Ever wondered what drives the world of extrusion molding? Knowing the materials is a real game-changer for product designers.
Extrusion molding commonly uses materials like thermoplastics (e.g., polyethylene, polypropylene, PVC), thermosetting plastics, rubber, and composites, each providing unique properties for diverse manufacturing applications.
I moved through my design career and soon understood the importance of choosing the right materials. Identifying the best materials is crucial for bringing ideas to life. Designers need more than just random plastic – they require a real partner for their work. I chose polyethylene for one project. It really transformed the product’s durability and functionality. Many materials exist, from thermoplastics to composites. Each one has unique benefits. These materials probably elevate our designs in surprising ways.
Thermoplastics are the main materials in extrusion molding.True
Extrusion molding predominantly uses thermoplastics like polyethylene and polypropylene, making them essential for various manufacturing applications.
Rubber is not used in extrusion molding processes.False
Contrary to the claim, rubber is indeed one of the materials utilized in extrusion molding alongside plastics and composites.
- 1. What Are the Advantages of Thermoplastics in Extrusion Molding?
- 2. How Do Thermosetting Plastics Compare to Thermoplastics?
- 3. What Role Does Rubber Play in Extrusion Processes?
- 4. What Are Composite Materials and Their Benefits in Manufacturing?
- 5. How Do I Choose the Right Material for My Extrusion Project?
- 6. Conclusion
What Are the Advantages of Thermoplastics in Extrusion Molding?
Do you ever think about how thermoplastics could transform extrusion molding? Let’s explore the amazing advantages they offer. These benefits help production become efficient, innovative and sustainable. Thermoplastics really change the game.
Thermoplastics have many advantages in extrusion molding. They give design flexibility. Companies save money because thermoplastics are recyclable. Their strong mechanical properties offer really good durability. Quick processing times allow manufacturers to meet market demands efficiently.
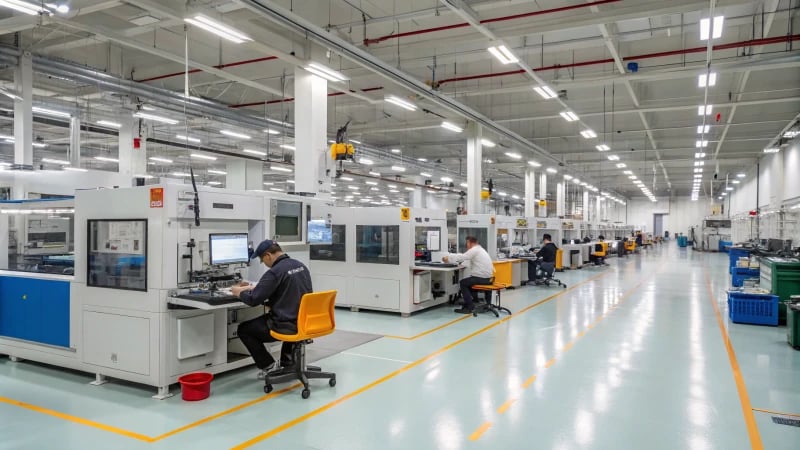
When I began learning about extrusion molding, I felt truly fascinated by thermoplastics. These handy materials change shape many times. Designers like me love this flexibility and creativity. My first project used Polyethylene (PE). I was amazed at how it molded into complex forms easily while keeping its strength.
Enhanced Flexibility and Design Freedom
Thermoplastics really offer flexibility in design. This allows creative exploration in various fields, especially automotive and consumer electronics. I designed a gadget part using Polypropylene (PP). Its ability to create intricate shapes added new possibilities for both function and looks.
- Polyethylene (PE): Acts like a chameleon. It adapts to many uses, from films to pipes, with its great flexibility.
- Polypropylene (PP): With strength and heat resistance, it is ideal for piping systems facing tough conditions.
This design freedom encourages innovation, as manufacturers can experiment with new shapes and forms without the constraints that rigid materials impose. Learn more about design flexibility1.
Cost-Effectiveness in Production
In production discussions, thermoplastics stand out. They can be recycled and molded again. This greatly reduces waste. During budgeting, I often feel relief when using thermoplastics. They lower costs and promote sustainability.
Material | Recyclability | Cost Per Kg | Typical Applications |
---|---|---|---|
Polyethylene (PE) | Highly recyclable | $1.00 | Films, pipes, insulation layers |
Polypropylene (PP) | Highly recyclable | $1.50 | Pipes, fibers, packaging |
Polyvinyl Chloride (PVC) | Limited recyclability | $1.20 | Profiles, window frames |
Polystyrene (PS) | Limited recyclability | $1.80 | Packaging materials, insulation |
This balance supports manufacturers and encourages a responsible production approach while contributing to more sustainable practices in production. Explore sustainability in production2.
Superior Mechanical Properties
In terms of durability, materials like Acrylonitrile-butadiene-styrene copolymer (ABS) and Polycarbonate (PC) are excellent.
- ABS: Like a trusty friend; suitable for strong items like luggage and electrical housings.
- PC: Impresses with clarity and heat resistance; perfect for lighting that needs both style and function.
These features help my designs meet standards and last longer while ensuring that products not only meet stringent performance standards but also last longer in their respective applications. Discover more on mechanical properties3.
Quick Turnaround Times
Thermoplastics process quickly due to their melting characteristics which allows for rapid production cycles in extrusion molding. During tight deadlines, I valued how fast materials like high-density polyethylene (HDPE) were extruded.
For instance, quick processing is vital in large-scale production scenarios such as making water supply pipes; it helps us keep up with market needs and new trends efficiently.Find out about production timelines4.
Conclusion
Reflecting on the advantages of thermoplastics, their flexibility, cost benefits, strength and quick processing give power to designers and manufacturers. Each use might need a different thermoplastic; understanding their benefits is crucial for better performance and new design possibilities.
Thermoplastics enhance design flexibility in manufacturing.True
Thermoplastics allow for the creation of complex shapes, essential for innovative designs in various industries.
Extrusion molding with thermoplastics is cost-effective.True
Their recyclability and ability to be remolded reduce waste and production costs compared to thermosetting plastics.
How Do Thermosetting Plastics Compare to Thermoplastics?
Navigating the world of materials can feel overwhelming, especially when it comes to understanding thermosetting plastics versus thermoplastics. But don’t worry, I’m here to break it down for you in a way that’s not only informative but relatable. Let’s dive into their unique traits and applications together!
Thermosetting plastics are very strong and resist heat. They do not change once cured. Thermoplastics have different properties. Manufacturers can remold and recycle them easily. This flexibility benefits diverse industries. Each type of plastic suits specific uses.
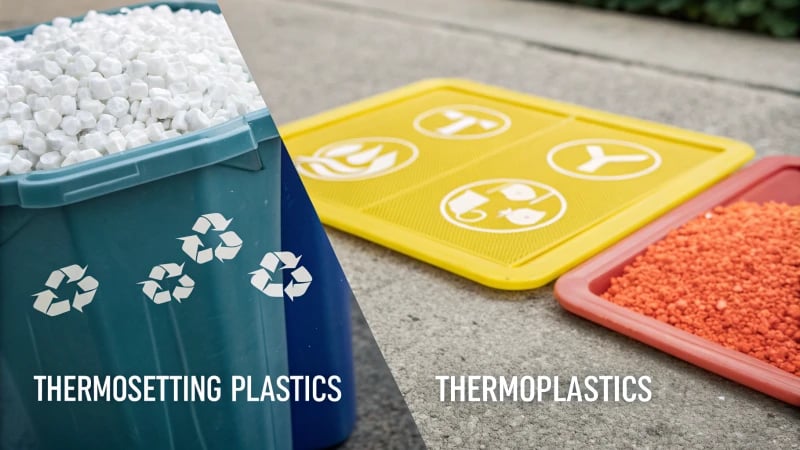
Overview of Thermoplastics
Thermoplastics are like a friend who quickly adapts and changes plans. They soften and become moldable when heated. They change shape and can be recycled. This flexibility is very useful in many design situations.
Common examples include:
- Polyethylene (PE): Think of those plastic bags at grocery stores or water pipes at home. PE is known for bending easily and resisting low temperatures.
- Polypropylene (PP): This plastic is strong and heat-resistant. It is used in building systems where strength is important.
- Polyvinyl Chloride (PVC): Depending on how it’s made, PVC can be stiff or bendable. It is common in construction and electrical insulating.
Overview of Thermosetting Plastics
Thermosetting plastics are like a determined friend who sticks to decisions. Once heated and shaped, they keep their form forever.
Examples include:
- Phenolic Resin (PF): This material is very good for electrical insulation because it resists heat and lasts long.
- Urea-Formaldehyde Resin (UF): I’ve noticed it in household things like buttons and tableware, where toughness and resistance to water matter.
Properties Comparison
Property | Thermoplastics | Thermosetting Plastics |
---|---|---|
Moldability | Re-moldable upon heating | Non-re-moldable after curing |
Heat Resistance | Lower thermal stability | High thermal stability |
Mechanical Strength | Varies significantly | Generally higher strength |
Chemical Resistance | Good, varies with type | Excellent, especially PF and UF |
Applications | Packaging, automotive parts | Electrical components, structural applications |
Applications in Industry
I see thermoplastics everywhere in my work. They quietly support consumer products like PE containers and sturdy ABS luggage. Thermosetting plastics excel in tough environments. I often consider the aerospace industry when thinking about materials that handle extreme conditions. Materials like PEEK are fantastic here as they provide accuracy and reliability in electronics.
Final Thoughts
Choosing between thermoplastics and thermosetting plastics is crucial for meeting project needs. Understanding their different qualities has made my design choices much clearer over time. If you explore material properties as I have, do not hesitate to view material comparisons. With the right knowledge, you’ll probably handle any design challenge!
Thermoplastics can be reshaped after cooling.True
Thermoplastics are moldable upon heating and solidify upon cooling, allowing for reshaping and recycling.
Thermosetting plastics are easily remolded after curing.False
Once thermosetting plastics are cured, they cannot be reshaped or remolded, making them rigid and durable.
What Role Does Rubber Play in Extrusion Processes?
Did you ever think about how rubber affects our daily lives? Rubber is crucial. Tires and toys use it. Rubber plays a major role in extrusion processes. This material is very important. Rubber is not just any material. It plays a key part in manufacturing success.
Rubber holds a vital place in extrusion processes. It provides flexibility, durability and resistance to wear. Natural and synthetic rubbers serve many industries. They help create high-performance components. Many rely on rubber for key products.
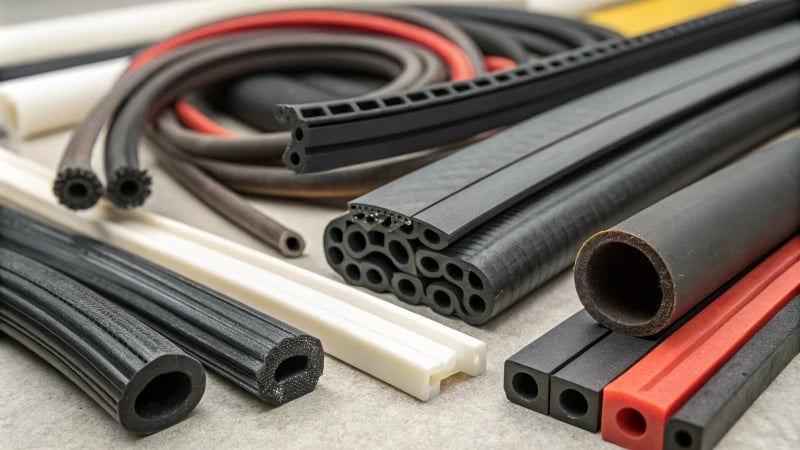
Introduction to Rubber in Extrusion Processes
Rubber is a friend that always helps when needed. In the extrusion process, rubber gives items flexibility and strength. This special material protects products from wearing out. Natural and synthetic rubber each play unique roles in different industries.
Natural Rubber (NR)
Natural rubber comes from rubber trees. It has impressive features for many uses:
- Excellent elasticity: Natural rubber bounces back to shape after stretching. This makes it great for products that need to return to their original form.
- Resistance to wear: Important for things like car tires. A mix of natural rubber creates durable products that handle road challenges.
- Fatigue resistance: This feature is crucial for long-lasting tire treads.
For example, car tires mainly use natural rubber. The extrusion process shapes the rubber into parts of sturdy tires.
Synthetic Rubber
Synthetic rubber is the new version of a trusted recipe. It comes from petroleum byproducts and offers several benefits:
- Styrene-butadiene rubber (SBR): This rubber is perfect for tires and hoses. It resists wear and aging very well.
- Butadiene rubber (BR): This rubber suits cold-resistant applications. It’s essential in tires needing high flexibility.
- Chloroprene rubber (CR): Used in seals and hoses due to its oil resistance.
Type of Synthetic Rubber | Key Properties | Common Applications |
---|---|---|
Styrene-butadiene rubber | Wear and aging resistance | Tires, hoses |
Butadiene rubber | High elasticity, cold resistance | Tire manufacturing |
Chloroprene rubber | Oil resistance | Seals, hoses |
Synthetic rubbers are versatile. They adapt to specific needs in extrusion processes.
Applications of Rubber in Extrusion
Rubber appears in many components across various fields. Some notable applications include:
- Automotive Industry: Tires, gaskets, and seals depend heavily on rubber extrusion. Rubber ensures smooth vehicle operation.
- Construction: Rubber provides weatherstripping and insulation in buildings. It protects from bad weather.
- Consumer Goods: Toys and shoes get their comfort from rubber extrusion. Remember colorful rubber bands and squishy toys? All thanks to this process!
The versatility of rubber emphasizes its necessity in performance and safety.
Conclusion
Reflecting on my work in product design, understanding the role of rubber in extrusion processes is vital for designers and engineers choosing the right materials. This choice optimizes production while meeting functional requirements.
Natural rubber is derived from rubber tree latex.True
Natural rubber originates from the sap of rubber trees, known for its elasticity and durability, making it essential in various applications like tires.
Synthetic rubber offers no advantages over natural rubber.False
Synthetic rubber provides specific benefits such as wear resistance and customization, making it advantageous for many industrial applications compared to natural rubber.
What Are Composite Materials and Their Benefits in Manufacturing?
Have you ever been amazed by the strength of a light bicycle frame? Or the smooth design of a modern airplane? That’s the wonder of composite materials! These materials are changing the way things are created.
Composite materials blend two or more different substances. These materials create better qualities when combined. They offer important advantages. Strength is increased without too much weight. They resist rust very well. Designers have more options. These materials save money. Composite materials play a crucial role in modern manufacturing.
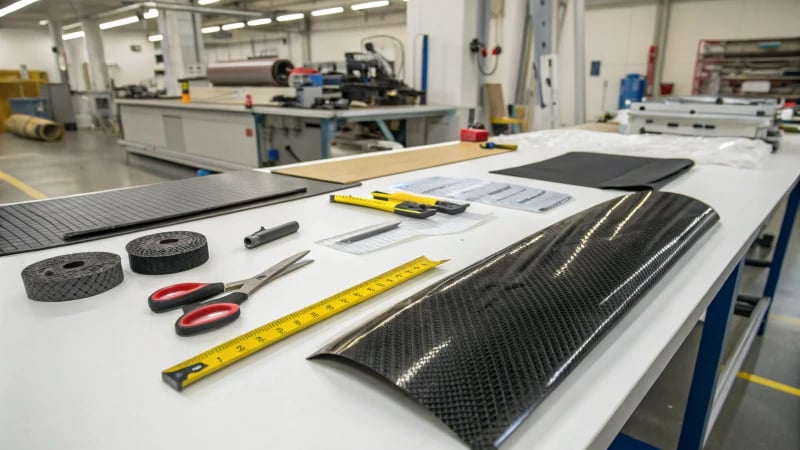
When I first discovered composite materials, I felt amazed. Two ordinary substances could join to create something extraordinary. I work as a product designer. I see how these materials turn ideas into reality. They allow for really innovative designs and push the limits of what seems possible.
Types of Composite Materials
Let’s explore different kinds of composite materials. Each type has unique properties and uses. These qualities inspire new creativity in designs.
Type | Reinforcing Material | Matrix Material | Applications |
---|---|---|---|
Glass Fiber Reinforced Plastic (FRP) | Glass fibers | Thermoplastic or thermosetting plastics | Construction, aerospace, automotive |
Carbon Fiber Reinforced Plastic (CFRP) | Carbon fibers | High-performance resins | Aerospace structural parts, sports equipment |
Aramid Fiber Reinforced Plastic (AFRP) | Aramid fibers | Thermosetting resins | Bulletproof vests, aerospace components |
Natural Fiber Composites | Natural fibers (e.g., hemp) | Biopolymers or thermoplastics | Automotive interior, building materials |
I notice how these composites improve our designs in many ways. Glass fiber is used in construction. Carbon fiber makes sports gear lighter and stronger. Each material plays a key role.
Benefits in Manufacturing
Why should we use composite materials in manufacturing? Here are some benefits I found in my career:
-
Strength-to-Weight Ratio
When I held CFRP for the first time, it felt like holding the future. Such a lightweight material supports heavy loads. It does not buckle easily. In aerospace, every gram matters. This property is very valuable. -
Corrosion Resistance
I designed a component with FRP for a chemical plant. It could endure harsh chemicals and lasted longer. This meant fewer repairs. Clients felt it was a great choice. Composites are perfect for challenging environments. -
Design Flexibility
Creative freedom provided by composites is exciting. Molding them into complex forms allows intricate designs that meet both functional and aesthetic needs. For designers, this flexibility brings new possibilities. -
Cost-Effectiveness
Initial costs may seem high but long-term savings are significant due to durability and less maintenance reducing costs over time; lighter materials mean lower transportation expenses making them appealing for future use. -
Thermal Stability
Using PEEK composites amazed me as they maintain shape under extreme heat which is crucial in high-performance areas like aerospace and medical devices. -
Reduced Environmental Impact
I love natural fiber composites because using renewable resources is very good for sustainability which meets consumer demand for eco-friendly products; making these choices feels good as they positively affect the planet.
Knowing these properties helps us pick the right materials while improving product performance and sustainability. Curious readers might explore more about composite materials by checking out related articles5 for interesting case studies and innovative uses.
Composite materials improve strength-to-weight ratios in aerospace.True
Composite materials like CFRP are crucial in aerospace for reducing weight while maintaining strength, enhancing performance and efficiency in aircraft design.
Natural fiber composites are not environmentally friendly.False
Natural fiber composites utilize renewable resources, making them eco-friendly and supporting sustainability efforts in manufacturing.
How Do I Choose the Right Material for My Extrusion Project?
Locating the ideal material for your extrusion project seems very difficult, right? This guide probably simplifies that process. You will choose the right material. You will feel more confident.
Selecting the best material for your extrusion project begins with knowing your choices. Types include thermoplastics, thermosetting plastics, rubber and composites. Each type offers unique properties. These properties impact performance and cost. Choose one that fits your project’s needs exactly. It is very important.
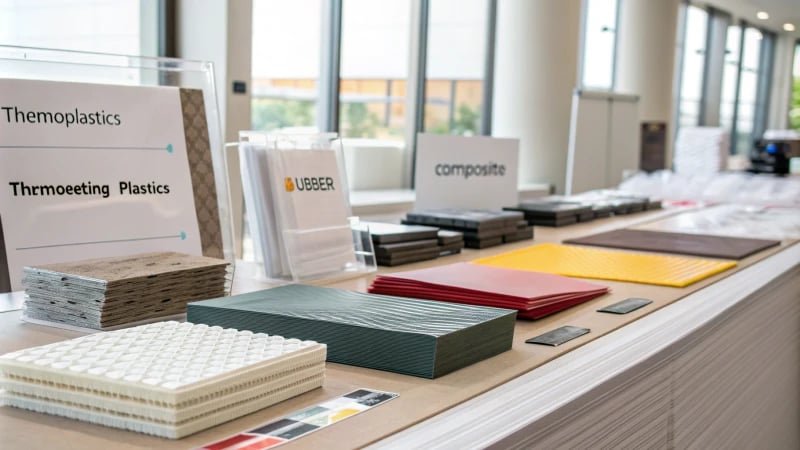
Choosing the right material for my extrusion project is crucial. The materials I select can influence the performance, durability, and cost-effectiveness of the final product. It’s like picking ingredients for a recipe; the outcome depends on the quality and type of what I pick.
Understanding Material Properties
When selecting a material, I consider properties like strength, flexibility, thermal resistance, and chemical durability. Each application may demand different characteristics. For instance, thermoplastics6 like Polyethylene (PE) and Polypropylene (PP) are known for their versatility in applications ranging from packaging to piping.
Material Type | Key Properties | Typical Applications |
---|---|---|
Thermoplastics | Flexibility, low-temperature resistance | Films, pipes, cable insulation |
Thermosetting Plastics | High mechanical strength, heat resistance | Insulating materials, brake pads |
Rubber | Elasticity, fatigue resistance | Tires, hoses |
Composite Materials | High strength-to-weight ratio | Aerospace components, sports goods |
Types of Materials in Extrusion
Understanding the different categories of materials is essential. Here are some of the commonly used materials:
-
Thermoplastics: These materials become pliable upon heating and can be remolded multiple times. Common thermoplastics include:
- Polyethylene (PE): Used for films and pipes due to its corrosion resistance.
- Polyvinyl Chloride (PVC): Excellent for making profiles and drainage systems because of its light weight and mechanical strength.
-
Thermosetting Plastics: These materials harden permanently after being molded. They are typically used in applications requiring durability and heat resistance, such as:
- Phenolic Resin: Commonly used for electrical insulation tubes.
- Urea-Formaldehyde Resin: Ideal for buttons and electrical components due to high hardness.
-
Rubber: Both natural and synthetic rubber are widely used in extrusion for their elasticity. For example:
- Natural Rubber (NR): Common in tire manufacturing due to its wear resistance.
- Styrene-Butadiene Rubber (SBR): Used in various rubber products for its aging resistance.
-
Composite Materials: These combine multiple materials to enhance strength and reduce weight. Examples include:
- Glass Fiber Reinforced Plastic (FRP): Used in construction due to its high strength-to-weight ratio.
- Carbon Fiber Reinforced Plastic (CFRP): Applied in aerospace for structural components due to low density and high strength.
Evaluating Project Requirements
Consider your project’s specific needs when selecting materials. Factors such as:
- Environmental Conditions: Will my product face chemicals or extreme heat?
- Mechanical Stress: What load does it need to handle?
- Cost Efficiency: Does the material cost fit my budget?
Understanding these aspects can help guide my material choice towards achieving optimal performance while minimizing costs.
Testing and Validation
Before finalizing my choice of material, conducting tests can provide insight into how well the material meets my project’s requirements. Consider performing:
- Mechanical Testing: Assessing strength and elasticity under various conditions.
- Thermal Analysis: Evaluating how the material reacts to temperature changes.
- Chemical Resistance Testing: Determining durability against potential exposure to chemicals.
By systematically evaluating these elements thoroughly ensures that my extrusion project utilizes the best material suited for its intended application.
Thermoplastics can be remolded multiple times.True
Thermoplastics become pliable upon heating, allowing them to be reshaped repeatedly without losing their properties.
Rubber is unsuitable for tire manufacturing.False
Natural rubber is widely used in tire production due to its excellent wear resistance and elasticity, making it ideal for this application.
Conclusion
Explore the essential materials for extrusion molding, including thermoplastics, thermosetting plastics, rubber, and composites, highlighting their unique properties and applications in manufacturing.
-
Discover the transformative impact of thermoplastics on manufacturing processes and how they can enhance your designs. ↩
-
Learn how incorporating thermoplastics can lead to more sustainable practices and lower production costs. ↩
-
Find detailed insights into how thermoplastics improve mechanical properties in various applications. ↩
-
Understand how thermoplastics speed up production timelines in extrusion molding processes. ↩
-
Explore the fascinating world of composite materials and their applications to enhance your understanding and decision-making in manufacturing processes. ↩
-
Explore this link to find expert insights on material selection tailored to your specific extrusion needs. ↩