Are you considering using ABS plastic injection molding for your next project? Understanding the costs involved is crucial.
The cost of creating an ABS plastic injection mold ranges from several thousand to hundreds of thousands, influenced by factors like product complexity, mold size, precision requirements, and steel quality.
While this brief overview gives you an idea of the cost range, diving deeper into each influencing factor can help you make more informed decisions. Read on to explore the complexities and considerations involved in determining the precise cost for your specific project needs.
Mold size directly affects the price of ABS molds.True
Larger molds require more material and complex processing, increasing costs.
How Does Product Complexity Affect Mold Costs?
Navigating mold costs? Product complexity can significantly sway your budget. Discover how intricacy impacts pricing.
Product complexity directly affects mold costs due to increased design, manufacturing difficulty, and precision requirements. Complex designs demand advanced techniques, leading to higher expenses.
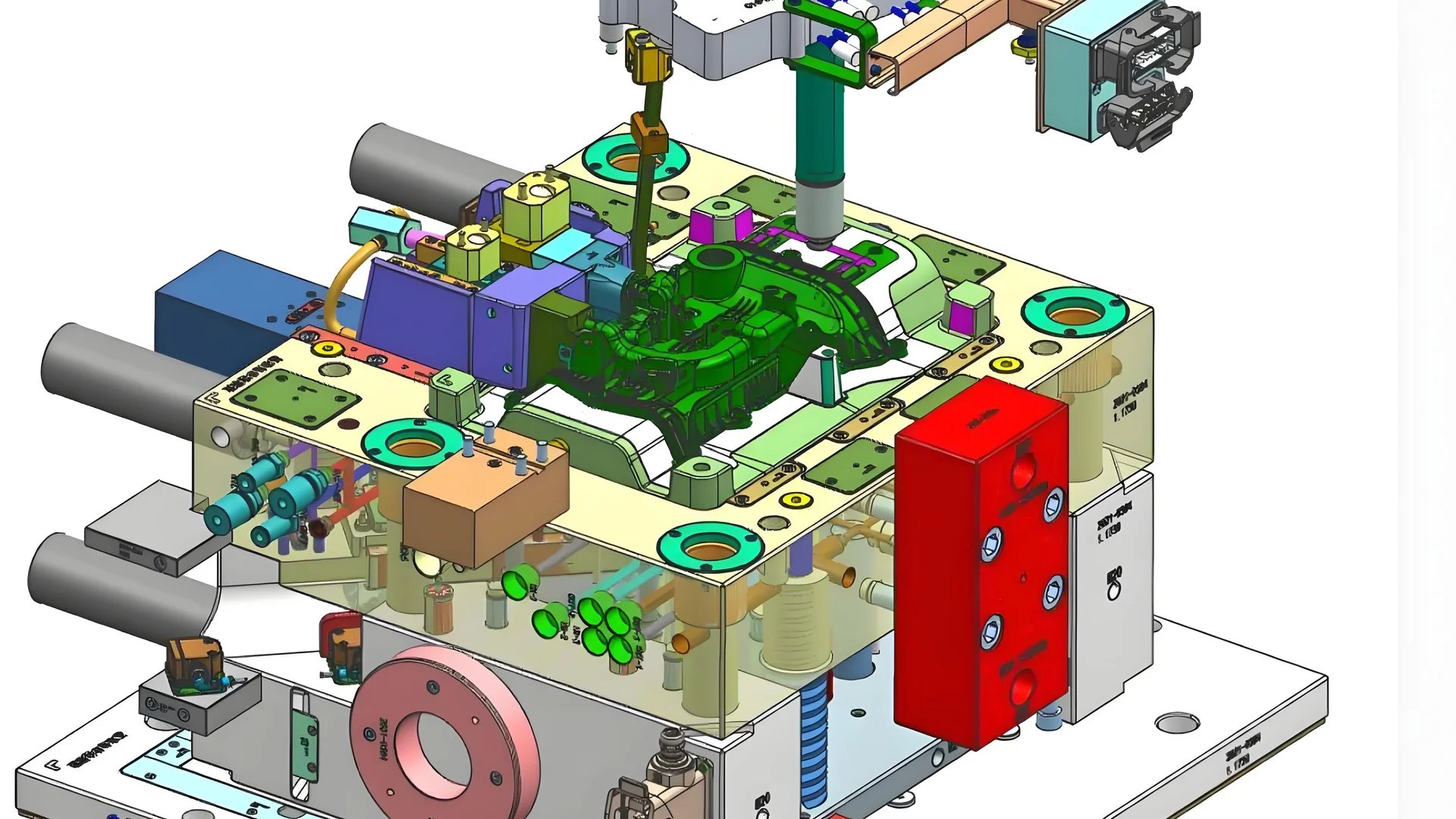
Understanding Product Complexity
When we talk about product complexity in the context of mold making, it refers to the intricacies involved in a product’s design and function. Complex products often feature detailed shapes, undercuts, or multiple components requiring precise alignment. Such complexity can dramatically increase the design and manufacturing1 challenges associated with molds.
Simple vs. Complex Structures
-
Simple Structure Products: These have straightforward designs with minimal features and are often smaller in size. For example, a simple plastic buckle might require a mold costing between $1000 to $2000 due to its limited complexity.
-
Complex Structure Products: In contrast, products with intricate designs like electronic device shells or automotive parts can drive mold costs significantly higher. The need for specialized shapes or additional functional requirements often results in molds priced between $10,000 to $50,000, or even beyond.
Impact on Design and Manufacturing
The complexity of a product influences several aspects of the mold-making process:
-
Design Time and Expertise: More complex molds require skilled designers to ensure that all parts fit together precisely. This often translates to more hours spent on CAD modeling and simulation.
-
Material Selection: Complex designs may necessitate high-quality materials to ensure durability and precision, further increasing costs.
-
Advanced Manufacturing Techniques: Intricate molds might require advanced manufacturing methods such as multi-axis machining or precision EDM (Electrical Discharge Machining), both of which add to the overall expense.
Case Study: Electronic Equipment Shells
Consider the case of injection molds for electronic equipment shells. These products often feature internal structures with precise dimensional requirements and may incorporate multiple moving parts. Such demands escalate both design complexity and manufacturing precision, making these molds cost upwards of $15,000. The high precision ensures that electronic components fit perfectly within their housing without compromising functionality.
Conclusion: Balancing Cost and Complexity
Ultimately, understanding how complexity influences mold costs can guide strategic decisions in product development. While more intricate designs offer enhanced functionality or aesthetics, they also necessitate a larger investment in mold creation. When planning your next project, balancing these factors will be key to managing costs effectively while achieving your design goals.
Complex designs increase mold costs significantly.True
More intricate designs require advanced techniques, raising expenses.
Simple molds are more expensive than complex ones.False
Simple molds cost less due to easier design and manufacturing.
What Role Does Mold Size Play in Pricing?
The size of a mold can significantly impact its cost, influencing material usage and processing complexity.
Mold size directly affects the price of ABS plastic injection molds due to the increased material and processing requirements for larger molds. Smaller molds generally cost less as they require fewer resources and simpler equipment.
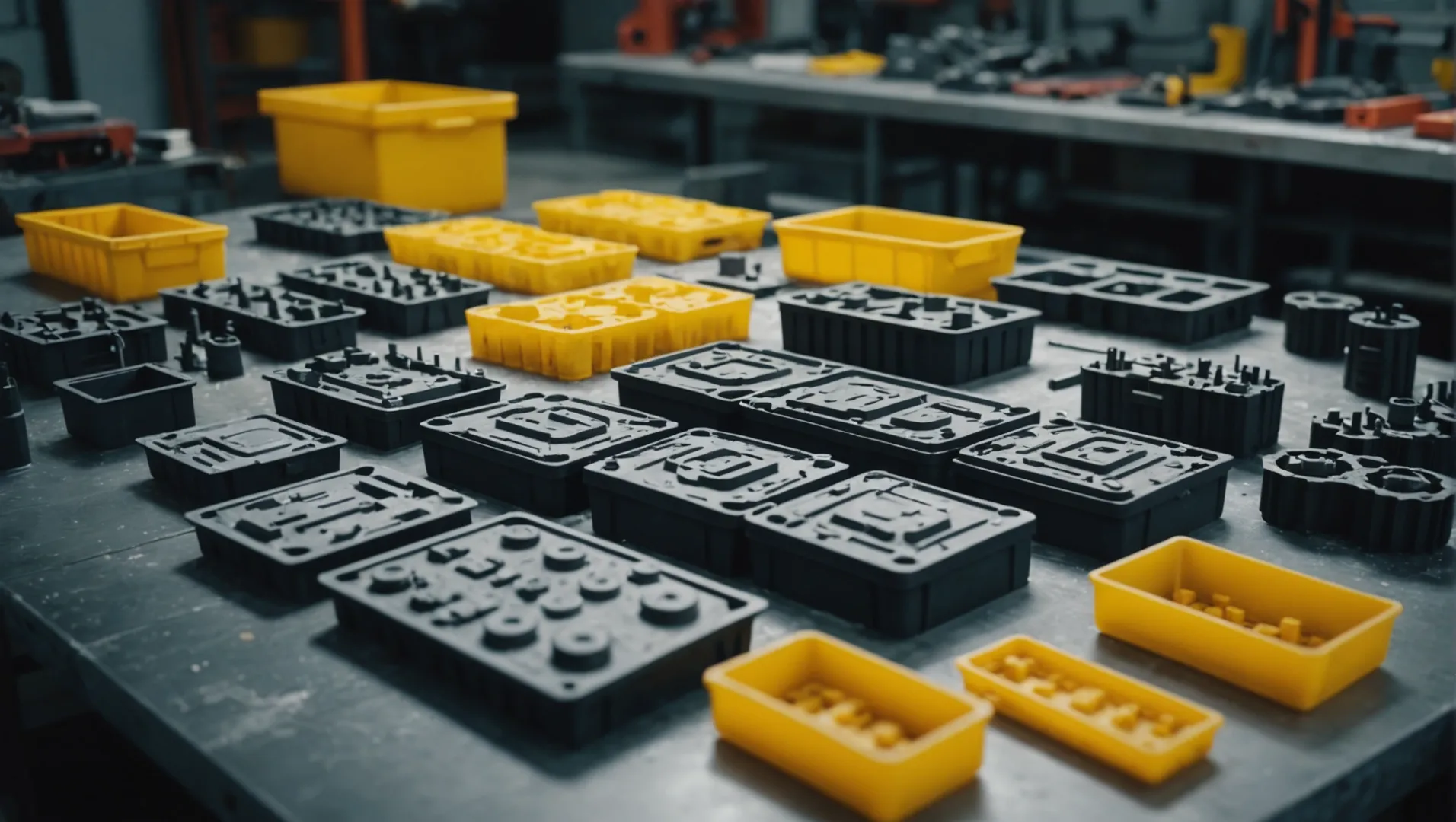
Understanding the Impact of Mold Size
When discussing the price of ABS plastic injection molds2, mold size is a crucial factor that cannot be overlooked. The relationship between mold size and pricing is straightforward: the larger the mold, the higher the cost. This is primarily because larger molds necessitate more raw materials, such as steel, and involve more complex manufacturing processes.
Small Molds: Cost-Effective Yet Limited
Small molds are often more economical, ranging from $2,000 to $10,000. These molds are less costly because they use less material and are easier to process. This makes them ideal for smaller projects or products with minimal complexity, like simple plastic parts or small buckles. The reduced need for advanced equipment and techniques further keeps costs down.
Mold Size | Price Range (USD) | Characteristics |
---|---|---|
Small | 2,000 – 10,000 | Less material, simpler processing |
Large Molds: High Cost but Greater Capability
On the other hand, large molds, such as those used for producing automotive parts like bumpers or large containers, can exceed $15,000. The higher cost is justified by the need for more raw materials and sophisticated processing technology. Additionally, larger molds require advanced equipment to ensure precision and quality during manufacturing.
Mold Size | Price Range (USD) | Characteristics |
---|---|---|
Large | 15,000+ | More material, complex processing |
These molds must withstand higher stress levels during injection molding, which demands better wear resistance and durability.
Balancing Size with Cost Efficiency
When planning a project involving ABS plastic injection molding, it’s essential to balance the desired mold size with cost efficiency. Considerations should include not only the initial cost but also long-term benefits like durability and performance. For instance, opting for a slightly larger mold might offer greater versatility for future production needs.
Understanding how mold size impacts pricing3 allows businesses to make informed decisions, ensuring that the chosen solution aligns with both budgetary constraints and production goals.
Larger molds require more raw materials.True
Larger molds need more steel and other materials, increasing costs.
Small molds are more expensive than large ones.False
Small molds are cheaper due to less material and simpler processing.
Why Are Precision Requirements Important for Cost Estimation?
Precision in mold-making is critical to cost estimation, impacting both quality and expense.
Precision requirements in mold-making significantly influence cost estimation by dictating the manufacturing processes, equipment needed, and quality control measures, ultimately affecting the overall expense.
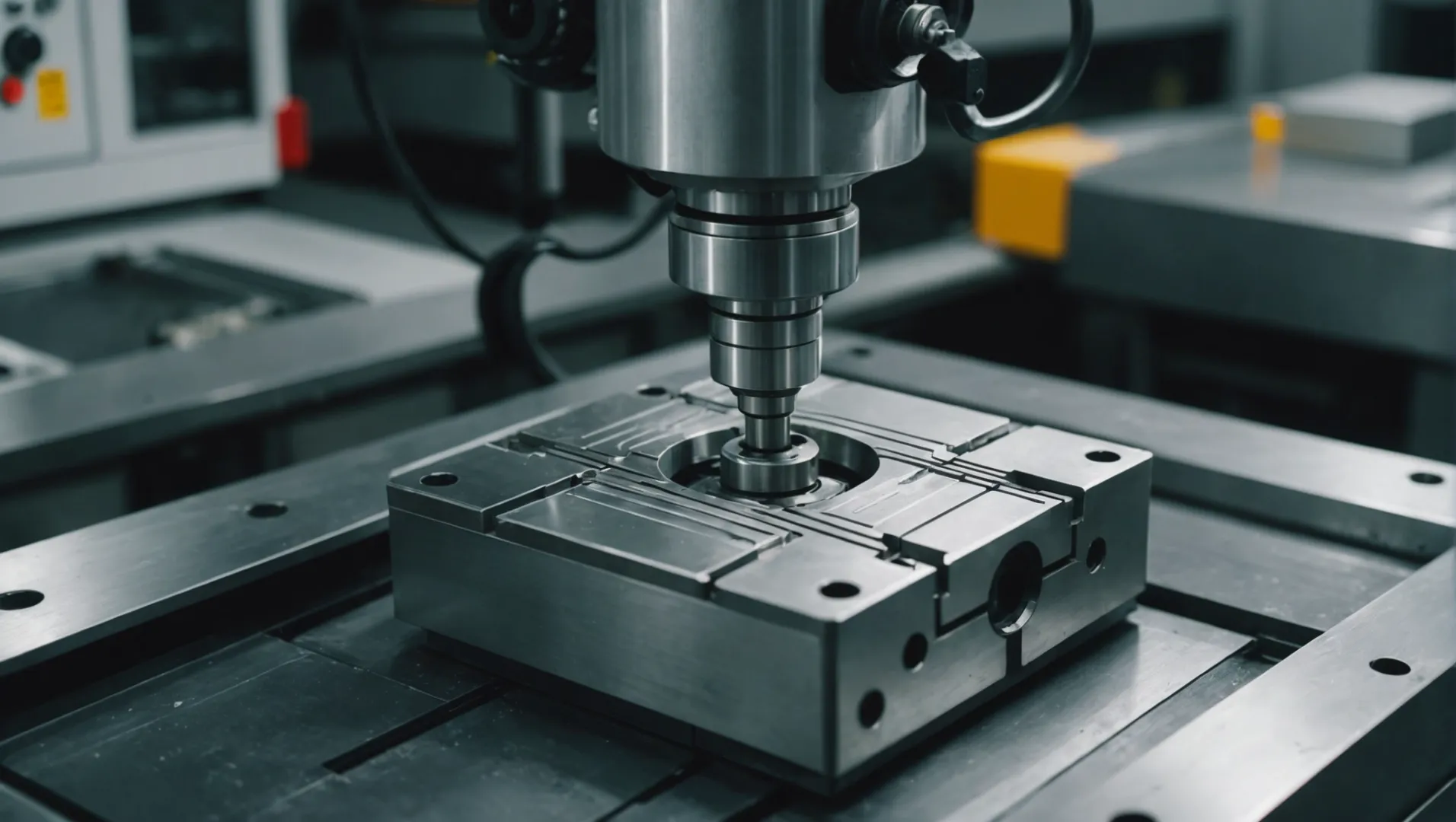
Understanding Precision in Mold-Making
In the realm of ABS plastic injection molding4, precision refers to the degree of accuracy and exactness required in the dimensions and surface quality of the molds. High-precision molds are crucial for products demanding tight tolerances and exceptional surface finishes, such as medical devices and electronics casings.
How Precision Impacts Cost
Equipment and Technology
High precision necessitates advanced machinery and technology. For instance, CNC (Computer Numerical Control) machines and EDM (Electrical Discharge Machining) are often required for high-precision molds. These machines not only cost more but also incur higher operational expenses, impacting the overall mold cost.
Skilled Labor
Crafting high-precision molds requires skilled labor with specialized training. Hiring experts increases labor costs, which is reflected in the final price of the mold.
Factors Influencing Precision Cost | Impact on Cost |
---|---|
Advanced Machinery | Increases |
Skilled Labor | Increases |
Quality Control | Increases |
Quality Control
Precision molds undergo rigorous quality control checks to ensure that they meet the specified standards. This process involves additional time and resources, further elevating costs.
Real-World Implications
Consider a scenario where a company manufactures plastic parts for a high-end electronics brand. The parts must fit perfectly within electronic devices, leaving no room for error. Here, precision becomes non-negotiable. The cost to achieve such precision can significantly impact the budget but ensures product reliability and brand reputation.
Ultimately, understanding the importance of precision in mold-making helps businesses allocate resources effectively and anticipate potential challenges during production. It underscores the necessity of investing in quality5 to achieve optimal results.
Precision impacts mold cost through advanced machinery needs.True
High precision molds require costly CNC and EDM machines.
Quality control reduces costs in high-precision mold-making.False
Quality control increases costs due to rigorous checks and resources.
How Does Steel Quality Influence Mold Expenses?
Discover how choosing the right steel quality can significantly impact your mold expenses.
Steel quality directly influences mold expenses by affecting durability, performance, and lifespan. High-quality steels offer better wear resistance and corrosion resistance, leading to longer-lasting molds but at a higher initial cost. Conversely, using ordinary steel can reduce upfront costs but may result in higher maintenance and replacement expenses over time.
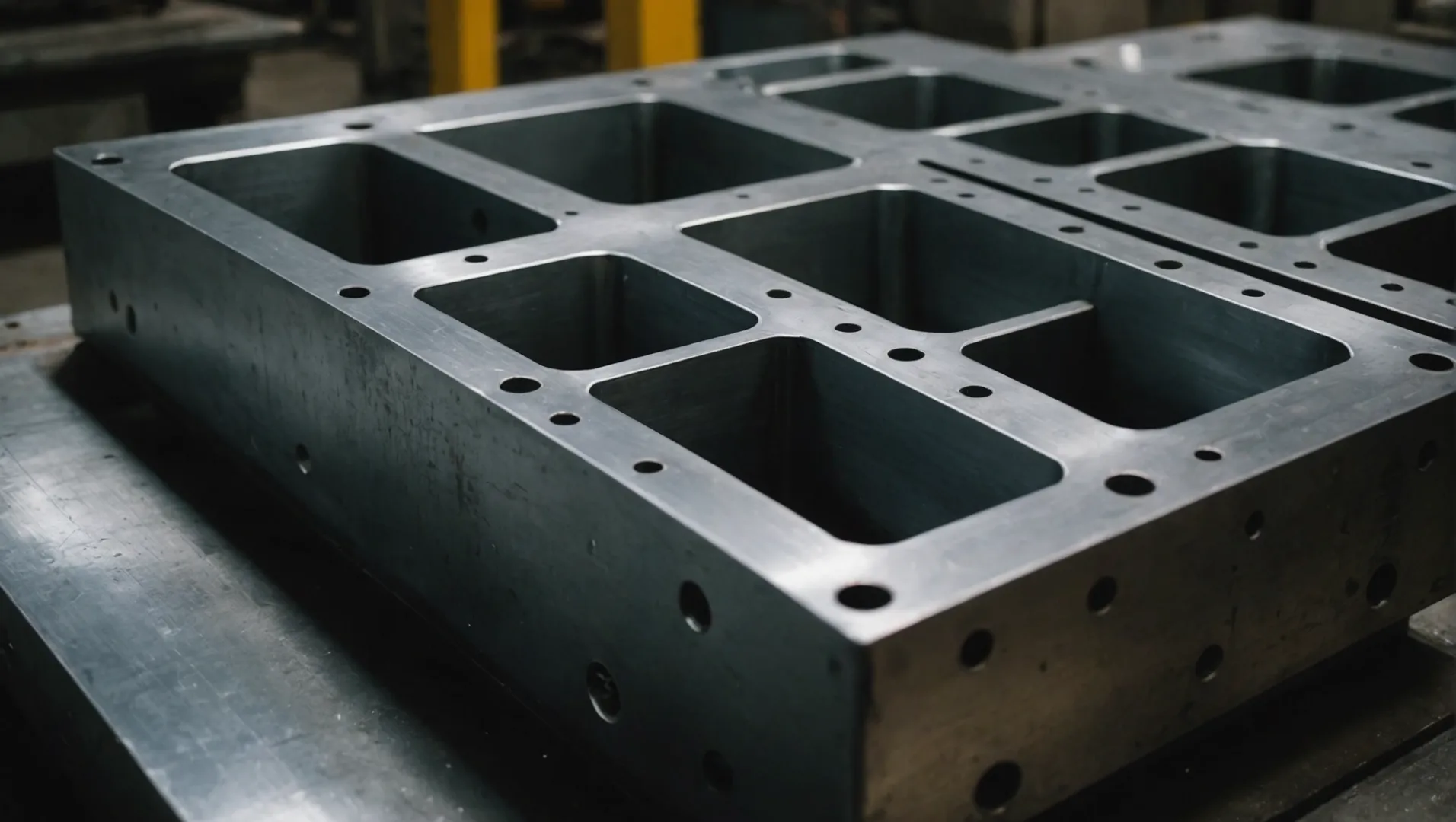
The Importance of Steel Quality in Mold Manufacturing
Choosing the right steel for mold manufacturing is crucial as it determines not only the mold’s durability6 but also its effectiveness and lifespan. High-quality steels like Japanese S136 or Swedish ASSAB are known for their superior performance, including enhanced wear resistance and corrosion resistance, which are essential for molds subjected to continuous use in industrial environments.
Factors Influencing Steel Quality
-
Wear Resistance: High-quality steels generally exhibit excellent wear resistance, which is vital for molds used in high-volume production. This property minimizes deterioration during repetitive cycles, thus maintaining the integrity and precision of the mold over time.
-
Corrosion Resistance: In environments where molds are exposed to moisture or corrosive substances, using steel with high corrosion resistance is beneficial. It prevents degradation and ensures the longevity of the mold.
-
Hardness and Toughness: The balance between hardness and toughness in steel affects its ability to withstand mechanical stresses without deforming or cracking. High-quality steels usually strike this balance effectively, providing both strength and flexibility.
Comparing Costs: Ordinary vs. High-Quality Steel
The choice between ordinary steel and high-quality steel involves a trade-off between upfront costs and long-term value.
Steel Type | Initial Cost | Maintenance Costs | Lifespan | Overall Value |
---|---|---|---|---|
Ordinary Steel | Lower | Higher | Shorter | Cost-effective short term |
High-Quality Steel | Higher | Lower | Longer | Cost-effective long term |
-
Ordinary Steel: While the initial cost of ordinary steel is lower, it often leads to higher maintenance expenses and a shorter lifespan. Such molds might require frequent repairs or replacements, which could increase the overall cost in the long run.
-
High-Quality Steel: The initial investment is higher for high-quality steels, yet they offer longer service life with minimal maintenance. This choice often proves economical over time, particularly for high-volume or precision-demanding applications.
Choosing the Right Steel for Your Project
When selecting mold steel, consider your specific production requirements, such as batch size, precision needs, and environmental conditions. Consulting with experts7 can help you balance cost with performance, ensuring that your investment aligns with your long-term production goals.
High-quality steel reduces long-term mold expenses.True
High-quality steel offers durability, reducing maintenance and replacement costs.
Ordinary steel molds have a longer lifespan than high-quality ones.False
Ordinary steel molds wear out faster, leading to a shorter lifespan.
Conclusion
Understanding the cost factors of ABS plastic injection molds empowers better budgeting and decision-making. Balance complexity, size, precision, and material quality when estimating expenses.
-
Gain insights on how complex designs increase manufacturing challenges.: The design of a part plays a significant role in determining the complexity and cost of the injection mold needed to produce it. ↩
-
Discover how mold size specifically influences mold pricing strategies.: A small and simple single-cavity plastic injection mold usually costs between $1,000 and $5,000. Very large or complex molds may cost as much as $80,000 or more … ↩
-
Explore detailed insights into how mold size alters production costs.: The main determinant of molding cost is the amount of time it takes to produce the tooling. This means, the more complex the part’s geometry, the higher your … ↩
-
Learn about why precision matters in ABS injection molding.: ABS injection molding is a common manufacturing process that involves injecting molten plastic into a mold cavity under high pressure and temperature. ↩
-
Discover how investing in quality impacts long-term success.: A reliable supply of parts and quality production can be ensured by investing in injection molds. Underinvesting can result in mold … ↩
-
Understand why wear resistance matters for mold longevity.: A strong enhancement of the wear resistance can only be achieved by existing of a second harder phase. Of great influence therefore are the carbide content, … ↩
-
Get expert guidance on selecting the right steel for your needs.: For molding materials that do not contain abrasives like glass fibers or corrosive ingredients, P-20 steel is the most common choice. ↩