I remember the first time I saw EDM in action—it was like watching magic unfold in a machine shop.
EDM revolutionizes injection mold manufacturing by allowing precise machining of complex shapes and hardened materials, boosting efficiency and enhancing product quality.
The real game-changer with EDM isn’t just the immediate boost in creating intricate molds. It’s the way it reshapes our entire manufacturing process. When I first experimented with EDM, it was for crafting an automotive interior mold—those complex curves were no match for traditional tools. But with EDM, I could precisely control every detail. It even handled post-quenching processing without breaking a sweat, maintaining dimensional accuracy and surface quality like a pro. For anyone in the mold-making world, exploring EDM‘s versatile applications feels less like work and more like unlocking a treasure chest of possibilities.
EDM enables precise machining of complex shapes.True
EDM allows for detailed and accurate machining of intricate designs.
EDM is ineffective on hard materials after quenching.False
EDM excels at machining hard materials, even post-quenching.
What Makes EDM Essential in Mold Manufacturing?
Diving into the world of mold manufacturing with Electrical Discharge Machining (EDM) feels like unlocking a secret toolbox. It’s all about precision and tackling those intricate designs with finesse. Let me share why EDM is such a game-changer.
EDM is crucial in mold manufacturing for its precision in cavity processing, ability to handle complex shapes, maintain dimensional accuracy, process fine structures, and ensure high-quality electrodes.
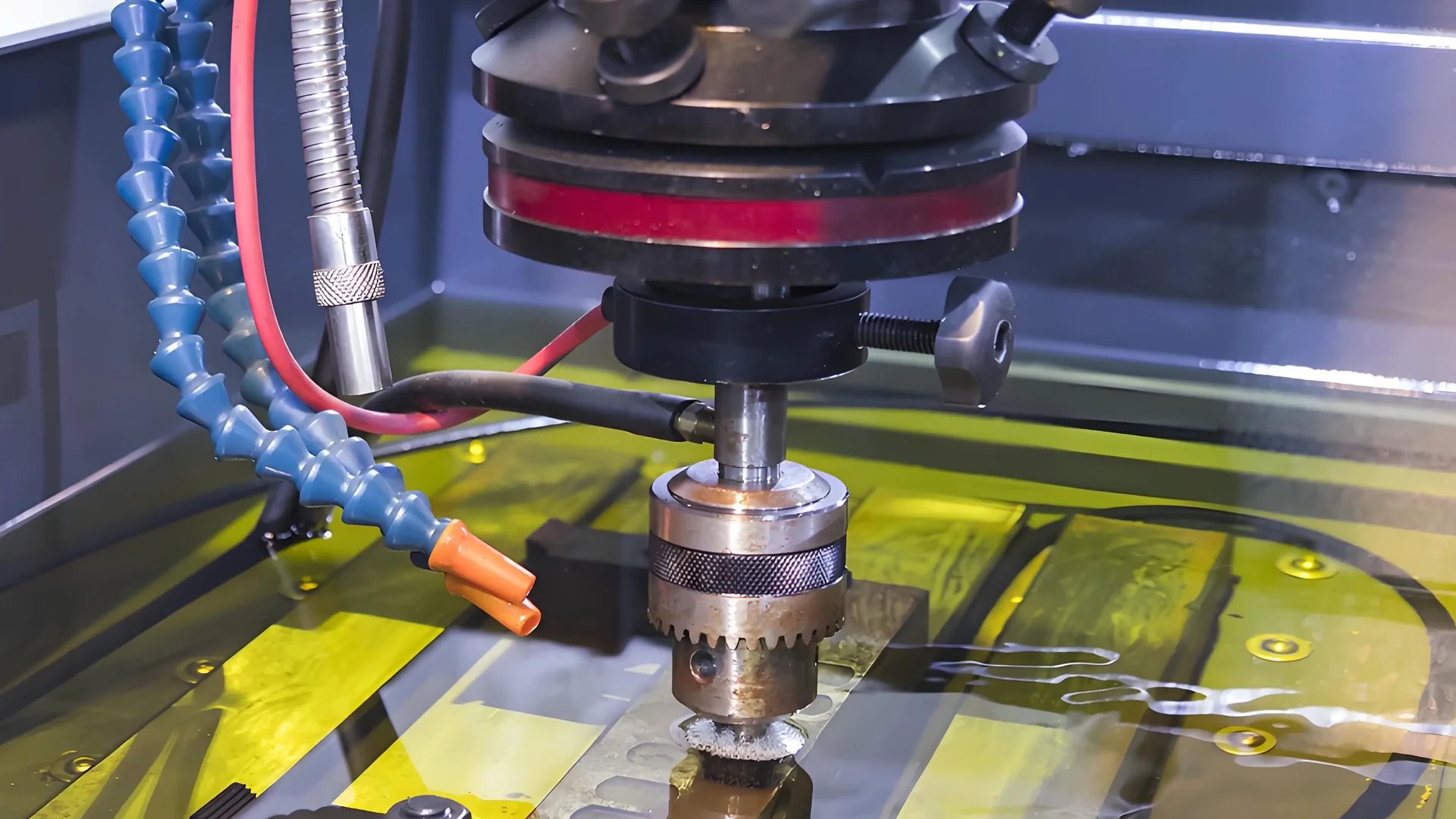
Precision in Cavity Processing
I remember the first time I saw EDM in action on a complex automotive mold. The way it effortlessly carved out intricate curves was almost mesmerizing. This is where EDM truly shines—it takes on those complex shapes that traditional methods would struggle with. Imagine being able to craft the perfect cavity that not only looks great but functions impeccably, all thanks to EDM‘s ability to etch away material precisely.
Application | Description |
---|---|
Cavity Processing | Handles complex shapes and post-quenching processing |
Post-Quenching Processing
Working with hardened materials post-quenching used to be a nightmare. I’ve seen colleagues sweat over trying to maintain dimensional accuracy using conventional tools, only to end up with deformed molds. With EDM, though, it’s like a breath of fresh air. It processes these tough materials effortlessly, preserving the mold’s integrity and ensuring superior surface quality.
Core Processing with Fine Structures
Every time I tackle a core with delicate features like ribs or tiny holes, EDM becomes my go-to tool. It’s like having a magic wand that precisely crafts these intricate details using small diameter electrodes. The result? High-quality inner surfaces for plastic products and enhanced mold reliability.
Electrode Production
Creating complex-shaped electrodes used to be daunting. With EDM, producing these electrodes becomes straightforward, ensuring they meet high precision standards. These electrodes are pivotal for further EDM operations, making them indispensable in mold manufacturing.
Ejector and Cooling Hole Processing
EDM’s ability to handle ejector holes with high positional accuracy is invaluable, especially when dealing with hard materials. Plus, its knack for processing cooling holes enhances mold cooling systems, boosting both productivity and quality in injection molding.
Explore how EDM technology1 continues to transform modern mold manufacturing through these numerous benefits, providing unmatched precision and efficiency across various applications.
EDM can process extremely hard materials post-quenching.True
EDM excels in processing hard materials, preventing deformation and maintaining accuracy.
Traditional cutting methods surpass EDM in complex shape processing.False
EDM is superior in handling complex shapes compared to traditional methods.
How Does EDM Enhance Cavity Processing for Complex Shapes?
Diving into the world of Electrical Discharge Machining (EDM) felt like opening a door to endless possibilities for crafting complex shapes with unmatched precision.
EDM enhances cavity processing in complex shapes by using controlled electrical discharges to etch materials, effectively handling varying hardness and intricate designs, ideal for challenging post-quenching scenarios.
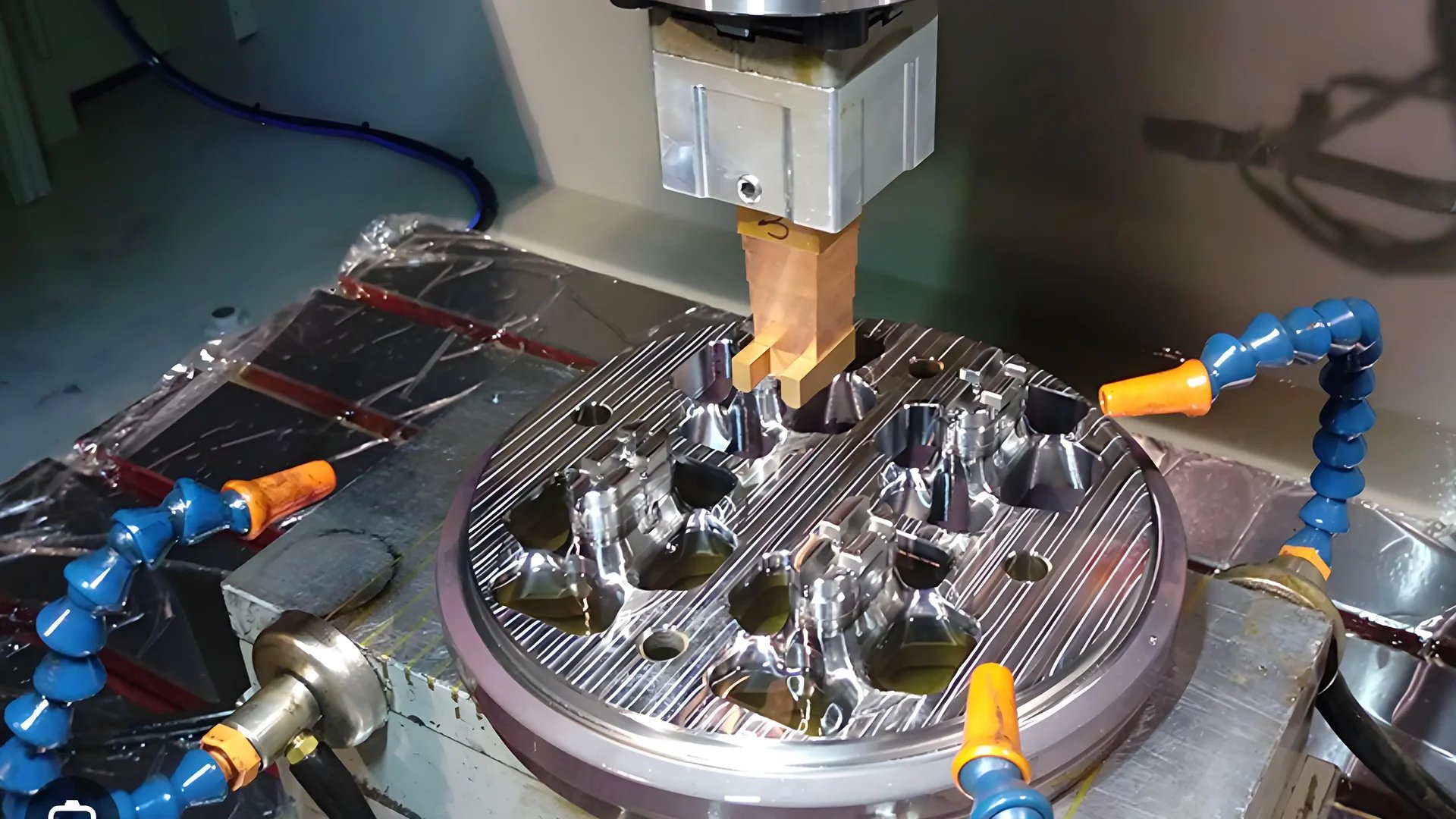
The Role of EDM in Manufacturing Complex Shapes
Imagine staring at a blueprint of an automotive interior with its intricate curves or an electronic product mold dotted with fine textures. It used to seem like an insurmountable challenge. Traditional cutting methods just couldn’t cut it (pun intended) when it came to precision and dealing with hard materials. That’s where EDM steps in, like a trusty sidekick in my design toolkit. By precisely controlling the electrode shape and discharge settings, it etches away at tough materials like mold steel, creating cavities that perfectly mirror the electrode’s shape. This magic trick ensures the product not only looks right but functions impeccably.
Traditional Methods | EDM |
---|---|
Limited by material hardness | Not constrained by material hardness |
Difficult for intricate details | Ideal for fine textures and complex curves |
EDM‘s Advantage in Post-Quenching Processing
When I first encountered post-quenching challenges, I felt like I was wrestling with a bear. The mold cavities would become incredibly hard, and conventional tools would often fall short, leading to deformation or heat treatment woes. EDM, however, tackles these issues head-on. It handles post-quenching processing with ease, preserving dimensional accuracy and surface quality without breaking a sweat. When working with quenched mold steel, EDM ensures the cavities remain true to their intended dimensions—crucial for the integrity of injection molds.
Precision and Flexibility
Beyond handling material hardness, EDM is my go-to for precise processing2 of intricate structures within mold cores. It’s like having a fine-tipped brush for an artist, allowing me to create small holes, grooves, or ribs that traditional tools would struggle with. Smaller electrodes come into play here, achieving the high precision necessary for injection molding’s demanding standards.
EDM also shines when producing unique shapes that align with design specs. Molds with asymmetric shapes or special curves benefit immensely from EDM‘s ability to craft electrodes to exact specifications.
Electrode Production for Complex Shapes
Crafting complex-shaped electrodes is another area where EDM truly excels. In parts of a mold that resist direct machining, EDM steps in to produce electrodes with intricate curved surfaces or fine features. This process guarantees both shape and dimensional accuracy, ensuring high-quality tool electrodes are ready for subsequent EDM operations.
In essence, while this isn’t the whole story, EDM offers significant advantages over traditional methods for processing complex shapes. It ensures that molds meet stringent design requirements essential for modern manufacturing while maintaining efficiency and precision.
EDM is limited by material hardness in processing.False
EDM is not constrained by material hardness, unlike traditional methods.
EDM maintains dimensional accuracy post-quenching.True
EDM effectively processes quenched materials without deformation, preserving dimensions.
How Does EDM Enhance Core Processing Precision?
Remember the first time you saw a magic trick and thought, "How did they do that?" That’s what EDM feels like in the world of machining.
EDM improves core processing precision by shaping intricate and fine structures accurately, even on hardened materials, enhancing both dimensional accuracy and surface quality.
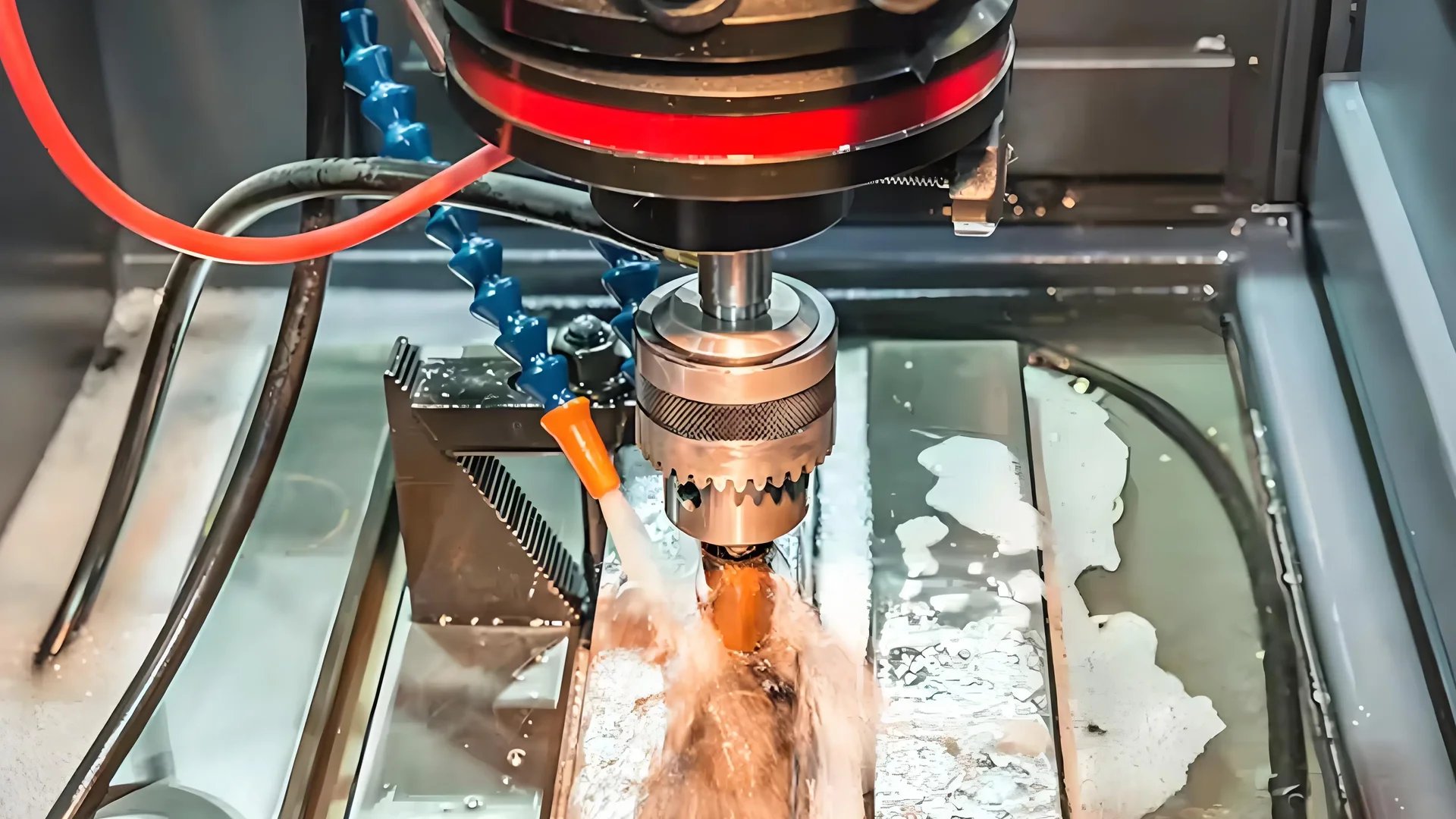
When I first encountered Electrical Discharge Machining (EDM) in my work, it was like finding the secret ingredient to my favorite dish. Suddenly, those intricate designs that seemed impossible with traditional tools were within reach.
Advantages of EDM in Core Processing
Processing Fine Structures
I remember wrestling with the idea of how to create these impossibly tiny grooves and ribs. It was like trying to sculpt a masterpiece with a butter knife. But then came EDM, which felt like swapping that butter knife for a precision scalpel. With EDM, crafting those tiny details becomes not just possible but almost effortless. It’s like when you finally find the right tool for assembling that tricky piece of IKEA furniture.
Feature | Traditional Methods | EDM |
---|---|---|
Fine Structure | Limited precision | High precision |
Learn more about manufacturing quality3.
Handling Hardened Materials
Think of traditional machining as trying to carve a statue out of diamond with a chisel. It just doesn’t work well. But EDM? It’s like having a laser that effortlessly shapes even the hardest materials post-quenching. I’ve seen how it prevents deformation, maintaining the perfect shape and size – a real game-changer for maintaining heat treatment efficacy.
Special-Shaped Structure Processing
Sometimes I look at a new design and think, "How on earth am I going to make that?" That’s where EDM‘s ability to handle special-shaped structures shines. It’s like being able to mold clay into any shape you can imagine, only you’re working with metal instead. The precision it offers for asymmetrical designs is unmatched.
Explore more about EDM capabilities4 and its applications in different industries.
Electrode Processing
Creating electrodes for those challenging mold parts used to be daunting. But with EDM, it’s like having a personal assistant who not only understands your needs but also anticipates them. I find it incredibly satisfying to see those intricate surfaces come to life with such precision.
- Corner Cleaning: Achieving sharp internal angles is no longer a limitation but an expectation. EDM surpasses conventional milling tools, bringing designs to life with crisp, clean edges.
Discover how EDM electrode production5 elevates mold manufacturing capabilities.
Small Hole Processing
I remember the frustration of trying to ensure every ejector hole was perfect, like threading a needle in low light. EDM wire cutting changed everything for me. Now, it’s like having an advanced sewing machine that stitches every detail with precision.
Hole Type | Requirement | EDM Advantage |
---|---|---|
Ejector Holes | High precision | Accurate dimension control |
Beveled Ejector Holes | Inclination accuracy | Improved fit and movement |
Learn how EDM wire cutting6 improves efficiency in mold production.
By embracing these capabilities, I’ve seen firsthand how EDM significantly boosts precision in core processing, tackling challenges traditional methods couldn’t handle. It’s this kind of versatility and precision that makes EDM not just a tool but an essential part of modern manufacturing.
EDM ensures no tool wear during machining.True
EDM uses electrical discharges, not physical contact, preventing tool wear.
Traditional methods handle hardened materials better than EDM.False
Traditional methods struggle with hardness; EDM excels in processing quenched materials.
Why Is Electrode Processing Critical in EDM Techniques?
When I first delved into EDM, I was amazed at how electrode processing could transform complex ideas into reality. It’s the heart of precision machining that engineers dream of.
Electrode processing is essential in EDM techniques for shaping electrodes accurately, enabling the precise etching of complex materials and creation of detailed molds and cavities.
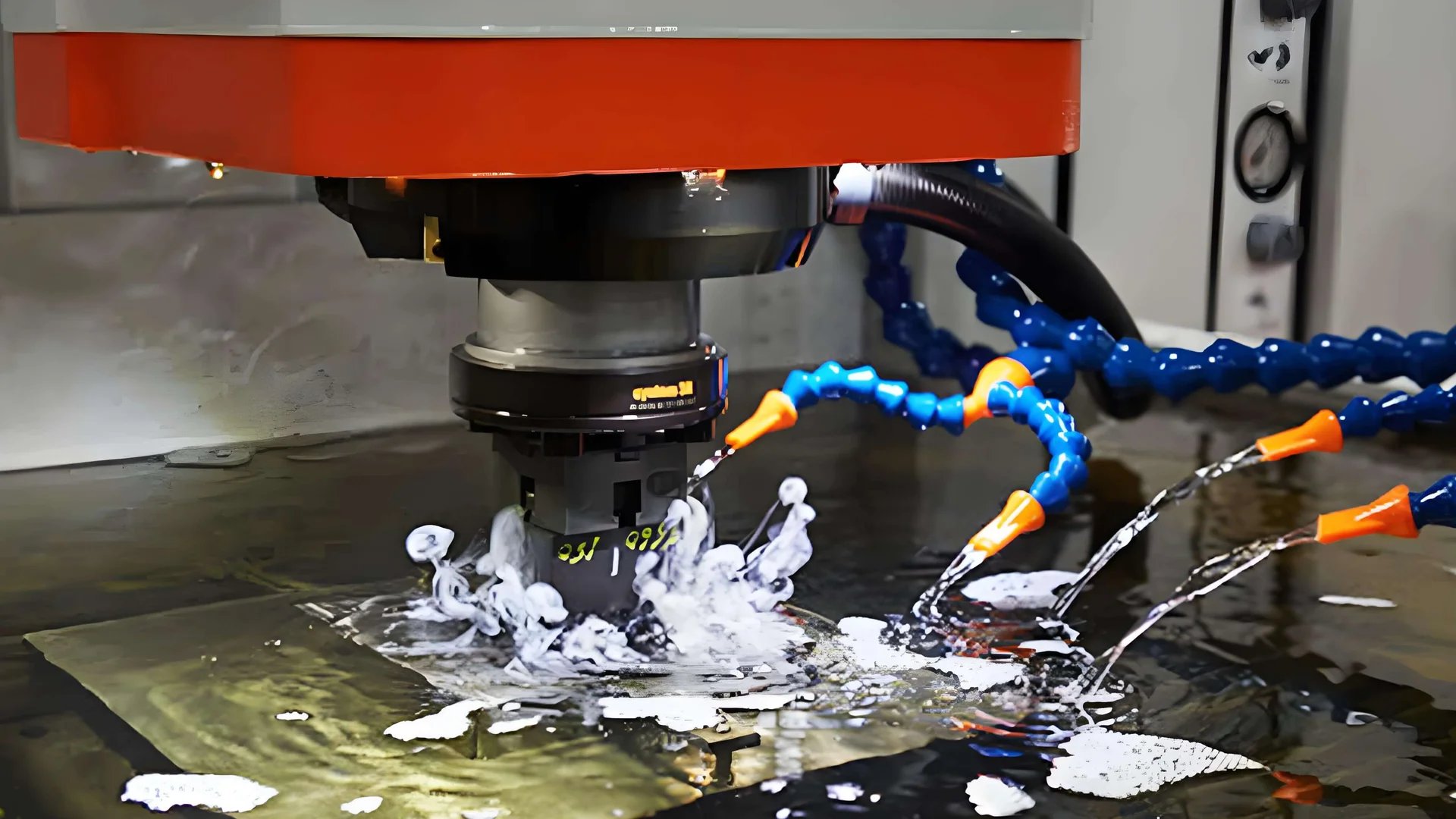
The Role of Electrode Processing in EDM
Reflecting on my early days in mold design, I recall the awe I felt witnessing electrodes in action during an EDM process. These aren’t just tools; they’re the sculptors of material through precise electrical discharges. The intricacy and finesse of these electrodes7 dictate the final product’s quality. For instance, creating those sleek automotive interiors or delicate electronic shells wouldn’t be feasible without EDM‘s touch. It’s akin to an artist carving out a masterpiece where traditional methods fall short.
Complex Electrode Production
I remember a particular project where traditional tools couldn’t capture the complexity needed for an automotive interior mold. Using EDM, we crafted electrodes with such precision that every curve and detail was spot-on. Techniques like wire cutting allowed us to achieve these intricate designs, setting a standard for quality and precision in electrode production that I strive to meet every day.
Electrode Type | Application Example |
---|---|
Complex Curved | Automotive interior molds |
Fine Features | Electronic product shells |
High Precision | Injection mold cavity and core processing |
Electrode Corner Cleaning
The challenge of achieving sharp internal angles in molds is something I’ve wrestled with multiple times. Traditional tools often fell short due to radius limitations, but with EDM, even the smallest corners could be cleaned with precision. It’s this capability that ensures every mold corner is as sharp and clean as the design demands, boosting both appearance and functionality.
Electrode Processing Impact on Core and Cavity Structures
EDM truly excels when it comes to crafting fine structures like grooves and ribs on cores. Smaller-diameter electrodes allow us to meet complex core design requirements with ease. Post-quenching treatments add another layer of complexity, but EDM isn’t fazed by hardened materials. It maintains dimensional accuracy and surface quality without compromising structural integrity.
By tweaking discharge parameters and electrode movement, I’ve learned to optimize processing for unique shapes or cross-sections. This adaptability significantly enhances injection mold performance and stability, something I’ve come to rely on heavily in my projects.
Exploring Electrode Processing Further
For those intrigued by EDM techniques8, diving into electrode processing offers invaluable insights. It underscores how essential this step is in achieving precision and quality in manufacturing processes involving tough-to-machine materials or intricate geometries.
EDM electrodes are used to remove material via electrical discharges.True
EDM uses electrodes to erode material through controlled electrical sparks.
EDM can process any material regardless of its hardness.True
EDM is not limited by material hardness, unlike traditional machining.
How Does EDM Facilitate Efficient Small Hole Processing?
Peeling back the layers of Electrical Discharge Machining (EDM) reveals a fascinating world where precision meets creativity, transforming tiny hole processing into a craft.
EDM improves small hole processing by using electrical discharges to precisely erode hard materials, ensuring accurate and high-quality machining essential for complex manufacturing.
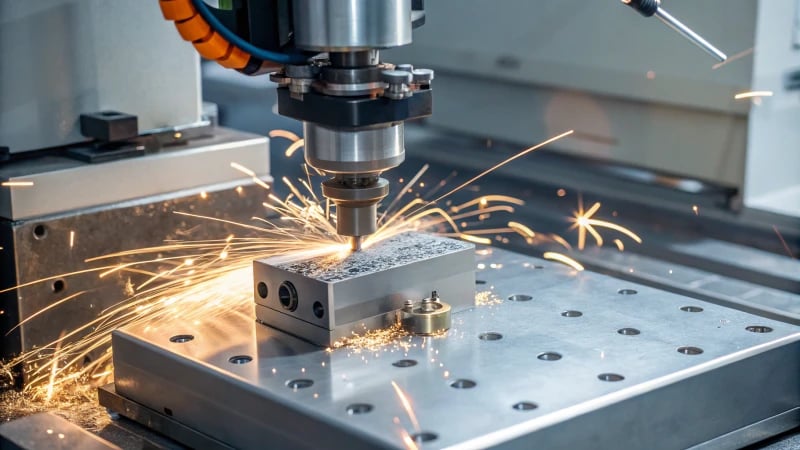
Understanding EDM and Its Role in Small Hole Processing
Electrical Discharge Machining (EDM) operates by eroding material with controlled electrical discharges between the electrode and the workpiece. This technique excels in processing hard materials where traditional methods fall short. EDM‘s unique ability to handle hard materials like mold steel is pivotal in small hole machining9. By avoiding the mechanical stresses typical of conventional techniques, EDM ensures high precision and accuracy.
The Advantages of EDM in Small Hole Processing
One of the standout benefits of EDM, in my experience, is how effortlessly it creates small holes with incredible accuracy. This is a game-changer for intricate applications—take ejector holes in injection molds, for example. These holes need to be spot-on to meet stringent specs, and EDM handles them like a pro, balancing efficiency with precision.
Example Applications:
- Ejector Hole Processing: Here, EDM shines by accurately processing multiple ejector holes simultaneously, enhancing efficiency and reducing costs.
Feature | Traditional Methods | EDM |
---|---|---|
Material Hardness Handling | Limited | Excellent |
Dimensional Accuracy | Moderate | High |
Surface Quality | Variable | Superior |
EDM‘s Role in Beveled and Cooling Holes
Beveled ejector holes present unique challenges due to their inclination and special shape requirements. With EDM wire cutting, you get pinpoint control over electrode movement—perfect for these tasks. Similarly, cooling holes that often require small diameters and deep depths benefit from EDM‘s precision, ensuring optimal cooling system function.
In summary, EDM enables engineers to overcome traditional limitations by offering solutions for complex geometries and high hardness materials. By leveraging these capabilities, manufacturers gain competitive advantages10 in precision engineering, optimizing both product quality and production efficiency. Understanding these nuances empowers designers and engineers to fully harness EDM‘s potential in their workflows.
Cavity Processing
There’s nothing quite like seeing EDM tackle the complex shapes within injection molds. Imagine crafting the intricate surfaces of a car interior mold or etching the fine textures of an electronic shell—EDM makes it all possible by etching away at materials until they mirror the electrode’s shape. After quenching, mold cavities become harder than a diamond in an ice storm; however, EDM maintains dimensional accuracy and surface quality without deformation.
Core Processing
Fine structures like tiny holes or grooves on cores demand the precision that EDM provides. I’ve often marveled at how smaller diameter electrodes create these detailed structures flawlessly. Whether dealing with special cross-sections or asymmetric shapes, EDM offers the precision needed to ensure quality and stability in injection molding.
Electrode Processing
Producing complex-shaped electrodes? It’s like having a tailor who can stitch the perfect fit every time, no matter how complex the design. Even when you need those sharp internal angles, EDM can achieve that tiny radius that other tools simply can’t manage.
EDM excels in processing hard materials like mold steel.True
EDM's electrical discharges effectively erode hard materials, unlike traditional methods.
Traditional methods offer higher dimensional accuracy than EDM.False
EDM provides higher dimensional accuracy, especially in small hole processing.
Conclusion
EDM revolutionizes injection mold manufacturing by enabling precise machining of complex shapes and hardened materials, enhancing efficiency, dimensional accuracy, and surface quality in production processes.
-
Understand the transformative effects of EDM technology on mold manufacturing processes. ↩
-
This link provides insights into how EDM achieves high precision in mold manufacturing. ↩
-
Explore how EDM’s precision benefits manufacturing quality across various industries. ↩
-
Discover the diverse applications of EDM technology in enhancing manufacturing processes. ↩
-
Learn about advanced techniques used in producing high-quality electrodes with EDM. ↩
-
Understand how EDM wire cutting enhances efficiency and accuracy in mold production. ↩
-
Explore how electrode design impacts EDM outcomes and why precision in electrode processing is crucial for machining success. ↩
-
Gain insights into how advanced EDM techniques enhance mold manufacturing, focusing on electrode processing’s role in achieving precision. ↩
-
Explore detailed insights into how EDM processes small holes efficiently, enhancing your understanding of its applications. ↩
-
Discover the competitive advantages that EDM offers in manufacturing, particularly in precision engineering applications. ↩