Have you ever dealt with annoying defects in your extrusion or injection molded products? Trust me, I have experienced it too. It’s really a big headache!
Control material purity, optimize process parameters, and maintain mold quality to prevent surface defects, incorrect sizes, and internal flaws in extrusion and injection molding.
On my journey through the molding world, I discovered common defects like surface problems and wrong sizes. These defects can turn a promising product into a disappointment. I remember when my carefully designed part came out with a rough surface. It felt like a punch to the gut! But here’s the good news꞉ using the right preventive actions such as checking material purity and refining process steps helps improve product results significantly. Let’s explore these insights together and find out how to avoid these mistakes.
Surface quality issues are common in injection molding.True
Surface quality defects often arise due to improper cooling or contamination during the molding process.
Material purity has no impact on extrusion defects.False
Maintaining material purity is crucial as impurities can lead to various defects in extrusion processes.
What Are the Key Differences Between Extrusion and Injection Molding?
Feeling overwhelmed about choosing between extrusion and injection molding for your project? Many people experience this. Understanding these differences truly impacts your manufacturing steps and product quality.
Extrusion and injection molding are critical methods for processing plastic. They differ in production style, applications, cycle times and defect management. These differences are important. Selection between these methods probably influences your project’s success. Understanding them really matters.
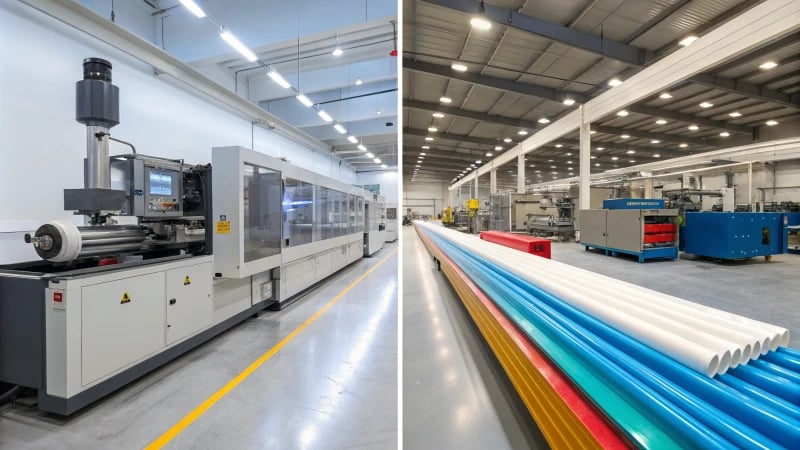
Overview of Extrusion and Injection Molding
When I began exploring plastic manufacturing, understanding the differences between extrusion and injection molding became very important. Each method has its unique use, especially for products we use every day, like electronics and household items.
- Extrusion involves forcing melted plastic through a die to create long shapes like pipes or sheets. Watching the molten plastic flow during my first factory visit was fascinating and a bit intimidating.
- Injection molding, on the other hand, injects molten plastic into a mold to produce intricate shapes with high precision. Holding a product made this way made me admire its sharp edges and perfect contours.
Understanding these differences can greatly influence production choices, costs, and the final product’s characteristics.
Process Differences
Feature | Extrusion | Injection Molding |
---|---|---|
Process Type | Continuous | Discrete |
Material Form | Typically produces long shapes (e.g., tubes) | Produces specific parts (e.g., casings) |
Cycle Time | Longer cycle times due to continuous process | Shorter cycle times due to quick mold filling |
Setup Cost | Lower initial setup costs | Higher initial setup costs due to molds |
Complexity | Less complex shapes | Capable of complex geometries |
Applications
Extrusion excels in projects needing uniform cross-sections, such as window frames. It is reliable and straightforward. However, for components needing detailed features, like smartphone casings, injection molding stands out. It’s about knowing the end use of your product.
Common Defects and Preventive Measures
With experience, I realized that both extrusion and injection molding have their own challenges. Recognizing defects and stopping them early leads to excellent results.
Common Defects in Extrusion
-
Surface Quality Problems
- Rough Surface: The gritty texture often results from impurities or uneven melt temperatures. I have tackled this multiple times.
- Preventive Measures: Screen raw materials and maintain a consistent melt temperature.
- Poor Gloss: I once got a dull batch due to a formulation issue.
- Preventive Measures: Optimize formulations and adjust cooling speeds for gloss.
-
Dimensional Accuracy Problems
- Dimensional Deviation: Projects can suffer when extruded products don’t match design specs, often due to speed inconsistencies or poor mold design.
- Preventive Measures: Accurately match extrusion speeds to avoid future issues.
Common Defects in Injection Molding
-
Appearance Defects
- Flash: A small overflow creates a big mess, usually caused by insufficient clamping force.
- Preventive Measures: Adjust clamping force and improve mold precision.
- Sink Marks: These depressions ruin parts and are often due to uneven thickness.
- Preventive Measures: Maintain uniform wall thickness and tweak holding time during injection.
-
Dimensional Accuracy Problems
- Dimensional Deviation: It’s frustrating when products miss design specs, often due to poor mold accuracy or incorrect process parameters.
- Preventive Measures: Enhance mold accuracy and monitor process parameters effectively.
Efficiency Considerations
My journey through extrusion and injection molding taught me that efficiency is crucial in decision-making. Injection molding typically provides faster production rates because of shorter cycle times but requires higher initial investment in molds. On the other hand, extrusion seems more affordable initially but might take longer.
Understanding these trade-offs helps us work more effectively while managing costs.
For further insights on optimizing processes and reducing defects, check out these resources:
Extrusion produces continuous shapes like pipes and sheets.True
Extrusion is specifically designed to create long, continuous shapes by forcing melted plastic through a die, unlike injection molding.
Injection molding is faster than extrusion for production cycles.True
Injection molding typically has shorter cycle times due to its discrete process, allowing for quicker production compared to the continuous nature of extrusion.
How Do Material Selection and Preparation Affect Defect Rates?
Ever thought about how the materials we pick and prepare greatly affect the quality of our products? I often think about this. Let’s explore the realm of manufacturing. These choices and preparations really influence defect rates.
Choosing good materials and preparing them well are very important. They probably affect how many defects show up. The quality of the product depends on it. High-quality materials help lower problems such as bubbles and rough surfaces. Proper preparation also reduces dimensional inaccuracies. This is key. It’s really crucial.
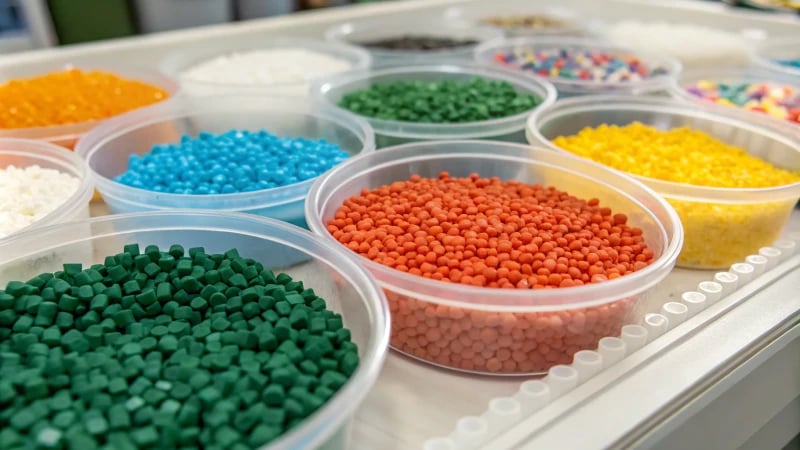
Understanding Material Selection
Material selection is a critical aspect in manufacturing that directly impacts defect rates. The properties of materials, such as strength, ductility, and thermal stability, play a significant role in determining the final product’s quality.
When I started in manufacturing, I was surprised by how material choice could greatly impact a product. It’s like picking the right ingredients for cooking. If starting with bad components, you might get a poor outcome.
For instance, using low-quality raw materials may lead to defects like bubbles or rough surfaces in the final product. Therefore, it is vital to screen materials thoroughly before usage. Explore more about material properties2.
The Importance of Material Preparation
Preparation of materials, such as drying and filtering, is equally essential in minimizing defects. If raw materials contain moisture or impurities, this can lead to internal quality issues like porosity or stress concentrations. Effective preparation methods include:
- Drying: Fully drying raw materials helps prevent bubbles in the product.
- Filtering: Screening to remove impurities ensures a smoother surface finish.
These preventive measures can significantly reduce defect occurrences. Learn about effective preparation techniques3.
Common Defects from Poor Material Choices
When materials are not adequately selected or prepared, various defects can arise. Here’s a table summarizing some common defects:
Defect Type | Description | Causes | Preventive Measures |
---|---|---|---|
Rough Surface | Grainy or orange peel texture on products | Impurities, uneven melt temperature | Screen raw materials, control melt temperature |
Bubbles | Internal voids reducing strength and density | Moisture, volatiles in raw materials | Dry materials thoroughly before processing |
Dimensional Deviation | Actual size not matching design specifications | Uneven cooling, inaccurate mold design | Optimize cooling systems and mold design |
Flash | Excess plastic on parting surface | Insufficient clamping force | Adjust clamping force and improve mold precision |
Sink Marks | Local depressions on the product surface | Uneven wall thickness during cooling | Ensure uniform wall thickness and adjust cooling |
During my career, I have seen defects from bad material selection and preparation.
Impact of Extrusion and Injection Molding Defects
Defects can differ based on the manufacturing process—extrusion or injection molding. For example:
- Extrusion often faces challenges like rough surfaces and dimensional deviations due to improper melt temperature and speed control.
- Injection molding may result in flash and sink marks from issues like insufficient clamping force and uneven wall thickness.
Understanding these differences allows for targeted defect reduction strategies. Discover more about manufacturing processes4.
Material selection affects the quality of manufactured products.True
Choosing high-quality materials directly influences the final product's defect rates and overall quality in manufacturing processes.
Drying raw materials prevents bubbles in the final product.True
Thoroughly drying materials eliminates moisture, which is a primary cause of bubbles and internal defects in manufactured items.
How Does Mold Design Help Prevent Common Defects?
Ever thought about how mold design influences a product? Mold design is crucial. It’s amazing how a technical part affects the quality of everyday items. Let’s explore this important aspect of manufacturing together.
Mold design greatly impacts the quality of molded products. It addresses common defects through smart design decisions. Designers improve surface quality. They also achieve precise dimensions and preserve the product’s internal structure. Manufacturers obtain better product performance through these methods.
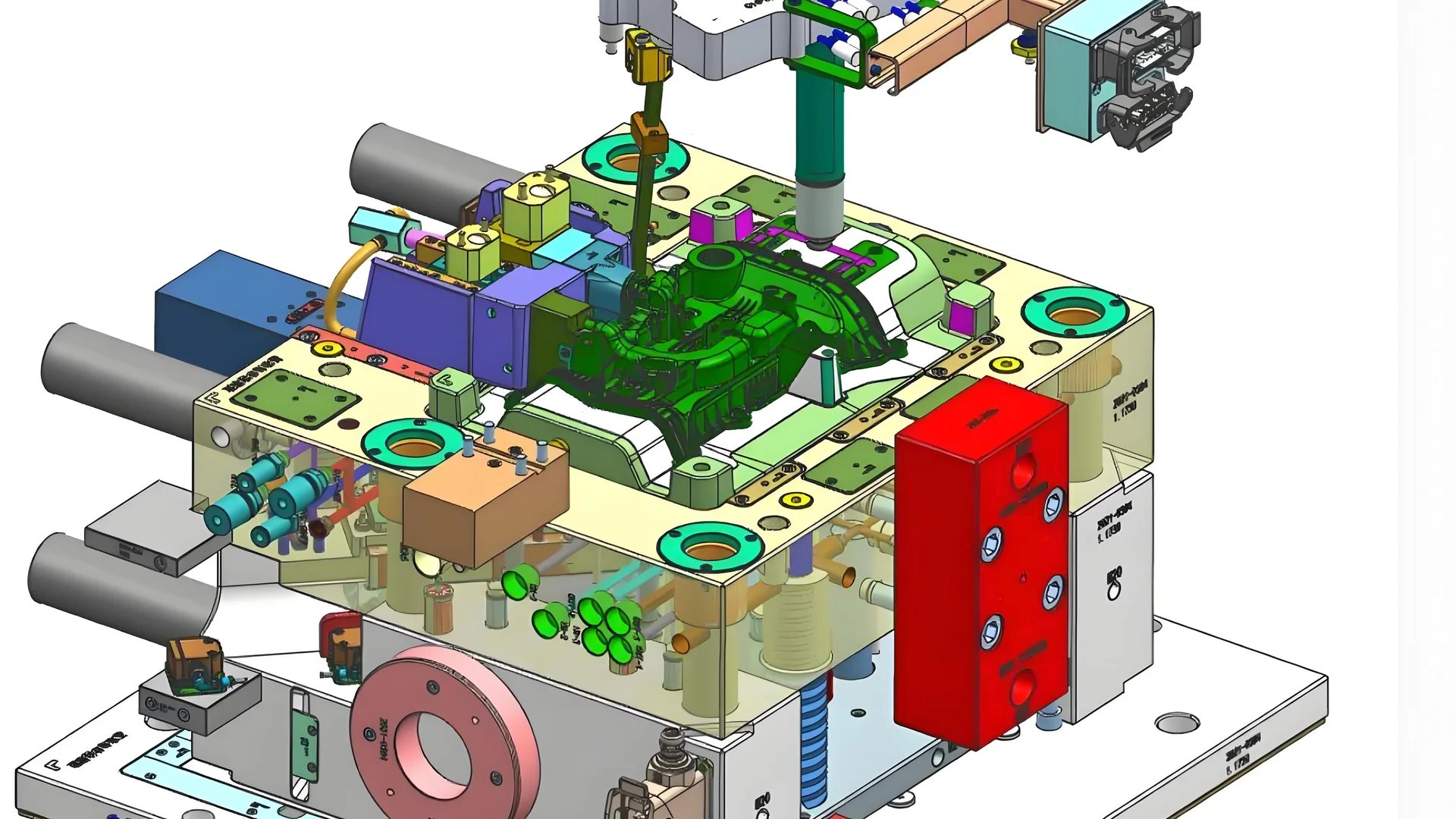
Understanding the Impact of Mold Design
Mold design is a critical factor in ensuring the production of high-quality molded products. It directly influences not only the aesthetics but also the functionality and durability of the final product. By addressing common defects through thoughtful mold design, manufacturers can enhance production efficiency and reduce waste.
Common Defects in Extrusion Molding
Extrusion molding often encounters several common defects, including:
Defect | Description | Preventive Measures |
---|---|---|
Surface Quality Issues | Rough surfaces or poor gloss can arise from impurities, uneven temperatures, or mold surface quality. | Screen raw materials, maintain consistent temperatures, and regularly polish molds to enhance surface finish. |
Dimensional Deviations | The size of products may deviate from design specifications due to speed mismatches or mold design flaws. | Use precision sensors to match extrusion and traction speeds, and optimize mold design for dimensional accuracy. |
Internal Quality Issues | Problems like bubbles or internal stress can compromise product integrity. | Dry materials thoroughly, control melt temperatures, and adjust cooling speeds to avoid defects. |
By focusing on these issues during the mold design phase, designers can implement solutions that significantly mitigate defect occurrence.
Addressing Injection Molding Defects
In injection molding, several common defects can arise, including:
Defect | Description | Preventive Measures |
---|---|---|
Appearance Defects | Issues like flash, sink marks, and flow marks can result from improper clamping or uneven melt flow. | Ensure sufficient clamping force, optimize gate positions, and control injection speed for uniform filling. |
Dimensional Accuracy | Inaccurate dimensions can stem from poor mold precision or incorrect process parameters. | Utilize high-precision equipment for mold manufacturing and accurately measure injection volumes during processing. |
Internal Quality Problems | Porosity and excessive internal stress can lead to structural failures during use. | Improve exhaust systems and optimize cooling methods to ensure even cooling and reduced stress concentrations. |
By incorporating these preventive measures into the mold design process, manufacturers can enhance product quality and performance while minimizing defects.
Conclusion: The Importance of Mold Design in Quality Control
In summary, effective mold design is integral to preventing common defects in both extrusion and injection molding processes. By understanding the relationship between mold features and defect outcomes, designers like Jacky can create more reliable products that meet industry standards. For further insights on optimizing your designs for enhanced quality, explore advanced techniques5 in mold design practices.
Mold design directly impacts product durability and functionality.True
Thoughtful mold design enhances product durability and functionality by addressing defects effectively during the manufacturing process.
Surface quality issues can be resolved through proper mold polishing.True
Regularly polishing molds helps to improve surface finish, reducing roughness and enhancing aesthetic quality in molded products.
How Can Process Monitoring Improve Quality Control in Molding Operations?
Ever wondered how process monitoring truly changes quality control in molding work? Let’s explore how this helps reduce defects. It really helps maintain consistent product quality.
Process monitoring greatly improves quality control in molding operations. It offers real-time data analysis. This information allows quick corrective actions. These actions reduce defects like flash and sink marks.
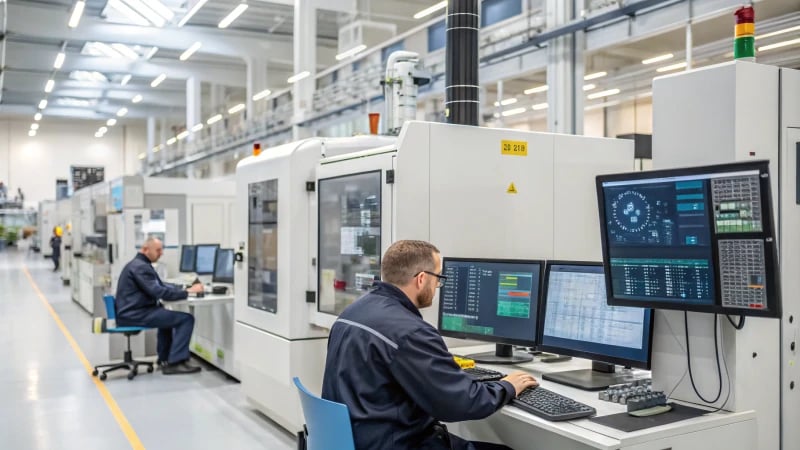
Understanding Process Monitoring in Molding Operations
Process monitoring involves continuous observation and analysis of the molding operation, which plays a crucial role in enhancing quality control. It allows manufacturers to detect anomalies in real-time, facilitating immediate corrective actions. This proactive approach can significantly reduce defect rates and improve overall production efficiency.
For instance, implementing sensors that monitor temperature and pressure during the injection process can help ensure that the conditions remain optimal. By collecting data from these sensors, manufacturers can analyze trends over time, identifying potential issues before they escalate. This leads to a more consistent product quality, minimizing the chances of defects such as flash or sink marks.
Common Defects Addressed by Process Monitoring
In molding operations, several defects can arise, each requiring specific monitoring techniques:
Defect Type | Description | Monitoring Techniques |
---|---|---|
Surface Quality Problems | Rough or dull surfaces due to impurities or uneven cooling. | Temperature and pressure sensors. |
Dimensional Accuracy Issues | Mismatched sizes caused by uneven cooling or improper speed. | Speed sensors and precision controllers. |
Internal Quality Problems | Bubbles or excessive internal stress that can weaken products. | Moisture sensors and exhaust monitoring. |
By addressing these defects through process monitoring, manufacturers can implement targeted preventive measures, ensuring higher quality output.
The Role of Data Analysis
Data analysis plays a vital role in enhancing quality control. By gathering data from various stages of the molding process, companies can apply statistical process control (SPC) methods to identify trends and anomalies. For example, control charts can be used to monitor key parameters such as injection pressure and cooling time.
In addition, advanced analytics can help in predicting when a defect is likely to occur based on historical data. This predictive capability enables manufacturers to make informed decisions about maintenance and adjustments before quality is compromised.
Technologies Enhancing Process Monitoring
Several technologies can enhance process monitoring in molding operations:
- IoT Sensors: Internet of Things (IoT) sensors can provide real-time data on machine performance and environmental conditions.
- Machine Learning: Applying machine learning algorithms allows for advanced predictive analytics based on large datasets.
- Automated Reporting Systems: These systems can automatically generate reports on production quality, highlighting areas that need attention. By using automated reporting, manufacturers can streamline their quality assurance processes.
Implementing these technologies not only improves quality control but also enhances the overall efficiency of molding operations.
Conclusion
In summary, effective process monitoring significantly enhances quality control in molding operations by allowing for real-time data collection, analysis, and corrective action. This proactive approach helps mitigate common defects, ensuring that the final products meet the desired specifications and quality standards. For further exploration on enhancing your molding operations, consider checking out related resources here for best practices and methodologies.
Process monitoring reduces defect rates in molding operations.True
Real-time data analysis from process monitoring allows manufacturers to detect and correct issues promptly, leading to lower defect rates in products.
IoT sensors are unnecessary for effective process monitoring.False
IoT sensors provide critical real-time data that enhances process monitoring, making them essential for effective quality control in molding operations.
Conclusion
Explore common defects in extrusion and injection molding processes, along with effective preventive measures to improve product quality and reduce manufacturing errors.
-
This link provides detailed comparisons of extrusion vs injection molding that can enhance your understanding of their applications. ↩
-
Explore this link for insights on how material choices impact manufacturing outcomes and defect rates. ↩
-
Learn about best practices for material preparation to reduce defects in production processes. ↩
-
Understand the relationship between manufacturing processes and defect types to enhance production quality. ↩
-
Discover effective strategies for mold design that prevent defects in molded products. ↩