Let’s unravel the mystery of cycle time in injection molding and discover how it impacts efficiency!
Cycle time in injection molding is calculated by summing the filling time, cooling time, and mold opening time. It is influenced by factors such as part size, material properties, and mold design. Accurate calculation helps enhance production efficiency.
While this straightforward answer gives us a good starting point, there’s much more to uncover. By diving into each component, we can find ways to significantly enhance our manufacturing process.
Cycle time in injection molding includes filling, cooling, and opening.True
Cycle time is the sum of filling, cooling, and mold opening times.
What Factors Influence Cycle Time in Injection Molding?
Understanding the factors affecting cycle time in injection molding is crucial for efficient production.
Cycle time in injection molding is influenced by part size and complexity, material properties, mold design, process parameters, and production requirements. Each factor plays a pivotal role in determining how quickly a part can be manufactured, impacting both efficiency and quality.
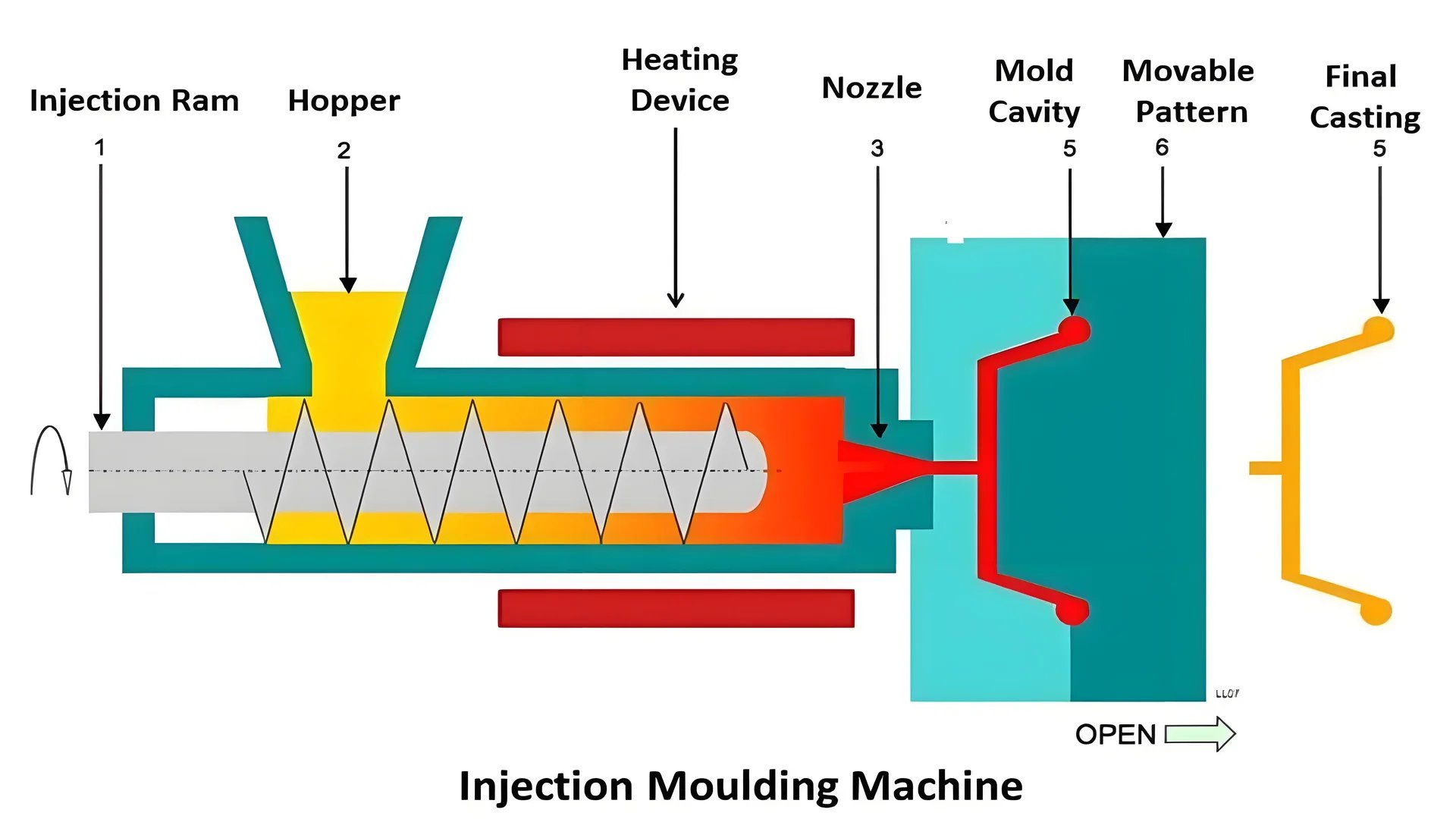
Part Size and Complexity
One of the primary factors influencing cycle time in injection molding is the size and complexity of the part being produced. Larger parts generally require longer cooling times due to their volume, while intricate designs may demand extended filling times to ensure precision. For example, a simple rectangular part might cool faster than a complex automotive component with multiple cavities and intricate details.
Material Properties
The type of plastic material used significantly affects the cycle time. Different materials exhibit unique fluidity, cooling speeds, and shrinkage rates. For instance, polypropylene may require less cooling time compared to polycarbonate, which has a higher heat resistance. Understanding these material characteristics is vital to optimize the cycle time efficiently.
Mold Design
The design of the mold is another critical factor. Features such as the cooling system’s efficiency, the placement, and number of gates can substantially impact cycle time. A well-designed mold with effective cooling channels can drastically reduce cooling time and improve overall efficiency. Designing molds with minimal flow restrictions ensures that filling times are kept at optimal levels.
Injection Molding Process Parameters
Process parameters like injection speed, pressure, and temperature are adjustable factors that directly influence cycle time. Higher injection speeds and pressures can shorten filling times but might increase wear on the mold or compromise part quality. Therefore, a balanced approach is necessary to achieve desired outcomes without sacrificing product integrity.
Production Requirements
Lastly, specific production requirements can also dictate cycle time. If higher quality checks and more stringent standards are in place, this might necessitate longer inspection times or additional process adjustments. Production scenarios demanding superior quality often involve iterative testing and adjustments, impacting the total cycle duration.
By considering these factors, manufacturers can strategize to achieve an optimal balance between speed and quality. Exploring further on mold design optimization1 or material selection strategies2 can provide additional insights into improving cycle times.
Larger parts in injection molding require longer cooling times.True
Larger volume leads to extended cooling due to heat retention.
Polycarbonate cools faster than polypropylene in injection molding.False
Polypropylene cools faster due to lower heat resistance than polycarbonate.
How Does Material Selection Affect Cycle Time?
Choosing the right material can significantly impact the efficiency and speed of the injection molding process.
Material selection affects cycle time by influencing factors such as cooling rate, shrinkage, and fluidity. Different materials require varying times to fill the mold, cool, and solidify, directly impacting the overall cycle time.
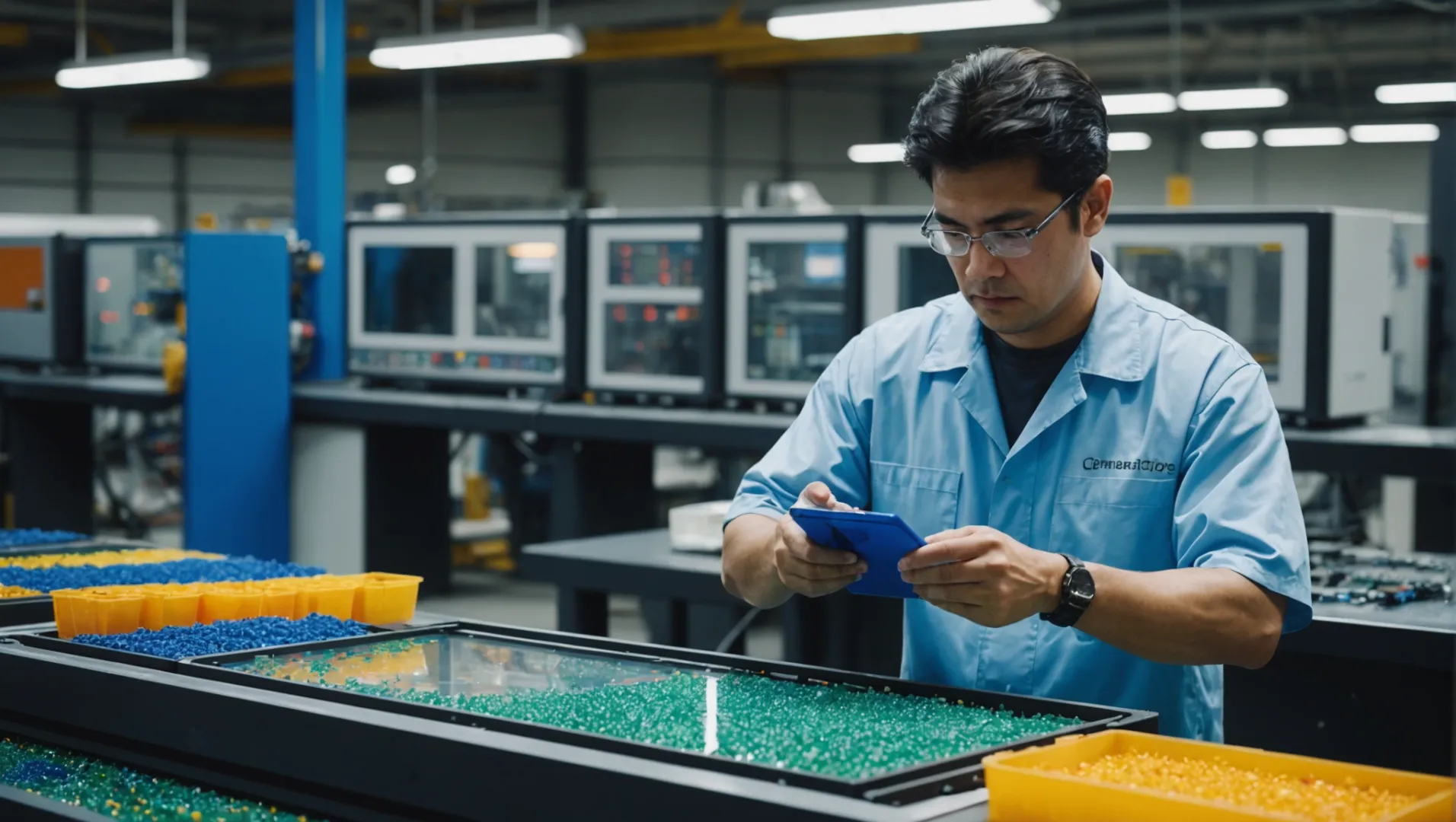
Material Properties and Their Impact
The inherent properties of materials play a crucial role in determining the cycle time in injection molding. Materials with higher fluidity often fill molds more quickly, which can reduce filling time. However, this can also lead to potential issues such as mold wear if not carefully managed. For instance, analyzing fluidity impacts3 can provide insights into optimizing material choices.
Cooling rate is another critical factor. Some materials, like certain thermoplastics, cool rapidly and allow for shorter cycle times. However, this quick cooling can sometimes cause warping or shrinkage, affecting the part’s final dimensions and quality. To mitigate these risks, it’s important to consider the thermal conductivity of the material.
Material Type | Cooling Rate | Shrinkage Risk | Recommended Use Cases |
---|---|---|---|
Polypropylene | Fast | Moderate | High-volume production |
ABS | Moderate | Low | Precision parts |
Polycarbonate | Slow | High | Durable and impact-resistant parts |
Matching Material with Part Requirements
Selecting materials that align with the functional requirements of the part is essential. For example, if a part needs to withstand high temperatures, materials like polycarbonate are preferable despite their longer cooling times. Conversely, for high-speed production, a material like polypropylene might be more suitable due to its rapid cooling properties.
Understanding material-specific processing parameters4 can guide manufacturers in adjusting their process settings accordingly, balancing cycle time with product quality.
Strategic Material Substitution
In some cases, substituting a different material can lead to improved cycle times without compromising quality. This strategy requires thorough testing and analysis to ensure that alternative materials meet all performance requirements.
For example, substituting a high-cost engineering plastic with a lower-cost alternative might not only cut costs but also reduce cycle time if the new material cools faster or fills the mold more efficiently. Conducting material substitution analysis5 can help make informed decisions in this area.
Polypropylene has the fastest cooling rate.True
Polypropylene cools quickly, making it suitable for high-volume production.
ABS has a high shrinkage risk.False
ABS has low shrinkage risk, ideal for precision parts.
What Role Does Mold Design Play in Cycle Time?
Mold design is crucial in determining the cycle time of injection molding, impacting efficiency and productivity.
Mold design influences cycle time by affecting cooling efficiency and filling speed. Efficient designs minimize cooling times and ensure optimal material flow, thereby shortening overall cycle time and enhancing production throughput.
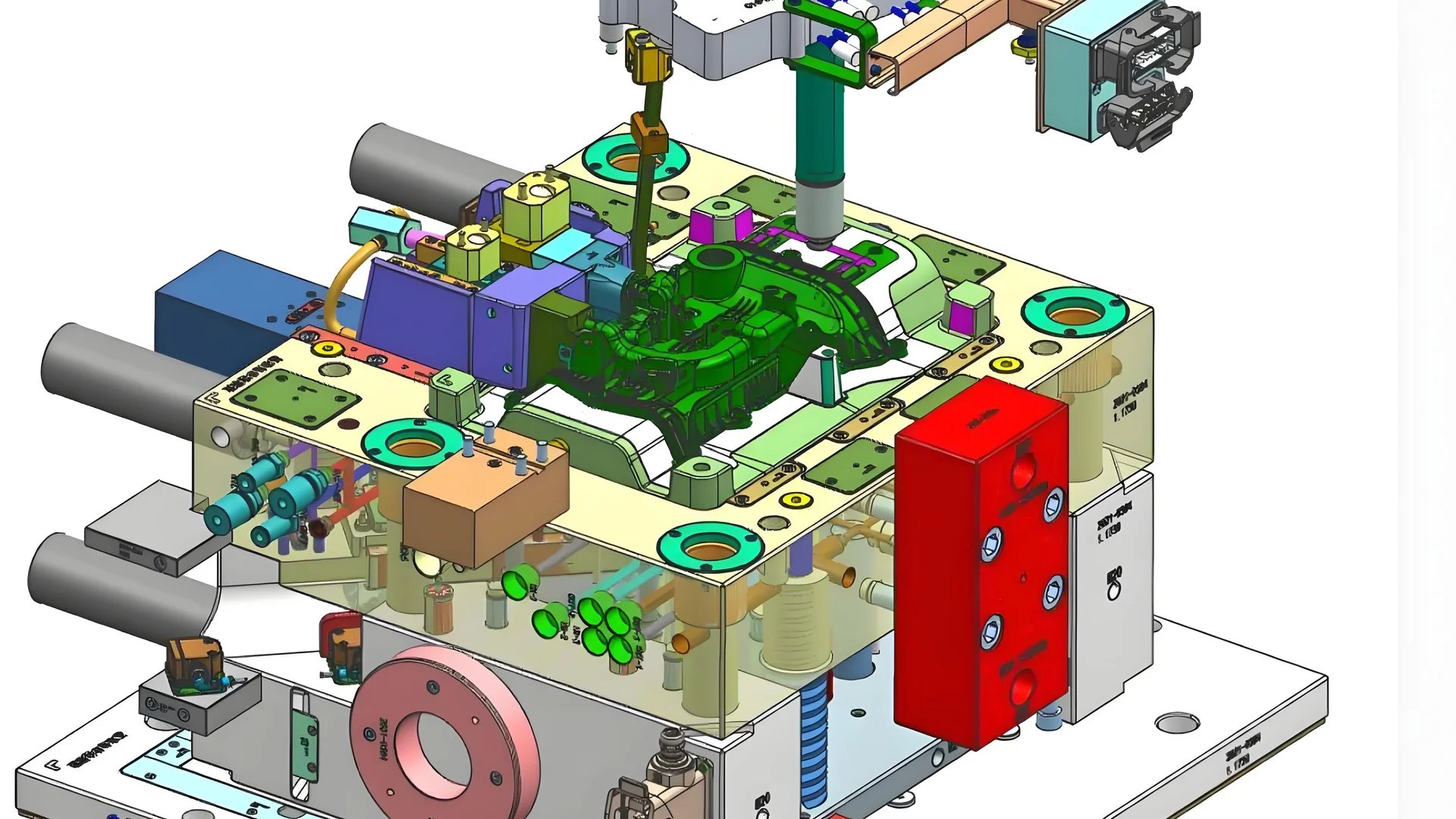
Understanding Mold Design’s Influence on Cycle Time
The cycle time6 in injection molding hinges significantly on the mold design, primarily through its impact on cooling efficiency and filling speed. Let’s explore how different aspects of mold design can streamline or elongate this critical process.
Cooling System Design
The cooling system within the mold is a pivotal component in dictating cycle time. Efficient cooling channels ensure uniform temperature distribution, which accelerates the solidification of the material, thereby reducing cooling time. Designs incorporating conformal cooling—a method using 3D printing to create channels that closely follow the shape of the part—offer superior cooling efficiency compared to traditional straight-line channels. This advancement can drastically cut down the cooling phase, which typically constitutes a significant portion of the cycle time.
Cooling System Type | Characteristics | Impact on Cycle Time |
---|---|---|
Traditional | Straight-line channels | Longer, less efficient cooling |
Conformal | Channels tailored to part contours | Faster, more uniform cooling |
Gate Location and Number
The placement and number of gates—the entry points through which molten plastic enters the mold—are crucial for determining the speed and uniformity of filling. Ideally, gates should be positioned to ensure balanced flow paths, minimizing the pressure drop and fill time. More strategically placed gates can also help in reducing potential defects such as warping or incomplete fills, thereby optimizing cycle time.
Material Flow Optimization
Optimizing material flow within the mold is another critical aspect. Features such as flow leaders or weld lines are carefully designed to promote seamless flow and minimize areas of high shear stress, which can affect both the quality of the molded part and the speed of production.
Practical Steps to Optimize Mold Design for Cycle Time Reduction
- Simulation and Testing: Employ computer-aided engineering (CAE) tools to simulate various designs and predict their impact on cycle time.
- Iterative Design Adjustments: Continuously refine mold designs based on simulation results and actual performance data.
- Material Compatibility: Ensure that the mold design aligns with the properties of the chosen material to enhance flow and cooling efficiency.
By meticulously designing molds with these considerations in mind, manufacturers can achieve significant reductions in cycle time, leading to increased throughput and reduced operational costs. For further exploration of mold design strategies and innovations, click here7.
Conformal cooling reduces mold cycle time.True
Conformal cooling provides efficient heat dissipation, shortening cycle time.
Gate placement has no effect on mold cycle time.False
Gate placement affects flow paths, impacting fill speed and cycle time.
How Can Process Parameters Be Optimized for Shorter Cycle Times?
Optimizing process parameters is crucial for reducing cycle times and boosting production efficiency.
To optimize process parameters for shorter cycle times, adjust injection speed, pressure, and temperature while ensuring product quality. High injection speeds and pressures can reduce filling time but may compromise mold longevity and part integrity if not carefully managed.
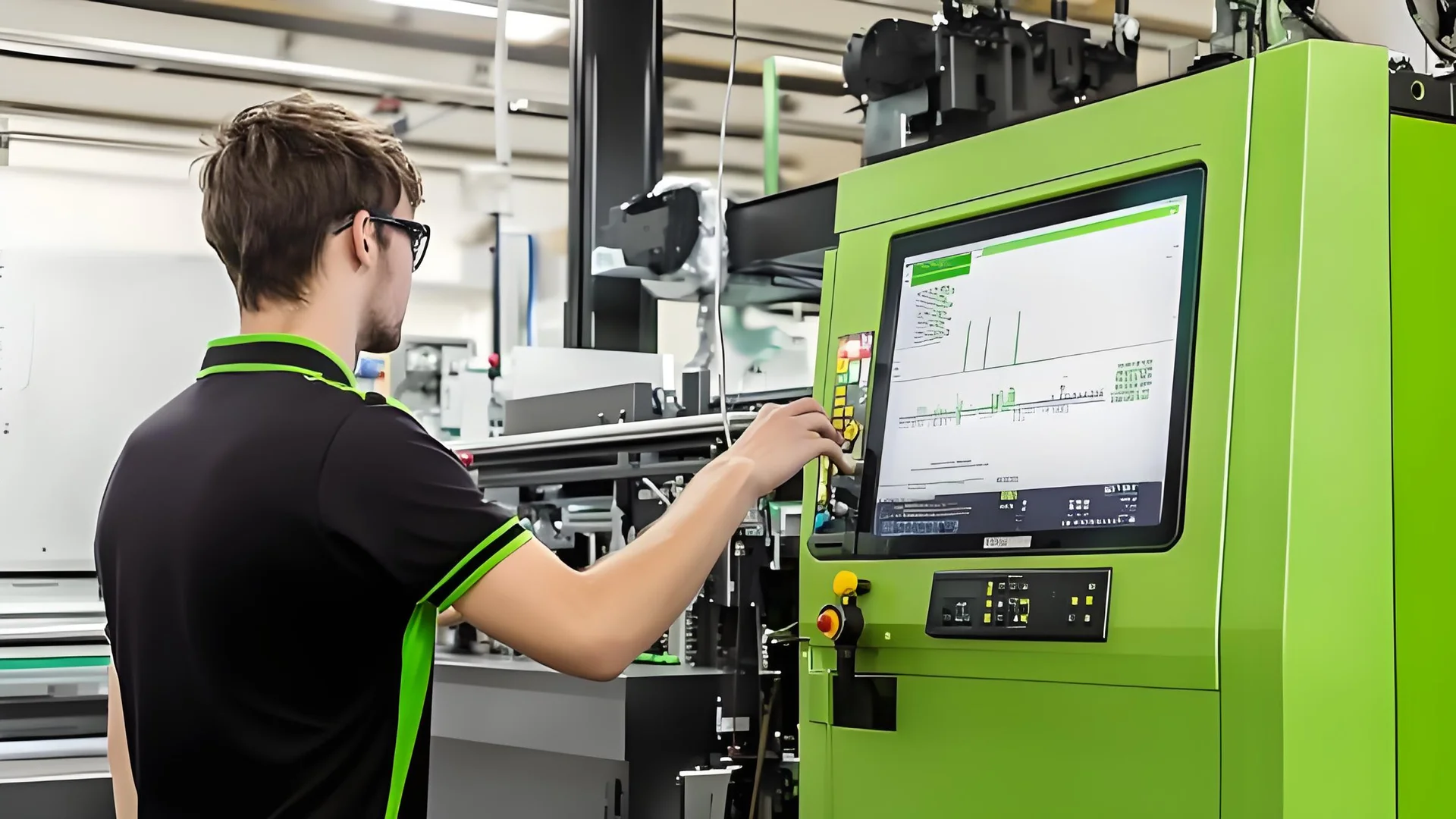
Understanding Process Parameters
The journey to optimizing cycle times begins with a thorough understanding of the process parameters involved in injection molding. These parameters include injection speed, pressure, and temperature, each playing a pivotal role in determining the cycle time.
-
Injection Speed: Increasing the injection speed can significantly reduce the filling time. However, it’s essential to balance speed with quality, as excessive speed can lead to defects such as flash or short shots. Conducting process testing8 helps determine the optimal speed.
-
Pressure: Adequate injection pressure ensures proper mold filling and compaction of the material. While higher pressures can decrease cycle times by speeding up the filling phase, they might also elevate the risk of mold wear. Regular monitoring and adjustments are crucial to maintaining mold integrity.
-
Temperature Control: Proper control of melt and mold temperatures can improve material flow and cooling rates. Lower melt temperatures might reduce cooling time but at the expense of increased viscosity, which can affect fill quality.
Balancing Parameters for Optimal Performance
Adjusting one parameter often impacts others, requiring a holistic approach to optimization:
-
Trial and Error Method: Implementing small changes incrementally allows you to measure their effects on cycle time and part quality. Use a systematic approach to adjust one parameter at a time, documenting results for future reference.
-
Simulation Software: Employing simulation tools9 can predict the outcome of parameter adjustments before physical trials. This technology assists in identifying potential issues and reducing costly trial runs.
-
Continuous Monitoring: Utilize sensors and feedback systems to monitor real-time data during production. This approach helps in making timely adjustments, ensuring consistent quality and efficiency.
Practical Steps in Parameter Optimization
- Conduct Initial Analysis: Evaluate current cycle times and identify bottlenecks or inefficiencies.
- Parameter Adjustment: Begin with minor changes in one parameter, such as injection speed, and assess its impact.
- Quality Check: Ensure that adjustments do not compromise product quality.
- Implement Feedback Loop: Use data from production runs to refine settings continuously.
- Review and Document Results: Keep detailed records of settings and outcomes for ongoing improvements.
By adopting a systematic approach to optimizing process parameters, manufacturers can achieve shorter cycle times without sacrificing product quality. This not only enhances production efficiency but also extends mold life and reduces operational costs.
High injection speeds reduce filling time.True
Increasing injection speed can significantly lower the time needed to fill molds.
Higher pressures always improve mold longevity.False
Excessive pressure may speed up filling but can also cause mold wear.
Conclusion
Mastering cycle time management in injection molding can lead to remarkable improvements in efficiency and quality. Take these insights and start implementing them today!
-
Explore efficient mold design techniques to reduce cycle time.: Steps to INJECTION MOLDING Process Optimization · 1. Tool functionality examination · 2. Short shot testing · 3. Gate seal studies · 4. Sample parts evaluation/data … ↩
-
Discover materials that enhance cooling efficiency.: The biggest attribute of these materials is their heat-transfer rate — tools made from MoldMAX cool 3-4 times faster than standard mold steels like P20 or H13, … ↩
-
Understand fluidity’s role in reducing mold filling time.: Flow Characteristics: The flow characteristics of plastic materials can have an effect on cycle time. Different plastics have differing flow … ↩
-
Discover tailored process settings for different materials.: Factors such as the complexity of the part design, the material used, and the specific process parameters like injection speed, pressure, and … ↩
-
Learn how material changes can optimize cycle time.: It minimises molding costs and is a highly repeatable way of producing plastic or elastomeric parts with high precision. Once set up, it can … ↩
-
Understand how mold design elements specifically influence cycle times.: Mold design and tooling. Mold design and tooling have a significant effect on cycle time. A well-designed mold with adequate cooling channels … ↩
-
Discover cutting-edge mold design techniques that optimize manufacturing.: Using a digital twin to validate the machining process saves time and reduces risk, especially with highly complex parts like those made in mold … ↩
-
Learn effective strategies for process testing in injection molding.: Learn five critical steps to testing and qualifying a tool during injection molding pre-production that ensures consistency and repeatability on the line. ↩
-
Discover top simulation tools for efficient parameter adjustments.: As a powerful software solution, Autodesk Moldflow® enables comprehensive injection molding simulations. The tool includes simulations for filling, holding … ↩