Ever wonder what makes injection molding tick? It’s all about the core and cavity sides.
In injection molding, the core side forms the internal features and the cavity side shapes the external surfaces, together determining the final part’s geometry.
Think of it like this: imagine making a complex jigsaw puzzle, where each piece must fit perfectly into the next. The core and cavity sides of an injection mold are like those interlocking pieces. When I first started learning about mold design, I remember being fascinated by how these two components worked together to create something whole. Understanding their distinct roles isn’t just technical know-how; it’s about seeing how every detail comes together to form a seamless product. As you dive deeper into this, you’ll find that mastering these differences can elevate your design and manufacturing processes to new heights, enhancing not only production efficiency but also the quality of your products.
The core side forms the internal features in injection molding.True
The core side shapes the internal aspects of the molded part.
The cavity side shapes the internal surfaces of the product.False
The cavity side actually shapes the external surfaces.
- 1. How Do Core and Cavity Sides Influence Part Design?
- 2. What Materials Are Best for Core and Cavity Construction?
- 3. How Does Temperature Control Differ Between Core and Cavity?
- 4. What Are Common Issues with Core and Cavity Alignment?
- 5. How Do Core and Cavity Sides Influence Cooling Time?
- 6. Why Is Maintenance Important for Core and Cavity Sides?
- 7. Conclusion
How Do Core and Cavity Sides Influence Part Design?
Diving into the dynamics of core and cavity sides in part design is like unlocking a secret code that transforms everyday objects into precise, reliable products.
Core and cavity sides impact part design by shaping internal and external features, respectively, affecting structural strength, surface quality, and manufacturing ease.
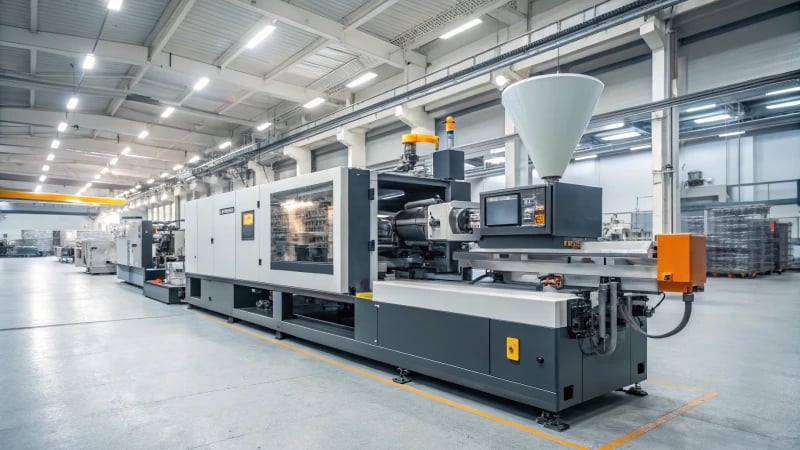
Understanding Core and Cavity Dynamics
When I first started exploring the world of injection molding, I was fascinated by how the core and cavity sides worked together to shape a product. The core side forms those intricate interior features1 that you might not see at first glance, like hidden chambers or delicate recesses. On the other hand, the cavity side takes charge of crafting the outer surfaces that everyone admires.
Influence on Aesthetics and Functionality
In my experience, getting the aesthetics right is a delicate dance. The cavity side often demands a high-quality finish2, which can be as critical as choosing the right paint for a masterpiece. Meanwhile, the core side keeps its focus on functionality, ensuring every support structure or rib is precisely where it needs to be.
Aspect | Core Side | Cavity Side |
---|---|---|
Surface | Interior features | Exterior features |
Focus | Structural integrity | Aesthetics and texture |
Complexity | Easier ejection | May require additional cooling |
Manufacturing Considerations
Designing for manufacturability is where art meets science. I’ve learned that a thoughtfully designed core can make ejection a breeze, shaving precious seconds off each cycle. Meanwhile, the cavity sometimes needs clever cooling channels3 to keep everything from going wonky due to warping.
- Draft Angles: Getting these right on the cavity side can be the difference between a smooth release and a sticky situation.
- Cooling Efficiency: Even though the core might not need as much cooling, it’s essential to optimize its thermal management.
Mitigating Common Pitfalls
Over the years, I’ve encountered my fair share of hiccups. Challenges like:
- Part Shrinkage: It’s like trying to predict how much your favorite shirt will shrink in the wash—it varies between core and cavity sides due to cooling differences.
- Warpage: Especially annoying if cooling isn’t even across the cavity.
By keeping these aspects in mind, I’ve found that not only does part quality improve but so does production efficiency, setting up each project for success. It’s a rewarding feeling when all the pieces come together seamlessly in the molding process.
The core side defines a part's exterior features.False
The core side shapes the interior features, not the exterior.
Cavity sides often require additional cooling to prevent warping.True
The cavity side may need extra cooling to manage thermal expansion and prevent warping.
What Materials Are Best for Core and Cavity Construction?
Ever found yourself staring at a mold design and wondering if you’ve picked the right materials for the job? I’ve been there too.
For core and cavity construction, tool steels like P20 and H13 and beryllium copper alloys are ideal due to their durability, machinability, and thermal conductivity, ensuring high-quality molds.
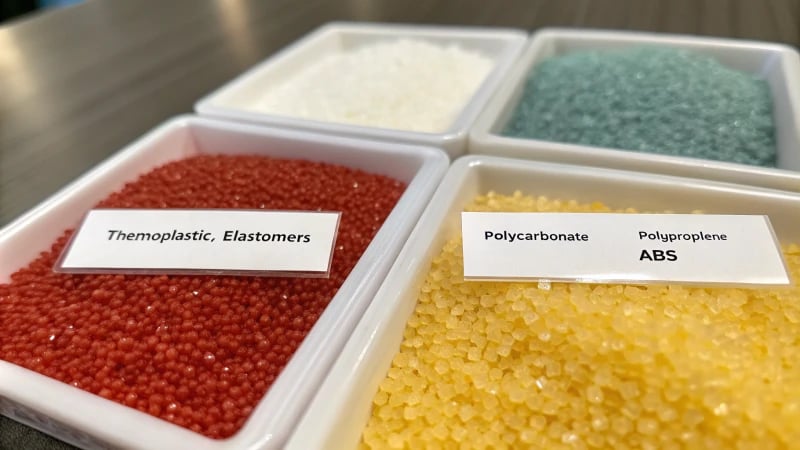
Understanding Material Properties
Reflecting on my early days in mold design, the decision to choose the right materials was daunting. It’s like picking the perfect recipe ingredients; each one plays a critical role in the final product. In mold construction, factors like thermal conductivity4, hardness, and machinability become pivotal.
Tool Steels
P20 Steel: When I first started using P20 steel, I was impressed by its machinability. It strikes a fine balance between strength and cost, making it ideal for moderate production runs—perfect for projects that don’t require the toughest materials but still demand reliability.
H13 Steel: In contrast, H13 has been my go-to for high-volume projects. Its resistance to thermal fatigue and cracking is like having an insurance policy for your molds—especially when you’re dealing with demanding production schedules.
Tool Steel | Benefits | Best Used For |
---|---|---|
P20 | Good machinability, durable | Moderate production |
H13 | Thermal fatigue resistance | High-volume runs |
Beryllium Copper Alloys
These alloys are like the unsung heroes of my toolkit. Their thermal conductivity is unmatched, helping reduce cycle times in molding operations by efficiently dissipating heat. I remember a particular project where switching to beryllium copper dramatically cut down our production time.
Comparing Material Costs
I’ve learned that while tool steels are generally more budget-friendly, beryllium copper can seem pricey initially. However, the savings come in the form of reduced cycle times—a significant advantage when speed is of the essence. Evaluating material costs5 versus potential efficiency gains is a strategy I’ve seen pay off time and again.
Material | Average Cost | Efficiency Gains |
---|---|---|
Tool Steels | Lower | Standard |
Beryllium Copper | Higher | Reduced cycle time |
Practical Application Insights
Over the years, I’ve gathered that experienced mold designers recommend assessing specific project requirements like desired surface finish and expected mold lifespan. Consulting with industry experts6 has helped me tailor material choices to fit project needs perfectly. It’s these insights that can really optimize your mold’s performance and longevity.
P20 steel is ideal for high-volume production.False
P20 steel is better suited for moderate production due to its machinability.
Beryllium copper alloys reduce cycle times in molding.True
Their excellent thermal conductivity helps dissipate heat efficiently.
How Does Temperature Control Differ Between Core and Cavity?
Ever wondered how the subtleties of heat can make or break a product in injection molding? It’s all about mastering the temperature dance between the core and cavity. Let’s unravel these thermal mysteries together!
In injection molding, the core cools slower due to higher thermal mass, while the cavity needs faster cooling for precise surface quality.
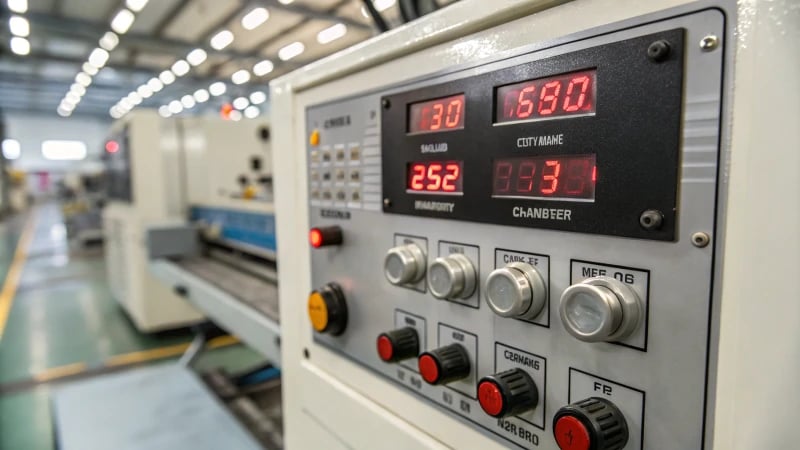
Understanding the Core and Cavity
When I first started exploring the world of injection molding, it felt like stepping into a symphony of heat and precision. The core and cavity are like the maestro’s baton, directing every nuance of the final product. The core7 is responsible for shaping those intricate internal features, while the cavity crafts the sleek external contours. Their temperature control isn’t just important—it’s essential to getting that perfect piece out of the mold.
Component | Role | Material Contact |
---|---|---|
Core | Shapes internal features | More prolonged |
Cavity | Shapes external features | Brief contact |
Thermal Dynamics: Core vs. Cavity
I remember the first time I realized that the core and cavity aren’t just static pieces of metal; they’re dynamic players in a thermal ballet. Each has its own rhythm when it comes to heat transfer.
-
Core Temperature Control
- Thermal Mass: Like a slow, deliberate waltz, the core takes its time cooling down due to its higher thermal mass. This gradual process ensures dimensional stability and wards off warping issues8.
- Cooling Strategy: We often use cooling channels in cores to spread out heat dissipation evenly, like a gentle breeze cooling down a hot summer day.
-
Cavity Temperature Control
- Surface Precision: The cavity dances to a faster beat, requiring precise temperature control to achieve that flawless surface finish.
- Rapid Cooling: Quick cooling is key here, reducing cycle times while keeping the surface texture consistently top-notch.
Methods to Optimize Temperature Control
I’ve seen firsthand how sophisticated cooling methods can transform production efficiency. By leveraging advanced systems tailored to each component, we can finesse every detail of temperature management:
- Advanced Cooling Systems: Techniques like conformal cooling9 are game-changers, allowing for unparalleled temperature uniformity.
- Material Considerations: Choosing materials with the right thermal conductivity can make all the difference in effective heat transfer, impacting both core and cavity strategies.
Table: Temperature Control Techniques
Method | Application |
---|---|
Conformal Cooling | Core & Cavity |
Thermal Conductivity | Material Choice |
By grasping these differences, we mold designers can fine-tune both core and cavity settings to not only enhance product quality but also cut down on production time. To dive even deeper into these techniques, exploring advanced resources10 can offer practical applications in mold design.
Industry Implications
For pros like Jacky, understanding these nuances isn’t just academic—it’s a career boost. With cutting-edge temperature control strategies, we can elevate both the aesthetic and functional qualities of products, significantly improving manufacturing efficiency. As tech evolves, staying updated with innovations like intelligent mold monitoring systems is crucial to staying ahead in this competitive field. Let’s keep pushing those boundaries!
Core has higher thermal mass than cavity in injection molding.True
The core's higher thermal mass leads to slower cooling rates.
Cavity cooling is slower than core cooling in injection molding.False
Cavity requires faster cooling for surface precision and reduced cycle time.
What Are Common Issues with Core and Cavity Alignment?
Imagine spending hours on a design, only to find alignment issues ruining everything.
Common core and cavity alignment issues in injection molding include parting line mismatches, flash, and uneven walls, typically caused by incorrect machine settings, mold wear, or poor design, impacting quality and efficiency.
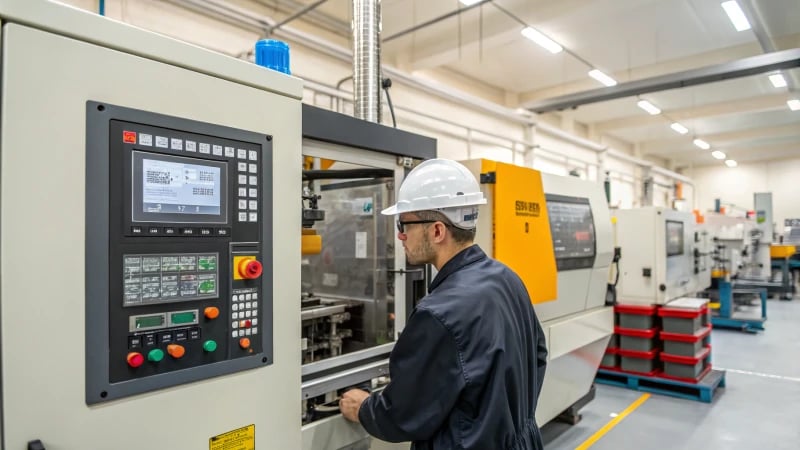
I remember the first time I faced a major hiccup with core and cavity alignment in my designs. It was like watching a beautifully crafted puzzle fall apart because one piece just wouldn’t fit right. Let’s dive into some common issues that can turn our precision crafting into a frustrating challenge.
Understanding Parting Line Mismatches
A parting line11 mismatch is more than just an aesthetic flaw; it can undermine the very function of our product. I learned this the hard way when a slight misalignment led to a batch of products being returned due to visible defects.
Causes of Parting Line Mismatches
- Machine Calibration: I realized that even a small oversight in calibration could throw everything off.
- Mold Wear: Over time, wear and tear can sneak up on us, affecting that perfect fit.
- Improper Setup: Setting up molds requires precision—any error here can lead to misalignment.
Flash Formation
Flash isn’t just an inconvenience; it adds to production time and cost. I recall a project where high injection pressure caused flash at the seams, leading to hours of extra work.
Cause | Impact |
---|---|
High Injection Pressure | Causes flash at weak points |
Poor Mold Design | Results in gaps between core and cavity |
Flash formation requires additional finishing work, increasing production time and costs.
Uneven Wall Thickness
Uneven wall thickness plagued one of my early projects, teaching me the importance of temperature control and proper insert alignment.
Factors Contributing to Uneven Walls:
- Temperature Variations: I found that inconsistent temperatures could create unexpected flow issues.
- Misaligned Inserts: Even a minor misalignment can lead to structural weaknesses.
Regular maintenance and thoughtful design are our best friends here. Using advanced simulation tools12 and CAD software helped me anticipate these issues, saving headaches down the road. By modeling and analyzing core and cavity fitment accurately, we can catch potential problems before they disrupt production.
Parting line mismatches only affect aesthetic quality.False
They also impact functional integrity, not just aesthetics.
Flash formation can increase production costs.True
Flash requires extra finishing work, raising production time and expenses.
How Do Core and Cavity Sides Influence Cooling Time?
Ever wondered how the core and cavity sides play a role in cooling during injection molding? Let’s unravel this mystery together!
Core and cavity sides affect cooling time in injection molding by impacting heat dissipation. Proper design and material selection can optimize cycle times and improve part quality.
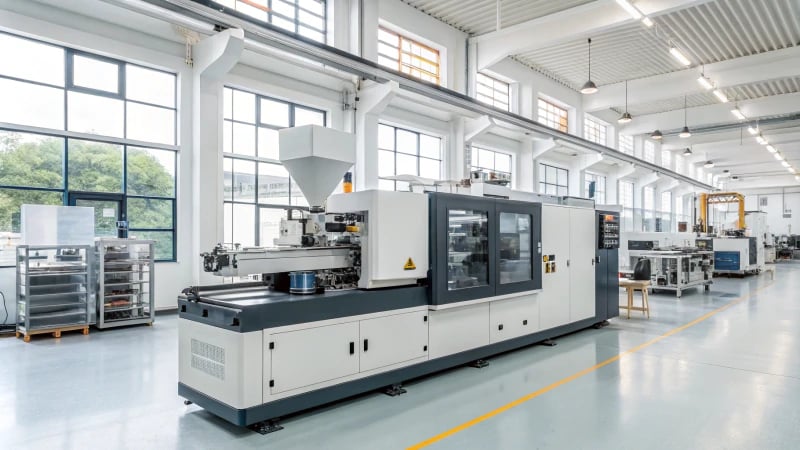
The Role of Core and Cavity in Heat Dissipation
Imagine standing at the helm of a grand orchestra. Each instrument needs to be perfectly timed to create a harmonious melody. This is quite similar to the relationship between core and cavity sides in injection molding. The cavity, being more exposed, cools faster—like the violins leading with a brisk tempo. Meanwhile, the core holds onto the heat a bit longer, akin to the deep, resonant cellos anchoring the rhythm.
Material Selection
I’ve spent countless hours pondering over material choices, like a chef selecting ingredients for a perfect dish. When it comes to cooling efficiency, metals with high thermal conductivity, such as copper alloys, are like the secret spices that quicken heat transfer and reduce cooling time. But just like how I must consider the budget for my favorite recipes, cost and durability considerations13 are crucial here too.
Material Type | Thermal Conductivity (W/m·K) | Cost Efficiency |
---|---|---|
Copper Alloy | 401 | High |
Aluminum | 205 | Moderate |
Steel | 50 | Low |
Design Strategies
Have you ever tried to find the perfect spot for your living room couch? That’s exactly how I feel when strategically placing cooling channels in a mold. Channels that hug the core closely are key to reducing cooling time. And just as I might use feng shui to arrange my furniture, conformal cooling techniques align perfectly with the mold contours to boost efficiency.
Balancing Cycle Times and Quality
Striking a balance between productivity and quality feels like walking a tightrope. I’ve learned that while it’s tempting to focus solely on reducing cycle time, maintaining part quality is equally vital. Poor cooling management can lead to defects like warping or shrinkage—akin to skipping crucial plot points in a story. By analyzing these factors, I can ensure a seamless production process where both cooling efficiency14 and part quality are prioritized.
As technology advances, exploring new tools like simulation software offers exciting possibilities for optimizing core and cavity design even further.
Cavity side cools faster than core side in molding.True
The cavity is exposed to more cooling channels, dissipating heat quicker.
Steel has higher thermal conductivity than copper alloy.False
Copper alloy has a higher thermal conductivity (401 W/m·K) than steel (50 W/m·K).
Why Is Maintenance Important for Core and Cavity Sides?
Ever wondered why keeping the core and cavity sides in tip-top shape is a game-changer for mold designers like me?
Maintaining core and cavity sides in injection molding is essential to ensure part quality, extend mold life, reduce downtime, prevent defects, enhance efficiency, and optimize production.
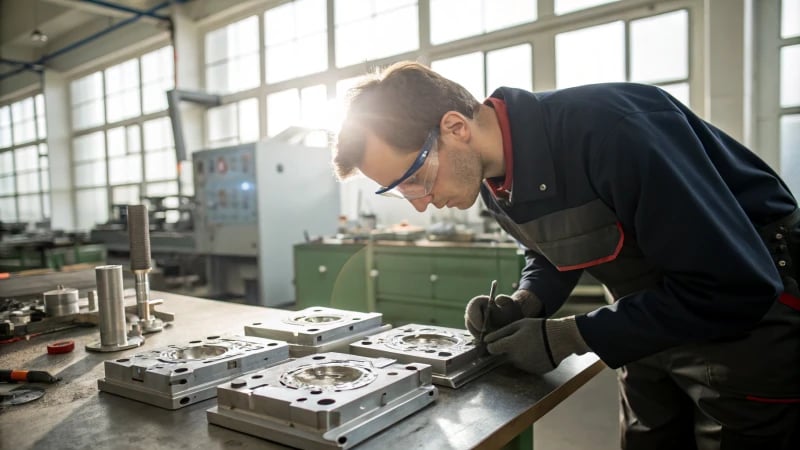
The Role of Core and Cavity Sides
I remember when I first delved into injection molding15—it felt like stepping into a world where precision was king. Core and cavity sides are at the heart of this process, shaping the final product’s every detail. Imagine trying to bake a cake without a properly shaped pan; the result would be a mess. That’s how I see these mold components—they’re the backbone that ensures each part comes out flawlessly, meeting the high standards my job demands.
Preventing Defects through Maintenance
Flashbacks of those frantic days when production halted due to defects still haunt me. Routine maintenance has since become my mantra, significantly minimizing issues like flash, warping, or short shots. A simple routine—keeping core and cavity surfaces free from wear or scratches—has saved me from countless headaches. By sticking to a regular inspection schedule, I’ve been able to catch potential problems early, much like a detective solving a mystery before it’s too late.
Maintenance Task | Frequency | Importance |
---|---|---|
Surface Cleaning | Weekly | Removes residue that can affect surface finish |
Lubrication | Monthly | Prevents wear on moving parts |
Alignment Check | Quarterly | Ensures accurate part production |
Extending Mold Lifespan
Every time I think about replacing a mold, I shudder at the cost. Regular maintenance has been my saving grace, stretching the lifespan of molds and sparing me from costly replacements. Investing time in caring for these core and cavity sides isn’t just about keeping things running smoothly—it’s about maintaining the high standards that have been the hallmark of my career.
Optimizing Production Efficiency
There’s nothing quite like the satisfaction of seeing a production cycle run without a hitch. With well-maintained molds, interruptions are fewer, boosting efficiency and ensuring consistent output. I’ve learned that a proactive maintenance strategy is my best ally in achieving this seamless performance.
Best Practices for Maintenance
Adopting best practices feels like following a trusted recipe—it ensures my molds remain in peak condition. From using non-abrasive cleaners to keeping meticulous records of maintenance activities, I’ve learned these habits help anticipate issues before they spiral out of control.
Best Practice | Benefits |
---|---|
Use of Non-abrasive Cleaners | Prevents surface damage |
Regular Inspection | Early detection of potential issues |
Documentation of Activities | Tracks mold history and predicts maintenance needs |
For those who want to dive deeper into why maintenance is so vital, exploring extended mold lifespan strategies16 could be enlightening. Proper maintenance not only ensures quality but also significantly cuts costs by preventing unnecessary repairs and defects.
Core and cavity maintenance prevents mold defects.True
Regular maintenance avoids defects like flash and warping, ensuring quality.
Skipping maintenance increases mold lifespan.False
Regular upkeep is crucial for extending mold life, not skipping it.
Conclusion
The core and cavity sides in injection molding play distinct roles, shaping internal and external features respectively, influencing product quality, efficiency, and manufacturing processes.
-
Explore how core side designs affect interior part features like holes or ribs for added functionality. ↩
-
Discover techniques to achieve superior finishes on cavity sides for better product aesthetics. ↩
-
Learn about optimizing cooling channel placement to reduce defects such as warping. ↩
-
Explore why thermal conductivity is crucial in mold materials and how it impacts production efficiency. ↩
-
Learn about the cost differences between tool steels and beryllium copper to make informed budgeting decisions. ↩
-
Discover how expert consultation can help you choose the best materials tailored to your specific project needs. ↩
-
This link provides insights into how the core shapes internal features, which is crucial for understanding its cooling requirements. ↩
-
Learn strategies to prevent warping, ensuring dimensional stability during cooling. ↩
-
Explore how conformal cooling improves temperature uniformity, crucial for both core and cavity. ↩
-
Discover comprehensive resources on advanced temperature control methods for mold design. ↩
-
Learn about parting line mismatches causes to improve mold quality control and reduce defects. ↩
-
Discover how simulation tools can predict and prevent alignment problems in mold design. ↩
-
Learn why copper alloys are preferred for injection molding due to their high thermal conductivity, which aids in reducing cooling time. ↩
-
Explore methods to maintain product quality while optimizing cooling efficiency, ensuring high-quality molded parts. ↩
-
Explore how core and cavity sides influence product quality and design. ↩
-
Discover how proper maintenance prolongs mold life and reduces costs. ↩