I remember my early days in mold design, struggling with core and cavity placement, and realizing how pivotal it was for successful results.
Best practices for core and cavity placement in injection molding involve precise alignment, strategic parting line placement, balanced wall thickness, and designing for easy mold release, all to minimize defects, reduce cycle time, and enhance product quality.
Thinking back to those initial challenges, I learned that while these core principles are essential, diving deeper into advanced techniques really made a difference in my projects. Understanding material-specific nuances and adopting innovative strategies can truly transform how designs meet both aesthetic and functional goals. Let’s explore how you can achieve that level of precision.
Proper alignment minimizes injection molding defects.True
Ensuring proper alignment reduces misalignment issues, leading to fewer defects.
Balanced wall thickness increases cycle time in molding.False
Balanced wall thickness actually reduces cycle time by ensuring uniform cooling.
- 1. How Does Parting Line Location Affect Mold Design?
- 2. How Does Wall Thickness Influence Core and Cavity Placement?
- 3. Why Is Alignment Crucial for Core and Cavity Success?
- 4. How Does Material Choice Affect Core and Cavity Design?
- 5. What Are Common Challenges in Core and Cavity Placement?
- 6. How Does Technology Enhance Core and Cavity Layouts?
- 7. Conclusion
How Does Parting Line Location Affect Mold Design?
Ever wondered how a simple decision can change everything? In mold design, choosing the right parting line location is one of those decisions. It can transform your product’s look and feel while boosting production efficiency.
Parting line location in mold design affects aesthetics, functionality, and production efficiency, ensuring smooth operations and improved product quality.
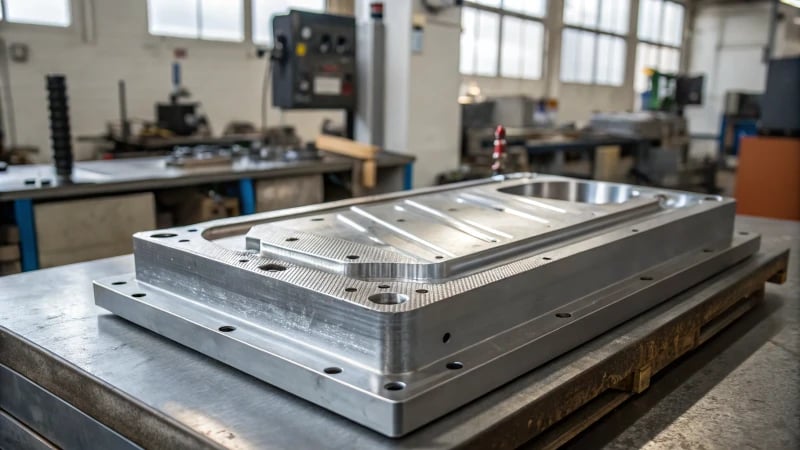
Understanding the Basics of Parting Lines
When I first started learning about mold design, the concept of a parting line seemed like a minor detail. But oh, how wrong I was! A parting line is where the two halves of a mold meet, and its position can make or break your design. It affects how easily the mold opens1 and closes, which in turn influences overall production efficiency.
-
Aesthetic Considerations:
- Visibility of the parting line on the final product. I remember a time when a misplaced line resulted in an unsightly seam on an otherwise perfect product.
- Potential for flash, which needs post-processing. I’ve had to spend hours correcting flash issues because of poor planning.
-
Functional Considerations:
- Sealing efficiency of the mold. A misaligned parting line once led to leaks, causing a headache during assembly.
- Alignment with other design features.
Factors Influencing Parting Line Location
I’ve learned through trial and error that several factors come into play when determining where that critical line should be:
Factor | Description |
---|---|
Geometry | Complex shapes may require multiple parting lines |
Material | Different materials may respond differently |
Draft Angle | Sufficient draft ensures easy ejection |
Impact on Mold Design Process
Choosing the right parting line location is like piecing together a puzzle:
-
Tooling Costs:
- Complex locations may increase costs. I’ve faced budget overruns because of underestimated complexities.
-
Cycle Time:
- Easier separation can reduce cycle time. Efficient designs have saved me countless hours on the production floor.
-
Surface Finish:
- Improper placement might lead to defects. I recall a project nearly derailed by poor surface finish issues due to wrong parting lines.
To explore more about parting line types2 and their specific applications, you can enhance your design strategies significantly. Analyzing these aspects has helped me refine my designs, ensuring they are cost-effective and high-quality.
By considering these factors, I’ve learned to strike a balance between cost, time, and quality in my designs. Understanding different scenarios where parting lines are pivotal can aid in making informed design decisions. I highly recommend looking into advanced CAD techniques3 to simulate these effects early in the design phase, thus avoiding costly redesigns later on.
Parting line affects mold opening and closing efficiency.True
The parting line's position impacts how smoothly a mold opens and closes.
Complex parting lines always decrease tooling costs.False
Complex parting lines typically increase tooling costs due to design intricacies.
How Does Wall Thickness Influence Core and Cavity Placement?
Ever wondered why your designs don’t always come out just right? It might have a lot to do with something as simple as wall thickness.
Wall thickness affects core and cavity placement by influencing cooling, material flow, and integrity. Proper design prevents defects like warping and sink marks, ensuring efficient, high-quality injection molding.
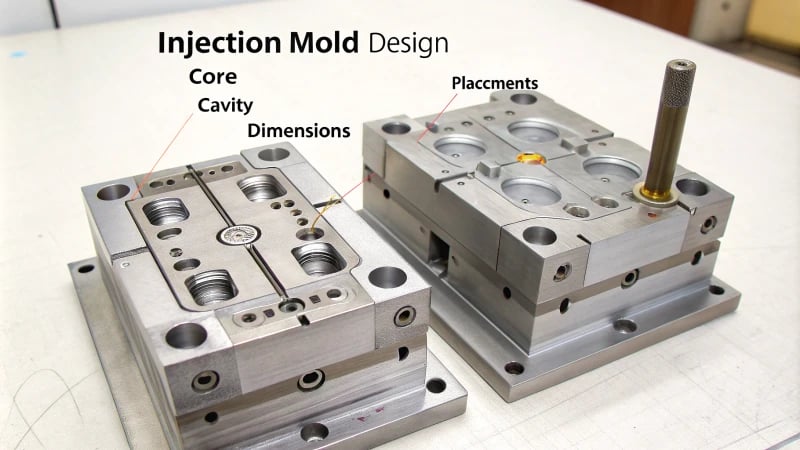
Understanding Wall Thickness and Its Implications
I remember the first time I realized how important wall thickness was in my designs. It was a project for a sleek, new gadget casing. Everything seemed perfect on paper, but the final product had annoying defects like warping. That’s when it hit me—wall thickness wasn’t just a minor detail; it was a game-changer.
In injection molding, wall thickness determines the strength, weight, and durability of the product. Uniform thickness is like a secret weapon against defects such as warping or sink marks. However, thicker walls take their sweet time to cool down, which can lead to uneven cooling issues4.
Aspect | Impact |
---|---|
Strength | Increases with thickness |
Cooling Time | Longer with thicker walls |
Material Usage | Higher with increased thickness |
Defect Risk | Sink marks more likely with thicker walls |
Core and Cavity Placement Considerations
The placement of core and cavity in mold design is like playing chess—strategic and crucial. Wall thickness directly influences this placement because it affects how the material flows. Proper placement ensures that the mold fills optimally, preserving product integrity5. I’ve learned to always consider the flow path and avoid areas where material might pool like a stubborn puddle.
Balancing Design and Functionality
Finding the sweet spot between design aesthetics and functionality is every designer’s challenge. I recall working on a design with thick walls to boost structural integrity, only to find out it compromised cooling efficiency6. On the flip side, thin walls cooled faster but couldn’t handle the pressure, leading to weaknesses. We have to weigh these factors carefully to create products that not only perform well but look great too.
Practical Applications and Examples
Take a smartphone case as an example. It needs just the right wall thickness to withstand impacts while remaining light enough to hold comfortably. I once adjusted core and cavity placement based on this principle and managed to avoid sink marks7, achieving a design that was both durable and attractive.
Understanding how wall thickness affects core and cavity placement is essential for anyone looking to produce top-notch injection-molded parts efficiently. By applying these insights, designers like us can enhance both the structural integrity and aesthetic appeal of our products, ultimately leading to better performance in the market.
Thicker walls increase risk of sink marks.True
Thicker walls cool slower, leading to uneven cooling and potential sink marks.
Uniform wall thickness prevents warping in molds.True
Even cooling from uniform thickness reduces warping risk during molding.
Why Is Alignment Crucial for Core and Cavity Success?
Ever tried piecing together a jigsaw puzzle only to find the pieces don’t quite fit? That’s what misaligned molds can feel like in injection molding.
Alignment in core and cavity design is vital for precise fits, reducing injection molding defects, optimizing mold performance, enhancing product quality, and lowering production costs.
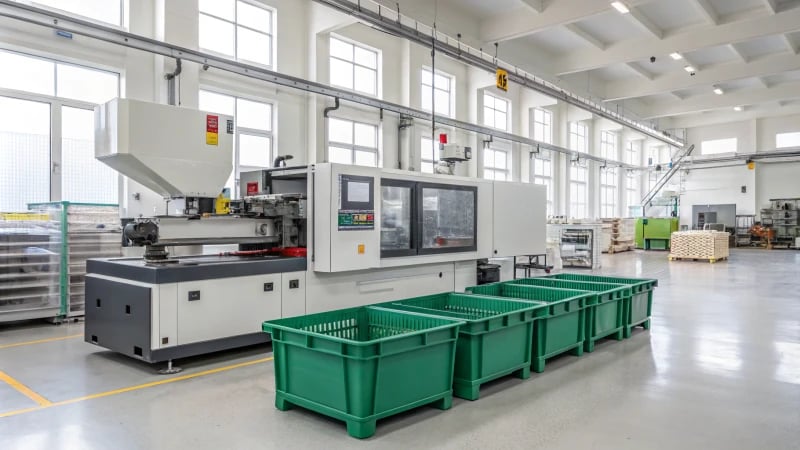
Understanding the Basics of Core and Cavity Alignment
In the world of injection molding8, it feels like I’m constantly fine-tuning a giant, intricate puzzle. The core and cavity are like those perfectly matched puzzle pieces that snap together to create a flawless picture—or in this case, a perfect hollow space for the plastic. Without perfect alignment, my efforts might unravel, leading to more than just a frustrating puzzle but real-world problems like excess material or part deformation.
- Precision: It’s all about getting those pieces to fit just right. When the core and cavity align perfectly, it ensures the final product is as close to the design specs as possible—just how I intended it.
- Efficiency: Misalignment not only throws off my precision but also wears down the mold components faster than I can say "adjustment," leading to more maintenance than I’d like.
Impact of Misalignment
Misalignment can result in several issues such as:
Issue | Description |
---|---|
Flashing | Excess material leaking out between mold halves |
Part Deformation | Warping or bending of the finished product |
Tool Damage | Increased stress on mold parts leading to premature wear |
These issues don’t just ruin a good day; they hit the bottom line hard.
Techniques to Ensure Proper Alignment
- Use of Guide Pins: I’ve found that incorporating guide pins is like having a trusty sidekick—they help align the mold halves during closure, cutting down on errors.
- Regular Calibration: Much like keeping my car tuned up, regularly checking and calibrating mold machines ensures everything stays on track.
- Advanced CAD Software9: This is where my design skills shine. Using advanced CAD software allows me to simulate and tweak alignment before anything goes into production.
Real-world Example
I remember working with a company that produced casings for electronic gadgets. Even the tiniest misalignment could lead to gaps or uneven surfaces. It wasn’t just about aesthetics—these flaws impacted functionality too. By focusing on perfect alignment, we managed to avoid those defects and deliver high-quality products.
Embracing these techniques has transformed how I approach mold design. It’s not just about maintaining product integrity; it’s about boosting production efficiency. For someone like me in the design field, mastering these alignment strategies truly makes a difference in achieving successful outcomes in mold design10.
Misalignment causes increased mold maintenance.True
Misalignment leads to wear and tear, requiring frequent maintenance.
Guide pins are unnecessary for mold alignment.False
Guide pins are crucial for aligning mold halves and reducing errors.
How Does Material Choice Affect Core and Cavity Design?
You wouldn’t believe how much choosing the right material can change everything in mold making!
Choosing the right material for core and cavity design influences mold durability, thermal conductivity, and surface finish, ensuring optimal performance and longevity in injection molding.
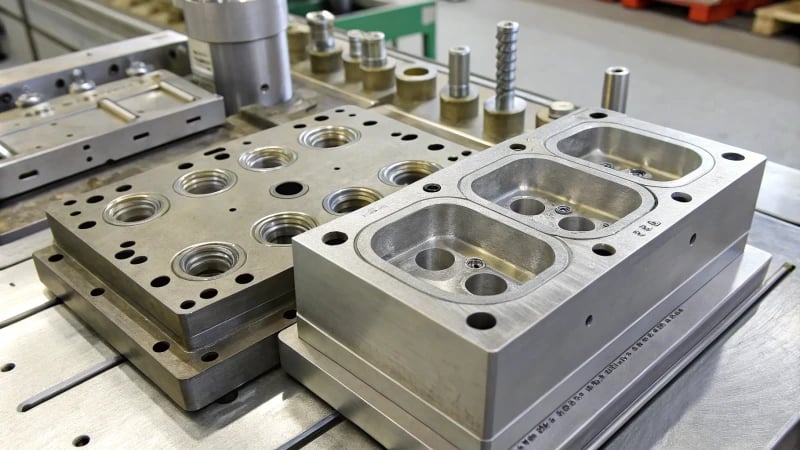
The Role of Material Properties
I remember the first time I had to choose a material for a core and cavity design. It felt like an overwhelming task. After all, material properties such as hardness, thermal conductivity, and corrosion resistance are critical to creating efficient molds. Take hardened steel11, for instance—its high hardness gives it excellent wear resistance, which is essential for molds that go through high cycle rates. On the other hand, copper alloys are fantastic for reducing cycle times because of their superior heat dissipation.
Material | Hardness | Thermal Conductivity | Corrosion Resistance |
---|---|---|---|
Hardened Steel | High | Low | Moderate |
Copper Alloy | Moderate | High | Low |
Cost-Effectiveness and Efficiency
Budget can make or break a project; I’ve seen it firsthand. While cutting-edge materials like beryllium copper12 offer outstanding heat transfer capabilities, they can be pricey. I’ve learned that it’s all about finding a balance. Sometimes, combining materials can maximize both cost efficiency and performance. For example, using a steel mold frame with copper inserts can enhance cooling without breaking the bank.
Impact on Surface Finish
The surface finish of a molded part can make a huge difference in its application. I once worked on a project where we needed a high gloss finish for consumer electronics casings—polished stainless steel was our hero. Conversely, aluminum was perfect for lightweight components that didn’t need to shine. The surface finish13 isn’t just about looks; it affects functional properties like friction and adhesion too.
Understanding these material impacts helps designers, like me, make informed decisions that harmonize performance, cost, and production efficiency in core and cavity design. Choosing the right material is crucial for achieving desired product outcomes and maintaining a competitive edge in manufacturing.
Copper alloys reduce cooling time in mold design.True
Copper alloys have high thermal conductivity, allowing faster heat dissipation.
Aluminum molds are ideal for high-gloss finishes.False
Polished stainless steel, not aluminum, is preferred for high-gloss finishes.
What Are Common Challenges in Core and Cavity Placement?
Diving into the world of core and cavity placement feels like solving a complex puzzle that demands both creativity and precision. Let’s explore the challenges and how to tackle them.
Core and cavity placement challenges involve ensuring structural integrity, managing shrinkage, and maintaining precise alignment, all crucial for successful mold design and production.
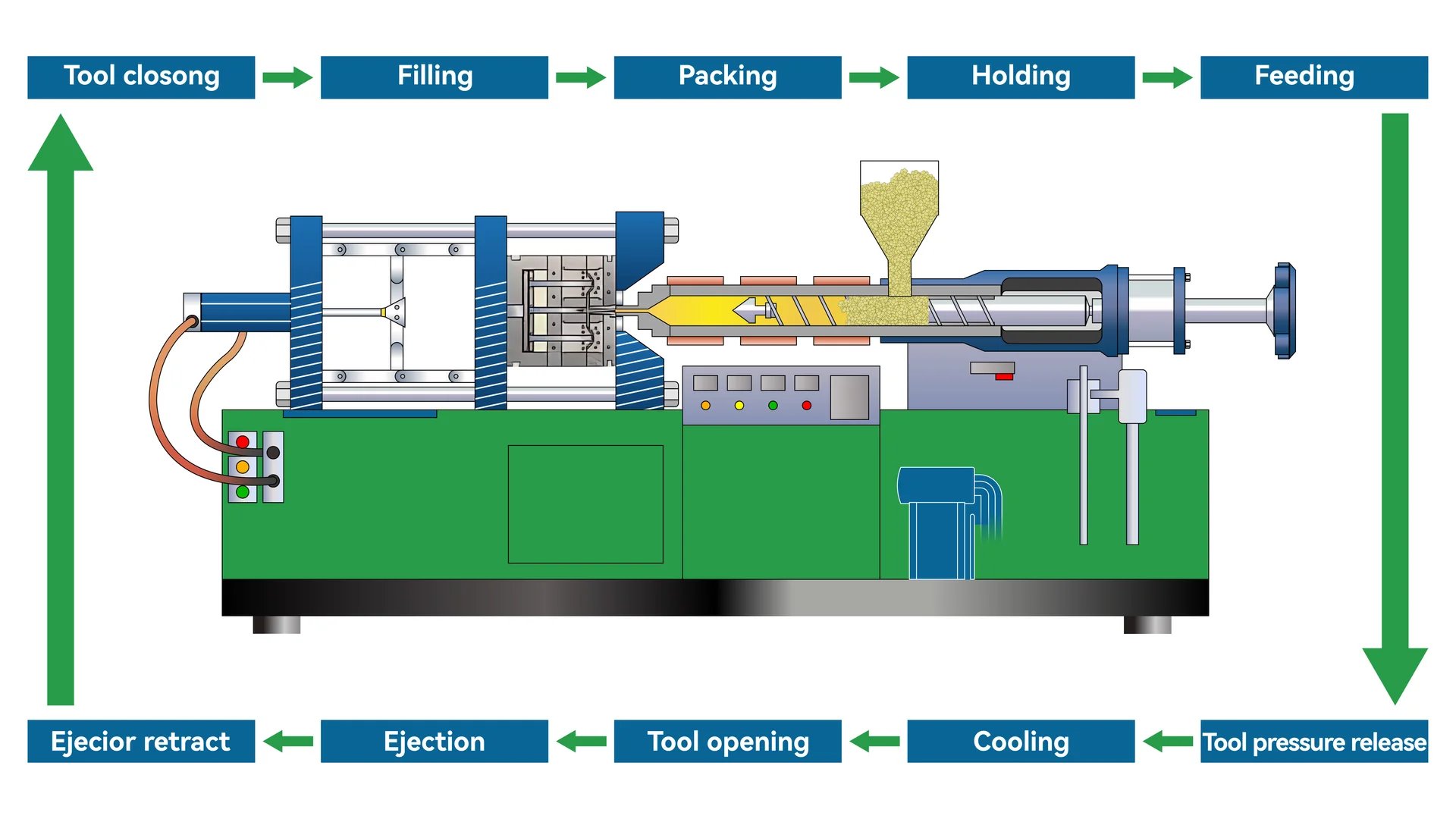
Structural Integrity Concerns
I remember the first time I realized the significance of core and cavity placement for mold strength. During a project early in my career, I misplaced a core, which led to a weakened mold and an array of defects. It was a hard lesson learned, but it taught me the importance of using simulation tools14 to assess stress distribution. Now, ensuring balanced pressure during molding is second nature to me, reducing potential weak points.
Managing Material Shrinkage
Material shrinkage often feels like a wild card in the design process. On one occasion, I underestimated the shrinkage of a new polymer, resulting in parts that didn’t quite fit together as planned. It was frustrating but a valuable experience that underscored the importance of consulting shrinkage data sheets15. These help predict material behavior, allowing me to adjust core and cavity dimensions accordingly.
Material Type | Typical Shrinkage |
---|---|
ABS | 0.4-0.7% |
Polypropylene | 1.0-2.5% |
Nylon | 1.2-2.0% |
Ensuring Precise Alignment
Precision is truly at the heart of quality mold design. I’ll never forget a project where a slight misalignment caused costly inconsistencies in wall thickness, leading to rejected parts. This experience taught me the value of employing precision alignment techniques16 to maintain quality standards.
Balancing Aesthetic and Functional Needs
As designers, we’re often caught between making products look good and function well. In one memorable project, I had to leverage advanced CAD software17 to navigate potential design issues before creating the physical mold. Balancing aesthetics with function became not just a goal, but a mantra.
Misplaced cores weaken mold strength.True
Correct core placement ensures structural integrity by distributing stress evenly.
All materials shrink at the same rate.False
Different materials have varied shrinkage rates, affecting final dimensions.
How Does Technology Enhance Core and Cavity Layouts?
I remember my first mold design project like it was yesterday—every detail felt monumental. Thankfully, technology has become my best ally, transforming the daunting process of optimizing core and cavity layouts into a streamlined, efficient art.
Technology enhances core and cavity layouts by using CAD software, simulation tools, and AI algorithms to improve design precision, reduce material use, and increase efficiency and cost-effectiveness.
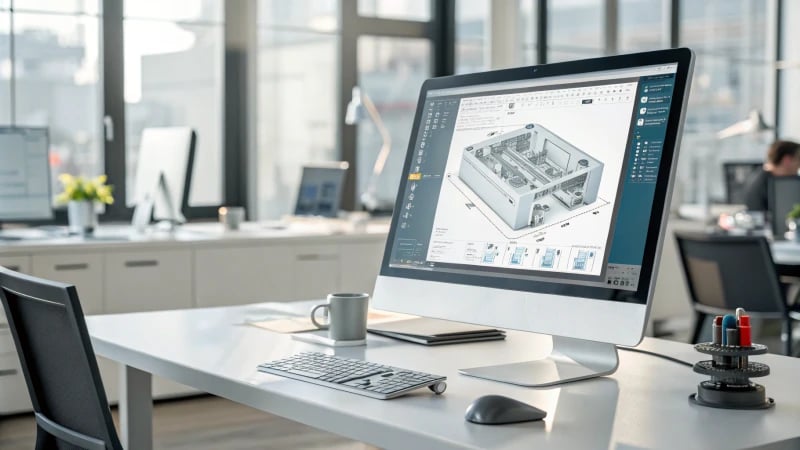
The Role of CAD Software
When I first started using CAD software, I was amazed at how it seemed to open up a whole new world of possibilities. Creating precise and detailed models was like sketching out dreams that could be easily tweaked and perfected before taking the leap into production. One time, I recall working on a particularly intricate design where each modification needed to be spot on. CAD made it so much easier to visualize and adjust without the headache of constant physical prototypes.
For fellow designers18, this flexibility can drastically cut down on trial-and-error stages, which means saving both precious time and resources. It’s a bit like having an eraser for your ideas—quickly refining them until they’re just right.
Advantages of CAD in Mold Design |
---|
Enhanced precision |
Easy modifications |
Cost-effective prototyping |
Simulation Tools for Mold Optimization
There was a moment early in my career when I realized the true power of simulation tools. Picture this: we’re about to finalize a mold design when a simulation revealed potential air traps. That insight saved us from what could have been a costly oversight. By running these simulations, I can foresee how a mold will perform during injection processes and adjust accordingly.
Mold flow analysis is particularly invaluable here. It helps in fine-tuning the placement of gates and runners—essentially the road map for material flow. This preemptive troubleshooting ensures fewer defects and a higher-quality end product. It’s like having a crystal ball that shows you the best path forward.
Understanding Mold Flow Analysis19 is crucial for anyone keen on optimizing their designs.
AI and Machine Learning in Mold Design
I’ve been fascinated by how AI and machine learning have begun transforming mold design. Imagine having a seasoned expert whispering insights into your ear, guiding you through complex calculations. AI systems analyze countless design parameters and recommend the most efficient core and cavity configurations.
This approach not only speeds up the design process but also enhances accuracy by reducing human error—a constant worry in manual calculations. It’s like having an extra set of eyes ensuring everything aligns perfectly for better production outcomes.
Explore how AI transforms mold design20 with cutting-edge solutions.
Future Trends in Mold Optimization
I can’t help but get excited about where we’re heading with future trends in mold optimization. Take 3D printing, for example. It’s becoming a game-changer, allowing for rapid prototyping and testing of intricate designs that were once deemed too expensive or downright impossible with traditional methods.
Staying informed about these emerging technologies is crucial for leveraging them to enhance our workflows. I’m constantly seeking out new ways to integrate these advancements, knowing they’ll pave the way for more innovative designs.
Designers should stay informed about these trends to leverage new technologies that enhance their workflows21.
CAD software reduces trial-and-error in mold design.True
CAD allows precise modeling and testing before production, saving resources.
AI increases human error in mold design processes.False
AI minimizes human error by automating calculations and optimizing designs.
Conclusion
This article outlines best practices for core and cavity placement in injection molding, emphasizing alignment, wall thickness, parting line location, and material selection to enhance product quality and efficiency.
-
Discover how mold opening mechanics influence manufacturing timelines and reduce bottlenecks. ↩
-
Learn about different parting line types and their applications to optimize your design. ↩
-
Explore cutting-edge CAD methods to simulate mold design scenarios effectively. ↩
-
Uneven cooling can lead to defects like warping or shrinkage, compromising product quality. Understanding its impact helps designers optimize wall thickness and core/cavity placement. ↩
-
Proper core and cavity placement ensures efficient material flow and prevents defects, crucial for maintaining product quality in injection molding. ↩
-
Wall thickness influences cooling rates in injection molding. This link explores how proper design can improve efficiency and minimize defects. ↩
-
Sink marks can mar product appearance and function. Discover strategies to prevent them through optimal wall thickness and mold design. ↩
-
Explore how injection molding works to understand core and cavity alignment’s impact on product quality. ↩
-
Discover top CAD tools to enhance precision in mold design, ensuring optimal core and cavity alignment. ↩
-
Learn advanced techniques to achieve precise alignment in mold design, reducing defects and improving efficiency. ↩
-
Discover how hardened steel enhances mold durability and extends lifecycle. ↩
-
Explore why beryllium copper is favored for its exceptional thermal properties. ↩
-
Learn how different materials affect the final surface quality of molded parts. ↩
-
Simulation tools help predict stress distribution, aiding in stronger mold designs. ↩
-
Shrinkage data sheets provide critical insights for predicting material behavior post-molding. ↩
-
Precision alignment ensures molds produce consistent, high-quality parts without defects. ↩
-
Advanced CAD software aids in visualizing and resolving design issues early on. ↩
-
Explore the capabilities of CAD software in enhancing mold design precision and efficiency. ↩
-
Discover the advantages of mold flow analysis in predicting and preventing design flaws. ↩
-
Learn how AI applications streamline mold design processes with high accuracy. ↩
-
Stay updated with future trends that can revolutionize injection molding processes. ↩