Let’s dive into the world of injection molding and discover the secrets to achieving perfect thickness in our products!
Achieving precise thickness in injection molded products is essential for quality and functionality. Manufacturers often face challenges in maintaining this consistency.
Now that we’ve touched on the basics, let’s explore deeper insights into mold design intricacies and the adjustments that can make all the difference in your manufacturing process.
Mold design doesn't affect thickness tolerance.False
Mold design impacts thickness tolerance by ensuring uniform material flow.
How Does Mold Design Affect Thickness Tolerance?
Mold design is pivotal in managing thickness tolerance, ensuring uniformity and minimizing product defects.
Mold design impacts thickness tolerance through structured runner systems, accurate cavity calculations, and efficient cooling layouts. By ensuring even material flow and cooling, molds maintain consistency in product thickness.
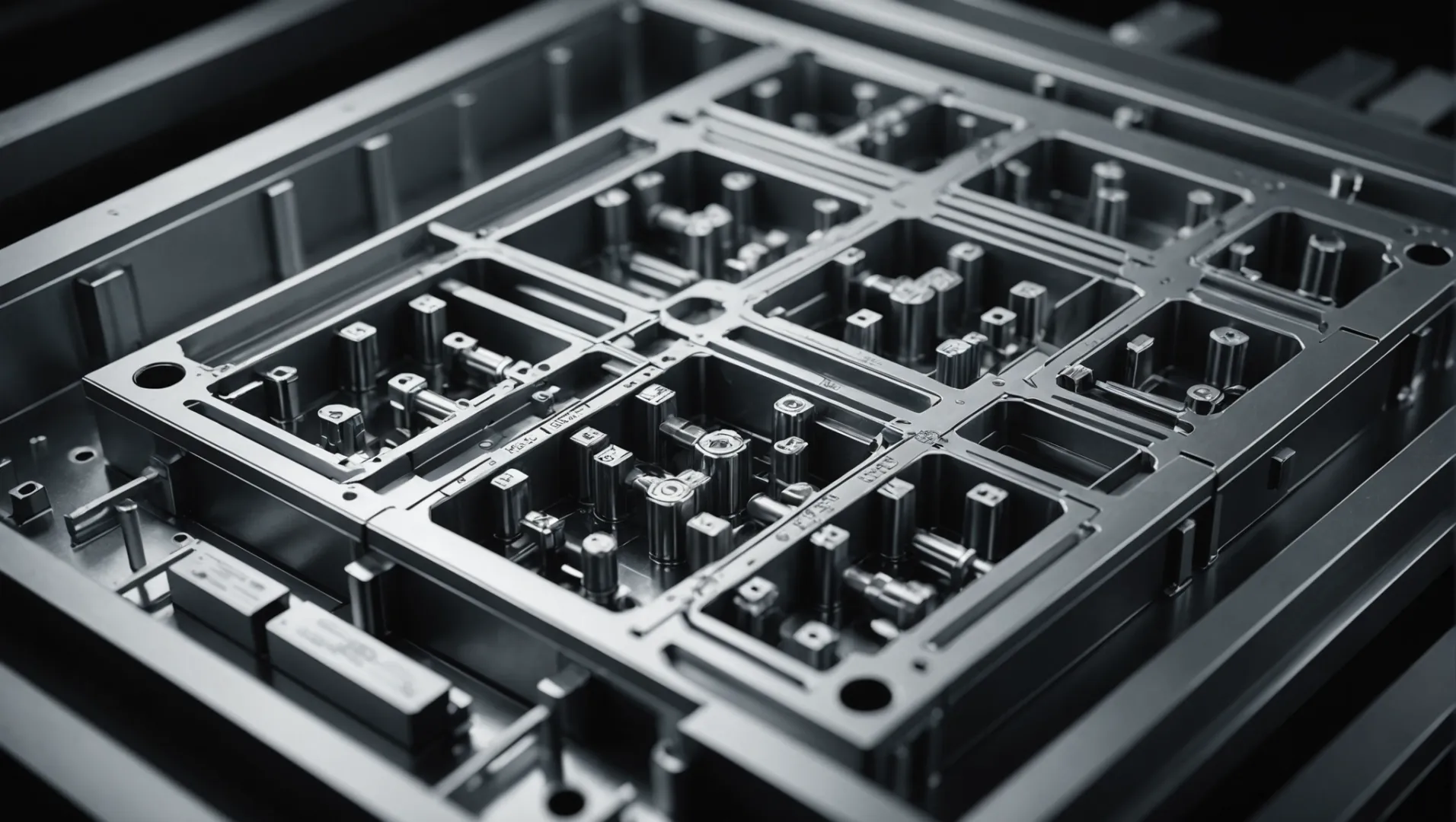
The Importance of Mold Structure
The mold structure plays a fundamental role in controlling thickness tolerance. A well-designed mold runner system ensures that the plastic melt flows evenly, preventing local over-thickness or thinness. For instance, a balanced runner layout helps distribute the melt uniformly across all cavities with equal pressure and speed.
Accurate calculation of the mold cavity size is critical. Designers must consider plastic shrinkage rates, which vary between materials. By predicting shrinkage accurately for the specific plastic type used, molds can ensure post-demolding product dimensions meet specified tolerances.
Cooling System Design Considerations
Cooling system design is another crucial aspect of mold design affecting thickness tolerance. Optimizing the cooling water channel layout ensures uniform cooling across all mold parts. Uneven cooling can lead to inconsistent product shrinkage and increased thickness variance.
For example, increasing the density of cooling channels in thicker product areas or using advanced techniques like conformal cooling channels1 can enhance efficiency. Additionally, controlling the cooling speed by adjusting the temperature and flow rate of the cooling medium can help achieve more uniform product shrinkage.
Impact on Product Quality
Effective mold design directly influences product quality by minimizing defects and ensuring consistent thickness. It not only addresses potential issues during the manufacturing process but also contributes to the overall reliability and performance of the final product.
The intricacies of mold design, from runner systems to cooling layouts, underscore its essential role in achieving precise thickness tolerance in injection molding. As industry professionals delve deeper into these aspects, they unlock opportunities for innovation and efficiency in manufacturing processes.
Balanced runner systems prevent thickness variance.True
Balanced runner systems ensure even material distribution, minimizing variance.
Cooling channel density is irrelevant to thickness uniformity.False
Cooling channel density affects cooling uniformity, impacting thickness consistency.
What Role Do Process Parameters Play in Tolerance Control?
Understanding process parameters is key to mastering thickness tolerance in injection molding.
Process parameters such as injection pressure, speed, holding pressure, and mold temperature are crucial for controlling thickness tolerance in injection molding. By carefully adjusting these parameters, manufacturers can ensure consistent product dimensions and quality, reducing defects and increasing reliability.

Injection Pressure and Speed
Injection pressure and speed significantly influence the filling behavior of the plastic melt within the mold. Adjusting these parameters ensures that the melt flows uniformly, preventing issues like local thinness or thickness discrepancies. For example, a high injection pressure might cause the material to spray, resulting in thin sections, while low pressure might lead to insufficient filling.
To address this, employing a multi-stage injection process can be beneficial. This method involves gradually adjusting the pressure and speed throughout different stages, allowing for a more controlled fill that reduces thickness variations. Learn more about multi-stage injection benefits2.
Holding Pressure and Time
The holding phase is critical for compensating the shrinkage that occurs during cooling. Correctly setting holding pressure ensures that the melt is compacted uniformly, preventing internal stresses that can lead to warping or thickness inconsistencies. If the pressure is too high, it might induce excess stress; too low, and it won’t adequately counteract shrinkage.
Similarly, the holding time should be optimized according to product dimensions and material properties. An extended holding time could unnecessarily increase cycle times without added benefit, whereas a shorter time might not suffice for proper shrinkage compensation.
Material and Mold Temperature
The temperatures of both the material and mold play pivotal roles in influencing shrinkage rates and flow characteristics of the melt. A higher material temperature reduces viscosity, enhancing flow but risking defects like flash. Conversely, a lower temperature may hinder flow, causing filling challenges.
Mold temperature impacts cooling rates and consequently affects shrinkage consistency. A balanced mold temperature facilitates even cooling, thereby maintaining uniform thickness. However, excessively high temperatures can prolong cycle times, while lower temperatures might exacerbate internal stresses or warping.
By understanding and manipulating these process parameters, manufacturers can achieve optimal tolerance control in their injection molded products. These adjustments not only improve product quality but also reduce material waste and production costs. Explore further strategies in process optimization3.
Injection pressure affects thickness consistency.True
Adjusting injection pressure ensures uniform melt flow, preventing thin spots.
High mold temperature reduces shrinkage rates.False
High mold temperature can increase shrinkage by affecting cooling rates.
Why Is Material Selection Crucial for Tolerance Management?
The choice of material significantly impacts the precision and reliability of injection molded products, influencing their tolerance levels.
Material selection affects shrinkage, fluidity, and stability, all crucial for maintaining tight tolerances in injection molding. Opting for materials with predictable behaviors ensures consistent product dimensions and performance.

Influence of Material Properties on Tolerance
Material properties, such as shrinkage rate and fluidity, play a pivotal role in determining the dimensional accuracy of injection molded products. For example, materials with low shrinkage, like engineering plastics4, are ideal for components requiring high precision. Conversely, materials with high shrinkage might lead to significant deviations from intended dimensions, complicating tolerance management.
Material Stability and Its Impact
The stability of the material, especially under varying environmental conditions, is another critical factor. Some plastics tend to degrade or absorb moisture over time, which can alter their properties during processing. Materials that maintain their characteristics, like polycarbonate, are preferable for maintaining consistent thickness and overall product quality.
Processing Considerations and Material Selection
Selecting the right material also involves considering its processing requirements. For instance, hygroscopic materials like nylon require drying before molding to prevent defects like bubbles or surface imperfections, which can impact tolerance. Proper material preparation ensures the final product meets desired specifications.
Table: Comparison of Material Properties Impacting Tolerance
Material | Shrinkage Rate | Stability | Pre-Processing Required |
---|---|---|---|
Polycarbonate | Low | High | Drying |
Nylon | Moderate | Moderate | Drying |
ABS | Low to Moderate | High | Minimal |
Understanding these nuances allows manufacturers to select materials that align with their specific tolerance goals, ultimately enhancing product reliability and performance.
Polycarbonate has low shrinkage in molding.True
Polycarbonate is known for its low shrinkage, ensuring precision.
Nylon does not require drying before molding.False
Nylon is hygroscopic and needs drying to prevent defects.
How Can Quality Inspection Enhance Thickness Control?
Ensuring precise thickness in injection molded products relies heavily on effective quality inspection techniques.
Quality inspection enhances thickness control by utilizing online and offline measurement systems to monitor and adjust production processes, ensuring consistent product dimensions.

The Role of Online Inspection Systems
Online inspection systems, such as laser displacement sensors and optical measurement tools, play a crucial role in real-time monitoring of product thickness. These systems continuously assess the dimensions of injection molded products during the production process. For instance, a laser displacement sensor5 can swiftly detect deviations from desired thickness, allowing for immediate adjustments to be made in the molding process.
Implementing such technologies reduces the risk of producing defective products, thus maintaining the overall quality and reliability of the output. This is particularly beneficial in high-volume manufacturing settings where consistency is paramount.
Benefits of Offline Inspection
Offline inspections complement online systems by providing a more detailed analysis of product quality. This involves periodic measurements using precise tools like micrometers and calipers, which offer insights into potential issues not easily detected online. Conducting these inspections helps identify trends and patterns in thickness variations, leading to more informed decisions regarding process improvements.
Table: Comparison of Online and Offline Inspection Methods
Inspection Type | Advantages | Limitations |
---|---|---|
Online | Real-time data, quick adjustments | May miss subtle defects |
Offline | Detailed analysis, comprehensive quality view | Time-consuming, not suitable for real-time |
Integrating Feedback Mechanisms
A crucial aspect of effective quality inspection is the feedback mechanism. By correlating online inspection data with process parameters, manufacturers can pinpoint key factors affecting thickness tolerance. This proactive approach facilitates timely adjustments and optimizations, ensuring that any deviations from desired standards are swiftly corrected.
For example, integrating feedback systems with process control software6 allows for automated parameter adjustments based on live data. This not only enhances precision but also reduces manual intervention, improving overall efficiency.
Incorporating both online and offline inspection methods along with robust feedback loops can significantly improve the management of thickness tolerance in injection molded products. These practices ensure that manufacturers can maintain high standards of quality while minimizing waste and inefficiencies.
Online inspection systems adjust thickness in real-time.True
They use sensors to monitor and modify production processes instantly.
Offline inspections are unsuitable for real-time adjustments.True
They provide detailed analysis but cannot adjust processes immediately.
Conclusion
Mastering thickness tolerance is key to enhancing product quality. Let’s implement these techniques for greater reliability!
-
Discover how conformal cooling improves efficiency and product quality.: By having the cooling channels closer to the part, you get more consistent cooling near the part’s surface and a higher quality plastic part. ↩
-
Discover how multi-stage injection enhances product uniformity.: Multi-shot injection moulding reduces production and labor costs. Secondary manufacturing processes, which include painting, the adding of logos … ↩
-
Gain deeper insights into optimizing injection molding processes.: Steps to INJECTION MOLDING Process Optimization · 1. Tool functionality examination · 2. Short shot testing · 3. Gate seal studies · 4. Sample parts evaluation/data … ↩
-
Discover more about engineering plastics suitable for precise applications.: Most of the shrinkage occurs in the mold while cooling. A small amount of shrinkage occurs after ejection as the molded part continues to cool. After that, the … ↩
-
Understand how laser sensors provide real-time thickness measurements.: Laser triangulation displacement sensors work by detecting the angle of the reflected light, which is then analyzed and used to calculate displacement. ↩
-
Learn how software optimizes manufacturing parameters automatically.: Process control refers to the monitoring and adjusting of process parameters to get a preset or desirable output. ↩