Are you feeling the frustration of pressure loss in your injection molding process?
To effectively control pressure loss in injection molding, focus on equipment selection, mold design, process parameter adjustments, and operator training. Each factor plays a critical role in minimizing pressure drop and optimizing manufacturing outcomes.
While the initial answer provides a glimpse into controlling pressure loss, delving deeper into each aspect reveals comprehensive strategies and expert insights. Continue reading to uncover detailed methodologies that can transform your injection molding processes.
Regular equipment maintenance reduces pressure loss.True
Regular maintenance prevents leaks and clogs, minimizing pressure loss.
What Role Does Equipment Play in Managing Pressure Loss?
Equipment is the backbone of managing pressure loss in injection molding, ensuring stability and precision throughout the process.
Equipment plays a vital role in managing pressure loss by providing the necessary stability, precision, and maintenance to minimize pressure drop during injection molding.
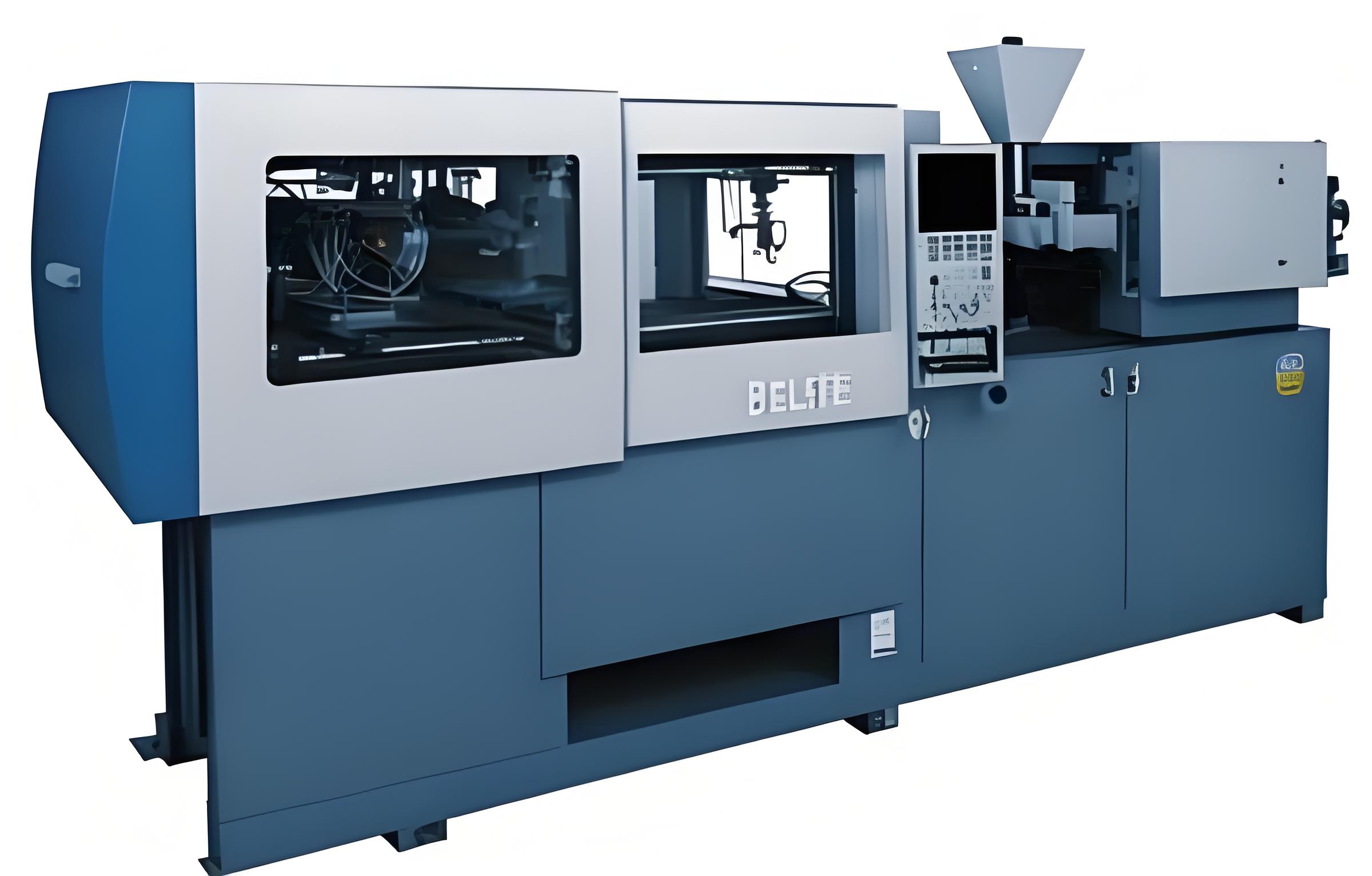
Choosing the Right Injection Molding Machine
Selecting an appropriate injection molding machine is pivotal. The rated pressure1 of the machine must align with production demands. Insufficient pressure can lead to increased pressure loss. Machines that offer stability and precision help mitigate fluctuations that contribute to pressure loss.
- Rated Pressure Consideration: Ensure the machine’s pressure capacity meets production requirements to prevent excessive loss.
- Stability and Precision: Machines with superior stability reduce pressure fluctuations, minimizing loss.
Importance of Regular Equipment Maintenance
Maintenance is crucial to sustaining equipment efficacy. Regular checks on the hydraulic system ensure no leaks or obstructions, which could cause pressure drops.
- Hydraulic System Checks: Regular inspection ensures unobstructed oil flow and leak prevention.
- Cleaning Protocols: Routine cleaning of nozzles and barrels prevents clogs that impede plastic flow, reducing pressure loss.
Equipment’s Influence on Pressure Stability
The equipment’s ability to maintain stable operating conditions directly affects pressure loss management. Advanced machines equipped with sensors and feedback systems can adjust parameters in real-time to sustain optimal conditions.
- Advanced Monitoring: Real-time feedback systems help maintain stable conditions, minimizing pressure deviations.
- Sensor Integration: Sensors provide data for adjusting parameters swiftly to counteract potential losses.
By focusing on equipment selection and maintenance, injection molding processes can achieve greater control over pressure loss. This foundational step sets the stage for improved efficiency and quality in manufacturing operations.
Advanced machines reduce pressure fluctuations.True
Machines with sensors adjust parameters in real-time, stabilizing pressure.
Regular maintenance increases pressure loss in systems.False
Maintenance prevents leaks and clogs, reducing pressure loss.
How Can Mold Design Influence Pressure Control?
Mold design plays a pivotal role in controlling pressure during the injection molding process. By optimizing design elements, manufacturers can significantly reduce pressure loss and enhance production efficiency.
Optimizing mold design involves designing a suitable flow channel system, ensuring proper exhaust, and maintaining high precision. These strategies help minimize pressure loss by reducing flow resistance and preventing air entrapment during the injection process.
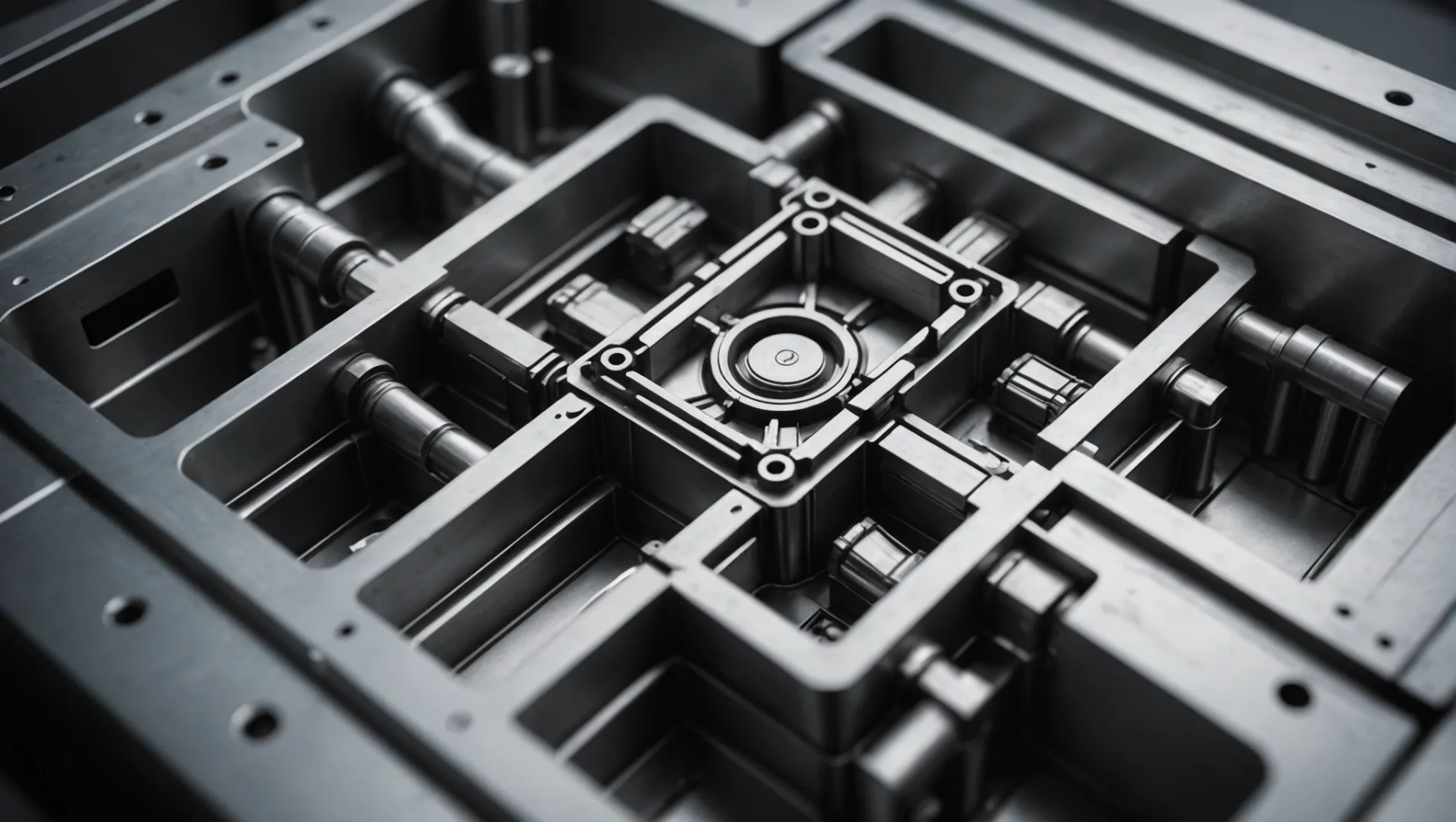
Designing an Efficient Flow Channel System
The design of the flow channel system is crucial in influencing pressure control during injection molding. A well-structured flow channel minimizes resistance and ensures smooth plastic flow. This involves:
- Shape and Size Optimization: The geometry of the flow channel should be tailored to suit the specific product being molded. For instance, a circular cross-section might be more suitable for certain products as it provides a consistent flow path and reduces pressure loss.
- Balanced Layout: Ensuring a balanced layout of the flow channels can prevent uneven filling, which could otherwise lead to increased pressure at certain points.
Ensuring Proper Mold Exhaust
Effective mold exhaust systems are essential for preventing pressure buildup caused by trapped air. Inadequate venting can lead to defects and increased pressure loss.
- Adding Exhaust Grooves: Incorporating exhaust grooves in critical areas allows trapped air to escape efficiently, thus reducing the pressure drop.
- Optimizing Exhaust Position: Placing vents strategically at points where air is most likely to be trapped can enhance exhaust efficiency, ensuring that plastic fills the mold without hindrance.
Maintaining High Mold Accuracy
High-precision molds contribute significantly to controlling pressure during the molding process. Precision impacts how well the plastic flows and fills the mold.
- Regular Mold Maintenance: Regularly inspecting molds for wear and tear ensures that any issues can be addressed promptly, preventing increased friction and leakage that lead to pressure loss.
- Utilizing Advanced Materials: Employing materials with low thermal expansion properties can maintain mold integrity over multiple cycles, ensuring consistent pressure control.
Benefits of Advanced Mold Technologies
Incorporating advanced technologies in mold design can further enhance pressure control.
- CAD/CAM Integration: Leveraging computer-aided design and manufacturing tools allows for precise mold design and testing, which can predict potential pressure loss issues before production begins.
- 3D Printing: Utilizing 3D printing technology for prototype molds can quickly test different designs, enabling rapid iteration to find the most effective solution.
By focusing on these aspects of mold design, manufacturers can achieve significant improvements in pressure control during injection molding. Such improvements not only enhance product quality but also increase overall production efficiency. For more insights on effective mold design strategies, explore expert strategies for mold design2.
A circular flow channel reduces pressure loss.True
Circular cross-sections provide consistent flow paths, reducing resistance.
3D printing hinders mold design iteration.False
3D printing allows rapid testing and iteration, enhancing design flexibility.
What Process Adjustments Are Crucial for Reducing Pressure Loss?
Fine-tuning process parameters in injection molding is vital for reducing pressure loss, enhancing both efficiency and product quality.
Key process adjustments for reducing pressure loss in injection molding include controlling injection speed, optimizing holding pressure, adjusting temperatures, and selecting suitable plastic materials.
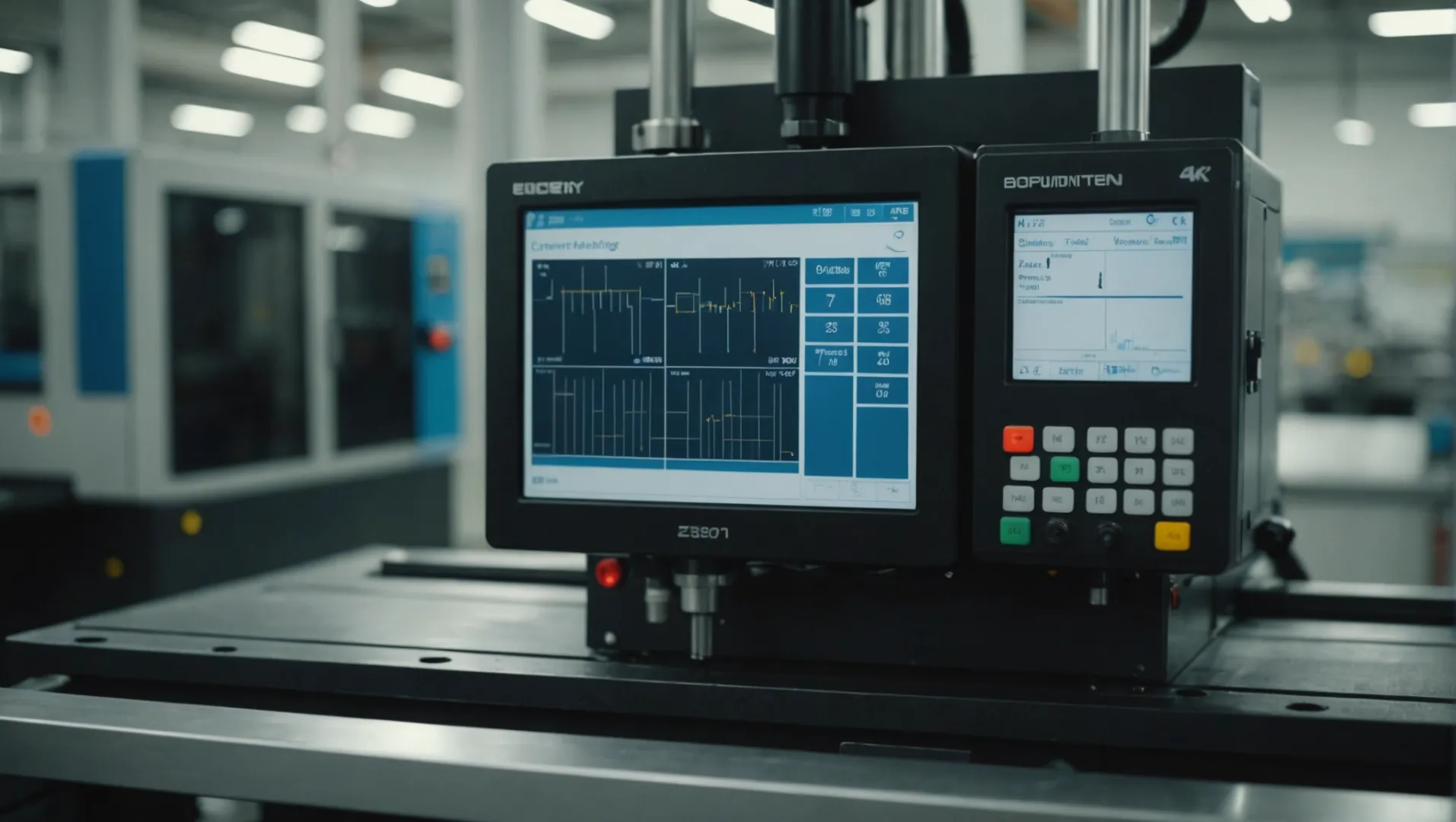
Control of Injection Molding Speed
Adjusting the speed at which material is injected into the mold is a delicate balance. While reducing speed can lower shear forces and thus pressure loss, too slow a speed might hinder production efficiency. This nuanced approach ensures smoother flow and less resistance.
Consider a scenario where excessive speed leads to shear thinning in the material, increasing friction and pressure loss. By carefully moderating speed, one can enhance flow stability3 and achieve more consistent results.
Optimization of Holding Pressure and Time
The holding phase is crucial for ensuring that the material fills the mold completely without voids. Optimizing this phase by adjusting pressure and timing helps in achieving compactness and reducing pressure loss. This can also help minimize shrinkage, which impacts product integrity.
Imagine a situation where holding pressure is maintained too long or too short. It can lead to defects such as sink marks or warping. Therefore, fine-tuning these parameters can significantly enhance product quality while managing pressure efficiently.
Temperature Adjustments
Temperature settings for the barrel and nozzle are pivotal in facilitating optimal material flow. Maintaining appropriate temperatures reduces viscosity, thereby decreasing resistance and pressure loss. However, excessively high temperatures can cause degradation or gas generation in materials.
For instance, calibrating the ideal temperature range4 for different polymers helps in maintaining the material’s integrity while optimizing flow conditions.
Selection of Plastic Material
The choice of plastic material directly affects its flow characteristics. Selecting materials with lower viscosity and good fluidity can reduce pressure loss significantly. Additionally, ensuring the plastic’s dryness prevents steam generation during molding, which can increase pressure loss.
For example, analyzing material properties5 like melt flow index (MFI) helps in selecting the right polymer that aligns with process requirements and minimizes resistance during molding.
Reducing injection speed decreases pressure loss.True
Lower speeds reduce shear forces, minimizing pressure loss in molding.
High temperatures always improve material flow.False
Excessive heat can degrade materials, increasing pressure loss.
Why Is Operator Training Essential for Controlling Pressure Drop?
In the injection molding industry, skilled operators are vital to minimizing pressure drops and enhancing production quality.
Operator training is crucial for controlling pressure drop as it ensures proper machine operation, timely maintenance checks, and adherence to standardized procedures, significantly reducing pressure loss during the injection molding process.
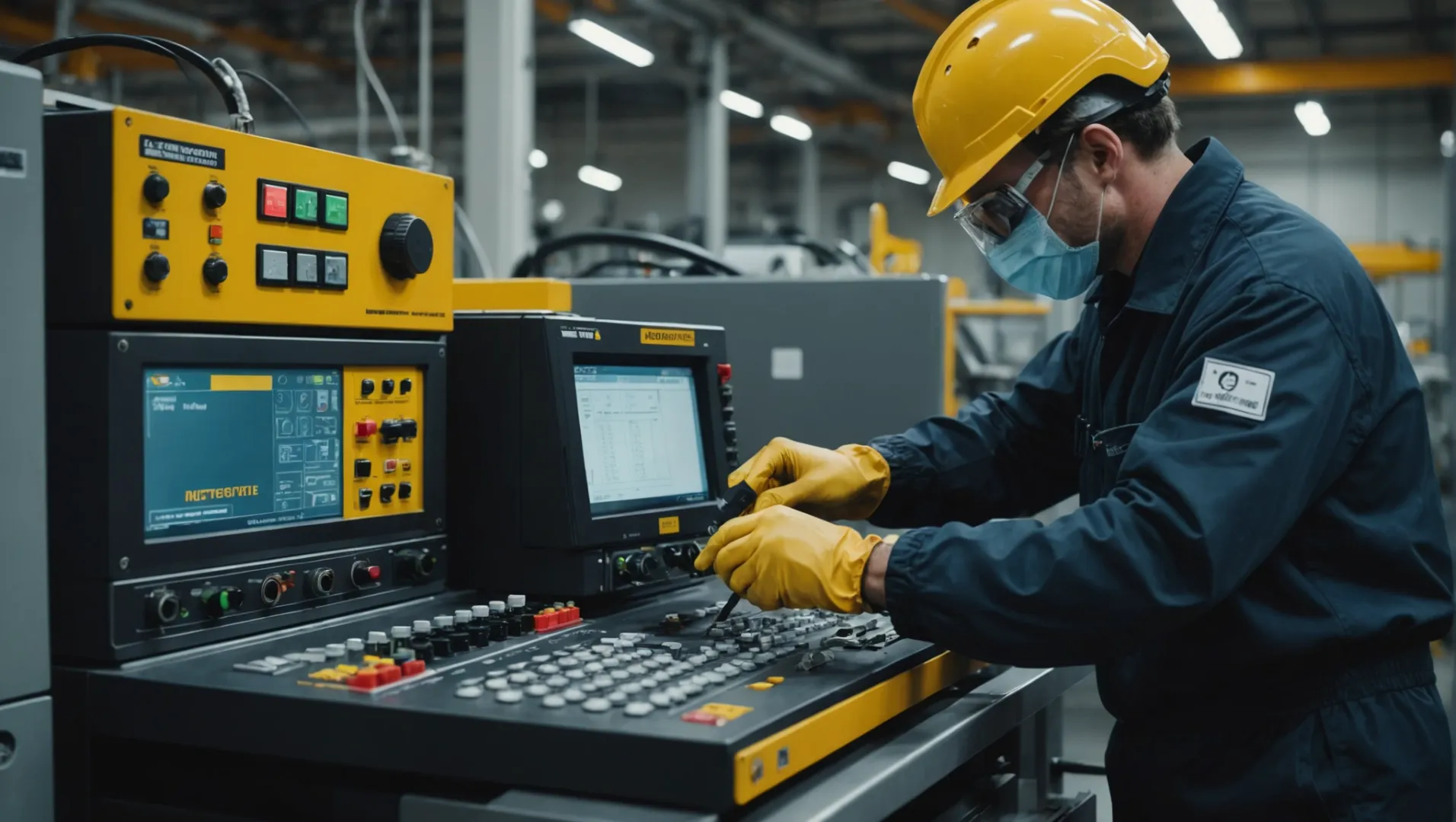
Understanding the Role of Operators in Pressure Management
Operators are on the front lines of the injection molding process, and their expertise can make or break the efficiency of production. Trained operators not only understand the mechanics of the machines they work with but also possess the skills to optimize machine parameters6 effectively. They are adept at recognizing early signs of pressure loss and taking corrective measures, thereby maintaining a stable production environment.
Importance of Familiarity with Injection Molding Equipment
Well-trained operators are familiar with the operation methods specific to different injection molding machines. This knowledge is pivotal because even minor deviations in machine settings can lead to significant pressure drops. Operators need to adjust these settings accurately to ensure that each cycle runs smoothly. By maintaining optimal parameters, such as injection speed and temperature, operators can prevent excessive shear forces that lead to increased pressure loss.
Regular Maintenance Checks
Trained operators play a key role in conducting regular maintenance checks on equipment and molds. These checks include monitoring the hydraulic system to prevent leaks and ensuring that nozzles and barrels remain unclogged. Such preventative measures can drastically reduce unexpected pressure drops by addressing issues before they escalate.
A proactive approach to maintenance involves documenting all inspections and repairs, ensuring that any recurring problems are identified and addressed promptly. This documentation is crucial for maintaining a historical record that can inform future adjustments or replacements needed for machines.
Adherence to Standardized Procedures
Operators must follow strict operational protocols to avoid mishaps that can lead to pressure loss. Standardized procedures guide operators through the correct steps when switching materials or molds, preventing potential damage that could compromise machine integrity. This adherence not only ensures safety but also maintains the efficiency of the injection molding process.
Ongoing Education and Skill Development
Continuous learning is essential in keeping up with technological advancements and process improvements in injection molding. Regular training sessions help operators stay informed about new techniques for pressure control7, which they can implement in their daily operations. These sessions often involve hands-on workshops and theoretical classes covering the latest industry standards and best practices.
Conclusion: The Impact of Operator Expertise on Pressure Management
The ability of operators to effectively manage pressure is contingent on their training and understanding of the injection molding process. By investing in comprehensive training programs, companies can ensure their operators are equipped with the skills necessary to minimize pressure drops, ultimately improving product quality and production efficiency.
Operator training reduces pressure drop in injection molding.True
Trained operators optimize machine settings and conduct maintenance, minimizing pressure loss.
Ignoring operator training has no impact on pressure management.False
Lack of training leads to improper machine handling, increasing pressure drops.
Conclusion
Effective pressure control in injection molding enhances quality and efficiency. Implement these strategies to streamline production and improve results.
-
Understand the criteria for selecting appropriate machine pressure.: It is determined by various factors such as the type of plastic material, machine condition, the size and shape of the product, and the design … ↩
-
Discover advanced techniques to optimize mold designs for better pressure control.: To mitigate these issues, designers often deploy strategies such as using ejector sleeves or increasing the surface area of the pins. In all, … ↩
-
Discover methods to stabilize flow, improving consistency and reducing pressure loss.: Enhancing the quality stability of injection molded parts by adjusting V/P switchover point and holding pressure. ↩
-
Learn optimal temperature ranges to maintain material integrity and optimize flow.: Water heating is suitable for mold temperatures below 100°C, while oil heating is used for temperatures above 100°C. For some high-temperature plastics … ↩
-
Explore techniques for selecting polymers that minimize resistance and optimize processes.: Learn about material properties to quantitatively analyze parts before selecting a thermoplastic resin · Comparing Injection Molding Materials · The Standard … ↩
-
Learn how precise parameter adjustments enhance injection molding efficiency.: Optimizing injection molding parameters is pivotal for ensuring the highest quality in production. The process’s complexity requires a nuanced … ↩
-
Discover new methods that experts use to minimize pressure drop effectively.: 1. Screw rotation in the plasticizing stage. 2. Slider feeder (the nozzle is close to the nozzle bushing). 3. Axial movement of the injection screw during … ↩