Figuring out manufacturing costs seems really difficult. Yet, it is crucial for product designers like us. Let’s explore this topic together!
To calculate the manufacturing cost of a plastic product, consider direct material and labor costs, and overhead expenses. This approach ensures accurate cost assessment and informed pricing decisions.
When I first started calculating manufacturing costs, I saw how important it was to understand every part of our products. It’s not only about numbers. It’s about the journey from raw material to finished product. Each cost part has a story. By knowing these details, we create better pricing strategies. We really make smart decisions that connect with our customers.
Direct material costs are essential in manufacturing cost calculations.True
Direct material costs significantly impact the overall manufacturing cost of plastic products, making them a critical factor in pricing strategies.
Overhead expenses are irrelevant to manufacturing cost assessments.False
Overhead expenses must be included in manufacturing cost assessments to provide a complete understanding of production costs and pricing strategies.
What Are the Key Components of Manufacturing Costs?
Do you sometimes wonder how to calculate manufacturing costs? I do, too! Knowing these costs matters a lot for planning budgets and setting prices. Let’s explore the important parts that add up to these expenses.
Manufacturing costs consist of three key components: direct material costs, direct labor costs, and manufacturing overheads, which include equipment wear and energy expenses. Each element significantly impacts overall production expenses.
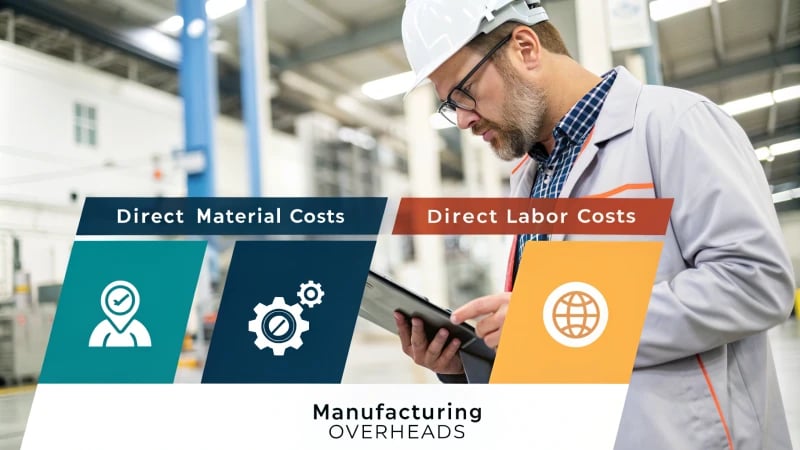
Understanding Manufacturing Costs
Manufacturing costs are crucial for businesses as they directly impact pricing, profitability, and budgeting. They can be broadly categorized into three key components: direct materials, direct labor, and manufacturing overhead.
Direct Material Cost Calculation
Direct material costs refer to the expenses incurred for the raw materials used in the production process. Here’s how to calculate it:
-
Identify Raw Materials: Determine all the raw materials needed. For example, when producing plastic products, you may need:
- Plastic particles (e.g., polyethylene)
- Additives (e.g., masterbatches)
- Packaging materials
-
Calculate Quantities: Assess the amount required based on design specifications or production processes. For instance:
- Injection molding products will require calculating the weight of plastic particles based on mold volume.
-
Cost Calculation: Multiply the amount of each raw material by its purchase price and sum them up. For example:
Material Type | Amount Used (g) | Unit Price (USD/kg) | Cost (yuan) |
---|---|---|---|
Plastic Particles | 100 | 2 | 0.2 |
Masterbatch | 5 | 4 | 0.02 |
Total Cost | 0.22 |
Direct Labor Cost Calculation
Direct labor costs account for the wages paid to workers involved in production. The calculation involves several steps:
-
Worker Identification: Identify all personnel involved in production, including machine operators and quality inspectors.
-
Track Labor Hours: Document the time spent by each worker on production-related tasks, which may include:
- Preparation time
- Actual production time
- Cleaning and maintenance time
-
Cost Calculation: Multiply the total labor hours by the wage rate. For example:
Labor Type | Hours Worked | Wage Rate (USD/hour) | Cost (USD) |
---|---|---|---|
Production Worker | 0.5 | 4 | 2 |
Manufacturing Overhead Calculation
Manufacturing overhead includes all indirect costs associated with production that are not direct materials or direct labor. Key components include:
Equipment Depreciation Cost
- Determine Values: Establish the original cost, expected life, and residual value of equipment.
- Depreciation Calculation: Using straight-line depreciation:
Equipment | Original Value (USD) | Expected Life (years) | Residual Value (USD) | Annual Depreciation (USD) |
---|---|---|---|---|
Injection Molding Machine | 150,000 | 10 | 15,000 | 15,000 |
- Per Product Cost: If this machine produces 100,000 products annually:
- Each product incurs a depreciation cost of:
Product Count | Depreciation Cost (USD) |
---|---|
Per Product | 0.15 |
Energy Costs
Calculating energy costs involves assessing the energy consumed during production processes:
- For example, if an injection molding machine uses:
- 10 kWh per hour at a rate of 0.8 yuan/kWh for a product taking 0.2 hours to produce:
Energy Source | kWh Used/hour | Rate (USD/kWh) | Time (hours) | Cost (USD) |
---|---|---|---|---|
Electricity | 10 | 0.15 | 0.2 | 0.3 |
Mold Costs
If applicable, allocate mold costs by assessing:
- Production cost of the mold and its lifespan.
- If a mold costs 1,000 USD and produces 100,000 items:
Mold Cost | Total Cost (USD) | Lifetime Production Count | Cost per Product (USD) |
---|---|---|---|
Injection Mold | 10,000 | 100,000 | 0.1 |
Total Manufacturing Cost Calculation
Finally, aggregate all calculated costs to determine total manufacturing costs:
- The total cost can be summarized as follows:
total cost =(direct material cost + direct labor cost + equipment depreciation + energy costs + mold costs)
By understanding these components manufacturers can better control their costs and optimize their pricing strategies.
To explore more about manufacturing costs check out further insights1.
Manufacturing costs include direct materials, labor, and overhead.True
These three components are essential for calculating total manufacturing expenses, impacting pricing and profitability.
Direct material costs are unrelated to raw material expenses.False
This statement is false; direct material costs specifically refer to the expenses for raw materials used in production.
How Do Direct Material Costs Impact Pricing?
Have you ever thought about how the costs of raw materials affect the prices we see in stores? This relationship is very interesting and complex. It plays an important role in manufacturing. Let’s explore this together!
Direct material costs impact product pricing by influencing pricing strategies and profitability. Changes in these costs can affect market competitiveness, highlighting their crucial role in pricing decisions.
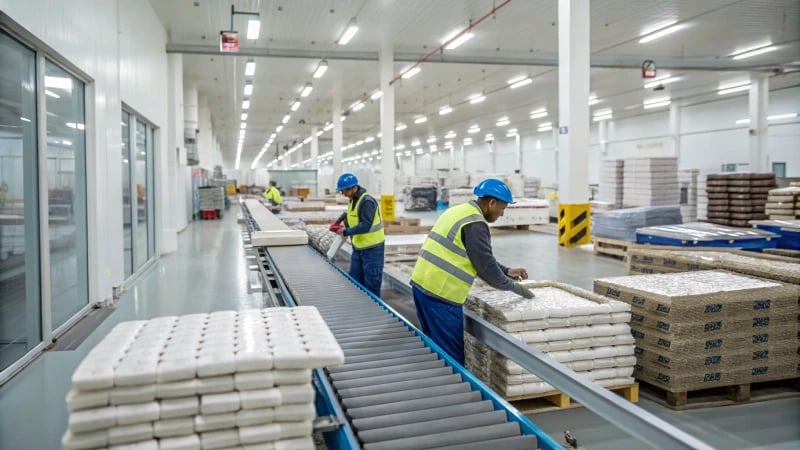
Understanding Direct Material Costs
Understanding direct material costs and how they affect pricing is more than just accounting for me. It’s a path I have traveled in my own career. I remember the early days of my job, working on product designs. I saw how each choice, like picking a certain kind of plastic, changed our pricing plan. Every decision seemed huge. I often wondered how to keep our products both high quality and affordable for our customers. Quality and price both matter a lot.
Direct material costs come from the raw materials used in production. These costs are not just numbers; they are real resources that create a product. I have often been deeply involved in calculations. My task was to figure out the exact material costs for a new design. This job can be very complex, including different parts like plastic pieces, additives, and sometimes even special packaging.
Calculation of Direct Material Costs
When I calculate these costs, I follow a step-by-step process:
-
Identify Raw Materials: First, I list everything needed for production. This list may include:
- Plastic particles (like polyethylene)
- Additives (such as masterbatches)
- Packaging materials
-
Calculate Amounts Used: Then, based on the design, I calculate the material amounts needed. For example, while designing a plastic toy, I found we needed:
- 100 grams of plastic at 2 USD/kg
- 5 grams of masterbatch at 3 USD/kg
-
Compute Total Cost: Finally, I multiply the amounts by their unit prices:
Item | Quantity (g) | Unit Price (USD/kg) | Cost Calculation | Total Cost (USD) |
---|---|---|---|---|
Plastic Particles | 100 | 2 | (100/1000)*2 | 0.2 |
Masterbatch | 5 | 3 | (5/1000)*3 | 0.015 |
Total | 0.215 |
Impact on Pricing Strategies
Over the years, I learned that direct material costs strongly influence product pricing. If these costs rise due to supply problems, businesses face tough choices:
- Absorb Costs: We might absorb these increases to keep loyal customers satisfied; this can lead to smaller profits.
- Pass Costs to Consumers: Sometimes we have to increase prices; this choice protects profit but may affect customer loyalty.
- Evaluate Alternatives: At times we explore cheaper materials or new suppliers; our goal is to keep quality high and costs low.
Broader Implications on Market Positioning
The link between material costs and pricing affects more than just profits:
- Competitive Advantage: Smart management of material costs helps companies offer better pricing; this can beat competitors.
- Consumer Perception: Price increases could lead to negative views; clear communication about quality and value is really important.
- Long-term Sustainability: Businesses must plan smartly for material cost changes; doing so helps them stay viable.
For more insights into managing production costs and pricing strategies effectively, check out this resource2. Understanding this relationship has shaped my approach to product design. It has empowered me to make decisions that fit my company’s goals and our customers’ needs.
Direct material costs directly affect product pricing strategies.True
Changes in direct material costs influence how companies price their products, impacting profitability and market competitiveness.
Absorbing rising material costs improves customer loyalty.False
While absorbing costs may enhance loyalty, it can also reduce profit margins, presenting a challenging balance for businesses.
How Important Are Labor Costs in Manufacturing?
Labor costs are not just numbers on a spreadsheet. They influence the success or failure of a manufacturing business. Their significance is very important. My experiences in this field provide personal insights.
Labor costs, including wages, benefits, and overhead, are crucial in manufacturing. Effective management enhances profitability and operational efficiency, vital for sustaining growth in today’s competitive market.
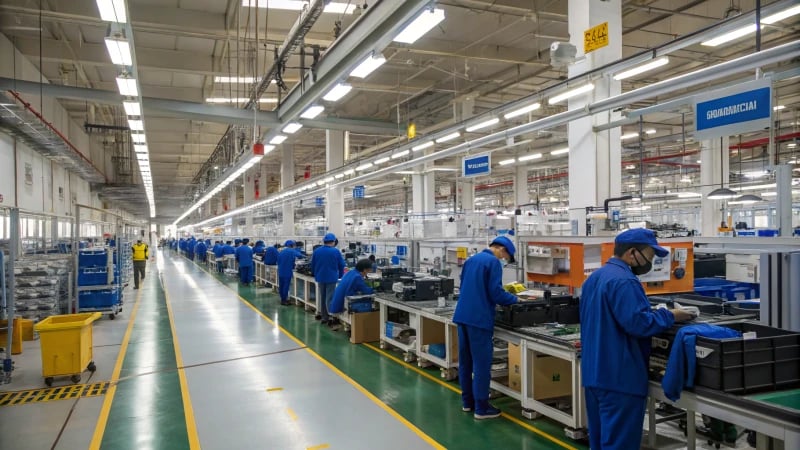
Understanding Labor Costs in Manufacturing
Understanding labor costs in manufacturing is like solving a complex puzzle. Every piece is important. I remember my early days in manufacturing. I struggled with how each cost affected our profits. Hiring people was not enough. Investing in their skills was very crucial. Every dollar spent needed to bring value to the company.
Labor cost is not just a number; it shows the heart of the manufacturing sector. These costs include wages, benefits, and other expenses for workers who create products. I have seen how changing labor costs shift production dynamics, affecting pricing and efficiency.
Consider a plastic manufacturing company I worked with. They faced rising labor costs, making the production process more complex as higher skills were needed. This situation was a wake-up call; they had to rethink their operations to keep profits while maintaining quality.
Direct Labor Cost Calculation
Calculating labor costs must be accurate; it is crucial in manufacturing. Here’s how I usually break it down:
Component | Description | Example |
---|---|---|
Number of Workers | Total workers involved in production | 5 operators for injection molding machines |
Working Hours | Time spent by each worker on production | 0.5 hours per product |
Wage Rate | Hourly wage including benefits | 3 USD/hour |
Direct Labor Cost | Calculated as Labor Hours × Wage Rate | 0.5 × 3 = 1.5 USD |
Watching those numbers add up feels like seeing a recipe come together; every worker, like an ingredient, influences the final product’s quality and cost.
Impacts on Manufacturing Cost
Labor costs form a big part of total manufacturing expenses, which also include materials and overheads such as:
- Total Manufacturing Cost = Direct Material Cost + Direct Labor Cost + Other Manufacturing Costs (like equipment depreciation and energy costs).
- A rise in labor costs can increase product prices, making it hard for manufacturers trying to remain competitive.
Managing these costs effectively improves profits and creates a happier workforce. Employee training leads to fewer errors and higher productivity; everyone wins.
Strategies for Managing Labor Costs
To keep labor costs in check, I have used several strategies:
- Time Tracking: Systems that monitor productivity precisely are game changers.
- Training Programs: These programs lift morale and sharpen skills, reducing mistakes.
- Flexible Work Hours: Adjusting shifts based on demand reduces idle time.
- Cross-Training Employees: Workers trained in multiple tasks can switch roles easily, lowering extra labor costs.
Once, we had high demand for a specific product; thanks to cross-trained workers, we met production goals without overspending.
Conclusion: Labor Cost’s Role in Decisions
Understanding labor costs is very important for manufacturing managers as they directly affect pricing and financial planning. From my experience, evaluating labor cost structures is key; it helps maintain profitability and efficiency.
For more tips on handling these costs, check resources like effective cost strategies3 and labor optimization methods. They could provide the advantage needed in this competitive field.
Labor costs directly influence total manufacturing expenses.True
Labor costs are a significant component of overall production expenses, impacting profitability and operational efficiency in manufacturing.
High labor costs always lead to increased product prices.False
While high labor costs can increase product prices, other factors like material costs also play a role in pricing decisions.
How Can Overhead Expenses Be Accurately Calculated?
Understanding overhead expenses is a very important skill I learned over the years. This is especially true in manufacturing. It’s about much more than numbers. It’s about knowing how to keep a business thriving. Keeping a business successful is really crucial.
To accurately calculate overhead expenses, categorize costs by identifying direct material, direct labor, and manufacturing costs, including depreciation, energy, mold, and maintenance expenses.
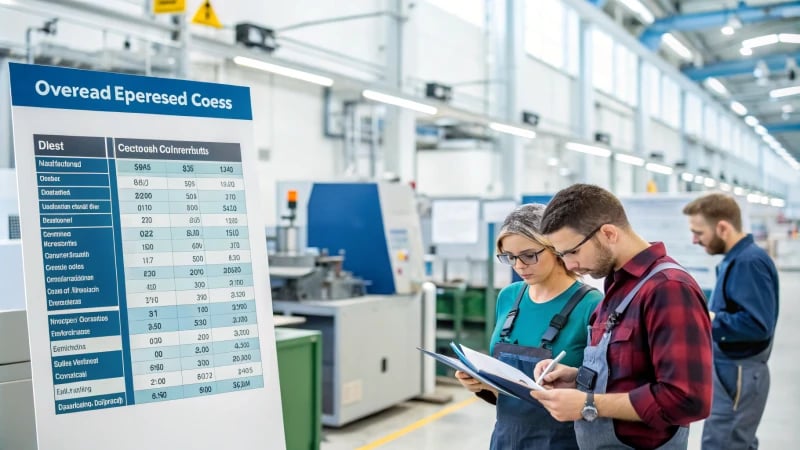
To accurately calculate overhead expenses, it’s essential to break down the costs involved into several categories. This not only provides clarity but also aids in budgeting and profitability analysis. Below are the primary components to consider:
Direct Material Cost Calculation
- Identify the various raw materials used, such as plastic particles (e.g., polyethylene) and additives (e.g., masterbatches).
- Calculate the required amount based on design specifications. For instance, to inject a plastic shell, determine the weight needed per injection.
- Multiply the quantity of each raw material by its unit price. For example:
Raw Material | Amount Used (kg) | Unit Price (USD/kg) | Total Cost (USD) |
---|---|---|---|
Plastic Particles | 0.1 | 2 | 0.2 |
Masterbatch | 0.005 | 4 | 0.02 |
Total Direct Material Cost = 0.2 + 0.02 = 0.22USD.
Direct Labor Cost Calculation
- Assess the number of workers and their working hours involved in production.
- Record total labor hours spent on tasks like equipment operation and product inspection.
- Use the formula:
Direct Labor Cost = Total Labor Hours × Hourly Wage Rate
For example, if a worker spends 0.5 hours producing a product with an hourly wage of 4 USD:
- Direct Labor Cost = 0.5 × 4 = 2USD.
Manufacturing Cost Calculation
Manufacturing costs can be further broken down into several categories:
Equipment Depreciation Cost
- Calculate annual depreciation using the straight-line method:
Annual Depreciation = (Original Value – Residual Value) ÷ Expected Service Life
For example, if an injection molding machine costs 150,000 USD, with a residual value of 15,000 USD and a lifespan of 10 years:
- Annual Depreciation = (150,000 – 15,000) ÷ 10 = 13,500.
- Allocate this cost based on output:
Depreciation Cost per Product = Total Annual Depreciation ÷ Number of Products Produced
If the machine produces 100,000 products:
- Depreciation Cost per Product = 13,500 ÷ 100,000 = 0.135 USD.
Energy Costs
- Measure the energy consumed during production. For instance, if an injection molding machine uses 10 kWh per hour at a rate of 0.15 USD/kWh for a production time of 0.2 hours***:
- Energy Cost = 10 × 0.15 × 0.2 = 0.3USD.
Mold Costs
- Evaluate the mold production costs and service life:
- For example, if a mold costs 10,000 USD and lasts for producing 100,000 products:
- Mold Cost per Product = Total Mold Cost ÷ Total Products Produced = 10,000 ÷ 100,000 = 0.1USD.
Equipment Maintenance and Repair Costs
- Record annual maintenance costs (e.g., 15,000 USD). If producing 500,000 products annually: -Maintenance Cost per Product = Total Maintenance Cost ÷ Total Products Produced = *15,000÷500,000=0.03USD**
Total Cost Calculation Combine all costs to determine the total manufacturing cost:
- Total Manufacturing Cost = Direct Material Cost + Direct Labor Cost + Manufacturing Costs – For instance:
Component | Cost (USD) |
---|---|
Direct Material Cost | 0.22 |
Direct Labor Cost | 2 |
Equipment Depreciation | 0.135 |
Energy Costs | 0.3 |
Mold Costs | 0.1 |
Maintenance Costs | 0.03 |
Total Manufacturing Cost | 2.785 |
By meticulously calculating these components you can ensure that your overhead expenses are accurately determined and effectively managed in your financial planning.
Direct material costs include raw materials and additives.True
Direct material costs encompass all raw materials and additives used in production, crucial for calculating total expenses accurately.
Energy costs are irrelevant to overhead expense calculations.False
Energy costs are a significant component of overhead expenses and must be included in total cost calculations for accuracy.
What Tools Can I Use for Cost Calculation in Manufacturing?
Exploring how to calculate costs in manufacturing might seem scary. But believe me, the right tools help a lot. Discover some useful choices that really simplify budgeting and planning.
Manufacturers leverage spreadsheet software, cost estimation tools, and online calculators for cost calculations, accommodating different complexities and user needs. Selecting the most appropriate tool tailored to your manufacturing context is crucial for effective cost management.
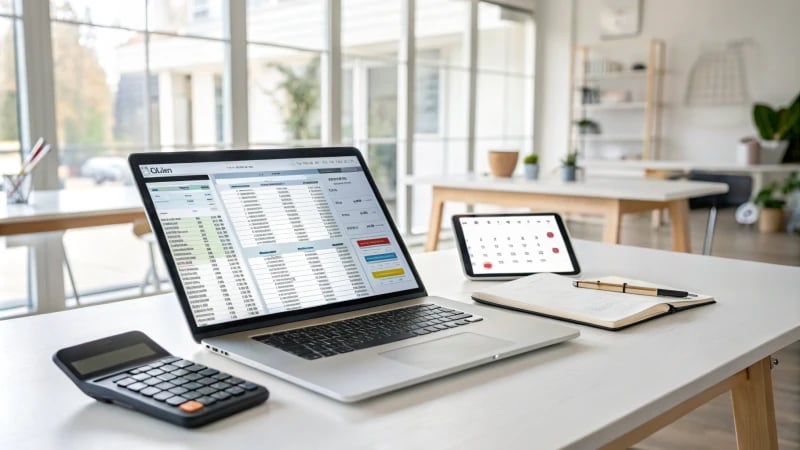
Introduction to Cost Calculation Tools in Manufacturing
I started in the manufacturing field and quickly realized that understanding costs is key to competing. Learning was tough, but having the right tools really helped. This article will share different cost calculation tools and how they fit into your processes.
Spreadsheet Software
My favorite resource is spreadsheet software like Microsoft Excel or Google Sheets. They are not just numbers; they are strong helpers for building custom cost models, doing complex calculations, and showing data with charts.
Key Features of Spreadsheet Software:
- Custom Formulas: I enjoy creating special formulas to figure out costs for materials, labor, and manufacturing. It feels powerful to build something unique!
- Data Organization: These spreadsheets hold my cost data neatly. Quick updates are easy when I need to change estimates.
- Visualization Tools: Charts and graphs let me see trends. Visual success is unbeatable!
To start a cost model in Excel, check this Excel Cost Calculation Template4.
Dedicated Cost Estimation Software
For complex projects, I use dedicated cost estimation software. These are designed for tough calculations with features that spreadsheets lack.
Advantages of Dedicated Software:
Feature | Description |
---|---|
Real-time Data | Allows for real-time updates on cost inputs and changes in production processes. |
Integration | Can often integrate with other business systems (ERP, MRP) for seamless data flow. |
Industry-Specific Tools | Offers templates and tools tailored to specific manufacturing sectors, improving accuracy. |
Examples I use include Costimator5 and MIE Trak Pro. They simplify calculations and improve overall project management efficiency.
Online Calculators and Templates
Besides software, I use online calculators and templates for quick cost estimates. Simplicity works best sometimes.
Benefits of Using Online Calculators:
- Accessibility: I enjoy using these tools on any device with internet – perfect for travel.
- Simplicity: Most calculators are easy to use with little input, making them very user-friendly.
- Instant Results: Immediate calculations without setting up a hard spreadsheet are the best!
Find useful online tools like the Manufacturing Cost Calculator6 to start basic estimates quickly.
Conclusion
I learned that the right tools for cost calculation in manufacturing are crucial. Simple spreadsheets or complex software have unique strengths. They fit different needs. Spend time exploring; they can change how you manage cost estimates!
Spreadsheet software is widely used for cost calculations in manufacturing.True
Spreadsheet programs like Excel allow for customizable cost models and complex calculations, making them popular among manufacturers.
Dedicated cost estimation software offers real-time data updates.True
Such software provides features like real-time updates and integration with other systems, enhancing accuracy in manufacturing cost calculations.
Conclusion
Learn how to accurately calculate the manufacturing costs of plastic products by considering direct materials, labor, and overhead expenses for effective pricing strategies.
-
Explore this link to gain deeper insights into manufacturing cost components and enhance your knowledge in this critical area. ↩
-
Discover comprehensive strategies on managing direct material costs and their implications on pricing decisions to enhance your business strategy. ↩
-
Discover how managing labor costs can boost your manufacturing efficiency and profitability. This link provides practical insights tailored for manufacturing professionals. ↩
-
This link provides an extensive guide on effective Excel templates for calculating costs in manufacturing, enhancing your budgeting accuracy. ↩
-
Discover the functionalities of dedicated cost estimation software designed specifically for manufacturers to optimize their costing processes. ↩
-
Find practical online calculators that help streamline your cost estimation process in manufacturing, perfect for quick calculations. ↩