Demolding may seem like a small step in the injection molding process, but it’s one that carries significant weight—literally!
To control demolding force in precision injection molding, optimizing mold design, adjusting process parameters, using suitable release agents, and considering secondary demolding techniques are essential. These strategies help manage friction and internal stresses, improving product release and overall production efficiency.
As we dive deeper into this fascinating topic, you’ll discover nuanced strategies that can transform your approach to overcoming demolding challenges.
Draft angles reduce demolding force in injection molding.True
Draft angles facilitate easier ejection by reducing friction between mold and product.
What Role Does Product Design Play in Demolding Force?
In precision injection molding, understanding the impact of product design on demolding force is essential for achieving optimal results.
Product design significantly influences demolding force in injection molding. Key factors include geometric complexity, draft angles, and structural features like undercuts. Properly designed products with smooth surfaces and suitable draft angles can minimize friction and adhesion, thereby reducing demolding force.
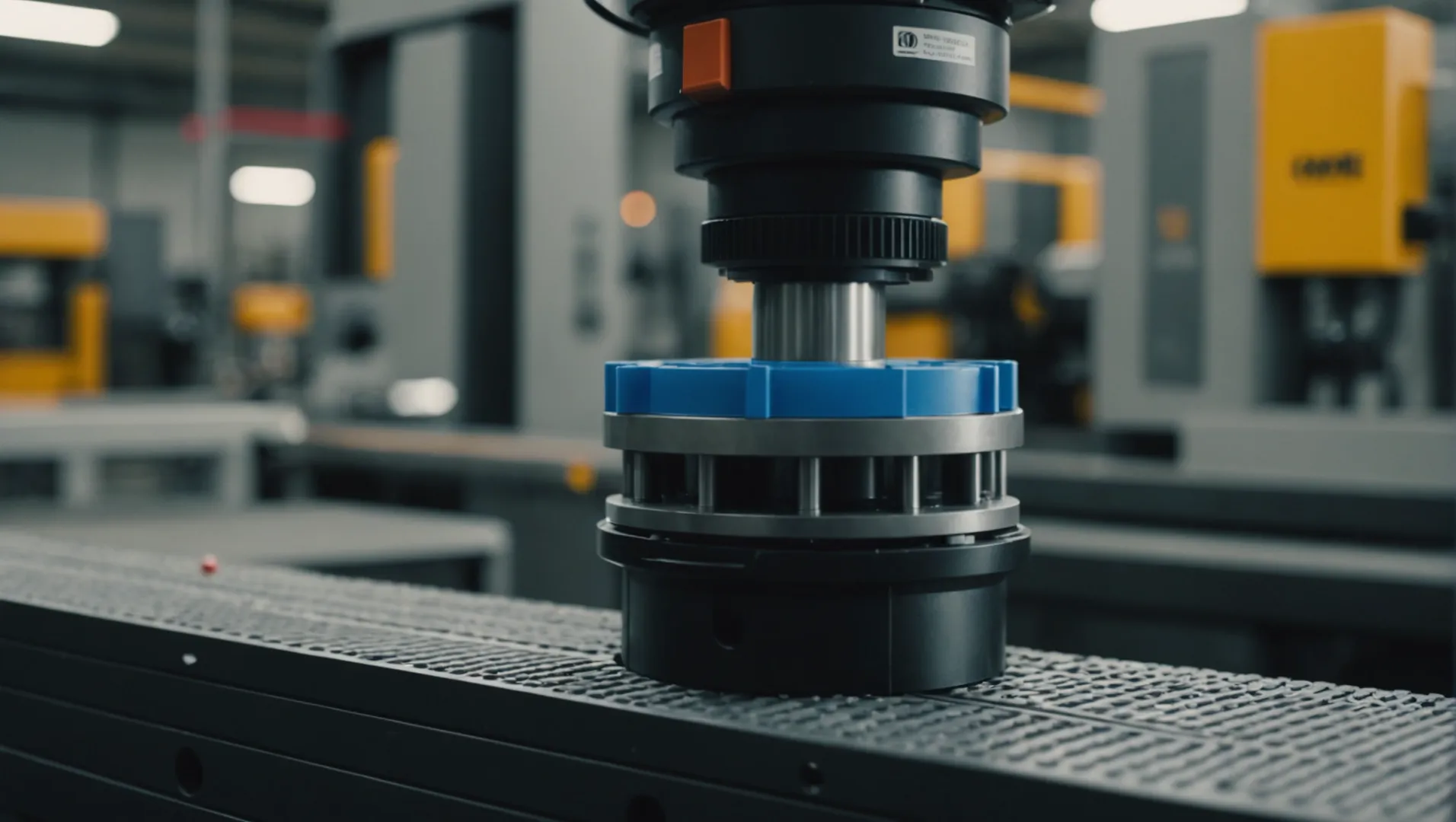
Understanding Product Geometry
The geometry of a product is a primary factor in determining the demolding force. Complex shapes with deep cavities or intricate undercuts often require more force to release from the mold due to increased surface contact and friction. For example, a product with a simple cylindrical shape will generally demold more easily than one with intricate latticework.
Draft Angles
Draft angles are tapered sections of a product’s design that facilitate easier ejection from molds. A well-calculated draft angle can significantly decrease the force required for demolding. Typically, a draft angle between 0.5° and 2° is recommended. This small taper helps reduce the friction between the mold and the product, ensuring a smoother release.
Structural Features
Certain structural features like thin walls can pose challenges during demolding. Thin-walled products might cool unevenly, leading to higher internal stress and increased demolding force. Careful design consideration must be given to balance structural integrity with ease of demolding.
Design Aspect | Impact on Demolding Force |
---|---|
Complex Geometry | Increases force due to friction |
Sufficient Draft Angle | Decreases friction, easing release |
Thin-Walled Structures | May increase stress and force |
Material Characteristics and Their Design Implications
Materials with high shrinkage rates tend to grip the mold tightly, resulting in higher demolding forces. Designers should consider material properties like shrinkage and hardness when developing a product design. Materials with lower shrinkage rates will generally lead to more manageable demolding forces.
Surface Finish Considerations
The surface finish of a product also plays a crucial role in demolding. A smoother surface reduces adhesion between the mold and the product, facilitating easier ejection. Techniques such as EDM (Electrical Discharge Machining) can be employed to achieve high-precision finishes that aid in reducing demolding force.
Innovative Design Approaches
Incorporating features that distribute the demolding force evenly across the product can prevent damage during ejection. For instance, integrating ribs or gussets can help manage stress distribution effectively.
Designers must leverage a combination of geometry, material characteristics, and surface finish to mitigate excessive demolding forces. By understanding these design principles, you can create products that not only meet functional requirements but also optimize manufacturing efficiency.
Draft angles reduce demolding force in injection molding.True
Draft angles help decrease friction, easing product release from molds.
Complex geometry decreases demolding force during molding.False
Complex shapes increase surface contact, raising friction and demolding force.
How Can Mold Design Innovations Reduce Demolding Force?
Mold design is crucial in minimizing demolding force, a key factor in injection molding efficiency and product quality.
Innovative mold design reduces demolding force by enhancing surface finishes, optimizing cooling systems, and employing advanced demolding mechanisms. These improvements lower friction and stress during product release, boosting efficiency and minimizing damage risks.
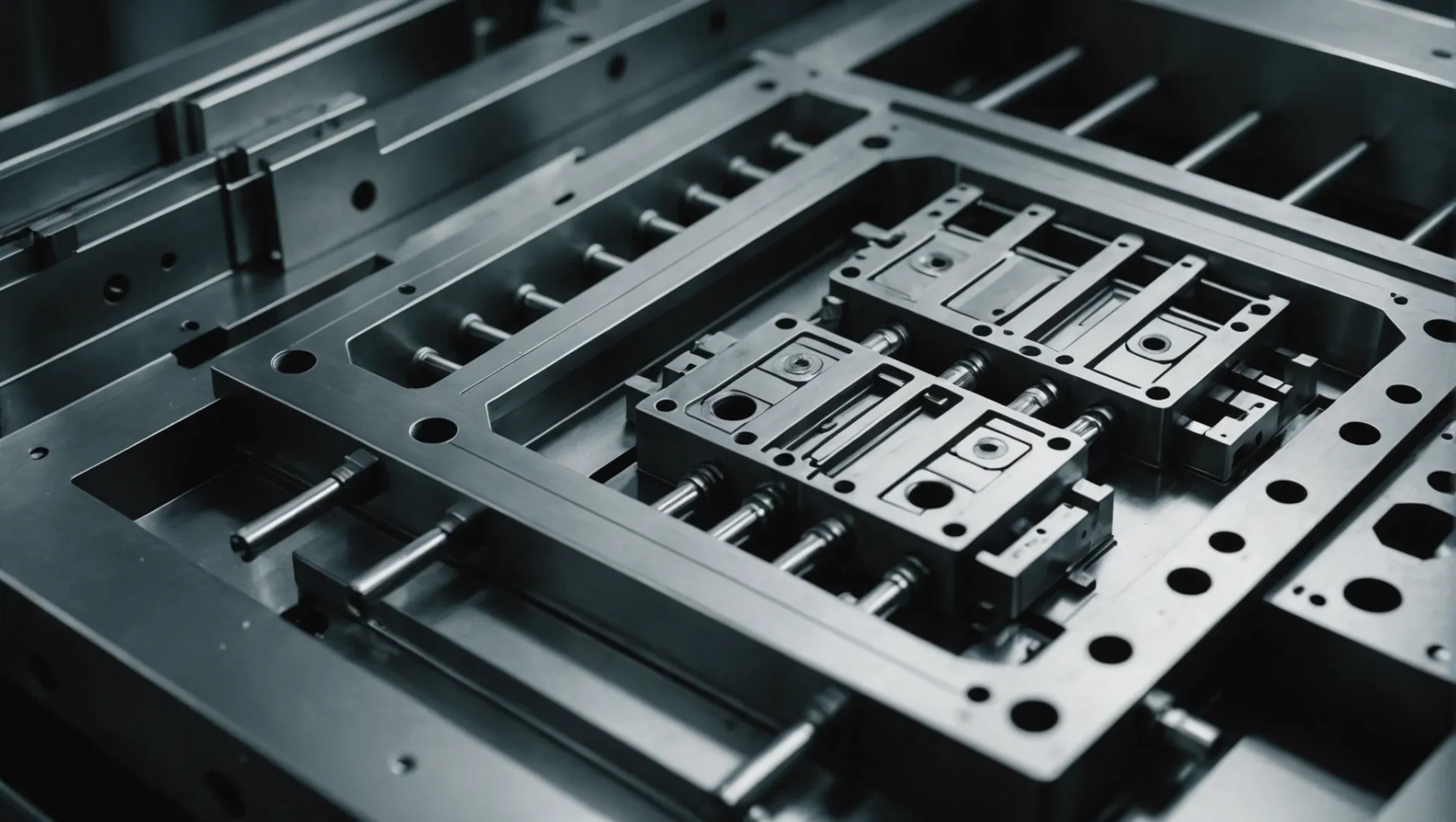
Importance of Surface Finish
A high-quality surface finish1 is essential for reducing friction between the mold and the product. Advanced techniques like EDM (Electrical Discharge Machining) and laser polishing create smoother surfaces that facilitate easier release. By minimizing friction, the demolding force required is significantly lowered, enhancing the production rate.
Cooling System Enhancements
An optimized cooling system2 is vital for uniform cooling, which reduces internal stresses within the molded part. By ensuring even temperature distribution, the potential for warping or shrinkage is minimized, thus lowering the demolding force. Innovations in cooling channel designs, such as conformal cooling, can further aid in achieving more efficient heat dissipation.
Traditional Cooling | Conformal Cooling |
---|---|
Straight channels | Custom-fitted channels |
Uneven cooling | Uniform cooling |
Increased stress | Reduced stress |
Advanced Demolding Mechanisms
Incorporating advanced mechanisms like ejector pins, sliders, and pneumatic systems can effectively reduce demolding force. These mechanisms work by distributing the force more evenly across the product, preventing localized stress and potential damage. For instance, sliders3 enable the controlled release of complex geometries, such as undercuts, that would otherwise increase resistance during demolding.
Innovations in mold design not only address existing challenges but also open new possibilities for creating complex and intricate designs without compromising on efficiency or quality. As technology evolves, embracing these innovations will be crucial for manufacturers aiming to stay competitive in the precision injection molding industry.
Advanced mold designs reduce demolding force.True
Innovations like improved surface finishes and cooling systems lower friction.
Traditional cooling systems increase demolding force.True
Straight channels cause uneven cooling, raising internal stresses.
Which Material Properties Influence Demolding Challenges?
In precision injection molding, understanding material properties is crucial for mitigating demolding challenges. This knowledge directly impacts the quality and efficiency of the production process.
Material properties like shrinkage rate, hardness, and elastic modulus are pivotal in influencing demolding challenges. Higher shrinkage rates can increase holding forces, while high hardness and low elastic modulus materials may deform easily, complicating demolding processes.
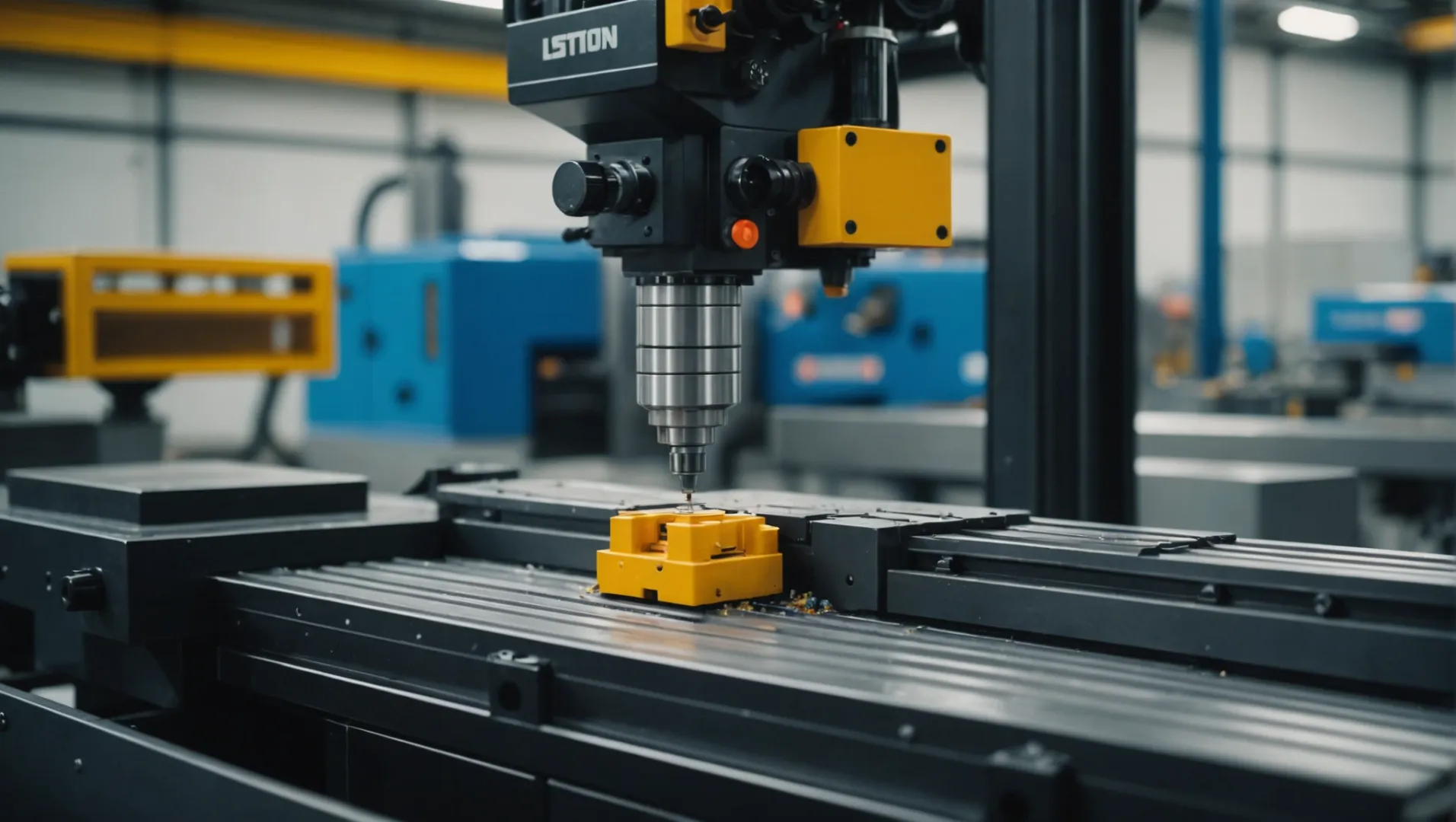
Understanding Material Properties in Injection Molding
The characteristics of the materials used in injection molding4 play a vital role in determining the ease or difficulty of demolding. These properties can either contribute to smooth ejection or pose significant challenges that need careful management.
Shrinkage Rate
The shrinkage rate of a plastic material is a critical factor. Materials with higher shrinkage rates tend to contract more upon cooling, which increases the holding force against the mold surfaces, making demolding more difficult. In contrast, materials with lower shrinkage rates can reduce such forces, facilitating easier release.
Example:
- High Shrinkage: Polypropylene (PP) generally exhibits high shrinkage rates, leading to increased demolding forces.
- Low Shrinkage: Acrylonitrile Butadiene Styrene (ABS) typically has lower shrinkage rates, easing demolding.
Hardness and Elastic Modulus
The hardness and elastic modulus of a material also significantly influence demolding challenges. Materials with higher hardness might resist deformation but can increase the friction between the product and the mold. Conversely, a low elastic modulus might lead to excessive deformation during demolding, complicating the process further.
Example:
- High Hardness: Polycarbonate (PC) materials, known for their toughness, may require additional strategies to ensure effective demolding.
- Low Elastic Modulus: Thermoplastic elastomers (TPEs) can deform easily, potentially leading to defects if not properly managed.
Strategies to Mitigate Material-Based Challenges
Given these properties, several strategies can be employed to mitigate their impact on demolding:
- Material Selection: Choose materials with appropriate shrinkage rates and balance between hardness and elasticity for your specific application.
- Adjusting Process Parameters: Fine-tuning temperature settings and cooling times can help manage the material behavior during demolding.
- Mold Surface Treatment: Implementing surface treatments or coatings on molds can reduce friction and accommodate material shrinkage variations.
- Release Agents: Use of compatible release agents that can form a barrier between the mold and the product, reducing friction and aiding in smooth demolding.
By understanding and strategically managing these material properties, manufacturers can significantly reduce demolding difficulties and improve overall production outcomes.
High shrinkage rates increase demolding forces.True
Higher shrinkage rates cause more contraction, increasing holding forces.
Low elastic modulus materials deform easily during demolding.True
Materials with low elastic modulus can deform, complicating demolding.
What Are the Best Practices for Using Release Agents?
Release agents are pivotal in the injection molding process, aiding in smooth product removal and ensuring surface quality. Understanding best practices can lead to superior results.
Using release agents effectively involves selecting the right type, applying it correctly, and considering its compatibility with materials. This minimizes demolding force, improves product quality, and enhances production efficiency.
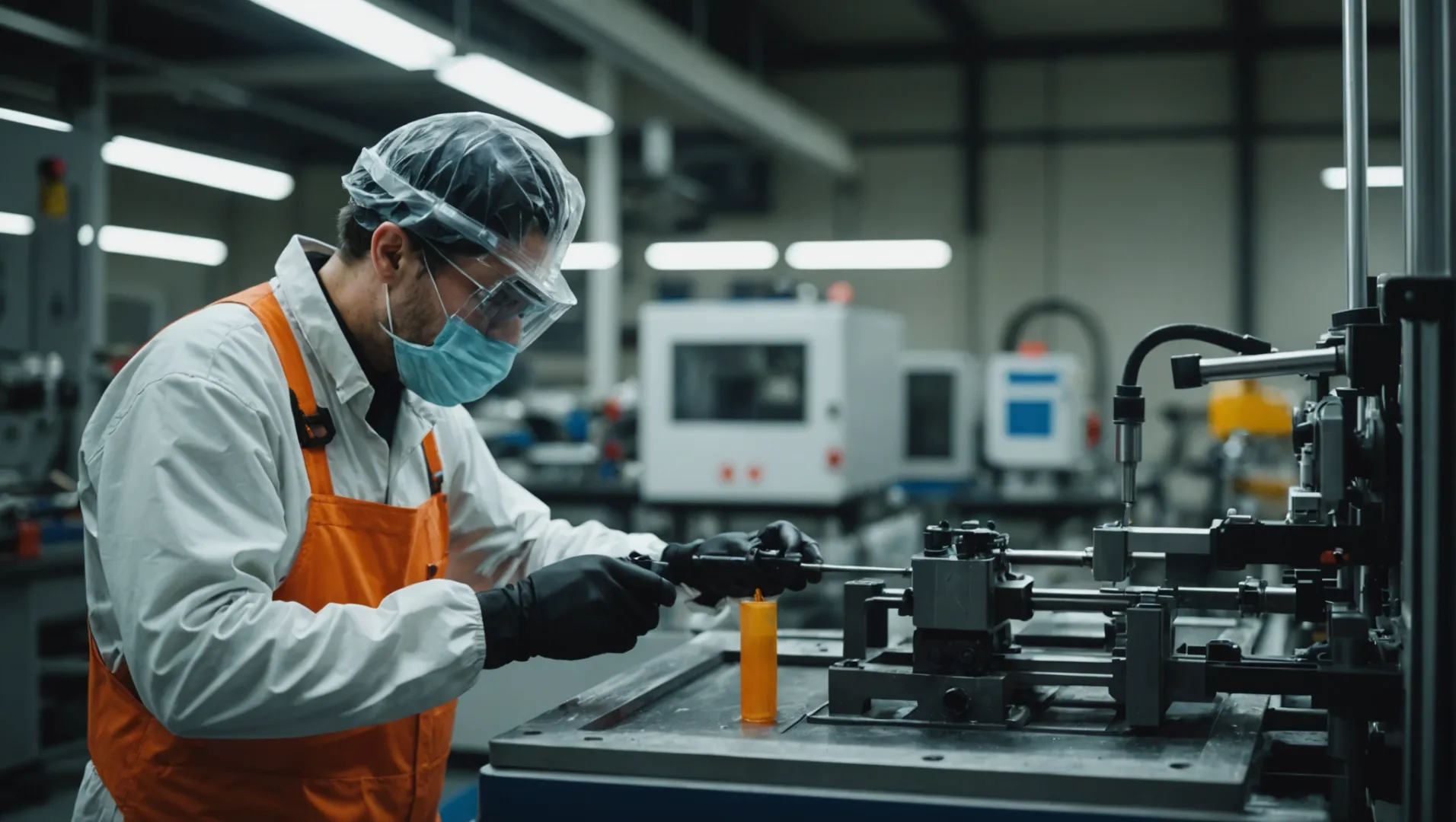
Selecting the Right Release Agent
Choosing a release agent begins with understanding its compatibility with the material you are working with. Different materials react uniquely to release agents, and a mismatch could compromise the surface finish or integrity of the molded product. For instance, silicone-based agents are excellent for high-gloss finishes5, while wax-based agents work well in high-temperature environments.
Application Techniques for Optimal Results
The way you apply a release agent can dramatically influence its effectiveness. Uniform application is crucial. Spraying ensures even coverage, reducing localized areas of excessive or insufficient agent, which can lead to defects. It’s recommended to use an airbrush for precision in application, especially for complex mold geometries.
Application Method | Benefits | Considerations |
---|---|---|
Spraying | Even distribution | Requires controlled environment |
Brushing | Good for small areas | Can be inconsistent |
Dipping | Complete coverage | Not suitable for large molds |
Managing Quantity and Frequency
Too much release agent can lead to residue build-up, affecting the surface quality of the finished product. Conversely, insufficient application might not adequately reduce friction. Monitoring the amount used and adjusting based on mold cycles is essential. Some advanced molding operations employ automated systems to regulate this process efficiently.
Environmental and Safety Considerations
While focusing on effectiveness, it’s also vital to consider environmental impact and safety. Opt for non-toxic and biodegradable release agents where possible. Proper ventilation during application can mitigate any potential health risks associated with fumes.
In conclusion, mastering the use of release agents involves a strategic approach in selection, application, and monitoring, ensuring they complement other demolding techniques effectively.
Silicone-based agents suit high-gloss finishes.True
Silicone-based release agents are ideal for achieving high-gloss surfaces.
Brushing ensures even release agent distribution.False
Brushing can lead to inconsistent application, unlike spraying.
Conclusion
Effectively managing demolding force is crucial for optimizing precision injection molding. By implementing expert strategies, I can enhance product quality and efficiency, ensuring successful production outcomes.
-
Explore how surface finish impacts friction and demolding efficiency.: Also, the mold sidewall roughness can affect the demolding process. In general, the demolding force increases with increasing sidewall roughness … ↩
-
Discover how cooling systems influence stress and demolding force.: Simulating the cooling stage can help determine what is happening inside of the mold and determine how the mold design can be improved. ↩
-
Learn about mechanisms that aid in reducing demolding resistance.: Explore key factors in mold design for efficient demolding mechanisms in injection molding, including part geometry, material properties, and production … ↩
-
Explore detailed insights on how material characteristics affect injection molding.: Impact properties are also influenced by temperature. Lower temperatures are more likely to produce brittle behavior in a material and the transition from … ↩
-
Discover which release agents excel at creating superior high-gloss finishes.: Mold releases act as a parting agent between layers of resin and the mold surface, so that cured parts can be removed without damaging the part or the mold. ↩