Have you ever wondered how some manufacturers produce such intricate plastic parts with ease? The secret often lies in a technique known as coring.
Coring in injection molding involves using core pulling mechanisms to efficiently remove parts with complex geometries from molds. This process enhances efficiency by minimizing material waste, reducing cooling times, and improving overall part quality.
While this brief overview highlights the core advantages of coring in injection molding, there is so much more to discover about its mechanisms and applications. Let’s dive deeper!
Coring reduces cooling times in injection molding.True
Coring minimizes material mass, allowing faster heat dissipation and cooling.
What Is Core Pulling in Injection Molding?
Core pulling, also known as the slider or side core operation, plays a crucial role in injection molding for creating complex parts.
Core pulling in injection molding is a mechanism designed to demold parts with features like inner holes or side concaves. It uses sliders, inclined guide pillars, and wedge blocks to ensure the smooth removal of the plastic part from the mold, enhancing efficiency and product quality.
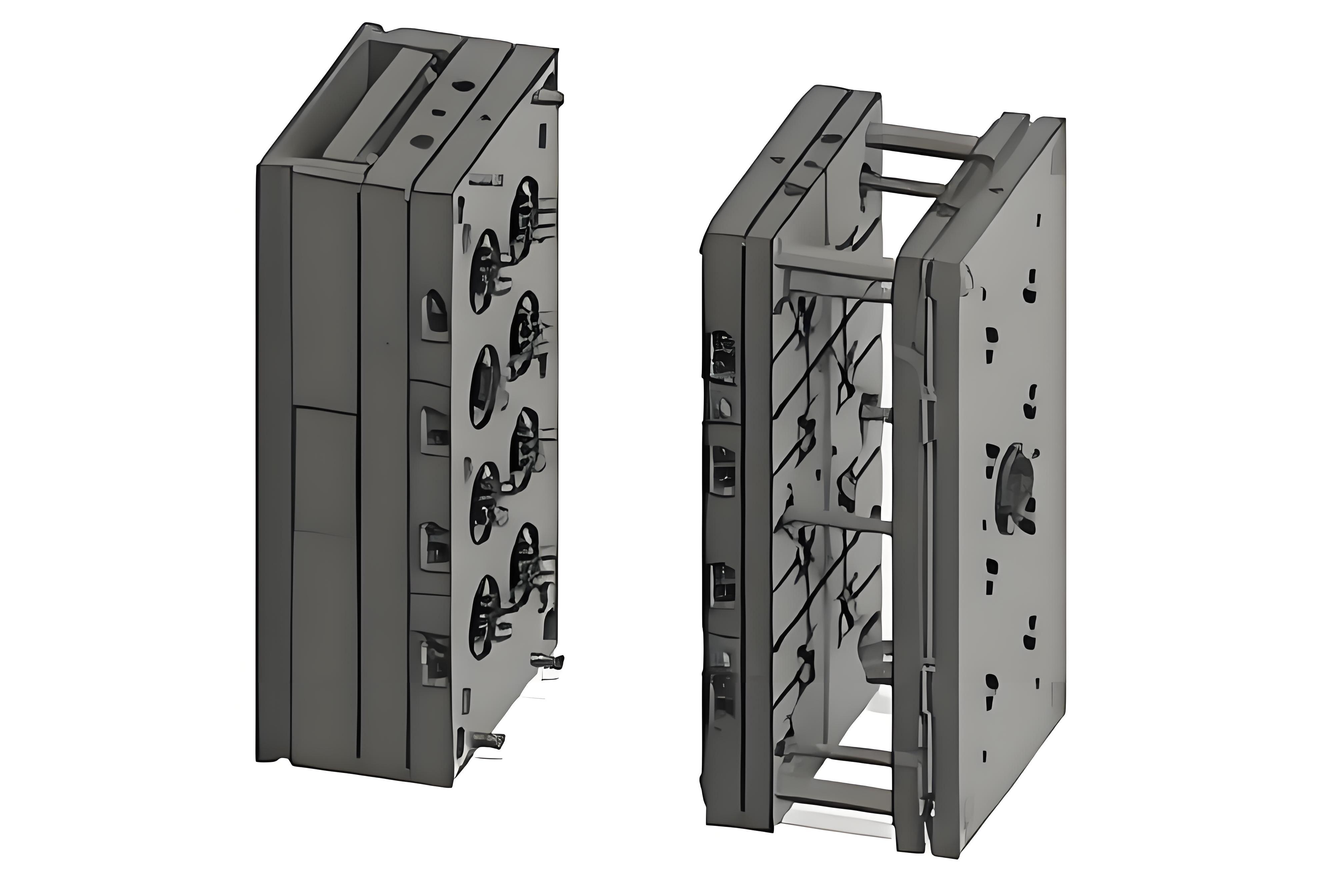
Definition and Function
In the realm of injection molding1, core pulling refers to a specific mechanism integrated into molds to facilitate the demolding of parts with complex geometrical features. These features might include inner holes or side concaves that do not align with the primary mold opening direction. The primary function of core pulling is to retract these side cores during the mold opening process, allowing for seamless ejection of the molded part.
Working Principle
Design Stage
The process begins at the design stage. Engineers assess the part’s shape and determine where core pulling is necessary. They then design a corresponding core pulling mechanism, which typically consists of components such as sliders, inclined guide pillars, and wedge blocks.
Injection Molding Stage
During the injection molding phase, the plastic melt fills the mold cavity, creating the plastic part. At this point, the core pulling mechanism remains in a closed position, forming a complete cavity with the rest of the mold.
Mold Opening Stage
Once the part cools and solidifies, mold opening commences. Here, the inclined guide pin and slider move relative to each other. The angle of the guide pin ensures that the slider moves in a specific direction, effectively pulling the side core out of the plastic part.
Demolding Stage
After successful core pulling, the plastic part can be smoothly extracted from the mold, ensuring high-quality production.
Importance of Core Pulling Mechanisms
Core pulling mechanisms are vital for manufacturing parts with intricate designs without compromising quality or efficiency. By enabling more complex geometries in molded parts, these mechanisms enhance product functionality while minimizing material waste and reducing cooling times.
Moreover, as manufacturers increasingly demand higher precision and efficiency, understanding how core pulling mechanisms work2 becomes essential for optimizing production processes and maintaining competitive advantages.
Core pulling is only for creating inner holes.False
Core pulling also creates side concaves, not just inner holes.
Sliders are part of the core pulling mechanism.True
Sliders help in retracting side cores during mold opening.
How Does Core Pulling Mechanism Work?
Unlocking the intricacies of core pulling in injection molding can significantly boost production efficiency and precision. This mechanism is pivotal for manufacturing complex parts.
Core pulling in injection molding involves a mechanism that facilitates the removal of parts with features like side concaves. It ensures smooth demolding by retracting side cores during mold opening, enhancing production efficiency.
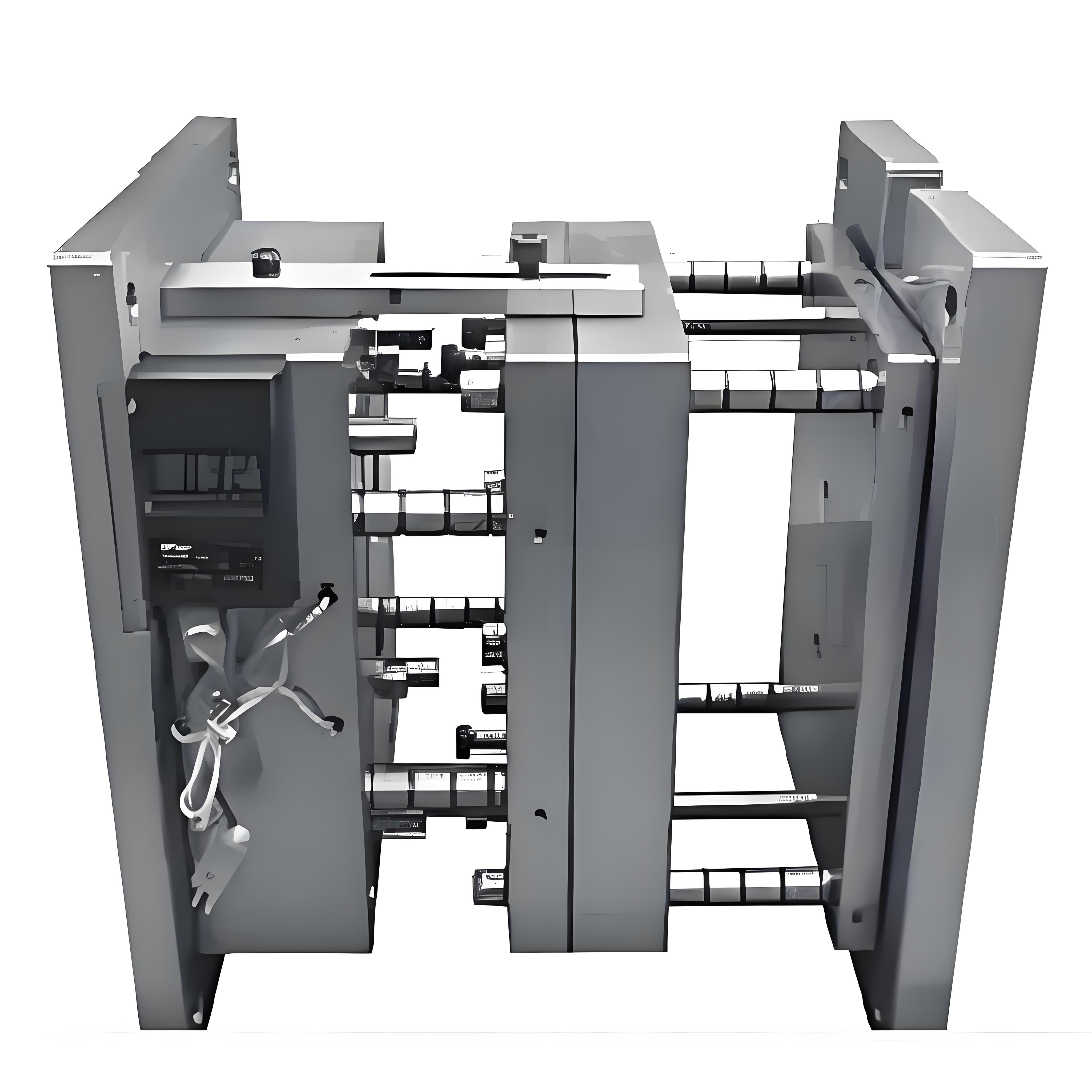
Understanding the Core Pulling Mechanism
In injection molding, the core pulling mechanism is crucial for removing molded parts with intricate designs. The process begins at the design stage, where engineers must identify areas requiring core pulling based on the plastic part’s features. These features could include inner or outer holes or side concave areas not aligned with the mold’s opening direction.
Design Components
The core pulling mechanism typically consists of key components such as sliders, inclined guide pillars, and wedge blocks. These elements work in harmony to facilitate the smooth removal of complex-shaped parts from the mold.
Component | Function |
---|---|
Slider | Moves to pull out the core from the part |
Inclined Guide | Directs slider movement during mold opening |
Wedge Block | Assists in secure positioning and movement |
During the injection molding stage, the mold cavity is filled with plastic melt, forming a complete structure in conjunction with the core pulling mechanism. This setup remains closed until the mold opens.
The Operational Stages
- Injection Stage: The plastic melt fills the cavity, creating a solid structure that incorporates the core pulling mechanism.
- Mold Opening Stage: After cooling and solidification, the mold opens, triggering the inclined guide pin and slider interaction. This interaction causes the side core to retract from the plastic part.
- Demolding Stage: With the side cores retracted, the plastic part can be easily removed from the mold without damage.
Exploring Different Core Pulling Methods
Core pulling methods vary based on production requirements:
- Manual Core Pulling: Ideal for small parts or low production volumes, where manual operation suffices.
- Motorized Core Pulling: Utilizes external power sources, enhancing automation and efficiency for large batches.
- Hydraulic Core Pulling: Employs hydraulic systems for larger parts or extensive core pulling distances, offering smooth and forceful operation.
To explore more about hydraulic systems3, which are integral to motorized core pulling, understanding their advantages can provide insights into enhancing injection molding processes.
Core pulling is only for simple parts.False
Core pulling is used for complex parts with intricate designs.
Sliders help in core pulling during mold opening.True
Sliders retract side cores to facilitate smooth demolding.
What Are the Different Core Pulling Methods?
Core pulling is vital in injection molding, facilitating the removal of complex parts from molds. But what methods are employed?
Core pulling methods in injection molding include manual, motorized, and hydraulic approaches, each catering to different production needs. Manual methods suit small batches, motorized methods boost efficiency for larger runs, and hydraulic techniques offer precision for heavy-duty applications.

Understanding Core Pulling Methods
In the realm of injection molding4, core pulling is a technique designed to extract plastic parts with intricate features like side holes or projections that do not align with the mold’s main opening direction. This mechanism not only ensures efficient demolding but also significantly influences the quality and precision of the final product.
1. Manual Core Pulling
- Application: Ideal for small-scale productions or prototypes.
- Mechanism: This involves manually operating the side cores to disengage them from the molded part.
- Advantages: Cost-effective with minimal setup requirements.
- Challenges: Limited to smaller parts and less efficient for large-scale operations.
2. Motorized Core Pulling
- Application: Suitable for medium to large production runs.
- Mechanism: Utilizes mechanical forces such as gears or motors to automate core pulling.
- Advantages: Enhances efficiency and consistency across production cycles.
- Challenges: Requires a more sophisticated setup and maintenance regime.
3. Hydraulic Core Pulling
- Application: Best suited for large, complex parts with demanding precision needs.
- Mechanism: Employs hydraulic systems to exert controlled force during the core pulling phase.
- Advantages: Offers smooth operation with significant pulling force, ideal for detailed parts.
- Challenges: Higher initial investment and complexity in design and maintenance.
Selecting the Right Method
Choosing the appropriate core pulling method depends on various factors including:
- Production Volume: Manual methods work well for low-volume, custom orders, whereas hydraulic systems are beneficial for mass production.
- Part Complexity: Complex designs with intricate details may require the precision and power of hydraulic systems.
- Budget Constraints: Manual methods are cost-effective for smaller operations, whereas motorized and hydraulic systems represent a more substantial investment.
Table: Core Pulling Methods Overview
Method | Best For | Key Benefits | Challenges |
---|---|---|---|
Manual | Small batches, prototypes | Low cost, easy setup | Limited to small parts |
Motorized | Medium to large production runs | Efficiency, consistency | Requires advanced setup |
Hydraulic | Large, complex parts | High precision, force | High initial cost |
By understanding the distinct core pulling methods5, manufacturers can optimize their injection molding processes, enhancing both efficiency and product quality. This knowledge is crucial for making informed decisions that align with production goals and financial considerations.
Manual core pulling suits small-scale production.True
Manual methods are cost-effective and ideal for prototypes or low-volume runs.
Hydraulic core pulling is best for small parts.False
Hydraulic methods are suited for large, complex parts requiring precision.
What Considerations Are Essential for Effective Core Pulling?
Core pulling is crucial in injection molding, facilitating the removal of parts with complex geometries. Effective core pulling demands careful attention to design, precision, and maintenance.
Effective core pulling requires a well-designed mechanism, precision control, and regular maintenance to ensure reliable and smooth operation, thus preventing defects and damage.
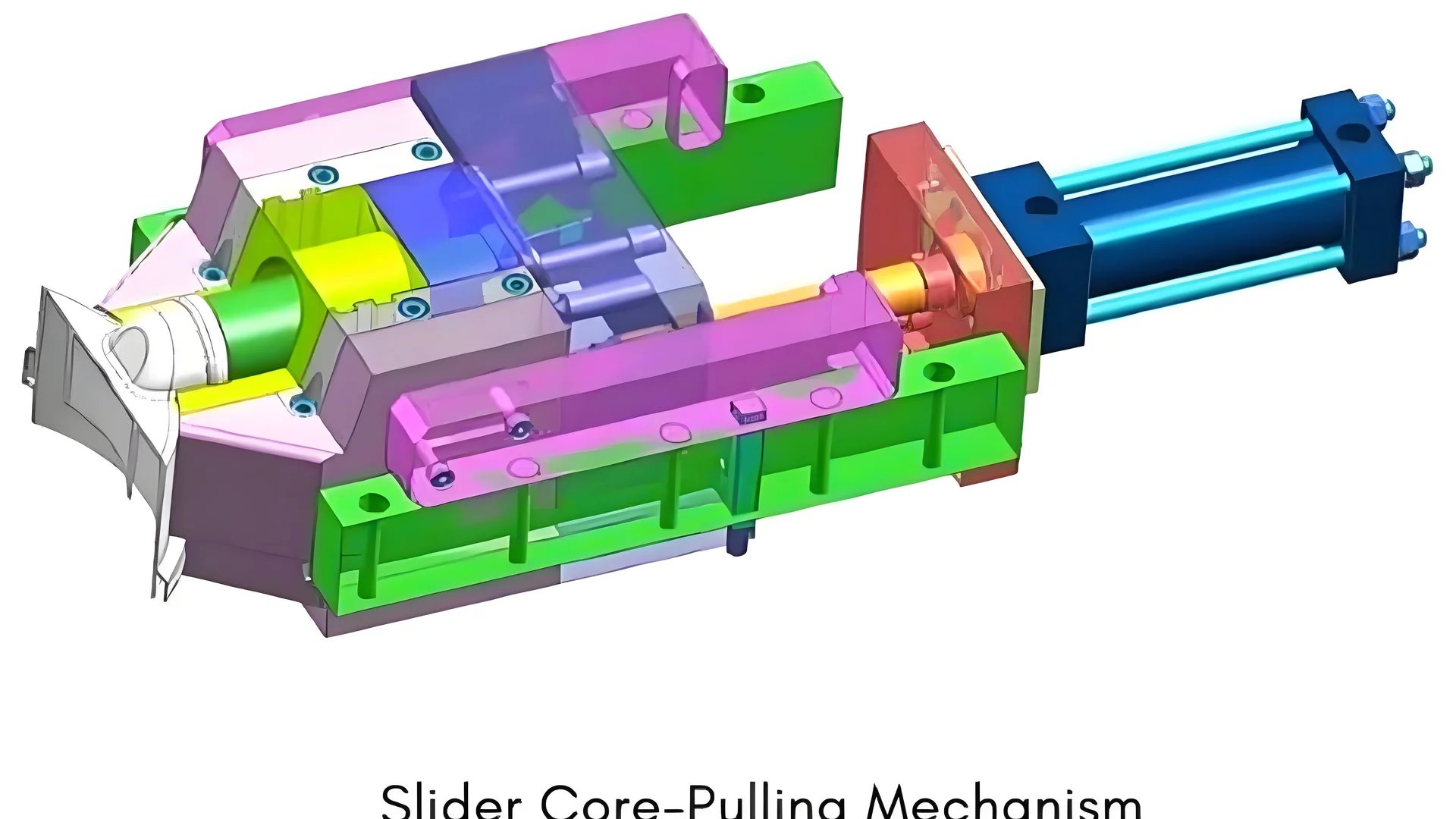
Design Considerations
One of the foremost considerations in effective core pulling is the design of the core pulling mechanism. The design must account for the specific features of the plastic part, such as inner holes or side concavities, that require core pulling. A well-thought-out design ensures that the mechanism can operate without jamming or causing damage to the mold or the part.
Key Design Elements:
- Sliders and Guide Pillars: The choice of sliders and inclined guide pillars is critical. These components must be robust enough to handle the stress of repeated use while maintaining alignment.
- Wedge Blocks: Used to ensure the sliders return to their original position after operation.
An effective design minimizes wear and tear, extending the lifespan of the mold. This approach also aligns with improving production efficiency by reducing downtime due to malfunctions.
Precision Control
Precision is another critical factor in core pulling. The mechanism must be capable of exact movements to maintain the integrity of the plastic part. High precision ensures that parts meet dimensional and surface quality requirements.
To achieve this:
- Maintain Tight Tolerances: Ensuring tight tolerances between the slider and other parts can prevent misalignment and ensure smooth operation.
- Use of High-Quality Materials: Selecting durable materials for the core pulling mechanism can improve longevity and performance.
Maintenance Requirements
Regular maintenance is essential to keep the core pulling mechanism functioning optimally. Maintenance involves checking components for wear, lubricating moving parts, and replacing any damaged elements promptly.
Maintenance Best Practices:
- Scheduled Inspections: Regularly scheduled inspections can identify wear before it leads to a malfunction.
- Component Replacement: Timely replacement of worn or damaged components prevents breakdowns.
By adhering to these maintenance practices, manufacturers can ensure that their core pulling systems operate efficiently, minimizing costly production interruptions and ensuring consistent part quality.
While understanding these considerations is vital, exploring the diverse core pulling methods6 used across different production scales can further enhance operational efficiency.
Sliders and guide pillars prevent core pulling misalignment.True
Sliders and guide pillars maintain alignment, preventing misalignment issues.
Regular maintenance of core pulling mechanisms is unnecessary.False
Regular maintenance prevents breakdowns and ensures efficient operation.
Conclusion
Embracing coring techniques can significantly improve your injection molding efficiency. By reducing waste and ensuring smooth demolding, you can enhance both production quality and output.
-
Understand the basics of injection molding processes and their components.: what injection molding is, what the injection molding machine looks like, and how the injection … ↩
-
Explore detailed working principles of core pulling mechanisms.: Here are 15 types of side core pulling mechanisms for injection mold. It includes four types … ↩
-
Learn how hydraulic systems enhance precision in injection molding.: The basic operation involved two halves of a mold, mounted on supporting platens, being clamped together at high pressure using hydraulic cylinders. ↩
-
Gain foundational insights into injection molding basics.: what injection molding is, what the injection molding machine looks like, and how the injection … ↩
-
Explore detailed descriptions of core pulling techniques.: Here are 15 types of side core pulling mechanisms for injection mold. It includes four types … ↩
-
Learn about various core pulling methods to optimize production efficiency.: Here are 15 types of side core pulling mechanisms for injection mold. It includes four types … ↩