Choosing the right method for shaping a product feels like picking the perfect recipe. This choice really determines the success or failure of your story!
Compression molding and injection molding are two key methods in plastic manufacturing. Each method has its own benefits and limits. Compression molding shapes materials directly in the mold with pressure. Injection molding melts raw materials and pushes them into a cavity. Knowing these differences is very important for smart manufacturing choices. It’s really crucial to understand these methods.
I remember my first time diving into the world of molding. The debate between compression and injection molding felt intimidating. Each process has its own characteristics, strengths and quirks. Compression molding uses a simple method. It applies pressure to shape materials directly. Simplicity often describes this technique. In contrast, injection molding amazes with its speed and efficiency. It melts materials and injects them into detailed designs. These differences are like a compass on my design journey. They guide me to the right choices for my projects.
Compression molding requires less material than injection molding.True
Compression molding typically utilizes raw materials more efficiently, leading to less waste compared to injection molding.
Injection molding is faster than compression molding for large batches.True
Injection molding allows for quicker cycle times, making it more suitable for high-volume production compared to compression molding.
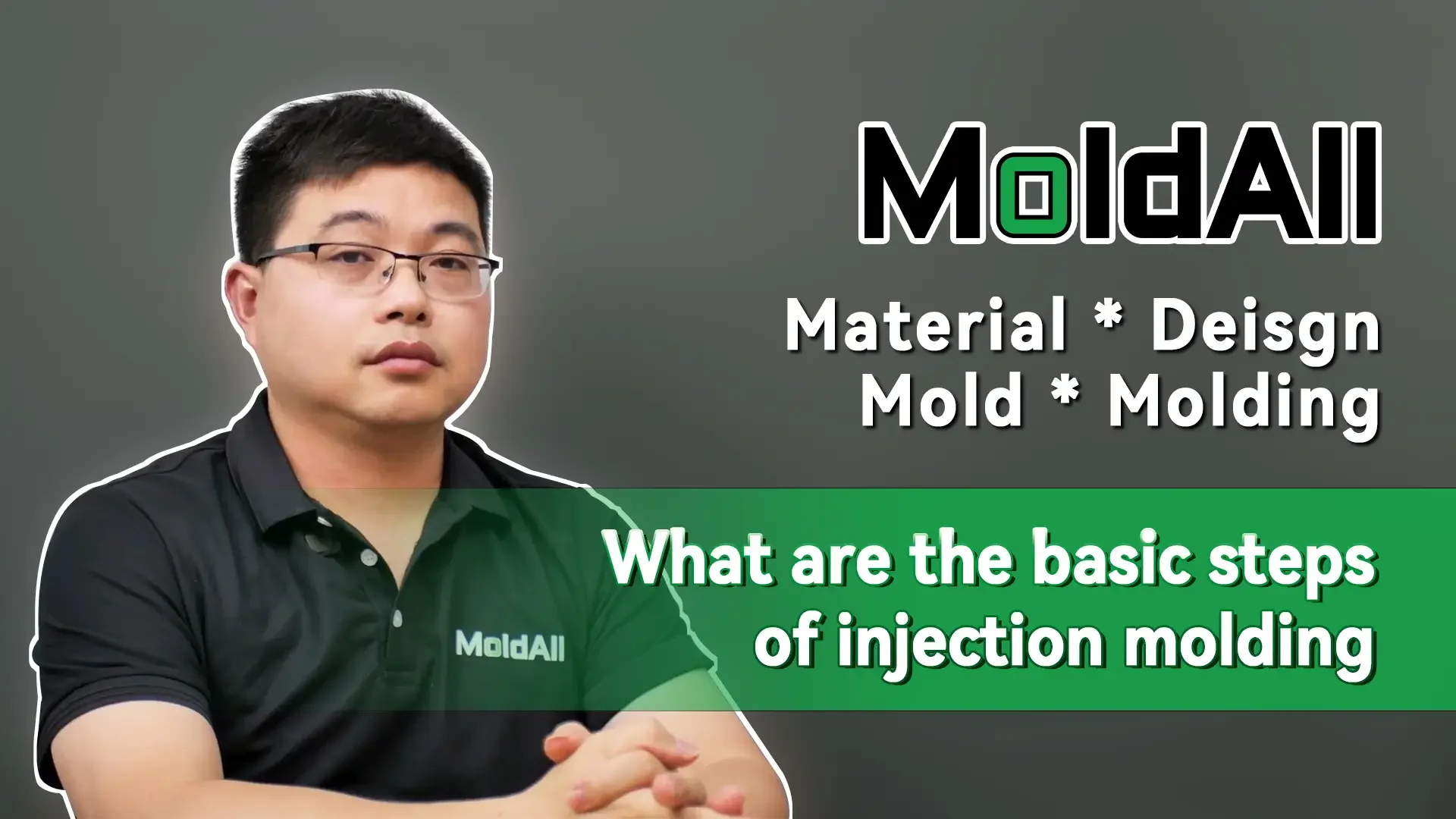
- 1. What are the Advantages of Compression Molding?
- 2. How Does Injection Molding Ensure High Precision?
- 3. What Factors Influence My Choice Between Compression and Injection Molding?
- 4. How Do Material Types Affect Molding Process Selection?
- 5. What Are the Cost Implications of Each Molding Technique?
- 6. Why Should You Choose Compression Molding Over Injection Molding?
- 7. Conclusion
What are the Advantages of Compression Molding?
Curious about the benefits of compression molding? Let me guide you through its unique advantages. It might just perfectly suit your next project. Compression molding really offers great benefits.
Compression molding provides many benefits. It is cost-effective and often suitable for larger parts. This method saves energy and reduces waste. Mold design becomes simpler with this technique. It is particularly perfect for thermosetting plastics. Compression molding also supports a wide variety of raw materials.
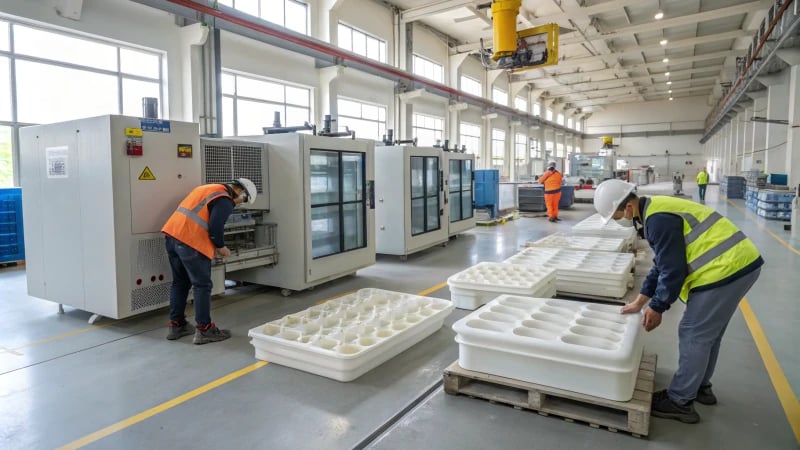
Cost-Effectiveness
Compression molding is budget-friendly. Injection molding requires complex, expensive equipment, while compression molding keeps things simple. A colleague at a small start-up shared how small compression molding equipment1 was revolutionary for them, producing high-quality parts without spending too much.
Suitable for Large Parts
Compression molding is great for making large parts. I worked on an automotive project needing thick plastic parts. Crafting large, sturdy pieces like dashboard panels was a big advantage. Compared to injection molding, compression molding often handles larger sizes better.
A comparison of the size limitations of both methods can be illustrated in the table below:
Molding Type | Size Limitations | Best Suited For |
---|---|---|
Compression Molding | Larger and thicker parts | Automotive parts, containers |
Injection Molding | Smaller, intricate parts | Electronics, toys, home appliances |
Versatility in Raw Materials
Compression molding fascinates me with its use of various raw materials – flakes, blocks, even fibers. One project used SMC (Sheet Molding Compound)2 with impressive results. This flexibility lets us adjust our methods for each specific application, really improving production.
Energy Efficiency
Saving energy is important in manufacturing. Compression molding reduces energy use thanks to shorter heating times. These savings grow quickly, especially in big production spaces where costs really matter.
Reduced Waste
Compression molding often creates less waste since it uses solid materials that are pressed into shape rather than melting and injecting excess plastic into molds. It’s beneficial for the earth and lowers disposal costs.
Ideal for Thermosetting Plastics
Compression molding is effective for thermosetting plastics. In a project with BMC (Bulk Molding Compound)3, high pressure was needed to cure properly. The outcomes were outstanding in both performance and quality. I now rely on this in my designs.
Simplified Mold Design
Compression molding has a simple mold design consisting of just two parts – the upper and lower mold. This simplicity makes them easier to create and helps lower maintenance costs over time compared to injection molds which have many extra systems.
Compression molding is more affordable than injection molding.True
The equipment for compression molding is simpler and cheaper, making it cost-effective for small businesses.
Compression molding is unsuitable for large plastic parts.False
Contrary to this claim, compression molding excels at producing larger and thicker components effectively.
How Does Injection Molding Ensure High Precision?
Injection molding captivates me with its ability to produce complex designs efficiently. What really happens behind the scenes to achieve such impressive precision? Let’s explore this intriguing process together!
Injection molding attains high precision through careful management of injection settings. Complex mold designs play a big role. Consistent material properties are crucial as well. Strong quality checks also contribute. These elements blend seamlessly to create detailed plastic parts. They meet very strict accuracy requirements.
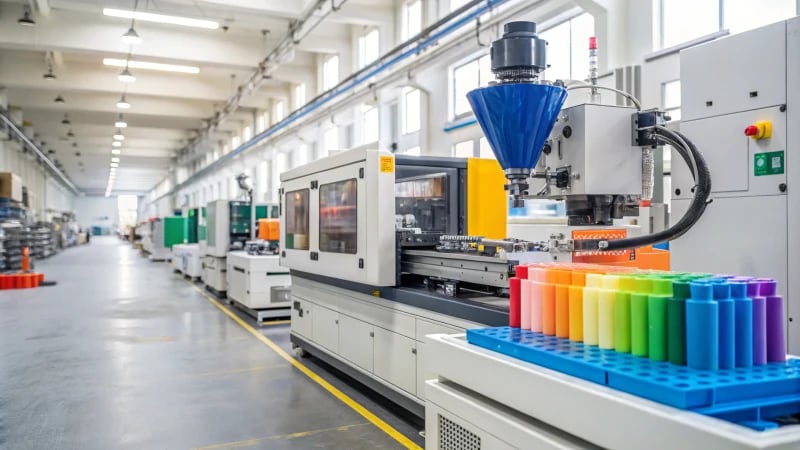
Understanding Injection Molding Precision
Injection molding is a fascinating way to produce plastic parts, blending art and engineering with great accuracy. I recall my first experience with this technique. Watching melted plastic flow into a detailed mold felt magical. What makes injection molding so accurate?
-
Controlled Injection Settings: Everything starts with precise settings. Speed, pressure, and temperature during the injection are adjusted carefully. This careful control allows the plastic to fill the mold smoothly, preventing mistakes and keeping everything consistent. Imagine the happiness of knowing each piece fits perfectly in its place!
-
Sophisticated Mold Design: Complex molds add to the precision of this process. Each mold is crafted with special cooling paths and pouring systems, which help control material flow and temperature. It’s like creating a small universe where every little detail is crucial. I have seen how this care improves the final product.
Factors Contributing to Precision
Learning about the different factors that give injection molding its precision helps me appreciate its benefits even more. Here’s a comparison with other methods:
Feature | Injection Molding | Compression Molding |
---|---|---|
Dimensional Accuracy | High precision, up to ±0.01 mm | Lower accuracy, may exceed ±0.5 mm |
Surface Finish | Excellent surface quality | Average surface quality |
Cycle Time | Short cycle time (seconds to minutes) | Longer cycle time (minutes to hours) |
Production Volume | Ideal for high-volume production | Best for lower volume, specialized parts |
Material Consistency
Materials in injection molding are very important. I remember seeing a factory line where tiny plastic pieces were fed into a machine, melted evenly and turned into beautiful parts. Here’s how it works:
- Even Melting: Raw materials are heated and mixed smoothly before entering the mold. This even melting is very important for achieving exact sizes and shapes.
- Material Properties: Different plastics give different precision levels. For instance, special engineering plastics provide better performance, similar to how the right ingredients improve a meal!
Quality Control Measures
Quality checks are the foundation of keeping precision in injection molding. Here are some measures used:
- In-Mold Sensors: These small devices track temperature and pressure, keeping everything within set limits.
- Statistical Process Control (SPC): Regular checks of production data find any issues early on, like checking a recipe while cooking.
- Post-Molding Inspections: Rigorous checks using tools like coordinate measuring machines (CMM) ensure each product matches design standards.
To learn more about these aspects, consider exploring advanced injection molding techniques4 or the role of materials in molding .
Injection molding can achieve precision up to ±0.01 mm.True
This claim highlights the exceptional dimensional accuracy of injection molding, making it suitable for high-precision applications.
Injection molding has longer cycle times than compression molding.False
This claim is false; injection molding typically has shorter cycle times compared to compression molding, enhancing efficiency.
What Factors Influence My Choice Between Compression and Injection Molding?
Navigating the world of molding seems overwhelming. Many others feel the same way, so you’re not alone. Choosing between compression and injection molding is a critical decision. This choice can influence your entire project. Let’s focus on what truly matters.
When choosing between compression and injection molding, consider mold complexity. Examine the forms of raw materials. Look at production efficiency. Evaluate product quality. Think about equipment investment. Assess which method suits the specific application better. Understanding these elements helps you decide wisely. Your decision will fit your project’s needs.
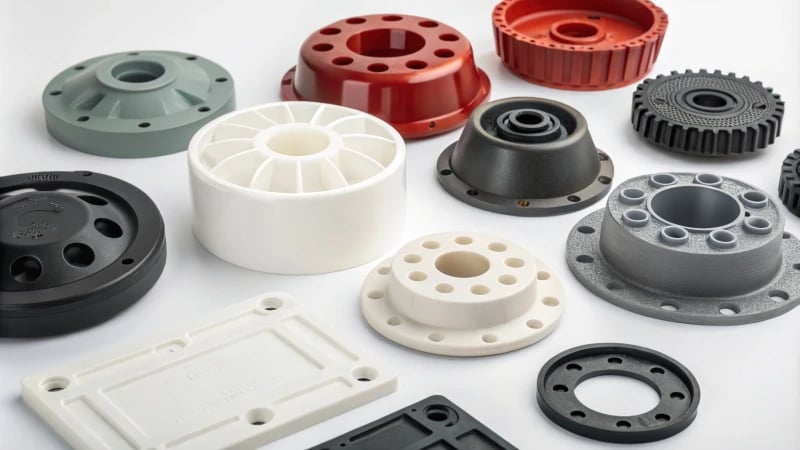
Understanding the Molding Principles
The molding principle is a foundational factor in determining the appropriate method for manufacturing plastic components. In compression molding, solid materials are placed directly into the mold and are melted and shaped by pressure.
On the other hand, injection molding involves heating granular or powdery raw materials until they flow and then injecting them into a mold cavity through a nozzle. This difference can greatly influence production efficiency and product quality.
For instance, compression molding5 is often ideal for larger, simpler shapes, while injection molding suits intricate designs that require precision.
Mold Structure Considerations
The complexity of the mold structure plays a crucial role in the decision-making process. Compression molds are typically simpler and consist of two parts, whereas injection molds have a more intricate design with additional systems.
Mold Type | Structure Complexity | Key Features |
---|---|---|
Compression Molding | Low | Simple two-part mold, suitable for larger parts |
Injection Molding | High | Complex systems for pouring, cooling, and ejection |
This structural complexity impacts both the cost and time associated with mold creation. Choosing the right mold structure can significantly affect production timelines and budget constraints.
Raw Material Forms
The forms of raw materials used in each process significantly influence their suitability for specific applications.
- Compression Molding: Utilizes flakes, blocks, or pellets. For example, SMC and BMC are common choices.
- Injection Molding: Primarily relies on granular or powdery plastics, which can melt quickly and evenly.
Choosing the right raw material form is essential to achieve desired product characteristics, such as strength and durability.
Production Efficiency Analysis
When considering production efficiency, injection molding generally offers faster cycle times compared to compression molding. The latter involves multiple steps including preheating and curing which can extend production times.
Molding Method | Cycle Time | Production Efficiency |
---|---|---|
Compression Molding | Longer (several minutes) | Lower efficiency due to more complex processes |
Injection Molding | Shorter (seconds) | High efficiency with potential for automated production |
For companies aiming for high-volume production, injection molding tends to be the preferred choice due to its speed.
Quality and Precision Factors
The quality and precision of the products produced can sway decisions between these two methods. Injection molding generally yields higher dimensional accuracy and better surface finishes compared to compression molding.
- Compression Molding: Often results in lower precision with potential defects like burrs.
- Injection Molding: Capable of producing highly detailed parts with consistent quality.
This factor is crucial for industries where product performance is directly tied to precision, such as in electronics or automotive components.
Equipment Investment Insights
Investing in equipment can vary drastically between the two methods. Compression molding requires less complex machinery and typically has lower upfront costs.
Molding Method | Initial Equipment Cost | Long-term Investment |
---|---|---|
Compression Molding | Lower | Suitable for small to medium enterprises |
Injection Molding | Higher | Significant investment needed for high efficiency machinery |
Understanding the financial implications of equipment investments is essential for making an informed decision that aligns with business goals.
Applications of Each Method
Different applications favor different molding techniques. Compression molding is often preferred for larger, simpler products while injection molding excels in producing small, intricate parts with high precision.
Injection molding is faster than compression molding.True
Injection molding offers shorter cycle times, making it more efficient for high-volume production compared to the longer processes involved in compression molding.
Compression molds are more complex than injection molds.False
Compression molds are simpler in design, typically consisting of two parts, while injection molds feature more intricate systems for production.
How Do Material Types Affect Molding Process Selection?
Have you ever thought about why some products roll smoothly off the production line while others have problems? Knowing how material types affect the choice of molding process holds the secret. This knowledge is very important. Let’s explore it!
Material types are very important in choosing molding processes like compression or injection molding. Thermal properties, viscosity and strength requirements are key factors. These factors affect both efficiency and product quality in manufacturing.
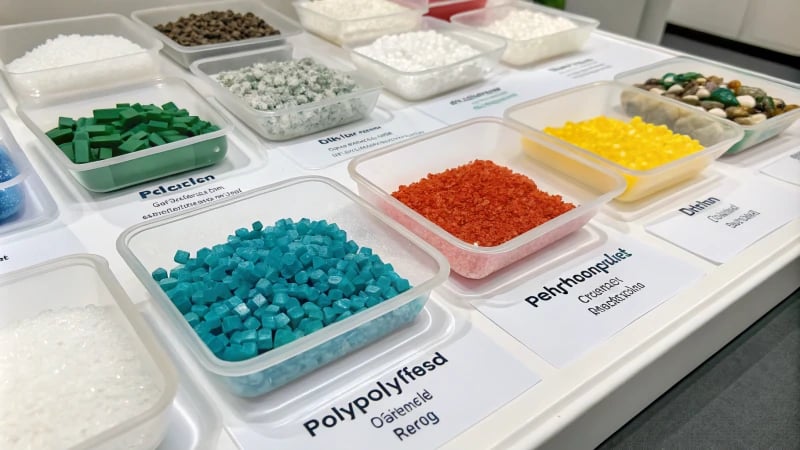
Understanding Material Properties
Material properties significantly influence the choice of molding processes, primarily due to their impact on thermal behavior, flow characteristics, and mechanical performance. For example, materials like thermoplastics are suitable for injection molding6 because they can be melted and re-molded multiple times without losing their properties.
In contrast, thermosetting plastics, which undergo a chemical change when heated, are more compatible with processes like compression molding7. This distinction arises because thermosets require a curing phase where the material must not be melted again once set.
Impact on Molding Process Selection
When selecting a molding process, designers must consider:
- Thermal Properties: High thermal stability materials can withstand elevated temperatures during molding.
- Viscosity: Low viscosity materials flow better in injection molds, ensuring uniform filling of intricate designs.
- Strength Requirements: Materials intended for load-bearing applications may require special molding techniques8 to enhance structural integrity.
Property | Thermoplastics | Thermosets |
---|---|---|
Melting Point | Lower (can be reprocessed) | Higher (cannot be remolded) |
Flowability | High (ideal for injection molding) | Lower (better for compression molding) |
Curing Process | None | Requires heat/pressure for curing |
Recycling Capability | Yes | No |
Choosing the Right Molding Process
The right selection between compression and injection molding can hinge on:
- Material Form: Granular forms favor injection molding due to ease of feeding.
- Complexity of Design: Intricate designs necessitate injection molding for better precision and detail.
- Production Volume: High-volume production aligns well with injection molding due to faster cycle times.
For example, manufacturing a complex component like an electronic housing typically utilizes injection molding9 due to its precision and speed, while larger, simpler components might be effectively produced using compression molding.
Conclusion on Material Influence
Understanding how materials and molding processes interact is crucial. This knowledge can elevate product quality and manufacturing effectiveness significantly. Proper attention to these factors transforms product performance.
Thermoplastics can be remolded multiple times without loss.True
Thermoplastics are designed to be melted and reshaped repeatedly, maintaining their properties throughout the process.
Compression molding is suitable for thermoplastics due to low viscosity.False
Thermoplastics are better suited for injection molding; compression molding fits thermosets due to their curing requirements.
What Are the Cost Implications of Each Molding Technique?
Have you ever thought about how picking a molding technique affects your budget? Knowing these money details is very important for people making manufacturing choices.
The cost implications of molding techniques change with different factors. The factors include material type, tooling complexity, production volume, labor needs, cycle time and product quality. Compression molding is generally cheaper for small production runs. Injection molding succeeds in high-volume situations.
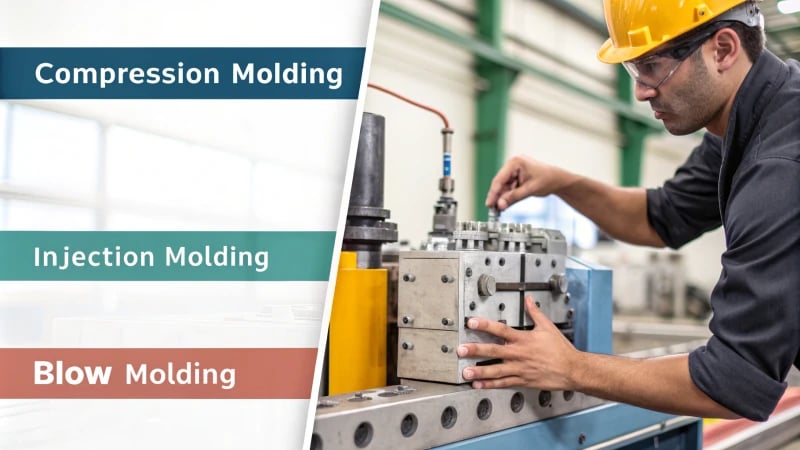
Understanding Cost Factors in Molding Techniques
When evaluating the cost implications of molding techniques, it’s essential to consider several factors that influence overall expenses.
-
Material Costs: The type of raw materials used significantly impacts the cost of production. For instance,
- Compression molding often uses bulk or sheet molding compounds which can be more affordable, especially in larger quantities.
- Injection molding typically requires higher-quality granular materials that are more expensive, reflecting in higher production costs.
-
Tooling Costs: The design and manufacturing of molds can vary greatly between the two techniques:
- Compression Molding Tooling: Generally simpler and less expensive. The mold can be made from less costly materials due to lower precision requirements.
- Injection Molding Tooling: More complex and expensive due to the need for precision parts and additional systems like cooling and ejection mechanisms.
Molding Technique | Tooling Complexity | Estimated Cost Range |
---|---|---|
Compression Molding | Low | $5,000 – $20,000 |
Injection Molding | High | $20,000 – $100,000+ |
-
Production Volume: The scale of production also plays a crucial role in determining costs:
- Compression molding is often more cost-effective for smaller production runs due to lower initial setup costs.
- Injection molding shines in high-volume production, where the per-unit cost decreases significantly with larger quantities due to faster cycle times.
-
Labor Costs: Labor involved in each process can influence overall costs.
- Compression molding typically requires more manual intervention and thus may incur higher labor costs per unit.
- Injection molding can often be automated, leading to lower labor costs per unit in high-volume scenarios.
-
Cycle Time and Efficiency:
- Compression molding has longer cycle times, which can lead to higher costs in terms of machine operation time.
- In contrast, injection molding boasts shorter cycles, which can improve throughput and reduce operational costs significantly. For example, a small part can take seconds to produce via injection molding compared to several minutes for compression molding.
-
Quality and Defect Rates:
- While compression molding may produce defects like burrs or flying edges that require rework, injection molding generally yields higher quality parts with fewer defects.
- This aspect not only affects immediate production costs but also long-term expenses related to rework and quality assurance.
For further insights on how these factors interact and impact your specific project budget, explore cost metrics for molding techniques10 or mold cost calculators11.
Compression molding is cheaper for small production runs.True
Due to lower initial setup costs, compression molding is often more economical for smaller quantities compared to injection molding.
Injection molding requires higher quality materials than compression molding.True
Injection molding typically uses more expensive granular materials, reflecting its need for higher quality in production.
Why Should You Choose Compression Molding Over Injection Molding?
Some manufacturers choose compression molding over injection molding. This might make you curious. Unique uses make compression molding stand out. It could be the best option for you.
Compression molding excels in applications that need larger components and lower costs. This method is really suitable for thermosetting materials. These materials are often used in automotive parts and construction materials.
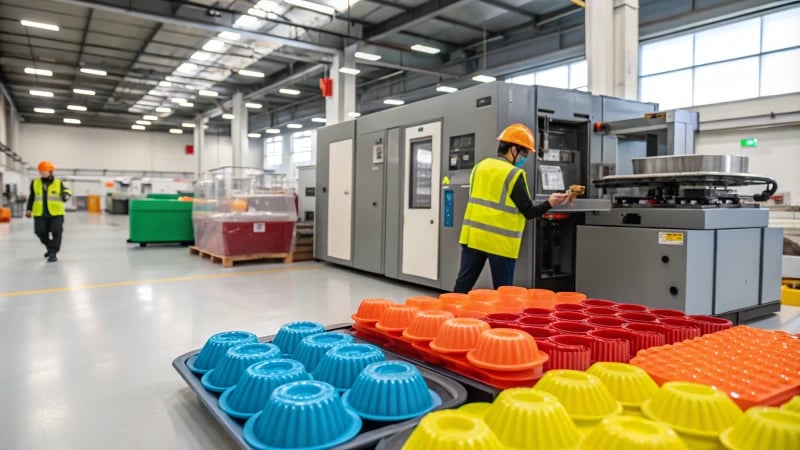
Understanding Compression Molding
When I first came across different ways of manufacturing, I felt curious about how compression molding functions. This process is simple yet powerful. Solid materials go into a heated mold, where pressure shapes these materials into strong parts. In contrast, injection molding focuses on precision, using melted granules injected into a mold. As I learned more, I saw that choosing between them depends on what you want to create.
Advantages of Compression Molding
- Cost Savings: Compression molds are less costly to produce. This is smart for large runs of simple shapes and crucial for budget-sensitive projects.
- Material Flexibility: Compression molding works very well with thermosetting plastics like SMC (Sheet Molding Compound) and BMC (Bulk Molding Compound). We really benefit from this flexibility to make robust and durable products that last long.
- Large Parts: For big parts like automotive panels, compression molding is ideal. I once worked on an automotive project where large parts were made easily; detailed precision was less important here.
Applications Favoring Compression Molding
Application Type | Description | Example Products |
---|---|---|
Automotive Industry | Suitable for large interior components that require strength and durability. | Dashboards, door panels |
Construction Materials | Used for items needing bulk and thickness rather than precision. | Plastic floor tiles, large containers |
Electrical Components | Allows for the molding of parts that need electrical insulation. | Electrical housings, insulators |
Consumer Goods | Ideal for items that are large but do not require fine details. | Garden furniture, storage bins |
Limitations of Injection Molding
Injection molding is excellent for precise parts but often comes with higher upfront costs for molds and machinery. Higher complexity leads to increased maintenance requirements and longer lead times for setup. Therefore, compression molding is often favored when:
- High initial costs need to be avoided.
- Products have simpler geometries and larger sizes.
- Thermosetting materials are necessary for performance.
Conclusion on Applications
In my manufacturing experience, compression molding is best for saving costs and making large parts while valuing size over detail. This is why it is often used in automotive and construction industries where durability is key. For further insights into molding processes12, consider exploring detailed industry reports.
Compression molding is ideal for producing small, intricate designs.False
This claim is false. Compression molding is best for larger components, not small, intricate designs which are better suited for injection molding.
Compression molding is cost-effective for large production runs.True
This claim is true. Compression molds are generally less expensive to produce, making them cost-effective for larger runs of simpler shapes.
Conclusion
Explore the differences between compression molding and injection molding, focusing on their processes, efficiencies, costs, and ideal applications in plastic manufacturing.
-
This link provides insights into the economic benefits of compression molding that could influence your decision-making process. ↩
-
Learn more about thermosetting plastics to understand why compression molding is optimal for certain applications. ↩
-
Explore common raw materials used in compression molding processes and their specific benefits. ↩
-
Discover how injection molding technology achieves precision in manufacturing, which could enhance your design processes. ↩
-
Explore how different molding methods impact manufacturing efficiency and product quality to make an informed decision. ↩
-
Explore how different materials influence mold selection to optimize your designs and production processes effectively. ↩
-
Gain insights into best practices for material selection in various molding processes to enhance production outcomes. ↩
-
Learn about the advantages of different materials in molding processes to improve your design strategies. ↩
-
Understand the recycling capabilities of various materials used in molding to align with sustainable practices. ↩
-
Clicking this link will provide you with essential metrics to better understand the costs associated with different molding techniques. ↩
-
This link leads to calculators that can help you estimate mold costs based on your specific requirements and variables. ↩
-
Discover why compression molding may be the better choice for your manufacturing needs and how it compares to injection molding in practical applications. ↩