Navigating the intricate world of multi-color injection molding can feel like a rollercoaster ride—thrilling yet daunting.
Common defects in multi-color injection molding of thermoplastics include poor color mixing, stratification, flash, bubbles, and dimension deviation. Solutions involve optimizing material selection, adjusting process parameters, and improving mold design to enhance product quality.
But understanding these defects is just the beginning! Join me as we explore practical solutions that can truly elevate your production outcomes.
Stratification occurs due to incompatible materials.True
Incompatible materials lead to poor adhesion, causing stratification.
How Does Material Selection Affect Multi-Color Injection Molding?
Choosing the right materials is crucial for successful multi-color injection molding, affecting both aesthetics and functionality.
Material selection impacts multi-color injection molding by influencing compatibility, color mixing, and defect rates. Selecting compatible materials can prevent common issues like stratification and dimension deviation. Proper material choice ensures effective color distribution and optimal product performance.
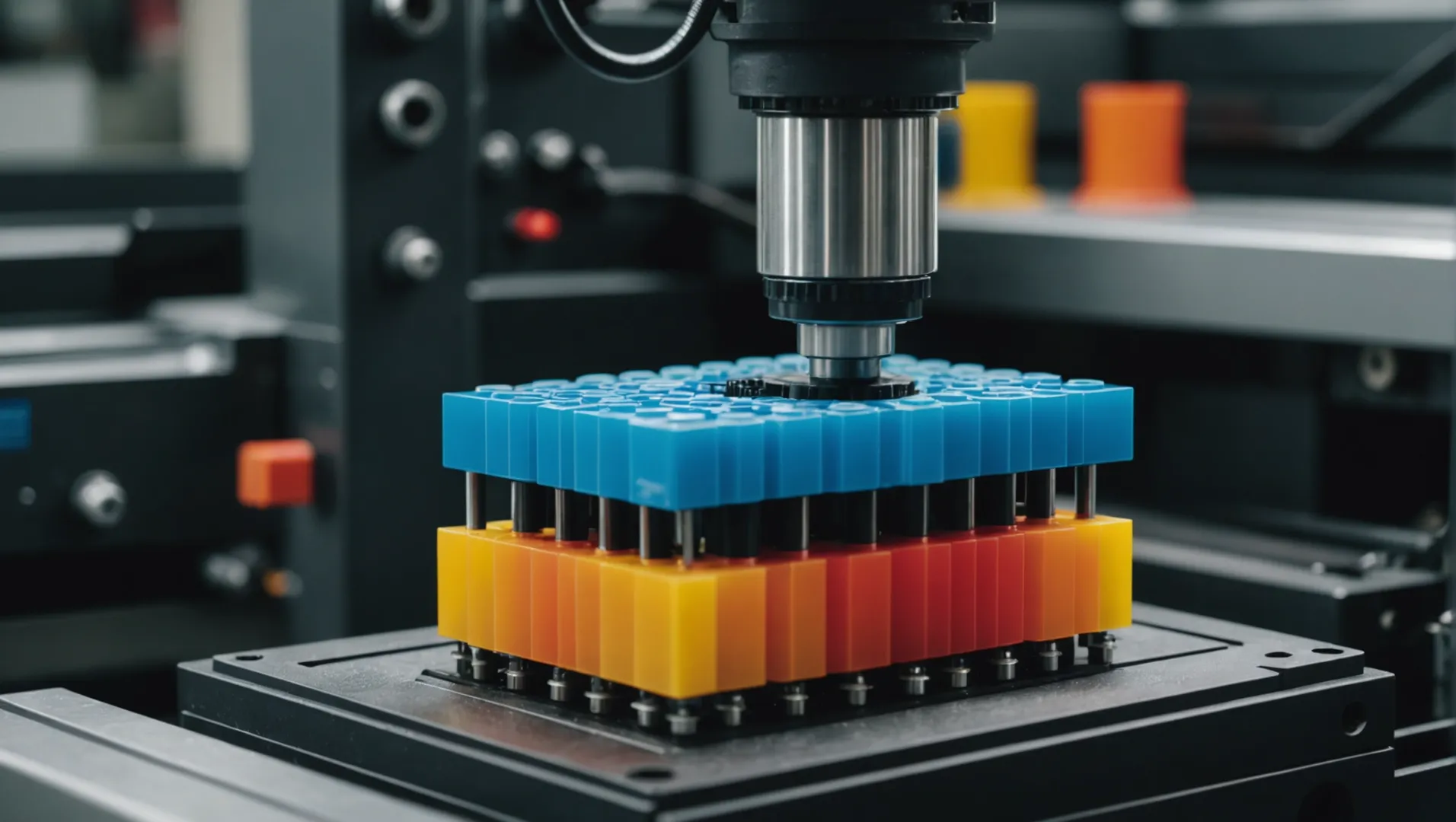
Material Compatibility in Multi-Color Injection Molding
When it comes to multi-color injection molding, the compatibility between different plastic materials is of paramount importance. Incompatible materials can lead to issues such as poor adhesion between layers, resulting in stratification. For example, materials with varying melting points or viscosities might not bond effectively, leading to weak interfaces.
To avoid such problems, it’s essential to select materials with similar processing conditions and compatible chemical structures. This compatibility ensures a seamless bond between layers and reduces the risk of stratification. Investigating material compatibility1 can involve consulting technical datasheets and conducting preliminary tests to evaluate the interaction between chosen materials.
Impact of Material Properties on Color Mixing
The properties of selected materials significantly affect how colors mix during the injection molding process. For instance, pigments in some plastics may disperse unevenly if the material’s flow characteristics are unsuitable. Materials with high viscosity can lead to uneven pigment dispersion, causing defects like poor color mixing.
By choosing materials with appropriate flow properties and pigment compatibility, manufacturers can achieve better color mixing. Techniques such as optimizing pigment dispersion2 through pre-mixing or using additives can further enhance color uniformity across the product.
Influence on Defect Rates
Material selection also plays a crucial role in determining defect rates in multi-color injection molding. Certain materials are more prone to issues like flash or bubbles if their physical properties don’t align well with the mold design or process parameters.
For example, selecting a material with excessive shrinkage might result in dimension deviation, while those with poor thermal stability could contribute to bubbles due to trapped gases. Opting for materials known for their stability and low shrinkage rates can mitigate these risks.
Defect | Cause Related to Material | Solution |
---|---|---|
Stratification | Incompatibility between layers | Select compatible materials |
Poor Color Mixing | High viscosity leading to uneven dispersion | Use materials with better flow characteristics |
Dimension Deviation | Excessive shrinkage | Choose low-shrinkage materials |
By understanding how different material properties affect the injection molding process, manufacturers can make informed decisions that improve product quality and reduce defects. Selecting the right combination of materials is a critical step towards achieving consistent and reliable multi-color injection molded products.
Incompatible materials cause stratification issues.True
Stratification occurs when incompatible materials fail to bond properly.
High viscosity ensures even pigment dispersion.False
High viscosity can lead to uneven pigment dispersion, causing defects.
What Role Does Mold Design Play in Defect Prevention?
Mold design is pivotal in preventing defects in injection molding, directly affecting product quality.
Effective mold design minimizes defects by ensuring optimal material flow, precise temperature control, and accurate cavity dimensions. It addresses issues like poor color mixing and flash through strategic design adjustments.
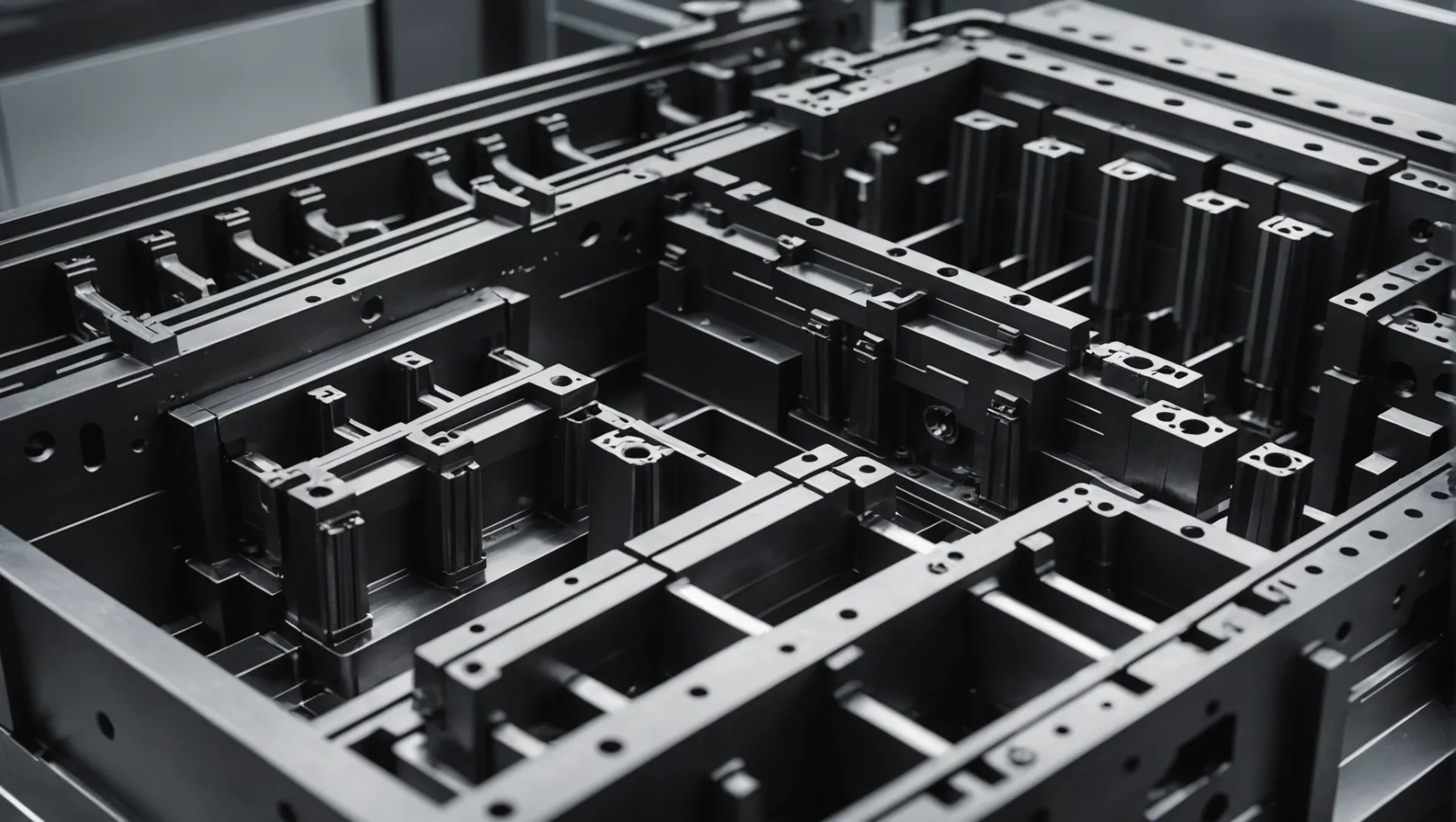
Ensuring Optimal Material Flow
One of the primary functions of mold design in defect prevention is to ensure optimal material flow. A well-designed mold facilitates uniform distribution of the melt, crucial for avoiding defects such as poor color mixing3. This involves strategically placing gates and runners to direct the flow smoothly.
For instance, using balanced runner systems helps distribute the melt evenly, preventing stratification. Moreover, the design of the mold should consider the viscosity of different plastic materials used in multi-color injection molding, as mismatched viscosity can lead to flow imbalance.
Precise Temperature Control
Temperature control is another critical aspect addressed through mold design. Poor temperature management can lead to issues like excessive flash or inadequate fusion of colors. Mold designs equipped with advanced temperature control systems, such as conformal cooling channels, help maintain consistent temperature throughout the molding process.
This ensures that the melt remains at an ideal temperature, reducing the risk of defects caused by improper thermal conditions. For example, incorporating sensors to monitor temperature variations allows for real-time adjustments, optimizing the quality of the final product.
Accurate Cavity Dimensions
Mold design also plays a vital role in ensuring accurate cavity dimensions. Any deviation can result in dimension deviations or unwanted features like burrs. The precision in mold manufacturing is crucial; it requires high-quality materials and advanced machining techniques.
Consider a scenario where a mold’s cavity size does not match the product specifications due to wear or initial inaccuracies. This mismatch leads to defects that compromise product integrity. Regular maintenance and precise fabrication help mitigate these risks.
Addressing Specific Defects through Mold Design
-
Flash and Burr Prevention: Flash occurs when excessive material escapes the mold cavity. This can be mitigated by enhancing clamping force precision and ensuring mold alignment.
-
Bubbles and Voids Reduction: Designing effective venting systems within the mold helps release trapped gases, addressing bubbles and voids that often occur during injection molding.
A table can be utilized to illustrate how different design elements impact specific defect types:
Design Element | Defect Type Addressed |
---|---|
Balanced Runners | Poor Color Mixing, Stratification |
Conformal Cooling | Flash, Burrs |
Precise Cavity Design | Dimension Deviation |
Effective Venting | Bubbles and Voids |
By focusing on these aspects, mold design becomes a proactive strategy for defect prevention in multi-color injection molding processes.
Mold design prevents poor color mixing in injection molding.True
Strategic gate and runner placement ensures uniform material flow.
Conformal cooling channels increase the risk of flash defects.False
They help maintain temperature consistency, reducing flash risk.
How Can Process Parameters Be Optimized for Better Results?
Optimizing process parameters in multi-color injection molding can significantly enhance product quality and reduce defects.
To optimize process parameters in injection molding, focus on controlling temperature, pressure, and speed. Adjusting these settings can improve material flow and color distribution, reducing defects like poor mixing and stratification. Regular monitoring and adjustments ensure consistent high-quality results.
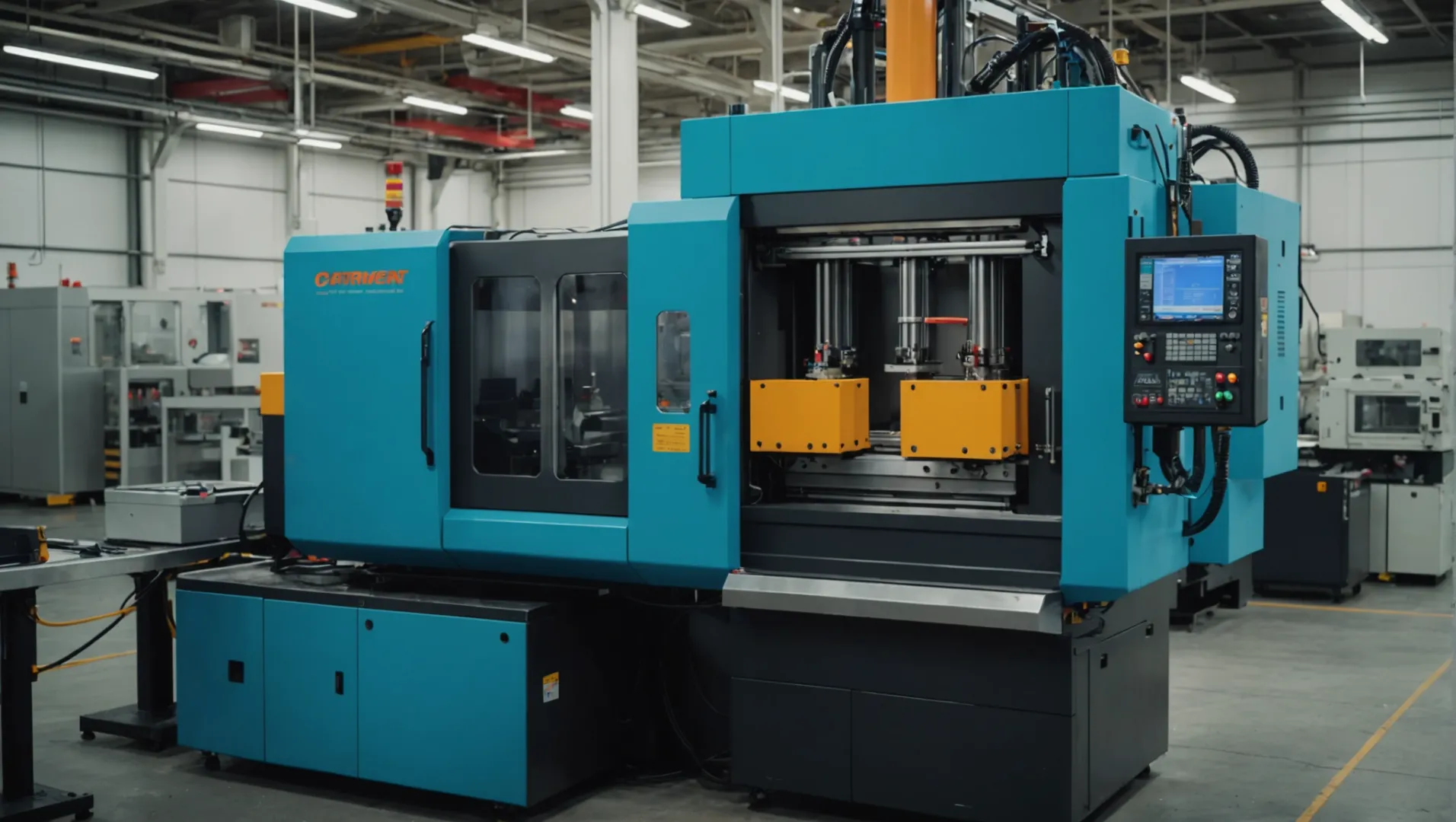
Understanding Key Process Parameters
In multi-color injection molding, several process parameters play a crucial role in determining the quality of the final product. These include melt temperature, injection speed, and pressure, each contributing to specific outcomes in the molding process.
-
Melt Temperature: The temperature at which the plastic material melts is vital for achieving proper flow and color mixing. Too high a temperature can lead to excessive mixing, blurring color boundaries, while too low can result in poor pigment dispersion.
-
Injection Speed: This parameter affects how quickly the molten plastic fills the mold cavity. A fast injection speed can cause different colored melts to disrupt each other, leading to uneven color distribution. Conversely, a slow speed might result in incomplete filling.
-
Injection Pressure: Proper pressure is essential for maintaining material flow within the mold cavity. Incorrect pressure settings can lead to flash or burrs on the molded parts.
Strategies for Optimization
1. Fine-Tuning Melt Temperature
To achieve optimal results, adjust the melt temperature according to the specific material and pigment characteristics. Conducting experimental trials can help determine the best temperature settings for each unique application.
2. Balancing Injection Speed and Pressure
Reduce injection speed and pressure carefully to allow smooth filling without disrupting the color distribution. Ensure these parameters are set precisely to avoid defects like stratification or bubbles.
3. Regular Monitoring and Adjustments
Implement advanced monitoring systems to track real-time changes in process conditions. Regularly reviewing data allows operators to make necessary adjustments swiftly, maintaining optimal production quality.
Advanced Techniques for Precision Control
Embracing technology can further enhance optimization efforts. For example, real-time monitoring systems4 provide insights into the molding process, enabling precise control over all parameters. Such systems can automatically adjust settings based on detected anomalies, ensuring consistent product quality.
Utilize pressure sensors5 to detect variations within the mold cavity, allowing for timely interventions that prevent defects like bubbles or voids.
Overall, optimizing process parameters requires a deep understanding of how each setting impacts the final product. By systematically adjusting these parameters and employing advanced technologies, manufacturers can significantly improve their multi-color injection molding processes.
High melt temperature leads to color blurring.True
Excessive melt temperature causes colors to mix excessively, blurring boundaries.
Slow injection speed improves color distribution.False
Slow speed may cause incomplete filling, not necessarily better color distribution.
What Are the Benefits of Advanced Monitoring Technologies?
Advanced monitoring technologies are revolutionizing industries by providing real-time insights and enhancing decision-making processes.
Advanced monitoring technologies offer numerous benefits, including real-time data collection, improved efficiency, predictive maintenance, and enhanced safety. By integrating these technologies, businesses can optimize operations, reduce costs, and improve overall productivity.
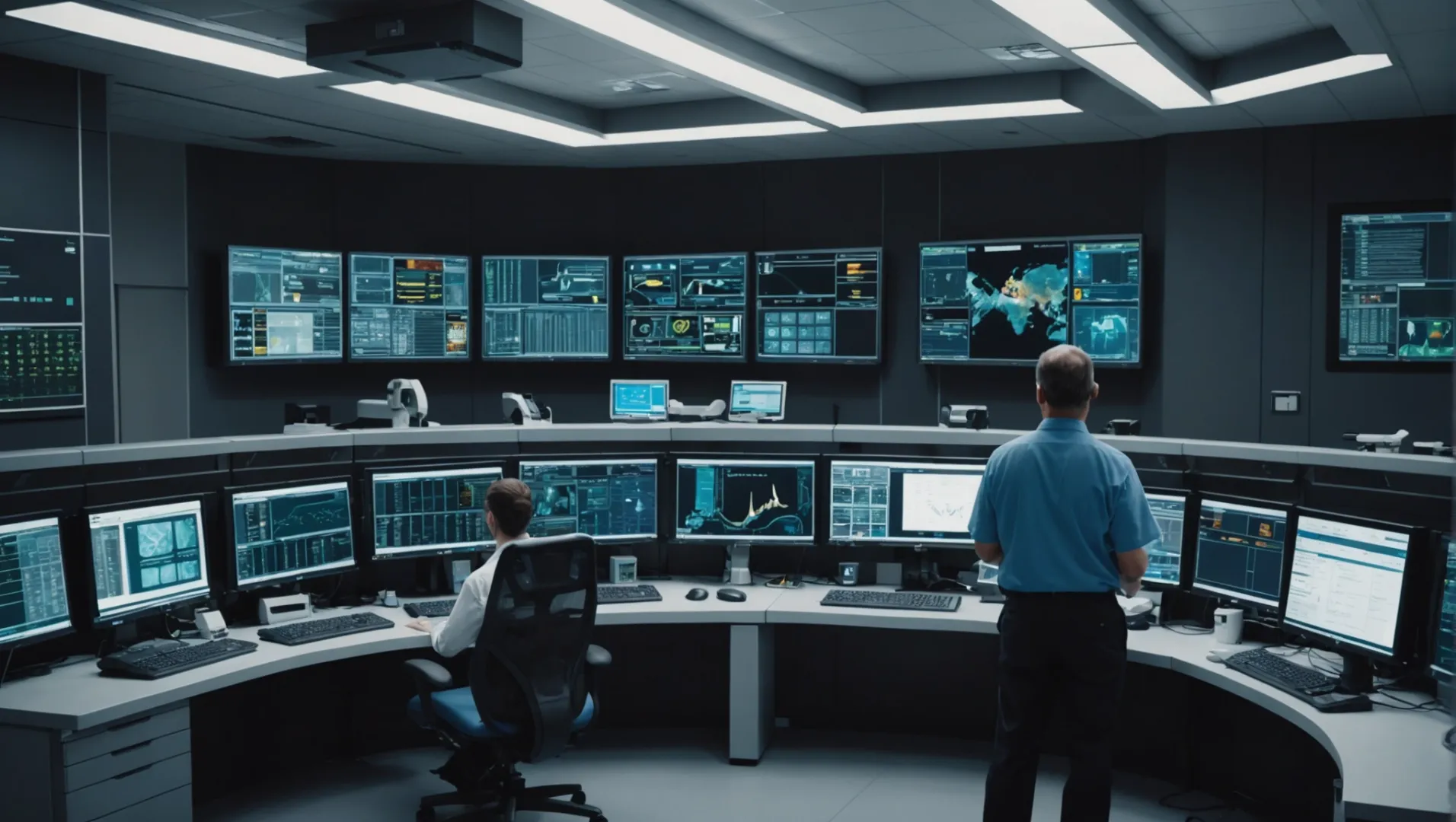
Real-Time Data Collection
One of the most significant advantages of advanced monitoring technologies is the ability to collect data in real-time. This capability allows businesses to make informed decisions quickly. For instance, in the manufacturing sector, real-time monitoring can help in tracking the production line performance and identifying bottlenecks, thus reducing downtime and improving efficiency.
Real-time data collection also aids in environmental monitoring. Industries such as agriculture can benefit by monitoring soil conditions, weather changes, and crop health, allowing for timely interventions to improve yield. Monitoring tools in agriculture6 showcase how these technologies enhance productivity.
Enhanced Efficiency
With real-time insights, businesses can streamline operations by reducing inefficiencies. For example, advanced monitoring systems in logistics can track vehicle locations and traffic conditions, enabling dynamic route adjustments. This not only saves time but also reduces fuel consumption and operational costs.
In healthcare, remote monitoring devices provide continuous patient data, reducing the need for hospital visits and allowing healthcare professionals to focus on urgent cases. This efficiency leads to better resource allocation and improved patient outcomes.
Predictive Maintenance
Advanced monitoring technologies enable predictive maintenance by analyzing historical data to forecast equipment failures. This proactive approach helps in scheduling maintenance activities before a breakdown occurs, minimizing unexpected downtimes and extending equipment life. Predictive maintenance benefits7 are evident in sectors like aviation and automotive, where equipment reliability is crucial.
Enhanced Safety
Safety is paramount in industries such as mining and construction, where environmental hazards are prevalent. Advanced monitoring systems provide alerts on potential risks, allowing for immediate action to prevent accidents. For instance, gas detectors in mines can identify harmful emissions early, ensuring worker safety.
In urban settings, smart surveillance systems use advanced monitoring to improve public safety by detecting unusual activities and dispatching emergency services promptly.
By leveraging these technologies, businesses not only enhance their operational capabilities but also ensure a safer working environment and deliver higher quality services. Exploring real-world applications of monitoring technologies8 reveals their transformative potential across various sectors.
Real-time data collection improves decision-making speed.True
Real-time data allows businesses to make swift, informed decisions.
Predictive maintenance increases unexpected downtimes.False
Predictive maintenance reduces unexpected downtimes by forecasting failures.
Conclusion
By tackling these defects head-on, you’ll not only enhance your production efficiency but also elevate the quality of your products.
-
Discover how to choose compatible materials for seamless layer bonding.: In this blog post, we will discuss the factors that need to be considered when selecting multiple materials for double-shot injection molding. ↩
-
Learn techniques to enhance color uniformity in molded products.: Proper mixing and dispersion of colorants within the resin are crucial for achieving uniform color. Insufficient mixing or improper dispersion … ↩
-
Learn how mold design influences color uniformity in injection molding.: With resin, several pigments are made for mixing, which can in turn widen your choices on what colors to use. In this process, pre-mixed or ‘compounded’ colors … ↩
-
Discover how monitoring systems ensure consistent quality and reduce waste.: Reduce manufacturing losses … The plastics industry is very competitive, which is why Clariprod is here to minimize your production losses. ↩
-
Learn how sensors enhance precision and defect prevention.: Using a high-quality pressure sensor can help minimize poor injection molded part quality and prolong tool life. ↩
-
Discover how real-time monitoring enhances crop management efficiency.: The Benefits of using IoT monitoring solutions in agriculture · Maximized productivity · Improved quality · Reduced need for pesticides. ↩
-
Learn how predictive maintenance minimizes downtime and extends equipment life.: 7 Benefits of Predictive Maintenance · Fewer equipment failures · Reduced MTTR · Increased asset lifetime · Precise assets data · Verification … ↩
-
Explore diverse applications of monitoring technologies across industries.: The best IT monitoring tools quickly detect problems in resources and alert the right respondents to resolve critical issues. ↩