Imagine this: You work in the engineering field, responsible for picking the right material for plastic gears. The pressure is great.
The best plastic material for manufacturing durable gears depends on the application requirements. PEEK offers high strength and wear resistance for demanding conditions, while POM provides good abrasion resistance with easier processing. PA66 is cost-effective but requires reinforcement for high-strength needs.
PEEK excels with its strong mechanical traits and remains durable even in extreme situations, yet it is expensive. On the other hand, POM and PA66 provide cheaper options with different performance levels. Continue reading to learn how these materials perform in areas like heat stability and chemical resistance.
PEEK gears have the highest wear resistance among plastics.True
PEEK's low wear rate renders it perfect for machinery with high load and high speed.
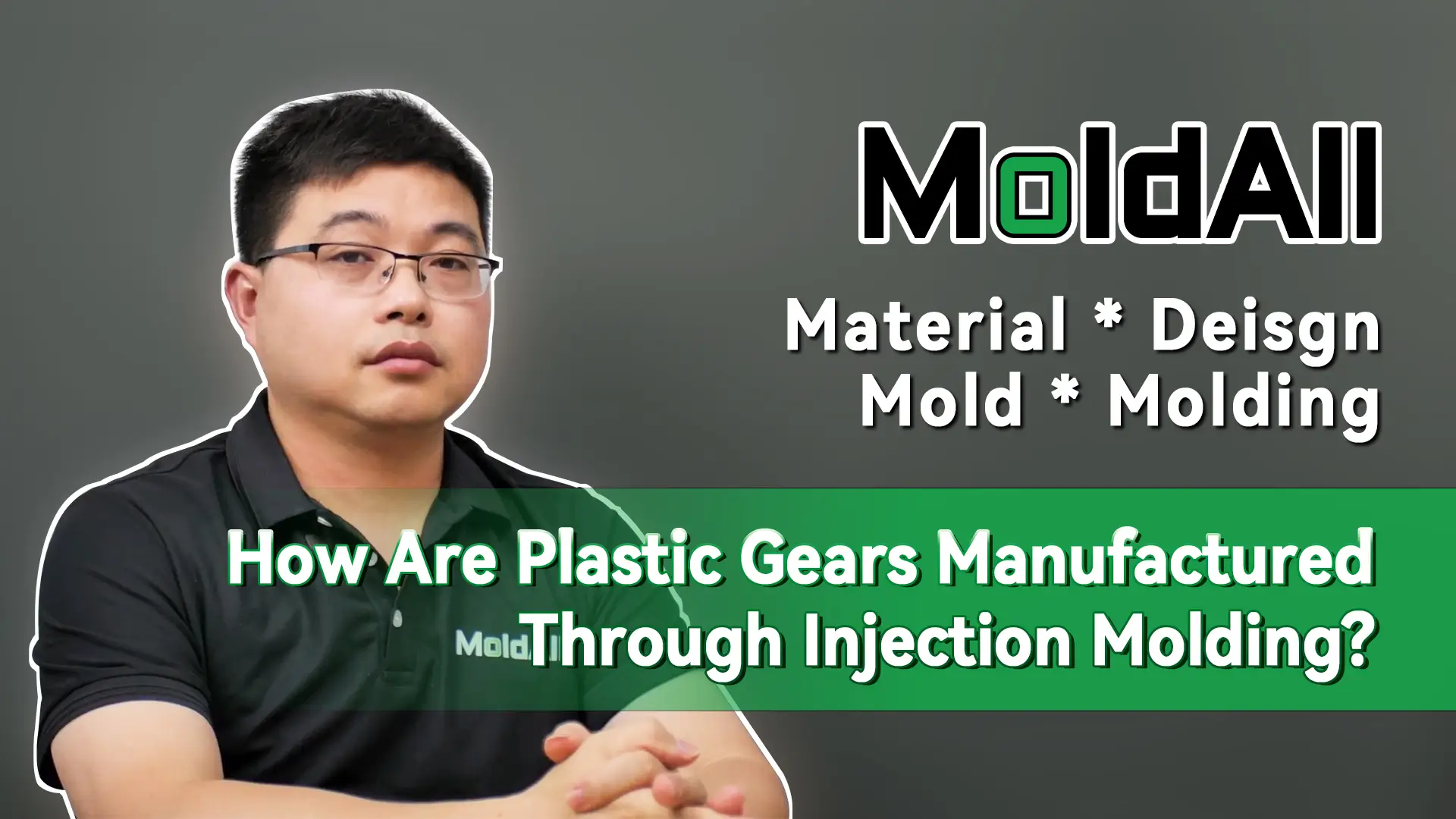
What Are the Mechanical Advantages of Different Plastics for Gears?
Study the mechanical benefits of different plastics to guide your choice in gear design.
PEEK, POM, and PA66 each offer unique mechanical benefits for gear manufacturing. PEEK excels in strength and wear resistance, ideal for high-stress environments. POM is favored for precision applications due to its dimensional stability. PA66 is cost-effective, suitable for less demanding uses when reinforced.
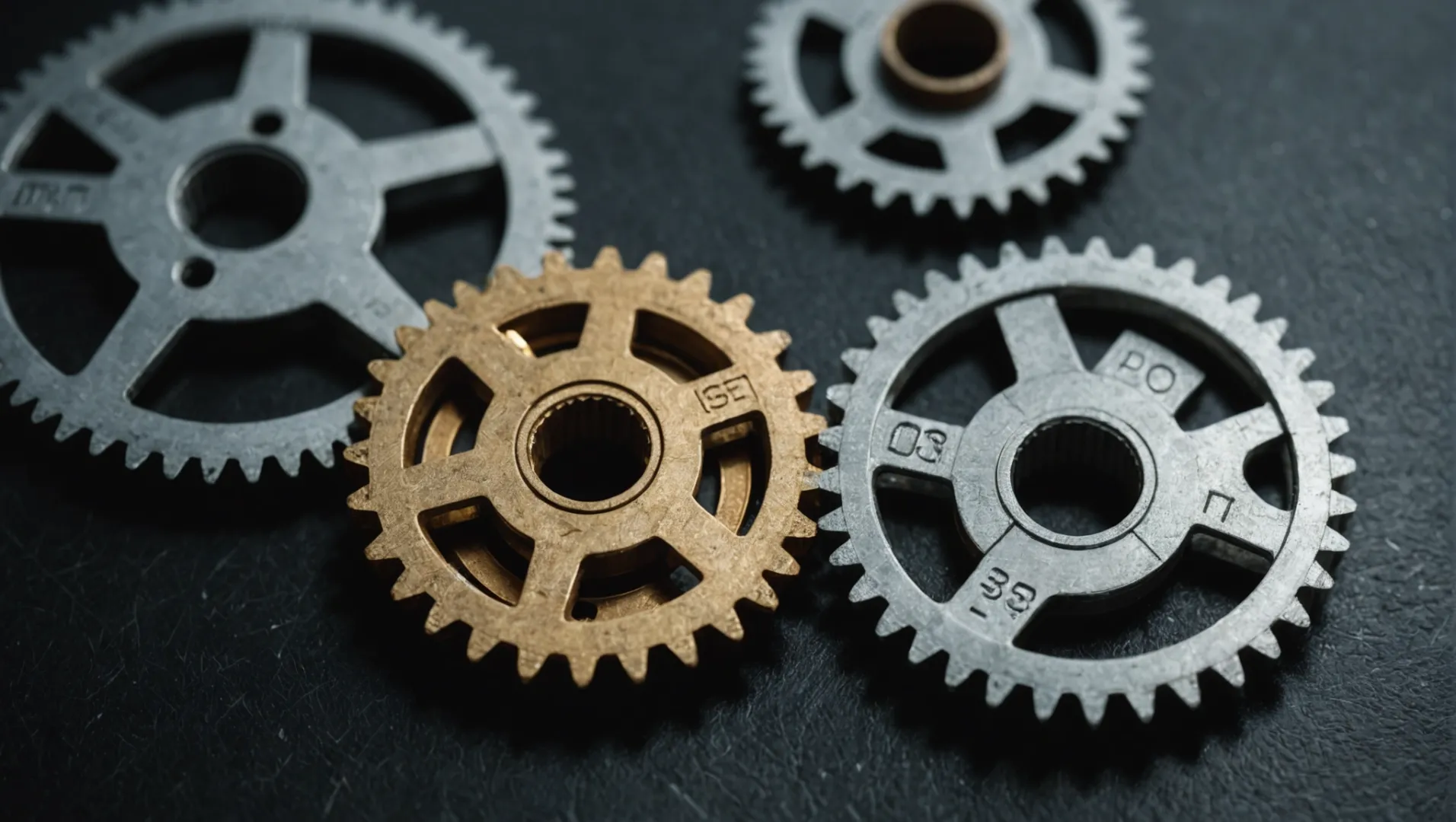
Strength and Stiffness
PEEK (Polyether Ether Ketone) is famous for its strong and stiff qualities. It is often used in top-level machinery and planes because it handles big weights and does not bend easily. It keeps working well even when very hot or under strong pressure.
POM (Polyoxymethylene) also provides strong and stiff features but is not as strong as PEEK. It fits well in tasks needing exact shapes because it does not change size much.
PA66 (Polyamide 66) is not as strong but becomes much stronger and stiffer when mixed with things like glass fibers. This makes it useful when saving money is important and extra strength is needed.
Wear Resistance
PEEK is the best among the three for resisting wear. It works well in heavy and fast systems because it wears out very little, helping gears last longer. For instance, PEEK gears often work in high-speed drive systems1.
POM resists wear well, just behind PEEK. It gives steady use in normal situations.
PA66 does not resist wear as well and often needs more fixing or changing in hard-wearing tasks.
Impact Resistance
PEEK‘s impact resistance is strong, so it handles hits without breaking. This is helpful in situations that get shocks.
PA66 also bears impacts well, especially when made tougher to soak up force and keep gears from harm.
POM does not handle impacts as well and breaks easier when hit hard.
Practical Applications Table
Property | PEEK | POM | PA66 |
---|---|---|---|
Strength & Stiffness | Very high | High | Moderate (better with fibers) |
Wear Resistance | Excellent | Good | Poor |
Impact Resistance | Good | Weak | Good (better when toughened) |
For work needing certain qualities, knowing these details is key in picking the right material. By matching these traits with work needs, makers can improve how long gears last and work. For example, aerospace tasks2 usually pick PEEK for its great work under stress and heat.
Picking the best plastic for gears involves weighing these good mechanical points with things like cost and how easy it is to process, as discussed more later on.
PEEK is ideal for high-stress gear environments.True
PEEK is strong and wears down slowly, fitting well for such situations.
PA66 has superior wear resistance compared to PEEK.False
PEEK provides greater wear resistance compared to PA66, which demands frequent upkeep.
How Do Temperature Extremes Affect Gear Performance?
Gears hold great importance in many fields. How do very high or low temperatures affect how they work?
Temperature extremes significantly impact gear performance. High temperatures can cause deformation and loss of strength, particularly in materials like PA66 and POM. Meanwhile, low temperatures can lead to brittleness, especially in POM gears. PEEK is notable for maintaining performance across temperature variations, making it ideal for extreme conditions.
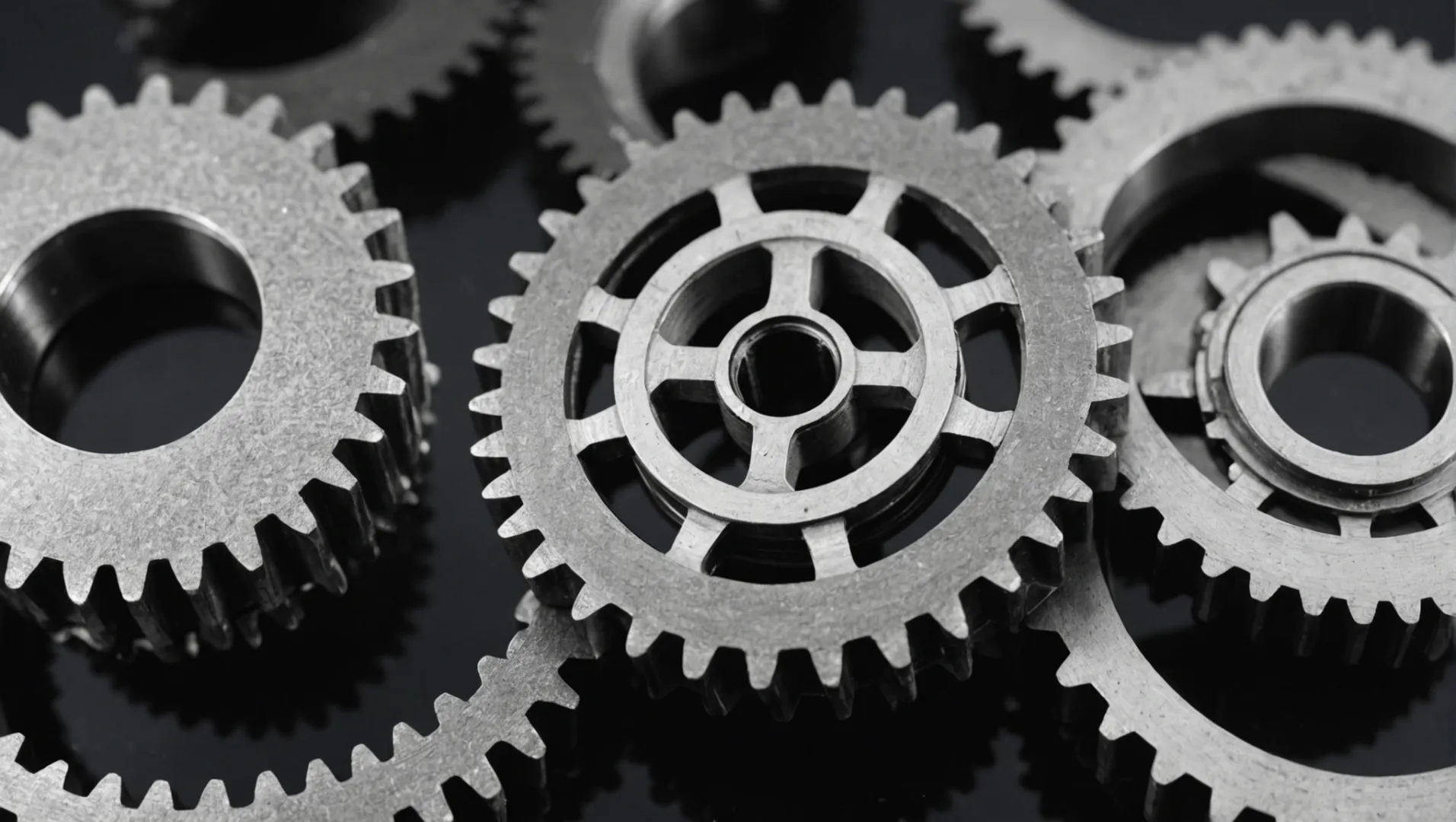
How High Heat Affects Gear Work
In places with high heat, gears made from different materials show different reactions:
- PEEK Gears: Strong against high heat, PEEK gears maintain strength and shape even at 260°C. This makes them very good for use in hot industrial machines3 and airplane parts.
- PA66 Gears: With a working temperature from 100 – 120°C, PA66 gears lose quality in high heat. This stops them from being used where the heat stays high.
- POM Gears: These soften and bend above 100°C, which means they do not work well in hot places.
Material | Working Temperature | High Heat Effects |
---|---|---|
PEEK | Up to 260°C | Keeps working well |
PA66 | 100 – 120°C | Loses quality |
POM | Below 100°C | Softens and bends |
Problems at Low Temperatures
Cold also creates problems:
- PEEK Gears: Tough and strong at temperatures down to -100°C, which helps in cold environments4.
- PA66 Gears: Usually good, but very cold can cause them to break easily.
- POM Gears: Bad in the cold; can break easily, causing problems in cold places.
Cost and Work Quality
Even though PEEK works better in very hot and cold temperatures, it costs a lot. PA66 and POM, being cheaper, need careful thought about where they are used to stop problems from heat changes. Picking the right material for gear use in places with different temperatures means thinking about cost and quality5 together.
Knowing how materials act with heat or cold helps gears stay useful and perform better for a long time.
PEEK gears maintain performance up to 260°C.True
PEEK is famous for handling very high heat well.
POM gears are ideal for high-temperature environments.False
POM becomes soft and changes shape when temperatures rise above 100°C.
What Role Does Chemical Resistance Play in Gear Longevity?
Chemical resistance matters a lot when deciding how long gears survive, especially in tough conditions.
Chemical resistance significantly impacts gear longevity by protecting against corrosive substances. Materials like PEEK offer exceptional resistance, extending gear life in chemical-laden environments. In contrast, PA66 may degrade without protective treatments.
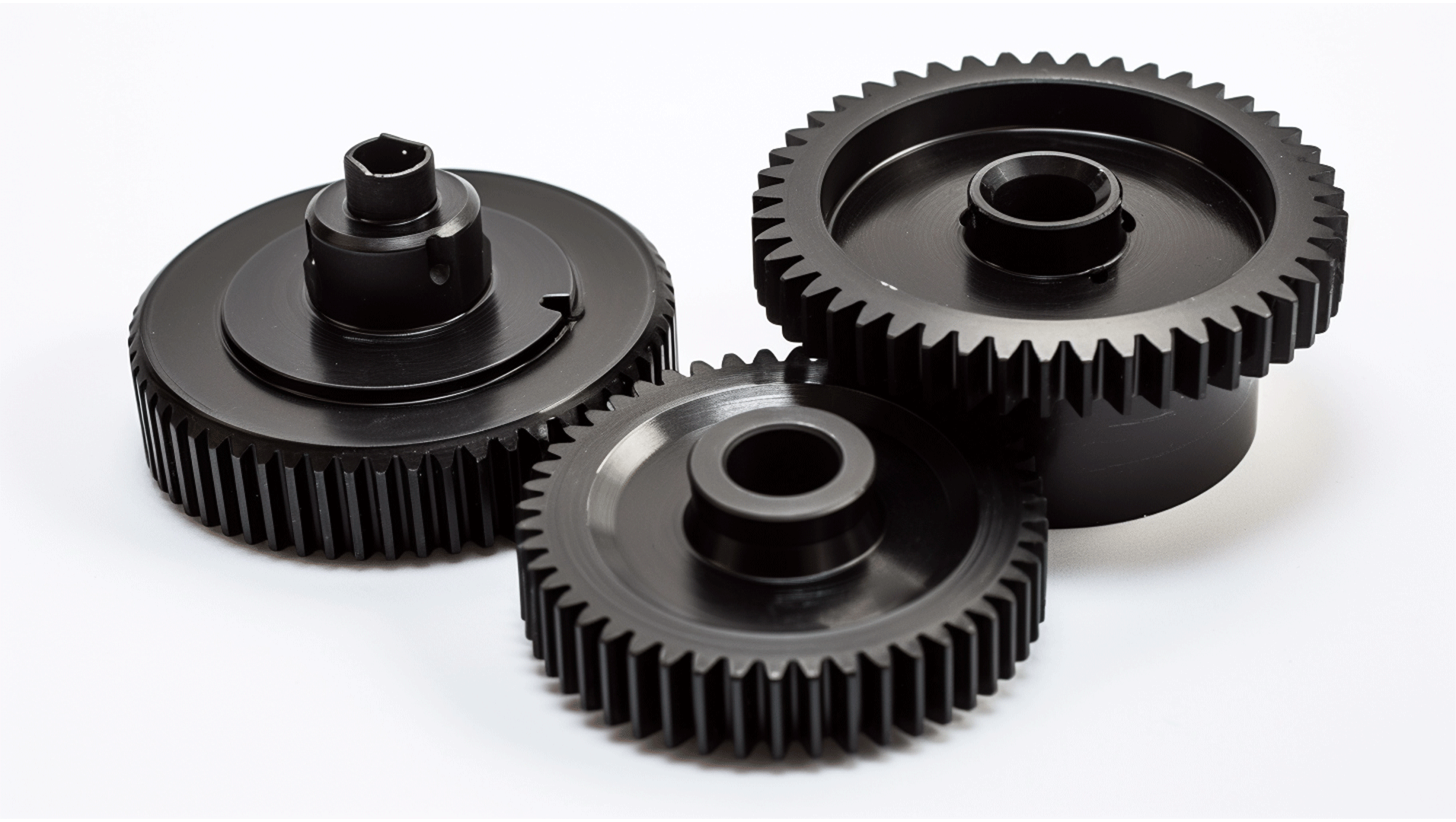
Understanding Chemical Resistance and Why It Matters
Chemical resistance means a material stays strong when near chemicals and does not break down. This trait is very important for gears used where lubricants, fuels, or other chemicals touch them. Gear life often depends on resisting these harmful substances, which could cause damage or even complete failure.
Compare Chemical Resistance in Plastics
PEEK (Polyetheretherketone) is famous for very good chemical resistance. It handles most acids, bases, and organic liquids without significant damage. PEEK works well in places where tough chemicals touch it often.
POM (Polyoxymethylene) has reasonable chemical resistance but is not as strong as PEEK. It behaves well in regular environments but might need extra shielding in very harmful settings.
PA66 (Polyamide 66) shows weak chemical resistance. Without special treatments, PA66 gears could get damaged by chemicals. Extra layers or elements might be needed to improve its performance there.
Material | Chemical Resistance | Suitable Environments |
---|---|---|
PEEK | Excellent | Tough chemical exposure |
POM | Good | Mild exposure |
PA66 | Weak | Little exposure |
Chemical Resistance and Gear Life
Gears built from materials with better chemical resistance run longer and more steadily in harsh environments. Knowing how materials interact with their work area is key in picking the right gear material.
For example, using PEEK where gears meet harmful chemicals can significantly reduce maintenance work and downtime. On the flip side, using PA66 without needed extras might mean more frequent replacements and higher running costs.
Real-Life Uses and Thoughts
In automotive or aerospace fields, where gears meet harsh chemicals and tough conditions, picking something like PEEK is probably necessary despite higher prices. But in easier tasks, POM or even strengthened PA66 might be a smarter financial choice.
So, when thinking about gear life, one must consider the chemical resistance6 aspects of materials against the specific challenges they face. This choice allows for optimal performance and long-lasting use.
PEEK has excellent chemical resistance.True
PEEK resists acids, alkalis and solvents without damage.
PA66 is ideal for harsh chemical environments.False
PA66 possesses low chemical resistance and requires protective measures.
How Do Material Costs Influence Gear Production Choices?
When selecting materials for gear production, expenses greatly influence decision-making methods.
Material costs directly influence gear production choices by affecting budget allocations and design strategies. Expensive materials like PEEK offer superior performance but limit application due to higher costs. Conversely, affordable options like PA66 can reduce expenses but may require compromises in strength and durability.
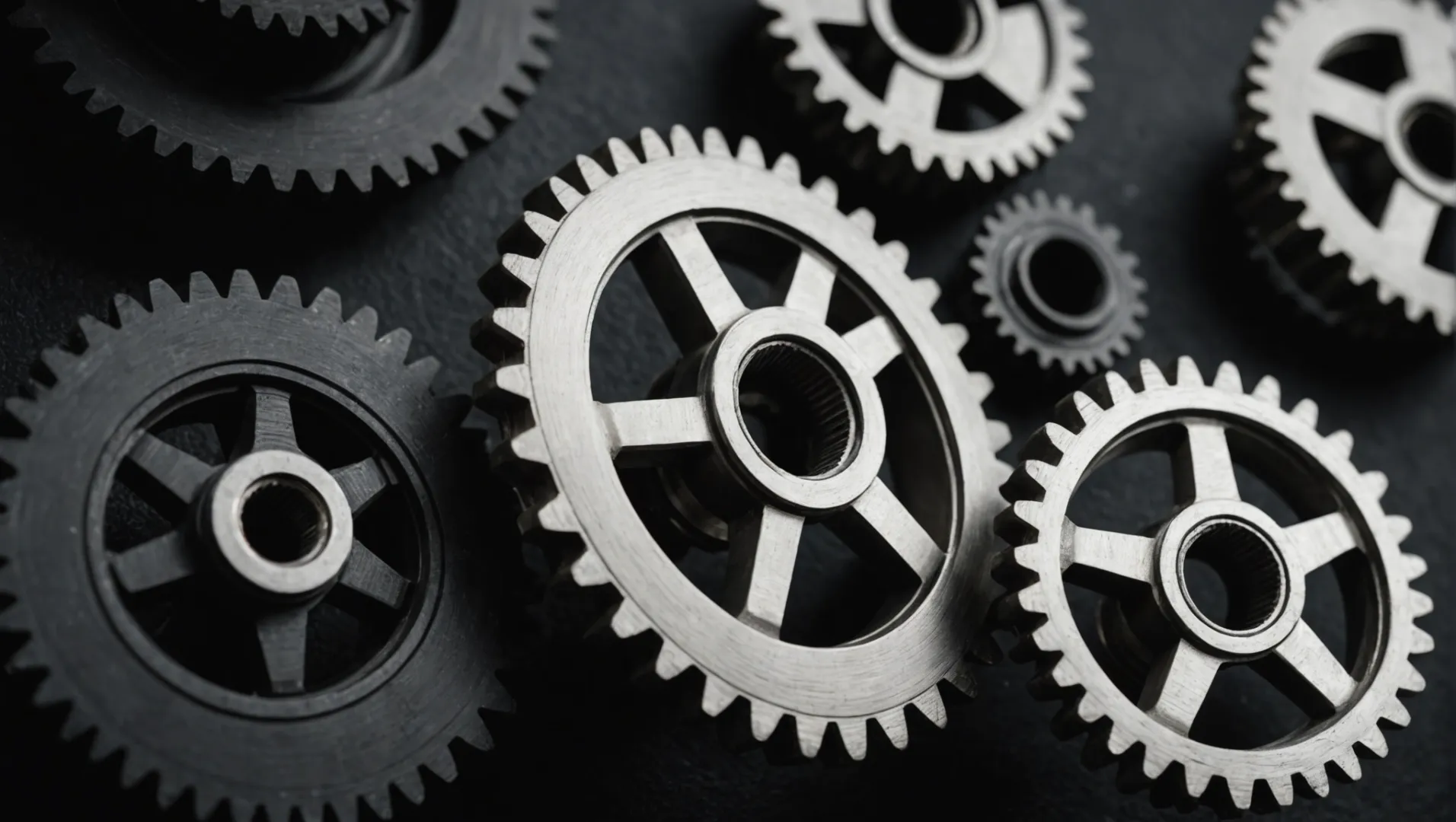
The Role of Material Cost in Gear Manufacturing
When manufacturers evaluate materials for gear production7, cost is a critical consideration that directly impacts financial planning and product design.
PEEK (Polyether ether ketone): Known for its exceptional mechanical properties, PEEK is the most expensive of the three primary plastics used in gear manufacturing. Its high cost often limits its use to high-end applications where performance under extreme conditions justifies the investment. For instance, PEEK gears are prevalent in aerospace and industrial machinery due to their ability to withstand high loads and temperatures.
POM (Polyoxymethylene): This material strikes a balance between performance and cost. It is more affordable than PEEK and offers good wear resistance and ease of processing. POM is often chosen for applications requiring moderate strength and precision, making it suitable for a wide range of commercial products.
PA66 (Polyamide 66): The least expensive of the three, PA66 is favored in situations where budget constraints are paramount. However, its lower strength and rigidity mean it might need reinforcement through additives like glass fibers, which can increase costs slightly but still remain economical compared to PEEK.
Cost-Benefit Analysis in Gear Selection
Material | Initial Cost | Processing Complexity | Application Scope |
---|---|---|---|
PEEK | High | High | High-end |
POM | Moderate | Low | Moderate |
PA66 | Low | Low | Cost-sensitive |
Selecting a material is not just about upfront costs. Processing expenses also play a significant role. PEEK, while costly, requires specialized equipment and processes, further increasing its manufacturing costs. On the other hand, both POM and PA66 offer simpler processing methods, enhancing production efficiency.
Strategic Decisions in Material Selection
Manufacturers must weigh these cost implications against performance benefits. For example, while PEEK‘s high initial outlay might seem prohibitive, its long-term durability can lead to lower maintenance costs and extended gear life, providing overall cost savings in demanding environments.
Conversely, for applications where extreme durability isn’t necessary, opting for more affordable materials like PA66 or POM can significantly reduce production costs without compromising on essential performance metrics.
In conclusion, understanding the relationship between material costs and gear production choices enables manufacturers to make informed decisions that align with both financial objectives and performance requirements.
PEEK gears are used in high-end applications.True
PEEK costs a lot but works well in tough places.
PA66 is the most expensive material for gears.False
PA66 is the cheapest, good for cost-conscious applications.
Conclusion
Finally, select the material that suits your requirements. Weigh performance against price to guarantee equipment durability and effectiveness.
-
Discover why PEEK excels in demanding high-speed drive systems.: PEEK plastic gears stand out for their superior wear resistance. Compared to metal gears, PEEK’s wear resistance is legendary for its ability to excel in harsh … ↩
-
Learn about PEEK’s pivotal role in aerospace engineering.: PEEK is optimal for aerospace applications because although it is a thermoplastic, it boasts heat resistance, little to no reaction against … ↩
-
Discover how PEEK excels in high-temperature industrial applications.: PEEK plastics exhibit excellent thermal stability with a heat deflection temperature of 160°C or 320°F. Maximum allowable service temperature for PEEK. Ketron® … ↩
-
Learn about PEEK’s capabilities in low-temperature environments.: PEEK dielectric properties are likewise especially beneficial in electrical circuitry involving low-intensity signals or output. PEEK drawn fiber can be used as … ↩
-
Explore strategies for balancing cost and performance in gear manufacturing.: This article explores the relationship between cost and quality in manufacturing, exploring their definitions, interdependence, and the trade-offs involved in … ↩
-
Understand why chemical resistance is crucial for gear longevity.: One plastic can be great at resisting the corrosion of acid but still melt when in contact with a solvent. ↩
-
Explore how material costs impact gear design and manufacturing choices.: When it comes to material-associated gear manufacturing costs, machining and gear-tooth cutting costs stand out as primary contributors. ↩