I recall when a plastic item broke because it shrank too much. It was a big surprise.
Too much shrinking in plastic items often causes internal flaws, lower density and misshapen forms. These issues reduce the strength and effectiveness of the products.
My early experience was tough, but it taught me valuable lessons. Shrinkage alters plastic strength. Learning about these changes is important to create successful products. Understanding is vital. Shrinkage affects your design. Let’s explore how this happens and discover ways to reduce these problems.
Excessive shrinkage increases porosity in plastics.True
Shrinkage creates gaps in the material, raising porosity levels.
Warping from shrinkage enhances plastic's tensile strength.False
Warping distorts shape, reducing tensile strength and performance.
Why does excessive shrinkage occur in plastics?
Have you ever felt annoyed when a plastic item did not last as long as you thought it would?
Too much shrinkage in plastics often comes from flaws inside, lower density and bending out of shape. These problems really weaken the material. Weakness often leads to performance failures in real-world uses.
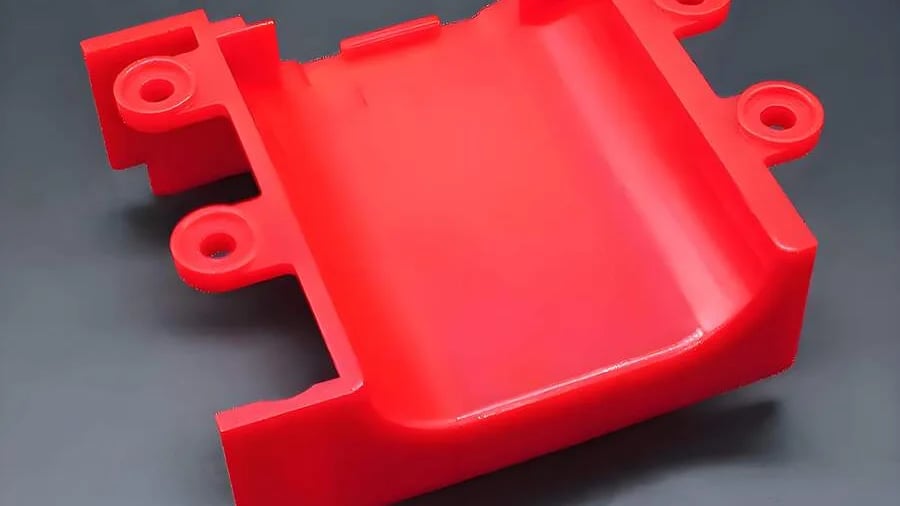
Internal Structural Defects and Reduced Strength
I recall the first time I faced a big issue with plastic shrinking. It happened during a project where we created parts for cars. The plastic shrank too much, leading to tiny internal holes that messed up the material. Think of these holes as small weak points. When force was applied, stress didn’t spread out evenly and cracks appeared around these areas. The decrease in tensile strength was very frustrating – it dropped by as much as half! It’s similar to using a phone with a cracked screen; it wasn’t reliable.
Factor | Impact on Plastic |
---|---|
Pores | Stress concentration, crack formation |
Defects | Reduced tensile strength |
Structural parts1 with high strength requirements, like automotive components, are especially vulnerable.
Reduced Density and Strength
I also learned the hard way how shrinkage impacted plastic density. Lower density means the material is not packed tight, weakening its structure. This was especially clear in nylon products I worked with. Normally, nylon’s strength comes from having good crystallinity, but shrinkage dropped it from 30-40% to just 20-30%. It’s like baking a cake with less flour; it doesn’t rise well.
- Normal Crystallinity: 30% – 40%
- Shrinkage-Induced Crystallinity: 20% – 30%
Nylon (PA) plastic2 products often suffer from this issue.
Warping Deformation and Strength Loss
Warping is another tricky problem. I spent many hours in design meetings to solve how this issue changes the shape of plastic parts. Imagine trying to fit a bent puzzle piece; it doesn’t fit right. This change adds extra bending and twisting, making parts more likely to break during use or joining.
- Effects of Warping
- Uneven stress distribution
- Increased chance of damage in some areas
- Trouble during assembly
Consider how warping deformation3 impacts design and assembly processes.
These lessons have been really important in my design work. With these insights, we have greatly lowered shrinkage issues, helping our products reach the high quality they are meant to have.
Internal defects lead to plastic shrinkage.True
Internal defects create pores, causing stress concentration and cracks.
Warping improves plastic strength.False
Warping causes uneven stress, weakening the material's performance.
Why Does Shrinkage Cause Structural Defects in Plastics?
People often ask why some plastic pieces don’t last as they should. Shrinkage could be the hidden reason behind this problem. Sneaky shrinkage.
Shrinkage creates small pores inside materials. Materials lose density. Stress builds up in specific areas. The shape of the structure can change. Structural strength might decrease. Structural integrity reduces.
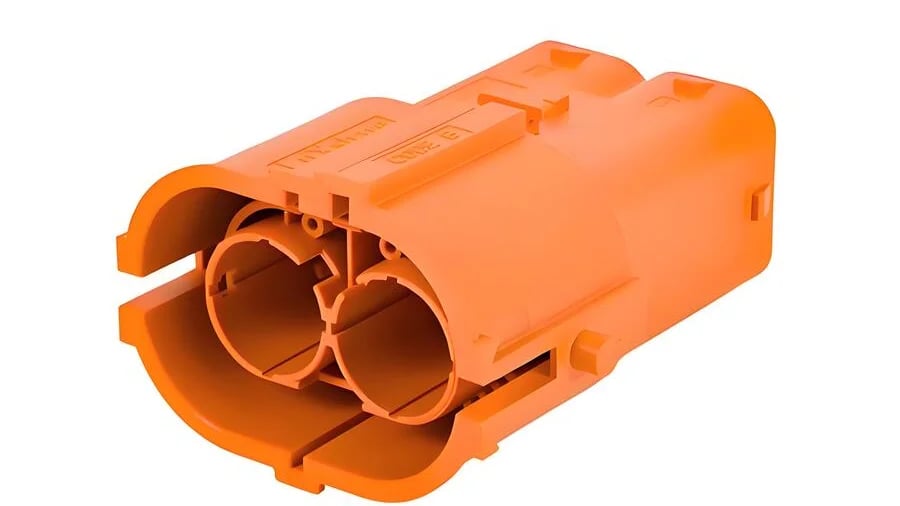
Internal Structural Problems and Less Strength
Excessive shrinkage creates pores within plastic products, disrupting material continuity. These pores hinder stress transmission, leading to stress concentration and potential cracking.
Think of this: An engineer designs a smooth, fast plastic piece for a car. But shrinkage happens and leaves tiny holes that mess up how the material handles pressure. When tension hits, these holes attract stress, causing cracks and reducing tensile strength by a huge 30% to 50%. This is a big problem for designers.
For instance, automotive parts subject to tensile forces may experience a reduction in tensile strength4 by 30% – 50% due to shrinkage.
Component | Normal Tensile Strength | Reduced Tensile Strength |
---|---|---|
Automotive Part | 1000 MPa | 500-700 MPa |
Lower Density and Less Strength
Shrinkage decreases a material’s density, weakening molecular interactions. This reduction affects the crystallinity of crystalline plastics like nylon. A typical nylon product may see its crystallinity drop from 30%-40% to 20%-30%, reducing hardness and strength.
Imagine the detailed molecular movement in plastics like nylon. Too much shrinkage upsets this balance, dropping crystallinity from a solid 30%-40% to a weak 20%-30%. This means weaker products that do not work well.
Material | Normal Crystallinity | Reduced Crystallinity |
---|---|---|
Nylon | 30%-40% | 20%-30% |
This change impacts the performance of components intended for mechanical use.
Warping and Strength Loss
Warping caused by excessive shrinkage alters a product’s shape, complicating stress distribution. For example, a warped flat plastic product may experience uneven stress when pressure is applied.
Warping is another issue and a big design headache. A flat plastic piece that bends under pressure is very problematic. It is not just ugly; it is dangerous. Uneven stress makes these pieces easy to damage and misalign during assembly.
Explore how warping deformation5 affects product assembly and its impact on structural strength.
Understanding these defects helps in designing products that meet load-bearing requirements and ensures structural reliability. Knowing these problems helps in creating designs that are not only attractive but also durable. By mitigating shrinkage during manufacturing, designers can enhance product durability and functionality.
Shrinkage causes pores in plastic products.True
Shrinkage leads to pore formation, disrupting material continuity.
Nylon's crystallinity increases with shrinkage.False
Shrinkage reduces nylon's crystallinity from 30%-40% to 20%-30%.
How Does Reduced Density Impact Plastic Strength?
Do you ever think about how the thickness of plastic affects its durability? Let’s explore a realm where even the tiniest holes count.
When plastic density decreases, its strength decreases due to more tiny holes, weaker connections and possible shape changes. This mix lowers the ability to stretch and harms the overall structure. Strength weakens. Overall stability suffers.
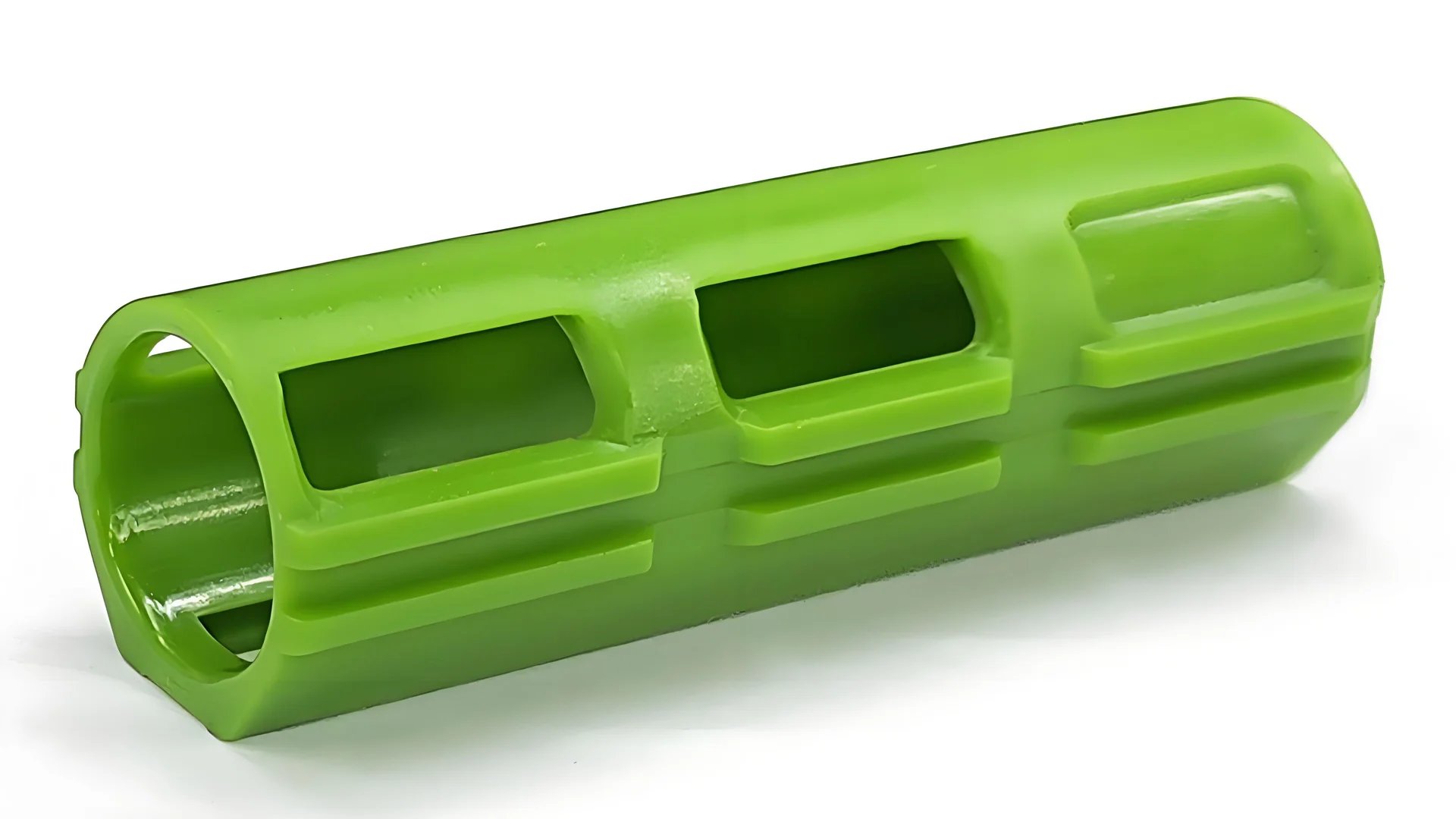
Understanding Reduced Density in Plastics
Reduced density in plastics often results from excessive shrinkage6. This phenomenon increases internal porosity, leading to structural defects. Remember stretching a rubber band until it breaks suddenly? That’s what happens inside plastic when density drops. Tiny pores form, disrupting the material’s structure. Like my work with car parts, these flaws disrupt stress flow, leading to cracks under pressure. Building on shaky ground results in weakness. These small defects can cut strength by half, especially in high-strength components like automotive parts.
Molecular Interactions and Crystallinity
Lower density affects molecular bonds, like dancers out of sync. In crystalline plastics like nylon (PA), crystallinity may fall from 40% to 30%, weakening the product. Losing the backbone in your shoes means less support. Problems arise as this shift impacts hardness and strength.
Plastic Type | Normal Crystallinity | Reduced Crystallinity |
---|---|---|
Nylon (PA) | 30% – 40% | 20% – 30% |
Discover more about crystalline structure impacts7.
Warping and Deformation Concerns
Imagine solving a puzzle but one piece is warped. Shrinking does that to plastic, creating uneven stress. Excessive shrinkage leads to warping, affecting plastic shape and introducing complex stress factors during use. In my work on electronic casings, warped surfaces complicate assembly.
When flat products warp, bending and torsion stresses arise, causing uneven stress distribution. This deformation not only reduces overall strength but also affects assembly with other components.
Check how warping affects assembly8 for more details.
These challenges reveal that reduced density isn’t just a technical issue; it’s a vital piece affecting plastic product quality.
Reduced density increases porosity in plastics.True
Reduced density leads to more internal pores, weakening structure.
Nylon crystallinity increases with lower density.False
Lower density decreases crystallinity, reducing mechanical properties.
How Does Warping Deformation Affect Product Performance?
Ever tried putting something together and found that nothing fits properly? Warping in plastic parts might be to blame. This hidden troublemaker ruins your efforts.
Warping deformation alters the shape and stress in plastic products a lot. Strength decreases and performance suffers. This change complicates assembly. Products may fail under load. Precise design and accurate manufacturing become very important. Perfect design and manufacturing are really essential.
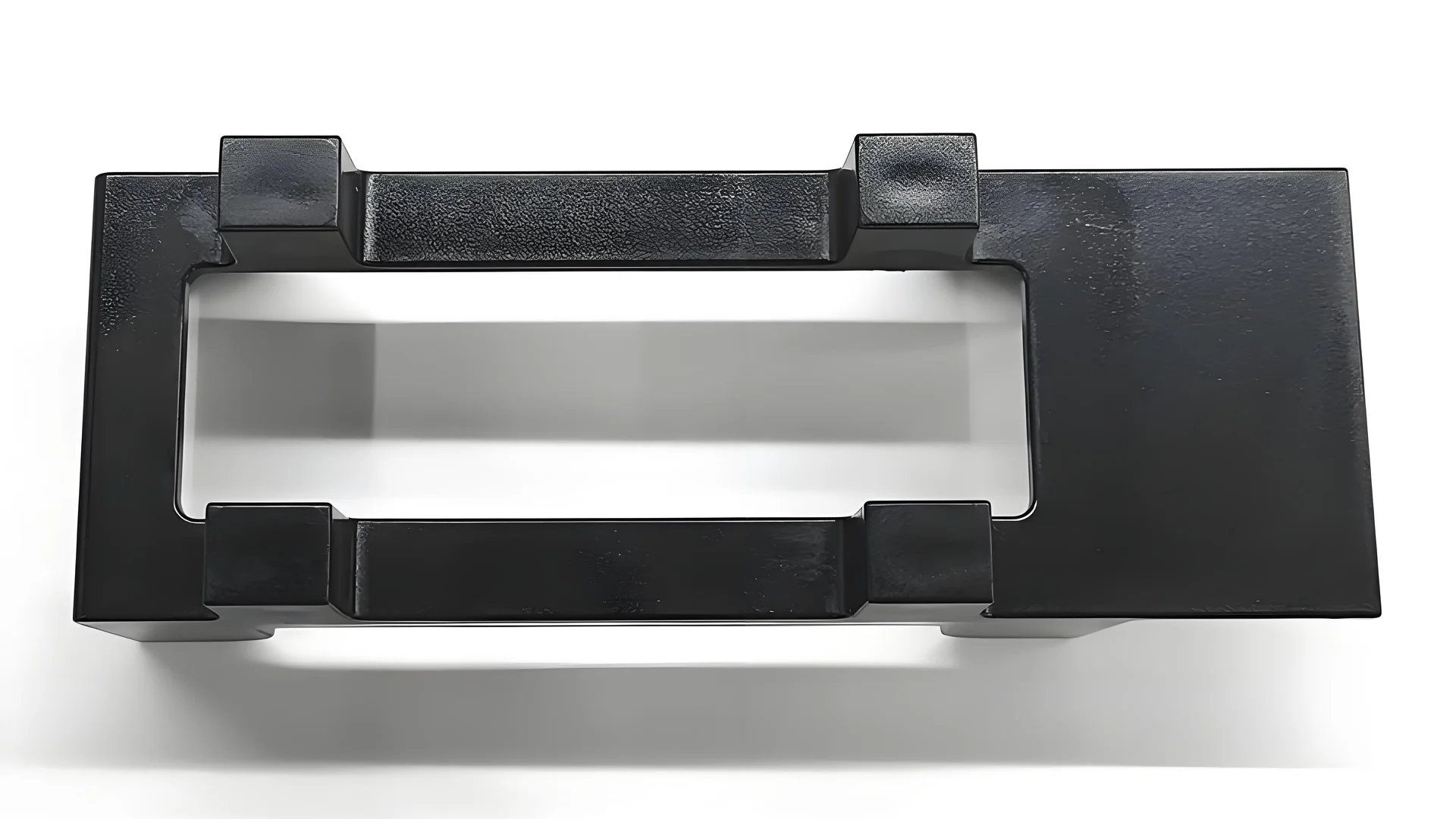
Understanding Warping Deformation
Think of spending hours crafting the perfect part, only to find it twisted and oddly shaped. Warping deformation occurs during the cooling phase of injection molding9. Uneven shrinkage changes the product’s shape. It messes with how things fit together and affects mechanical properties.
Impact on Mechanical Properties
Internal Structural Defects: I recall facing warping issues with automotive parts we worked on. The defects inside concentrated stress in the wrong spots. Cracks appeared when pressure was applied. Strength dropped by 50%. This drop was significant, far below what load-bearing parts needed.
Density and Strength: Uneven shrinkage doesn’t just change shape; it reduces product density. Crystalline plastics like nylon experience reduced crystallinity from 30%-40% to 20%-30%. Hardness and strength suffer greatly.
Product Type | Normal Crystallinity | Reduced Crystallinity |
---|---|---|
Nylon (PA) | 30%-40% | 20%-30% |
Effects on Product Assembly
Piecing together warped parts was exhausting. It felt like forcing a square peg into a round hole. Misalignment stresses components through bending and twisting. Uneven stress increases the likelihood of damage, making breaking more possible.
Complications in Design and Manufacturing
Design is not just about looks; functions under pressure matter too. Predicting warping is critical for reliability. Advanced CAD software10 now predicts these effects, helping solve issues before production even begins.
Warping affects not only appearance but also how well products work and last. Engineers consider material choice, processing details, and molding techniques11 to lower risks. Each decision is crucial as it probably determines the final product’s success or failure.
Warping reduces nylon crystallinity by 10%-20%.True
Warping decreases crystallinity in nylon from 30%-40% to 20%-30%.
CAD software cannot predict warping effects.False
Advanced CAD software can simulate and predict warping effects.
Conclusion
Excessive shrinkage in plastics leads to internal defects, reduced density, and warping, significantly weakening product strength and performance, especially in high-stress applications like automotive components.
-
Discover how internal defects can lead to decreased tensile strength, which is crucial for understanding the material’s durability. ↩
-
Learn about how crystallinity reduction affects the strength and hardness of nylon products. ↩
-
Explore how warping impacts stress distribution and assembly efficiency, key for ensuring product performance. ↩
-
This link explains the mechanism by which shrinkage reduces tensile strength, aiding designers in identifying potential design issues. ↩
-
Explore how warping deformation affects product assembly and performance, offering insights for optimizing design processes. ↩
-
Learn about the internal defects caused by excessive shrinkage and their impact on plastic strength. ↩
-
Understand how changes in crystallinity due to density reduction affect plastic performance. ↩
-
Explore how warping from shrinkage affects the assembly and strength of plastic products. ↩
-
Explore how warping occurs in injection molding, affecting product shape and performance. ↩
-
Discover the best CAD tools for simulating and addressing warping issues in design. ↩
-
Learn about effective molding techniques that help reduce warping in plastic products. ↩