficient pressure leads to inadequate material filling, causing sinks.
How Does Flash Occur Due to Injection Pressure?
Have you ever questioned why some plastic items have annoying extra pieces on the edges? Pressure causes this problem. Learn how injection pressure creates flash and explore possible solutions.
Flash happens when too much injection pressure pushes plastic melt to spill over at the mold’s seams or gaps. This spill affects the product’s look. Trimming work increases as a result.
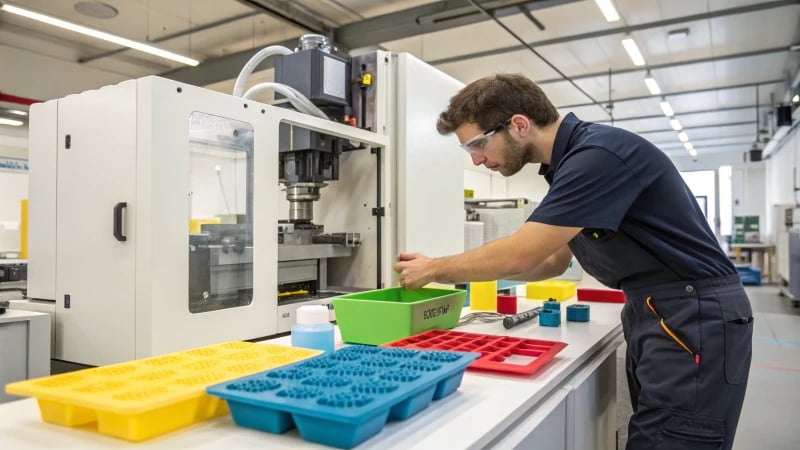
The Role of Injection Pressure in Flash Formation
I remember the first time I saw flash in my work. I stared at a batch of new molded parts, each with unwanted plastic pieces hanging on the edges. It felt like painting a beautiful picture and then spilling paint on it. Flash happens when injection pressure gets too high. The plastic melt rushes into the mold so hard that it spills out at the seams and gaps. This ruins the product’s look. It also adds more work after production because of extra trimming.
Table: Effects of High Injection Pressure
Issue | Cause | Impact |
---|---|---|
Flash | Excess pressure causing overflow | Poor appearance, increased trimming |
This taught me how important it is to find the right injection pressure. Too high gives flash. Too low risks short shots, leaving parts unfilled. Precision and patience are key here.
Comparison with Other Defects
Balancing injection pressure avoids more than just flash. It helps prevent defects like short shots, weld marks, and sink marks. Each defect shows different pressure issues.
- Short Shot: Filling a glass with just a little water doesn’t work. Similarly, low pressure leaves mold cavities unfilled, causing incomplete products.
- Sink Marks: These dents resemble a cake cooling without enough batter. Uneven wall thicknesses cool unevenly; without enough pressure, there isn’t enough material for shrinkage.
- Weld Marks: These lines show where plastic flows fail to join well, often due to low pressure. It’s like two rivers not merging smoothly.
Adjusting machine settings, checking mold integrity, and using effective cooling methods1 reduce these flaws significantly. Regular checks keep production quality steady.
Understanding injection pressure’s role in flash and other defects improved my designs’ look and function. It really helps align my projects with design goals while increasing production efficiency.
High injection pressure causes flash in molding.True
Excess pressure forces plastic melt to overflow, creating flash.
Flash improves the aesthetic appeal of molded products.False
Flash detracts from appearance and requires additional trimming.
What Causes Short Shots in Injection Molding?
Short shots in injection molding might result in a product that seems incomplete, similar to a cake that didn’t rise well. There are reasons why this occurs. Solutions exist.
Short shots happen when plastic doesn’t completely fill the mold. Not enough pressure usually causes this. Parts become incomplete. They look different and don’t work properly.
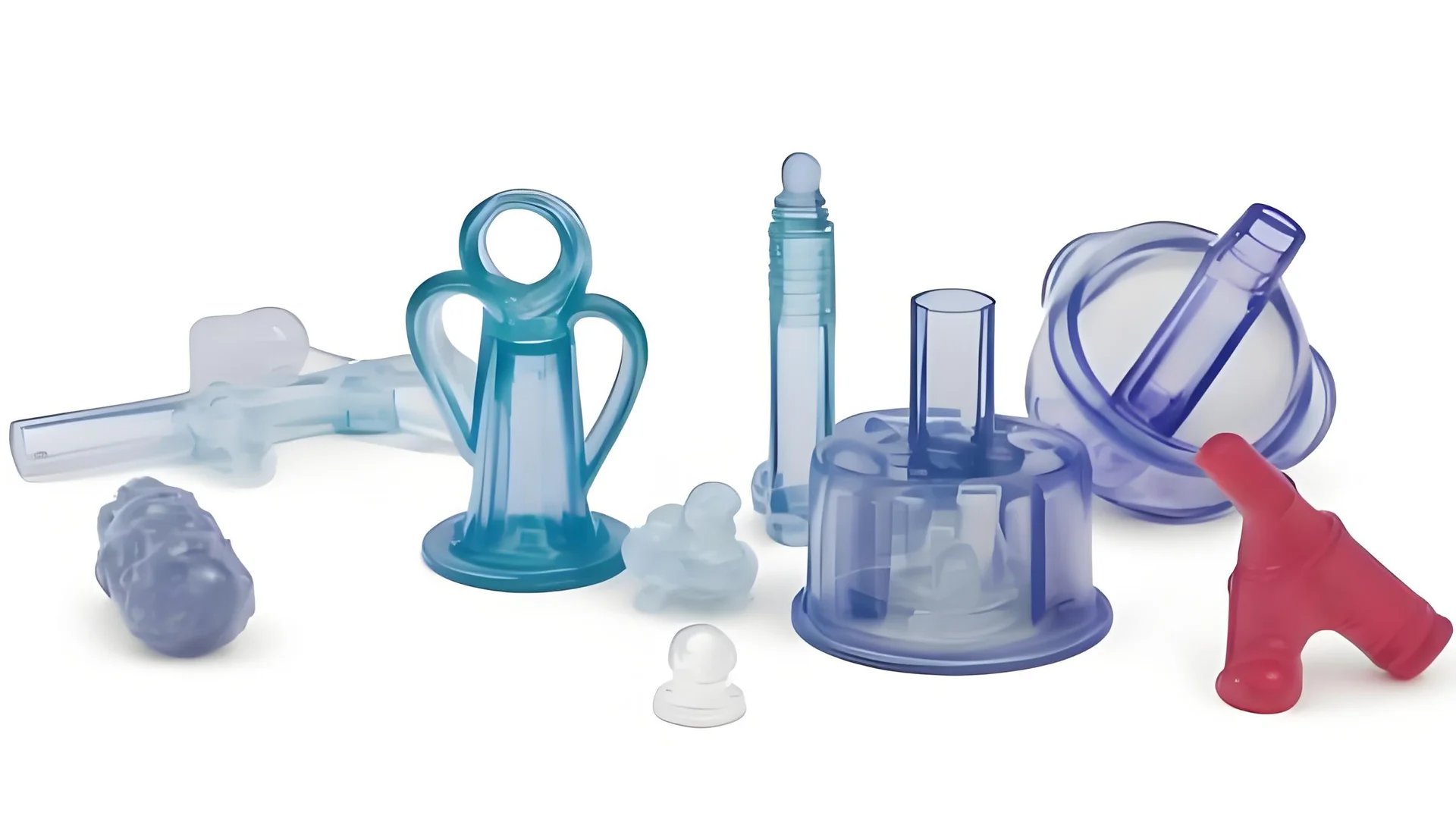
Understanding Short Shots
Many people feel upset when a molded part is incomplete. This is normal. Imagine baking a cake and noticing you have no flour halfway through. Short shots are bothersome defects. The mold does not fill fully, affecting the product’s quality and use. I recall my first experience with short shots; it was a nightmare near a project deadline.
Key Causes of Short Shots
-
Insufficient Injection Pressure
Think about pushing a beach ball underwater with one hand. This is similar to low injection pressure. When the pressure is too low, the plastic doesn’t have enough force to fill the mold, especially in designs with thin walls or a lot of detail.
Impact: The parts may look like a shark bit them – very bad for looks and use.
-
Inadequate Material Flow
Imagine a river frozen solid; that’s what happens with high viscosity or quick cooling material. It just cannot reach all parts of the mold.
Factors Affecting Flow Impact Material Temperature Higher temperature improves flow Mold Temperature Affects cooling rate Design Complexity Influences fill path -
Improper Venting
Venting issues are like holding your breath too long while swimming – you just can’t function. Air trapped in the mold blocks full filling, so vent design is crucial to let air out.
-
Material Selection
It’s like trying to blend a smoothie with frozen fruit. The wrong material might not flow well if it doesn’t match the design and use.
-
Machine Limitations
Using old machines can feel like driving a car with a broken transmission. Steady pressure and speed are needed, and without these, filling problems happen.
Addressing Short Shots
Adjusting things like injection parameters2, such as pressure and temperature, helps solve short shots—it’s very important. Regular checks of your mold design and machine are necessary for smooth operation.
Using simulation software is like having an extra security layer at home; it predicts problems before they occur, helping fine-tune designs for better results.
For someone like me who has faced these challenges, these steps are very helpful in keeping production steady.
Low injection pressure causes short shots.True
Insufficient pressure fails to fill the mold completely, causing defects.
High material viscosity prevents short shots.False
High viscosity restricts flow, increasing the risk of incomplete filling.
What Causes Sink Marks on Molded Products?
Did you ever see those annoying dents on your beloved plastic objects?
Sink marks result when insufficient pressure is used during the injection molding process. The natural shrinking of the material as it cools causes this. Areas with uneven wall thickness are especially affected. You see obvious dents on the product’s surface.
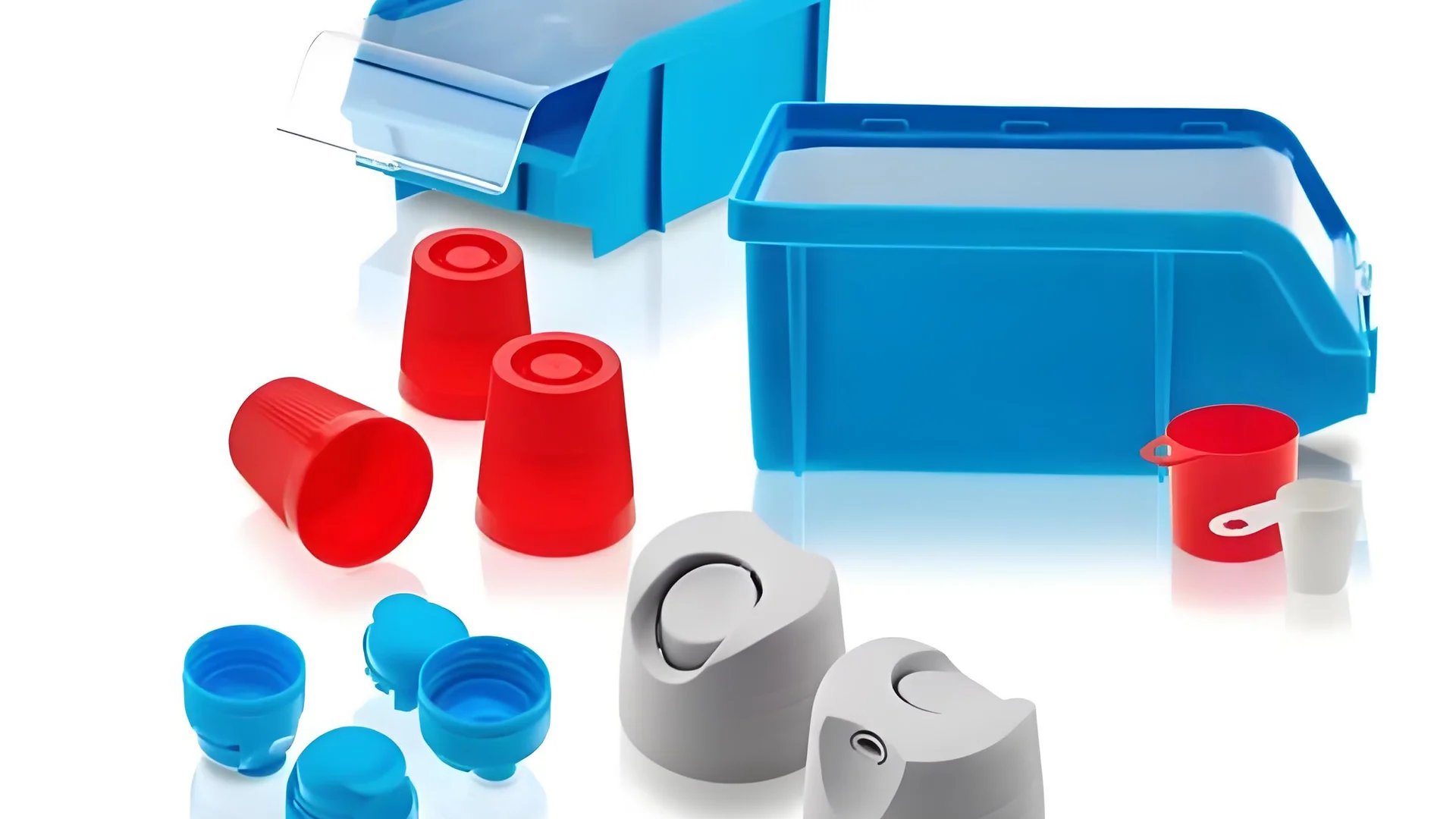
Knowing Sink Marks in Injection Molding
Ever looked at a plastic part and saw unexpected dips or dents? Many people have experienced this. Sink marks are quite troublesome in injection molding. I remember the first time I saw them on parts I designed. It felt like finding a blemish on your nose before a big event – annoying and surprising!
Why Sink Marks Appear
- Low Injection Pressure: Imagine trying to blow up a balloon without enough force. If pressure is too low, the plastic might not fill the mold completely, especially in thicker areas that need more material for shrinkage.
- Cooling Differences: Uneven cooling can cause problems too. It’s like baking a cake where parts cook faster than others. Thick sections cool slowly, causing more shrinkage than thin parts.
- Material Behavior: Different materials shrink differently, similar to how different cake recipes rise differently. Choosing the right plastic helps avoid these marks.
Factor | Impact on Sink Marks |
---|---|
Injection Pressure | High pressure prevents sink marks by ensuring proper filling and compensating shrinkage. |
Cooling Time | Longer cooling times can reduce shrinkage and minimize sink marks. |
Material Selection | Choosing materials with lower shrinkage rates can help avoid sink marks. |
Fixing Sink Marks
So, how do we handle these annoying sink marks? Here are some tricks I’ve learned:
- Adjust Injection Pressure: Find the perfect pressure where enough material fills the mold properly.
- Design Changes: Avoid big changes in wall thickness. Just like in fashion, keeping things consistent works well. Add features like ribs or bosses to distribute material evenly.
- Choose Suitable Materials: Pick plastics that shrink less. This matters for products where looks are very important, such as car interiors3 or electronic cases4.
Other Defects to Watch
While fixing sink marks, you might see other problems. It’s like a game where fixing one issue causes another to appear!
- Flash (Overflow): Happens when too much force pushes plastic out of the mold, creating excess along parting lines.
- Short Shot: Not enough pressure results in incomplete filling, which is bad when every detail matters.
- Weld Marks: Wrong pressure causes lines where different flows meet but don’t merge well.
- Spray Marks: Fast injection speeds cause these snake-like defects.
Understanding these issues helps refine production and improve product quality. For more solutions, explore advice on manufacturing best practices5. Once you master these tips, you’ll be the expert people turn to for fixing these molding puzzles!
Sink marks are caused by low injection pressure.True
Insufficient pressure fails to fill the mold fully, causing sink marks.
High cooling rates increase sink mark occurrence.False
Uneven cooling, not high rates, causes shrinkage leading to sink marks.
How Do Weld Marks Affect Product Integrity?
Picture working on a project and you spot those tricky weld marks. They really change the strength of the product. These marks might alter the integrity of the item. They change everything.
Weld marks appear when streams of plastic join but do not connect properly because of temperature or pressure problems. These lines may look small but often weaken a product. They can also ruin its appearance.
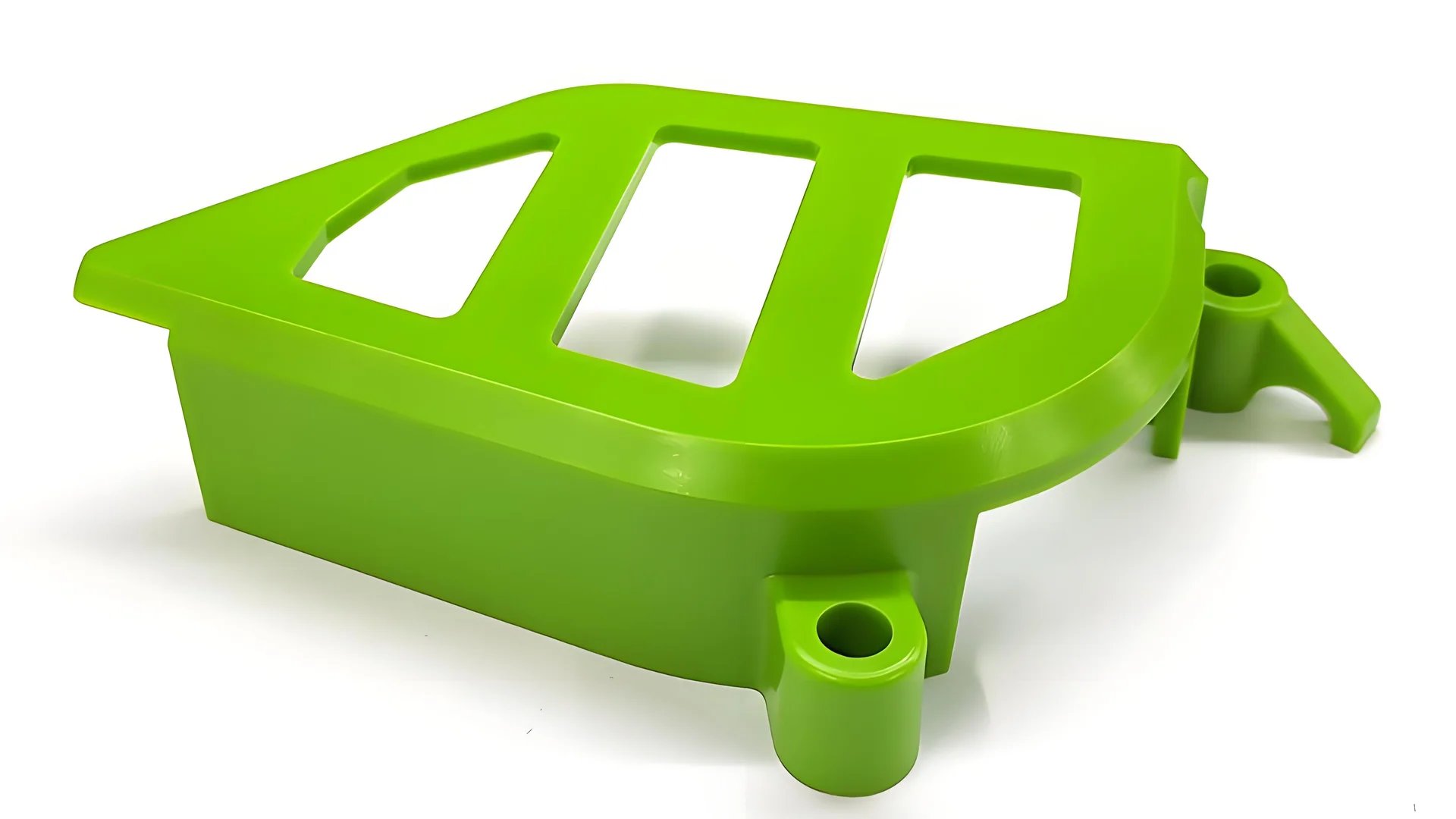
Understanding Weld Marks
Ever spent hours on a design, only to see annoying weld lines spoil the look? I feel that frustration too. These weld marks, the lines you see on a product’s surface, often appear during plastic injection molding6. They show up when different streams of plastic meet but don’t mix well, usually because of temperature drops or wrong pressure.
Factor | Cause | Impact |
---|---|---|
Temperature | A significant drop as the plastic flows through the mold cavity. | Poor bonding between the melts, resulting in visible lines. |
Injection Pressure | Inadequate pressure causing slow flow and premature cooling. | Weak areas within the product, making it susceptible to breakage under stress. |
Effects on Product Integrity
-
Structural Weakness
I remember working on a car part; weld marks were a big problem. These marks cause weak spots, especially in parts where durability7 cannot be ignored.
-
Aesthetic Concerns
Then there’s the look of the product. Visualize a lovely cosmetic package spoiled by these lines. It’s like drawing a mustache on the Mona Lisa!
-
Compromised Functionality
For products with complex shapes or important sizes, weld marks often disrupt how things work. I once had to fix an electronic device where these marks messed up the fit of the parts.
Reducing Weld Marks
Over time, I’ve realized that solving weld marks involves adjusting several factors:
- Temperature Control: Steady temperature leads to smooth flow and proper merging.
- Injection Pressure: Correct pressure prevents early cooling and results in better bonding.
- Material Choice: Choosing materials with good flow traits probably reduces weld mark risks.
For anyone like Jacky8, understanding these details is key to keeping quality and integrity, especially with bigger production volumes. It’s about using challenges to create better processes and superior products.
Don’t forget other molding problems like flash, short shots, and sink marks:
- Flash comes from high injection pressure, causing overflow and extra trimming work which may change product size.
- Short shots occur when low pressure stops full mold filling, impacting the product’s form and use.
- Sink marks result from not enough pressure during cooling, leading to uneven surfaces – bad for high looks standards.
These factors remind me that even in manufacturing, perfection is always moving, but aiming for it is where the real magic occurs.
Weld marks always cause structural weakness.False
Weld marks can cause weakness but not in all cases; it depends on use.
Temperature drop leads to weld marks.True
A temperature drop can prevent proper merging of plastic melts.
What Causes Spray Marks in Injection Molding?
Do mysterious spray marks ever appear on a new product? Perhaps, people often wonder, "Where is the problem?" The process of injection molding holds these puzzling answers. Let’s explore this world to find out why these annoying spots appear.
Spray marks in injection molding often result from too much pressure and wrong injection speed. These issues cause the plastic melt to rush into the mold. Such haste then creates unpredictable flow patterns.
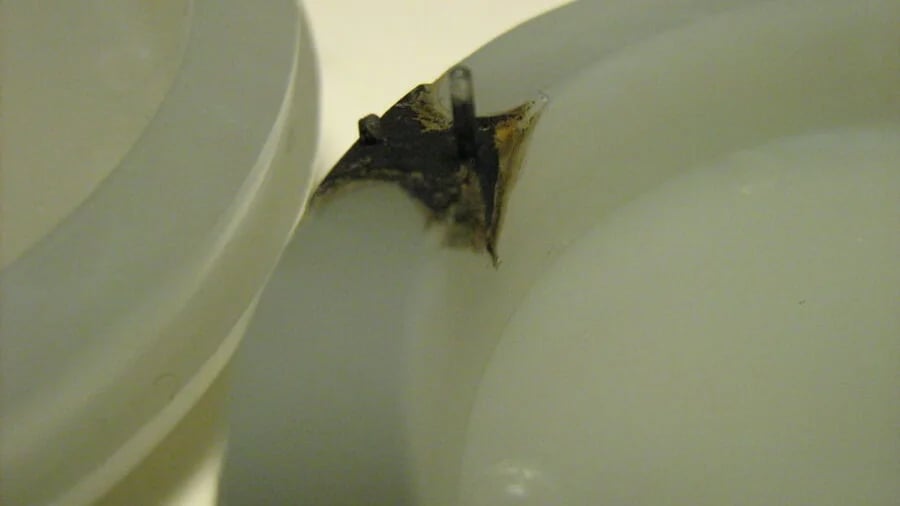
Understanding Injection Pressure’s Role
In my early industry days, I faced spray marks for the first time. This happened during a project for luxury cosmetic packaging. These snake-like marks on product surfaces were confusing and frustrating. What I discovered then and what remains true today is the crucial role of injection pressure9 in this process.
When pressure is too high, it forces the plastic melt into the mold cavity too strongly, creating irregular patterns that result in spray marks. Imagine pouring too much water into a funnel too quickly – overflow happens. Similarly, excessive pressure pushes the melt too fast, causing visible defects on the product surface.
Impact of Injection Speed
I have personally witnessed how injection speed affects a project. In another project with complex designs for electronic housings, using an incorrect injection speed caused many defects. The quickly injected plastic melt made spray marks worse, especially on products needing a perfect finish like cosmetic bottles.
Finding the balance between pressure and speed is key. Too fast and you get turbulence; too slow and the mold might not fill properly. This balance is vital for a flawless finish.
Common Defects Linked to Pressure and Speed
Defect | Cause | Impact |
---|---|---|
Flash (Overflow) | Excessively high injection pressure leads to plastic overflow from mold parting surfaces or gaps in moving parts like sliders or ejectors. | Affects product appearance and increases trimming workload; can cause non-compliance with size requirements due to excess plastic. |
Short Shot | Insufficient injection pressure prevents complete filling of the mold cavity. | Results in incomplete products, affecting functionality and appearance, particularly in complex designs with thin-walled parts. |
Sink Mark | Low injection pressure fails to compensate for shrinkage during cooling, especially in products with uneven wall thickness. | Causes uneven product surfaces and is unacceptable for high-appearance products like automotive interiors. |
Weld Marks | Inadequate pressure results in slow melt flow; when strands merge, they may not fuse properly, leading to marks. | Reduces product strength and appearance quality; weld marks appear as lines that weaken under external forces. |
Spray Marks | High pressure and inappropriate speed cause irregular melt flow, forming snake-like patterns on surfaces. | Compromises aesthetic quality, critical for products requiring fine appearances. |
Strategies for Reducing Spray Marks
After many trials, I learned that adjusting both pressure and speed10 is crucial for reducing spray marks. Balancing these helps the plastic melt flow smoothly and minimizes bad patterns.
Also, re-examining mold design changes everything. Adding venting systems11 controls internal pressures inside the mold cavity, further reducing risks.
Maintenance is very important. Keeping equipment in great condition and checking molds regularly for wear or damage is essential. Modern monitoring tools give real-time feedback and help maintain good conditions during the molding process. This proactive approach probably prevents costly defects later.
High injection pressure causes spray marks in molding.True
Excessive pressure leads to irregular melt flow, forming spray marks.
Proper mold venting eliminates all spray marks.False
While venting helps, it doesn't fully prevent spray marks alone.
Conclusion
Improper injection pressure in molding leads to defects like flash, short shots, sink marks, weld marks, and spray marks, affecting product appearance and functionality.
-
Effective cooling techniques minimize defects like sink marks by managing material shrinkage efficiently. ↩
-
Learning how to adjust injection parameters helps prevent defects like short shots by optimizing machine settings. ↩
-
Explore how automotive interiors demand high aesthetic standards, where sink marks are unacceptable. ↩
-
Learn about the design principles that minimize defects in electronic housings. ↩
-
Discover industry best practices that enhance product quality and reduce defects. ↩
-
This link provides an in-depth explanation of how weld marks form during plastic injection molding. ↩
-
Discover how weld marks can compromise the strength and durability of plastic products. ↩
-
Gain insights into methods that manufacturers can employ to minimize weld marks. ↩
-
This link provides detailed insights into how injection pressure affects molding quality and defect formation. ↩
-
Exploring this link reveals how injection speed contributes to achieving desired molding results. ↩
-
This resource explains how venting systems reduce defects by controlling internal pressures during molding. ↩