Have you ever considered how much energy is wasted during the injection molding process? It’s a staggering thought! Let’s explore how controlling heat loss can not only save energy but also enhance the quality of our products.
Effectively controlling heat loss during injection molding involves optimizing equipment design, maintaining proper thermal insulation, managing mold temperature, and regulating environmental factors. These strategies reduce energy consumption and improve product quality.
While we’ve laid a solid foundation with these initial strategies, there’s so much more to uncover. Let’s delve into the details to discover innovative techniques that can elevate your operational efficiency!
Optimizing mold design reduces heat loss in injection molding.True
Efficient mold design minimizes heat loss by improving thermal management.
What Role Does Equipment Optimization Play in Reducing Heat Loss?
In manufacturing, reducing heat loss is pivotal for energy efficiency. Equipment optimization plays a significant role in achieving this.
Equipment optimization in injection molding minimizes heat loss by enhancing machine design, ensuring effective insulation, and maintaining regular equipment checks. These measures improve energy efficiency and ensure stable production conditions.

Enhancing Machine Design
Optimizing the design of injection molding machines is a primary step in minimizing heat loss. One key aspect is selecting an efficient heating system, such as electromagnetic heating, which offers rapid heating and high energy utilization. This technology reduces heat loss during transfer, conserving energy and maintaining process efficiency.
Additionally, the thermal insulation performance of machines must be top-notch. By employing high-quality thermal insulation materials to wrap components like barrels and nozzles, heat dissipation into the surrounding environment can be minimized.
Importance of Regular Maintenance
Regular maintenance of equipment is crucial in controlling heat loss. This includes inspecting the working status of heating elements and replacing them promptly if damaged. Ensuring that these elements function normally and stably is essential for consistent heat provision.
Moreover, keeping equipment clean from dirt and dust prevents dust accumulation from affecting heat dissipation. This simple maintenance step can have a significant impact on reducing indirect heat loss.
The Role of Insulation Materials
Incorporating superior thermal insulation materials in equipment design is an effective strategy for reducing heat loss. These materials act as a barrier, preventing heat from escaping into the environment and ensuring that the generated heat is effectively utilized within the process.
Advanced Technological Implementations
Adopting advanced technologies such as predictive maintenance systems can further aid in optimizing equipment performance. These systems can monitor equipment conditions and predict potential failures before they occur, thus minimizing downtime and ensuring consistent energy efficiency.
Advanced Technologies1 in equipment design not only reduce heat loss but also enhance overall process reliability and product quality. By leveraging such technologies, manufacturers can achieve superior thermal management and operational performance.
Electromagnetic heating reduces heat loss in machines.True
Electromagnetic heating offers rapid heating and high energy utilization.
Regular equipment maintenance increases heat loss.False
Regular maintenance ensures stable heating elements, reducing heat loss.
How Can Mold Design Impact Thermal Efficiency?
Mold design significantly influences thermal efficiency in injection molding, affecting energy consumption and product quality.
Mold design impacts thermal efficiency by optimizing flow channel paths, selecting appropriate materials, and applying insulation coatings. These elements minimize heat loss, enhance energy efficiency, and ensure product integrity during the molding process.
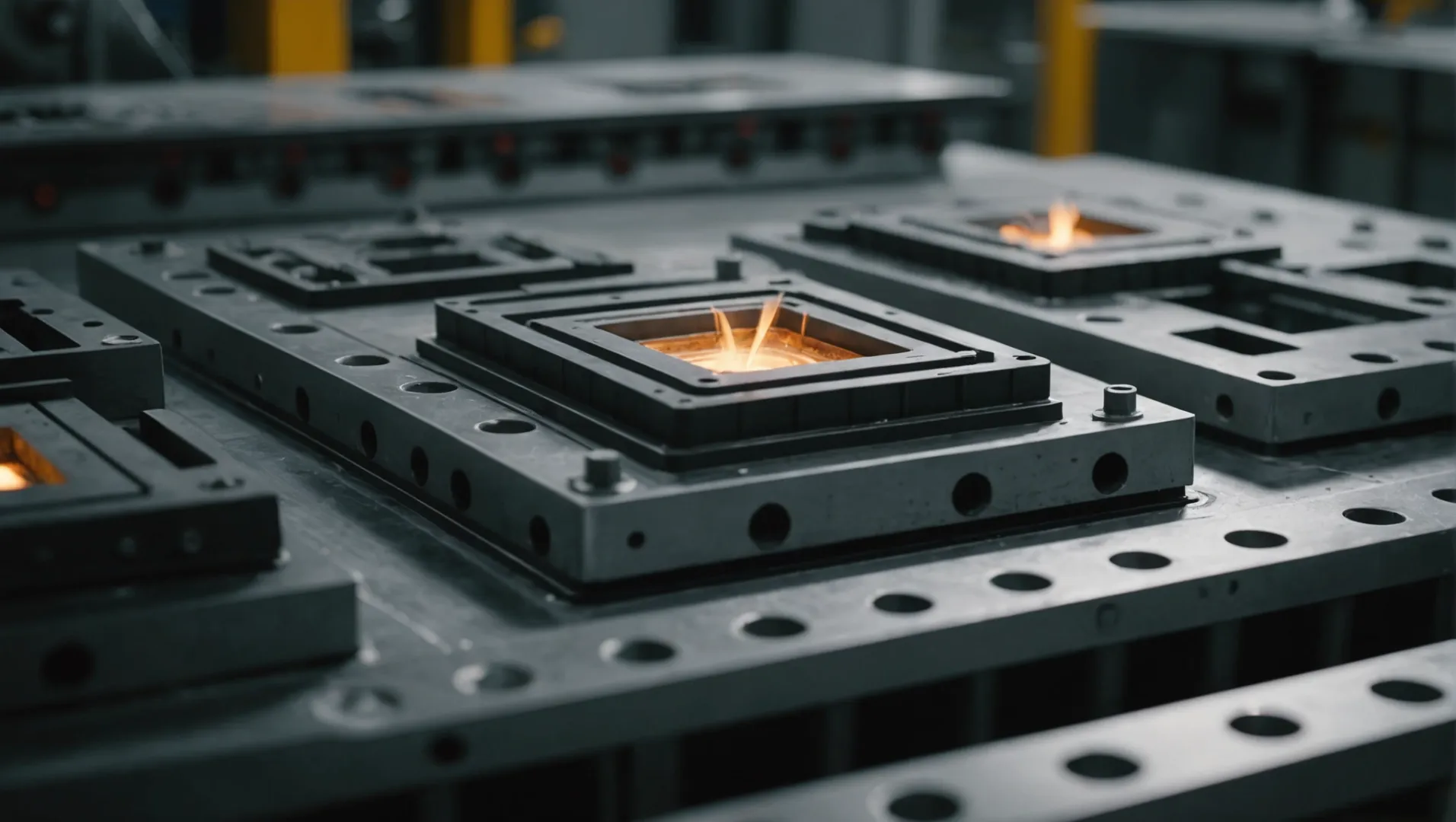
The Importance of Flow Channel Design
In injection molding, the flow channel is a critical component. By keeping the channels short and straight, you can significantly reduce heat loss during the flow of the melt. This design ensures minimal resistance and efficient heat conduction, leading to enhanced thermal efficiency. A well-structured flow channel not only conserves energy but also maintains the integrity of the final product.
Selecting Suitable Mold Materials
Choosing the right materials for mold construction is paramount. Materials with excellent thermal conductivity like specific mold steels help in rapid heat transfer while reducing dissipation. This balance ensures that while the mold transfers heat efficiently, it doesn’t excessively lose it to the environment, maintaining energy efficiency.
Utilizing Insulation Coatings
Applying insulation coatings to mold surfaces is an effective way to minimize heat dissipation. These coatings work by reflecting heat back into the mold rather than allowing it to escape. For instance, in large molds where maintaining a stable temperature is challenging, insulation coatings are essential for preserving thermal energy.
Integrating Auxiliary Heating Systems
For larger molds, auxiliary heating systems like heating rods or plates can be integrated alongside a precise temperature control system. This approach helps maintain a consistent mold temperature, which is crucial for reducing heat loss. By sustaining optimal temperatures, auxiliary systems contribute to both the energy efficiency of the process and the quality of the end product.
By focusing on these aspects of mold design, manufacturers can significantly improve thermal efficiency in injection molding processes. For more in-depth insights into mold materials and their properties2, explore additional resources that detail how these choices impact operational outcomes.
Flow channels should be long for better thermal efficiency.False
Short and straight flow channels reduce heat loss, improving efficiency.
Insulation coatings reflect heat back into the mold.True
Coatings minimize heat dissipation, enhancing energy efficiency.
Why Is Process Control Crucial for Heat Management?
In the intricate dance of injection molding, mastering process control can significantly curtail heat loss, boosting both efficiency and product quality.
Process control is vital for heat management in injection molding as it ensures precise regulation of injection temperature, speed, and pressure. This minimizes heat loss, maintains energy efficiency, and prevents material degradation, leading to superior product quality.
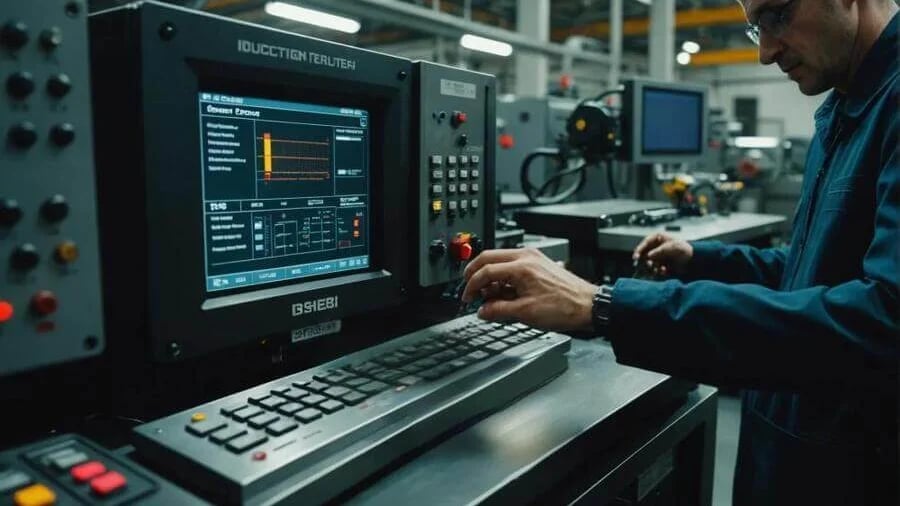
Importance of Controlling Injection Temperature
Controlling the injection temperature is pivotal in managing heat within the injection molding process3. A carefully set temperature range prevents excessive heat loss while avoiding the pitfalls of plastic degradation due to overheating. For instance, if the temperature is set too high, not only does it lead to faster heat dissipation, but it can also result in material breakdown.
Conversely, a low temperature increases the melt’s viscosity, demanding higher injection pressure and more energy consumption. Achieving the right balance requires precise control of barrel, nozzle, and mold temperatures according to the specific plastic material and product specifications.
Optimizing Injection Speed and Pressure
Injection speed and pressure directly influence the thermal dynamics of the process. By optimizing these parameters, you can reduce the melt’s residence time in the barrel and mold, significantly decreasing heat loss. However, it’s crucial to strike a balance; excessively high speeds might cause defects like flow lines or burn marks on the finished product.
Similarly, selecting an appropriate injection pressure ensures smooth mold filling without undue temperature spikes that could lead to heat loss. Proper control here guarantees that the melt fills the mold efficiently while mitigating heat accumulation.
Shortening the Molding Cycle
Reducing the molding cycle time is another effective method of controlling heat management. By shortening non-productive phases such as mold opening, closing, and cooling times, you can minimize unnecessary heat dissipation. Implementing rapid cooling systems is one strategy that accelerates product cooling, thereby reducing cycle time.
Synchronizing With Environmental Conditions
The production environment plays a critical role in heat management. Ensuring a stable workshop temperature helps maintain an optimal thermal balance. External factors like air flow can also be regulated by installing screens or isolation devices to prevent unnecessary heat removal by drafts or ventilation systems.
Incorporating these process control strategies not only enhances energy efficiency but also elevates the overall quality of the manufactured products. By scrutinizing each element within the process control framework, manufacturers can achieve remarkable advancements in operational effectiveness while minimizing heat-related issues.
Precise temperature control prevents plastic degradation.True
Controlling temperature avoids overheating, preventing material breakdown.
Higher injection speed always reduces product defects.False
Excessive speed can cause defects like flow lines or burn marks.
What Environmental Factors Should Be Considered to Minimize Heat Loss?
Environmental conditions play a pivotal role in minimizing heat loss during injection molding, directly impacting energy efficiency and product quality.
To minimize heat loss in injection molding, maintain a stable production environment temperature and minimize air flow around the equipment. These measures help preserve heat within the system, optimizing energy use and ensuring consistent product quality.
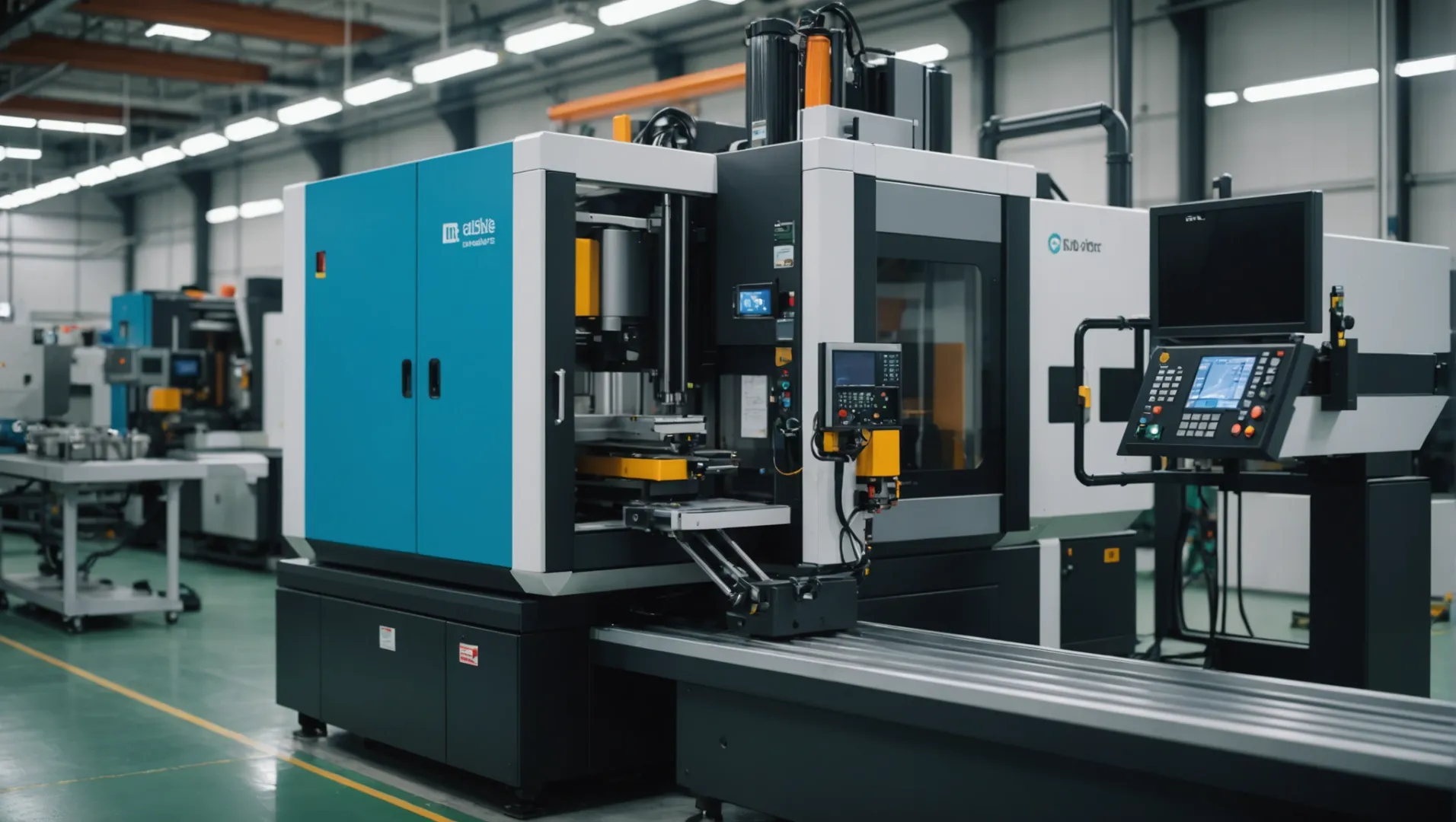
Maintaining a Stable Production Environment
One of the most significant environmental factors that can influence heat loss during injection molding4 is the ambient temperature of the production environment. Keeping this temperature within an optimal range is crucial.
-
Impact of Temperature Fluctuations: Variations in the production environment’s temperature can lead to inconsistent heat transfer, which affects the molding process. For instance, a colder environment can increase heat loss from the injection system to the surroundings, leading to higher energy consumption as the system works harder to maintain optimal temperatures.
-
Strategies for Control: To combat this, it’s advisable to insulate the production area effectively and employ climate control systems to keep the temperature stable. This ensures that the energy used in heating is efficiently retained within the system.
Minimizing Air Flow
Air flow around the injection molding machine is another environmental factor that significantly impacts heat retention.
-
Reducing Heat Removal: Strong air currents can strip away heat from the machine surfaces, increasing energy demands to compensate for this loss. This is especially problematic in environments where large fans or vents are present.
-
Practical Measures: Implementing barriers or screens can help minimize unwanted air flow around critical areas of the equipment. Additionally, positioning machines away from direct drafts or creating isolated sections within the production floor can further reduce unnecessary heat loss.
Additional Environmental Considerations
-
Humidity Control: While primarily a concern for material storage and handling, humidity levels can also affect heat retention. High humidity may lead to condensation on cooler parts of the equipment, inadvertently impacting thermal efficiency.
-
Lighting and Equipment Layout: The positioning of lighting and other heat-generating equipment should be considered. Excessive heat from these sources can lead to uneven thermal conditions, affecting the molding process’s consistency.
These environmental adjustments not only enhance thermal efficiency but also contribute to a more sustainable operation. By carefully managing these factors, manufacturers can achieve reduced energy consumption and improved process stability.
Stable temperature reduces heat loss in injection molding.True
Maintaining a stable production temperature minimizes inconsistent heat transfer.
High air flow improves heat retention in molding machines.False
Strong air currents increase heat loss from machine surfaces, not retention.
Conclusion
By adopting these practices, you can significantly reduce heat loss, boost efficiency, and enhance product quality. Reflect on these insights and take action to optimize your processes!
-
Discover cutting-edge solutions to enhance thermal management.: Direct Metal Laser Sintering (DMLS) is a new technology in plastic injection molding that utilizes metal 3D printing to create molds. This … ↩
-
Discover the top mold materials that enhance thermal management.: So, for difficult mold geometries, especially larger molds, a good distribution may be obtained when using high thermal conductivity steels. As … ↩
-
Understand how controlling injection temperature optimizes energy use and product quality.: Inappropriate temperature levels during the molding process can mar the desired outcome in no small measure. ↩
-
Understand how environmental temperature influences injection molding processes.: 2. Impact on Product Dimensions. If the mold temperature is too high, the melt may undergo thermal decomposition, increasing the shrinkage rate … ↩